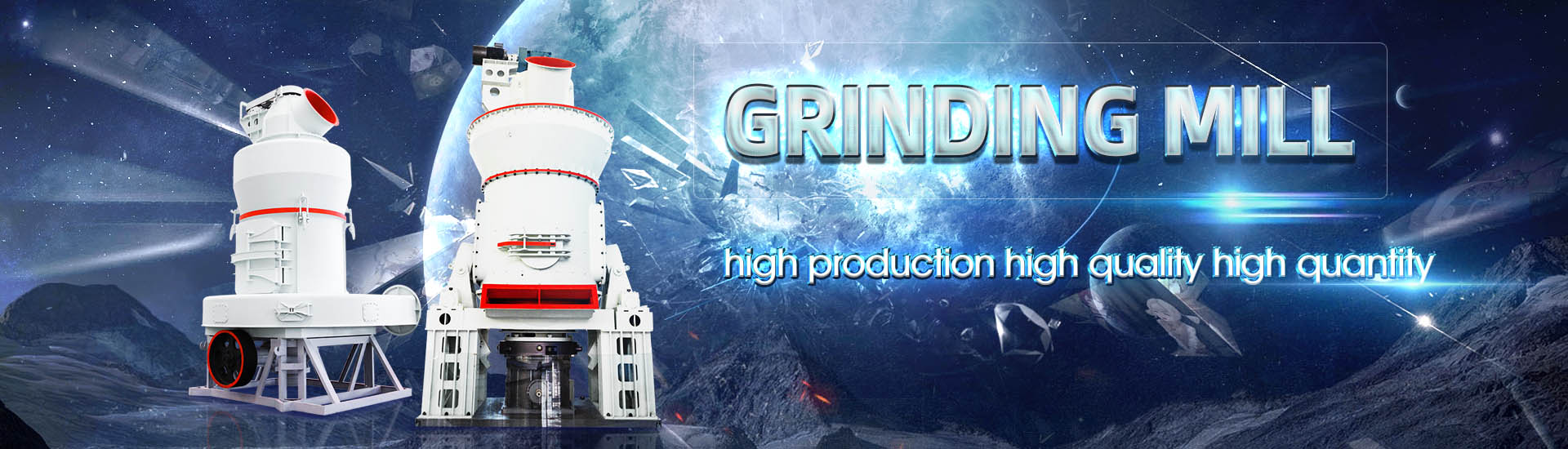
What parameters are needed to draw a high pressure roller mill
.jpg)
Optimization of working parameters of highpressure roller mill
2024年11月15日 In order to improve the crushing efficiency of highpressure roller mill and reduce energy consumption, the optimal parameter combination of highpressure roller mill is sought,The main performance parameters of the highpressure Roller Mill are production rate, power consumption and percentage of discharge size, which can be predicted based on materialOptimization of working parameters of highpressure roller mill 2024年11月15日 In order to improve the crushing efficiency of highpressure roller mill and reduce energy consumption, the optimal parameter combination of highpressure roller mill is Optimization of working parameters of highpressure roller mill 2017年4月1日 The control of the circulating load is achieved by adjusting the pressure drop over the mill comprising out of the gas flow and the solid loading inside the mill Higher classifier Operational parameters affecting the vertical roller mill
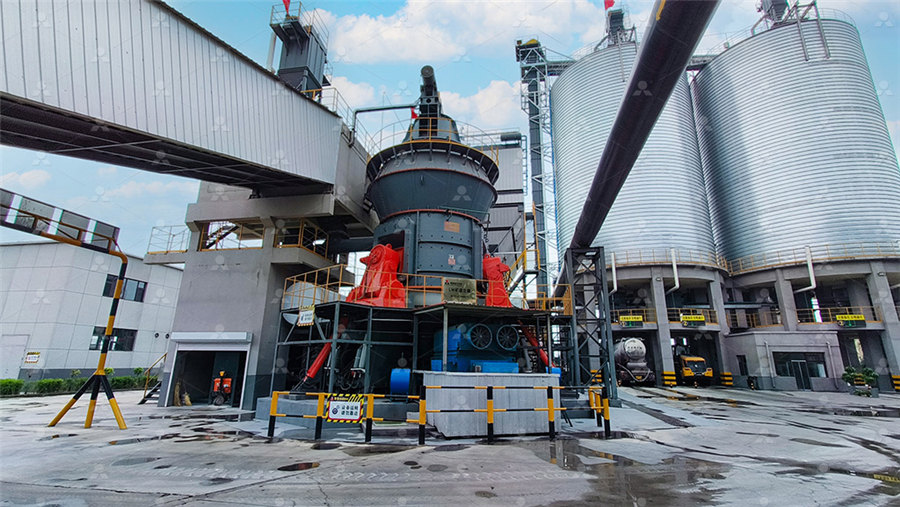
Schematic diagram of highpressure roller mill structure
In order to improve the crushing efficiency of highpressure roller mill and reduce energy consumption, the optimal parameter combination of highpressure roller mill is sought,HighPressure Roller Mill The highpressure roller mill, also called the roller presser or the extrusion mill, is a grinding equipment based on the principle of material layer crushing It was Roller Mill Springer2013年8月1日 This article reviews the principle and structure features of high pressure roller mill Moreover, the major progress in structure and technology parameters is summarized For the A Review on the Development of High Pressure Roller MillHigh Pressure Grinding Rolls (HPGR) technology is accepted as an energyefficient and costeffective alternative for treating specific mineral ore types HPGR technology has been A Review of the Modeling of High Pressure Grinding Rolls JSTAGE
