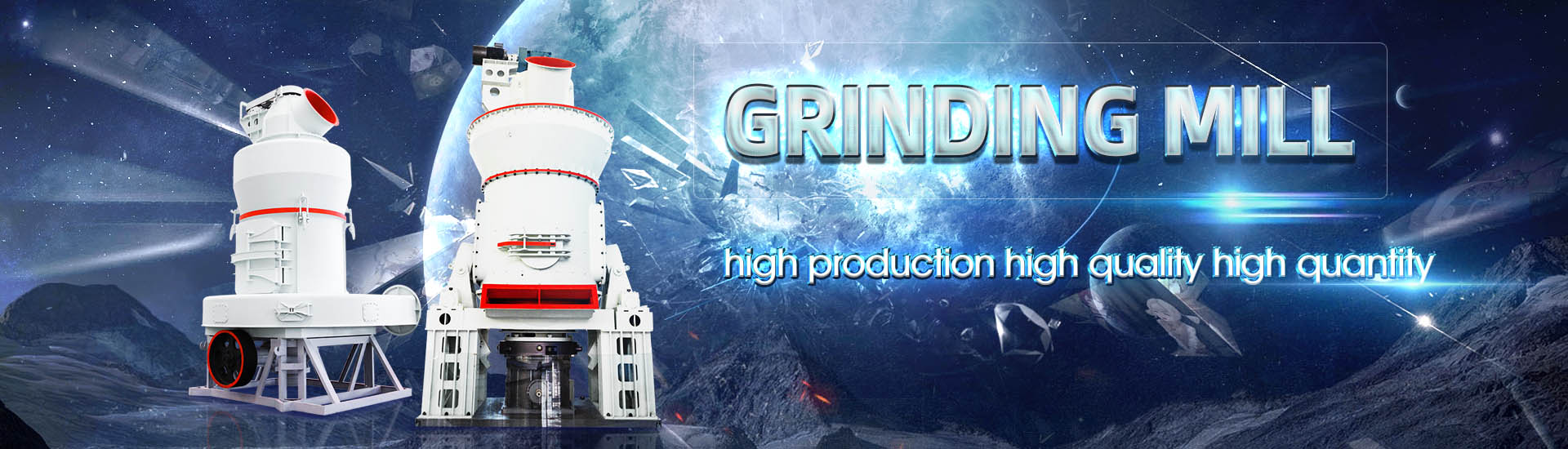
Ore powder production accounting
.jpg)
Metallurgical Accounting Guide (Updated 2024)
2024年2月26日 Metallurgical accounting is a systematic approach involving the measurement, analysis, and reporting of the metal production process, spanning from ore extraction and plant processing to the creation of a final saleable US GAAP Accounting treatment: Capitalize Costs • Development costs are usually carried forward until the mine is commissioned (production begins) because the expenditure is for future benefit from the mineral extraction • Capitalized development costs are then amortized using 2012 Americas School of Mines PwC2020年7月7日 Metal accounting activities in stockpiles cover aspects of ore classification based on the abovementioned grades, bulk density measurements, moisture determination, stockpile volume measurements, calculation and Systematic Framework toward a Highly Reliable Metallurgical accounting is a standard requirement in all mineral processing operations and recognisable at most levels of a mining organisation as an essential input into business reporting processesMetallurgical Accounting in Practice: Performance Non
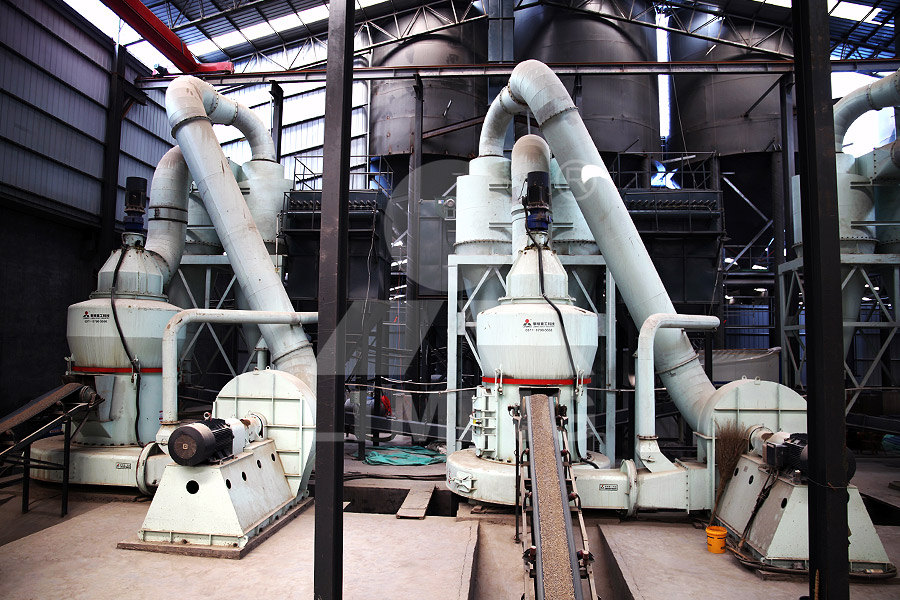
Raw materials management in iron and steelmaking firms
2018年7月23日 This study provides such knowledge by drawing on insights from Höganäs AB, a world leader in ferrous powder metallurgy, and their efforts to identify key aspects and principles of raw materials management Our elaboration of a more holistic view on raw materials 2012年10月29日 Considering all measurement errors, including errors associated at each step of the process – from sampling and analytical errors to measurement errors in circuit instrumentation, can improve theA New Approach to Metallurgical Accounting2020年2月25日 Micon’s metal accounting practices entail an allinclusive view, which starts at the Mineral Resource, includes transfer of ore from the mine to the concentrator, smelter, and refinery, and ultimately into the financial accountsFrom Metal to Money: The Importance of Reliable CONTEXT, Met Op Accounting, the Overall Picture Business Systems Total Values Avg, Cummulated Production Stats Operational KPI Real vs Program Line/Area Values Process Values Consumables Data AggregationValidation Operational Contexts Inventories Functional From Material Balance to Operational Accounting Sigmafine
.jpg)
Metal Accounting Centre for Minerals Research
Metal accounting research is ‘themed’ into measurement network design and accounting for multiple ores sources This research was initiated in 2004, and has involved a number of industrial test campaigns on mining operationsAs a primary constituent of renewable biomass fuel, lignin can be effectively utilized as a reducing agent in the ironmaking process, thereby significantly mitigating CO 2 emissions throughout the procedure This study meticulously evaluates the impact of lignin on the reduction of iron ore powder across diverse levels of mechanical activation through thermogravimetric analysisReduction characteristics and mechanism of mechanically 2022年7月30日 PDF In order to study in depth the differences in basic characteristics between iron ore fines commonly used by a