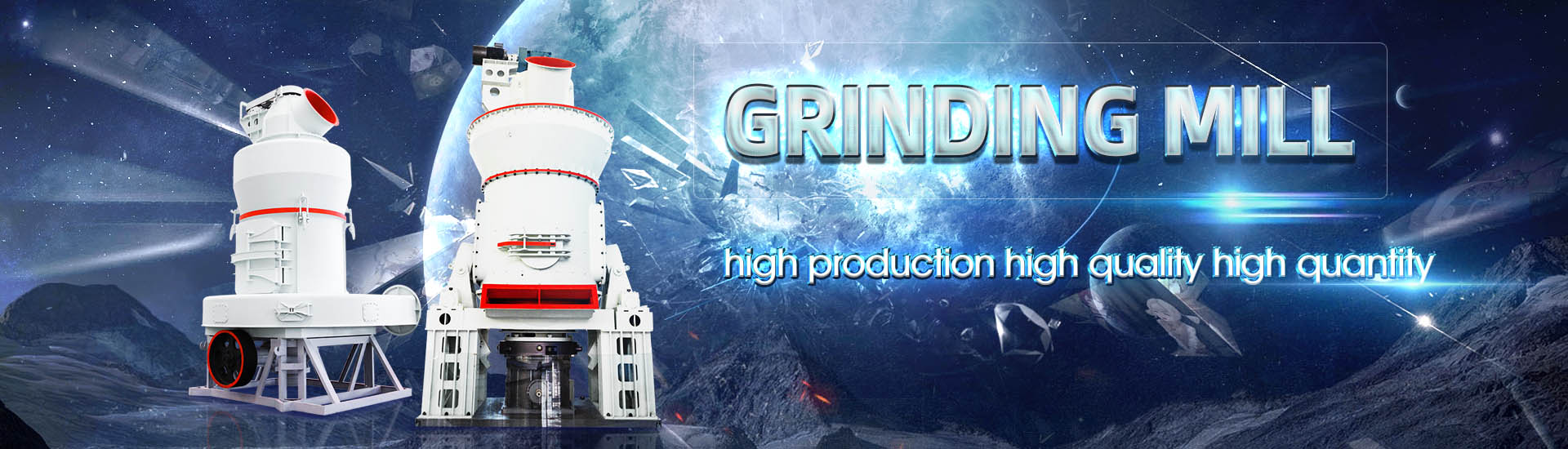
HOME→Comparison of limestone pulping system solutions in dry grinding and desulfurization of feldspar processing large fire reduction unit
Comparison of limestone pulping system solutions in dry grinding and desulfurization of feldspar processing large fire reduction unit
.jpg)
ReviewRecent advances in process and materials for dry
The newly developed dry desulfurization processes including source/end control technologies and the various dry desulfurization materials including Calcium/Magnesium/Sodium/Carbonbased The current study presents a detailed comparison and selection, in consideration of technology and economical efficiency, of two limestone grinding systems: dry grinding system andA comparison between limestone grinding systems of the wet 2017年7月1日 Desulfurization tests show greater performance in terms of gypsum production SO 2 removal efficiency compared to the limestone treated with a traditional mill Multicriteria Enhancing the recovery of gypsum in limestonebased wet flue 2018年10月15日 Research Cottrell has demonstrated the commercial availability of limestone flue gas desulfurization on a 115 MW installation Certain chemistry and process Comparison of flue Gas Desulfurization Technologies ResearchGate
.jpg)
Production and resource utilization of flue gas desulfurized
2021年11月1日 The main methods are the wet limestonegypsum method, the magnesium oxide method, seawater desulfurization, and the double alkali method The two most common wet 2021年10月13日 A Technical and Economic Comparison of Ball Mill Limestone Comminution with a Vertical Roller Mill Wet flue gas desulfurization (WFGD), using limestone with forced A Technical and Economic Comparison of Ball Mill Limestone 2021年3月17日 Comparison of SDA with wet limestone FGD Spraydry absorption offers several advantages over the wet FGD process, including the following: A dry waste byproduct Spray drying absorption for desulphurization: a review of recent 2019年3月1日 Firstly, it summarizes the existing desulfurization and denitration technologies, then summarizes the research progress of the combined desulfurization and denitration Progress of Desulfurization and Denitration Technology of Flue
.jpg)
(PDF) A Review of Desulfurization Technology using Limestone in
