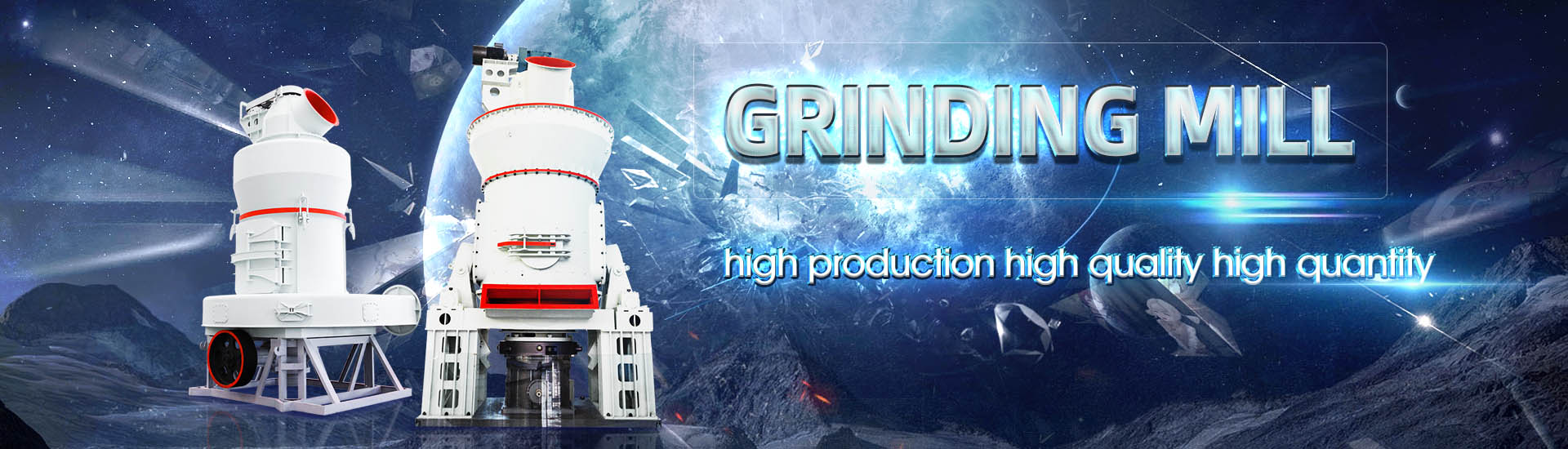
Ball mill finished product 300 mesh
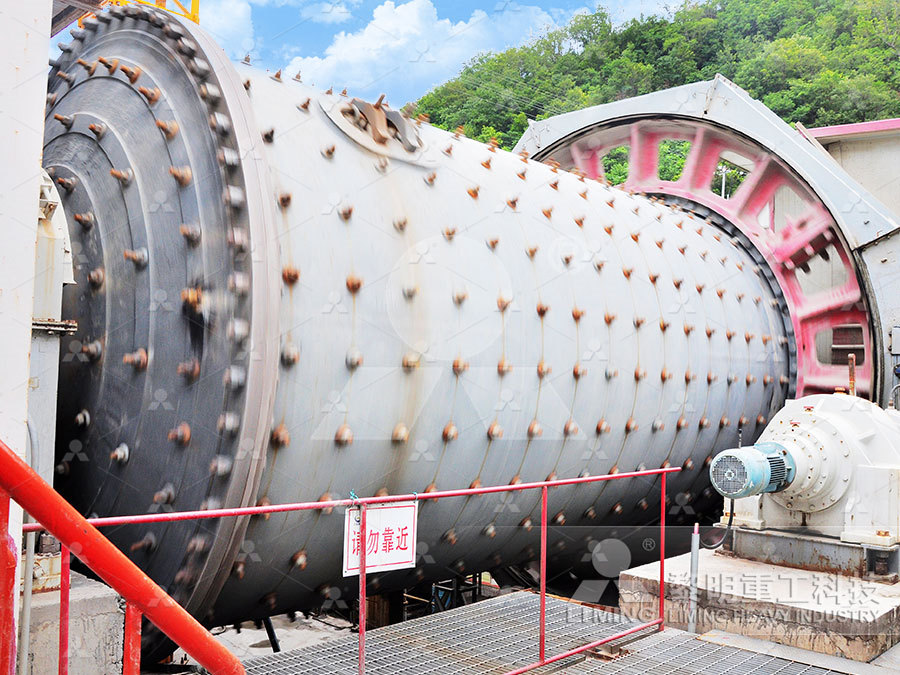
LABORATORY BALL MILL – (BALL OR ROD)
A batchgrind technic is described which was designed for use in studying the rate of production of finished product in a ball mill roughly, twice as great when grinding finished minus65 mesh product as when grinding floor space 27 x DOVE Ball Mills are supplied in a wide variety of capacities and specifications DOVE small Ball Mills designed for laboratories ball milling process are supplied in 4 models, capacity range of (200g/h1000 g/h) For small to large scale Ball Mill Ball Mills Wet Dry Grinding DOVERaymond mill is a highefficiency pulverizing mill that replaces ball mill to process ore powderIt has outstanding the cover, and also includes the reducer, the analyzer, the fan, the finished product cyclone separator, and the dust Limestone Raymond mill 80600 mesh SBM Ultrafine Recently, a customer asked us “Can the ball mill grind the material to 325 mesh?” The finished product is even, the screening rate is up to 99%, and the particle size can be adjusted arbitrarily between 80325 mesh If you want to know more information, Can the Ball Mill Grind the Material to 325 Mesh? JXSC Machine
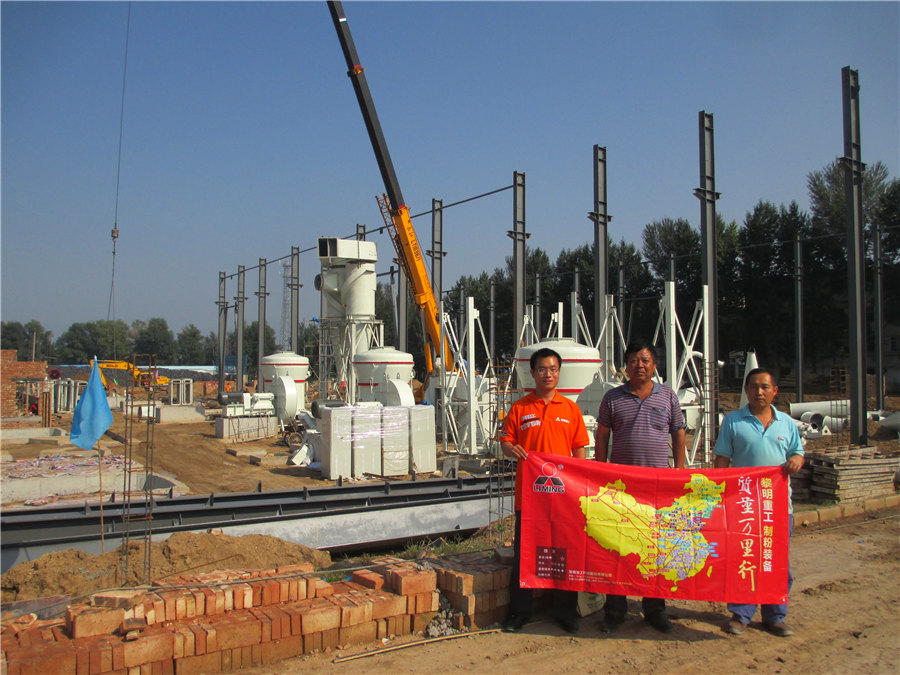
AS 300 Control Sieve Shaker Glen Mills, Inc
The analytical sieve shaker AS 300 control is used in research development, quality control of raw materials, interim and finished products as well as in production monitoring The controllable electromagnetic drive offers an optimal adaption for every product Sharp fractions are obtained even after short sieving times2017年7月3日 Because of this, the rod mill can effectively reduce 1″ feed size to 10 mesh or finer in open circuit The voids (or interstitial space) within a rod load are approximately half those in a ball mill grinding load Rods in place weigh approximately 400 pounds per cu ft and balls in place approximately 300 pounds per cu ftBall Mills vs Rod Mills 911MetallurgistThe quality is controlled right from raw materials to finished product at each stage of manufacture » read more Ball Mill Ball mill is the key equipment for grinding materials like