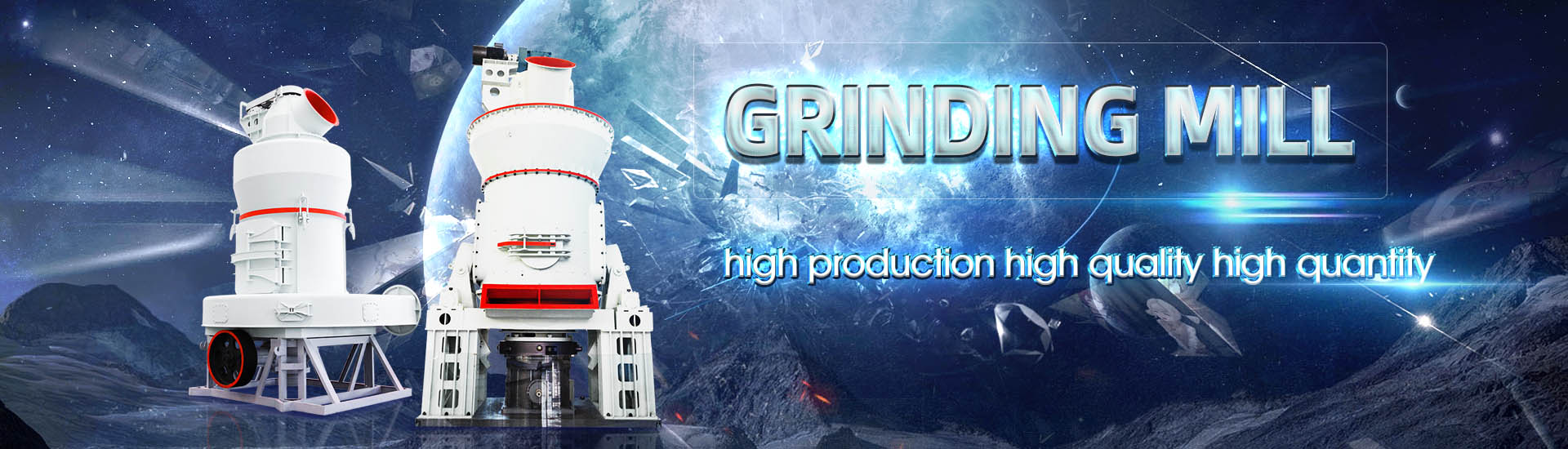
Reverse ore mill
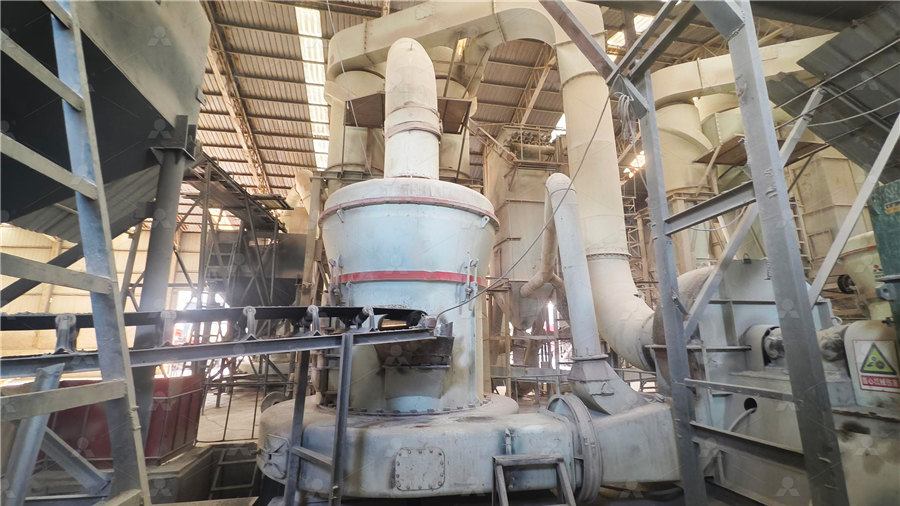
钢铁可逆冷轧机 SMS group GmbH
用于非连续性冷轧生产的穿带和甩尾辅助系统,以最大限度地减少带钢厚度超差重量和/或超差长度,从而显著提高产量。 我们推出了XPact ® TRC ®,作为XPact ® 自动化系统中工艺控制包的一部分。 它可大幅减少超差长度和重量,提高非 Reversing Cold Mills (RCM) are the ideal plant type for an annual production in the range of 100,000 to 500,000 tons They can roll a wide range of steel grades Reversing cold mills are also a good solution for demanding silicon or Reversing cold mills for steel SMS group GmbHThere has been developed a new rolling method and facility (ZoomMillTM, ZeroOriented Offgauge Minimization) that allows a leader strip and a product coil are connected using a spot New Rolling Method Of Reversing Cold Rolling Mill Steel Plantech2023年8月1日 Reverse cationic flotation, which involves the flotation of the gangue mineral, is the most widely used method of fine iron ore beneficiation (Filippov et al, 2014) Amines are Transforming iron ore processing ScienceDirect
.jpg)
New Rolling Method R f Reversing Cold Rolling Mill Steel Plantech
reversing cold rolling mill, which takes relatively inexpensive capital investment, is put into use The reversing cold rollin g mill is used mainly for producing coils of normal carbon steel in Accordingly, a typical beneficiation circuit includes a fourstaged crushing/screening plant, followed by grinding in a closedcircuit ball mill, desliming in hydrocyclones and final ore Transforming iron ore processing – Simplifying the comminution Traditionally, the hot reversing mill stays idle during a cropping operation, which in turn negatively affects the mill cycle time In view of these issues, described herein are improved systems and SYSTEMS AND METHODS FOR TWO INGOT ROLLING 2023年8月1日 Reverse cationic flotation, which involves the flotation of the gangue mineral, is the most widely used method of fine iron ore beneficiation (Filippov et al, 2014) Amines are Transforming iron ore processing – Simplifying the comminution
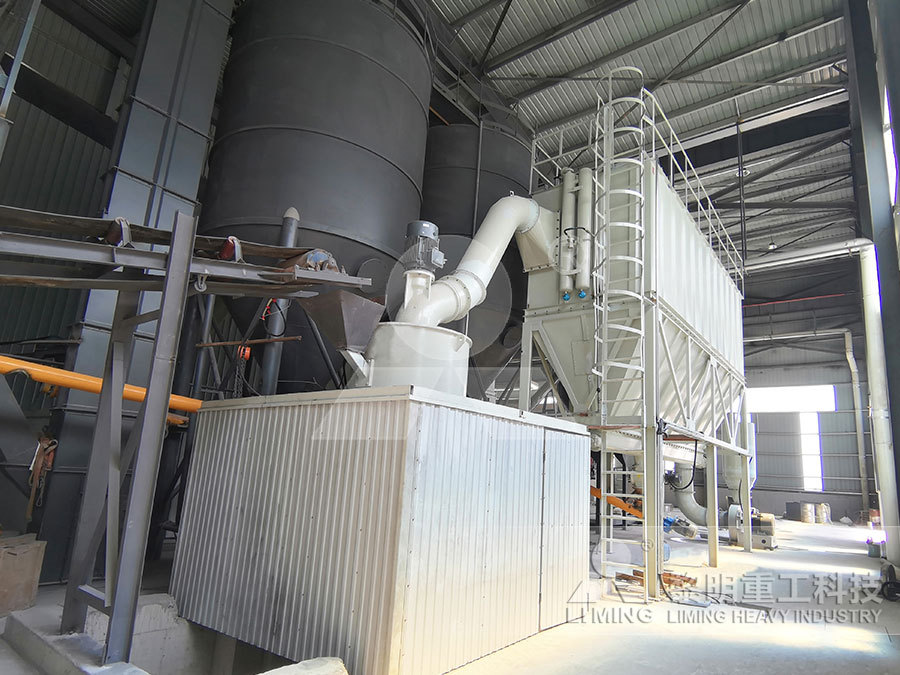
Transforming iron ore processing Simplifying the comminution