2015年10月30日 This study investigated that status of domestic and international furnace desulfurization and desulfurization characteristics of limestone for fluidized bed use depending 2015年7月27日 The various flue gas desulfurization (FGD) technologies available in the market, for the reduction of sulfur dioxide emissions, are presented The process descriptions are Review of Design, Operating, and Financial Considerations in Flue 2022年1月15日 In the industrial production of China, the processing of phosphate rock, volcanic eruptions, kerosene combustion and aluminum smelting will lead to flue gas emissions containing a large amount of SO 2SO 2 is a highly irritating gas Because SO 2 is freely soluble in water and enters the respiratory tract, it can generate corrosive sulfurous acid, sulfuric acid, and sulfate Summary of research progress on industrial flue gas desulfurization 2017年5月25日 Finally, clays for the preparation of ceramic slips would reasonably be expected to be ground wet, since the initial condition of the clay is wet and it is required in a wet form for subsequent processing Clearly, in such Dry Grinding VS Wet Grinding 911Metallurgist

Impact of grinding aids and process parameters on dry stirred media
2018年7月15日 Request PDF Impact of grinding aids and process parameters on dry stirred media milling The demand on minerals with increasing product fineness is currently rising in many industrial applicationsPDF On Oct 15, 2018, Cara Niu published Comparison of flue Gas Desulfurization Technologies Find, read and cite all the research you need on ResearchGateComparison of flue Gas Desulfurization TechnologiesJune 2022; ARCHIVE Proceedings of the Institution of Mechanical Engineers Part C Journal of Mechanical Engineering Science 19891996 (vols 203210) 236(2):1107(PDF) A comprehensive review on the grinding process: 2006年1月1日 However, the performance of the grinding aid depends on both the type and the amount used in the grinding process [5] Different types and amounts of grinding aids affect the properties of the Effect and Behavior of Liquid Additive Molecules in Dry Ultrafine
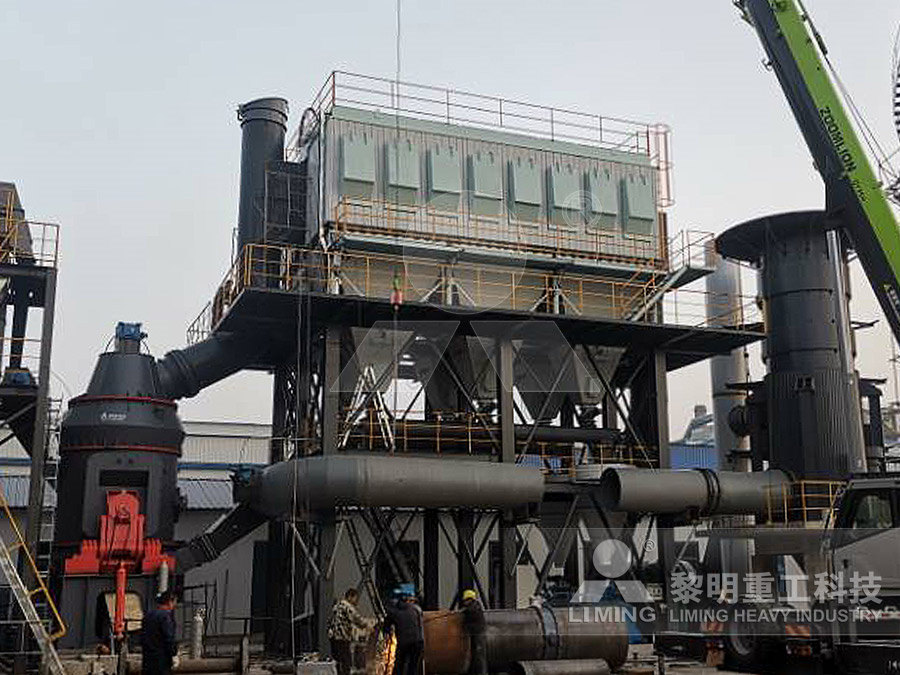
Sulfur dioxide removal: An overview of regenerative flue gas