ores, chemicals, ceramic raw materials, minerals, paints etc in to fine powder or fine paste 923007678403 Mill, Industrial Ball Mill, Crushing Equipment, Paint Industry 2013年8月3日 In Grinding, selecting (calculate) the correct or optimum ball size that allows for the best and optimum/ideal or target grind size to be achieved by your ball mill is an important thing for a Mineral Processing Engineer AKA Metallurgist to do Often, the ball used in ball mills is oversize “just in case” Well, this safety factor can cost you much in recovery and/or mill liner Calculate and Select Ball Mill Ball Size for Optimum Grinding
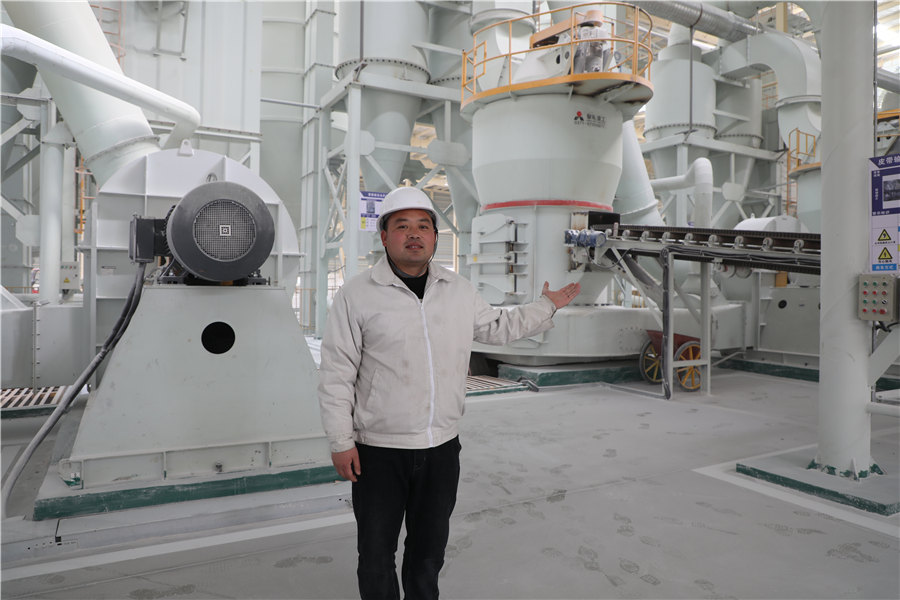
Ball Mill Rod Mill Design 911Metallurgist
2016年4月22日 In these cases, the feed to the ball mill may be from 10 to 100 mesh or even finer Where the finished product does not have to be uniform, a ball mill may be operated in open circuit, but where the finished product must be uniform it is essential that the grinding mill be used in closed circuit with a screen, Project Name: Superfine Talc Powder Production Line Processing material: Talc Annual output: 100,000 tons Finished product fineness: 800 mesh, 1250 mesh, 3000 meshVarious industrial grinding mills for sale, stone powder processing 800 Mesh Superfine Talcum Powder Production Line In The 21 Liter (5 gallon) 911METALLURGY 911MPE21BM dual function Laboratory Rod Mill / Ball Mill is designed to meet the industrial requirements to grind coal, cement and a wide variety of oresThe dual duty Laboratory Grinding Mill LARGE BATCH LABORATORY ROD MILL / BALL MILL2016年3月14日 The ball consumption for mills delivering a coarse product, all passing 8mesh and containing 10 to 20 per cent, below 200mesh, the mill being run in open circuit, is about ½ lb per ton for steel balls and 1 lb for cast composition ballsPeripheral Discharge Ball Mills Theory and Practice
.jpg)
Why use Different Size Balls in a Mill 911Metallurgist
