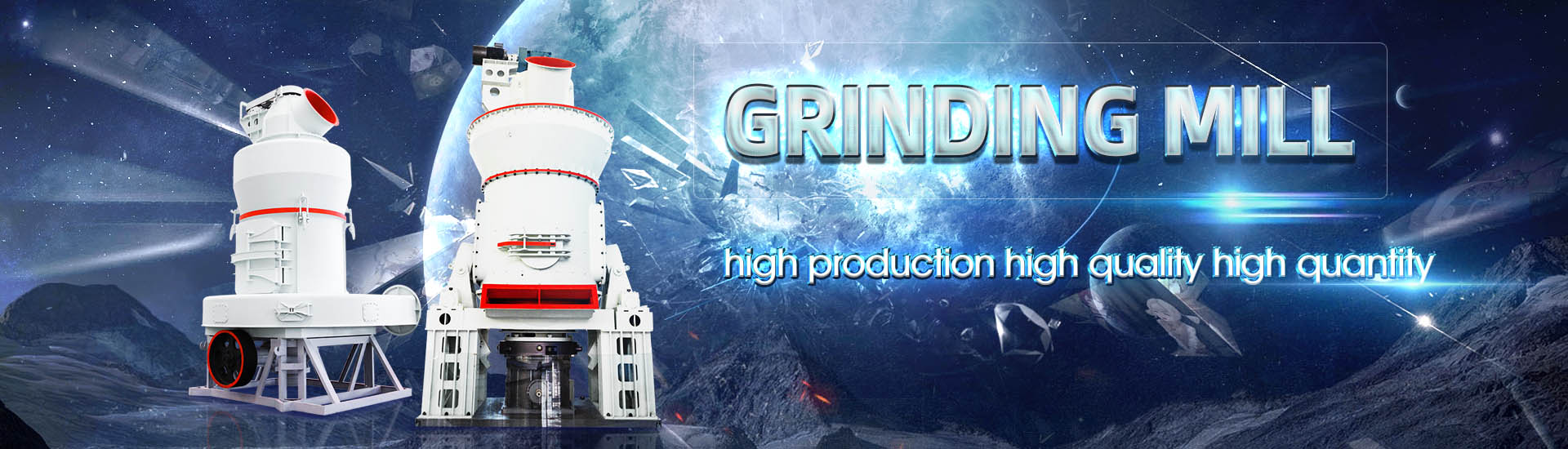
Measures to increase the output of 3x13M cement mill
.jpg)
BALL MILLS Ball mill optimisation Holzinger Consulting
Ball mill optimisation As grinding accounts for a sizeable share in a cement plant’s power consumption, optimisation of grinding equipment such as ball mills can provide significant cost Optimizing the operation of cement mills is essential to maximize productivity, reduce energy consumption, and improve the quality of the final cement product In this article, we will delve Cement Mill Optimization: Practical Strategies for Enhanced Optimization of the Cement Ball Mill Operation Optimization addresses the grinding process, maintenance and product quality The objective is to achieve a more efficient operation and OPTIMIZATION OF CEMENT GRINDING OPERATION IN BALL MILLSThe mill performance is evaluated and recommendations are formulated based on the past history of the mill operations, inspections, process measurements, feed/product characteristics and PROCESS DIAGNOSTIC STUDIES FOR CEMENT MILL
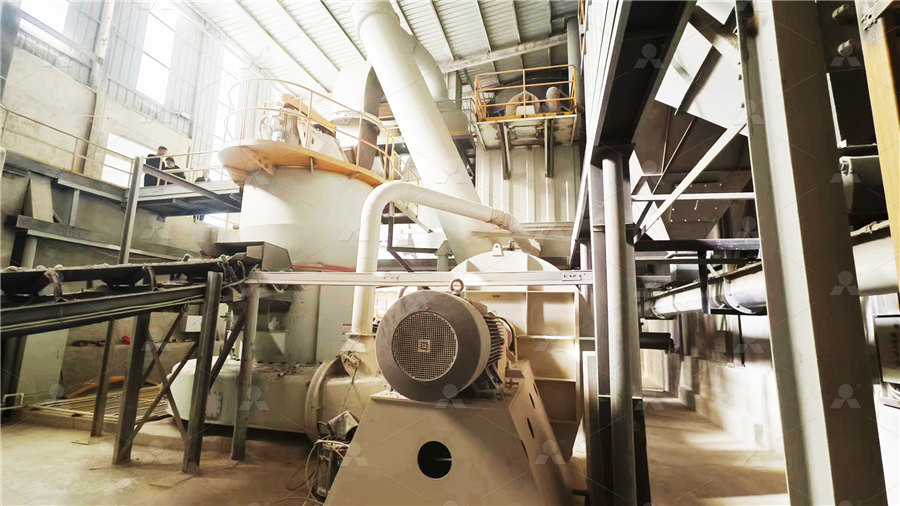
How to Improve Cement Ball Mill Performance
In this article, we will discuss the measures that can improve the ball mill’s performance The particle size of the feed material is an important process parameter that restricts the grinding Cement grinding capacity of Ball mill increases by adjustment of air gap in the V Separator with proper air distribution Maintaining uniform air gap between plates and steps in the V INCREASING OUTPUT OF CEMENT GRINDING IN BALL MILL CASE 1987年8月1日 Optimizing control for ball mills enabled us to increase the mill throughput by 35% and to reduce the specific power consumption by 35% But after we integrated these Optimization of Cement Manufacturing Process ScienceDirectOptimization addresses the grinding process, maintenance and product quality The objective is to achieve a more efficient operation and increase the production rate as well as improve the run Optimization of Cement Grinding Operation in Ball Mills PEC
