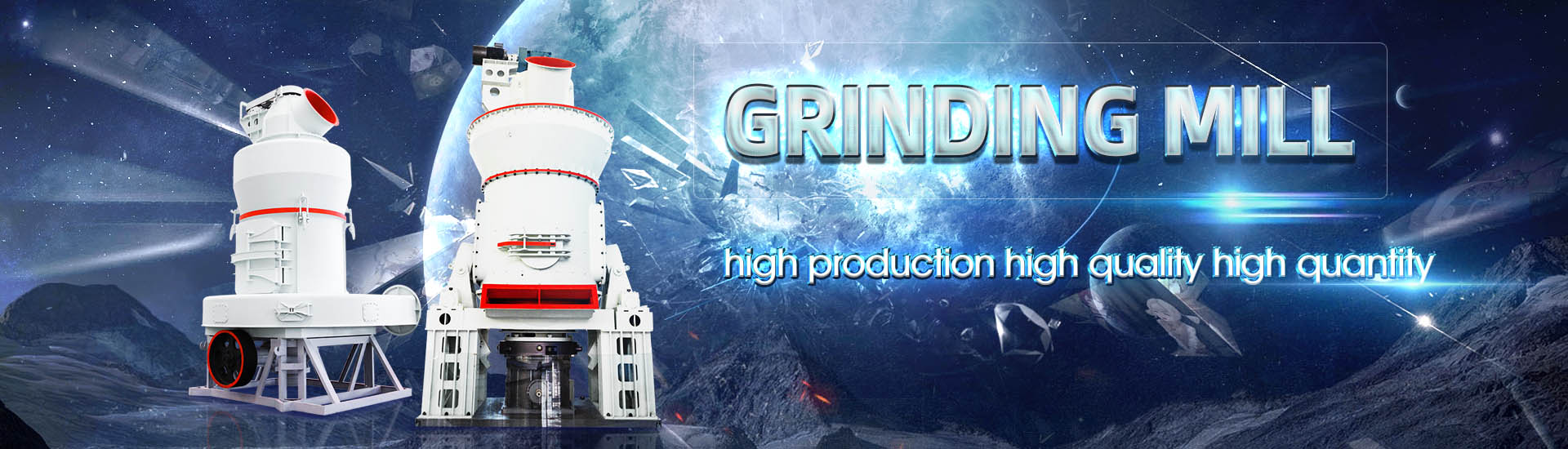
HOME→3.2*9m WindSweep Ball Mill Steel Ball Ratio3.2*9m WindSweep Ball Mill Steel Ball Ratio3.2*9m WindSweep Ball Mill Steel Ball Ratio
3.2*9m WindSweep Ball Mill Steel Ball Ratio3.2*9m WindSweep Ball Mill Steel Ball Ratio3.2*9m WindSweep Ball Mill Steel Ball Ratio
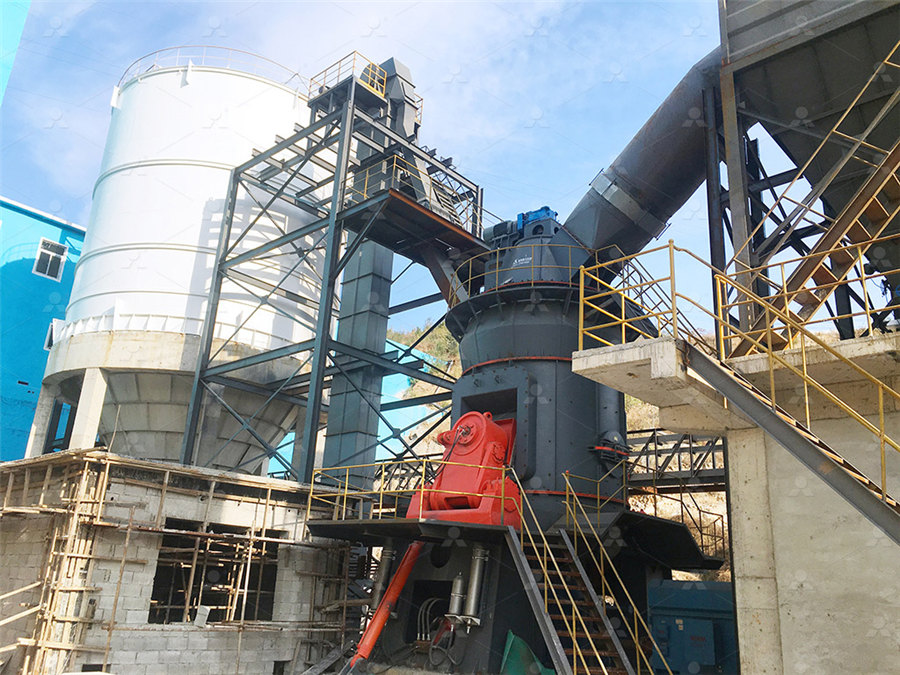
Tubular Ball Mills ScienceDirect
2016年1月1日 The design of different types of Tubular Ball Mills used for size reduction of crushed RunofMine ores is described in some detail followed by descriptions and The design of different types of Tubular Ball Mills used for size reduction of crushed Tubular Ball Mills2014年3月1日 With a view to developing a sound basis for the design and scaleup of ball mills, a large amount of data available in the literature were analyzed for variation of the two key mill (PDF) Analysis of ball mill grinding operation using mill power 2023年10月27日 The performance of grinding media in a ball mill is measured in terms of wear rate, which is a function of the media composition, hardness, phase structure, and A Review of the Grinding Media in Ball Mills for Mineral Processing

Grinding in Ball Mills: Modeling and Process Control ResearchGate
2012年6月1日 The paper presents an overview of the current methodology and practice in modeling and control of the grinding process in industrial ball mills Basic kinetic and energy The balls of 3rd and 4th groups are manufactured of steel with carbon equivalent of no less than 075% and carbon weight percentage of no less than 060% provided that the required STEEL MILLING BALLS FOR BALL MILLS Specifications2021年1月1日 In this paper, the design method of three chamber ball mill is introduced Comchambered with the design of Φ 35 × 13m threechamber ball mill, the design process of (PDF) Design of Threechamber Ball Mill ResearchGate2017年7月5日 The simulation reveals that the ball milling velocity, ball volume fraction inside the canister, ball size, and impeller shaft design are all important parameters for energyefficient Modeling and Analysis of HighEnergy Ball Milling Through Attritors
.jpg)
Design of Threechamber Ball Mill IOPscience
