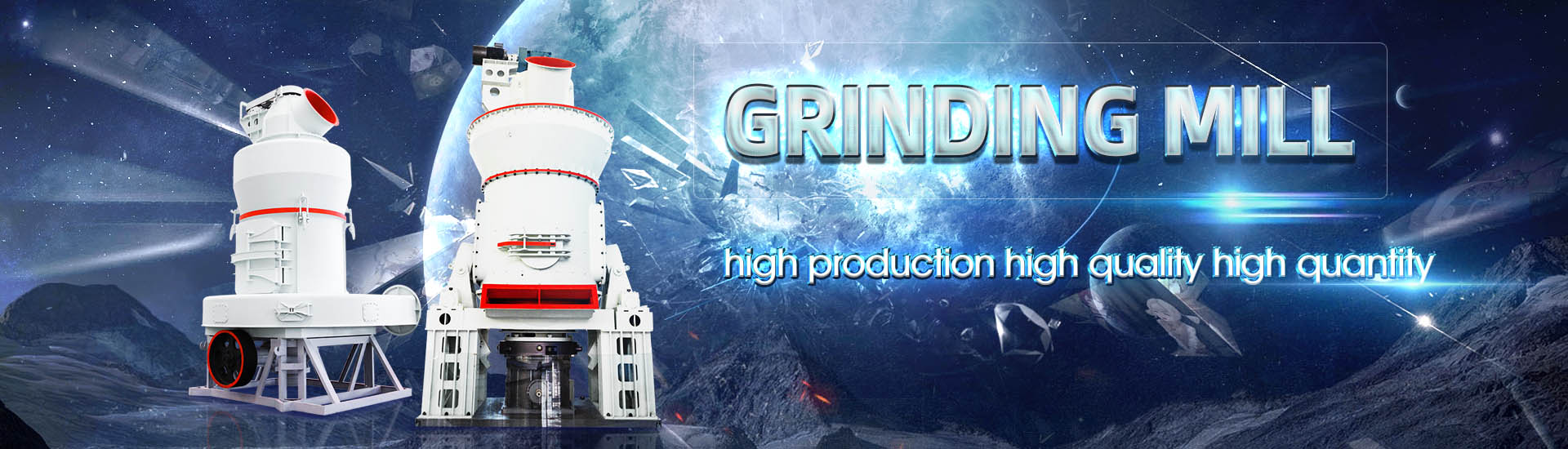
Cement plant process flow
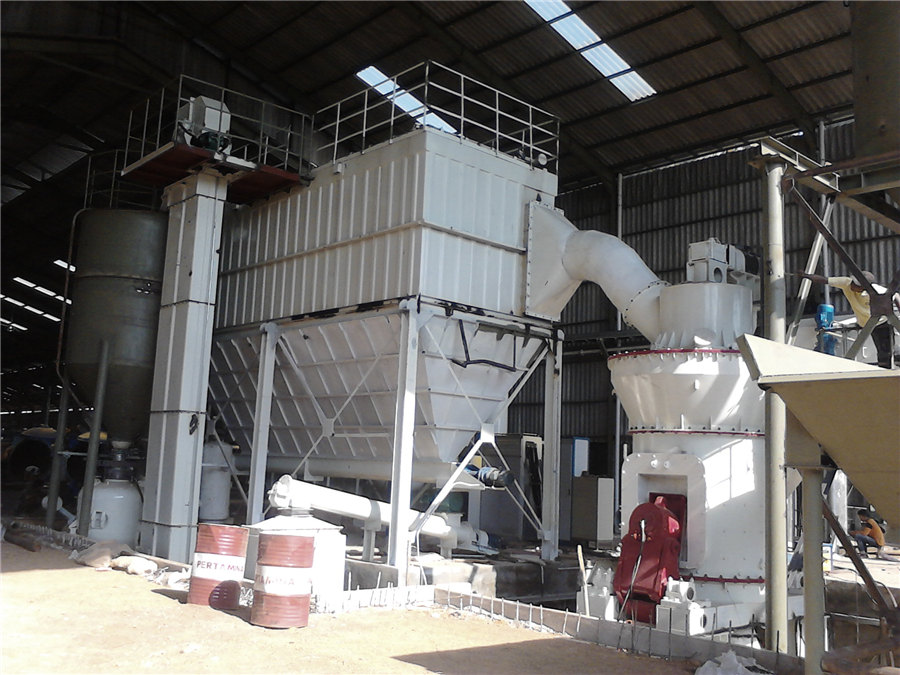
Typical cement manufacturing process flow diagram
The purpose of this study is to examine the production process, its economic support, raw material availability, demand, process modification, optimization steps to implement the production Download scientific diagram Cement Manufacturing Process Flowsheet (Flow Chart) from publication: Cement Manufacturing – Process Modeling and TechnoEconomic Assessment (TEA) usingCement Manufacturing Process Flowsheet (Flow Chart)Manufacturing of cement involves various raw materials and processes Each process is explained chemical reactions for manufacture of Portland Cement Manufacture of Cement Materials and Manufacturing 2018年8月28日 Production of cement completes after passing of raw materials from the following six phases These are; Cement uses raw materials that cover calcium, silicon, iron and aluminum Such raw materials are limestone, clay Cement Manufacturing Process The Engineering
.jpg)
The Cement Manufacturing Process Thermo Fisher
2023年12月20日 Cement manufacturing is a complex process that begins with mining and then grinding raw materials that include limestone and clay, to a fine powder, called raw meal, which is then heated to a sintering temperature as Cement Plant: The Manufacturing Process worldcementassociation 1 Limestone (CaCO3) is taken from a quarry 2 4 3 The limestone is fed into a crusher and then stored until needed The Cement Plant: The Manufacturing Process 4 5 World Cement The Cement Plant Operations Handbook is a concise, practical guide to cement manufacturing and is the standard reference used by plant operations personnel worldwide Providing a The Cement Plant Operations Handbook International Cement 2021年3月9日 In this study the process flow diagram for the cement production was simulated using Aspen HYSYS 88 software to achieve high energy optimization and optimum cement flow rate by varying the flow rate of calcium Simulation and Optimization of an Integrated Process
.jpg)
Cement Plant: The Manufacturing Process 4 5 World Cement
