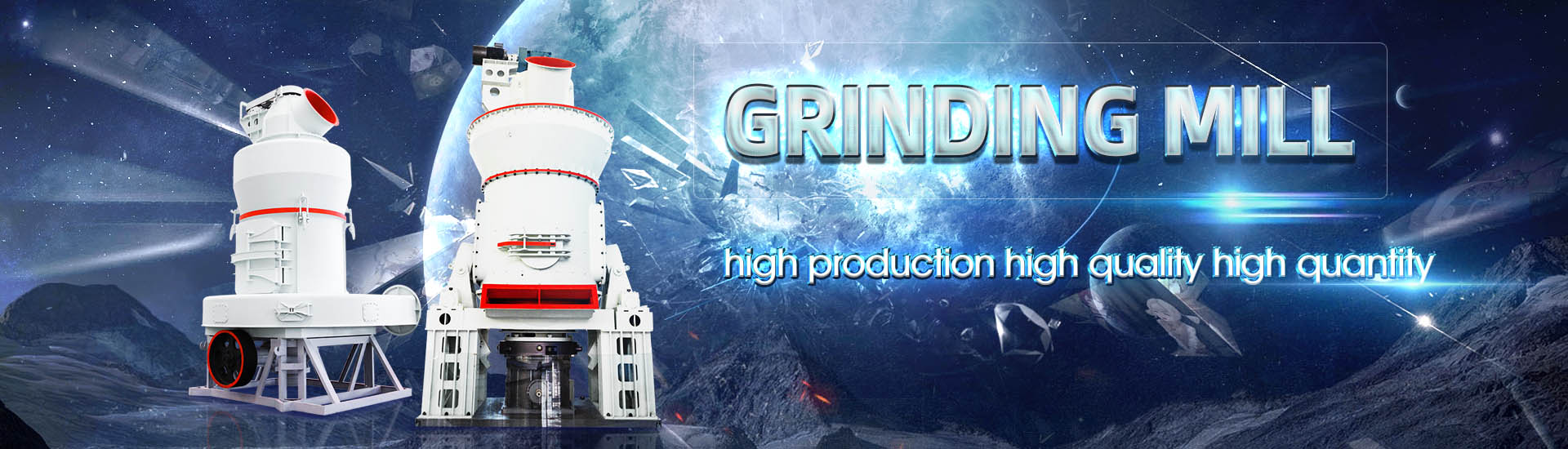
Coke drum mechanical screen AK
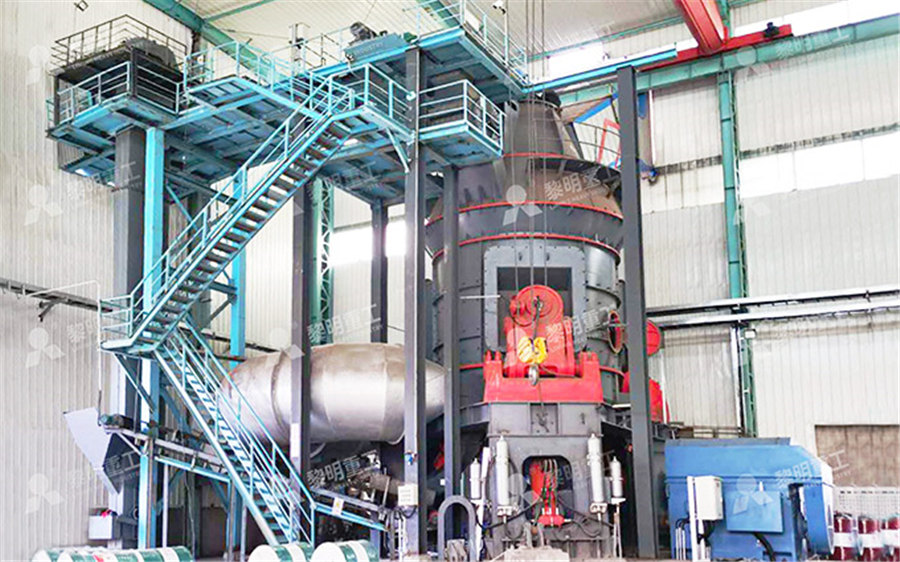
COKE DRUM DESIGN – LONGER LIFE THROUGH INNOVATION
In addition, coke drums typically experience significant down time during their useful life to make needed repairs or partial shell replacements due to the damage caused by the service Skirt and shell failure modes that are common in coke drums can lead to leaks and fires Drum design, fabrication, and operation influence coke drum life Premature drum replacement can Failure Modes and Inspection Needs of Coke DrumsTo help understand and predict the behavior of the most common types of shell cracks in a set of coke drums, crack propagation assessment procedures from API 5791/ ASME FFS1 of 2007 Development of Crack Screening Guidelines for Coke Drums• Field of Expertise: Coke drum mechanical integrity coker crane structural integrity management, fire damage assessment, tankage mechanical integrity programsCoke drums inspection, assessment, and life extension
.jpg)
Laser Scanning Ameriscan LLC
Ameriscan uses the most advanced laser scanners to provide an accurate dimensional profile of new and inservice coke drums without the need for errorproducing vibration filters By using In the Operating Coke Drum, the material from the Coker Furnace, at high temperature and low pressure, is injected into the bottom of the drum and is further ‘cracked’ into (1) gaseous Coking 101 An Introduction to Delayed CokingToday, WSI is the largest provider in the industry of structural repairs for coke drums Our unique process consists of installing a highly engineered weld metal overlay to the existing vessel to WSI Coke Drum Services Industryleading Engineered SolutionsDetermine actual cyclic stress in shell and skirt Perform structural, mechanical and metallurgical evaluation of the drum Develop Long Term Operation, Inspection, Repair and Replacement Coke Drum Inspection Overview and Management Tools for Coke
