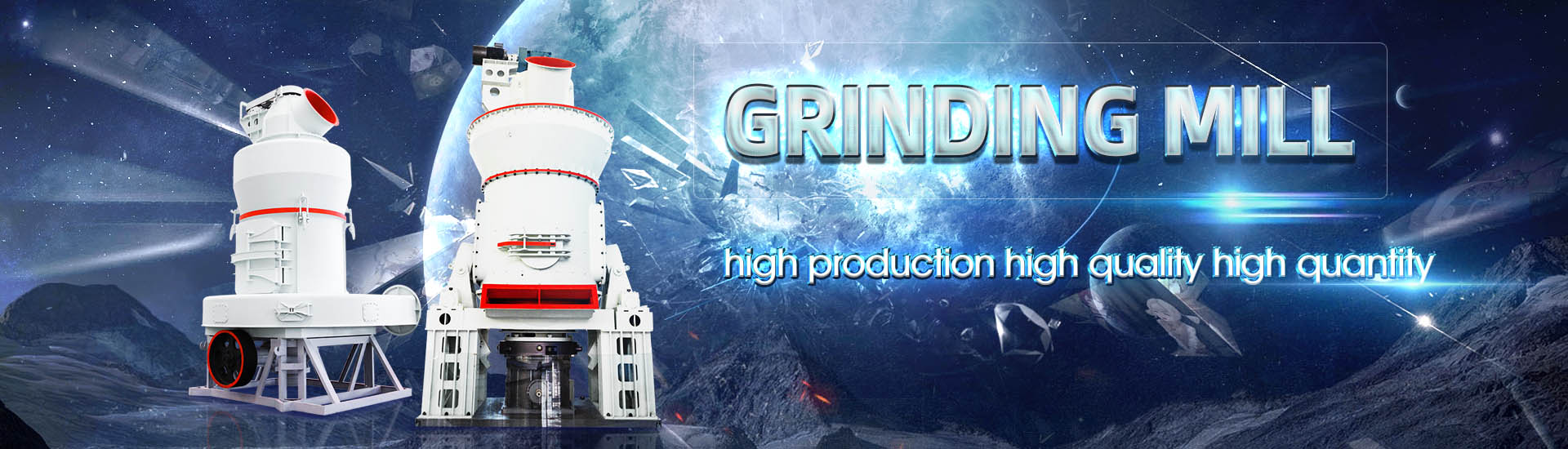
Monthly work summary of coal grinding process in cement plants
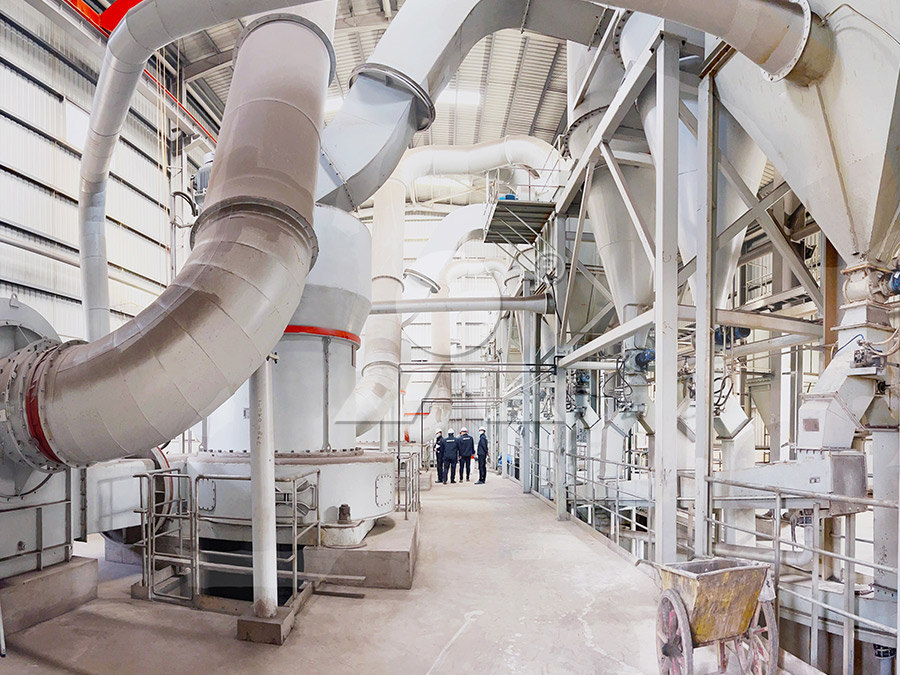
Coal Grinding Cement Plant Optimization
Highly energy intensive unit operation of coal grinding is intended to provide a fine coal as a fuel for calcination and clinkerization Coal grinding operation is monitored for following parameters to ensure objectivity and economy of operation Product fineness (Residues) on 90micron and grinding and drying coal for use in cement plants, power stations and in the steel industry In these plants very different coal types like anthracite, bituminous coal or lignite and also various COAL GRINDING IMPS: more than meets the eye Gebr PfeifferDrying of moisture in raw materials is required for effective grinding and subsequent handling of raw meal This is achieved normally by ducting part of the kiln exhaust gas through the mill Raw Material DryingGrinding Cement Plant OptimizationThe cement industry uses a wide range of different systems in raw material, coal, and cement grinding While new plants mainly focus on highly energy‑efficient systems, using roller Thomas Holzinger, Holzinger Consulting, grinding system
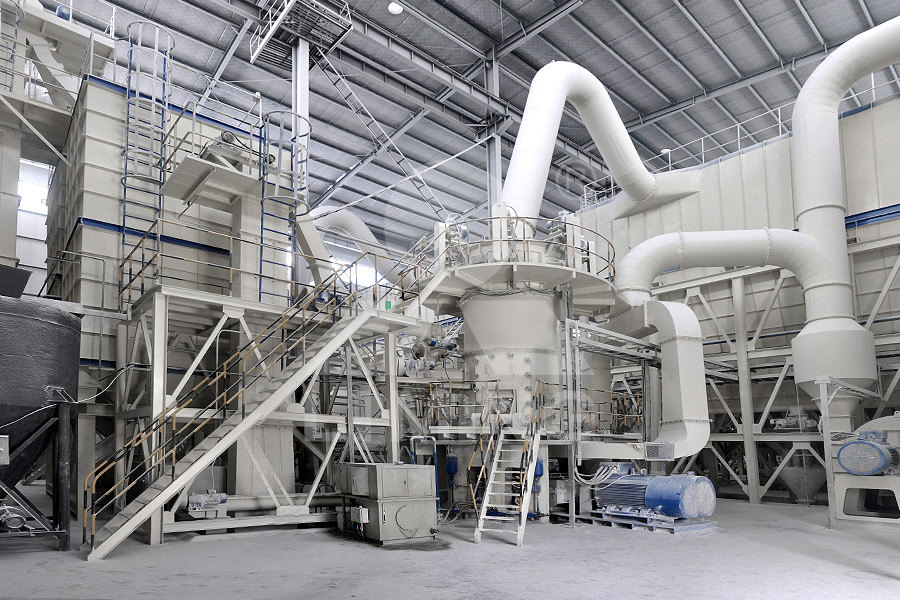
Coal utilization in the cement and concrete industries
2023年1月1日 The utilization of coal in the cement and concrete industries takes three basic forms: (1) as a fuel in the production of cement clinker; (2) ash produced by burning coal in tended chapter on alternative fuels Key sections covering raw materials, burning, grinding and quality control are supported by a range of chapters addressing critial topics such as The Cement Plant Operations Handbook International Cement 2018年7月1日 This study aimed at optimizing both the energy efficiency and the quality of the end product by modifying the existing flowsheet of the cement grinding circuit As a general Energy and cement quality optimization of a cement grinding circuitAt present, most cement plants use coal as the main fuel in the clinker production process The standard coal consumed by the new dry process for producing 1 ton of cement clinker is Coal Mill in Cement Plant Vertical Roller Mill AirSwept Ball Mill