Reverse cationic flotation, which involves the flotation of the gangue mineral, is the most widely used method of fine iron ore beneficiation (Filippov et al, 2014) Amines are employed as 2023年4月27日 The overflow ball mill can grind iron ore, copper ore, ferrous metal, and nonferrous metal, and is very popular in metallurgy, building materials, construction, the chemical industry, and other fields It belongs to How an Overflow Ball Mill Works? JXSC MineralWatermill of BraineleChâteau, Belgium (12th century) Interior of the Lyme Regis watermill, UK (14th century) A watermill or water mill is a mill that uses hydropowerIt is a structure that uses a water wheel or water turbine to drive a Watermill Wikipedia2022年5月13日 Figure 52: Zeta Potential of hematite ore at increasing concentrations of Magnesium, Calcium, Barium, and Strontium 111 Figure 53: Sampling location at the iron ore concentrator plant: autogenous mill screen underflow, right before dispersant additionMichigan Technological University Digital Commons @ Michigan
.jpg)
EFFECTS OF MAGNETIC FLOCCULATION ON IRONBEARING ORE
2021年8月1日 Successful upgradation of lowgrade iron ore fines through reverse flotation route with proposed reagent regimes is envisaged (HNMPC) is developed for a runofmine ore grinding mill circuit2009年8月1日 Mill scale is an iron oxide waste generated during steelmaking, casting and rolling Total generation of mill scale at JSWSL is around 150 t/day and contains 60–70%FeO and 30–35%Fe2O3Recycling of steel plant mill scale via iron ore ResearchGateAmphiboleType Oxidized Iron Ore via Reverse Anionic Flotation Processes 2023 hematite was ground to 0074 mm with a ceramic ball mill, and qualified single hematite minerals of the Flotation Characteristics of AmphiboleType Oxidized Iron Ore via 2018年12月1日 Analysis of reverse cationic iron ore fines flotation using RSMDoptimal design – An approach towards sustainability @article{Pattanaik2018AnalysisOR A Comparative Study on a Vertical Stirred Mill Agitator Design for Fine Grinding C Eswaraiah N Venkat Bijay K Mishra R Holmes Engineering, Environmental ScienceAnalysis of reverse cationic iron ore fines flotation using RSMD
.jpg)
Comminution Theory Process Equipment 911Metallurgist
