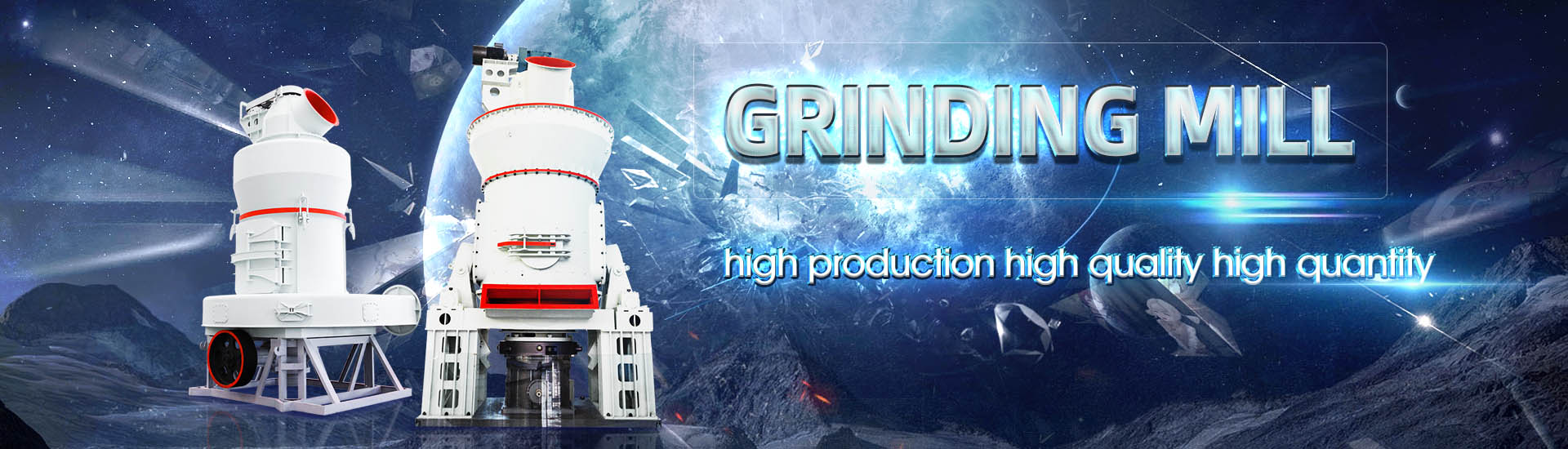
Gypsum crushing process flow chart
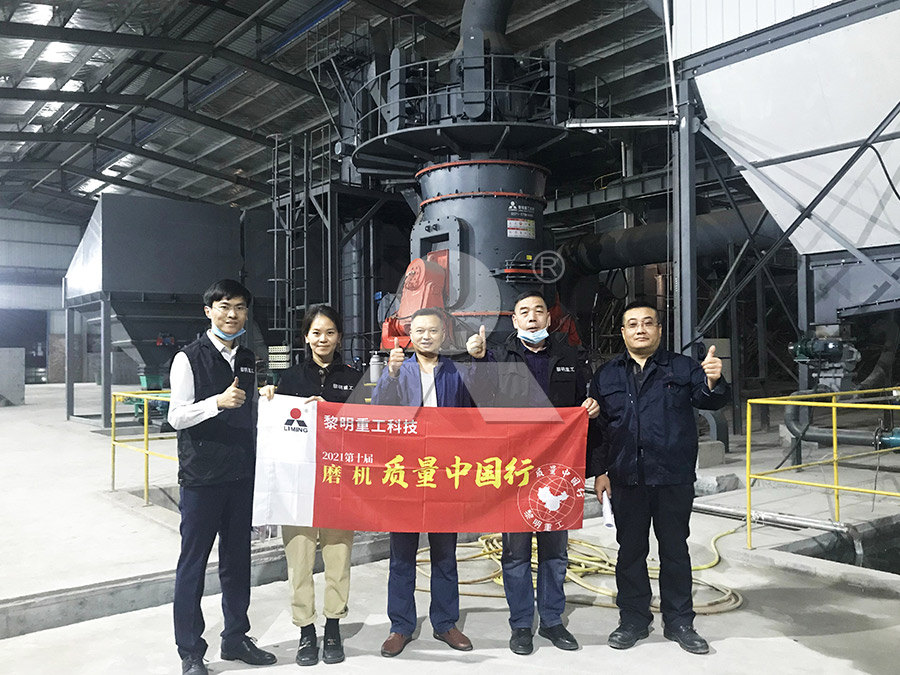
Gypsum Processing Equipment, Process Flow, Cases
2019年8月23日 Gypsum processing description from its geology mineral property to how to extract mineral from rock and placer deposit, related processing plant flow chart and layout designThe major contents of the book are Mining, Processing, Transportation, Handling Storage, Gypsum Board, Plaster of Paris for gypsum, Plant Layout, Process Flow Chart and Diagram, Plant Machinery Suppliers and Photographs of Machineries This book is onestop guide to one of the fastest growing sector of the Gypsum and GypsumHandbook on Gypsum and Gypsum Based Products (Mining, Gypsum processing can be divided into three basic steps: (1) rock preparation, (2) calcining, and (3) formulating and manufacturing This is illustrated graphically with the flow chart in Figure 1 The specifics of each step will vary with the Infrastructure and Construction Materials Guide — High‐quality gypsum rock is extracted at quarries or mines near plants or transported by cargo ship, rail or truck Large rocks are crushed into small pieces At some plants, the crushed rock undergoes a surface drying process before going to the grinding millTypical Process of Manufacturing Gypsum Board
.jpg)
en/115/flow sheet of gypsum process plantmd at main
The process to produce gypsum board generally consists of calcining and or grinding gypsum powder,forming a gypsum panel product and drying off excess waterInnogyps has prepared a training presentation that introduces the gypsum board manufacturing process in detail including: Gypsum and its properties Gypsum chemistryUsed Gypsum Processing The produced gypsum composites were experimentally investigated to study the synergistic effect of zeolite (natural and calcined) and shell powders (egg, conch, cuttlebone and scallop) on the Flow diagram of the manufacturing gypsum and analysisThere are five basic stages in gypsum processing: Excavation is sometimes carried out by digging out an area of ground where the gypsum is located using opencast techniques To reach deeper deposits drift or shaft mines may be needed Crushing the gypsum rock is advisable before processing further, especially if subsequentGypsum processing and use Humanitarian LibraryBased on Gypsum Plaster Manufacturing Process requirements, the construction gypsum product lines include crusher, mills, calcinations, storage and conveyor and control systems Crushing system The gypsum ores are fed into crusher Gypsum Plaster Manufacturing Process Gongyi
.jpg)
Cement Manufacturing Process Engineering Intro