2017年7月3日 It is not denied that the coarse particles have to be crushed else no fine material would accrue, but here the fact is emphasized that when crushing to 200mesh stress should be on the selection of balls of the right size and amount to crush, say, from 100 to 200mesh; or, when crushing to 65mesh, the operator should judiciously load the mill for crushing from 48 2015年3月30日 MATERIAL: Through 20 Mesh to finishing mill OVERSIZE: On 20 Mesh returned to preliminary mill for further grinding PRODUCT: Direct to finished Mill Stream OVERSIZE: Returned to mill for further grinding The Conical Ball Mill is lined with “Titanite” metal plates which are held in place by heavy chrome steel bars and heavy taper head boltsConical Ball Mills Benefits Advantages: Hardinge2015年6月25日 The cost of a ball mill conversion from overflow to grate discharge is ‘fairly’ affordable at $65,000 for a 13′ x 15′ mill This is only for the discharge head, grates and pulp filters (rubber) A comparison in laboratory of Overflow Discharge Ball Mill VS Grate Discharge Ball MillOverflow VS Grate Discharge Ball or Mill – Why RetrofitRetsch visualises the features and strengths of each ball bill model in a diagram to help finding the right model for a specific application In the example shown it is easy to see that the Planetary Ball Mill PM 300 offers advantages in terms of power, final fineness and maximum jar volume compared to the Mixer Mill MM 500 controlBall Mills Suitable for every application Retsch
.jpg)
Grinding Mill Design Ball Mill Manufacturer 911Metallurgist
2017年2月20日 Grinding Mill Specifications Data According to formula 423/√d, where d is equal to internal shell diameter within new liners In this case the thickness used was 60 mm for small mill sizes up to and including 2940 and 80 mm for larger mills2015年6月19日 The basic parameters used in ball mill design (power calculations), rod mill or any tumbling mill sizing are; material to be ground, characteristics, Bond Work Index, bulk density, specific density, desired mill tonnage capacity DTPH, operating % solids or pulp density, feed size as F80 and maximum ‘chunk size’, product size as P80 and maximum and finally the type of Ball Mill Design/Power Calculation 911Metallurgist2016年3月21日 Pulp Densities Pulp densities indicate by means of a tabulation the percentages of solids (or liquidtosolid ratio) in a sample of pulp This figure is valuable in two ways—directly, because for each unit process and operation in Common