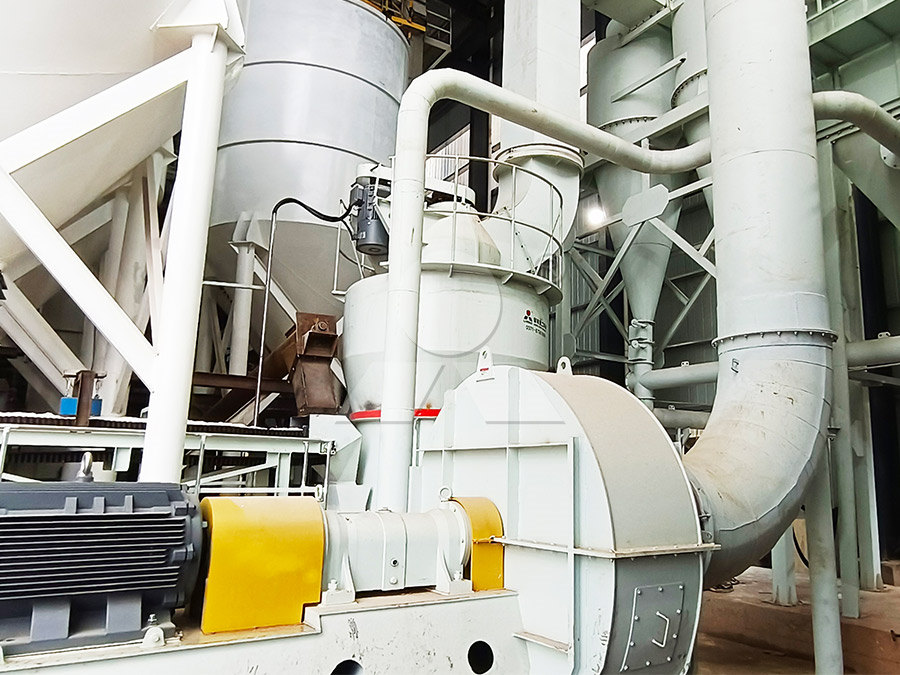
(PDF) A JOURNEY TO OPTIMAL ROLLING MILL DESIGN FROM
2011年9月14日 For the cluster mill, the materials of the rolls (particularly the work roll) are selected specially so as to tolerate the extreme high contact stress of the small work roll 2015年6月19日 The basic parameters used in ball mill design (power calculations), rod mill or any tumbling mill sizing are; material to be ground, characteristics, Bond Work Index, bulk density, specific density, desired mill Ball Mill Design/Power Calculation 911Metallurgist2010年1月1日 High Pressure Grinding Rolls ('HPGRs') presently are seen as a standard technology to be considered in feasibility studies, as an alternative to be compared with more conventional crushing and High pressure grinding rolls scaleup and Chapter 3: Pellet Mill Design drive, thus providing longer overall service life than a belt drive The highlyvariable loads which can occur in a pellet mill can generate overload conditions Stalled conditions are usually caused by the die plugging and/or trying to start the mill under load GearPellet mill design Feed Strategy
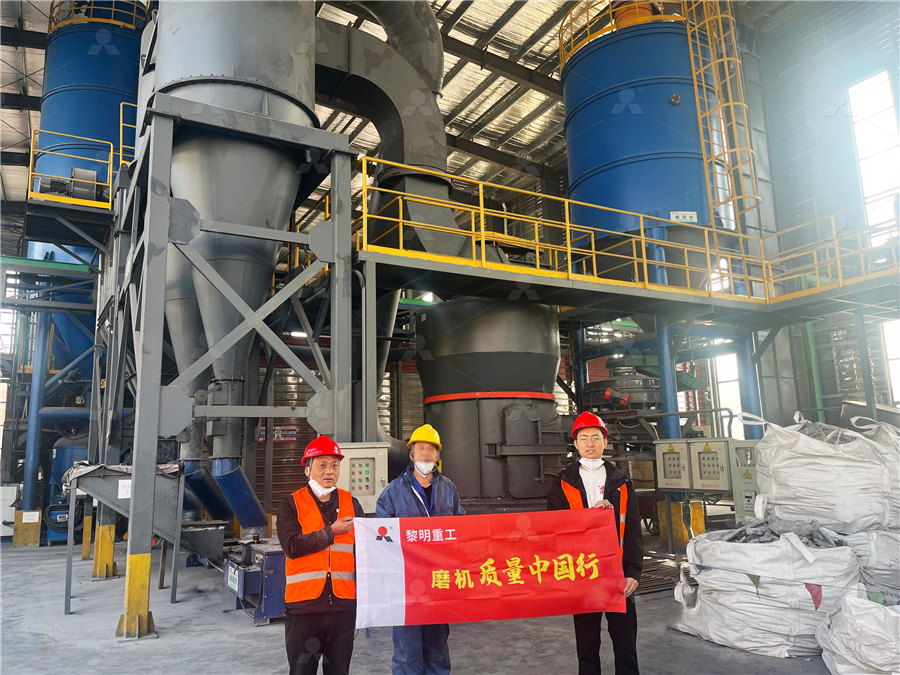
Session 11 Optimisation of Roller Press System
This document discusses roller presses, which are compaction tools used primarily as pregrinders in cement production to increase grinding capacity Key points: Roller presses apply high pressure to compact and crack raw materials, reducing energy needed for further grinding Configurations include pregrinding, hybrid, and finish grinding systems Pregrinding %PDF14 %âãÏÓ 91 0 obj > endobj xref 91 20 00000 n 00000 n 00000 n 00000 n 00000 n 00000 n 00000 n 00000 n 00000 n 00000 n 00000 n 00000 n 00000 n 00000 n Microsoft Word designdrawsprocket5docroller L/2 p aveA L»RDh Dh = h bh f F pA F roller ave y \ = å=0 2 2 / FL F L TorquerollerrF roller =× roller=× roller= µf µf a f f T wpRd wpRd n n =òò 0 2 2 entry exit ME 206: Manufacturing Processes I Instructor: Ramesh Singh; Notes by: Prof SN Melkote / Dr ColtonRolling IIT Bombay2019年2月21日 The paper analyzes the interrelation of: motion, particle size of ground rice grains, displacement, and grinding in a roller–plate mill The purpose of the study was to analyze and evaluate A study of operating parameters of a roller mill with a new
.jpg)
(PDF) Matrix Model Simulation of a Vertical Roller Mill with High
2014年5月1日 After the introduction of high compression grinding mills (High pressure grinding rolls (HPGR), vertical roller mill (VRM) and Horomill), various circuit configurations have been developed for 2013年5月30日 Fig 4 Roll configurations in rolling mills Twohigh mill roll configuration – This is the most commonly used rolling mill configuration In this configuration, there are two horizontally mounted rolls The rolling mill motor drives either both rolls (top and bottom) or only one roll (normally the bottom roll) with the top roll rotating due to the friction between the roll and the Basics of Rolling and Rolling Mills – IspatGuru3 What are the signiicant control parameters in roller compaction operations? Roller compaction/dry granulation is not a complex process to understand at the basic level Raw material powder is densiied by compressing it through two rollers under great pressure ThatFive Common Questions About Roller Compaction/ Dry Granulation2016年10月5日 In this chapter an introduction of widely applied energyefficient grinding technologies in cement grinding and description of the operating principles of the related equipments and comparisons over each other in EnergyEfficient Technologies in Cement Grinding
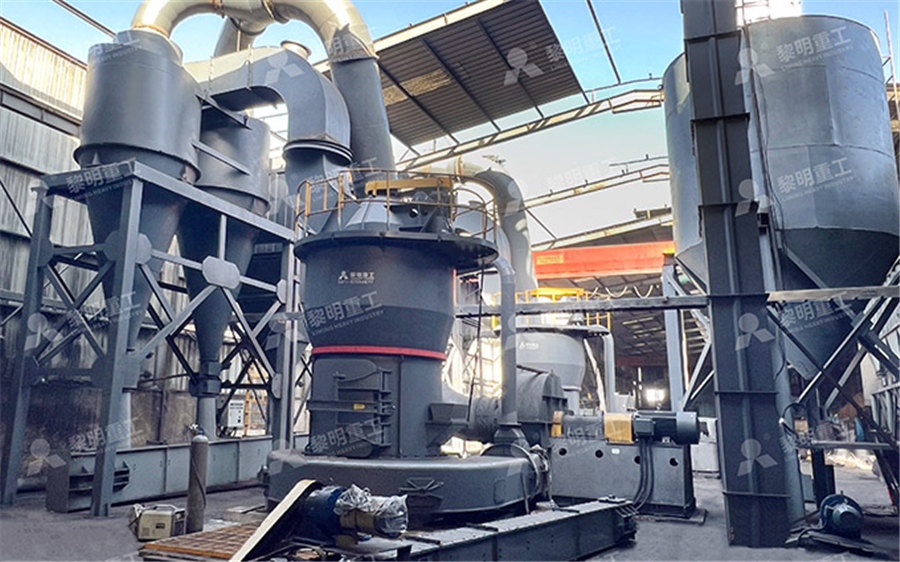
Rolling Process for Steel – IspatGuru
