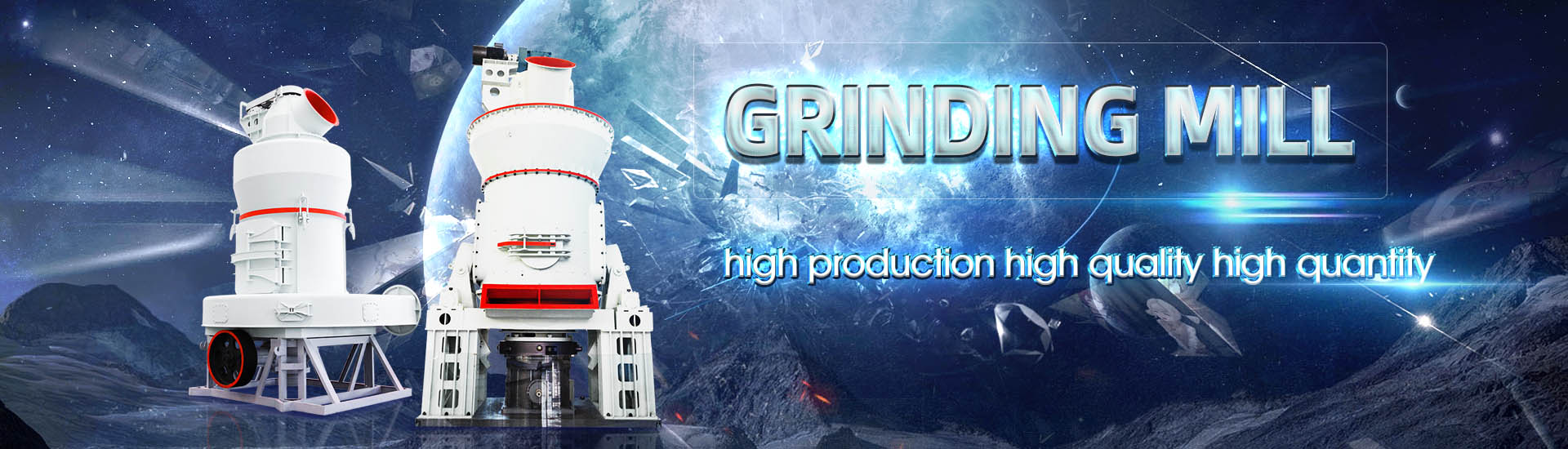
Coal mill co monitoring device bid
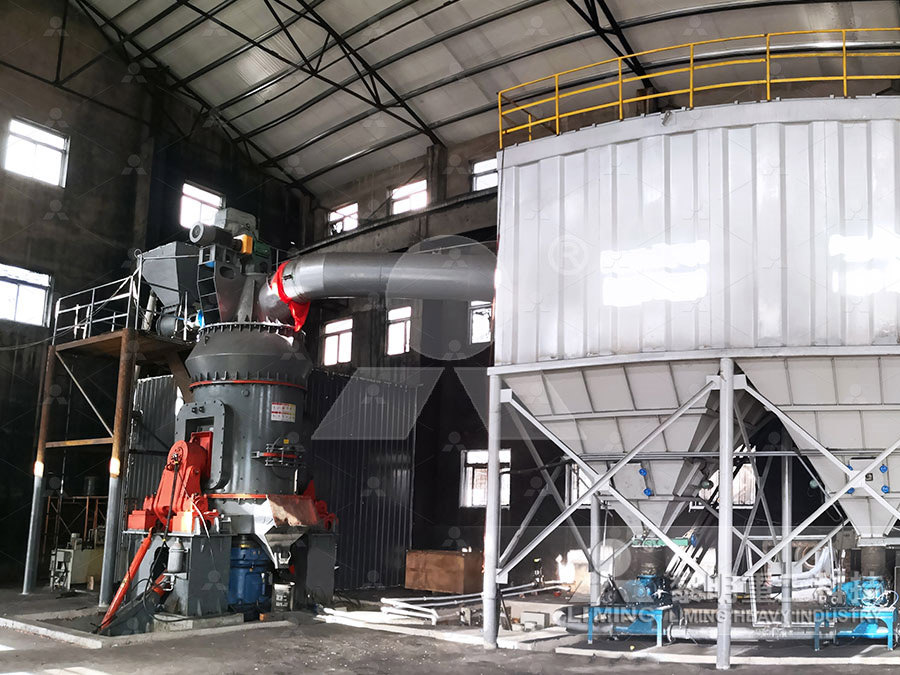
Coal Mill Monitoring CODEL International LTD
CODEL’s products for coal mill monitoring offer advanced technology and reliable performance to meet the stringent demands of coalfired power plants With continuous CO monitoring, CODEL’s systems provide realtime data on gas Specifically designed for early detection of potential fire risk in pulverizing mills in coal or biomass processes, Millwatch monitors and quickly responds to sudden carbon monoxide (CO) buildup, allowing preventative action to be taken Millwatch: Coal and Biomass Mills Carbon Monoxide Coal mill monitoring is essential for ensuring the safe and efficient operation of coal mills Monitoring carbon monoxide (CO) levels is particularly important as it helps detect and prevent Coal Mill Monitoring CODEL International LTDComplete range of Coal Mill monitors using EC and IR technology Early detection of fires in coal pulverising mills is essential to avoid catastrophic damage to plant and to avert the threat of injury to personnelCO Mill Fire Monitoring Systems CODEL International
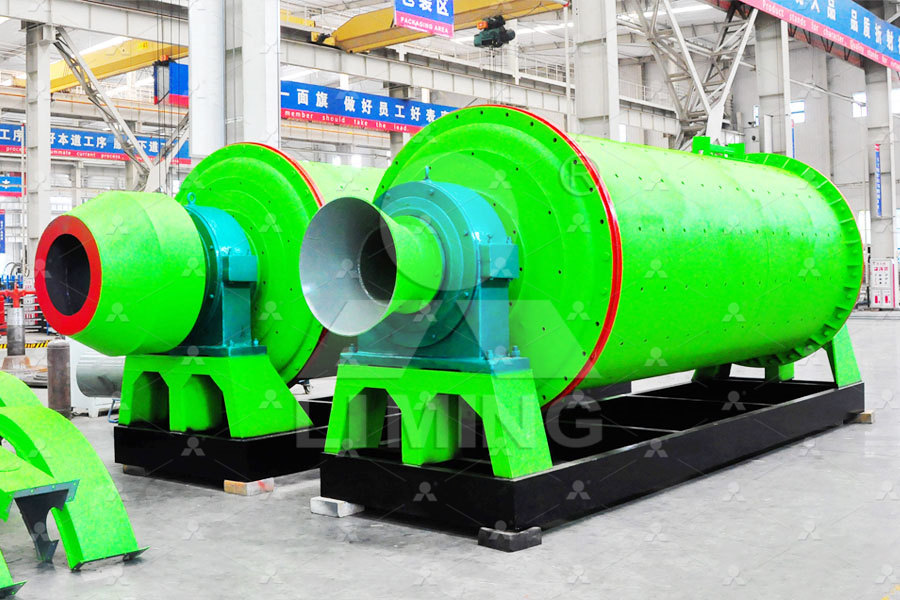
CoalMill Millfire CO Analyser Codel International PDF Catalogs
Detection and measurement of carbon monoxide levels produced by combustion within the mill is a proven method of detection of coal mill fires Any such system must be capable of detecting MONITORING COAL MILLS Specifically designed for coal mills Sensitive 2 ppm detection limit Automatic calibration verification Rugged sample probe with abrasion shield, largearea filter COALFIRED POWER PLANTS Land Instruments InternationalThe most reliable and accurate method of detecting coal fires or smouldering is to monitor the carbon monoxide levels within the coal handling plant areas such as silos and mills and to detect rapid increases in concentrationCO measurement in coal millsCarbon monoxide (CO) and oxygen (O2) measurement in the coal pulverizer is important for early warning of a smoldering fire and/or a leak in the inertization system The MKAS analyzer Protecting the coal mill by monitoring CO and O2