.jpg)
Optimizing the control system of cement milling: Process
2014年3月1日 Based on a dynamical model of the grinding process in closed circuit mills, efficient efforts have been made to optimize PID controllers of cement milling The process A 10 MW cement mill, output 270 tonnes per hour A cement mill (or finish mill in North American usage [1]) is the equipment used to grind the hard, nodular clinker from the cement kiln into the fine grey powder that is cementMost cement is currently ground in ball mills and also vertical roller mills which are more effective than ball millsCement mill Wikipedia2019年3月1日 An essential part of modern quality management system in cement production is stateoftheart radiation measurement technologies based on methods of neutron activation, Xray fluorescence and X (PDF) Cement Quality Control By Using Modern 2021年2月8日 Abstract China is the largest cement producer and consumer in the world Cement manufacturing is highly energyintensive and is one of the major contributors to carbon dioxide (CO2) and air pollutant emissions, which ACP Carbon and air pollutant emissions from
.jpg)
Control System Architecture for a Cement Mill Based on Fuzzy
2015年2月14日 T aking into consideration the loop for grinding circuit of the cement mill, inputs and output The measures of risk resulting system to increase the throughput of the mill by 326% and How to improve output of Cement vertical mill has always been the concern of users Due to the lack of attention to some small factors, the output of the vertical mill may be reduced One of the more obvious performances is that vertical grinding roller and disc liner are worn after a period of use Invisible is equivalent to increasing the height of the retaining ring, increasing the How To Improve Output Of Vertical MillPDF On Oct 1, 2015, Mohan Singh Panwar and others published INCREASING OUTPUT