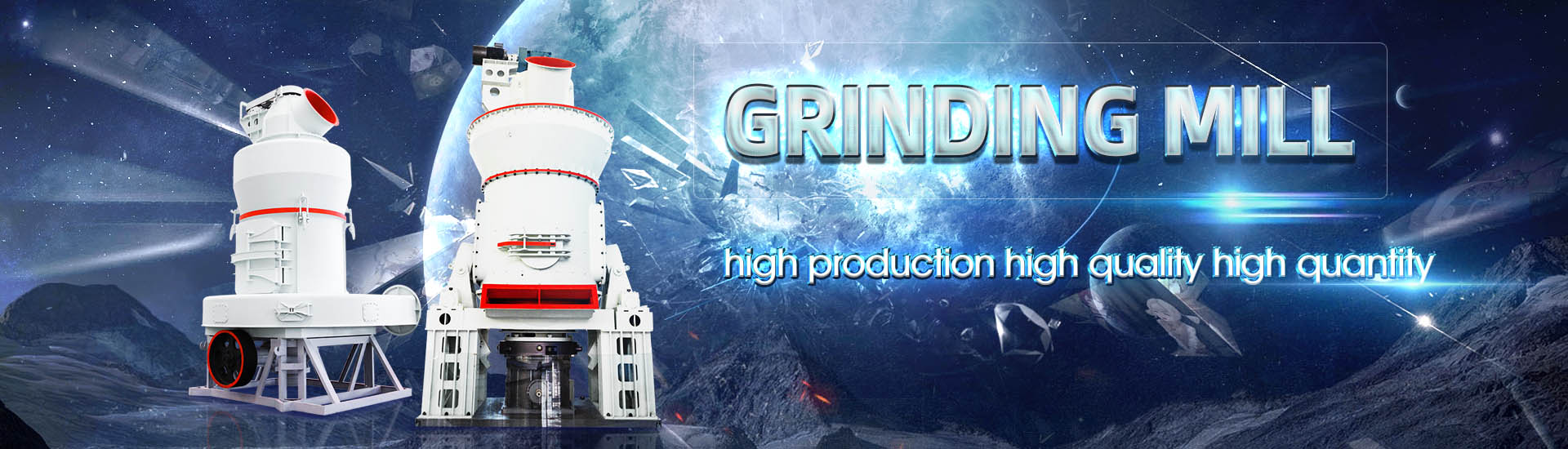
HOME→Design of hydraulic rock drill with normal pressure in the front chamber and oil return in the rear chamber
Design of hydraulic rock drill with normal pressure in the front chamber and oil return in the rear chamber
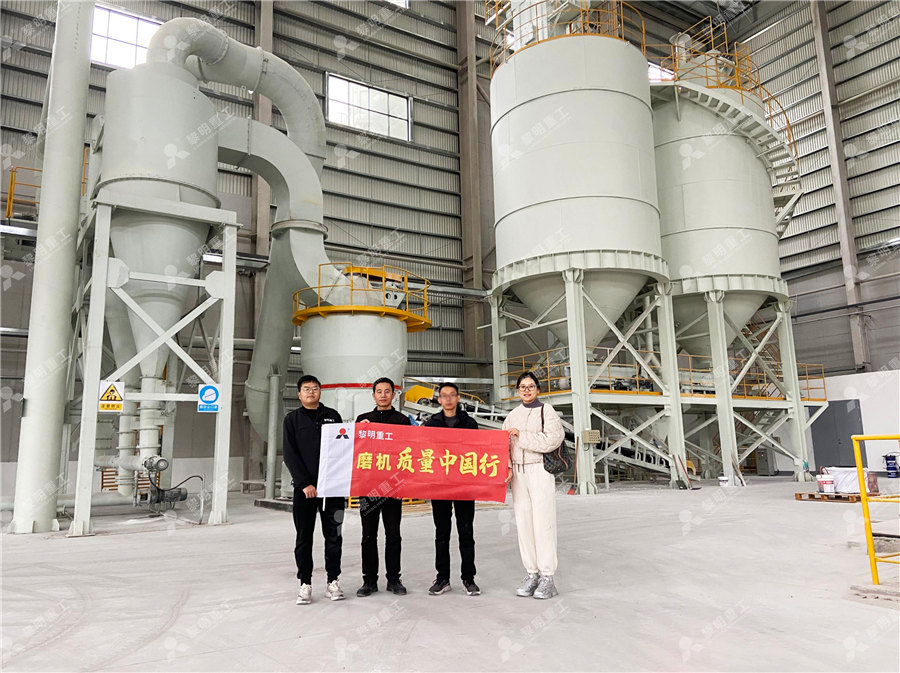
Percussion characteristic analysis for hydraulic rock drill
2019年4月19日 The pressure in the impact piston’s frontchamber and rearchamber, and valve’s leftchamber and rightchamber was tested synchronously The sampling frequency could reach 2048 kHz with 40 opening channels In order to ensure optimal working parameters of impact system for the new hydraulic rock drill drifter controlled by sleeve valve, the performance test system is built using the arm and the Impact performance for high frequency hydraulic rock drill drifter 2014年1月1日 Based on the research of hydraulic rock drill with no constantpressurized chamber which is the most popular type, dynamic simulation of numerical calculation and test Dynamic simulation and test research of impact performance of 2024年10月14日 Yang et al 8, 9 constructed a numerical model of hydraulic rock drill impact system by Amesim for front constantpressurized chamber hydraulic rock drills, then optimized Experimental study on impact coupling characteristics of high
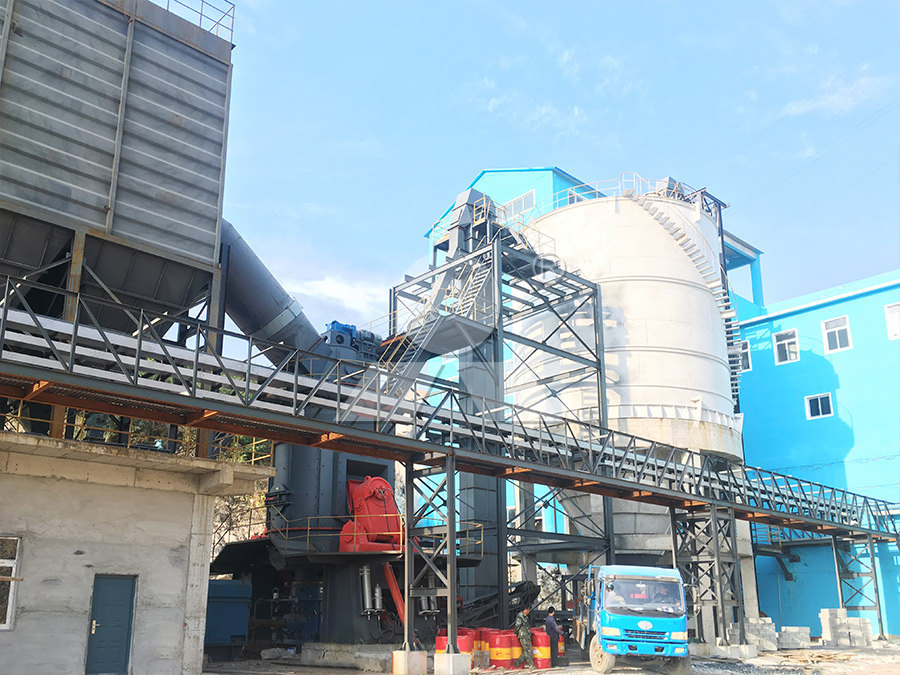
(PDF) Impact System Dynamic Characteristics of Hydraulic Rock
2018年9月19日 The inner mechanism experiment of the hydraulic rock drill was designed to test the pressure characteristic curves in the piston of the frontrear chamber and in the reversing 2019年4月19日 Simulation results of the percussion system: (a) pressure curves of impact piston’s frontchamber and rearchamber, valve’s leftchamber and rightchamber; (b) Percussion characteristic analysis for hydraulic rock drill with no The inner mechanism experiment of the hydraulic rock drill was designed to test the pressure characteristic curves in the piston of the frontrear chamber and in the reversing valve of the Impact System Dynamic Characteristics of Hydraulic Rock Drill 2018年10月9日 Their movement obeys the principle of hydraulic slave The pressure in frontchamber and rearchamber exchanges under a certain frequency The frequency of rock drill Percussion characteristic analysis for hydraulic rock drill with no
.jpg)
Analysis and optimization of the working parameters of the impact