steel company, and guide the Find, read and cite all the research you need (PDF) Study on the Basic Characteristics of Iron Ore Definition Direct Labor Costs can be defined as payroll costs that are incurred to manufacture a certain product These are the costs that can directly be traceable and attributable to a certain product In other words, direct labor can also be referred to as the wages that are paid to employees and the payroll who work directly on manufacturing products and bring them to a Accounting For Direct Labor Costs – Definition, Example, And
.jpg)
Intelligent Optimization and Impact Analysis of Energy Efficiency
2024年11月5日 In the complex production chain of steel, sintered ore is the most important raw material in the ironmaking process, and its production scale has exceeded 1078 billion tons in 2022 Notably, it is worth stating that the sintering process accounts for the secondlargest proportion of energy consumption and carbon emissions in the steel manufacturing process, 2024年2月26日 Oxidised pellets have become an indispensable highquality charge for blast furnaces Nevertheless, highquality pellet feeds are becoming scarcer and scarcer To broaden the range of sources of pellet feeds and reduce the production cost of pellets, more steel mills are predicted to use coarse iron ore fines with a relatively low iron grade and low impurities for the Grinding of Australian and Brazilian Iron Ore Fines for LowCarbon process stages, the ore is exposed to a number of heat cycles, which lead to material oxidation35 Therefore, the pellets and the iron ore fines mainly consist of hematite (Fe 2O 3) by the end of their manufacturing process In this study, iron ore powder fines, collected from the iron ore pelletization process, with a size range between 10 Laserassisted reduction of iron ore using aluminum powder DiVA2021年9月6日 Before smelting, the ore must be broken utilizing mechanical methods such as crushing and milling because of lowergrade content The industrial production of iron powder started in 1937 in the USA [3, 4]Ore powder production is generally executed by the ball milling method that requires reduplicative ball milling []Multistage crushing together with the ball Micronsized ore powder production by propulsion and rapid
.jpg)
Techtonica Database Item Details
Copper Ore Powder: contentcopy Created by threshing Copper Ore doublearrow: Category: Threshed Resources menu: Stacksize: 500 autoawesome: Threshable Production Quantity: 1 rotateright: Base Production Speed: 30 sec precisionmanufacturing: Produced in: Thresher Thresher MKII: Recipe 2 (Chrushing) settings 1 Electrical Industry: The electrical and electronic industries are the areas where copper is used most, accounting for more than half of the total consumption, for the production of cables and wires, motors and transformers, switches, manufacturing of industrial valves and fittings, meters, plain bearings, molds, heat exchangers and pumps 2 Copper Ore powder processingWhen production of the group exceedsthe standard – 200 pieces per hour – each employee in the group ispaid a bonus for the excess production in addition to wages at hourlyrates The bonus is computed thus: the percentage of production in excessof the standard quantity is found, and one half of the percentage isregarded as the employees' shareChapter 7: Accounting for labour2022年4月1日 The use of iron ore tailing as total LP replacement showed great potential for use as raw material for concrete roof tiles production, allowing the correct disposal and development of new, more Effect of Iron Ore Tailing and Glass Powder on