Cement Plant: The Manufacturing Process worldcementassociation 1 Limestone (CaCO3) is taken from a quarry 2 4 3 The limestone is fed into a crusher and then stored until needed The clinker is mixed with additives, such as gypsum, and then ground in a 2017年8月15日 Providing information on bulk materials handling (liquid and solid), plant systems engineering, specialty machine design, and process control engineering Industry focus for the following posts are bulk handling systems, ELiquid (EJuice) manufacturing equipment, Biomass, plastics and polymersThe Cement Manufacturing Process2023年12月20日 The Cement Manufacturing Process flow chart sums up where in the process each type of technology is making a difference Cement operators also use these analysis systems to analyze and adjust the coal mix instream, The Cement Manufacturing Process Thermo Fisher Download scientific diagram Process flow diagram for the cement manufacturing process, showing electricity and heat consumption or inputs [39] from publication: Energy Savings Associated with Process flow diagram for the cement manufacturing process,
.jpg)
Cement Manufacturing
CEMENT INDUSTRY SYMBOLS Name of substance Chemical symbol Cement industry symbol Molar mass Calcium oxide or lime CaO C 56 Silica SiO 2 S 60 Alumina2014年6月10日 Evolution of the cement Process • Wet process easiest to control chemistry better for moist raw materials • Wet process high fuel requirements fuel needed to evaporate 30+% slurry water • Dry process kilns less fuel requirements • Preheater/Precalciner further enhance fuel efficiency allow for high production ratesCement manufacturing process PPT Free Download SlideShare2021年3月9日 In this study the process flow diagram for the cement production was simulated using Aspen HYSYS 88 software to achieve high energy optimization and optimum cement flow rate by varying the flow rate of calcium oxide and silica in the clinker feed Central composite Design (CCD) of Response Surface Methodology was used to design the ten experiments for Simulation and Optimization of an Integrated Process Flow Sheet 2015年9月17日 6 00 Limestone Quarry and Crushing plant The major raw material for cement production is limestone The limestone most suitable for cement production must have some ingredients in specified quantities ie, calcium carbonates, silica, alumina, iron,etc Belt Conveyors The quarried raw material is transported to the cement plant, using mechanical conveying Cement Production Process PPT SlideShare