2017年7月7日 This study provides a theoretical basis for the design and optimization of the impact system parameters of the hydraulic rock drill with a sleeve valve An impact system is 2014年1月31日 The inner mechanism experiment of the hydraulic rock drill was designed to test the pressure characteristic curves in the piston of the frontrear chamber and in the reversing Dynamic simulation and test research of impact performance of Aspects of software design that predict ‘in time’ wellbore hydraulics by coupling downhole drilling fluid rheology to annular pressure in the absence of PWD measurements while tripping and casing are also described that further improve the capability to manage bottomhole pressure and wellbore security in crucial narrow hydraulic operating windowsDrilling Hydraulics an overview ScienceDirect Topicschamber, whereas that for stroke motion is called the back chamber Common hydraulic drifter are categorized into two types according to the pressure change in the front and back chambers The first type exhibits normal pressure in the front chamber, and the back chamber serves as the control; hence, this drifter is called the backchamber Analysis on the Main Design Parameters Influencing the Impact
.jpg)
(PDF) Influence of Piston Mass and Working Pressure
2023年10月25日 Accordingly, when developing a hydraulic rock drill, it is advisable to select a shorter piston and a higher working pressure, thus allowing the drill to provide good impact performance Discover 2019年4月19日 Pressure curves of the piston’s frontchamber and rearchamber, and valve’s leftchamber and rightchamber were obtained by field rock drilling test Then, the velocity curve of impact piston was obtained after judging the striking point through the feature of rearchamber’s pressure spike, so were the rock drill’s impact energy, impact frequency, and impact powerPercussion characteristic analysis for hydraulic rock drill with 2018年10月9日 Pressure curves of the piston’s frontchamber and rearchamber, and valve’s leftchamber and rightchamber were obtained by field rock drilling test Then, the velocity curve of impact piston was obtained after judging the striking point through the feature of rearchamber’s pressure spike, so were the rock drill’s impact energy, impact Percussion characteristic analysis for hydraulic rock drill with no 2018年8月7日 The inner mechanism experiment of the hydraulic rock drill was designed to test the pressure characteristic curves in the piston of the frontrear chamber and in the reversing valve of the left Effects of Double Damper System’s Floating Characteristic on