OF CEMENT GRINDING IN BALL MILL CASE STUDY Student, 2 Guide, 3 External Guide Find, read and cite all the (PDF) INCREASING OUTPUT OF CEMENT GRINDING IN BALL MILL • Increased output By continually monitoring both the loading of the mill and the balance of material flows through the system, it is possible to identify situations when the feed to the mill and the output can be increased Increased output over extended periods of time has been observed on mills controlled by Expert OptimizerIndustrial : Optimization for the Cement Industry ABB
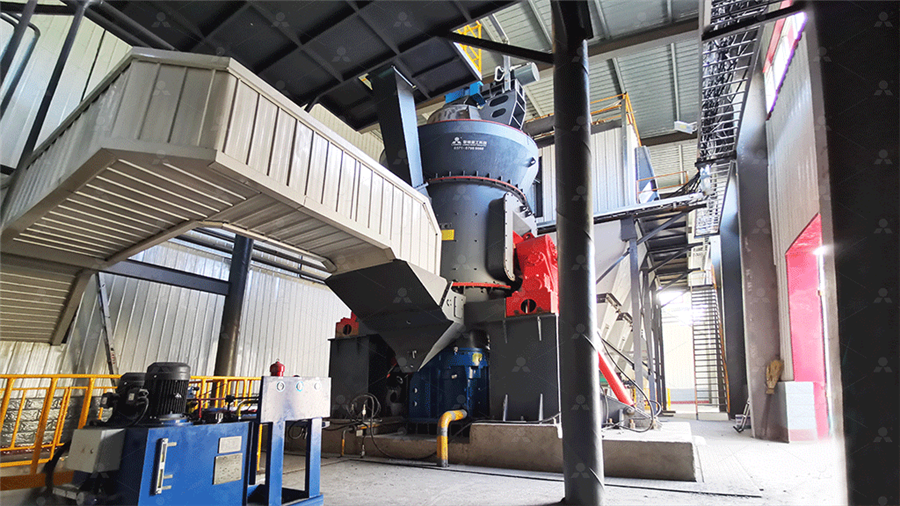
(PDF) Cement mill optimization: Design parameters
1995年10月29日 The control system, based on a 2S4265 CNC unit, allows the milling machine to be operated in universal mode (with manual control), automatic mode (to a set program), copying mode, gauging mode ABSTRACT The increasing demand for ‘‘finer cement’’ products, and the need for reduction in energy consumption and green house gas emissions, necessitate the optimization of grinding circuitsThe Improvement of Mill Throughput Using Barmac2019年1月8日 Overview of cement demand models Chinese scholars have carried out many studies on the cement output and demand predictions As early as the 1990s, Gao used the logistic prediction model (LPM) to predict China’s cement output and demand by 2000Although the model forecasts up to 2000, the cement output and demand before the year is close to the China’s cement demand and CO2 emissions toward 2030: from 2018年11月11日 Fig 1 Illustration of the cement mill Z1 in kufa cement plant 22 The principle of grinding process The idea of grinding clinker and turning it into cement with a certain specific surface is basedIMPROVING PRODUCTIVITY BASED ON THE MOVEMENT OF
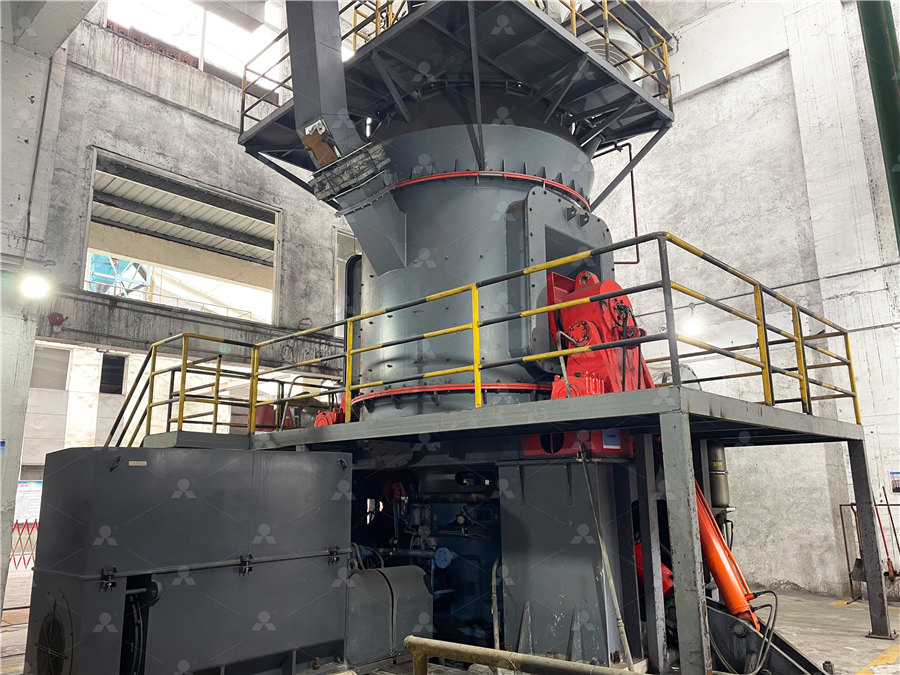
IMPROVING THERMAL AND ELECTRIC ENERGY