2020年8月1日 Sulfur dioxide removal: An overview of regenerative flue gas desulfurization and factors affecting desulfurization capacity and sorbent regeneration2003年6月5日 The properties of hardened mortar and concrete made with limestone portland cement are examined and compared to those made with nonlimestone portland cements–including compressive and flexural The Use of Limestone in Portland Cement: A StateoftheArt 2009年6月1日 The present literature review explores the energyefficient ultrafine grinding of particles using stirred mills The review provides an overview of the different techniques for size reduction and Comparison of energy efficiency between ball mills and stirred 2011年9月25日 An indicative comparison could be derived for dry grinding energy cons umption between a system of HPGR and dry ball milling (F igure 16) , and a system involving HPGR and VSK ® classification FEASIBILITY OF DRY HIGH PRESSURE GRINDING AND CLASSIFICATION
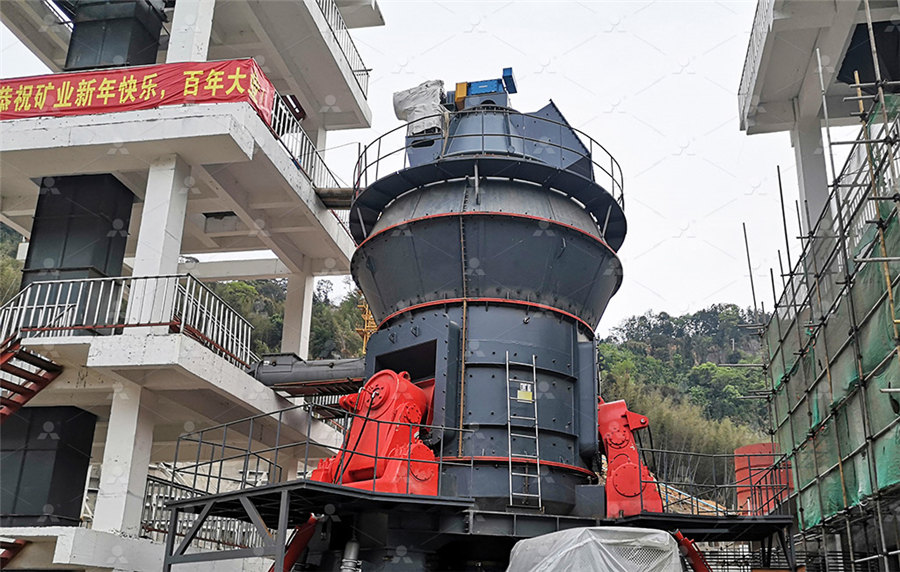
Effect of particle size distribution on grinding kinetics in dry
2012年1月1日 For dry ball mill grinding operation, the effect of ball and mill diameters on grinding rate parameters of the sizediscretized population balance model has been investigated for quartz, limestone 2017年7月1日 The most common types of FGD system are based on the contact between the flue gases and an alkaline sorbent such as lime or limestone (Wang et al, 2005)Furthermore, the major types of largescale power plant FGD systems include (i) spray towers, (ii) spray dryers and (iii) dry sorbent injection systems (Song et al, 2012)These FGD systems can achieve about Enhancing the recovery of gypsum in limestonebased wet flue 2012年6月24日 Dry grinding is usually preferred in regions where water is scarce and following process is dry The effect of wet and dry grinding environment prior to flotation of sulfide ores has been a (PDF) WET AND DRY GRINDING METHODS EFFECT 2022年5月22日 Fine and ultrafine grinding of limestone are frequently used in the pharmaceutical, chemical, construction, food, and cosmetic industries, however, research investigations have not yet been published on the combination of energy and life cycle modeling Therefore, the first aim of this research work was the examination of main grinding parameters EnergyModel and Life CycleModel for Grinding Processes of Limestone
