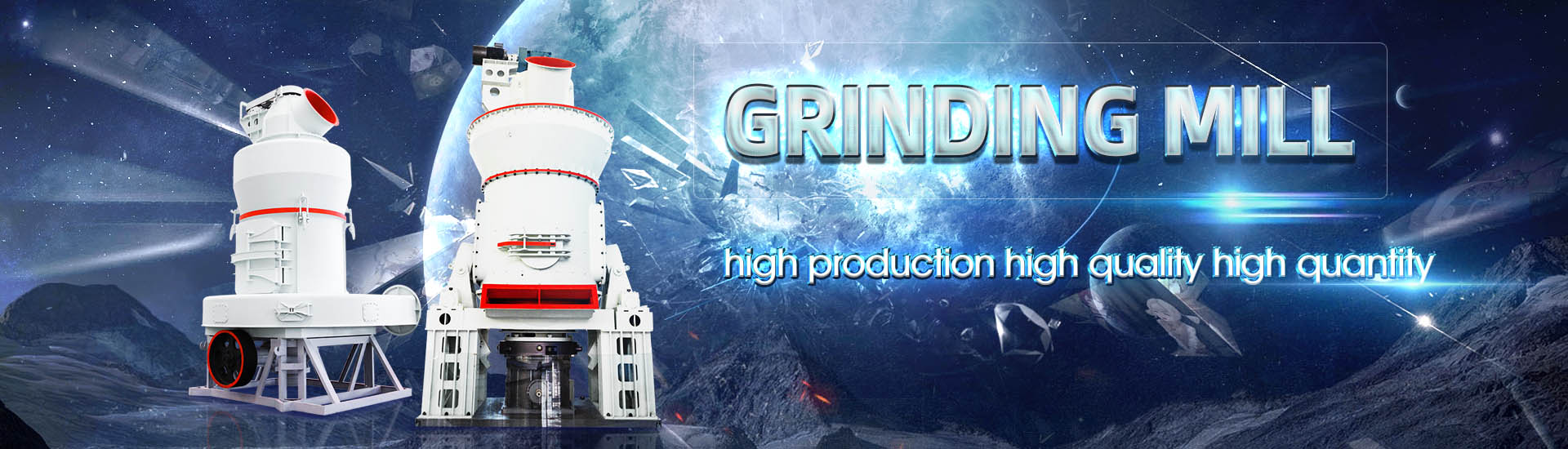
How much does it cost to overhaul the aluminum electrolytic cell slag grinding production line
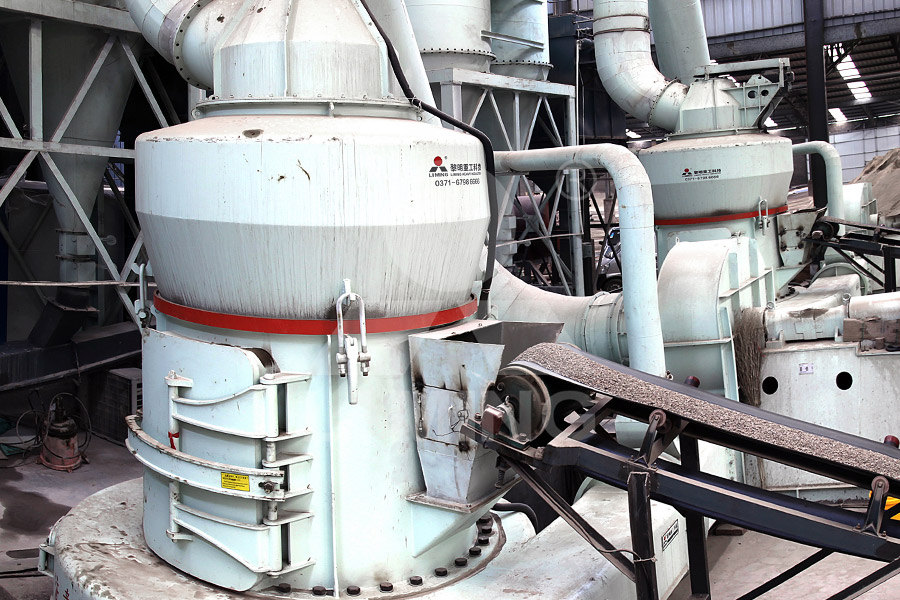
Cost breakdown of the aluminium produced
Hence, the estimated power‐to‐X cost for the Al‐based H2 is estimated in the range of 42–96 € kg–1 H2, while wind and solar power based green H2 production cost varies from 65 to 12 2021年5月5日 The cost of primary aluminum produced by electrolysis can be roughly divided into three parts, namely, raw material cost, electrical energy cost, and production management Aluminum Electrolysis Production Process SpringerLink2023年4月25日 本文以拖担水库大坝左岸中等倾角顺层滑坡为例,研究了其发育特征和形成机制,并进一步分析了该类型古滑坡体扰动复活发生滑动变形的规律和模式,对滑坡的综合治理提 Research Progress of Electrolytic Aluminum Overhaul Slag Disposal2016年10月24日 Because of the interference of multiple physics fields and the changing status of mass and energy balance, the cell status in aluminum electrolysis is quite complex Any Progress in Aluminum Electrolysis Control and Future Direction for
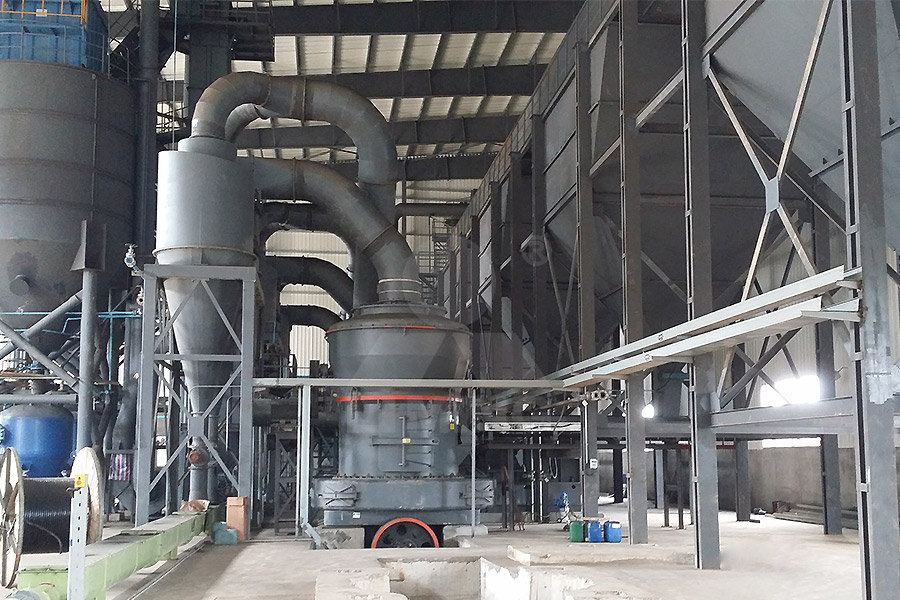
Present and future cost of alkaline and PEM electrolyser stacks
2023年10月1日 Stack costs may reduce to 52–79 €/kW (AE) and 63–234 €/kW (PEM) by 2030 Cost reductions are driven by higher current density (AEPEM) and lower catalyst loading 2018年10月1日 The world average energy use for only the electrolysis cell is 134 kWh/kg Al produced [10] If rectifiers and other cell auxiliaries, such as pollution control equipment, are Review of measures for improved energy efficiency in production 2024年5月23日 Here, we review carbonrich solid wastes with focus on sources and hazards, detoxification, separation, recovery, recycling and disposal Treatment techniques include The recycling of carbonrich solid wastes from aluminum 2023年4月13日 Aluminium is produced by electrolysis using alumina (Al 2 O 3) as raw material and cryolite (Na 3 AlF 6) as electrolyte In this Hall–Héroult process, the energy consumption A comprehensive review of aluminium electrolysis and the waste
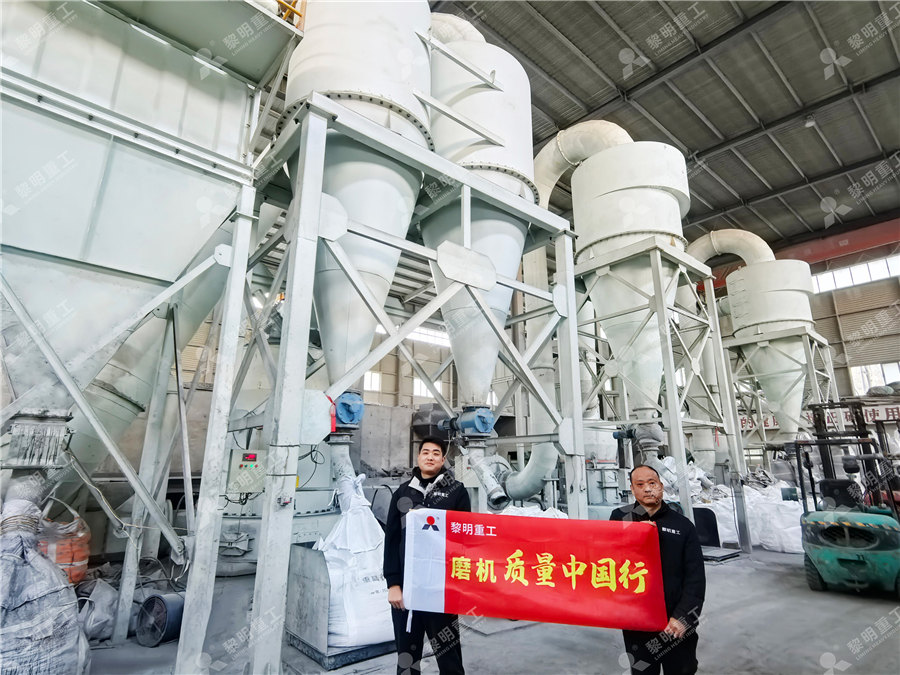
UltrahighEfficiency Aluminum Production Cells Energygov