2014年3月27日 Fig 3 Rolling of thick plate in a plate mill Prediction of stresses and rollseparating force – Once the spread (the boundary of the deformation zone) has been calculated, this information can be used to predict the 2013年12月1日 The stress distribution of the high pressure grinding roller is an important index of the grinding mill design A simulation model of high pressure grinding roller is created by means of Analysis on influence parameters of combined roller of high pressure 1998年1月1日 The high pressure roll mill, HPRM, a newly invented size reduction equipment, has been recently added to the list of comminution machines and is classified as a highly efficient equipment(PDF) THE PERFORMANCE OF THE HIGH PRESSURE ROLL MILLRoll pressure and interfacial shear stress distributions, obtained during warm rolling of 1100H14 aluminium alloy strips, have been presented by Malinowski et al (1993)A comparison of the predictions of the present model to the measurements by Malinowski et al (1993) is shown in Figure 512The 628 mm thick strip has been reduced by 393% at 100°C at a roll speed of 12 Roll Pressure an overview ScienceDirect Topics
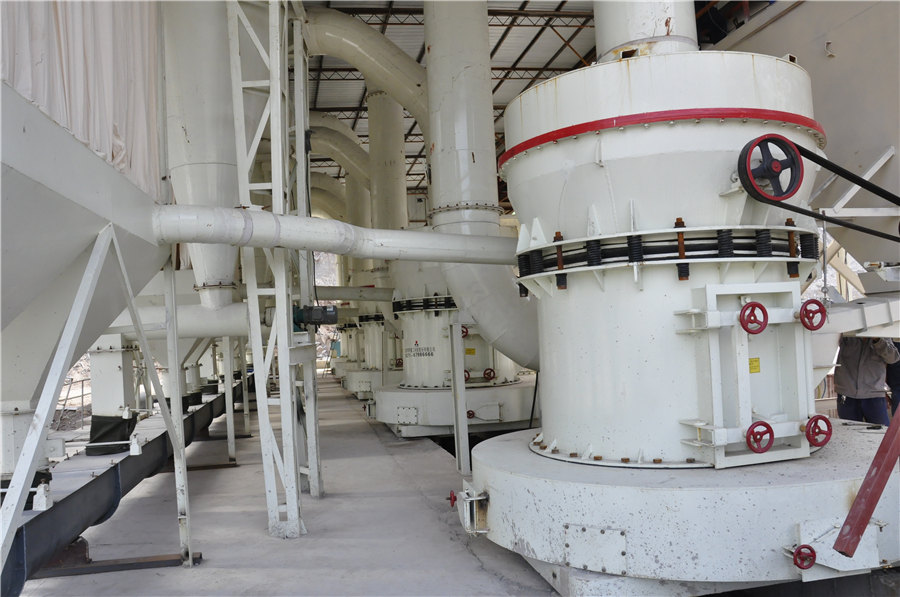
Roller Mill SpringerLink
2023年7月4日 The highpressure roller mill mainly consists of the feeding system, working rollers (a fixed roller and a movable roller), the driving system (main motor, reducer, belt pulley, and gear shaft), the hydraulic system, the stand, the transverse leakproof device, the discharge device, the control system, etcRecognized as the most trusted name in roller compaction technology and dry granulation equipment for more than 70 years, our customers are supported by worldleading applications and development experts, offering budgetfriendly, industrialstrength, highperformance roll compactors for dry granulation processing, with each new generation of machinery Roller Compaction Technology for dry granulationpressure difference between inlet and outlet, the grain size of