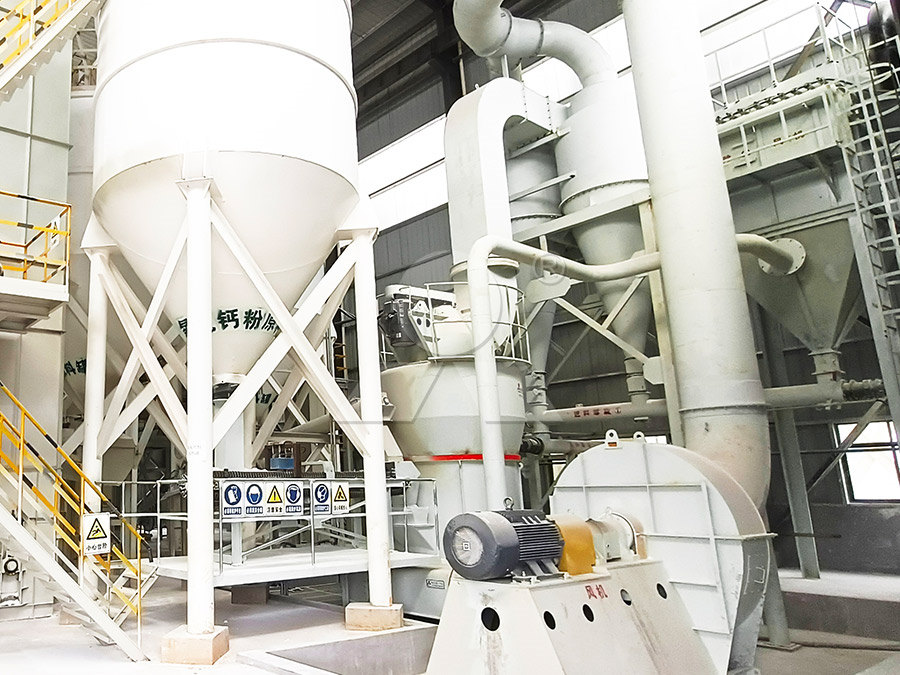
Review of Design, Operating, and Financial Considerations in
2015年7月27日 3 Flue Gas Desulfurization Technologies Flue gas desulfurization is an efficient method for the reduction of the sulfur dioxide emissions Citation 2 Many processes are available in the market, such as (a) wet scrubbers, (b) spray dry scrubbers, (c) sorbent injection, (d) regenerable processes, and (e) combined SO 2 /NO X removal processes The different flue 2012年9月24日 For dry ball mill grinding operation, the effect of ball and mill diameters on grinding rate parameters of the sizediscretized population balance model has been investigated for quartz, limestone EFFECT OF PARTICLE SIZE DISTRIBUTION ON GRINDING KINETICS IN DRY 2023年2月11日 Calciumbased desulfurization ash (CDA) is mainly produced in dry and semidry flue gas desulfurization processes The property of CDA is extremely unstable because its main component, calcium sulfite, makes it difficult to be directly applied to the field of building materials The modification of desulfurization ash can be realized by hightemperature Resource utilization of flue gas calciumbased desulfurization 2022年5月22日 Normalized and weighted values in the wet grinding process in nanograms (Functional unit: 1 kg of limestone product Impact assessment method: CML 2001/Aug 2016EnergyModel and Life CycleModel for Grinding Processes of Limestone
.jpg)
(PDF) Progress of Desulfurization and Denitration Technology of
2019年3月30日 The use of ammonium reagents in the processes of semidry desulfurization of flue gas is promising, since the product of desulfurization is ammonium sulfate, which can be used as a mineral fertilizer2019年10月1日 Request PDF Wet and dry grinding of coal in a laboratoryscale ball mill: Particlesize distributions In this study, experimental data for wet and dryground coal samples under wet and dry Wet and dry grinding of coal in a laboratoryscale ball mill: Particle 2021年11月1日 Three desulfurization methods are commonly used: dry desulfurization, semidry desulfurization and wet desulfurization (Michalski, 2017) Dry flue gas desulfurization ( Klaka et al, 2018 ) refers to the application of powder and granular absorbents to