2021年1月1日 According to the specifications and parameters of the ball mill, the general layout, grinding body, lining plate, partition device, support device, transmission part and feeding and 2024年1月1日 The ball mill in a concentrator is mainly composed of feeding part, discharging part, rotating part, and transmission part (speed reducer, small drive gear, motor, and electric Ball Mill SpringerLink2012年6月1日 is lined with mill liners protecting the steel body of the mill and incorporating mill lifters which help to raise the content of the mill to greater heights before it drops and cascades down [36]Grinding in Ball Mills: Modeling and Process Control2015年6月1日 In wet grinding practice, highstress abrasion occurs over a small region when ore particles are trapped between the grinding balls and the mill liner, and the load is sufficient to fracture An investigation of the corrosive wear of steel balls
.jpg)
(PDF) Grinding Media in Ball MillsA Review
2023年4月23日 of cement clinkers was higher with cylpebs grinding media than with steel balls in a ball mill Table 2 Adapted from [51] Ball filling ratio also affects the grinding rate2020年7月2日 For this purpose, batch ball mill experiments were conducted with three narrowsize fractions (−335 + 236 mm, −170 + 118 mm, and −085 + 060 mm) of the feed and product samples of an (PDF) Effects of Ball Size Distribution and Mill Speed and Their Three types of catalyst were prepared among these one catalyst was prepared by using 175 g of K 2 CO 3, 4002 g of cAl 2 O 3, and 0975 g of sepiolite and 03 g of Fe 3 O 4 /g of catalyst, the components were homogenised by milling and extruded by syringe device by adding water drop wise, dried at 105 °C for 16 h and calcined at 500 °C for 4 hBall Mill an overview ScienceDirect Topics2013年9月8日 SAG Ball consumption is “average” at 400 g/t while Ball Mill grinding media (3″ balls) usage in 550 g/t Yet, you add steel and nothing seems to happen, tonnage is not noticeably improved You need more tonnage and could actually use a larger/coarser transfer size from the SAG to Ball MillSAG Mill Ball Size Evaluator Evaluation Factors Calculate
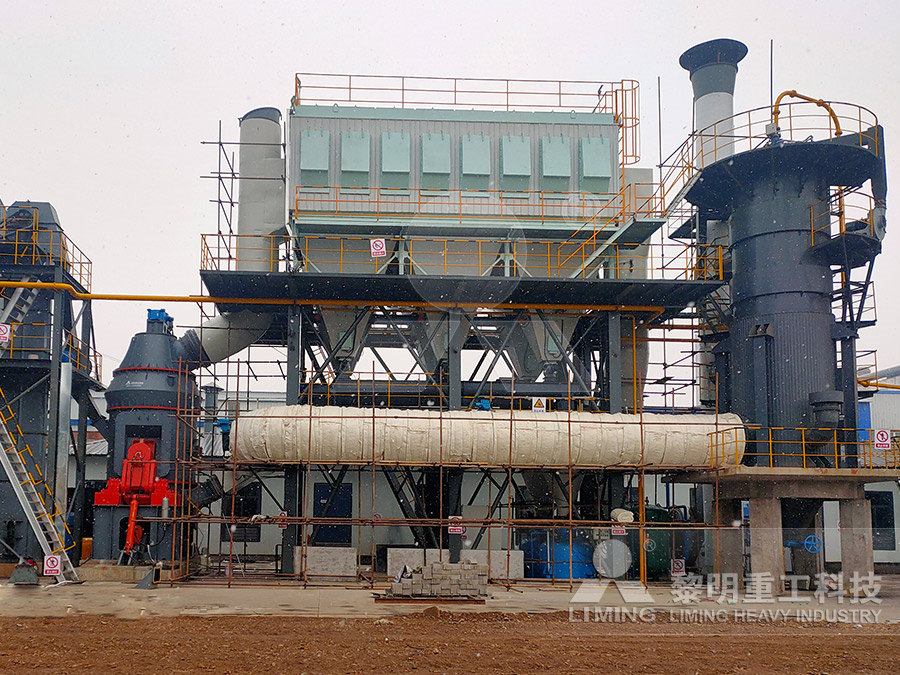
Ball Mill an overview ScienceDirect Topics