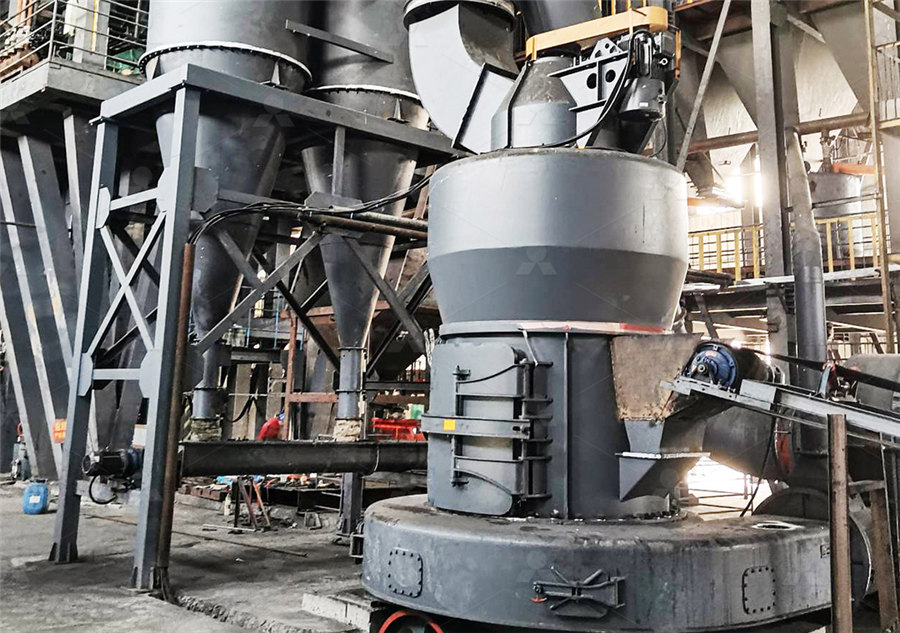
Cement Manufacturing Process Flowsheet (Flow Chart)
Download scientific diagram Cement Manufacturing Process Flowsheet (Flow Chart) from publication: Cement Manufacturing – Process Modeling and TechnoEconomic Assessment (TEA) using SuperPro The cement manufacturing process starts from the mining of raw materials that are used in cement manufacturing, mainly limestone and clays A limestone quarry is inside the plant area and a clays quarry is as far from the plant area as 25 kmManufacturing process LafargeA development of this process is the 'precalciner' kiln Most new cement plant is of this type The principle is similar to that of the dry process preheater system but with the major addition of another burner, or precalciner With the additional Manufacturing the cement kiln Understanding 1971年8月17日 116 Portland Cement Manufacturing 1161 Process Description17 Portland cement is a fine powder, gray or white in color, that consists of a mixture of hydraulic cement materials comprising primarily calcium silicates, aluminates and aluminoferrites More than 30 raw materials are known to be used in the manufacture of portland cement, and these116 Portland Cement Manufacturing US EPA
.jpg)
116 Portland Cement Manufacturing US Environmental
the process during the finish grinding operations described below These materials, also excavated from quarries or mines, are generally purchased from an external source, rather than obtained directly from a captive operation by the cement plant The portland cement manufacturing industry is relyingChoose an optimal location for the cement plant Design the layout of the cement factory Acquire the necessary equipment Construct the factory and install the equipment Recruit and train staff to operate the plant What is the process for making concrete? The concrete manufacturing process includes: Batching, where all required ingredients StepbyStep Guide to the Manufacturing of Cement PRACTICAL While each cement plant may differ in layout, equipment, and appearance, the general process of manufacturing portland cement is the same: crushed limestone and sand are mixed with