.jpg)
(PDF) Influence of Sinter Parameters on CO Emission in
2022年7月15日 Carbon monoxide is the major hazardous component in flue gas exhausting from the iron ore sintering This study aims to reduce the CO emission by changing the sinter parameters by sintering pot 2022年1月1日 Turning to iron ore exports and imports, the tonnages are summarized in Table 11 for 2012 and 2018 (Australian Department of Industry, Science, Energy and Resources, 2021; US Geological Survey, 2020; United National Conference on Trade and Development (UNCTAD), 2021)As shown in Fig 13, China is the largest iron ore importing country and imported about Introduction: Overview of the global iron ore industryPDF On Jul 11, 2018, Guangrong Li published The Chinese Iron Ore Deposits and Ore Production Find, read and cite all the research you 300 million tons, accounting for 05% of the total (PDF) The Chinese Iron Ore Deposits and Ore Production2023年4月16日 Chromium ore is an important metallic raw material that is widely used in the metallurgy industry, chemical industry, and refractory Clarifying the consumption mechanism of chromium ore is crucial for policy making, enterprise production, and commodity investment Based on the signal decomposition tool and Scurve model, a new hybrid complete ensemble Exploring Chromium Ore Consumption: New Perspectives from
.jpg)
Ironore concentrates in ironpowder production ResearchGate
2009年9月1日 Iron powder may be produced from natural iron ore The production of ironore superconcentrates containing less than 03% silica for ironpowder manufacture is consideredAssume Quality Chicken uses the production method of accounting for byproducts What are the ending inventory values for each joint product on July 31,2012 , It purchases cocoa beans and processes them into two intermediate products: chocolate Chapter 16, Cost Allocation: Joint Products and Byproducts2024年2月15日 The global annual production of steel is approximately 2 billion tons, accounting for 8 % of the world's energy demand and 7 % of carbon dioxide (CO 2) emissions in the energy sectorCoalbased direct reduced iron (DRI) reduces CO 2 emissions by 38 % compared with traditional blast furnace–basic oxygen furnace (BFBOF) ironmaking Using a combination gas Direct reduction of iron to facilitate net zero emissions in the steel 2017年2月14日 In the zeal for opening up new orebodies, or for extracting the ore from attractive bodies already opened up, we very often lose sight of the fact, that, 911 Metallurgist is a trusted resource for practical insights, solutions, and support in mineral processing engineering, helping industry professionals succeed with proven expertise Cost Accounting in MiningCost Accounting in Mining 911Metallurgist
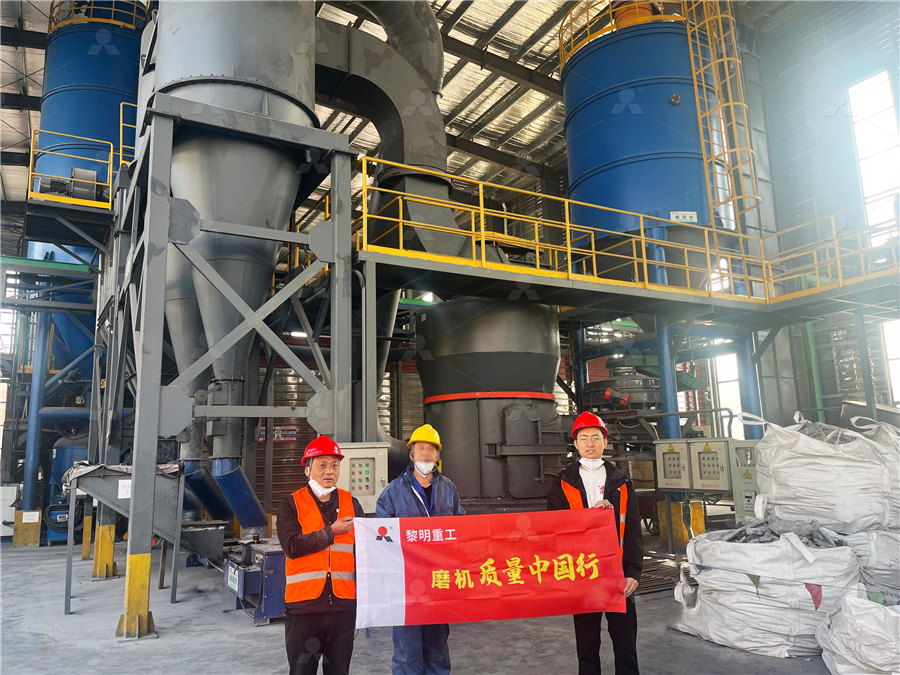
A review of tantalum resources and its production ScienceDirect