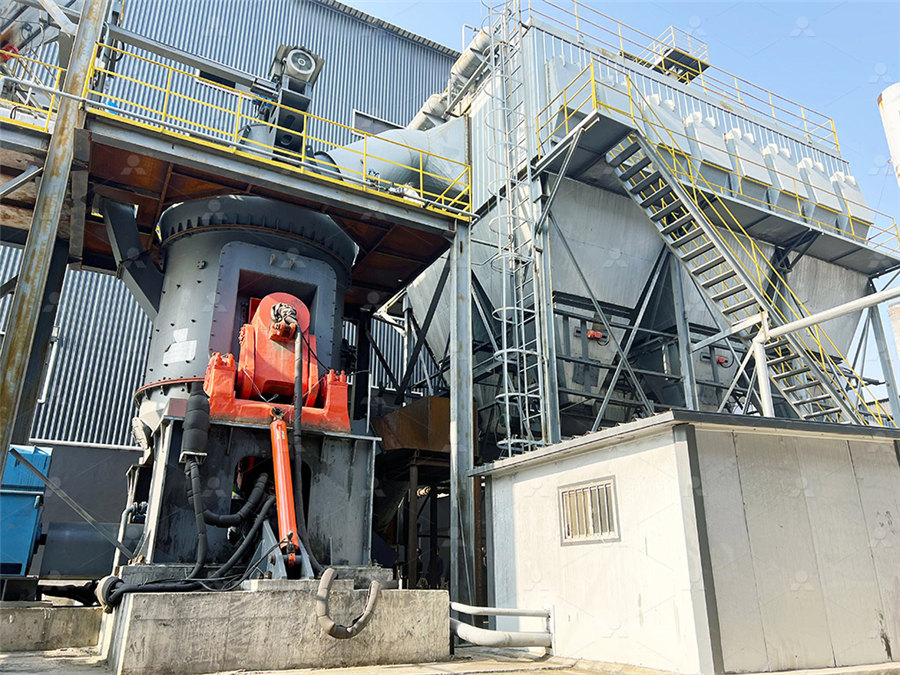
Inicio cokedrumintegrity
CDI is a Houstonbased company that has a team of specialist engineers and technical inspectors with decades of experience in providing technical support for the inspection and structural COKE DRUMS ISSUES •Coke drums are special pressure vessels subjected to strong and varied transient loads •They are expensive items with a long manufacturing cycle, therefore a COMPREHENSIVE LIFE ASSESSMENT OF A COKE DRUM Refining API INSPECTION MECHANICAL INTEGRITY SUMMIT Coke Drum Lifecycle Efforts Summary • Coke drum history • Type of turnarounds within the Coker and why – intent for doing module TA’s? • Drum integrity management and replacement timeline • Sustainable module strategy to manage drum integrity pre/post replacementCoke drums inspection, assessment, and life extensionEffect of Banana Effect in Stress Analysis of Coke Drum Piping of a Delayed Coker UnitFull Paper2019pdf Free download as PDF File (pdf), Text File (txt) or read online for free The document discusses the "Banana Effect" Effect of Banana Effect in Stress Analysis of Coke Drum
.jpg)
Assessment of Coke Drum Materials Based on ASME Material Property
2015年12月1日 Coke drums operating under such conditions require proper design and material selection in order to sustain the high stresses caused by the thermal–mechanical loading This paper has the objective to explore alternative material selections for coke drum applications based on material property data provided in ASME Boiler Pressure Vessel Code, Section 2014年7月1日 [Show full abstract] thermalmechanical cyclic fatigue tests of coke drum materials were firstly conducted to obtain strainlife curves, Fatigue behaviour of coke drum materials under thermalmechanical 2011年12月1日 Request PDF Global and Local ElasticPlastic Stress Analysis of Coke Drum Under ThermalMechanical Loadings Coke drums are critical equipment in the petroleum industry The failure modes