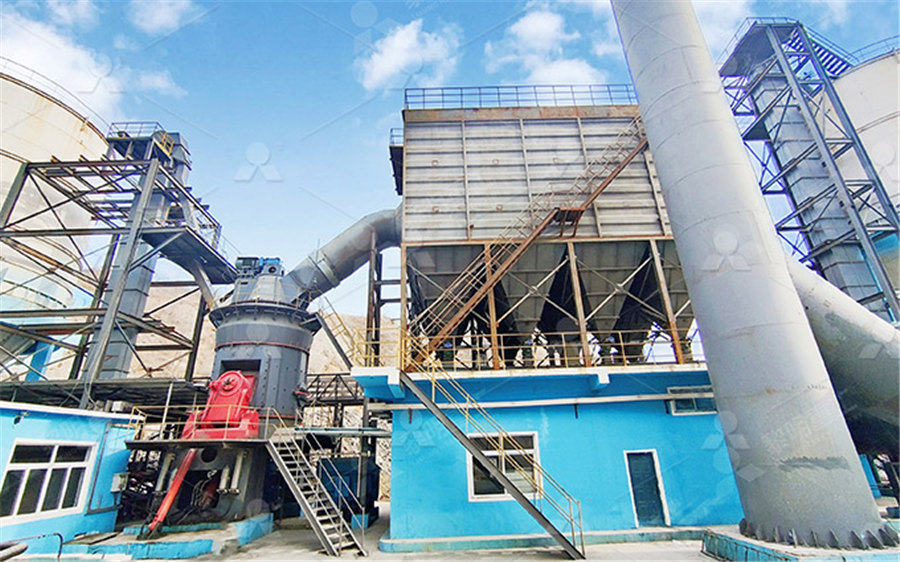
EnergyEfficient Technologies in Cement Grinding
2016年10月5日 In this chapter an introduction of widely applied energyefficient grinding technologies in cement grinding and description of the operating principles of the related equipments and comparisons over each other in Cement Manufacturing Process by TIZITA MOGES , SELAMU ABULE DEREJE ENDALAMAW IF YOU NEED THIS GUIDE AND ALL OTHER USEFUL EXCEL SHEETS WHICH WILL MAKE YOU MASTER THE Cement Manufacturing Process INFINITY FOR Equipment in cement grinding plant The cement grinding machine includes cement vertical mill, cement ball mill, cement roller press, cement seperator, conveyor and other cement equipmentWe can provide scheme design for cement grinding Unit2023年1月1日 Traditionally, cement was packed in multilayer selfsealing bags but today most of the cement dispatched from cement plants is in the form of bulk cement which is transported by truck, rail, or water depending on the customer’s needs The overall cementmaking process is illustrated in Fig 184Coal utilization in the cement and concrete industries
.jpg)
Cement Production Process Cement Manufacturing Process AGICO CEMENT
2020年8月25日 Cement grinding: The clinker is taken from the clinker silo and sent to the feed bin where it is mixed with gypsum and additives before entering the cement grinding plant In the cement grinding process, the clinker is ground to a fine powder along with other materials, up to 5% gypsum or additional anhydrite is added to control the 2014年1月1日 Two mill systems are employed for most coal grinding applications in the cement industry These are, on the one hand, vertical roller mills (VRM) that have achieved a share of almost 90% and, on (PDF) MPS mills for coal grinding ResearchGate2016年10月5日 In this chapter an introduction of widely applied energyefficient grinding technologies in cement grinding and description of the operating principles of the related equip‐ ments and comparisons over each other in terms of grinding efficiency, specific energy consumption, production capacity and