.jpg)
Silowatch: Coal and Biomass Storage Silos CO Detector
Silowatch provides fast, accurate monitoring of CO in the silo, using AMETEK Land’s unique dualsensor detection system The detection of sudden CO buildup enables operators to act quickly, protecting your personnel, securing CO Monitoring Industrialquality carbon monoxide monitors can be used as complete, standalone equipment or can be integrated into preexisting PLC or SCADA networks Real life experience Prevention of Fires in CoalHandling Facilities: Continuous A simple energy balance model of the coal mill is derived in (Odgaard and Mataji 2006), this model is based on a more detailed model found in (Rees and Fan 2003)In this model the coal mill is seen as one body with the mass m mThe following variables are defined: T(t) is the temperature in the coal dust flow in the mill, ṁ PA (t) is the primary air mass flow, T PA (t) is Coal Mill an overview ScienceDirect TopicsAlbinger and Smoker/CO Monitoring Page 2 Thermal Monitoring and IR Scanning All power plants must have some type of riskmanagement system to mitigate the possibility of fire A proactive approach to fire prevention focuses not so much on detecting smoke, which indicates fire, but rather on monitoring CO, which indicates thePrevention of Fires in CoalHandling Facilities: Continuous Monitoring

Fire Detection Methods for Coal Pulverizer Systems Babcock
Carbon Monoxide Monitoring CO monitoring samples the fuel/ air mixture generally near the classifier exit After a baseline of normal level of CO is determined, a rise in the CO level is interpreted as a pocket of smoldering coal Without com plete combustion, a smoldering pocket of fuel will produce CO This type of monitoring has proven main tenance state of eac h mill 2 CO AL MILL MODELING The MPC con troller for coal mills is based on a nonlinear ph ysical mo del to describ e the grinding, drying, and separation pro cesses o ccurring