of Global and Local ElasticPlastic Stress Analysis of Coke Drum 2023年5月30日 While coke drum failures are not typically highconsequence failures from a safety MFP, Kummari, SR, Hantz, B, A Comparative Study of the ThermalMechanical Behavior and Fatigue Life Predictions of Different Coke Drum Support Skirt Designs, PVP201765807, Proceedings of the ASME 2017 Pressure Vessels and Piping Leveraging Advanced Analysis for Coke Drum Reliability
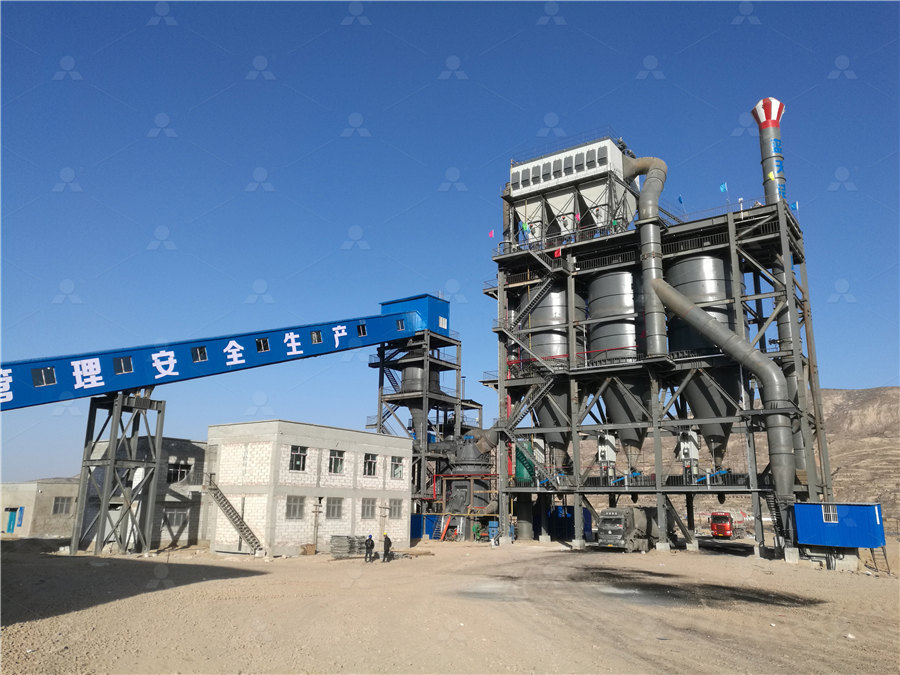
Coking 101 An Introduction to Delayed Coking
the petroleum coke that solidifies in the drum •The other offline drum is steamed, vented, and cooled prior to the drum being opened to atmosphere After the drum is opened, the petroleum coke is cut from the drum using high pressure water Petroleum coke or simply “coke” is similar to coal and is typically used for fuel in power plantsFatigue behaviour of coke drum materials under thermalmechanical cyclic loading Author: Jie Chen Subject: Theoretical and Applied Mechanics Letters, 4 (2014) doi:101063/2Fatigue behaviour of coke drum materials under thermalmechanical Coke drums are a key equipment item on the Delayed Coking Unit and require continuous attention and analysis throughout the equipment lifecycle to help maximize drum life Wood’s extensive analysis has proven that a joint team effort by our Reliability, Process and Operations team can effectively optimize the thermal gradients in the coke drums during operation, Coke Drum Life Cycle Management Refining Community2 Coke Drums Self Destruct • Coke Drums are pressure vessels in batched, thermal cyclic service • Operated for maximum production goals • Cyclic wear and tear from thermal expansion self constraint is seen as metal fatigue and defect crack growths • Eventually leaks happen • And cracks are repaired • And sometimes they are preventedCoke Drum Inspection Overview and Management Tools for Coke Drum
.jpg)
Delayed coker design and project execution DigitalRefining