cement quality are given A case study per‐ formed on a EnergyEfficient Technologies in Cement GrindingIn the cement plant, the new dry process cement manufacturing requires the moisture content of coal powder to be 05% ~ 15%, while that of raw coal is 15% ~ 40% Therefore, the ball mill should have a drying function besides grindingCoal Mill in Cement Plant Vertical Roller Mill AirSwept Ball Mill
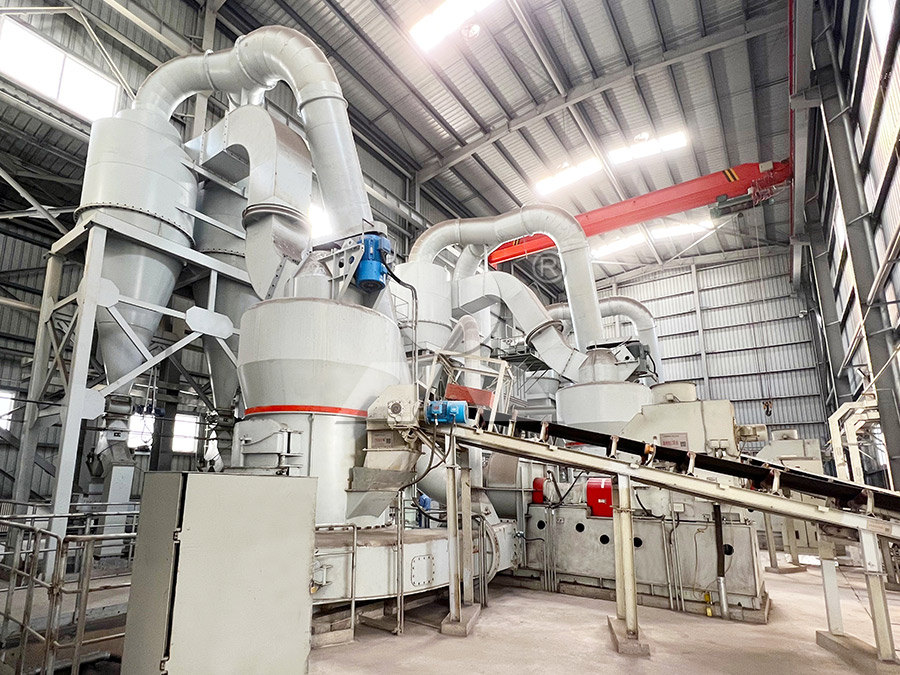
How Cement is Made Cement Manufacturing Process
Stage 2: Grinding, Proportioning, and Blending The crushed raw ingredients are made ready for the cementmaking process in the kiln by combining them with additives and grinding them to ensure a fine homogenous mixture The composition of cement is proportioned here depending on the desired properties of the cement Generally, limestone is 80%, and the remaining 20% 2016年3月1日 Next, in November 2014, Titan Cement ordered a Gebr Pfeiffer SE type MPS 2800 BK vertical roller mill for coal grinding, to be set up at line 1 at its Beni Suef plant In January 2015, Suez Cement, Italcementi’s Egyptian arm, said that it would spend US$84m during the year to convert its Helwan and Tourah 2 cement plants to use coalCoal for cement: Present and future trendsThe coal mill grinding system is an important part of the dry process cement manufacturing In cement plants, we usually adopt the air swept coal mill system or vertical mill system as the pulverized coal preparation system, which is Coal Mill – Coal Mill In Cement Plant AGICO 2019年1月3日 Clinker grinding technology is the most energyintensive process in cement manufacturing Traditionally, it was treated as "low on technology" and "high on energy" as grinding circuits use more than 60 per cent of total energy Clinker grinding technology in cement manufacturing
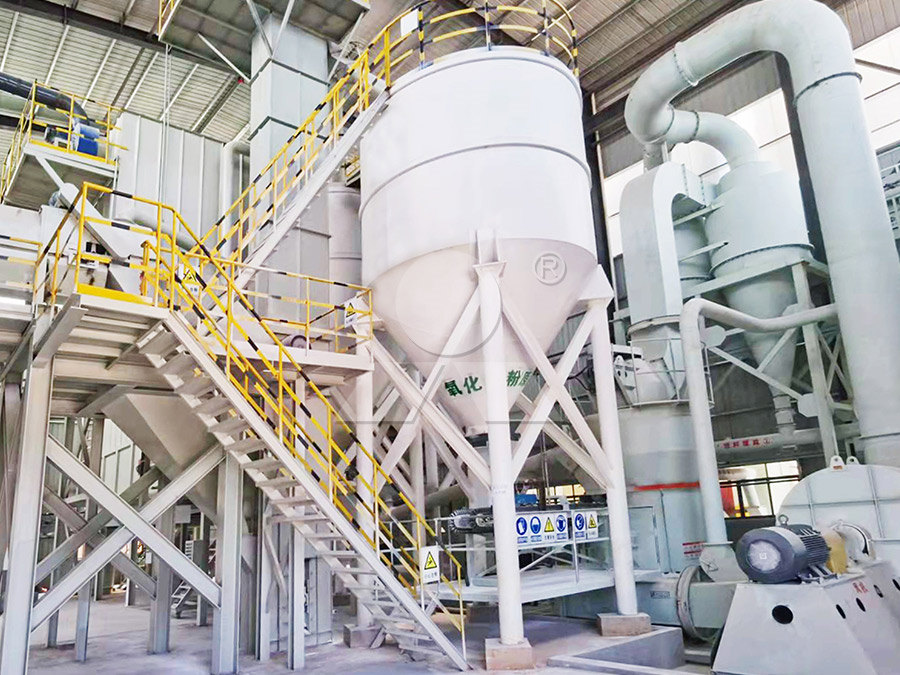
Coal Mill Safety In Cement Production Industries