.jpg)
Percussion characteristic analysis for hydraulic rock drill with no
Pressure curves of the piston’s frontchamber and rearchamber, and valve’s leftchamber and rightchamber were obtained by field rock drilling test Then, the velocity curve of impact piston was obtained after judging the striking point through the feature of rearchamber’s pressure spike, so were the rock drill’s impact energy, impact Key words: hydraulic rock drill, double damper system, key parameters, design example, dynamic simulation 1 Introduction Hydraulic rock drills were widely used in mining, coal mine roadway excavation, railway tunnel, highway tunnel and rock excavation projects with advantages of highefficiency, clean, safety and so on [1 – 3]2019 ПРИКЛАДНАЯ МЕХАНИКА DESIGN ON KEY PARAMETERS 2012年1月1日 Pressure curves of the piston’s frontchamber and rear point through the feature of rearchamber’s pressure is belonging to the doublechamber scavenge oil hydraulic rock drillDynamic Simulation of the Impact Mechanism of Hydraulic Rock Drill 2017年7月7日 An impact system is the core part of the hydraulic rock drill The dynamic simulation model of the hydraulic impact system is established based on the system simulation platform AMEsim We used the AMEsim simulation model to verify the displacement, velocity curves of the piston, and valve by using stress wave testing data The following key features of Analysis and optimization of the working parameters of the impact
.jpg)
Percussion characteristic analysis for hydraulic rock drill with no
Pressure curves of the piston’s frontchamber and rear chamber, and valve’s leftchamber and rightchamber were obtained by field rock drilling test Then, the velocity curve of2019年11月28日 A high frequency hydraulic rock drill drifter with sleeve valve is developed to use on arm of excavator In order to ensure optimal working parameters of impact system for the new hydraulic rock Design on Key Parameters of Double Damper System for Hydraulic Rock DrillAs shown in enlarged figure of areas “b and c,” the overlapped reversing valve contributes to appearance of a higher peak when the pressure