Roughly onethird of the cost to produce aluminum from ore is associated with the use of energy and associated environmental compliance In 2003, the aluminum industry consumed more Faraday's laws of electrolysis One mole of electric charge (96,500 coulombs), when passed through a cell, will discharge half a mole of a divalent metal ion such as Cu 2 +This relation was first formulated by Faraday in 1832 in the 1610: Electrolytic Cells and Electrolysis Chemistry 2024年5月23日 The first primary source was separation recovery; the method usually results in a high purity electrolyte, and the electrolyte can be directly returned to the aluminum electrolytic cells but can only be used in the startup phase of the aluminum electrolytic (Li The recycling of carbonrich solid wastes from aluminum electrolytic 2020年1月2日 The invention discloses a fluorineretaining agent for overhaul slag of an aluminum electrolytic cell The fluorineretaining agent comprises the following components of, by mass, 80100 parts of calcium sulfate, 6080 parts of calcium oxide, 5070 parts of calcium hydroxide and 3060 parts of calcium chloride The invention further discloses a method for Fluorineretaining agent for overhaul slag of aluminum electrolytic
.jpg)
Aluminum Electrolysis Production Process SpringerLink
2021年5月5日 522 Strengthening Production Management and Extending the Effective Production Time of the Electrolytic Cells Electrolytic cells are disconnected mainly due to damaged lining and cell overhaul The cost of cells for overhaul is as high as onethird of the cost of the newly built cells2023年12月1日 U c e l l d t ∫ 0 Δ t f H 2 d t Where N cell is the number of cells that constitute the electrolysis module, f H2 is the hydrogen production rate in Nm 3 /h, and I cell and V cell are the cell current in A and voltage in V, respectively, determined for a given time interval of ΔtHydrogen production by water electrolysis technologies: A review2021年7月30日 Aluminum is the second mostconsumed metal in the world, only outranked by steel Primary aluminum is produced through the HallHeroult process1 In this process, alumina dissolves in a sodium cryolite melt, and aluminum is reduced at the