The ball mill is a tumbling mill that uses steel balls as the grinding media The length of the cylindrical shell is usually 1–15 times the shell diameter (Figure 811)The feed can be dry, with less than 3% moisture to minimize ball coating, or slurry containing 20–40% water by weight2015年6月20日 A Ball Mill Critical Speed (actually ball, rod, AG or SAG) is the speed at which the centrifugal forces equal gravitational forces at the mill shell’s inside surface and no balls will fall from its position onto the shell The imagery below helps explain what goes on inside a mill as speed varies Use our online formula The mill speed is typically defined as the percent of the Ball Mill Critical Speed 911Metallurgist2020年5月14日 section of ball mill, it was meshed into 100×100 cells, which represents the number of particles Main characteristics of the simulation parameters are listed in Table 1 Table 1 Simulation parameters Parameters Values Steel ball size /mm ∅6,8,10 Steel ball density /kgm3 7800 Steel ball filling 30% Steel ball shear modulus/Pa 7×1010PAPER OPEN ACCESS Effect of Lifter Shapes on the Mill Power in a Ball MillHighSpeed Steel Ball End Mill Sets Use these end mills for general purpose milling in most material, such as aluminum, brass, bronze, iron, and steel BallEnd Router Bits BallEnd Router Bits For smooth contour carving in wood, plastic, and BallNose End Mills McMasterCarr

Vibration characteristics of an operating ball mill
2019年7月1日 The steel ball gradually changed from spherical to nonspherical, and the size of the steel ball gradually became smaller According to the literatures (KatirciogluBayel et al, 2019;Orozco 2023年11月17日 Helical rolling (HR) with high temperature is an efficient forming process to produce bearing steel balls with diameter more than 25 mm This article discusses the advantages and disadvantages of two HR roller designing methods: single side variable lead method and double side variable lead method Finite element (FE) simulations of HR Numerical and experimental investigation of helical rolling process 2024年2月19日 The ratio of steel balls in the ball mill depends on the effective length of your mill, whether it has a roller press, the size of the feed particles, the lining and structure used, the expected sieve residue fineness and ratio, how Ball Mill Steel Balls: Quality And Gradation JXSC 2014年3月1日 the test ball mill for a period of 12 min Pregrinding of the crushed material ensures that the 330 g steel balls including 200 pieces of 6 materialball ratio, and medium properties (PDF) Analysis of ball mill grinding operation using mill power
.jpg)
Best way to determine the balltopowder ratio in ballmilling?