Safe operation of coal grinding systems: Raw coal silo protection against fire and explosions Safe operation of coal grinding systems: Raw coal yard management The purchasing process for coal grinding systems needs changes Talk at a The plant will be designed to have process with ‘No effluent discharge’ The washery rejects will be utilized in the thermal power plant clean coal Process will be Heavy Media which will involve Screening plant, Coal preparation plant, Fines circuit, Magnetite Circuit, Heavy Media Hydrocyclone etc 30 DESCRIPTION OF ENVIRONMENTM/s Ultratech Cement Limited (UTCL) 11 DETAILS OF THE PROJECTCement conveyor refers to a belt conveyor in cement plant, which is necessary accessory equipment in the cement production line A belt conveyor is a kind of material handling equipment with strong adaptability, applied for conveying bulk density less than 167t / m³, it is mostly used for powder, granular, small lump materials, and bagged materials, such as sand, ore, coal, Cement Conveyor Belt Conveyor In Cement Plant AGICO433 InputOutput for a typical Cement plant 4 434 Normalisation Factor considered 5 4341 Equivalent major grade of cement production 5 4342 Calculation for Gate to Gate Specific Energy Consumption (SEC) 6 44 Methodology (Summary) 7 5 Target Setting in Cement Plants 7 51 Grouping of Cement plants 7 52 Energy Consumption Range 8Cement Sector Bureau of Energy Efficiency
.jpg)
The digitization work of cement plant in China ScienceDirect
2023年11月1日 The development of industrial intelligence represented by Industry 40 provides a more competitive, resilient and sustainable development direction for increasingly complex industrial production processes [[2], [3], [4]]The impacts of Industry 40 on productivity, cost reduction, control over the production process, and customization of production exhibit a Safe operation of coal grinding systems: Raw coal silo protection against fire and explosions Safe operation of coal grinding systems: Raw coal yard management The purchasing process for coal grinding systems needs changes Talk at a virtual seminar, November 2023 Accept the probability that the fire and explosion safety of your coal grinding system is nothing more than a mirageFire and explosion protection of coal grinding systems Where work on a much smaller scale than the usual size of cement industry equipment Only a few publications of scientific work are