changes in the front chamber and rear chamber, the peak valve of pressure can get to 30∼37 MPa, and the peak is relatively stable when pressure transitions between the front chamber and rear chamber with underlapped and overlapped Impact System Dynamic Characteristics of Hydraulic Rock Drill 2019年4月19日 Pressure curves of the piston’s frontchamber and rearchamber, and valve’s leftchamber and rightchamber were obtained by field rock drilling test Then, the velocity curve of impact piston was obtained after judging the striking point through the feature of rearchamber’s pressure spike, so were the rock drill’s impact energy, impact frequency, and impact powerPercussion characteristic analysis for hydraulic rock drill with
.jpg)
Cavitation erosion of the damping piston in double damping
2018年11月1日 Pressure curves in the primary, secondary damping chamber and noise spectra of cavitation were obtained by the field rock drilling test The simulation and experimental results had consistency2023年1月12日 The hydraulic rock drill is the main working mechanism of the hydraulic drill rig, but it has high technical content, complex structure, and high requirements for use and maintenance, while hydraulic drill rig is widely used in coal mine excavation, once the hydraulic rock drill breaks down, it will cause the drill rig to stop production, thus affecting the progress Working Principle and Precautions of Hydraulic Rock DrillThe hydraulic rock drill with no constantpressurized chamber impact mechanism has an advantage of high energy utilizationHowever, the antechamber's cavitation may lead to the erosion of its piston and front bushIt can severely impact the rock drill's normal operationIn this study, the operating principle of the impact mechanism was introducedConsidering the Cavitation mechanism for hydraulic rock drill with no constant Rock drill You need a rock drill that lets you focus on drilling accurate blow and support holes Fast and safe The RD100 has a soft start function that is easy to reach with one hand This means you can work with more precision, and collaring is made especially easy When it’s time to go faster, the RD100 is one of the most powerful drills onEpiroc HRD100 Hydraulic Rock Drill brochure
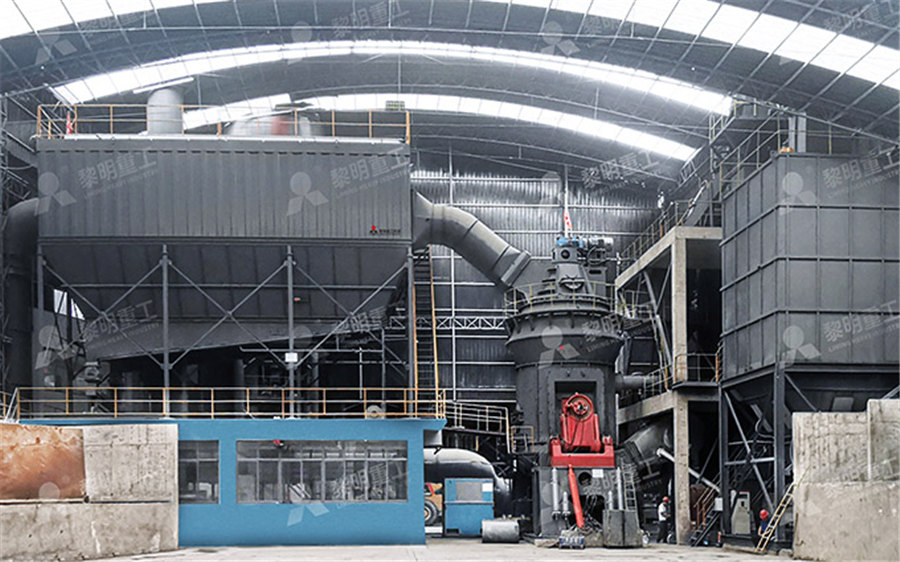
Cavitation mechanism for hydraulic rock drill with no constant