Basic Formulas for Mineral Processing Ball Mill Ball Mills are mainly used in metallurgy, chemical industry, electric power, cement and other industrial and mining business to make all kinds of ores and other grindable materials by virtue of such characteristics as strong adaptability to raw materials, excellence in continuous production, high crushing ratio and easy to adjust the fineness of the finished productBall Mill
.jpg)
Ball Mill Grinding Theory – Crushing Motion/Action Inside
2017年4月28日 Testing Plant Equipment: In order to determine, among other things, the operating conditions of the ballmill In order to determine, among other things, the operating conditions of the ballmill when working on this rock, a test mill of about 300 but since only the material below 200 mesh is considered finished product The E max is an entirely new type of ball mill for high energy milling 300 – 2000 min1: Cooling: controlled integrated water cooling / option: interim and finished products as well as in production monitoring The AS 400 control is used for the sieving of dry goods with test sieves of a diameter up to 400 mm In this, Emax High Energy Ball Mill Glen Mills, IncThe term ‘Mesh’ is used to describe the size of an abrasive particle In some instances, such as with Aluminum Oxide Grit or Silicon Carbide Grit, a single number is usedThis does not mean every particle in that product is exactly that size but rather than mesh size indicator is approximately the mean or average size of the range of particles in that gradeMesh Size, Mesh to Micron Comparison chart Kramer Industries Inc2015年10月9日 Calculating a grinding circuit’s circulating loads based on Screen Analysis of its slurries Compared to %Solids or Density based Circulating load equations, a more precise method of determining grinding circuit tonnages uses the screen size distributions of the pulps instead of the dilution ratiosPulp samples collected around the ball mill or rod mill and Ball Mill Circulating Load Formula 911Metallurgist
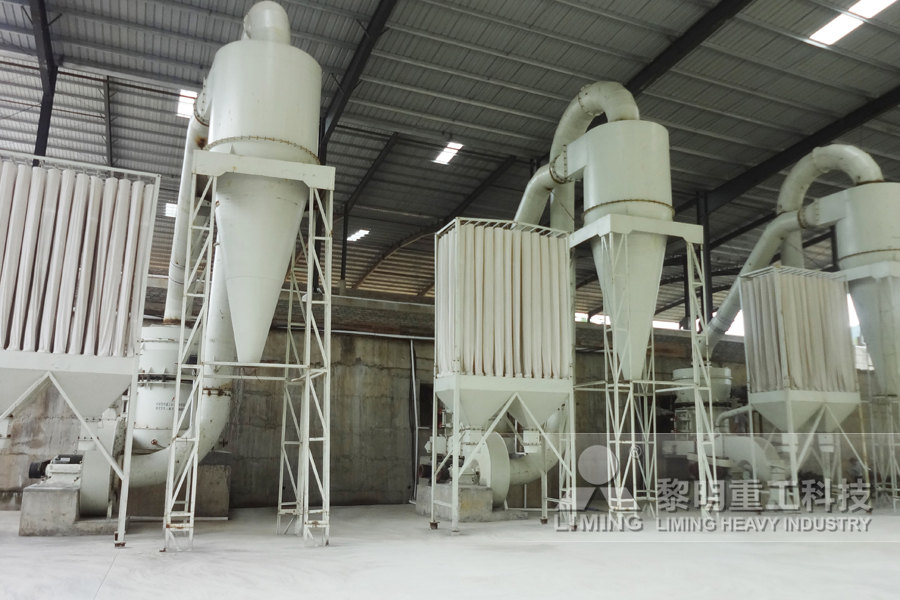
Analysis of the efficiency of the grinding process in closed circuit