aluminum liquid cathode pool while the anode products are significant amounts of \({\mathrm{CO}}{2}\) and other A Review of Secondary Aluminum Production and Its ByproductsCostcompetitive green hydrogen: 41 Energy consumption per unit of production molecules into hydrogen and oxygen2 – is well in line with net zero objectives Given this, and in order to spur the development of ‘green’ H 2, some of the nations that had previously pledged to becomeCostcompetitive green hydrogen: how to lower the cost of
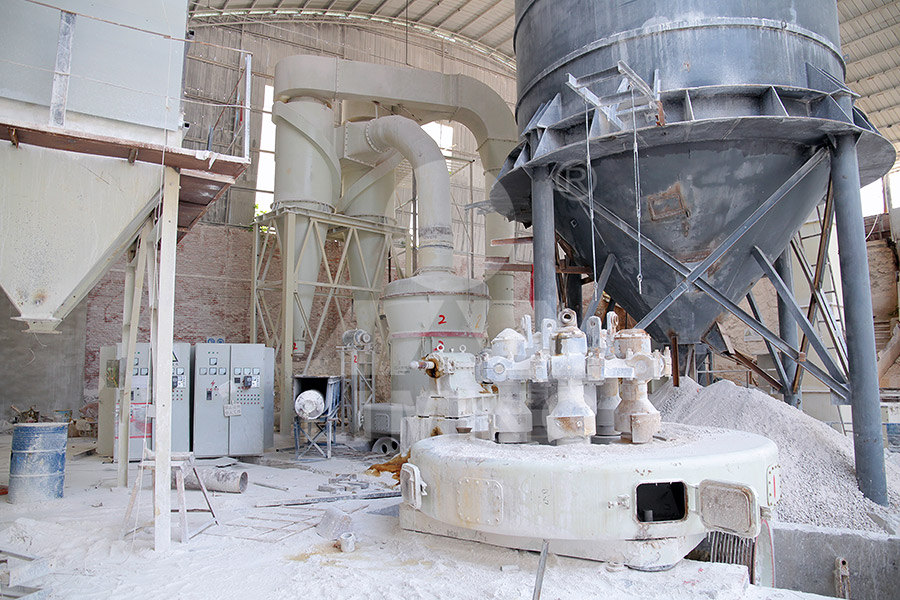
Solved 6A Practical Application of the electrolysis process
How much does it cost to generate the mass of aluminum (140 g) in one beverage can The aluminum in the can is produced by reducing Al+ to Al(s) The reaction is run commercially at 50,000 A and 40 V (40 J/C), 1 kWh ofelectricity cost about 10 cents and 1 kWh is 360 x 10s J Energy charge x voltageAluminum electrolytic capacitors are made of two aluminum foils and a paper soaked in electrolyte The anode aluminum foil is anodized to form a very thin oxide layer on one side and the unanodized aluminum acts as cathode; the anode and cathode are separated by paper soaked in electrolyte, as shown in Fig 810A and BThe oxide layer serves as a dielectric and Aluminum Electrolytic Capacitor ScienceDirect Topics2016年10月24日 The industrial aluminum reduction cell is an electrochemistry reactor that operates under high temperatures and highly corrosive conditions However, these conditions have restricted the measurement of key control parameters, making the control of aluminum reduction cells a difficult problem in the industry Because aluminum electrolysis control Progress in Aluminum Electrolysis Control and Future Direction aluminum processing, preparation of the ore for use in various products Aluminum, or aluminium (Al), is a silvery white metal with a melting point of 660 °C (1,220 °F) and a density of 27 grams per cubic cm The most abundant metallic element, it constitutes 81 percent of Earth’s crust In nature it occurs chemically combined with oxygen and other elementsAluminum processing History, Mining, Refining, Facts
.jpg)