the raw material [1, 2] For VRM the production capacity denotes both the capacity of grinding and drying of mill The grindability affects the capacity of grinding, type of mill and roller pressure The capacity of the mill is calculated Using G K * D 251PROCESS CONTROL FOR CEMENT GRINDING IN VERTICAL ROLLER MILL 2002年1月22日 The compaction of the particle bed in a high pressure roller mill causes pressure and shear forces on the rollers, which have been measured simultaneously with a sensorShear stresses and material slip in high pressure roller mills
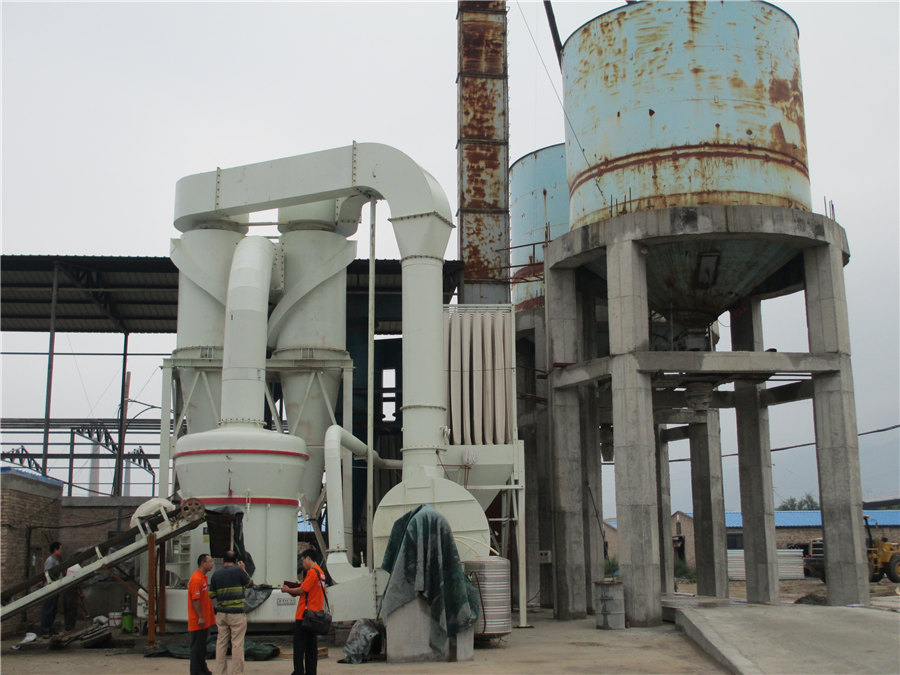
Cements ground in the vertical roller mill fulfil the quality
2013年3月1日 This study investigated a mathematical model for an industrialscale vertical roller mill(VRM) at the Ilam Cement Plant in Iran The model was calibrated using the initial survey's data, and the 2015年2月2日 As with any material, rock particles only break when the applied tensile stress exceeds the tensile strength of the rock However, in terms of comminution, the main interest is to derive reliable ways of assessing how a particular material breaks in a comminution device such as a crusher or a mill []In general, the breakage of rock particles is dependent on two factors: Comminution SpringerLinkEnduron® high pressure grinding rollers (or rolls) are the primary grinding tools of the Enduron® HPGR Built to last, these grinding rolls contain a superior autogenous wear layer that effectively protects their surface and improves their overall nipping properties They are a high quality product with a low operational costEnduron® High Pressure Grinding Rolls (HPGR) Weirrollers are run by frictional surface contacts of the bottom rollers The top rollers must be pressed with relatively high force over bottom rollers by spring load, air pressure or magnetically The drafting force is needed to draft the fibre strand which gets from the loading of the pressure of top rollers by pressure arm [2]Effect of Changing Front Top Roller Pressure of Drafting Zone of