2019年3月8日 PDF Efficiency Best Practices in Cement Plantsi Find, read and cite all the research you need on ResearchGate2016, Grinding Aid Effectiveness in Cement Ball Mill The introduction of the grinding aid (GA) has been started more than 50 year ago, to facilitate clinker grinding in cement mills improve mill output despite of the above features, the wear of mill interior parts well be increase`Grinding Aid Effectiveness in Cement Ball Mill Academiayield substantial benefits in terms of energy savings and capacity increase Optimization of the Cement Ball Mill Operation Optimization addresses the grinding process, maintenance and product quality The objective is to achieve a more efficient operation and increase the production rate as well as improve the run factorOPTIMIZATION OF CEMENT GRINDING OPERATION IN BALL MILLSFLSmidth acquired the rights to his patent and started selling an improved version of this mill all over the world For the cement industry the ball mill was really an epochmaking breakthrough as for almost 80 years it was the predominant mill for grinding of raw materials and coal, and still today is the most used mill for cement grindingCement grinding Vertical roller mills VS ball mills
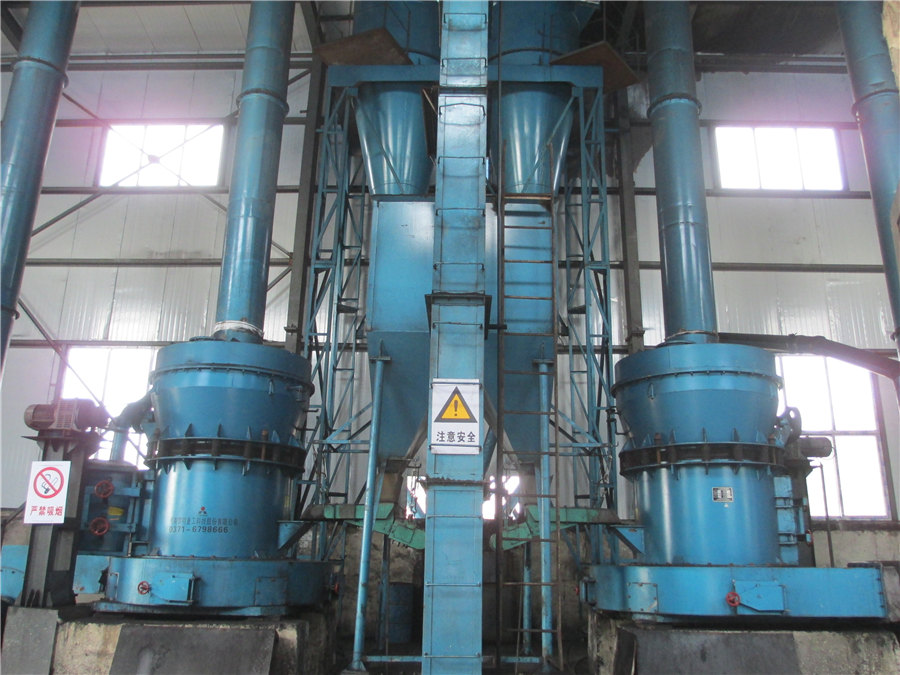
(PDF) The improvement of mill throughput using Barmac pregrinding
2007年1月1日 The results show that significant clinker size reduction occurs in Barmac VSI crushers, which can increase the cement mill throughput and decrease the energy consumption in finish milling2013年3月1日 High efficiency classifiers have been shown to bring about a reduction of 28–37 kW h/t in raw materials, save fuel and yield a narrow particle size distribution, increase the grinding mill capacity by up to 15%, produce more uniform particles of raw meal and cement and thus enhance the quality of the product and the clinker [90]An overview of energy savings measures for cement industries2011年3月1日 Kiln capacity increased from 6100t/day to 6300t/day This could be further increased to 6750t/day Specific fuel consumption decreased from 795kcal/kg of clinker to 770 kcal/kg