2016年10月21日 This page is devoted to the subject “From the Comminution Theory to Practice by selection of the correct Process Equipment” by taking you step by step through some of the variables encountered in the specific part of Comminution called grinding and how each of these affect your operations Should it be possible to reduce all of these variables to a simple Understanding Mine to Mill is presented in five parts Part A – Setting the Scene provides some definitions of Mine to Mill (M2M) and the historical background A chronology of Mine to Mill developments is followed by brief descriptions of the very wide range of Mine to Mill applications which have been implemented over the last 15 yearsUNDErsTaNDINg MINE TO MILL 911 MetallurgistTransforming iron ore processing followed by grinding in a closedcircuit ball mill, desliming in hydrocyclones and final ore mineral concentration via multistage reverse flotation and thickening of the final product With the need for decarbonisation in the iron and steelmaking industry, Transforming iron ore processing – Simplifying the comminution A magnetite bearing ore is liberated in a milling circuit prior to concentration; the circuit consistsof a ball mill, a discharge sump and a slurry pump followed by a hydrocyclone classifier Freshore that is fed to the mill has a moisture content of 5% and consists of 85% of class 1 (dry basis)which has a representative size of 600 microns, 10% ofSolved A magnetite bearing ore is liberated in a milling Chegg
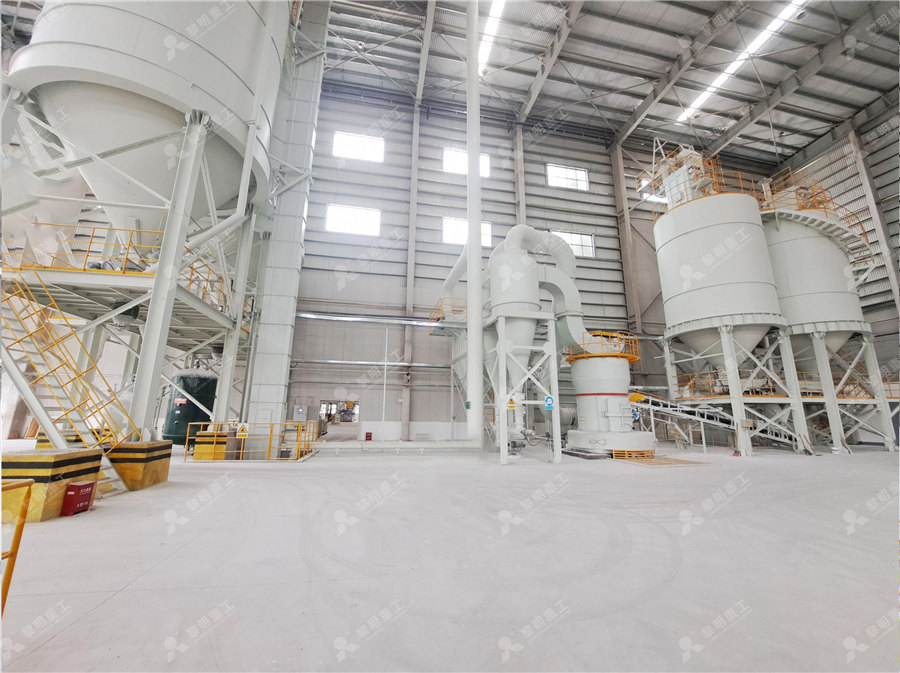
Grinding Mills Harcliff
Orespecific ball charge trajectory simulations; Mechanical 3D computer modelling; All drive trains are designed and constructed in accordance with American Gear Manufacturing Association (AGMA) standards and 2023年6月16日 It covers different types of collecting agents used in reverse iron ore flotation, the surface characteristics of minerals commonly present in iron ores (eg, iron oxides, quartz, aluminabearing An Investigation of Approaches for Enhanced Reverse Flotation of 2017年1月1日 Thus, the performance of an industrial ball mill can be adequately described using the orespecific breakage distribution function together with the