react with sulfur dioxide under dry conditions, and the reaction products are also in a dry stateProduction and resource utilization of flue gas desulfurized A process system and limestone technology, applied in the field of limestone dry milling and pulverizing process system, can solve the problems of large dust pollution, insufficient grinding capacity, strict requirements on the particle size of limestone feed, and achieve the effect of less environmental pollution and strong grinding capacityLimestone dry grinding powder manufacturing process system
.jpg)
Dry grinding in planetary ball mills: Evaluation of a stressing
2017年11月1日 Planetary ball mills at laboratory scale are widely used for grinding and alloying processes However, in contrast to other mill types, no applicable mechanistic model exists to describe the 2022年2月28日 Comparing dry and wet grinding curves in a ball mill in the same condition (an equal amount of materials and grinding media has been used on each pair of wetdry experiments) (Fig 17) indicated two significant differences at higher power values of wet grinding, specifically when speed exceeded 06 critical speed and for higher ω Pmax in the Grinding SpringerLink2020年5月16日 Numerous mitigation techniques have been incorporated to capture or remove SO2 with flue gas desulfurization (FGD) being the most common method Regenerative FGD method is advantageous over other methods due to high desulfurization efficiency, sorbent regenerability, and reduction in waste handling The capital costs of regenerative methods are Sulfur dioxide removal: An overview of regenerative flue gas 2023年6月6日 Sulfur dioxide, which comes from the flue gas emitted by the steel and coal power industries, is extremely harmful to humans and the natural environment Due to its high efficiency and economy, dry fixedbed desulfurization technology and Cabased adsorbents have attracted wide attention In this paper, a detailed outline of the process of the fixedbed reactor, Application of Cabased adsorbents in fixedbed dry flue gas
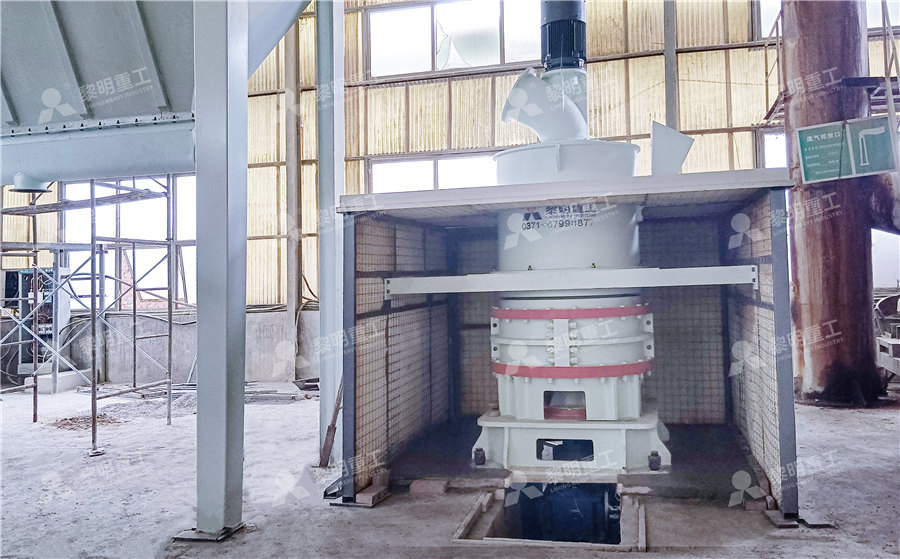
Limestone Grinding Mill Plant TAYMACHINERY