in typical coal mill pulv erizers Similar mo dels ha ve b een describ ed b y F an and Rees [1994], Zhou et al [2000] and Niemczyk et al Coal Mill Modeling for Monitoring and ControlWorldwide Support Over 25 distributors and support centres worldwide Flexible maintenance contracts Tailor made plant specific contracts with 24Hr Support 30 years experience Developing, manufacturing and installing Getting the Design Right for a Reliable CO Mill Fire Monitoring System Potential coal fires and coalinduced explosions in a coal handling system pose Getting the Design Right for a Reliable CO Mill Fire Monitoring COAL HANDLING Protecting the coal mill by monitoring CO and O 2 CO and O 2 measurement in the coal mill is important for early warning of a smoldering fire and/or a leak in the inerting system The MKAS analyzer system equipped with an explosionprotected sampling probe is the ideal solution for this The MKAS can be configured to sequentiallyPOWER SICK
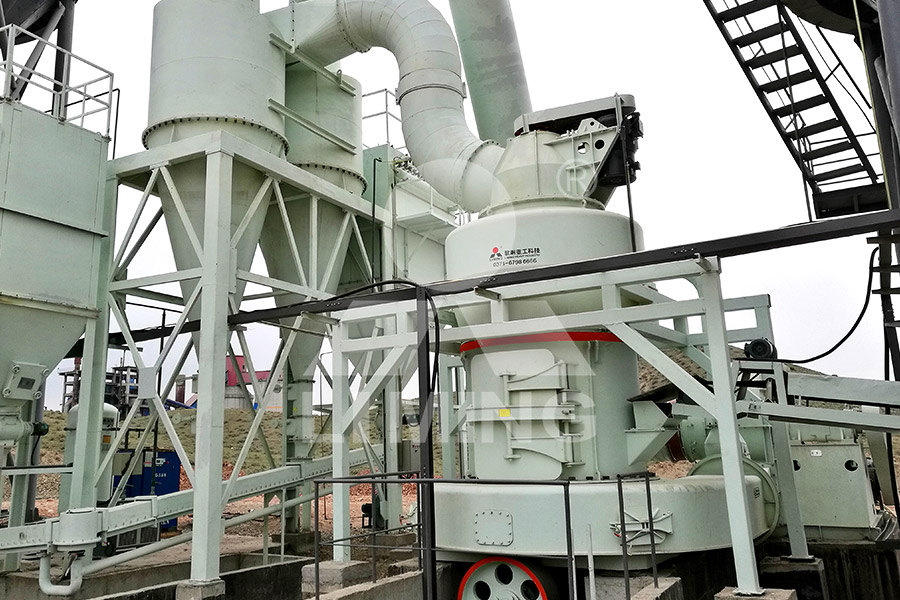
In discussion: Coal Mill Safety Coal Mill Safety, Explosion and
In discussion: Coal Mill Safety At best, coal mill safety is not well understood and, at worst, it is ignored When it comes to coal mill systems, most cement plant operators just presume that the supplier of the equipment knows all of the standards and rules and is 100% capable of making a system that conforms to these and is therefore safe2001年5月18日 The addition of CO monitoring offers significant advantages in such conditions When choosing to monitor and control using CO, it is important to take account of other operational factors Selection of technology also needs to be carefully considered Combined monitoring of O2 and CO has been shown to offer optimal combustion controlImproving combustion efficiency by incorporating CO monitoringCO Mill Fire Monitoring, getting the design right for a reliable CO measurement for the early detection of fires Saltar al contenido +44 (0)1629 CO Mill Fire Monitoring Systems CODEL International LTDVertical Coal Mill (VCM) is equipment for grinding and pulverizing coal into micron size Rotary kilns then use the powders as fuel burners The VCM has a housing section equipped with a lining The layout of the coal mill with a rotary classifier