systematic variation of the material transport (PDF) Performance optimization of an industrial ball mill for The Ore Sawmill is a Reborntier utility upgrader added in the Reincarnation Update It was first revealed in a screenshot on Foxy's Twitter The Ore Sawmill has a unique hybrid function that duplicates ore, but also halves both their value and size Ores may be duplicated again with the Ore Replicator The description is a parody of a nowinfamous infomercial for Flex Tape, a Ore Sawmill The Miner's Haven Wikia Fandom
.jpg)
SIDERITE ORE PHYSICAL SEPARATION AND REVERSE FLOTATION
2012年1月1日 It is very common to upgrade iron ore by reverse flotation, because it usually has a high irongrade 1:1 and for each test the mill is charged with 330 g siderite ore and 330 ml tap water 112024年8月2日 The aim of this work is to develop lowconcentration carbonate phosphate from the Sra Ouertane region Indeed, the Sra Ouertane lowgrade phosphate ore needs an efficient process to remove the impurities, such as carbonates, silicates as well as clay minerals, to meet the requirements of the phosphate industries Froth flotation is considered as the prevalent Beneficiation of lowgrade carbonated phosphate ore by reverse ORE MILL Bar Grille, Warren, New Hampshire 1,606 likes 1 talking about this 1,133 were here Serving locallysourced food, craft beer, wine and cocktailsORE MILL Bar Grille Warren NH Facebook2023年8月8日 To explore the flotation feasibility and flotation law of iron minerals from amphiboletype iron oxide ore with fullsize minerals, a systematic study on the flotation behaviors of single minerals hematite, quartz, and amphibole was carried out with the anionic reverse flotation system The effects of collectors, depressants, activators, and pH on the floatabilities Flotation Characteristics of AmphiboleType Oxidized Iron Ore via
.jpg)
(PDF) Reverse flotation studies on iron ore slime by the synergistic
