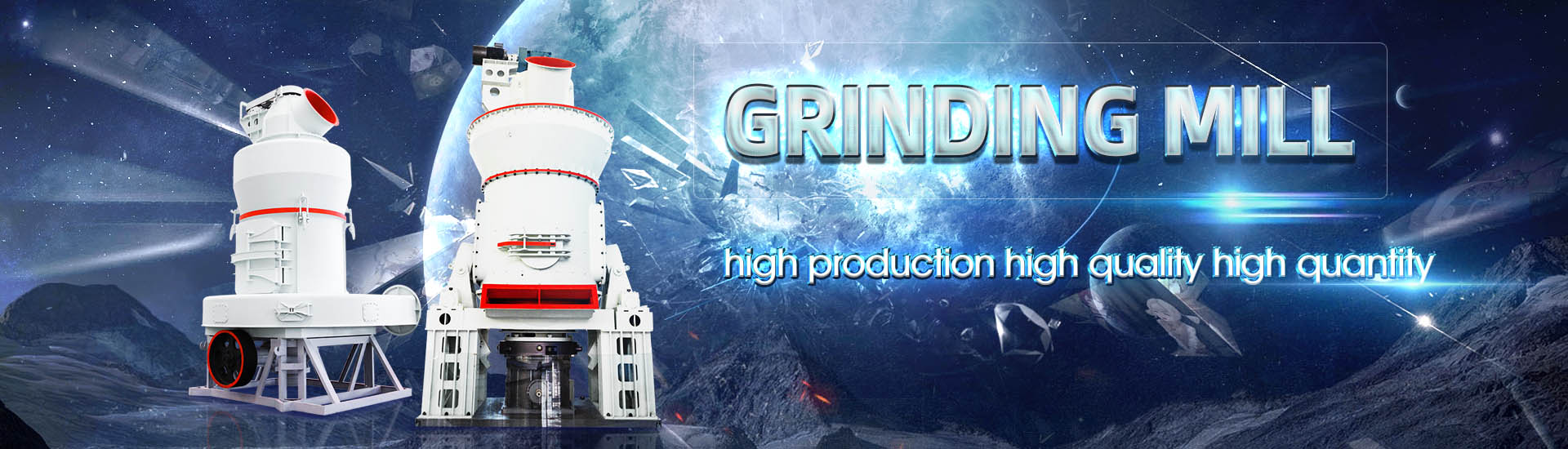
HOME→Cement raw material mill vertical mill process cement raw material mill vertical mill process cement raw material mill vertical mill process
Cement raw material mill vertical mill process cement raw material mill vertical mill process cement raw material mill vertical mill process
.png)
Vertical raw mill Cement Plant
Vertical raw mill is one kind of raw mill, generally used to grind bulk, granular, and powder raw materials into required cement raw meal in the cement manufacturing plant Vertical raw mill is an ideal grinding mill that crushing, drying, grinding, 2021年1月1日 Vertical roller mill has proved to be a popular choice for finished cement grinding over all other machineries due to advantages like low power consumption, higher capacity, Review on vertical roller mill in cement industry its performance Our bestinclass OK™ Mill is a globally successful vertical roller mill solution for grinding raw material, cement and slag Its cuttingedge design features consistently deliver the highest quality products with the greatest efficiency It OK™ Raw and Cement MillAGICO Cement Vertical Mill AGICO Cement Ball Mill Cement Vertical Mill Grinding System Cement vertical mill, also called roller mill, is another raw mill commonly used in cement pared with the cement ball mill, it has a Raw Mill – Raw Mill In Cement Plant AGICO Cement
.jpg)
Vertical roller mill for raw Application p rocess materials
vertical roller mill Application process Raw material process Background In the vertical roller mill which is widely used in the raw material grinding process, raw materials input grinding table are crushed and pulverized on it and transported to separator by kiln exit gas introduced into the mill as drying, transporting and separating purposeThe vertical cement mill is largescale cement grinding machine With advantages of energyefficient and stable quality, vertical roller mill is widely applied to many industries, such as cement, power, metallurgy, chemical and nonmetallic mining industry and etc As a typical type of Cement Mill, vertical cement mill set crushing, drying, grinding, grading transportation in one, it grind Vertical Cement MillPart Three: Raw Mill Process of Raw Mill The proportioned raw material is feed first to a grinding mill In the mill, particles ground in to very fine sizes In the grinding unit, drying, grinding and mixing takes place simultaneously Hot gas from clinker burning unit is passed into the grinding unit to assist the drying and grinding processCement Manufacturing Process INFINITY FOR CEMENT EQUIPMENT2021年1月1日 Stacking Reclaiming of Raw material: Swing type stacker Reclaimer: Limestone other raw material are stored in open area into a longitudinal storage unit called stockpile through Stacker These are then extracted transversely from the stockpile through reclaimer: 3: Raw Meal Grinding Homogenization: Grinding Mill Vertical Roller Mill Review on vertical roller mill in cement industry its