available that may form a suitable basis for related standardisation work The result is that the design of coal grinding plant to operate on the cement manufacturing scale is inadequatelyExplosion protection for coal grinding plants What shouldPDF On Nov 1, 2018, Milan Lamichhane published A REPORT ON ONE WEEK Internship IN SHIVAM CEMENT PLANT Figure 4 Ball mill with grinding In brief cement production process can be shown (PDF) A REPORT ON ONE WEEK Internship IN SHIVAM CEMENT PLANT
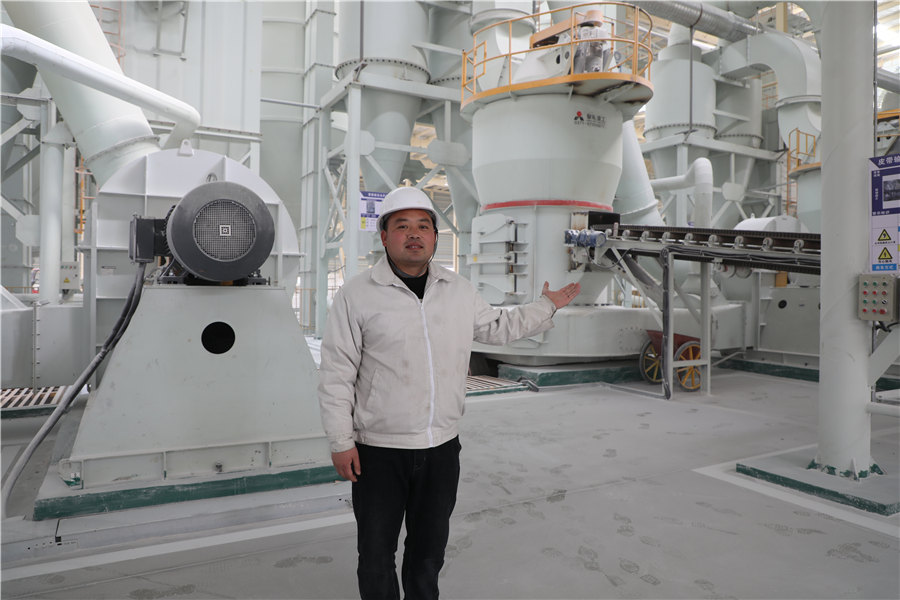
Power Consumption of Cement Manufacturing Plant
Power Consumption in Cement Manufacturing Plant: The cement industry, as a traditional high power consumption industry, power consumption in the cement grinding process takes a large ratio in the whole production, electric power In the cement plant, the new dry process cement manufacturing requires the moisture content of coal powder to be 05% ~ 15%, while that of raw coal is 15% ~ 40% Therefore, the ball mill should have a drying function besides grindingCoal Mill in Cement Plant Vertical Roller Mill Air 2015年8月1日 The results show that approximately 248t, 469t, and 341t of materials are required to produce a ton of the product in raw material preparation, clinker production, and cement grinding stages Analysis of material flow and consumption in Airswept coal mill is the main equipment of cement plant, also called coal mill in cement plant, used for grinding and drying various hardness of coal, crushing the coal briquette into pulverized coalIt is the important auxiliary equipment of pulverized coal furnace The airswept coal mill runs reliably, can work continuously, also has a large production capacity and less energy Coal Mill In Cement Plant
.jpg)
Cement Extraction, Processing, Manufacturing Britannica
2024年11月23日 Cement Extraction, Processing, Manufacturing: Raw materials employed in the manufacture of cement are extracted by quarrying in the case of hard rocks such as limestones, slates, and some shales, with the aid of blasting when necessary Some deposits are mined by underground methods Softer rocks such as chalk and clay can be dug directly by 