Then, the optimal mass ratio of ball to powder in ball mill is 75*24/(25*176)= 409 to 75*21/ I want to ball mill 60 gm of Al powder in steel jar with 10mm diameter ball sizePDF On Apr 28, 2014, Huynh Xuan Kho and others published Planetary Ball Mill Process in Aspect of Milling Energy Find, read and cite all the research you need on ResearchGatePlanetary Ball Mill Process in Aspect of Milling EnergyThe cutting area is evaluated with calculating the uncut chip thickness Figure 30 shows simulation of the height in the cutting area when cutting with a 2 flutes ball end mill during a rotation of the cutter Because the cutting edges were divided into small segments in the simulation, the cutting areas are designated by symbolsBall End Mill an overview ScienceDirect Topics Denver 30" Diameter x 54" long Ball Mill, Steel liners, Ball charge, Incudes infeed hopper with spout feeder, 3 x 3 Denver Ball Mill, Made in USA, Operating skid constructed from square tubing, 5' x 3' (15m x 09m) SAG Mill with 20 HP (15 kW) motor View Details Contact Seller Request Price ExpandUsed Ball Sag Mills for Sale Mining Surplus Record
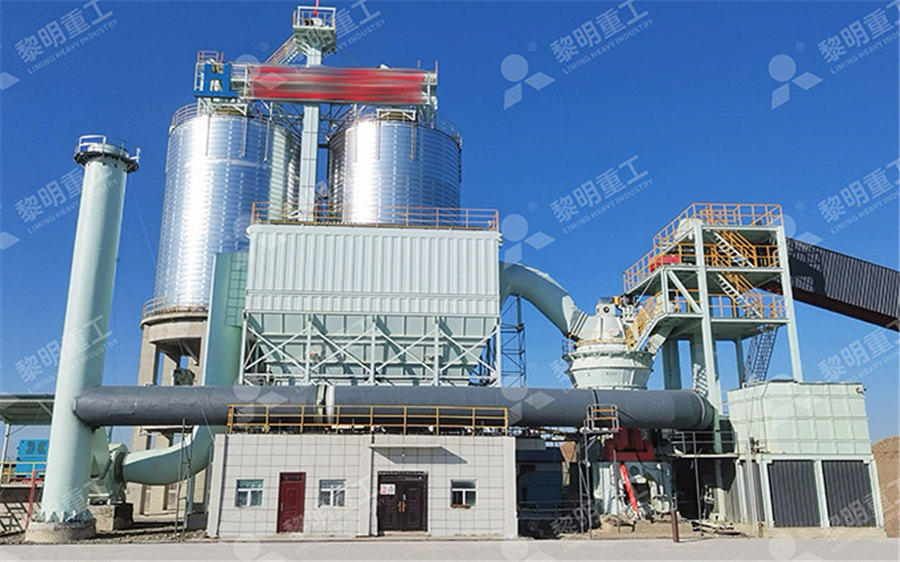
STEEL MILLING BALLS FOR BALL MILLS Specifications
Note 2 Calculation of ball volume and weight is performed using values of nominal diameter provided that the steel density is 785 g\cm3 33 Example of conventional values of a ball with diameter 60 mm and nominal hardness (1): Ball 601 SSU3 49997 4 TECHNICAL REQUIREMENTS 41 Characteristics 411The above is intended as a guide only Individual ball hardness readings may fall outside the range listed above Nominal Ball Diameter in (inch) Mass in (g) Nominal Ball Diameter in (mm) Mass in (g) Ball Diameter (in) Minimum Mass (g) Maximum Mass (g) Ball Diameter (mm) Minimum Mass (g) Maximum Mass (g) 35 2869 3156 94 3392 3731MCGBLSAGTS20 Version 20 SAG Balls Technical2019年8月30日 1 Calculation of ball mill capacity The production capacity of the ball mill is determined by the amount of material required to be ground, and it must have a certain margin when designing and selecting There are many Ball Mill Parameter Selection – Power, Rotate Speed, The Sepor Batch Ball Mills are constructed of 304 stainless steel (wetted parts), with structural steel frame and support structure The rugged forged steel trunnions with hubs provide support for the shaft and give structural support Sepor Stainless Steel Batch Ball Mill
.jpg)
AS/NZS 11702 Wind Load Calculation Example