To provide the required flexibility in the coke drum design to achieve increased capacity via shorter cycle time, proper drum life through consideration for the range of heating/cooling frequencies expected and design drum accordingly, and optimised design for best results, taking into account coking cycle lengths, operating conditions, feed rate, coke yield, and the number 2019年12月4日 Temper bead technique for better mechanical properties to avoid PWHT Optimized weld parameters to minimize HAZ width Largest Coke Drum manufactured; Dia 10 m, Length 35 m Timely delivery Total 72 nos Coke Criticality in Coke Drum Repair2011年10月3日 Coke drums are critical equipment in the petroleum industry The failure modes of coke drums include excessive bulging deformation and fatigue cracking The elasticplastic behavior of a coke drum, subjected to both thermal and mechanical loadings, is analyzed for a complete cycle of operation The effects of multiple operational cycles and localized hot/cold Global and Local ElasticPlastic Stress Analysis of Coke Drum Drain valve left open during coke drum warmup Open vent line on live coking drum Open drain line on drum in warmup mode Align feed to open coke drum Open overhead vapor line on live coking drum Air Free open coke drum Environmental risks: Warmup condensate line left open to MF Open vent line on live coking drumDelayed Coker Coke Drum Valve Operations Integrity Refining
.jpg)
Delayed Coking Operational Optimization Refining Community
– Provide adequate Coke Drum outage – Provide adequate Coke Drum diameter (make note of maximum vapor velocity limit) – Provide adequate number and type of Coke Drum level detectors • Operation – Optimize antifoam injection – – Reduce unit feed rate to reduce vapor velocity in drum – Increase Coker Heater coil outlet temperature 2020年8月3日 The coke drum is subjected to a combination of thermalmechanical loads during operation, so its safety and reliability must be