of clinker After phase II this could be further reduced to 729 kcal/kg of clinker The cement mill capacity was increased from 135t/hr to; 145t/hrIntegrated performance enhancement in the cement industry2020年2月1日 They showed that the polymerbased grinding aid increases the specific surface, prevents agglomeration and ball coatings, and improves the roundness, fineness and fluidity of the ground cementEnergy and exergy analyses for a cement ball mill of a new
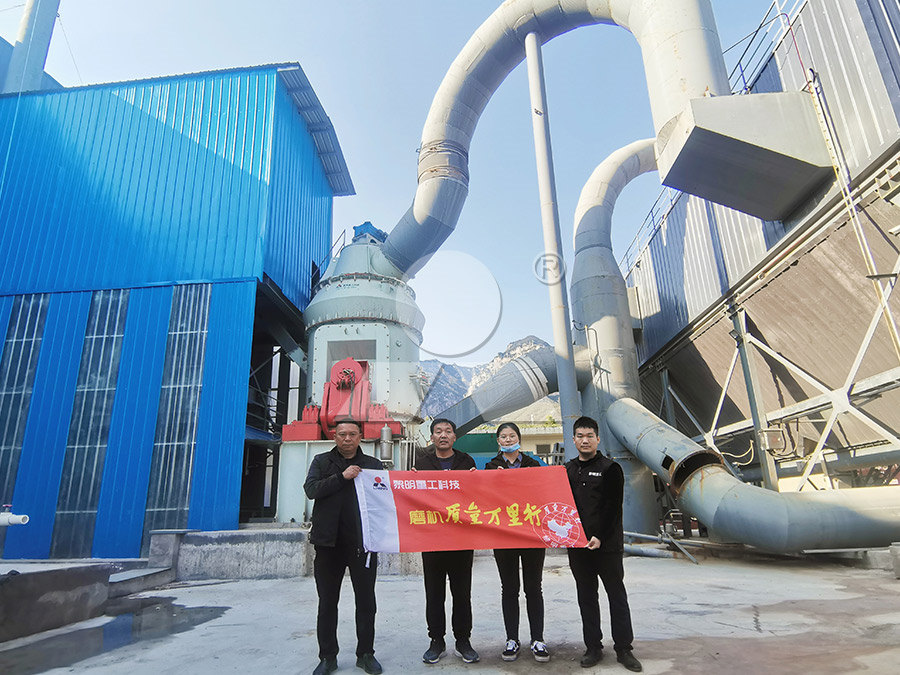
Ball Mill For Cement Grinding – Cement Ball Mill Ball Mill
Pregrinding:it refers to adding a grinding machine in front of the cement ball mill to increase the output of the original grinding system by a large margin This method features large investment and relatively complex process but it can increase the output of cement ball mill by up to 50%Relative to cement ball mill, crushing the storehouse of all functions and most of the fine grinding storehouse function has moved to pregrinding section, ball mill is concentrated on finish grinding fine cement particles and plastic, pre Roller Press Install For PreGrinding Before Cement Previous Post Next Post Contents1 Ball charge optimization2 1 How to use the BP21 2 Description of the main indicators used in this BP2101 The residue on 2mm/4mm before partition wall2102 Material filling level and ball charge expansion211 Cement mill specific power 1st compartment 212 Raw mill specific power 1st compartment Ball charge Ball charge optimization INFINITY FOR CEMENT EQUIPMENT2021年6月29日 Nowadays, ball mills are widely used in cement plants to grind clinker and gypsum to produce cement The research focuses on the mill speed as well as air classifier speed effect on the two Effects of Mill Speed and Air Classifier Speed on
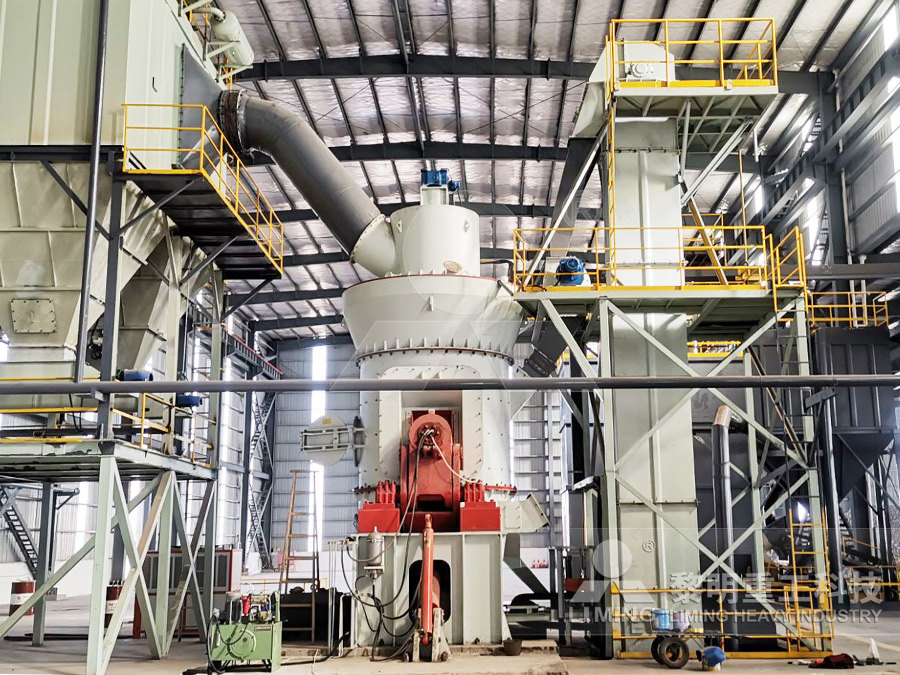
The use of electrical energy in cement production