.jpg)
An investigation of performance characteristics and energetic
2020年8月12日 Altun et al [15] explored the influence of the parameter settings of a vertical roller mill on grinding performance and demonstrated the influence of grinding pressure values on the size and mass 2018年1月1日 Operational experiences with High Pressure Grinding Rolls (HPGR) have shown that the rollers do not wear at the same rate This differential wear rate over time leads to differences in the (PDF) Roller life extension of high pressure grinding rolls with High pressure grinding mill, also known as high pressure roller mill, can grind nonflammable and explosive materials with Mohs hardness not greater than 93 and humidity below 6%Its main components include main engine, reducer, analyzer, pipeline device, blower, dust collector, jaw crusher, bucket elevator, electromagnetic vibrating feeder, electric control system, etcYGM High Pressure Grinding Mill2021年1月29日 VRM Production Rate and Specific Power It can be clearly seen in Figure 3 that last 6 months average breakdown frequency Rate was 6016 tripping per month means per day more than 2 trippingIncrease productivity of vertical roller mill using seven QC tools

CNC Machining Parameters: 11 Types, Setup and Adjustment
2024年7月29日 Cutting Parameters: Adjusting cutting parameters such as feed rate, spindle speed, and depth of cut based on the tool path ensures consistent material removal and highquality finishes Avoiding Collisions : Careful planning of the tool path helps in avoiding collisions with fixtures, clamps, and the workpiece, ensuring safety and precision2016年7月14日 HPGR or highpressure grinding rolls have made broad advances into nonferrous metal mining The technology is now widely viewed as a primary milling 911 Metallurgist is a trusted resource for practical insights, solutions, and