2016年12月1日 The hydraulic rock drill with no constantpressurized chamber impact mechanism has an advantage of high energy utilization However, the antechamber's cavitation may lead to the erosion of its 2017年7月7日 An impact system is the core part of the hydraulic rock drill The dynamic simulation model of the hydraulic impact system is established based on the system simulation platform AMEsim We used the AMEsim simulation model to verify the displacement, velocity curves of the piston, and valve by using stress wave testing data The following key features of Analysis and optimization of the working parameters of the impact 1985年8月1日 Oil hydraulic rock drills have been used on the field of mining and public works This paper treats the percussion type rock drill, which is driven by the interaction of a piston and valveStudies on the Design of Oil Hydraulic Rock Drill (1st Report hydraulic rock drills Yelin et al derived a change law for hydraulic oil in test holes for cylinder blocks and other important components of hydraulic rock drills They established a mathematical model of a hydraulic rock drill and provided a theoretical basis for the fault diagnosis and improvement of hydraulic rock drills [7] Jakobsson et Hydraulic Rock Drill Fault Classification Using XVectors
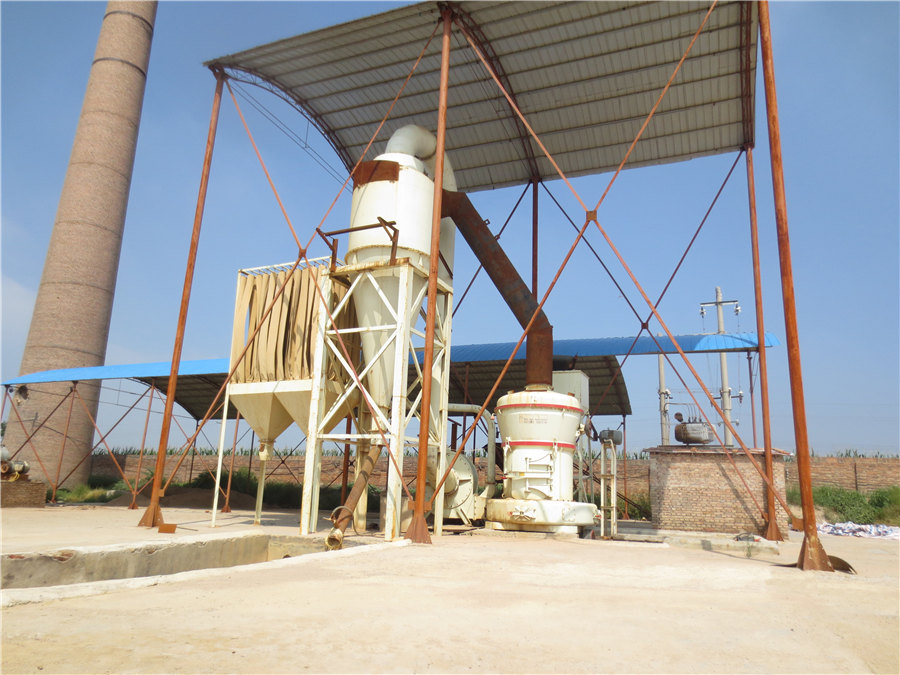
Research on the Matching of Impact Performance and Collision
2021年3月8日 ESM for the impact energy was 1307, and ESM for impact frequency was 769% Li [11, 12] and Li et al [13] presented the research results on impact performance of hydraulic rock drill Zhang [14 2022年10月29日 This work describes the collection and properties of the publicly available rock drill fault classification data set rockdrill11, used for the 2022 PHM Conference Data Challenge(PDF) Dataset for Fault Classification in Rock Drills, a Fast 2024年6月21日 In response to the issues of overheating of the shell and insufficient impact energy of the hydraulic rock drill, this paper focuses on the hydraulic rock drill with alternating front and rear Impact performance optimization for hydraulic rock drill based 2024年6月21日 Hydraulic rock drills, known for their costeffectiveness, rapid operation, and strong adaptability, play a vital role in tunnel excavation, mining operations, and piercing through iron mouths 1–3 The development of new hydraulic rock drills is characterized by high frequency, high power, and intelligent features The hydraulic rock drill features alternating front and rear Impact performance optimization for hydraulic rock drill based