2016年1月1日 Ball mills for fine grinding cement clinker and additives are widely used around the world To improve the efficiency of a ball grinding the ball mills are transferred in closed circuit with air The new Cutting Mill SM 300 excels especially in the tough jobs where other cutting mills fail The high torque of the new 3 kW drive with RES technology (additional flywheel mass) allows for an exceptionally effective preliminary size reduction of heterogeneous mixtures, such as waste or electronic components100 / 150 / 305 / 400 / 450 mm Mesh Sieves Glen Mills, Inc2015年4月24日 10 • Weight of the balls: With a heavy discharge of balls,we get a fine productWe can increase the weight of the charge by increasing the number of balls or by using a ball material of high density • Speed rotation of Ball mill: low speeds,the balls simply roll over one another and little grinding is obtained while at very high speeds the balls are carried along Ball mill PPT Free Download SlideShare2017年1月6日 The speed of mills depends upon their diameter; a ballmill of 3 feet revolves 35 times a minute, and one of 5 or 6 feet, 29 or 27 times Tubemills run at a revolution or two faster (see Fig 117) Some ores require much finer grinding than others to liberate the minerals, and this increases the milling cost Ball Mill Product ClassifyingBasic Ball Mill Grinding Circuit 911Metallurgist
.jpg)
Vertical Roller Mill SBM Ultrafine Powder Technology
Vertical Roller Mill Discharge fineness: 1503000 mesh Feed size: 20 mm Output: and finished product packaging It is a largecapacity ultrafine grinding and separation equipment developed by SBM, save 20~30% power 2020年7月2日 A comprehensive investigation was conducted to delineate the effect of ball size distribution, mill speed, and their interactions on power draw, charge motion, and balls segregation in a (PDF) Effects of Ball Size Distribution and Mill Speed and Their Ball mill product 403% passing 905 µm; and SAG mill screen undersize 410% passing 905 µm Laboratory test result, survey ore sample A Bond ball mill grindability test was performed at the Dawson laboratory on a sample of SAG mill feed collected at the time of the survey Table 1 – Ball mill grindability test Test closing mesh, µmMethod of assessing ball mill health Get Ball Mill Continues