support in mineral processing engineering, helping industry professionals succeed with proven expertise HPGRHPGR 911MetallurgistRoller shell dimension of different roller, as shown in table 1 tjprc editor@tjprc 830 R R Karthi L Emmanual Table 1: Shell Dimensions Rollers Outer Diameter (mm) Groove Depth (mm) Pitch Circle Diameter (mm) Feed 878 778 8002 Top 915 48 867 Discharge 900 615 8385 Setting: Feed roller side =36mm, Discharge roller side =145mm, Trash plate side =70mm (PDF) DESIGN AND ANALYSIS OF ROLLER SHAFTS FOR SUGAR Mill Configuration REVERSING ROUGHING MILL WIDTH REDUCTION: Slab width is reduced up to two inches with the vertical edging rolls (squeeze) THICKNESS REDUCTION: Roughing mill reduces slab thickness in five (5) to seven (7) reversing passes down to 1125” (transfer bar) DESCALING: High pressure descale water on entry side of mill removesPrinciples of Hot Rolling AIST
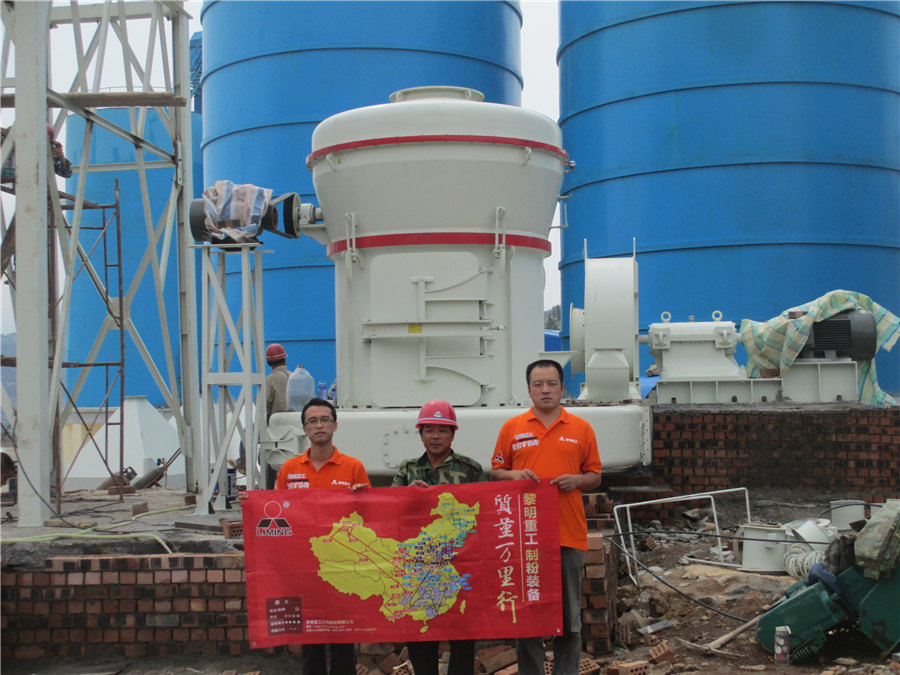
Review on vertical roller mill in cement industry its
2021年1月6日 Download Citation Review on vertical roller mill in cement industry its performance parameters India is the world's second largest producer of cement and produces more than 8 per cent of 2019年10月24日 The quality characteristics of the mill roller in sand casting has been affected by casting defects caused by in proper process parameter usage and intern affects its proper function that lead to large number of shop floor trials, high rate of rejection, and low casting yield The objective of this research is to design and analyze sand casting process of mill roller In Design and analysis of sand casting process of mill roller2020年3月1日 Grain milling might be the oldest manufacturing process in the world Archaeologists have found drawings, dating back to 2600 BC, of the basic process of rubbing or grinding using two stones on the walls of Egyptian tombs (Walker Eustace, 2016)Grinding (milling) of cereal grains is the