2023年10月1日 Ta can also be recovered from tin smelting slag, lithium ores, endoflife tantalum products, etc, and they can account for 37% of the total Ta production The HF leaching−solvent extraction−sodium potassium fluorotantalate reduction process is the most widely used technology in producing Ta2023年9月5日 12 The primary determining factors of powder particle shape: The shape of powder particles depends on the method of powder production For instance, electrochemical processes produce dendritic particles; reduction Powder Metallurgy: A Comprehensive Guide for 2024年1月13日 After Germany, the United States, the Soviet Union, and Japan used powder metallurgy technology to produce cemented carbide; and iron powder was produced by vortex grinding, solid carbon reduction, and molten metal atomization; powder metallurgy ironbased parts were developed; sintered friction materials were put into production; and metal button Powder Metallurgy SpringerLink2019年1月1日 Implementation of ActivityBased Costing Method in Calculating Production Cost of Coffee Powder Manufacturing Company In Aceh January 2019 DOI: 104108/eai3102018Implementation of ActivityBased Costing Method
.jpg)
The proportion of each particle size of iron ore powder
Therefore, the basic characteristics of iron ore powder of −1 mm, −3 mm, and −5 mm particle sizes were studied, and the basic characteristics of different particle sizes were studied to Here, we delve into the key components and technologies that make up the modern ore powder production process Key Components of Ore Powder Production Equipment: 1 Crushers The initial step in ore powder production is the reduction of ore size, which is accomplished by crushers Jaw crushers, cone crushers, and impact crushers are commonly Advancements in ore powder production process equipment: 2023年7月21日 A novel ambient condition production of superior strength, nonabrasive, nonsticky iron ore pellets devoid of undesirable fines under the compression stress of 4 kN is presented(PDF) Effect of Gangue Distribution on Compressive Strength of Iron Ore Let’s journey through time and explore the history of aluminium production The story of aluminum began in the 19th century when it was considered a rare and precious metal The journey of aluminium, from ore to powder, is truly fascinating Through From Ore to Powder: the Fascinating Journey of Aluminium
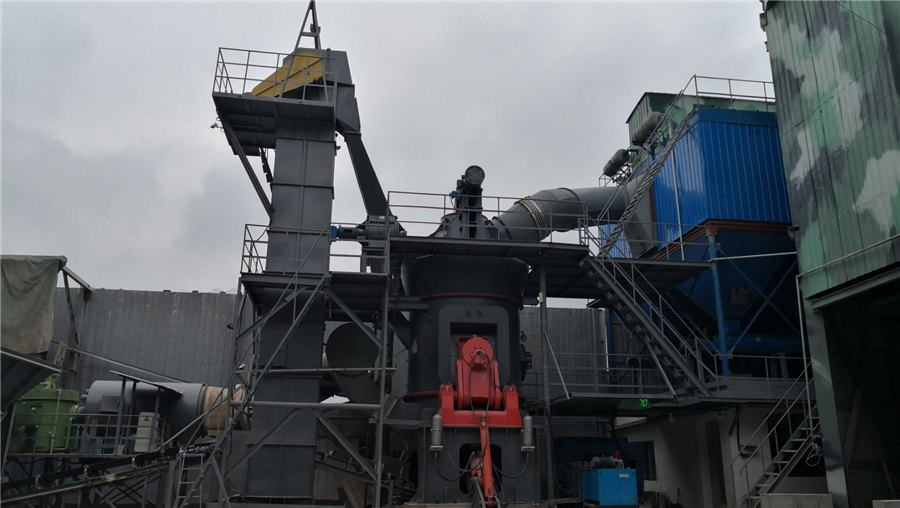
Micronsized ore powder production by propulsion and rapid
2021年9月6日 Request PDF Micronsized ore powder production by propulsion and rapid unloading of highpressure gas We describe a micronsized ore powder production by propulsion and rapid unloading of high 2008年1月1日 The production of iron metal with low greenhouse gas emissions can be performed by electrolysis However, the electrolytic reduction of iron ore is not a technique that has reached a high degree Iron Metal Production by Bulk Electrolysis of Iron Ore Particles isij , , , , , , , , , , , , , , , , ,Mineralization Characteristics of Iron Ore Sinter and the Effects of 2022年1月1日 Australia’s mineraldependent economy faces several challenges that add uncertainty to the sustainability of iron ore supplies Adapting to carbon constraints, potential tax changes, land use conflicts, social license issues, changing global demands, and the risks of trade disputes all require an indepth understanding of Australia’s iron ore resources, Iron ore in Australia and the world: Resources, production