.jpg)
Vertical Roller Mill Operation in Cement Plant
The vertical roller mill (VRM) is a type of grinding machine for raw material processing and cement grinding in the cement manufacturing processIn recent years, the VRM cement mill has been equipped in more and more cement plants around the world because of its features like high energy efficiency, low pollutant generation, small floor area, etc The VRM cement mill has a The power ingesting of a grinding process is 5060% in the cement production power consumption The Vertical Roller Mill (VRM) reduces the power consumption for cement grinding approximately 3040% associated with other grinding mills The process variables in cement grinding process using VRM are strongly nonlinear and having large timePROCESS CONTROL FOR CEMENT GRINDING IN VERTICAL ROLLER MILL The mill will not run at this time The feed group is stopped when there is sufficient material in the mill The material is then distributed in the mill manually with a shovel When the mill is too full the mill main drive can be overloaded and it will be necessary to remove some material from the mill Preparations for mill start upPROCESS TRAINING for operators of Vertical RAW MillsA mediumsized dry process roller mill A raw mill is the equipment used to grind raw materials into "rawmix" during the manufacture of cement Rawmix is then fed to a cement kiln, which transforms it into clinker, which is then ground to make cement in the cement millThe raw milling stage of the process effectively defines the chemistry (and therefore physical properties) of the Rawmill Wikipedia
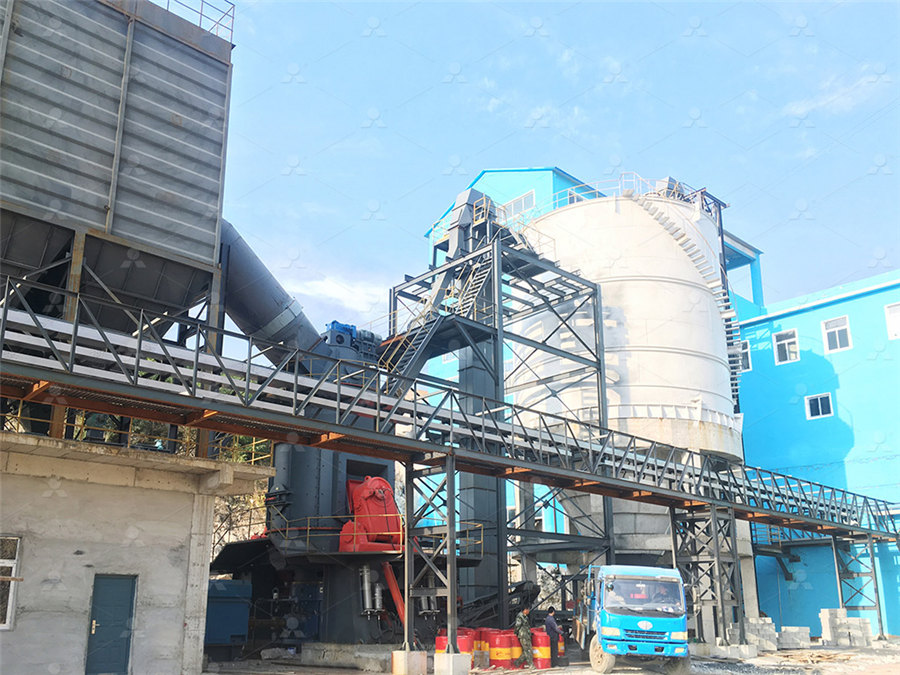
Cement Mill Cement Ball Mill Vertical Cement Mill
Wide product range: For meeting various requirements from different clients, our cement mill range from cement ball mill, vertical cement mill, Raymond mill, coal mill in cement plant, etc Strong production ability : AGICO CEMENT has a for Loesche Vertical Mills Variable clocking • 50 / 100 ms: Signal detection • 1 second – 10 minutes: Signal evaluation • Material grindability • Material temperature • Material moisture • Mixture composition • Composition of raw material • Grinding roller wear • Fineness (Blaine) or residue (VOA) • Mill motor speedPROCESS OPTIMISATION FOR LOESCHE GRINDING PLANTSOur bestinclass OK™ Mill is a globally successful vertical roller mill solution for grinding raw material, cement and slag Its cuttingedge design features consistently deliver the highest quality products with the greatest efficiency It Vertical roller mills FLSmidth CementDry Grinding: Open circuit Ball mill, closed circuit Ball mill, vertical roller mill, Roll Press or Roll press in circuit with ball mill However, it would be seen that the most significant process and types used for raw material grinding operations in modern cement industry are: Process: Dry Closed circuit drygrinding Type of mill: Ball and Raw Material DryingGrinding Cement Plant Optimization