Hydrogen Production Department of Energy
The overall challenge to hydrogen production is cost DOE's Hydrogen and Fuel Cell Technologies Office is focused on developing technologies that can produce hydrogen at $2/kg by 2026 and $1/kg by 2031 via netzerocarbon pathways, in support of the Hydrogen Energy Earthshot goal of reducing the cost of clean hydrogen by 80% to $1 per 1 kilogram in 1 decade The results show that the EU27 has the third highest production costs for hot rolled coil via the integrated route (458 EUR/t) The main contributors to these costs are the raw material costs 65%, the ‘other costs’ 27% and energy costs 17% The CO 2 cost is included in ‘other costs’ and for the EU27 represents 2% of the total production Production costs from iron and steel industry in the EU and2015年6月17日 The first article in this series [1] covered the early history of electrolytic capacitors, from their invention around 1880 to the invention of the modern Al electrolytic capacitor structure in 1925 To summarize the early history, "valve metals" were recognized in the 1880s for their ability to conduct in one direction but impede current flow in the opposite The modern era of aluminum electrolytic capacitorsIt is possible to construct a cell that does work on a chemical system by driving an electric current through the system These cells are called electrolytic cells Electrolytic cells, like galvanic cells, are composed of two halfcellsone is a reduction halfcell, the other is an oxidation halfcellElectrolytic Cells Chemistry LibreTexts
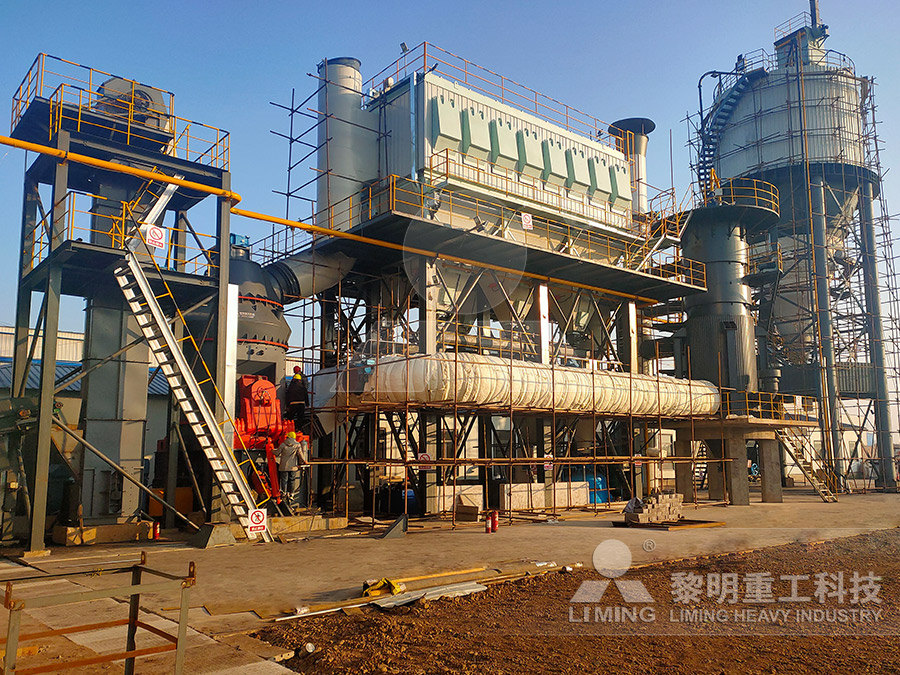
The Electrolytic Process for Aluminium Production
2013年1月1日 The industrial production of aluminium is based, since the end of the nineteenth century, on the electrolysis process Aluminium is in fact not present in the nature in its pure metallic form but as an oxide called Alumina (Al 2 O 3) and an adapted processing (electrolysis) is to be used to extract the metalAluminium electrolysis is performed in large HallHéroult cells, strategies to reduce product costs This multiple comparative case study explored the strategies used by 4 aluminum producers in Western Europe: 2 