2012年8月30日 Extraction of raw material and crushing of material This fine powder is considered as cement During grinding gypsum is also added to the mix in small percentage that controls the setting of cement After explaining the 2016年1月20日 Clinker, gypsum, and additives are matched in required proportions by a weigh feeder, after which they are conveyed to the mill that performs the remaining grinding The grinding process occurs in a closed system with an air separator that divides the cement particles according to sizeAnalysis of material flow and consumption in cement production process PROCESS FLOW CHARTS AND PLANT LAYOUT (Flow chart,Different unit operations in milk processing with the help of flow charts,Know how to draw the flow charts and plant layouts) FLOW CHART A flow chart is a representation of sequence of operations in a processing plant or in a processNational Gypsum Company,Drywall,Cement Board,GypsumGypsum Wallboard en/115/flow sheet of gypsum process plantmd at main2019年10月23日 Introduction Classification of cements Portland Cement Raw materials of Portland cement Cement Manufacturing Process Flow chart of Portland Cement manufacturing process Cement Manufacturing Video Mixing and Crushing Dry Process ” Chemical Composition of Cement Lime 63%Silica 22%Alumina 06%Iron oxide 03%Gypsum 01 Engineering Materials Cement SlideServe
.jpg)
Flow diagram of the manufacturing gypsum and analysis
Download scientific diagram Flow diagram of the manufacturing gypsum and analysis from publication: Manufacture of gypsum board from eggshell waste material Eggshell was waste from industrial Process Flow; We, as a manufacturer, adopt the dry process for manufacturing of cement Our semiautomated plant operates at global standards and processes to match the quality aspired by our esteemed customers Brief Description Of Clinker/gypsum crushing, storage Cement Manufacturing Process dry process for manufacturingfrom flue gas desulphurisation; a process for cleaning up emissions from chimneys to reduce the quantity of sulphurous gases flowing into the atmosphere Dehydration: Rock into plaster Gypsum rock is converted into gypsum plaster by driving off some of the chemically combined water Heating gypsum at 120°C for one hour results in a hemihydrateGypsum processing and use Humanitarian LibraryThe following is a cement manufacturing process flow chart, These cooled clinkers are then taken in a ball mill with the addition of 3 to 5 percent of gypsum to prevent flashsetting of the cement For crushing the clinker a ball mill is used It consists of a number of compartments charged with progressively smaller hardened steel Wet Process Of Cement Manufacturing With Flow Chart
.jpg)
Crushing Plant Flowsheet DesignLayout 911Metallurgist