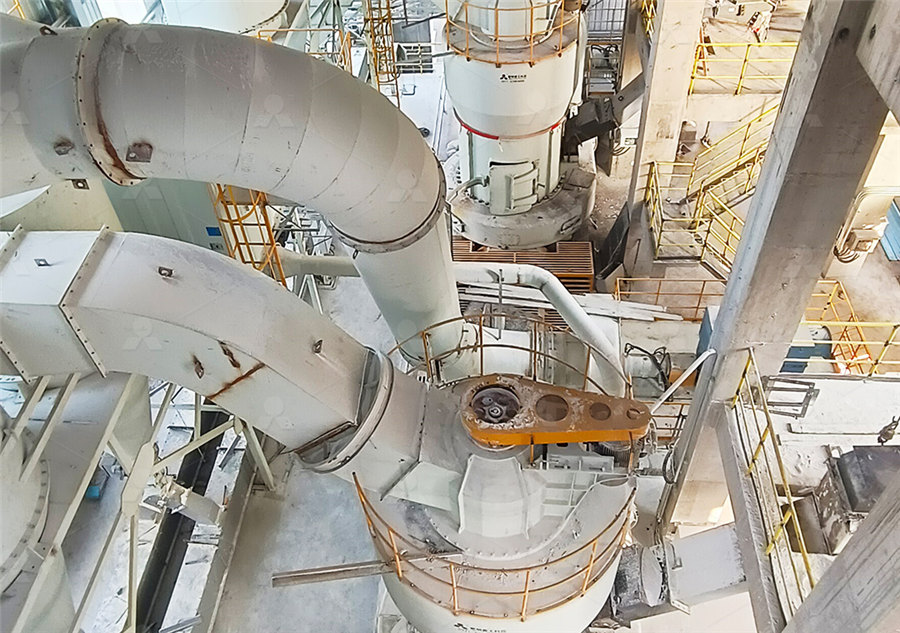
Measurement Solutions in Coalfired Power Plants
2010年11月1日 Inside pulverizing coal mills and silos, carbon moNO X ide (CO) monitoring provides earlier detection of combustion to prevent mill firesThese detection systems are specifically designed to CO Mill Fire Monitoring, getting the design right for a reliable CO measurement for the early detection of fires Pular para o conteúdo +44 (0)1629 CO Mill Fire Monitoring Systems CODEL International LTD2019年1月1日 The work in this part is based on a ZGM113N medium speed coal mill equipped in a subcritical 600MW unit Combined with existing research [1, 53] and relevant theoretical knowledge [54], 15 Abnormal Condition Monitoring and Diagnosis for Even in routine mill shutdowns, there is a danger that any residual coal left within the mill will oxidise, and may explode as the mill is restarted The Millwatch system is installed near the classifier and can detect the CO emitted from any hot inclusions within the residual coal With many baseload plants nowCOAL HANDLING SAFETY Land Instruments International
.jpg)
An investigation of performance characteristics and energetic
2020年8月12日 Ultimately, the energetic efficiency of coal mill has been investigated and performance value has been found to be a maximum value of 962% KEYWORDS: Vertical roller coal mill; energetic performance; coalfired power plant; Co =: Coal outlet M =: Motor CLS =: Classifier Log in via your institution Access through your institution2006年6月1日 null Typical Point Level Applications (LS1) Empty Belt Detection – Coal is transported using conveyor belts In order to ensure continuous operation, the belt should have coal on it at all timesLevel Measurement Solutions for Coal Handling ApplicationsCEMS monitoring (Continuous Emissions Monitoring) is crucial in power plants, including