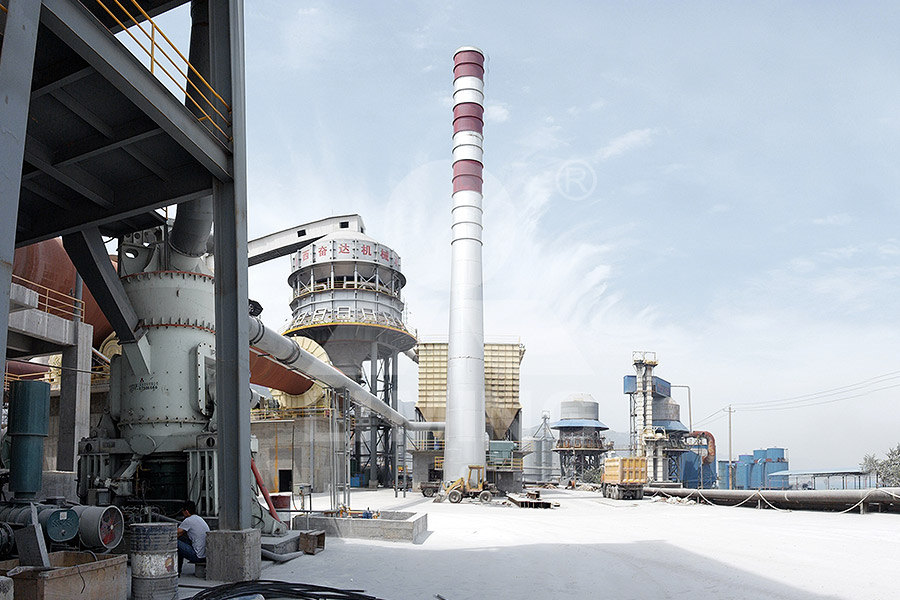
Analysis and optimization of the working parameters of the impact
2017年7月1日 Yin et al [17] built a model for the impact mechanism of hydraulic rock drill with AMESim software and obtained the displacement curves of the piston and valve core, and the pressure of the DOI: 101016/JAUTCON201512012 Corpus ID: ; Hydraulic–mechanical coupling modeling by bond graph for impact system of a high frequency rock drill drifter with sleeve distributorHydraulic–mechanical coupling modeling by bond graph for Rock drill You need a rock drill that lets you focus on drilling accurate blow and support holes Fast and safe The RD100 has a soft start function that is easy to reach with one hand This means you can work with more precision, and collaring is made especially easy When it’s time to go faster, the RD100 is one of the most powerful drills onHRD100 Hydraulic rock drill First Breakon hydraulic rock drills Therefore, investigating the structural factors influencing the impact characteristics of hydraulic rock drills with alternating front and rear return chambers holds significant importance4,5 As the reliability of hydraulic rock drills continues to improve, there is increasing research on the factorsImpact performance optimization for hydraulic rock drill based
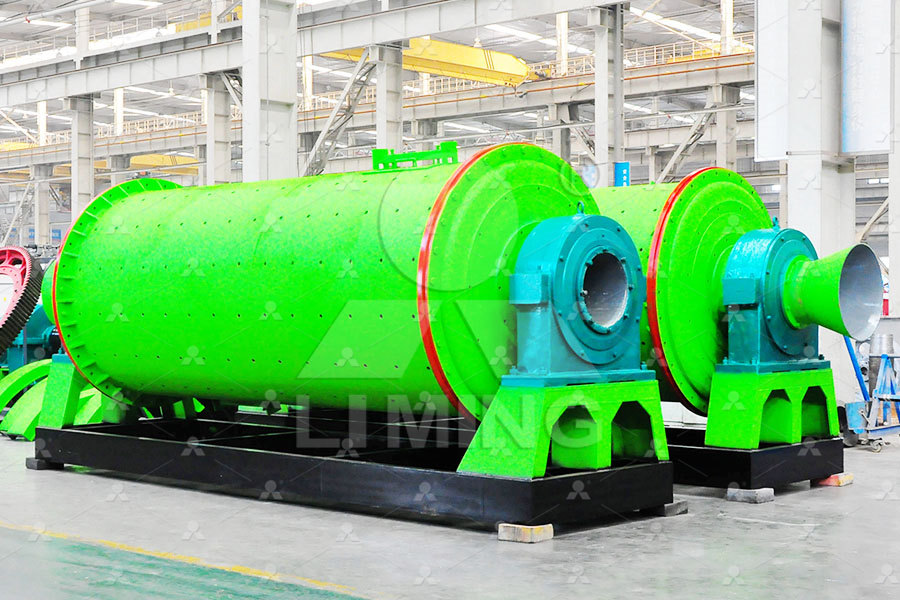
Key problems in hydraulic rock drill design ScienceDirect
1987年1月1日 (4) Among the curves in Fig 5: (1) M is the largest opening for the front chamber and 1 M for the rear, thus the oil flows into two chambers alternately, without interruption (2) Both front and rear chamber have a closed stage between oil charging and dis charging; X for the rear chamber and Y for the frontThe operating principle of hydraulic impact mechanism with doublechamber oil scavenger is introduced with the formula of its piston's moving velocity given To minimize the energy loss due to piston shoulder in sealing section,the formula to calculate the gap between piston and inner surface of cylinder block and oil sealing length are provided Analyzing the energy loss due to Design on Part of Structural Parameters of Hydraulic Rock Drill2022年12月15日 Although the current hydraulic power pipe tong can improve