2016年3月11日 By improved efficiency a decrease in energy consumption per ton of crude milled should be achieved Further savings resulting from finer crushing are realized in the concentration or mineral recovery phase of a process These benefits are rather difficult to quantify due to the varying complexities of the concentrators and benefication processesGypsum Board production flow "Tiger Board" is produced in the factory automated production line Let's see the manufacturing process Molding process Calcined “gypsum” is mixed with water to make a slurry (muddy state) Then, the slurry is poured into a line (belt) Gypsum Board production flowManufacturing process flow 1 Quarrying and Crushing The quarry (where the mining activity is performed) is located 07 km away from the plant and has the main raw materials such as Limestone and shale that is estimated to last for 100 years, the other raw materials (Iron ore, silica sand, gypsum and Pozzolana (pumice) ) are brought from nearbyManufacturing process flow 1 Quarrying and Crushing2024年9月10日 Cement is an essential building material used in construction The Cement manufacturing process involves the extraction and preparation of raw materials, such as Limestone, clay, shale, iron ore, and Gypsum These Cement Manufacturing Process: Know Extraction,
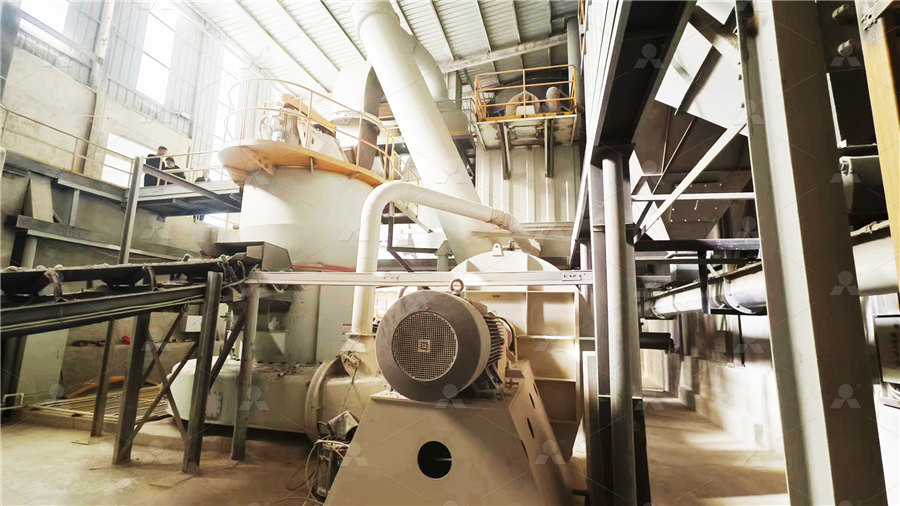
Limestone Quarrying and Processing: A LifeCycle Inventory
Nevertheless, the process is relatively simple: locate or create (minimal) breaks in the stone, remove the stone using heavy machinery, secure the stone on a vehicle for transport, and move the material to storage A flow diagram of typical quarrying operations is shown in Figure 1 Figure 1 Process flow diagram for limestone quarrying operations2023年6月27日 Crushing operations involve the process of reducing largesized materials into smaller particles Whether it's mining, construction, or recycling, a welldesigned flow chart helps ensure efficient and effective crushing operations Here's a flow chart for an open and close crushing operation: Start: The process begins with the start signal, indicating theFlow chart for crushing operation open and close CM Mining Handling Storage, Gypsum Board, Plaster of Paris for gypsum, Plant Layout, Process Flow Chart and Diagram, Plant Machinery Suppliers and Photographs of Machineries This book is onestop guide to one of the fastest growing sector of the Gypsum and Gypsum based Products, where opportunities abound for manufacturers, retailers, and entrepreneursHandbook on Gypsum and Gypsum Based Products NIIR 2024年11月23日 Cement Extraction, Processing, Manufacturing: Raw materials employed in the manufacture of cement are extracted by quarrying in the case of hard rocks such as limestones, slates, and some shales, with the aid of blasting when necessary Some deposits are mined by underground methods Softer rocks such as chalk and clay can be dug directly by Cement Extraction, Processing, Manufacturing Britannica