companies that have successfully reduced production costs and 2 companies that have not Wicksteed’s economic theory of production and production costs was the conceptual framework for this researchAluminum Production Costs: A Comparative Case Study of Production 2020年6月15日 The aluminum electrolytic capacitor provides a unique value in high energy storage and low device impedance Call Us Now! Toggle navigation Toggle navigation This technology keeps changing due to new ideas for materials and improvements in the production process They've become much more robust and reliable, How to Choose the Perfect Aluminum Electrolytic Capacitor2013年9月1日 A schematic of a typical aluminum electrolysis cell used for the production of aluminum is depicted in Fig 1The electrolysis process is driven by direct electric current that flows from the anodes to the liquid aluminum layer through a cryolitebased electrolyte in which alumina is dissolved [1], [2]Due to the fact that the electrolyte has a relatively low electrical Optimization of the cathode block shape of an aluminum electrolysis cell
.jpg)
Hydrogen Production Cost and Performance Analysis Energygov
production pathways • Assess the potential to meet H 2 production cost targets (H2 Shot: $1/kg of H 2 by 2031) • Evaluate the uncertainty and show the potential for H 2 cost reduction for each pathway through single and multivariable sensitivity analyses2024年5月13日 The purpose of this work is to analyze the development direction and prospects in the field of aluminum electrolysis and to provide reference information for related research and industry personnel The scientific papers on aluminum electrolysis published in Scopus database from 1970 to 2023 were collected Bibliometric methods and knowledge mapping visualization Research on Aluminum Electrolysis from 1970 to 2023: A2023年5月11日 This article describes aluminum electrolytic capacitors’ types, features, characteristics and behaviour The primary strength of aluminium electrolytic capacitors is their ability to provide a large capacitance value in a Aluminum Electrolytic Capacitors doEEEt2013年7月16日 She literally had a climb prop on one side and a cruise prop on the other I can only imagine how much smoother that engine must have seemed following the prop overhaul Overhaul of a fixedpitch propeller is also an Propeller care: Overhauls AOPA