efficiency and reduce strength, there are still some deficiencies Among them, the inevitable defects are a low degree of automation (PDF) Design and Performance Analysis of Hydraulic System of WaterHydraulic Robotic Drill 5 pass the flrst from entering the oil fllled bearing chamber A vent to outside is provided between the two sealsDevelopment of a WaterHydraulic SelfPropelled Robotic Drill
.jpg)
Impact performance optimization for hydraulic rock drill based
2024年6月21日 Hydraulic rock drills, known for their costeffectiveness, rapid operation, and strong adaptability, play a vital role in tunnel excavation, mining operations, and piercing through iron mouths 1–3 The development of new hydraulic rock drills is characterized by high frequency, high power, and intelligent features The hydraulic rock drill features alternating front and rear It is widely used in mining, tunnel excavation, urban construction, and other engineering operations [2] A hydraulic rock drill uses oil as its working medium, converting the pressure energy of Working principle of rock drill Download Scientific DiagramThe hydraulic rock drill is a rock drilling machine that uses highpressure oil as a power to push the piston to impact the drill and attaches an independent rotary mechanism The piston is controlled by the valve (and also has no valve) to reciprocate Since the oil pressure is much higher than the gas pressure, it is more than 10MPaHydraulic Rock Drill Hydraulic Rock Drilling Machine Factory Weight incl oil kg 45 Oil flow l/min 38 Hydraulic oil temperature °C 20 60 Nominal pressure bar 120 Pump type Helical rotor pump, directly driven from the motor shaft Filtration 10µ filter in return line Filter bypass valve Cooling system Water Motor type Inverter controlled 3 phase PM motor Input power kW 10HRD100 Hydraulic rock drill Canadian Mining Expo
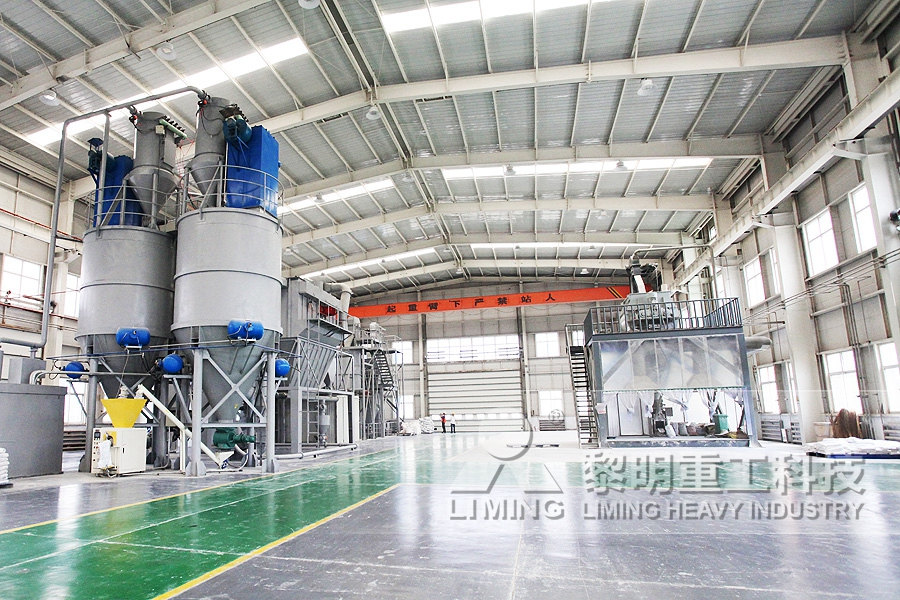
Hydraulic–mechanical coupling modeling by bond graph for
2016年3月1日 Then, the velocity curve of impact piston was obtained after judging the striking point through the feature of rearchamber’s pressure spike, so were the rock drill’s impact energy, impact 2018年2月1日 Hydraulic ram pump is an automatic waterpumping equipment generally used to pump drinking and irrigation water in mountainous and rural areas having short of powerOptimal design and performance analysis of hydraulic ram