coalfired, gasfired, and oilfired facilities, to continuously measure and report emissions of pollutants such as sulfur dioxide (SO2), nitrogen oxides (NOx), particulate matter CEMS Monitoring CODEL International LTD2023年5月8日 The disturbance occurs because it operates using LowRank Call (LRC) coal with high moisture, causing the changing in the operating pattern of the coal pulverizer mill, such as the coal flow rate setting and primary airCoal pulverizer mill system modeling for failure simulation
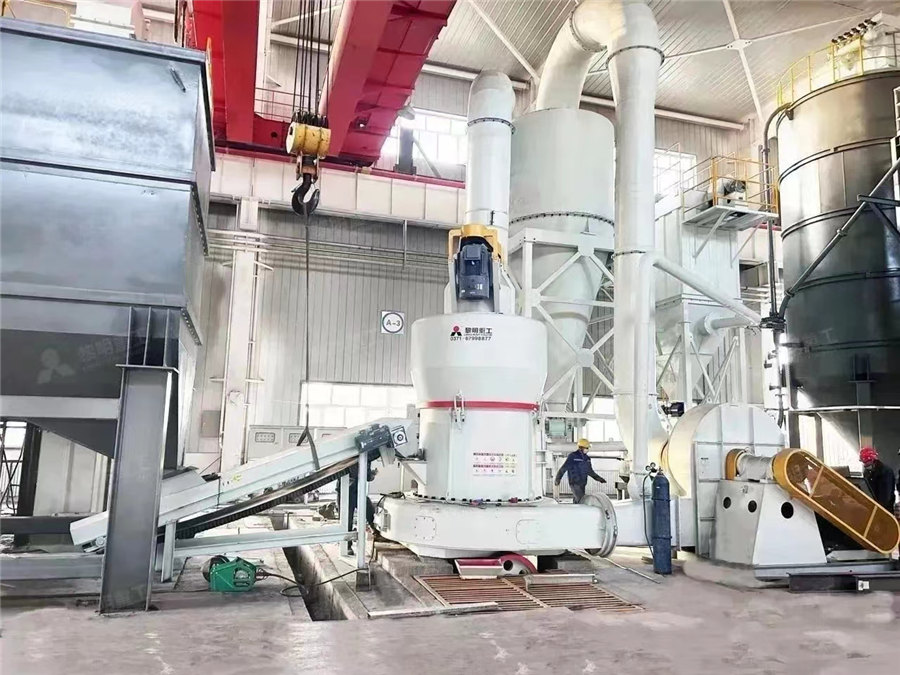
Monitoring Coal mill Performance PPT SlideShare
2019年5月10日 • In pulverized coal combustion, the ratio of coal to carrying gas is usually in the range of y = 0506 kg/kg • Assuming a coal density rc = 15 x 103 kg/m3, and the density of the carrying gas as rg = 09 kg/m 3, the volume fraction of OF CO IN A HORIZONTAL OR VERTICALAXIS MILL Millwatch detects the rapid buildup of CO in a horizontal or verticalaxis mill, giving a continuous indication of the CO MONITORING COAL STORAGE SILOS Specifically designed for storage silos Sensitive, 2 ppm detection limit Automatic calibration verification Optional O 2COALFIRED POWER PLANTS Land Instruments International2023年5月23日 The device is in the observation state when the HI value is between 80 and 90, which indicates that the coal mill may have worn components or be in the early stage of fault, and the operator should be concerned about Health indicator construction and application of coal 2023年6月18日 Underground coal mine environment is hazardous and accident prone The present work proposes an internet of things (IoT) based smart under ground mine monitoring system at the excavation site The developed system establishes a communication link to enable data transmission between underground smart devices and above the ground monitoring IoT and LoRa based smart underground coal mine monitoring
.jpg)
Ministry of Coal, Government of India