2019年4月21日 In the reverse flotation of iron ore, refraining from achieving equilibrium recovery could help limit entrainment, but this was not necessarily the case in direct flotation2016年10月12日 Stockpiling of ore ahead of the mill can aid in smoothing out some of the fluctuations although it must be stored in such a manner that no segregation occurs In operating a grinding circuit, like any other unit process, Closed Circuit Grinding VS Open Circuit Grinding2015年10月9日 Calculating a grinding circuit’s circulating loads based on Screen Analysis of its slurries Compared to %Solids or Density based Circulating load equations, a more precise method of determining grinding Ball Mill Circulating Load Formula 911Metallurgist2016年3月1日 mill ion de tons in 2012) Furthermore, Recent advances in reverse flotation of diasporic ores Minerals Engineering, v 17, p 10171022, 2004 Received on (first version): 19/11/2014, Concentration of manganese tailings via reverse
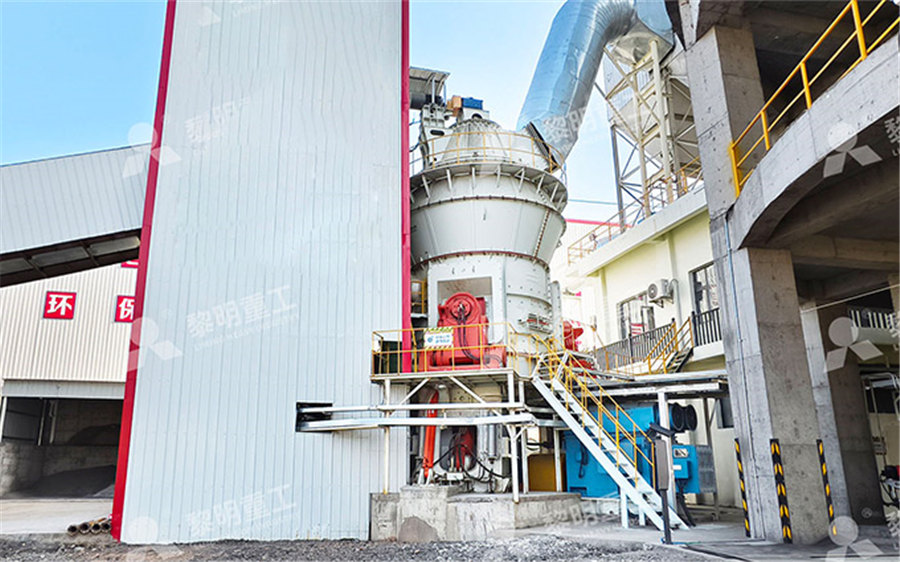
Understanding the SAG Mill in Copper Ore Mining Process
The rod mill is another type of grinding mill used in the copper ore mining process This machine uses steel rods as the grinding media instead of balls, which are commonly used in ball mills The rods grind the ore by tumbling within the mill, similar to the action of a rotating drum2008年1月15日 Reverse flotation of hematite from a local silica sand ore has been investigated using a batch, benchscale mechanical flotation cell The effects of various operating parameters such as type and Removal of hematite from silica sand ore by reverseIt’s really fun! So fun that we started a Reverse Drafting Club to work remotely on this practice with friends near and far In 2022, we had nearly 400 members in this exclusive club, scattered across the globe* THE WEAVING MILL 1801 North Spaulding Ave, Chicago IL, 60647Reverse Drafting Club The Weaving Mill911 Metallurgist can enter the scene and see what you have become blind to We can fix issues in ways you never thought possible Our fresh eyes will open new opportunities for your plant Each mineral processing plant has varied ore types, mining equipment, (crusher, ball mill, flotation, tailings), and management (operating) philosophyThe evaluation and prioritization of variables Metallurgists Mineral Processing Engineers 911Metallurgist
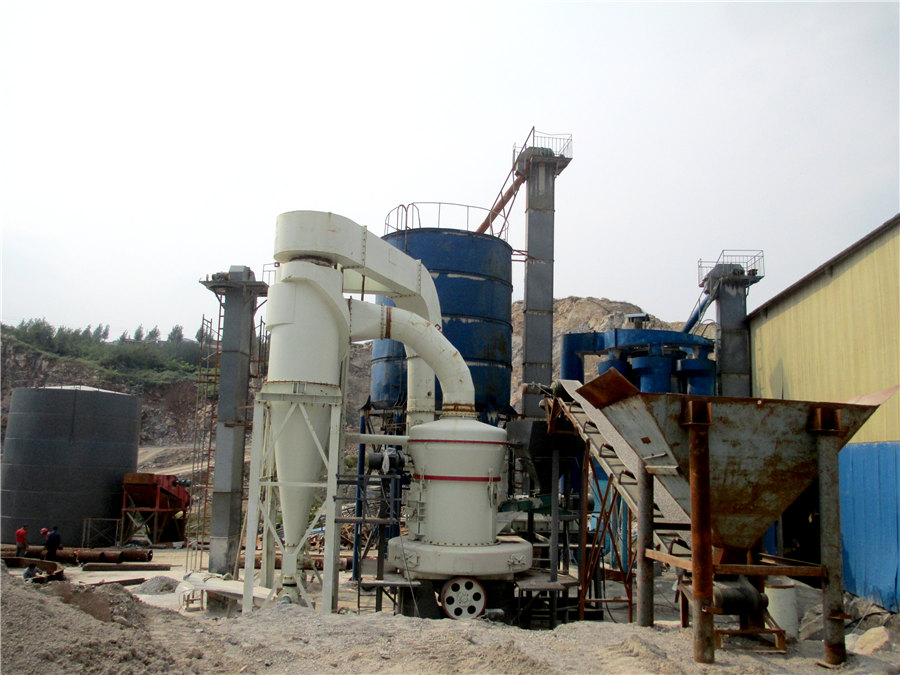
12th Mill Operators' Conference 2014 AusIMM