ground clay, shale, iron ore, fly ash and alternative raw materials The clinker comes out of the kiln redhot with a consistency like a lava flowHow Cement is Made Portland Cement AssociationCement manufacturing: components of a cement plant This page and the linked pages below summarize the cement manufacturing process from the perspective of the individual components of a cement plant the kiln, the cement mill etc For information on materials, including reactions in the kiln, see the ' Clinker ' pagesCement manufacturing components of a cement plant Understanding Cement
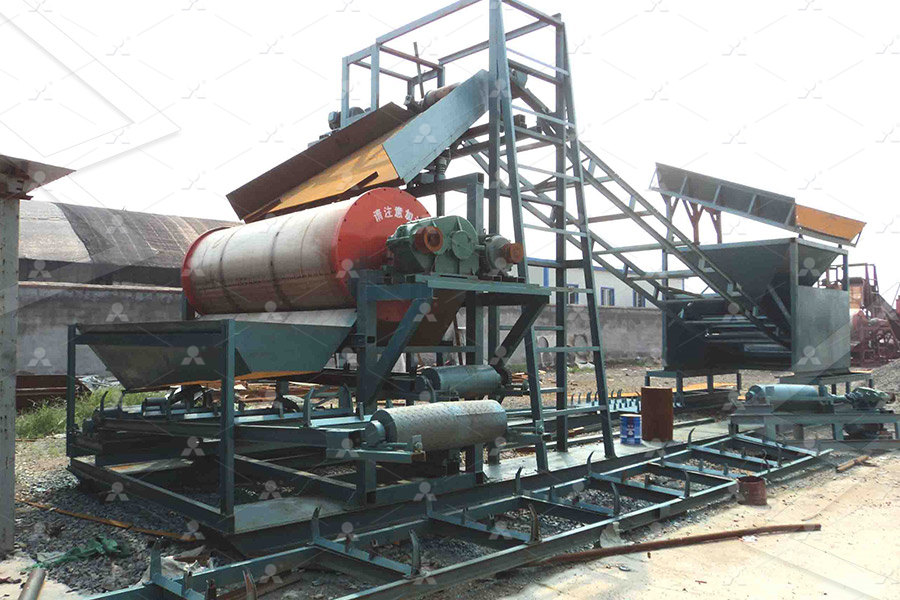
Process flow sheet of a CAP process integrated in a cement plant
Download scientific diagram Process flow sheet of a CAP process integrated in a cement plant (adapted from [46]) from publication: CO2 Capture, Use, and Storage in the Cement Industry: State of 2022年11月9日 Hope this will help cement plant process operators to get benefit by implementing new technology against conventional flow measurement and acknowledge the benefits offered Author MrManish S Patel , A Chartered Mechanical Engineer with more than 24 years rich experience in process industries especially in flow measurement with a wide range Advanced Air Process Gas Flow Monitoring in Cement Plants2023年9月5日 Process control experts in the cement industry need to be wellversed with the process flow, the chemical reactions, and the physical transformations that occur in a cement plant They need to understand the interdependencies between the various process parameters and how they affect the quality of the cement and the efficiency of the production processMastering Process Control Instrumentation in Cement Plants: A Download CAD block in DWG General plan of the cement manufacturing process it is a vertical grinding system (65357 KB)Cement plant in AutoCAD Download CAD free (65357 KB) Bibliocad
.jpg)
The cement plant of tomorrow ScienceDirect