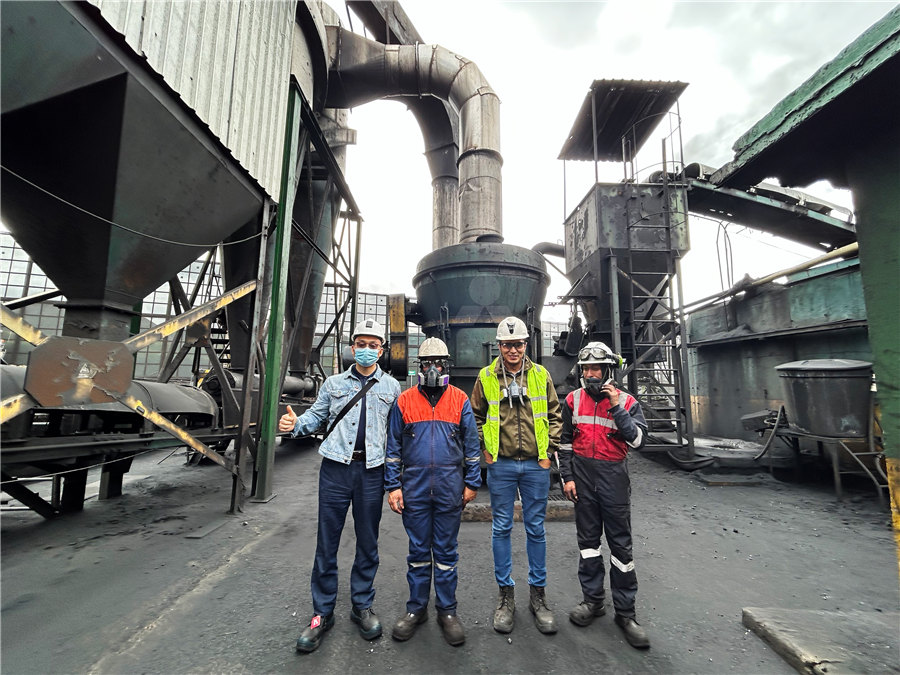
Aluminum Industry Worldwide Statistics Facts Statista
2023年12月18日 As of March 2022, the average cost of aluminum reached 3,496 US dollars per metric ton, Aluminum production processes are highly energy dependent, from mining to the final productDuring aluminum electrolysis there must be an optimum cell voltage for a given cell design at constant amperage This optimumvoltage target depends on the goal, which may change with economic conditions Although cell voltages have been reduced steadily during the last 50 years, they now seem to have reached a constant level at 41 V to 42 V, at least for cells larger than Cell voltage in aluminum electrolysis: A practical approach2011年7月15日 Some other facts about aluminium: the least efficient smelters may use as much as 20kWh/kg Al – relying on very cheap coal fired power in China, which dominates world smelting capacity, and although China does now have some modern smelters and the Three Gorges hydro electric plant and a number of nuclear stations, two thirds of it electricity comes Electricity consumption in the production of aluminium2021年2月24日 The CVD has been taken as an important judgment for cell overhaul in most aluminum electrolysis enterprises The CVD of series cells in an electrolytic aluminum enterprise began to rise rapidly from October 2016, and the average Prevention and Control Measures of the Cathode Voltage Drop
.jpg)
All About Aluminum Anodizing Xometry
2022年11月23日 Hardcoat Anodizing This type still uses sulfuric acid as the electrolyte, but it’s designed to make much thicker coatings (usually between 127μ and 508μ or 00005 and 0002in) because it uses a higher voltage, longer immersion time, and a lower bath temperature1 DOE Hydrogen and Fuel Cells Program Record Record #: 20004 Date: September 14, 2020 Title: Cost of Electrolytic Hydrogen Production with Existing Technology Originator: James Vickers, David Peterson, Katie