2024年10月25日 This is the official website of Coal Ministry, Government of India You can find information related Tenders, (Bid GEM/2024/B/)885 KB (12/11/2024) National Coal Index Base year 20172018 Coal Import Monitoring System Photo Gallery View more Footer menu Website Policy; Help; Contact Us; Terms and Conditions;of the filter for monitoring the grinding plant CO and temperature are monitored in the pulverized coal silo If the preset limits of CO and O 2 concen tration are reached, the safety systems, such as safety dampers, CO 2 inertization of the mill, filter and silo are activated 4 Rating of MPS mills for coal grindingReprint from ZKG 3 Gebr PfeifferWorldwide Support Over 25 distributors and support centres worldwide Flexible maintenance contracts Tailor made plant specific contracts with 24Hr Support 30 years experience Developing, manufacturing and installing Getting the Design Right for a Reliable CO Mill Fire Monitoring System Potential coal fires and coalinduced explosions in a coal handling system pose Getting the Design Right for a Reliable CO Mill Fire Monitoring The coal mill grinding system is an important part of the dry process cement manufacturing In cement plants, we usually adopt the air swept coal mill system or vertical mill system as the pulverized coal preparation system, which is arranged at the cement kiln head or kiln tail to provide fuel for clinker calcination However, due to the flammable and explosive Coal Mill – Coal Mill In Cement Plant AGICO Cement Equipment
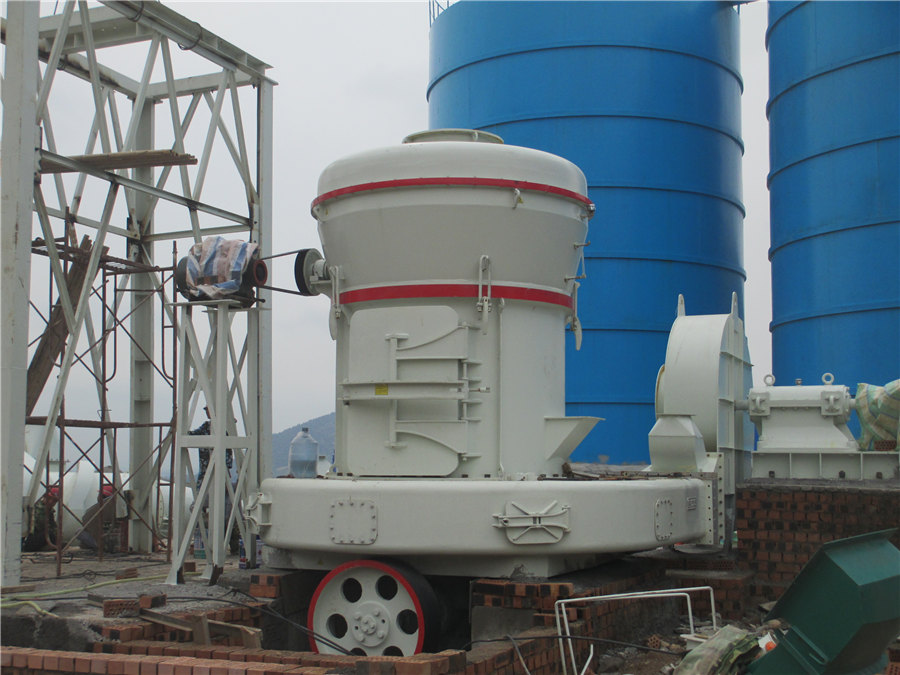
Modeling of Coal Mill System Used for Fault Simulation MDPI
2020年4月7日 Monitoring and diagnosis of coal mill systems are critical to the security operation of power plants The traditional datadriven fault diagnosis methods often result in low fault recognition rate or even misjudgment due to the imbalance between fault data samples and normal data samples In order to obtain massive fault sample data effectively, based on the to avoid coal dust deposits • pressure shockresistant design of mill and classifier housing, filter and pulverised coal silos • use of rapidaction flaps, rupture disks and explosion vents in certain