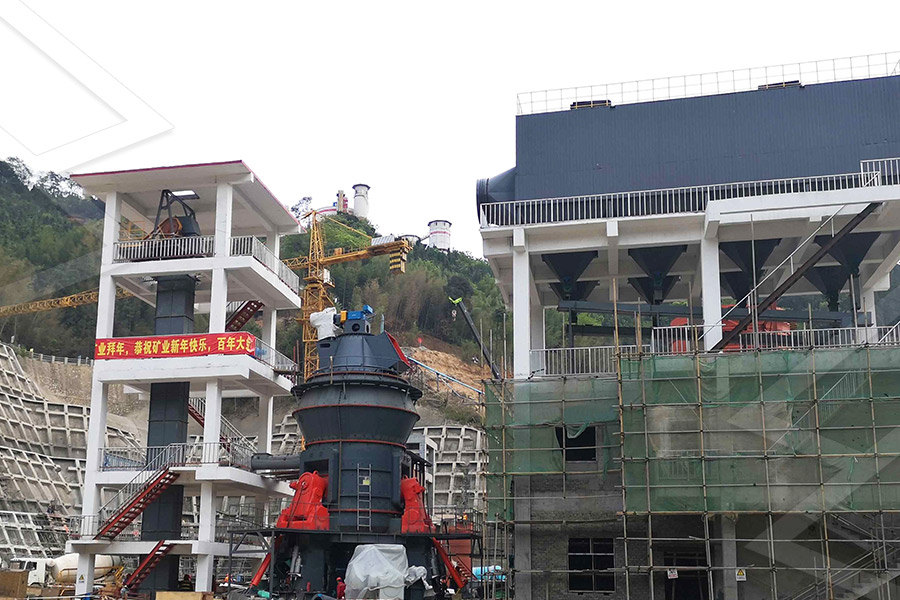
The Cement Plant Operations Handbook International Cement
Providing a comprehensive guide to the entire cement production process from raw material milling – 3 Separators (classifiers) – 4 Ball mill circuit control – 5 Cement storage – 6 Cement dispatch mentioned in Chapter 3 for dry raw milling – AGICO Cement supplies cement equipment for cement raw material production as you need, such as cement mill, cement crusher, onestop turnkey project, welcome to contact! Skip to content +86 Preparation Of Cement Raw Material Cement Mill, Cement Usually each raw component is stored and fed separately to the mill, from which product is sampled and chemically analysed to determine adjustment of feed proportions by addition of corrective components tG maintain the target clinker compositionOlder mills may have silos for raw material storage, but the occurrence of feed problems with Raw milling and blending INFINITY FOR CEMENT EQUIPMENT2017年9月11日 Due to the compact design and material transportation system of vertical roller mills (VRM), some important streams (total mill feed and discharge, dynamic separator feed and reject) remain in the (PDF) Performance Evaluation of Vertical Roller Mill in Cement
.jpg)
(PDF) ANALISA KINERJA ALAT VERTICAL RAW MILL PABRIK II PT
2022年10月3日 Raw materials grinding process is a first step of cement production which is has an important role in the first grinding step Vertical Raw Mill is a main equipment that is used in grinding or What Is Cement Vertical Mill The cement vertical mill is a type of grinding equipment that merges fine crushing, drying, grinding, and powder separating into a single, which simplifies the production process and has many irreplaceable advantages, such as high grinding efficiency, large feeding size, low power consumption (2030% less power than a cement ball mill), large Cement Vertical Mill Vertical Grinding Mill Vertical MillPada Vertical Cement Mill terjadi empat proses yang berlangsung secara simultan Keempat proses tersebut yaitu penggilingan, pengeringan, transport, dan separasi Proses penggilingan, pengeringan EVALUASI KINERJA VERTICAL ROLLER MILL (Cement Mill)Table 3 Power Consumption Of Roller Press Grinding System Overall, we can conclude the three tables: After the longterm operation, although unit raw material grinding power consumption of the cement roller press grinding Comparison Of Vertical Roller Mill And Roller Press Mill
.jpg)
Cement Raw Materials Grinding Process (Raw Mill