considered in actual productionNumerical Simulation of ThermalMechanical Stress Field of Coke Drum • Skirt and shell failure modes that are common in coke drums can lead to leaks and fires • Drum design, fabrication, and operation influence coke drum life • Premature drum replacement can be avoided and common failures can be effectively managed with proper analysis, assessment (PSI), inspections, and repairsFailure Modes and Inspection Needs of Coke DrumsBecht Engineering Utilizes Mechanical Experts in Coke Drum Repairs 1 Shim plates corroded and ejected 2 Vessel tilted and/or rotated 3 Cracks in steel skirt 4 Cracks in skirt to vessel weld 5 Skirt deformation and buckling 6 Broken, bent and corroded anchor bolts 7A Total Engineered Approach to Coke Drum Skirt and Foundation Repairs
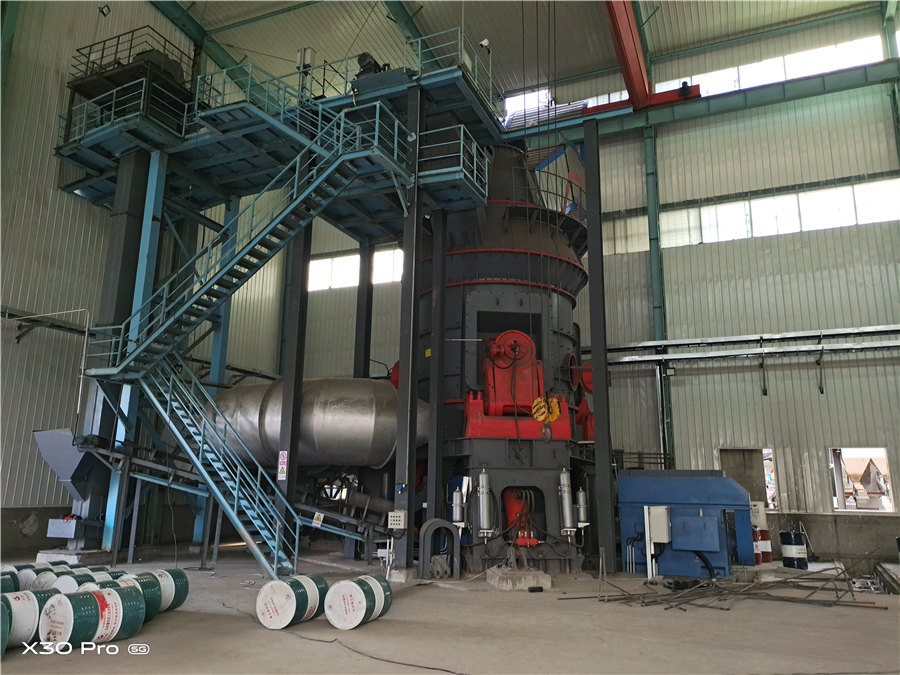
Coking Drum an overview ScienceDirect Topics
The coke drums are on a 48 h cycle (Parkash, 2003; Gary et al, 2007; Speight, 2014, 2017; Hsu and Robinson, 2017) in which the coke drum is usually onstream for ~ 24 h before becoming filled with porous coke after which time the coke is removed by the following procedure: (i) The coke deposit is cooled with water; (ii) one of the heads of the coking drum is removed to permit the 2007年1月1日 A coke drum experiences operating conditions that are severe and unrelenting, and their lifespans reflect this In this paper, a coupled thermalmechanical model of an operating coke drum is StateoftheArt Improvements in Coke Drum Design and1997年1月1日 Shorter cycle times increase productivity but operation and inspection records of coke drums show that shorter cycle times often shorten the drum life There are drums with over 30 years of service that have no major damage while there are others with less than 10 years of service that have bulged and crackedIncreasing the Life of Coke Drums InspectioneeringA case study is presented detailing how the measurement and stress modeling of a coke drum