Randolph Peer Reviewed by: Levi Irwin, Daniel DeSantis1, Monjid Hamdan2 Approved by: Ned Stetson, Eric Miller, and Sunita Satyapal Date: September 22, 2020DOE Hydrogen and Fuel Cells Program Record 20004: Cost of Electrolytic 2011年3月11日 Exergy analysis of the current industrial process for primary aluminum production, with coalbased electricity (all input and output flows are calculated at 25 C and atmospheric pressure)(PDF) Energy and Exergy Analysis of the Primary Aluminum Production By the late 1930s, a pound of aluminum cost just 20 cents; its uses numbered more than 2,000 Smelting into aluminum An electrolytic reduction process known as smelting dissolves the alumina in a cryolite bath inside carbonlined Production of Aluminum: The HallHéroult Process
.jpg)
Global land and water limits to electrolytic hydrogen production
2023年9月8日 Electrolytic production of hydrogen using lowcarbon electricity can contribute 1,2,3 to achieve netzero greenhouse gas (GHG) emission goals and keep global warming below 2 °C In 2020, global 2022年2月25日 Industrial aluminium production is based on patents filed by Charles Martin Hall (1863–1914) in the USA in July 1886 [] and Paul Louis Toussaint Héroult (1863–1914) in France in April 1886 [] (Fig 2)Both developed similar principles to produce aluminium, namely, alumina (Al 2 O 3) dissolved in a cryolite (Na 3 AlF 6)based molten salt electrolyte, commonly called Aluminium production process: from Hall–Héroult to modern 2024年2月1日 Aluminum metal was produced using the cryolitealumina molten salt electrolysis method (Ishak et al, 2017)A large amount electrolytic aluminum slag (EAS) is generated during the electrolysis process, as the falling of carbon particles on the anode into the electrolysis cells and the accumulation of lithium fluorine result in energy consumption and electrolyte scrapping Efficient lithium recovery from electrolytic aluminum slag via an Electrolytic Cells If we construct an electrochemical cell in which one electrode is copper metal immersed in a 1 M Cu 2 + solution and the other electrode is cadmium metal immersed in a \(\,1\; M\, Cd^{2+}\) solution and then close the circuit, the potential difference between the two compartments will be 074 V The cadmium electrode will begin to dissolve (Cd is oxidized to 209: Electrolysis Chemistry LibreTexts