2022年3月3日 Cement Raw Materials Grinding Process (Raw Mill System) English VersionRaw Mill System is a system for grinding raw materials in the form of raw materialsLearn about the raw mill in cement blending and concentrating on the quality of raw materials are the two key factors that decide the superiority of the cement Raw material blending is manufacturing facility houses technologically advanced Stacker Reclaimer System for preblending and homogenizing the raw mill This process Raw Mill in Cement Plant Cement Manufacturing Raw Materials2024年2月23日 The operation of the cement raw mill is a critical step in cement production By grinding the raw materials into a fine powder, these powders can be more easily mixed with other cement ingredients and burn more evenly during the cement clinker process Therefore, the efficient operation of the cement raw mill directly impacts the production efficiency and quality How Does a Raw Mill Work in a Cement IndustryStage of Cement Manufacture There are six main stages of the cement manufacturing process Stage 1: Raw Material Extraction/Quarry The raw cement ingredients needed for cement production are limestone (calcium), sand and clay (silicon, aluminum, iron), shale, fly ash, mill scale, and bauxite The ore rocks are quarried and crushed into smaller pieces of about 6 inchesHow Cement is Made Cement Manufacturing Process
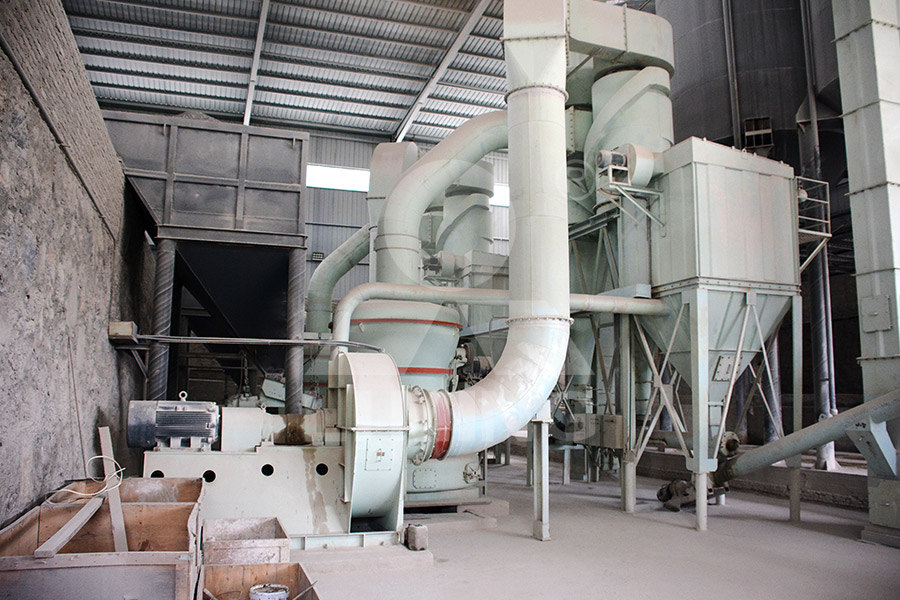
ANALISA KINERJA ALAT VERTICAL CEMENT MILL DI PABRIK II PT
Vertical Cement Mill digunakan untuk mencampurkan dan menghaluskan clinker dan bahan – bahan korektif Selain itu, alat ini juga digunakan sebagai pengering dengan memanfaatkan udara panas dariVertical cement mill has high grinding efficiency and low power consumption (20% – 30% less than ball mill) The granularity of the feeding material is larger(VRM cement mill is 80mm120mm, cement ball mill is less than or equal to 30mm)Vertical Cement Mill Cement Clinker Grinding Equipment in Cement Based on the analysis of the process of cement raw meal vertical milling system, this paper points out the key control output in the process, the mill vibration, and designs a controller to control it by iterative learning and modelfree adaptive control methods Firstly, the PPD state observer is designed for dynamic linearization, and the controller design is based on the MFAC method of ModelFree Adaptive Controller Design Based on DataDriven ILC Cement Mombasa Cement Ltd ordered a QMK² 24/12 with three roller units for the 5,000 tons per day kiln line In addition, the raw material grinding process will be supported by a QMR² 48/24 For the 4,000 tons per day kiln line Shiva Cement Ltd contracted a quadropol® vertical roller mill for grinding pet coke with a QMK² 32/16quadropol® thyssenkrupp Polysius Grinding Technologies
.jpg)
Analisa Kinerja Alat Vertical Cement Mill di Pabrik II