surface profile was applied to a drum where a throughwall crack had occurred 2 COKE DRUM DESIGN, FAILURES AND INSPECTION PRACTICES 21 Coke Drum Design Delayed coke drums are typically designed and built to the ASME “Boiler and Pressure Vessel Code”STRESS ANALYSIS USING ACTUAL COKE DRUM BULGE PROFILES
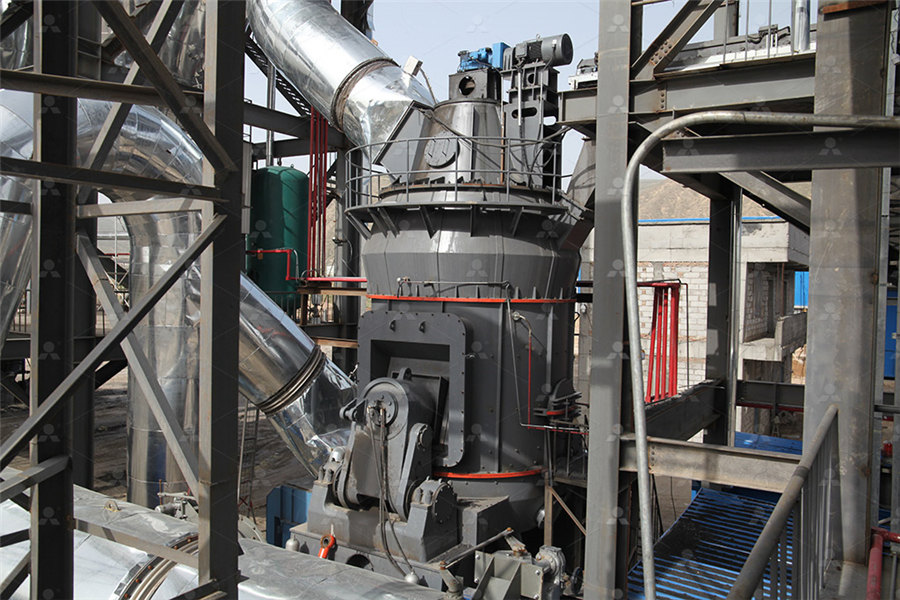
Optimal slot dimension for skirt support structure of coke drums
2018年3月9日 Nikic M Optimal selection of delayed coke drum materials based on ASME Section II material property data Thesis for the Master’s Degree Edmonton: University of Alberta, 2013 Google Scholar Chen J Experimental study of elastoplastic mechanical properties of coke drum materials Thesis for the Master’s Degree2017年1月1日 In this study, the thermalmechanical behavior of multiple coke drum skirt designs, including forged, welded, and sliding configurations is investigated using elastic and elasticplastic finite Probabilistic Life Prediction for Crack Initiation on Coke Drums A 4drum delayed coking unit in a petroleum refinery A delayed coker is a type of coker whose process consists of heating a residual oil feed to its thermal cracking temperature in a furnace with multiple parallel passes This cracks the heavy, long chain hydrocarbon molecules of the residual oil into coker gas oil and petroleum coke [1] [2] [3] Delayed coker Wikipediacracks and bulges in the coke drum and suggested means to improve coke drum life covering design, fabrication, operation, and maintenance Ramos et al [3] presented the mechanical integrity evaluation of coke drums made of Cr–Mo alloys Failure mechanism analysis, field measurement, and numerical studiesGlobal and Local ElasticPlastic Stress Analysis of Coke Drum John
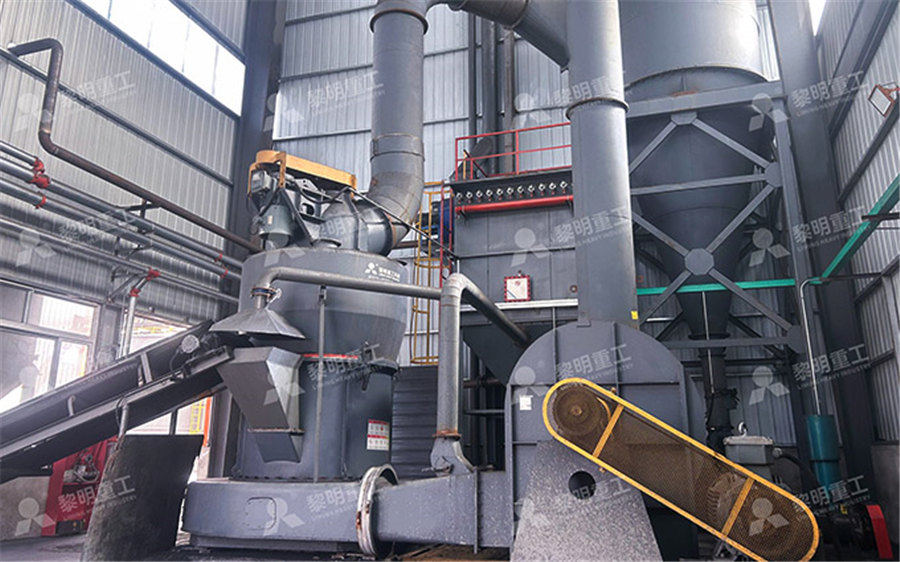
Numerical Simulation of ThermalMechanical Stress Field of Coke Drum