Flow in Tigri, Ball Mill: For Fine Mesh Powder 100 Mesh To 300 Mesh; Continues Grinding Process; Low Maintenance; Constant Production; Oil Field, Steel, Cement, Sugar, Paper, Cloth etc, we are the specialist to serve in various type of Health Sector product Services, Live stock (Veterinary) Products Ball Mill Continues Flow IndiaMART
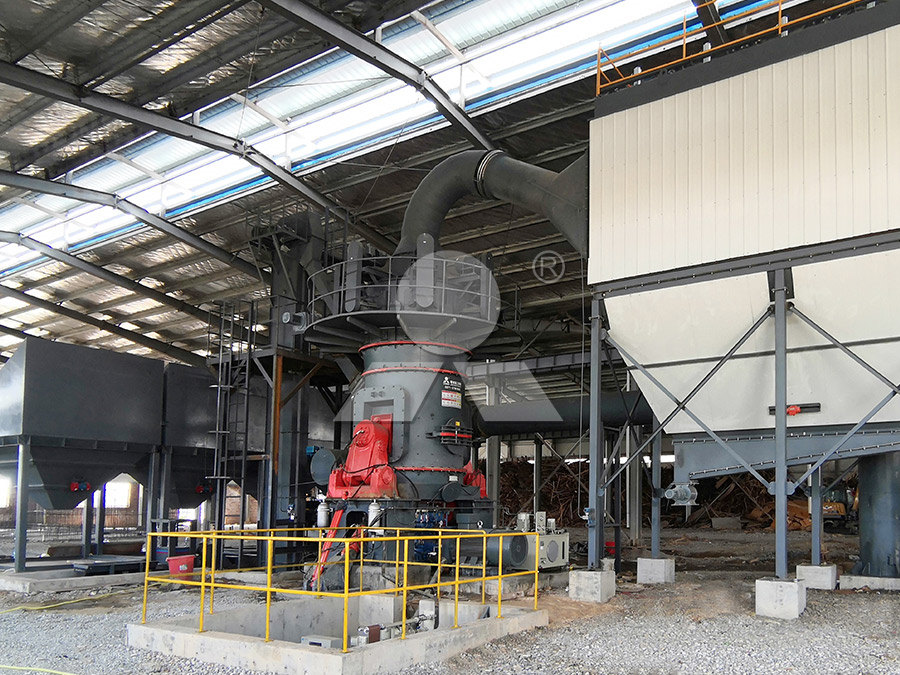
Testwork: Bond ball mill work index
75300 µm Models: Bond models, SGI, Morrell Mi The Bond ball mill work index is one of the most commonly used grindability tests in mining, and is often referred to as the Bond work index P 80: Sample finished product size in µm (and usually will provide a particle size distribution)The analytical sieve shaker AS 300 control is used in research development, quality control of raw materials, interim and finished products as well as in production monitoring The controllable electromagnetic drive offers an optimal adaption for every product Sharp fractions are obtained even after short sieving timesSieving Glen Mills, Inc2015年2月21日 Cytec Handbook Why have a large circulation load: If a product all finer than a certain critical size is required, the capacity of the ball mill is increased considerably by using it in closed circuit with a classifier and this increase is made still greater by increasing the circulating load in between the ball mill and the classifier (Fig 70)Circulating Load Calculation Formula 911MetallurgistThe knife mill GRINDOMIX GM 300 is the ideal instrument for grinding and homogenizing foods and feeds It allows to process sample volumes up to 07 liters quickly and reproducibly With four sharp, robust blades and a powerful 1000 W motor, it is ideal for homogenizing substances with a high water, oil or fat content as well as for grinding dry, soft and mediumhard productsGrindomix GM 300 Knife Mill Glen Mills, Inc
.jpg)
Tyler Mesh Glen Mills, Inc
The analytical sieve shaker AS 300 control is used in research development, quality control of raw materials, interim and finished products as well as in production monitoring The controllable electromagnetic drive offers an optimal adaption for every product Sharp fractions are obtained even after short sieving times