2022年1月10日 Vertical Cement Mill is the main tool used in the final process of making cement at PT Semen Baturaja (Persero) Tbk Vertical Cement Mill is used to mix and grind clinker and corrective materials2015年1月1日 Vertical cement mill (vertical mill) is a machine that plays an important role in the raw meal production process of the newtype dry cement, and it is a set breakage, drying, grinding, transport in one []Raw material grinding process is a vital and energy consumption link in the cement productionModeling Based on the Extreme Learning Machine for Raw Cement Mill The roller grinding mill technology, patented in 1928 and continuously developed since then, has become synonymous with Loesche‘s pioneering engineering knowhow CEMENT BLAST FURNACE SLAG CEMENT RAW MATERIALCement Industry Loesche2020年8月25日 Raw meal: In the raw meal working site, the raw materials are processed by the raw mill to ensure the highquality mixing; cement ball mill and cement vertical mill are generally used in the raw meal process; the finished raw meal are finally sent to the stacker and reclaimer for storage and further mixingCement Production Process Cement Manufacturing Process AGICO CEMENT
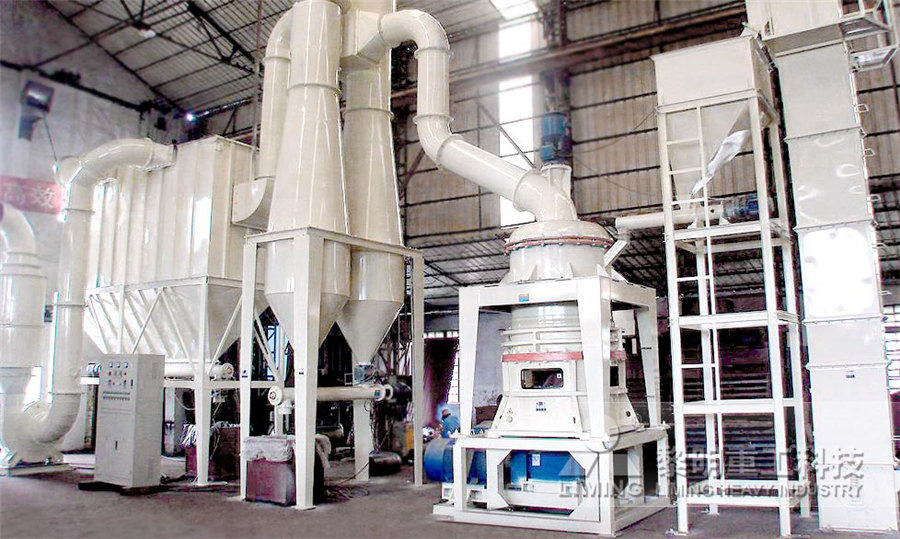
MVR vertical roller mill with planetary gearbox Gebr Pfeiffer
For the preparation of cement raw material, cement, and granulated blastfurnace slag with small to medium output rates, the MVR mill with conventional drive is the right choice This mill type is by the way the core piece of our modular ready2grind system2022年5月9日 The raw materials were mixed in a certain proportion and fed into a vertical roller mill (LOESCHE mill) The raw vertical roller mill has four rollers, 3000 KW main drive, 48 m table diameter, 2 Modeling of energy consumption factors for an industrial cement 2023年7月4日 Raw material grinding: The crushed raw materials are ground into a fine powder, called raw meal, using grinding equipment like ball mills or vertical roller mills 4 Pyroprocessing: The raw meal is heated in a rotary kiln at high temperatures (around 1450°C) to form clinker, a semifinished product consisting of small, nodular lumpsVertical Roller Mill in Cement Manufacturing PlantThe cement raw material mixtures are ground, dried, and classified in the Pfeiffer vertical roller mill For drying the material, hot gases are directed into the mill (0063 to 02 mm) The ground and dried product is separated from the process gas in a cyclone collecting system which is followed by the mill fanRaw mills for all requirements Gebr Pfeiffer
.jpg)
OK RAW AND CEMENT MILL
OK RAW AND CEMENT MILL RELIABLE AND EFFICIENT RAW MATERIAL GRINDING Vertical Roller Mills (VRMs) have been the standard OK™ RAW MILL Optimum raw, cement and slag grinding BEST IN CLASS 0 200 400 600 800 1000 1200 1400 1600 1800 OK 373 OK 283 OK 776 OK 716 OK 666 OKa Loesche mill, with a grinding track diameter of only 11 metres, was used as long ago as 1935 However, the breakthrough in grinding this type of material on the vertical roller mill did not take place until the beginning of the 1990’s 1935 The first Loesche mill for grinding cement clinker, an LM 11, was commissioned in Joao Pessao, Brazil2 µm 5 µm Loesche