In cement industry about 110 kWh of electrical energy is consumed to produce one ton of cement and about 26% of the total electrical power is used during farine production2023年12月28日 For example, in the cement industry, actual production shows that when the product fineness is 5 to 10%, the output decreases by 5% for every 2% decrease in fineness When the fineness is controlled below 5%, choosing the appropriate powder selection efficiency and cycle load rate is essential in increasing the mill’s output 7Factors Affect The Output and Quality of Ball Mills And How to Beside the well known chemical interaction between the cement and the additive, another critical contribution to the mill output increase and the cement strengths improvement is represented by the two following improvement obtained with the use of MAGA/VM 10: Enhanced classifier performances Improved particle size distributionImprovement of cement performances through the use of 2024年1月23日 The efficient operation of a cement mill is vital for the overall productivity and quality of the cement production process Constant adaptation and optimization are essential in the dynamic environment of cement manufacturing to meet quality standards and How To Optimize The Operation Of The Cement Mill
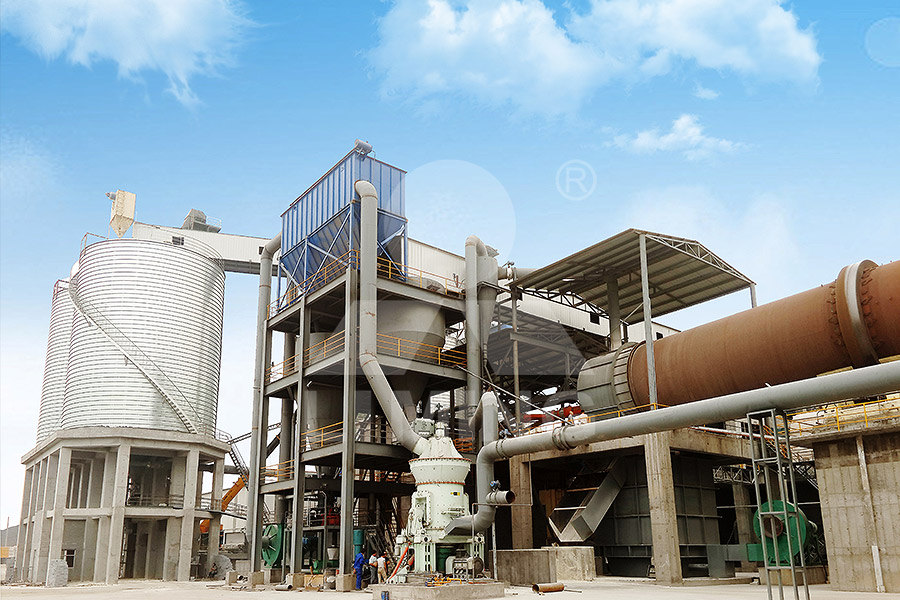
Environmental impact of cement production and Solutions: A
2022年1月1日 As the demand for cement supply is continually growing, this causes an increase in the use of aggregate, especially limestone since it is important in the production of Portland cement [13], [14]Exhaustion of the earth’s nonrenewable resources is a growing dilemma when the reason is that the energy consumption has rapidly increased during the 21st century [15]Primary Ball mill controls are: Mill drive power or mill differential pressure to control mill feed rate Mill Sound level to control filling level inside mill with feed rate Mill outlet gas temperature Mill outlet material temperature Cement temperature Outlet gas flow determined from mill inlet and outlet drafts or