parts of the plant • monitoring of O2, CO and dust concentration levels in critical places • supply of CO2 in the event of safetyCOAL GRINDING IMPS: more than meets the eye Gebr PfeifferCODEL’s range of gas monitors for stack emissions are suitable for a wide variety of processes offering measurements of CO, NO, SO2, CO2, NO2, CH4, HCL and H2O Our multichannel stack emission monitors operate as fully integrated and automated CEMS systems or as standalone process control gas monitorsCEMS Gas Monitors Stack Analysers CODEL International LTDMechanisms for monitoring of mine environment used currently in mines under CIL(Coal India Limited): Detection of mine gases by using a Methanometer, COdetector, Multigas detector etc Continuous monitoring of mine environment by installing Environmental TeleMonitoring System (ETMS) Local Methane Detectors (LMD) etcSurvey On Coal Mine Safety Monitoring Systems Seventh Sense
.jpg)
Modeling and Parameter Identification of Coal Mill
2009年9月20日 A control oriented model was then developed by Fan (1994) and Fan and Rees (1994) In 2009, coal flow and outlet temperature of mill were modelled using mass and heat balance equations for startup 2016年8月1日 It is shown herein that the mill throughput can be monitored online using a simple mill energy balance that successfully predicts the coal throughput within 233% as compared to a calibrated coal (PDF) Mass flow and particle size monitoring of 2010年12月31日 Specifically, this case study covers the following topics: 1)coal mill operational and maintenance problem identification; 2)sensing and data acquisition system design and implementation; 3)mill 10 Advanced monitoring and process control technology for coal in the coal surge bin In a typical coal power plant, lignite (soft coal) and anthracite (hard coal) are stored temporarily in bins up to 30 meters high To ensure that the coal belts are continuously loaded without interruption, a robust and reliable level measuring system is required Additional point level detectors are used toLevel and pressure instrumentation for energy production