fundamental operation currently used to produce flour, which is Stone milling versus roller milling: A systematic review of the 2020年7月28日 Highpressure grinding rolls (HPGRs) CRITICAL HPGR PARAMETERS HPGR roll diameters typically range from 05 m to 28 m, up to 50% of the energy needed for the dry grinding mill could be saved In wet grinding, the High Pressure Grinding Rolls 911Metallurgist
.jpg)
Improving Yarn Quality by Modification on Drafting Zone
TABLE III: THE MODIFICATIONS OF DRAW FRAME BOTTOM ROLLERS Bottom Drafting Rollers Finisher Drawframe 1 2 3 MiddleFront Roller 366 mm 386 mm 406 mm Back to Middle 418 mm 438 mm 458 mm TABLE IV: DRAW FRAME TOP ROLLERS PRESSURE ARRANGEMENTS Top drafting rollers Finisher Draw frame Top arm pressure in kg DRSC1 2021年2月19日 The results of improving ore crushing in a highpressure rollerpress are presented Application of a rollerpress enables higher crushing efficiency due to both power saving and reduction of (PDF) Ore crushing in the highpressure rollerpress as a 2012年3月1日 Vertical roller mills are the mills traditionally used for processing granulated blastfurnace slag and for grinding composite cements From the energy aspect they are superior to grinding plant Operating experience with a vertical roller mill for grinding with too high a proportion of large grains These cannot be ground by an unadjusted ball charge and as a result, mill performance is yet again reduced As shown in Figure 1, all these small, interlinked process steps need to be adjusted to achieve optimal ball mill performance Analysing the grinding process regularlyBALL MILLS Ball mill optimisation Holzinger Consulting
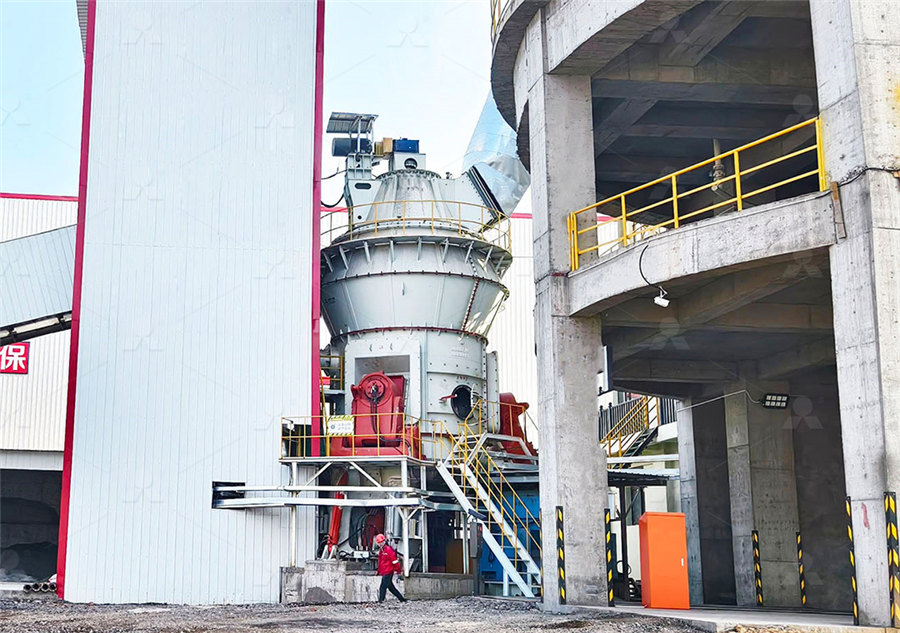
Calculated parameters for the highpressure roll crusher model
Download scientific diagram Calculated parameters for the highpressure roll crusher model and the selection function for the PF1 test The angles are in degrees and the factor γ from