The limestone grinding production line is a production process for the fine processing of limestone raw materials The limestone grinding production line grinds limestone into powders of different fineness through crushing, grinding, classification, and other processes to meet the needs of different fields This production line covers the complete process from raw material processing Abstract Although pulping processes from wood are wellcemented technology, the emergence of biobased nanotechnology, as well as the increase in concern about the environmental impact that these processes can have, calls for a reevaluation of the impacts that the traditional pulping methods have on the surfaces of the fibers and how variances will then affect the generation Pulping Processes and Their Effects on Cellulose Fibers and 2012年10月10日 A largescale continuous stirred media mill called the MaxxMill® system in dry mode was used to investigate the comminution characteristics A limestone powder below 2 mm was used as a feed materialDry grinding of sodium feldspar in a stirred ball mill2023年9月15日 Dry grinding machine: A dry grinding machine uses no liquid element and relies on particleonparticle contact to reduce the size of the materials Wet grinding machine: On the other hand, a wet grinding machine uses a liquid, such as water or solvent, as a lubricant and cooling agent to disperse the particles in a slurryDry Grinding Vs Wet Ball Mill Grinding Economy Ball Mill
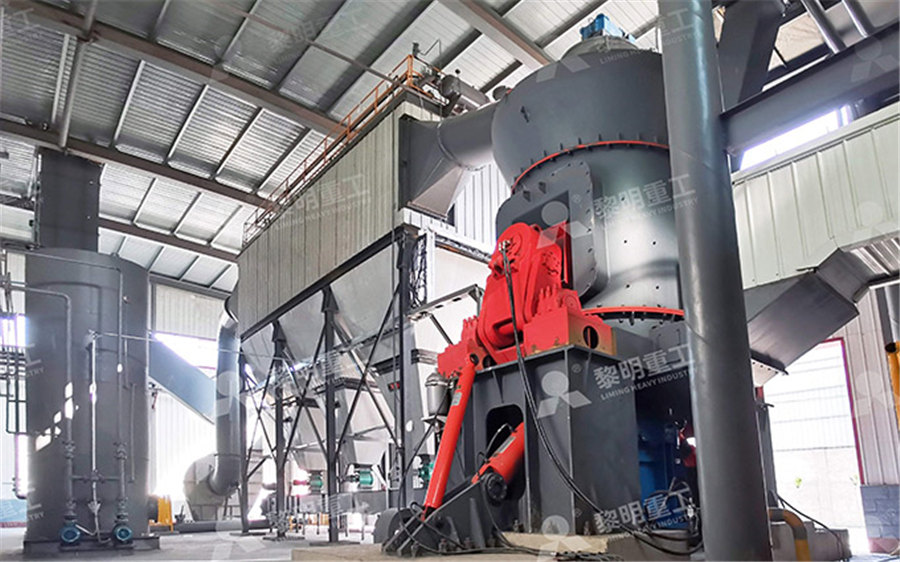
Evaluation of particle size reduction and agglomeration in dry grinding
2020年5月15日 Ultrafine grinding is a key unit operation in the processing of industrial minerals and rocks such as quartz, feldspars, gypsum, kaolinite, limestone and dolostone Besides the high energy consumption, the greatest problem when dealing with size reduction below 10 μm is related to particleparticle interactions, which is closely dependent to the milling system and 2019年3月13日 Introduction Sulfur dioxide (SO 2) is one of the major pollutants contributing to frequent hazy weather in ChinaA large amount of SO 2 in the atmosphere comes from coal combustion As the amount of coal for power Modeling and optimization of wet flue gas 2021年1月1日 Compared to traditional drymilling, wet grinding shows higher efficiency and can avoid dust generation Since most of IOTs are directly discharged into the river or exposed to