It is normalised based upon the ore resistance to breakage, so it provides feedback about the health' of the milling process under varying operating conditions and ore types Mill grinding efficiency is measured at the same time as CSE through circuit samplingFunctional performance analysis combines CSE and mill grinding efficiency to provide mill, desliming in hydrocyclones and final ore mineral concentration via multistage reverse flotation and thickening of the final product With the need for decarbonisation in the iron and steelmaking industry, there is a growing demand for high grade iron ore concentrate at more than 67% Fe In the context of declining ore grades,Transforming iron ore processing Simplifying the comminution 2019年3月1日 A worldwide survey on grinding mill circuits in the mineral processing industry was conducted The aims of this survey are to determine how milling circuits are currently controlled, and to find Evaluation of grinding circuits for iron ore ResearchGateTherefore, the reverse circuit would not provide any energy savings compared with the direct circuit (which presented an energy consumption of 44 kWh/t) This exercise shows that the benefits of removing natural fines from the mill feed Performance of direct and reverse Samarco grinding
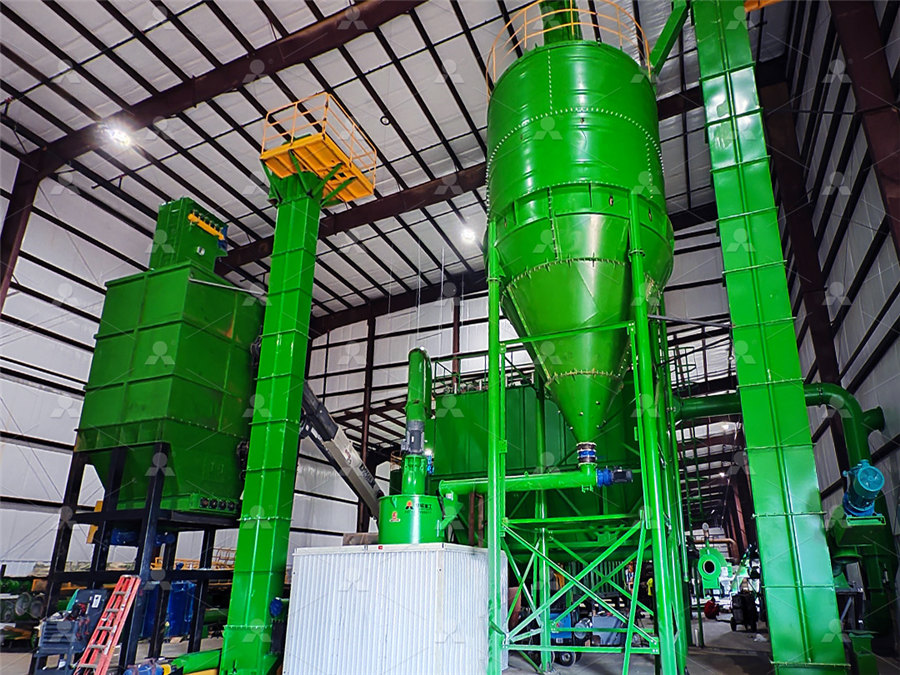
Comminution and classification technologies of iron ore
2022年1月1日 Ore that is less than 40 mm but greater than 8 mm is conveyed to the lump stockpile Ore that is finer than 8 mm, but greater than 1 mm is conveyed to the fines stockpile Any ore that is finer than 1 mm in size is conveyed to a desanding plant consisting of cyclones, upper current classifiers and two stages of spirals for further beneficiation2016年5月7日 Potash ores generally contain 20 to 40 percent KCL with the balance being NaCl and a small amount of clay slime, the latter usually in the order of 1 to 1½% Flotation has been developed as the principal separating process for the potash salts which generally are coarsely crystalline and free from the sodium salts at about 10 to 14 meshPotash Flotation Process 911Metallurgist2019年11月13日 Processing of a complex carbonaterich CuCo m ixed ore