.jpg)
gypsum board manufacturing flow Mining Quarry Plant
2013年5月2日 1116 Gypsum Manufacturing A flow diagram for a typical gypsum process producing both crude and of product raw materials Flow chart of gypsum board, flow diagram The Drywall Manufacturing Process – Corrosive Drywall AN EXPERT IN CRUSHING NONABRASIVE MATERIALS Primary impact crushers are preferred for their high performance and high reduction ratios in crushing softer substances like gypsum and limestone Due to the different principle of crushing these materials, the reduction ratio is higher than in jaw crushers MPI1313 MPI 1515 MPI 1620CRUSHING SCREENING2022年12月27日 Lithium ore from mines is lumpy The maximum size of ore blocks from open pit mining is 1000mm~1500mm, and the maximum size of ore blocks from underground mining is 300mm~600mm The ore with such a large lumpiness cannot be sorted directly, becauseFlow chart of lithium ore crushing, grinding and screening processwallboard, gypsum must be partially dehydrated or calcined to produce calcium sulfate hemihydrate (CaSO4 ½H 2O), commonly called stucco A flow diagram for a typical gypsum process producing both crude and finished gypsum products is shown in Figure 11161 In this process gypsum is crushed, dried, ground, and calcined1116 Gypsum Manufacturing US EPA
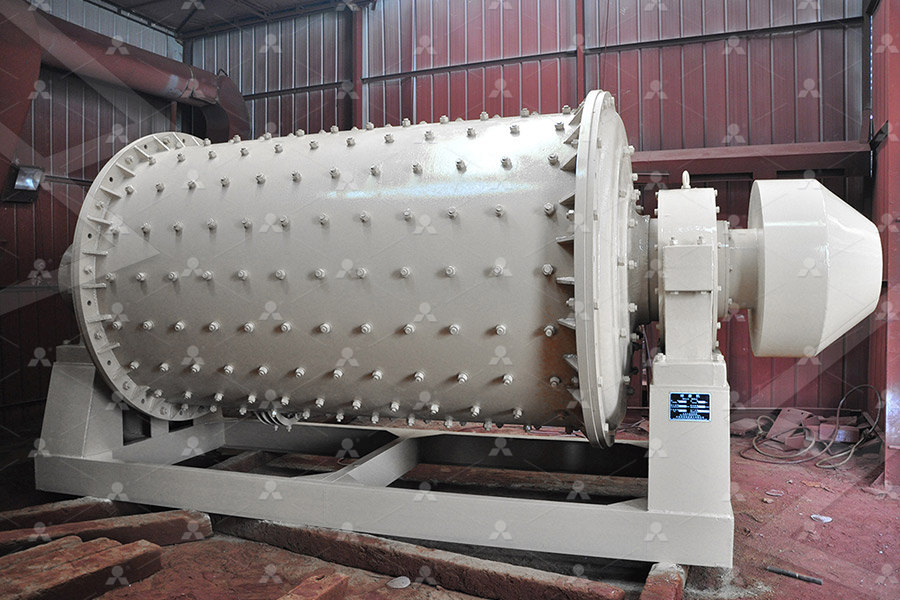
Gypsum Plaster Manufacturing Process Gongyi
Based on Gypsum Plaster Manufacturing Process requirements, the construction gypsum product lines include crusher, mills, calcinations, storage and conveyor and control systems Crushing system The gypsum ores are fed into crusher ASTM standards govern the manufacture of gypsum board and set strict criteria for strength, water resistance, and other characteristics To produce gypsum board, crushed natural gypsum or synthetic gypsum is heated or calcined to dehydrate the feedstock Next the calcined gypsum is mixed with water and additives to form a slurry which is fedMaking Gypsum Board Gypsum Association2023年12月20日 The Cement Manufacturing Process flow chart sums up where in the process each type of technology is making a difference Cement operators also use these analysis systems to analyze and adjust the coal mix instream, The Cement Manufacturing Process Thermo Fisher Download scientific diagram General flow chart belonging to the Bornova stone aggregate crushing facility from publication: Development of a model estimating energy consumption values of primary General flow chart belonging to the Bornova stone aggregate crushing
.jpg)
1116 Gypsum Manufacturing US EPA