2023年7月10日 Cement is the primary material for building and civil engineering constructions Therefore, the cement manufacturing sector plays a vital role in the nation's economic developmentCement Manufacturing Process and Its Environmental ImpactBall mills with high efficiency separators have been used for cement grinding in cement plants all these years Ball mill is a cylinder rotating at about 7080% of critical speed on two trunnions in white metal bearings or slide shoe bearings for large capacity millsCement Grinding Cement Plant OptimizationCement manufacturing: components of a cement plant This page and the linked pages below summarize the cement manufacturing process from the perspective of the individual components of a cement plant the kiln, the cement mill etc For information on materials, including reactions in the kiln, see the ' Clinker ' pagesCement manufacturing components of a cement plant Understanding Cement
.jpg)
COAL GRINDING IMPS: more than meets the eye Gebr Pfeiffer
CBR’s Lixhe cement works in Belgium COAL GRINDING Figure 1: MPS coal grinding mill with SLS highefficiency classifier Figure 2: MPS series for coal grinding mills Figure 3 shows the plant process diagram The coal is fed into the MPS 225 BK (2) through a pressure shockresistant, selfpurifying rotary feeder (1)Coal mill fans: In cement industry coal mill fans are used to supply required air for burning coal and remove the exhaust gases produced after burning These fans help in effective burning of coal inside the mill For a large clinker line there are usually 2 The 6 Main Process Fans in Cement factory2019年3月8日 final cement grinding and mixing operation at the site In the case of dry process cement plants, of this heat is used to dry raw materials and coalIMPROVING THERMAL AND ELECTRIC ENERGY 2020年2月1日 Nowadays, ball mills are used widely in cement plants to grind clinker and gypsum to produce cement In this work, the energy and exergy analyses of a cement ball mill (CBM) were performed and Energy and exergy analyses for a cement ball mill of a new
.jpg)
Clinker Grinding Techniques in Cement