2024年10月24日 A fully worked example of AS/NZS 11702 (2011) wind load calculations SkyCiv’s wind load calculator now has several code references including the Australian/New Zealand Standards In this article, we will be The sand is weighed by the belt scale, and the ratio of water and sand is automatically controlled by the computer The ball mill is a necessary part of the raw material preparation section There are two kinds of ball mill in an AAC production line: wet type and dry type Wet type ball mill is used to mill sand while the dry type is for lime Ball Mill, Milling Machine – TEEYERDownload Table Ball mill characteristics and test conditions Mill Diameter, D (cm) 204 Length, L (cm) 166 Volume, V (cm 3 ) 5,423 Operational speed, Ν (rpm) 66 from publication Ball mill characteristics and test conditions Mill Diameter, D Ball mill is widely used in mineral processing plants for wet or dry grinding materials and equipped with spiral classifier, high efficiency Skip to content JXSC Machinery Us +86 Home The ball mill is a tumbling mill that uses steel balls as grinding mediaBall Mill Mining Grinding Mill JXSC Machinery
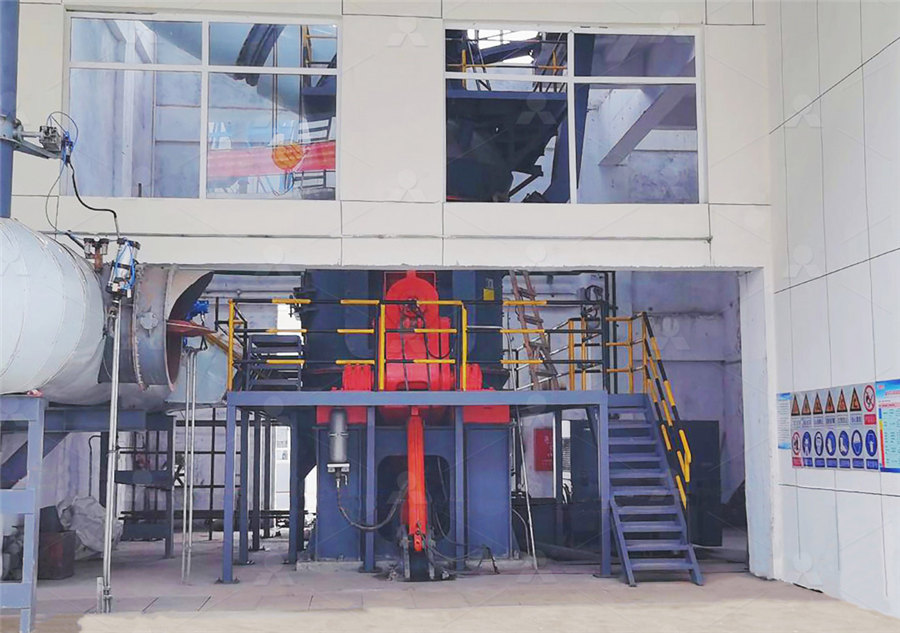
Ball Mill Rod Mill Design 911Metallurgist
2016年4月22日 Grinding (Rod) or (Ball) Mill TYPE D Has single weld, triple flanged, construction which means the shell is furnished in two sections, flanged and bolted in the center All flanges are double welded as well as steel head to shell, note design Tumbling Mill (Rod or Ball) Mill TYPE E Has quadruple flangedDenver 4' Diameter by 5 Foot Long Ball Mill Description: Excellent condition Denver Ball Mill Steel Ball Mills are one of the most precise ID: Quote + Eimco 4 ft x 4 ft Ball Mill New Rubber Liners Installed Dimensions: 4 ft Dia x 4 ft Long Teco 30 HP Electric Motor Volts: 230/460 3 Phase Hz: 60 RPM 1750 ID: Quote +New and Used Ball Mills for Sale Ball Mill Supplier Worldwide2023年9月18日 254 cm in diameter were used (2475 cm 3 / 858 cm 3 ≈288 steel balls, to min imize the interstitial spaces) The weight of the balls in small mills also affects th e grain size of the productBond´s work index estimation using nonstandard ball mills2021年4月1日 Milling devices used: (a) knife mill, (b) impact mill (IM), (c) rotary ball mill (RBM), (d) stirred ball mill (SBM), and (e) vibratory ball mill (VBM) KR Rajaonarivony, C Mayer Laigle, B (PDF) Comparative comminution efficiencies of rotary, stirred and
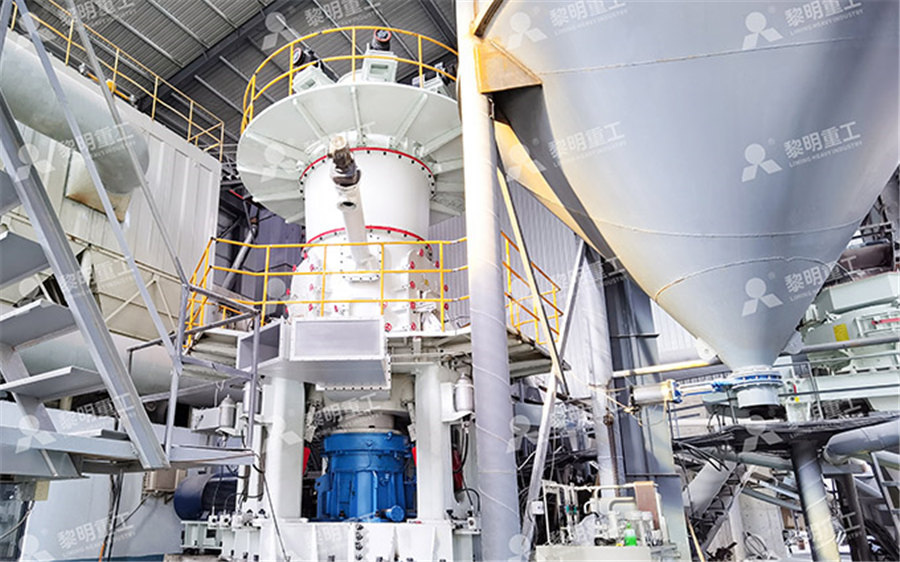
09 KHD Ball Mill PDF Mill (Grinding) Bearing