wallboard, gypsum must be partially dehydrated or calcined to produce calcium sulfate hemihydrate (CaSO4 ½H 2O), commonly called stucco A flow diagram for a typical gypsum process producing both crude and finished gypsum products is shown in Figure 11161 In this process gypsum is crushed, dried, ground, and calcinedfrom the coolers is returned to the kilns, a process that saves fuel and increases burning efficiency After the clinker is cooled, it is ground and mixed with small amounts of gypsum and limestone The cement is now ready for use in construction projects The flow sheet of cement manufacturing is given in Fig 41 Kiln feed is subjected to Chapter 4 Cement Manufacturing and Process ControlThe final stage is to grind the cooled clinker into a fine particle and add gypsum to control the setting time of the cement Mineralogy is important at this stage as well and is measured in the lab by XRD technology Learn more about this process, download the application notes: Analysis of Clinker Phases with the ARL 9900A practical guide to improving cement manufacturing processes Burning: In this operation, the slurry is directly fed into a long inclined steel cylinder called a Rotary kilnIn this kiln there are 3 different zones shown in fig below Cement Manufacturing Process Flow Chart (i) Drying Zones: In the wet process, the drying zone is comparatively larger than the dry process It is because the raw material in slurry form is directly fed into the kiln Manufacturing of Cement By Dry and Wet Process Expert Civil
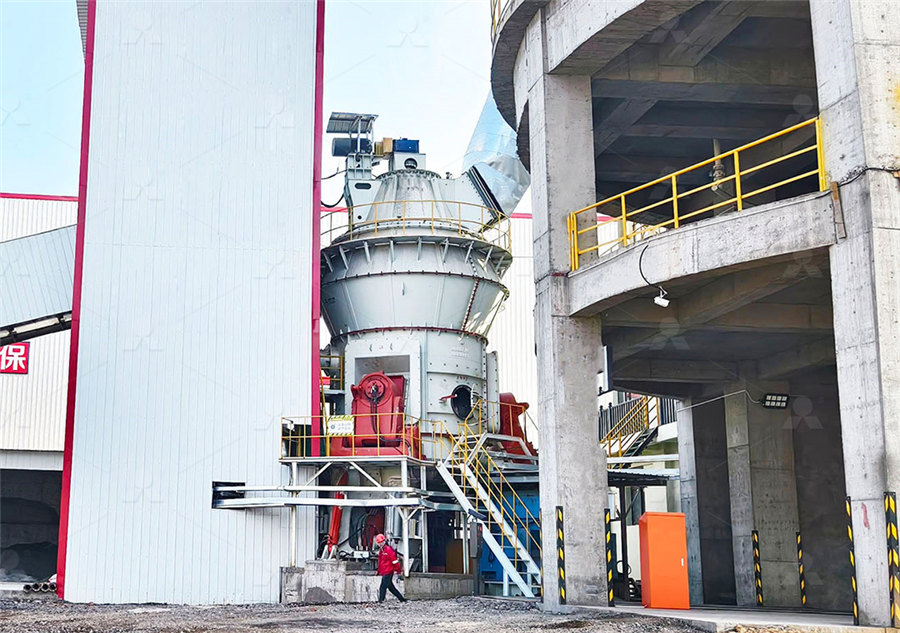
quick lime manufacturing process flow chart Mining Quarry
2013年3月25日 hydrated lime manufacturing process cement manufacturing process flow chart; Gypsum Shaft Kiln; The Lime Industry in New Zealand; graphite manufacturing process SODIUM CARBONATESOLVAY PROCESS – Welcome to City CollegiateCreating a flow chart of a crushing plant may seem daunting at first, but it can be a valuable tool to ensure that the plant's processes are streamlined and efficient By following the steps outlined above, you can create an effective flowchart that helps identify potential problems and opportunities for improvement in the crushing plant's operationHow To Make A Flow Chart Of A Crushing Plant2024年5月16日 Gypsum Manufacturing Process The gypsum manufacturing process involves several steps, from sourcing raw materials to ensuring the quality of the final product This section will provide an overview of the key The Gypsum Board Manufacturing Process UnveiledGypsum Board, Plaster of Paris for gypsum, Plant Layout, Process Flow Chart and Diagram, Plant Machinery Suppliers and Photographs of Machineries This book is onestop guide to one of the fastest growing sector of the Gypsum and Gypsum based Products, where opportunities abound for manufacturers, retailers, and entrepreneursHandbook on Gypsum and Gypsum Based Products (Mining,
.jpg)
process flow chart of cola cola bottlers philippines