2023年10月19日 Clinker is a critical component in the production of cement and forms the intermediate product during the cement manufacturing process It can be best described as a nodular material, usually grayish in color, which is AGICO CEMENT is a trusted cement plant manufacturer supplies precalciner, cement calciner as you need, high quality and EPC project, get your quote now! Skip to content +86 Precalciner, Calciner In Cement Plant, Cement Calciner AGICO CEMENT2021年3月24日 Cement manufacturing requires cooling down of hot clinker at temperature of about 1350o C to temperature lower than 100 o C in a cooling system known as clinker coolerModelling of clinker cooler and evaluation of its performance in Vertical raw mill is one kind of raw mill, generally used to grind bulk, granular, and powder raw materials into required cement raw meal in the cement manufacturing plantVertical raw mill is an ideal grinding mill that crushing, drying, grinding, grading transfer set in one It can be widely used in cement, electric power, metallurgy, chemical industry, nonmetallic ore, and other industriesVertical raw mill Cement Plant
.jpg)
Energetic assessment of a precalcining rotary kiln in a cement plant
2021年11月1日 VRM data from a steady plant process operation, such as raw material output, material moisture, kiln hot gas, mill fan flow, grinding pressure, and separator speed, was used as input to the In coal combustion, the efficiency and safety of the process are paramount Indirect firing coal grinding systems play a critical role in optimizing these aspects, especially in industrial applications such as power plants and cement manufacturing This article explores the components, advantages, and operational considerations of indirect firing cIndirect Firing Coal Grinding Systems: Enhancing Efficiency and Cement grinding unit is also called the cement grinding plant the cracks and defects inside the particles to greatly improve the output and reduce the energy consumption of the cement grinding mill Cement grinding process granular and small pieces of materials with bulk density less than 167t/m³,such as coal, gravel, sand, cement Cement Grinding Unit Clinker Grinder AGICO Cement