2023年11月1日 Cement plant process technology and condition Power and fuel costs Availability of excess heat Availability of materials Space requirements Schematic flowsheet of a multistage grinding plant for the production of Portlandcements including 3 2016年1月20日 The LN cement plant, located in the southwest of Shandong Province, was considered as a case study for the mass flow and balance analysis This cement plant operates on a dry process line with a fivestage suspension preheater and an inline precalciner The kiln is 4 m in diameter and 60 m in lengthAnalysis of material flow and consumption in cement production process The whole process of cement manufacturing in Messebo Cement plant which consists of two separate Cement Production lines can be summarized into the following processes ;as can be seen in the process and Quality flow diagram below; 1 Quarrying and Crushing 2 Raw material Storage and Transportation 3 ProportioningCEMENT PRODUCTION AND QUALITY CONTROL A Cement manufacturing ProcessIn this process, the steps of raw material processing, fuel preparation, clinker burning and cement grinding constitute major emission sources for particulate components While particulate emissions of up to 3,000 mg/m 3 were measured leaving the stack of cement rotary kiln plants as recently as in the 1960s, legal limits are typically 30 mg/m 3 today, and much lower levels are Cement kiln Wikipedia
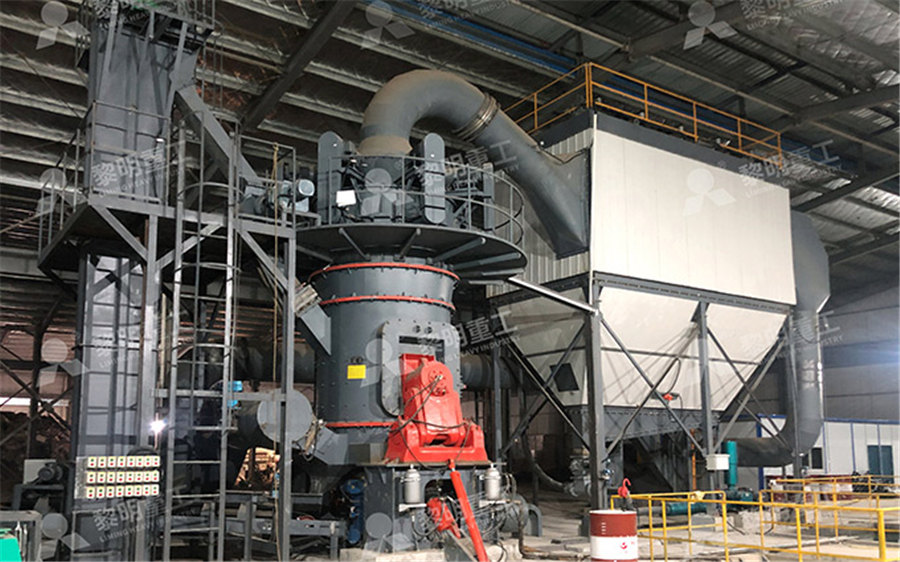
Cement Manufacturing Process Simplified Flow Chart
2013年5月11日 Cement manufacturing process components of a cement plant from quarry to kiln to cement mill Skip to content Menu Home; Resources Civil PowerPoint Presentations Civil ppts; Interview Questions; Cement Manufacturing Process Simplified Flow Chart March 15, 2017 May 11, 2013 by Johnny2020年9月26日 Cement Manufacturing Process: ement is a material which is used to bind other materials together Binding means it has an effect of gluing the substances Coriolis Flow Transmitter Working November 6, 2020 Instruments Boiler Drum Level Control November 3, 2020 Instruments Deluge Valve System WorkingCement Manufacturing Process Chemical Engineering WorldFully revised and updated with improved content, the new Sixth Edition of the Cement Plant Operations Handbook is now available Covering some 300 pages, the cement industry’s favourite technical reference book offers indepth information on the various aspects of cement productionThe Cement Plant Operations Handbook 6th Edition from Download scientific diagram CEMENT MANUFACTURING PROCESS FLOW CHART from publication: Industrial Geology ResearchGate, the professional network for scientistsCEMENT MANUFACTURING PROCESS FLOW CHART