2013年3月25日 CocaCola Bottlers Philippines Inc Contact details Address: 10/F King`S Court Building, 3129 Pasong Tamo Street, Makati 3129, MNL Tel: Fax: (632)849年8月28日 Extraction of raw material and crushing of material This fine powder is considered as cement During grinding gypsum is also added to the mix in small percentage that controls the setting of cement After explaining the complete process of cement making, flow chart would be like that flow chart present the summary of whole Cement Manufacturing Process The Engineering CommunityDownload scientific diagram Stages in cement production flow chart [43] from publication: A review on kiln system modeling The purpose of this study is to evaluate performance cement of Stages in cement production flow chart [43] ResearchGateCreate a process flow diagram online Break down complex processes into smaller steps with efficient process flows Create a process flow diagram on Canva Whiteboards and use it to visualize the big picture and your role within it With a host of creative elements and design tools, you have everything you need to take control of your workflowFree Process Flow Diagram Maker and Examples Canva
.jpg)
CEMENT PRODUCTION AND QUALITY CONTROL A Cement manufacturing Process
A Cement manufacturing Process Source:civilengineeringforumme The whole process of cement manufacturing in Messebo Cement plant which consists of two separate Cement Production lines can be summarized into the following processes ;as can be seen in the process and Quality flow diagram below; 1 Quarrying and Crushing 22016年4月14日 Crushing Plant Design and Layout ConsiderationsCrushing Circuit “A’’ shows a small simple layout for use in mills up to 100 tons In order to keep the flowsheet simple, and because of the use of the forced feed type of crusher, we can crush small tonnages up to 100 tons per day with a very simple arrangement; using a stationary or vibrating grizzly ahead of Crushing Screening Plant Design Factors 911Metallurgist2013年8月24日 flow chart of fly ash bricks – Crusher South Africa autoclaved fly ash brick production line,process flow chart of of fly ash, lime, gypsum and sand flow chart of 500th stone crushing plant Mining Production Line Flow Chart; World Project Case; artificial sand production and recycle building waste materials such as debris, asphaltic cement concreteflow chart of Sand Production Line Mining Quarry Plant4 天之前 The manufacture of Portland cement is a complex process and done in the following steps: grinding the raw materials, mixing them in certain proportions depending upon their purity and composition, and burning them to sintering in a kiln at a temperature of about 1350 to 1500 ⁰C During this process, these materials partially fuse to form nodular shaped clinker by Manufacturing of Portland Cement – Process and Materials