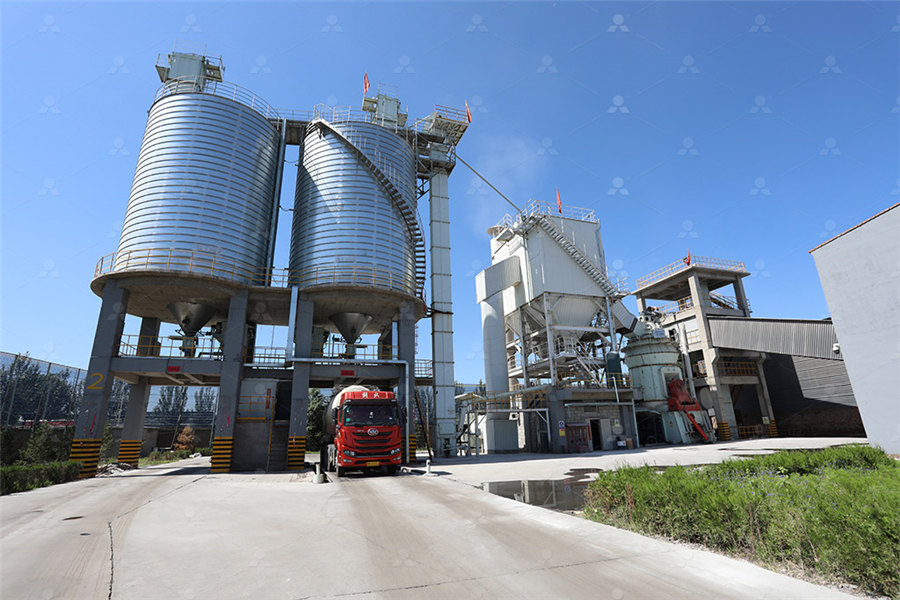
132 Loesche Mills For Solid Fuels Coal Mill E 2016
132 Loesche Mills for Solid Fuels Coal Mill E 2016 Free download as PDF File (pdf), Text File (txt) or read online for free Loesche has been involved in processing solid fuels since 1925 Some key events include delivering their first coal mill in 1927 and introducing hydraulic systems in 1961 Their mills are distinguished by grinding without metal contact, suitability for Coal Mill Safety Pte Ltd introduction(12) Evaluating the fire and explosion safety of systems with all kinds of ‘engineering culture’ backgrounds on all continents has led to the understanding described below The following is an analysis after many years of work in the cement industry and with technologyAccept the probability that the fire and explosion safety of your coal 2022年8月4日 1 International Journal of Trend in Scientific Research and Development (IJTSRD) Volume 6 Issue 4, MayJune 2022 Available Online: ijtsrd eISSN: 2456 – 6470 @ IJTSRD Unique Paper ID – IJTSRD50274 Volume – 6 Issue – 4 MayJune 2022 Page 1093 Coal Mine Safety Monitoring and Alerting System using IOT Based R Karthick1 Coal Mine Safety Monitoring and Alerting System using IOT Based2020年4月7日 PDF Monitoring and diagnosis of coal mill systems are critical to the security operation of power plants The traditional datadriven fault diagnosis Find, read and cite all the research Modeling of Coal Mill System Used for Fault Simulation
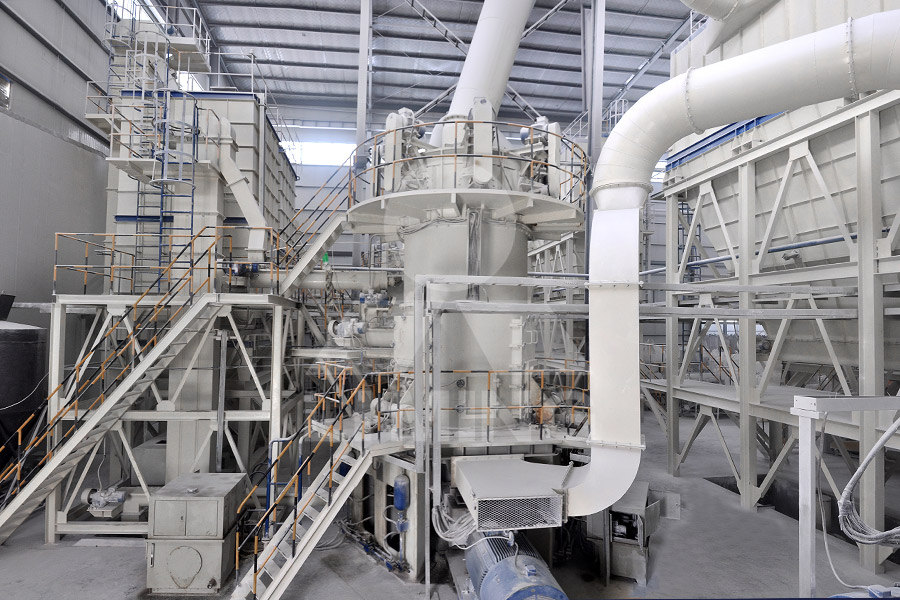
The monitoring indicator of coal mill under normal condition
In this study, a new method of construction of the coal mill health indicator (HI) is proposed, and the operation condition monitoring approaches of the device are designed based on the HI value2016年1月1日 Download Citation Coal mill explosionproof monitoring system design and development Based on the actual operation of the simulation data and adopted PLC program control, it can become an Coal mill explosionproof monitoring system design and