.jpg)
A practical guide to improving cement manufacturing processes
The cement production process 1 The Quarry: The cement production process begins with the extraction of limestone and clay from the quarry 2 Crusher and PreBlending: The material is then crushed to reduce particle sizes and blended to reduce variability in composition 3 Raw Mill and Kiln: Raw materials and additives arevi Improving Thermal and Electric Energy Efficiency at Cement Plants: International Best Practice Cement is paramount for economic development and poverty reduction in emerging markets Along with aggregates and water, cement is the key ingredient in the production of concrete, and, as such, is an essential construction materialIMPROVING THERMAL AND ELECTRIC ENERGY EFFICIENCY AT CEMENT In September 2015, this system was put into operation at the San Antonio Cement Plant in Texas, US, and its output exceeded 75 kt CO 2 /year The SkyMine® process was used to capture 90% of the CO 2 from one of the flue A review of lowcarbon technologies and projects for Cement Manufacturing and Process Control 41 Cement Manufacturing: Basic Process and Operation To design the Refractory for the lining of different equipments in a cement plant, it is necessary to understand the total operational process of a cement plant in depth It is necessary to know the conditions prevailing in different equipments and theChapter 4 Cement Manufacturing and Process Control
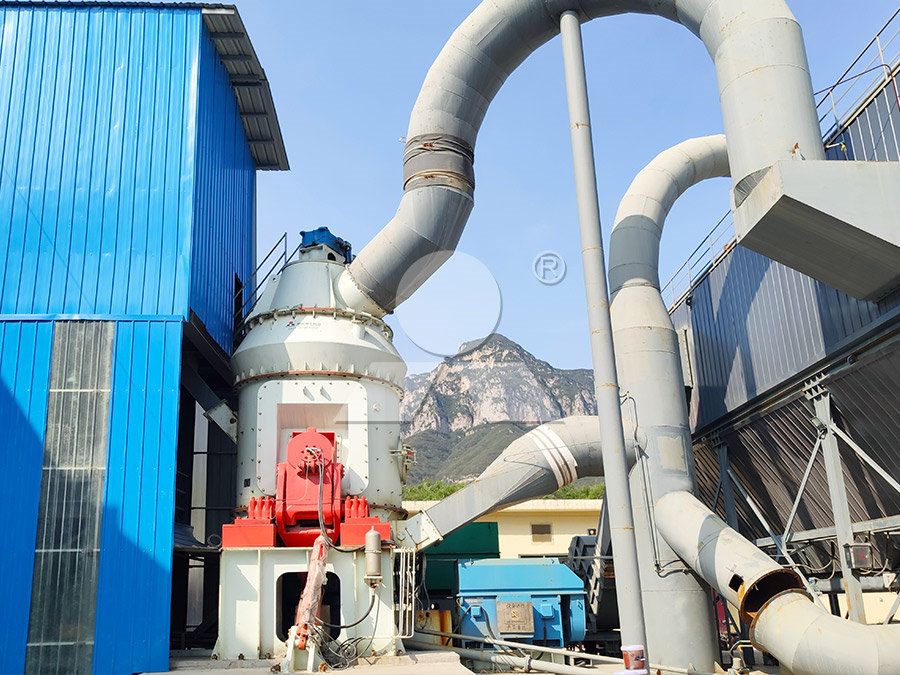
Cement Production an overview ScienceDirect Topics
Flow sheeting modeling, Pinch Analysis and mixed integer linear optimization techniques are applied to study an existing cement production facility Read more Skyonic has retrofitted a cement plant in Texas with CC In this process, the hydrated cement reacts with CO 2 The use of fossil fuels such as coal, natural gas, and oil is common in cement production, both as a fuel for the kiln and as a source of heat for other parts of the process which leads to CO2 emitted by combustionHowever chemical reactions happening in the kiln (calcination) are also responsible for up to 60% of the total of emissions of the cement production process [PCA]Cement Production Demystified: StepbyStep Process and The comparison data between the wet process cement production line and the new dry process cement production line shows that with the same rotary kiln size (diameter), the production capacity of the cement kiln which adopts the predecomposition production process increases more than 200%, the output rises from 2777kg /m3 to 20082kg /m3, and the unit heat Cement Making Process Cement Production Process Cement Plant2012年4月30日 Plant Process Flow Diagram 2 Samanta et al [2] worked on the "automation of a cement process plant" with the aim of eliminating the challenges associated with the manual operation of the plant(PDF) Process Automation of Cement Plant ResearchGate
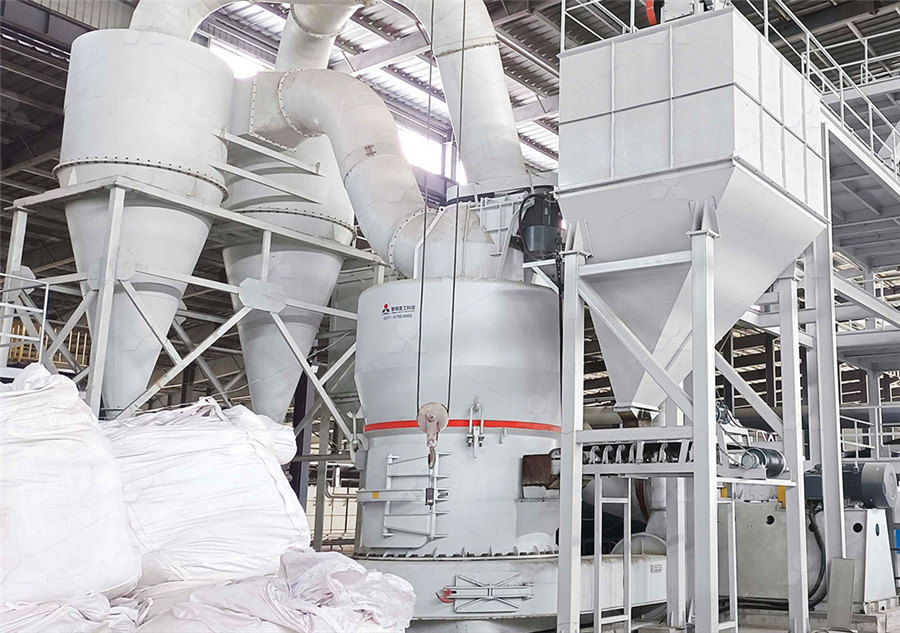
Cement processing equipment Qlar
For a new plant, this approach delivers many relevant savings Your specialist partner every step of the way With more than 80+ years of experience working with the world’s leading cement producers, we have the deep application knowhow you can count on to tailor plantwide solutions to meet your most exacting needsIt can not only grind cement clinker but also process cement admixture, such as gypsum, fly ash, furnace slag, coal gangue, etc, realizing a stable, highquality and automated cement production Unlike the cement production line , the cement grinding plant is usually established around the sales market, which saves a lot of transportation costsCement Grinding Unit Clinker Grinder AGICO CementIn addition, the required precalciner volume of tertiary air flow precalciners is less than the volume required for total flow and hybrid precalciners Examples of the currently used total flow and tertiary air flow precalciners are, respectively, the F L Smidth Co’s InLine Calciner (Figure 326), and SeparateLine Calciner (Figure 327)Everything you need to know about Preheaters and PrecalcinersClinker is the intermediate product used in the manufacturing of cement There are two primary processes used to manufacture clinker: the dry process and the wet process Our plants use the dry process, which is more energy efficient In the wet process, the raw materials are mixed with water to form slurry, which is fed into a kilnProduction Process CEMEX Philippines