via reverse flotation Quentin DEHAINE 1,2* , Lev O FILIPPOV 3 , Inna V FILI PPOVA, Laurens T TIJSSELING 1 , and Hylke J GLASS 1Processing of a complex carbonaterich CuCo mixed ore via reverse 2024年7月19日 The reversing mill is so named because the steel runs back and forth between the rollers, reducing the thickness incrementally with each pass A reversing mill can be used to reduce material to gauge Reversing mill plants are preferable for Reversing Mill Corrosionpedia
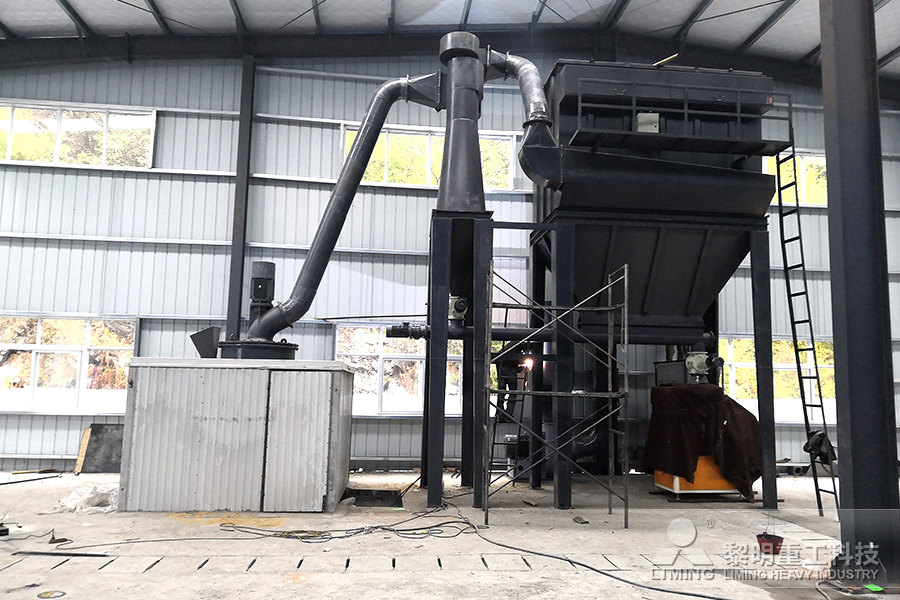
Closed circuit ball mill – Basics revisited ScienceDirect
2013年4月1日 Circulating load and classification efficiency effect on ball mill capacity revisited Relative capacity model introduced and validated Relationship between circulating load and classification efficiency verified by industrial data Existing fine screening technology could increase ball mill circuit capacity 15–25%2024年4月26日 Learn about the key stages in iron ore processing, including crushing, screening, and beneficiation techniques for optimal resource utilization +86 ; xlyin@ The choice of grinding mill depends on factors such as the desired product size, capacity requirements, and energy consumption b Autogenous and Semi Iron Ore Processing: From Extraction to ManufacturingPDF On Jan 1, 2011, W M Jansen and others published Tracerbased minemill ore tracking via process hold ups at Northparkes mine Find, read and cite all the research you need on ResearchGate(PDF) Tracerbased minemill ore tracking via process2016年4月20日 In China, directreverse flotation is proved to be applicable to most phosphate ores However, because the ratio of froth product is generally high, current directreverse technology faces Beneficiation of a Sedimentary Phosphate Ore by a Combination
制粉项目-2023.11.17.jpg)
REMOVING IRON IMPURITIES FROM MAGNESITE ORE BY ASYNCHRONOUS REVERSE
from magnesite ore is under alkaline pH conditions, with fatty acid collectors by positive flotation (floating Mg and inhibiting Si and Ca) After the flowsheet of reverse flotation, the positive flotation is used to process the magnesite ore for most magnesite ores containing quartz/silicate and carbonate gangue minerals [2,3]