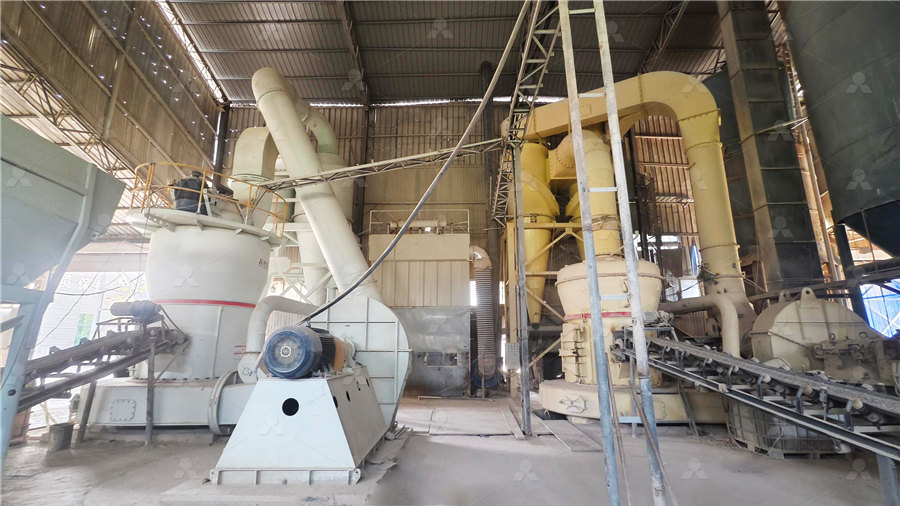
Electrolytic production of aluminium as a case study for linking
2023年12月4日 And they should arrive at the conclusion that 2945 million US$ are needed “to pay the energy bill” of the electrolytic process only We find that if the students calculate themselves the high electricity costs involved in electrolytic production, the realization that electrolytic production is an energyintensive process will be more acute2014年5月1日 For many years, efforts have been made to find alternative smelting technologies to replace the centuriesold energyintensive HallHéroult process (Cochran, 2016;Kvande and Drablos, 2014)(PDF) The Aluminum Smelting Process and InnovativeElectrolytic Cells – Core Concepts In this tutorial, we will learn about a second type of electrochemical cell: electrolytic cellsWe will also learn broadly about the concept of electrolysis, how it applies to electrolytic cells and chemistry, and its realworld applicationsYou will also learn the difference between galvanic cells (like a battery) and electrolytic cellsElectrolytic Cells and Electrolysis ChemTalk2023年10月1日 Research has been conducted on expected electrolyser system cost decline by 2030 Topdown analysis was conducted by Schmidt [5] using an expert elicitation process involving academic and industrial expertsExperience curve approach was used by Schoots [[6], [7], [8]], and [9]A bottomup approach was used by Mayyas [10] to estimate 200 kW and 1 Present and future cost of alkaline and PEM electrolyser stacks
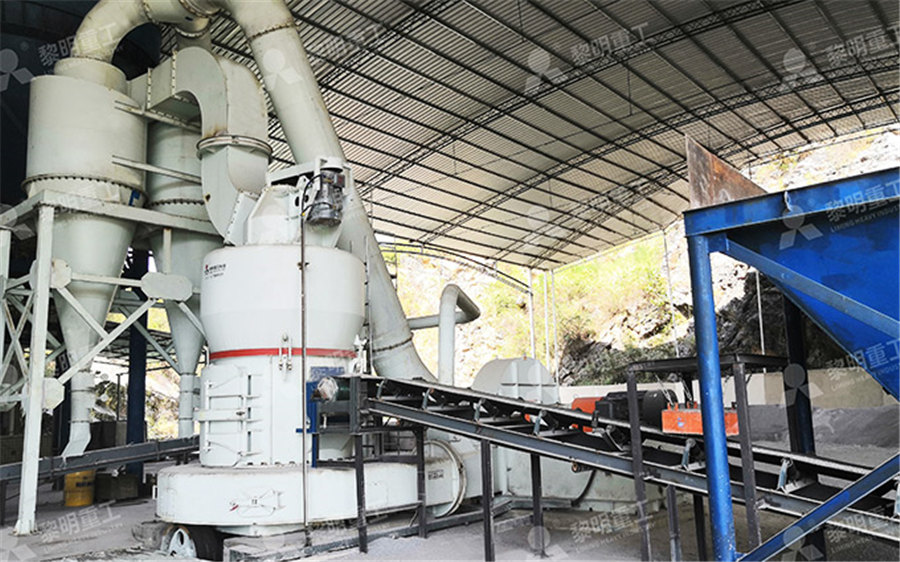
How to Recondition (Reform) Electrolytic Capacitors and Why
2015年11月22日 Used capacitors that came from a circuit, where the operating voltage was much lower than the rated voltage of the capacitor Example: 63V electrolytic caps that were used on the CPU filter output of a motherboard (where the working voltage is often less than 1/3 to 1/4 of the rated voltage) Why should electrolytic capacitors be reformed?