rainwater, wet (PDF) Different Effects of Wet and Dry Grinding on the Activation of The project of two public a desulfurization unit limestone pulping system, limestone slurry to set two wet ball mill system, each wet ball mill output 75 percent by means of two FGD slurry amount required to consider, after grinding limestone product size ≤0063mm (250 mesh, by 90%)Limestone FGD New Technology
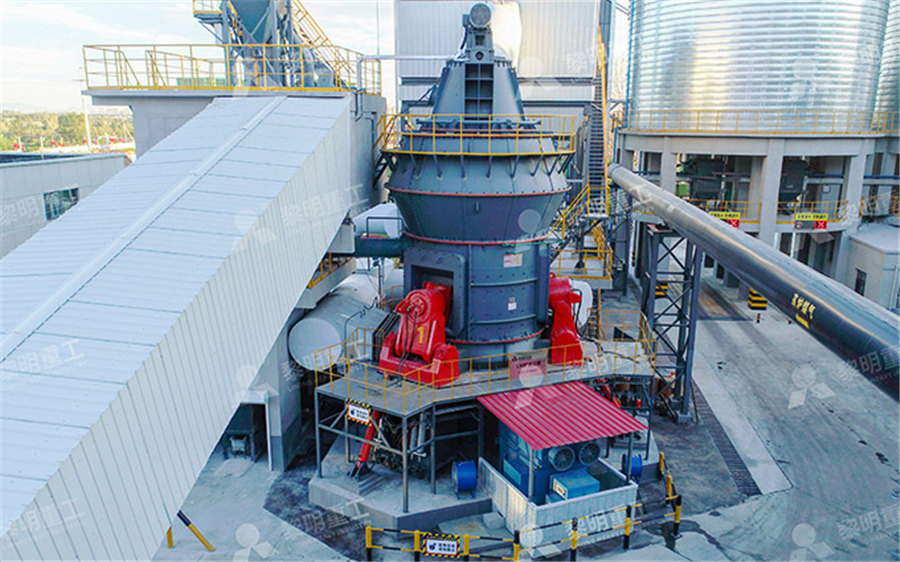
(PDF) Environmental Hazards of Limestone Mining and
2020年2月18日 The limestone mined is used chiefly for the manufacturing of cement, lime and edible lime etc Scientific studies revealed that loss of forest cover, pollution of water, soil and air, depletion of 2021年3月17日 The performance of a wet FGD system is greatly influenced by gas–liquidphase mass transfer, ieof Ca 2+ ions in the liquid phase and of SO 2 from the gas phase to the aqueous phase (Hrdlička and Dlouhý 2019)This is further influenced by the rate of dissolution of limestone in the system, directly affecting the concentration of dissolved ions in the slurry Spray drying absorption for desulphurization: a review of 2019年1月11日 In the present study, size reduction experiments were performed on HighPressure Grinding Rolls (HPGR), ball mill and stirred mill of PGE bearing chromite orePerformance comparison of stirred media mill and ball (BOND) The parameters in mth order grinding kinetics were analyzed, and grinding specific rates were visualized Ore particles experienced three inherent stages in ball grinding mills, that is i) rapid grinding of coarse fraction, ii) dynamic grinding of medium size fraction, and iii) single grinding of medium size parison of grinding characteristics in highpressure grinding
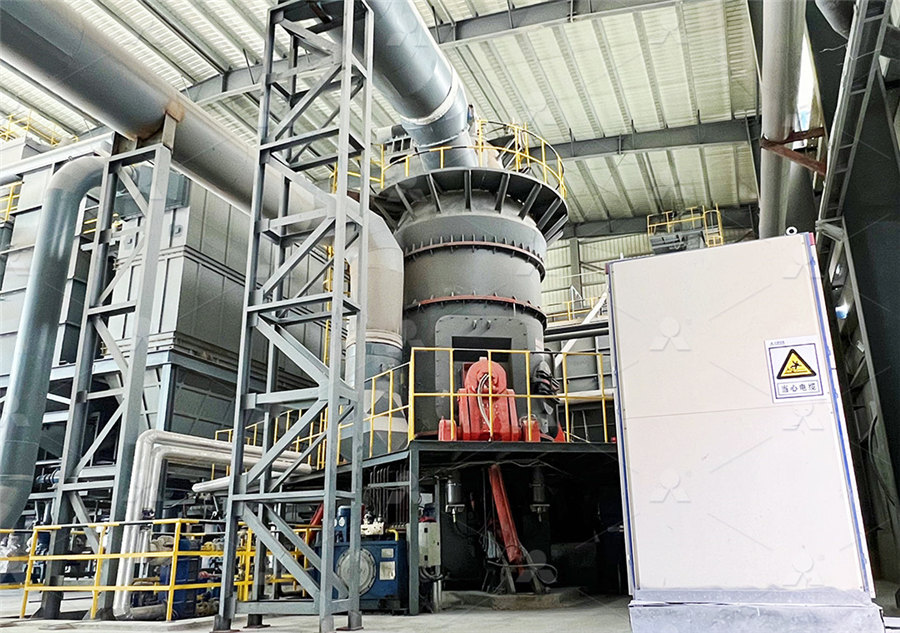
A comparison of intergrinding and blending limestone on
2013年6月1日 The nucleation rate of the CSH phase at the surface of filler grains substantially depends on the size of the specific surface area (fineness) and its proportion in the cement mass [80,61,110]2019年5月29日 This paper examines the behavior of Portland limestone cements (PLCs) made by intergrinding clinker, gypsum and limestone in a full sizecement plant, while varying the content of limestone Comparison of dolostone and limestone as filler in blended