.jpg)
Laserassisted reduction of iron ore using aluminum powder
2023年3月15日 This study reports on the laserassisted reduction of iron ore waste using Al powder as a reducing agent Due to climate change and the global warming situation, it has become of paramount 2023年9月6日 3 Drying: After crushing, the talc ore is typically dried to remove moisture This step is crucial to prevent clumping and improve the flow characteristics of the powder Various drying techniques can be employed, including rotary dryers, fluidized bed dryers, or flash dryers 4 Milling: The driedTalcum Powder Production Process2014年11月17日 Chromite ore processing residue (COPR) is a waste byproduct of chromate production that contains high levels of hexavalent chromium (Cr[VI]) Although the high temperature chromite process was (PDF) A Review of Chromite Ore Processing Residue (COPR): Past 2022年5月6日 In this study, based on the hightemperature basic characteristics of iron ore powder used in the experiment, sinter pot tests were carried out with different lowsilicon ore ratios, and the (PDF) Study on Influencing Factors of HighTemperature Basic
.jpg)
Production and Sales Report 2022 Vale
2023年1月31日 • Iron ore production totaled 308 Mt in 2022, 2% lower y/y, mainly due to (i) licensing delays at Serra Norte; and (ii) jaspilite waste processing and operational performance at S11D This was partially offset by (i) continued production rampup at Vargem Grande; (ii) higher dry processing production at Brucutu; and (iii) higher thirdparty purchasethe reduction reaction, iron ore powder had the highest reaction rate, with iron ore powder reduced by approximately 0055%/s The higher the temperature, the greater the reaction rate Subsequently, the reaction rate of iron ore powder rapidly decreased; at this stage, the reaction rates between different temperatures were insignificant, and theEffect of temperature and reaction path interaction on fluidization 2024年1月22日 Crrich electroplating sludge (CRES) is a complicated solid waste with high contents of chromium and iron It can be used as a main feed of the FINEX ironmaking process, which requires gasbased reduction before smelting reduction to produce molten iron with the proper addition of iron ore powder In this study, the CO–H2 gasbased reduction behavior of COndash;H2 GasBased Reduction Behavior of CrRich MDPIManganese ore powder agglomeration method mainly comprises the group of pressure, sintering and three kinds of techniques of pelletizingAt present, sintering process is adopted in the manganese ore agglomeration more in the worldIn these several main methods, the group's of pressure method technique is simple, production cost low and environment is good, but Sintering process of manganese ore powder Google Patents
.jpg)
(PDF) Coproduction of DRI Powder and Semicoke from Siderite Ore
2015年11月26日 PDF Effective utilization of low grade iron ore and low rank coal by excessive coalbased direct reduction process to coproduce DRI powder and Find, read and cite all the research you need