flow meters installedCement Grinding Cement Plant Optimization2021年6月10日 However, the cement compressive strength (3, 7 and 28 days) decreases and the cement setting time (initial and final) increases by reducing the cement finenessVentilation Prediction for an Industrial Cement Raw Ball Mill by 2021年6月1日 A major challenge is to ensure that production, supply, and customer processes are correctly implemented and stabilized These processes transform the input material and increase its value [1][2 Implementation of Lean Manufacturing in a
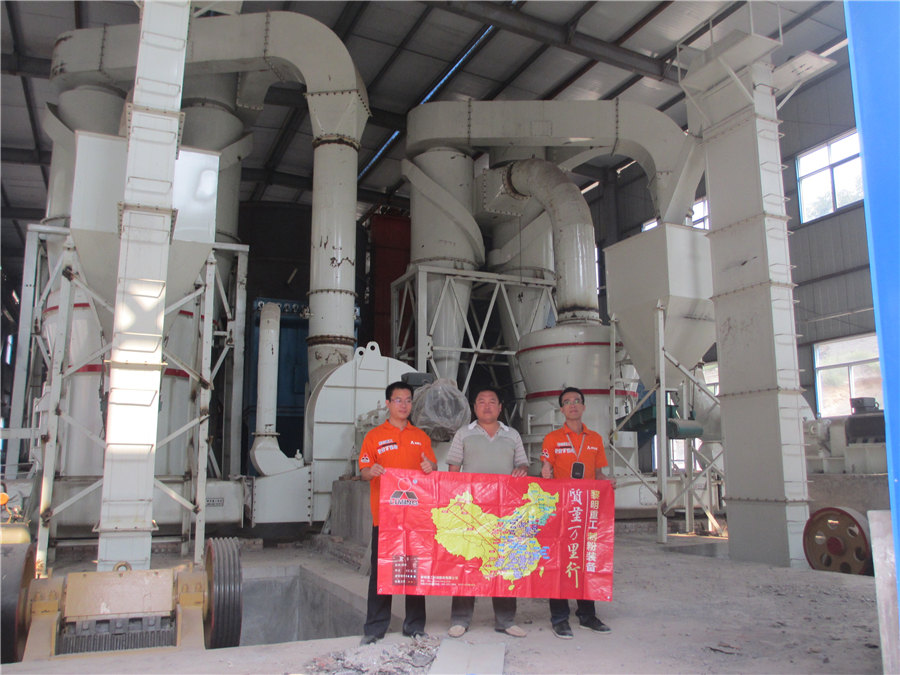
Picture: Loesche GmbH, Germany CEMENT SikaGrind® FOR VERTICAL ROLLER MILL
Recognisable increase in early strength SikaGrind®200 Minor treatment cost Typical dosage: 004% Chloride free High increase in early strength SikaGrind®120 Moderate treatment cost Typical dosage: 015% Contains Chlorides Very high increase in early as well as final strength SikaGrind®184 Significant treatment cost Typical dosage: 015%2023年1月25日 Abstract An improved differential evolutionary cement mill operation index decision algorithm based on constraint control and selection strategy is proposed to address the problem that the operation index is usually decided by manual experience in the cement mill operation process, which causes unqualified cement specific surface area and excessive The Decision Algorithm of Cement Mill Operation Index Basedpage 08 41 MILL OUTPUT INCREASE page 09 42 QUALITY AND WATER DEMAND OPTIMISATION page 09 5 THE optimising both mill output and cement quality Besides high levels of energy efficiency, vertical mills have the following no additional measures to reduce noise disturbances are needed Disadvantages are: • Necessity to use water Technical Notebook CEMENT ADDITIVES FOR VERTICAL MILLS2014年3月1日 For each cement type a PID set is selected and put in o peration in a closed circuit cement mill output, u 1, constitutes the By applying a step increase of the mill Optimizing the control system of cement milling: Process