09 khd ball mill Free download as PDF File (pdf), Text File (txt) or view presentation slides online Separator 1520 Closed circuit mills with separator 1520 Double compartment mills 3040 Ball mills are commonly used for Explain the role of ball mill in mineral industry and why it is extensively used In ball mills, steel balls or hard pebbles to break particle based on impact and attrition Diameter Ratio: 14 to 18: 05 to 35: 025 to 050: Feed Size: 25 AMIT 135: Lesson 7 Ball Mills Circuits – Mining 2016年5月30日 Steel BallMill,” Material Transactions, JIM, Vol 36, No 2 estimated by the Raman intensity ratio, of 25 nm for the agate ballmill is smaller than that of 35 nm for the stainless DESIGN AND FABRICATION OF MINI BALL MILL (PART HighSpeed Steel Ball End Mill Sets Use these end mills for general purpose milling in most material, such as aluminum, brass, bronze, iron, and steel BallEnd Router Bits BallEnd Router Bits For smooth contour carving in wood, plastic, and Ball End Mills McMasterCarr

Ball mill, Ball grinding mill All industrial manufacturers
The High Energy Ball Mill (model: 8000M), manufactured by Horiba Scientific, is capable of accommodating samples sizes ranging from 02 up to 10g In addition, this type of mill is best Compare this product Remove from comparison tool2022年11月1日 It is also known that the ore processed by the plant is iron, with a Mohs hardness of between 8 and 85 and a specific gravity of 42 The P80 of 028 mm and the P50 of 010 mm, as depicted in Fig 1, represents the particle size distribution of the feed to the secondary millIt should be emphasised that the 30 mm refers to the diameter of the daily Can ceramic balls and steel balls be combined in an2020年10月1日 The effect of tempering temperature on mechanical properties of the quenched low alloy steel was studied The asreceived low alloy steel samples were heated to 950 °C, held for 30 min, and then A Review on Current Mill Liner Design and Performance2015年9月1日 scale overflow ball mill and into a trommel using a 2way coupled DE M/SPH model where DEM is used to represent the ball charge and SPH for the fluid slurry containing the fine productSimulation of overflow ball mill discharge and trommel flow using
.jpg)
Effect of Sintering Temperature on the Pitting Corrosion of Ball
2018年3月30日 Effect of Sintering Temperature on the Pitting Corrosion of Ball Milled Duplex Stainless Steel by using Linear Sweep duplex stainless steel by h igh energy ball mill [2][3][4][5 ][6] [7 2024年1月31日 Ceramic ball milling has demonstrated remarkable energysaving efficiency in industrial applications However, there is a pressing need to enhance the grinding efficiency for coarse particles This paper introduces a novel method of combining media primarily using ceramic balls supplemented with an appropriate proportion of steel balls Three grinding media Enhancing the Grinding Efficiency of a Magnetite SecondStage Mill