CFB石灰石脱硫剂制备——磨机公众号12.8 推送案例(8)53.jpg)
17 Signs of Problems with Ball Mills: Quickly Remove Hidden Troubles
2023年2月15日 High temperature of the ball mill will affact the efficiency 3 For every 1% increase in moisture, the output of the ball mill will be reduced by 8% 10% 4 when the moisture is greater than 5%, the ball mill will be unable to perform the grinding operation 5 The bearing of the ball mill is overheated and the motor is overloaded Reasonsthe thermal energy savings to be 009–031 GJ/t, electrical energy savings to be 8–28 kW h/t and emission reduction to be 128–2509 kgCO2/t 6 General energyefficiency measures in cement industry 54 Horizontal roller mill for finish grinding Due to their widespread use, efficient strategies for controlling motors are of the essenceAn overview of energy savings measures for cement industries2022年3月16日 Ⅰ Introduction of cement ball mill Cement ball mill is a kind of equipment for fine grinding of materials It is a device for the next step of fine grinding of coarsegrained materials It can What is a Cement Ball Mill? How to Use It? by cicemech Medium2020年5月1日 Cement industry consumes a huge amount of electrical energy that is about 100 kWh/t (kWh per ton (10 3 kg) of cement) [16]In a cement plant, about twothirds of the total electrical energy is used for particle size reduction of raw materials and clinker [17]There is a diverse range of options to decrease the production expenses as well as CO 2 emissions that Energy and exergy analyses for a cement ball mill of a new
.jpg)
Improvements in New Existing Cement Grinding Mills by Tim
o For ball mills, only 3 – 6% of absorbed energy is utilized in surface production, the heat generated can increase mill temperature to > 120⁰ C causes excessive gypsum dehydration media coating if mill ventilation is poor Types of cement mills There are basically 4 types of cement mills in use today: Ball Mill (BM)