2020年10月28日 Abstract The coke drum is subjected to a combination of thermalmechanical loads during operation, so its safety and reliability must be considered in actual production In each production cycle, the thermal stress generated by temperature fluctuations in the coke drum is the main cause of structural failure Based on this, a longterm service carbon steel coke 2012年9月17日 Coke drums deform due to a complex combination of mechanical and thermal cyclic stresses Bulges have progressive behavior and represent the main maintenance problem related to these drums(PDF) COKE DRUMS INSPECTION AND EVALUATION USING STRESS Download Table Cold strength of coke nuts in drum tests from publication: Quality comparison of coke nuts The strength, reactivity, and technical analysis of coke nuts are discussed Nuts from Cold strength of coke nuts in drum tests Download Tabletemperature to about 500°C (930°F) The coke drum then separates lighter vapours out of the crude, including hydrocarbon gases During quenching, the coke drum is inevitably subjected to a rapid drop in temperature because cooling water is injected directly into the coke drumAnalysis of Mechanical behaviour of Bulging Reduction in Coke Drum
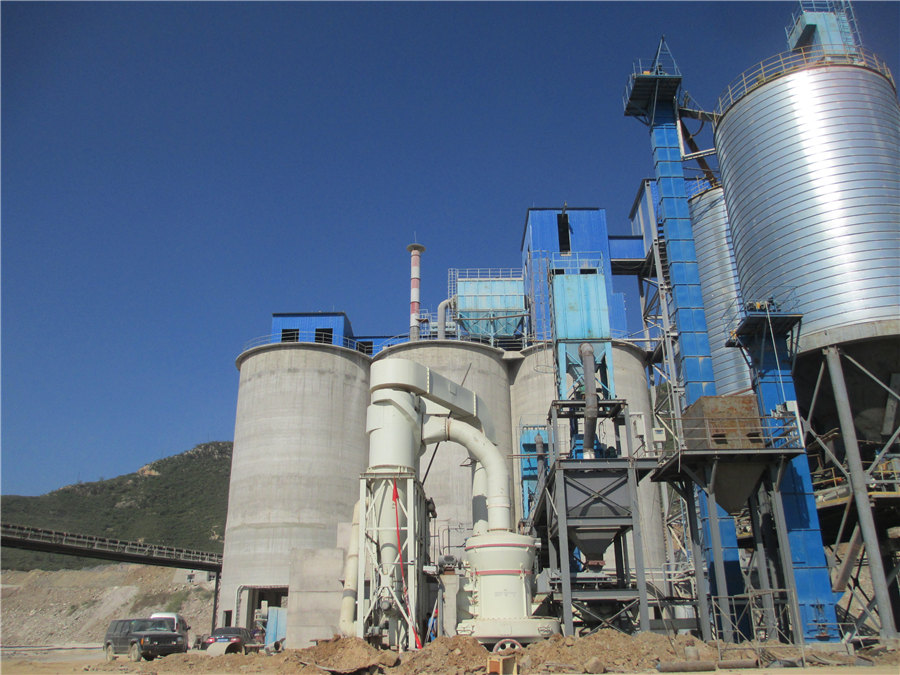
Delayed Coker Coke Drum Structure Safety during Shutdowns Maintenance
Special Mechanical/Contractor Access can be granted if: 1 Pilot hole has been drilled in coke bed 2 "HOT" portion of coke in coke drum has been removed 3 No top head is " open" to prevent accidental fall into drum 4 Proper LOTO in place and verified by all parties 5 One "closed or OOS" drum separates work area from "open" drum being cut 62019年2月27日 Thermo‐Mechanical Measurement of U1 Coke Drum 05C‐4 19Z05‐SOW‐A Title Revision Number Page Program Overview A 8 of 15 welding contractor should weld with P3 (coke drum surface) to P43 (strain gauge mounting material)THERMO‐MECHANICAL MEASUREMENT OF U1 COKE DRUM 2020年12月29日 Cracked hot gas leaves the coke drum from the top and the solid coke is formed inside the drum Once the drum is full up to the predetermined level, hot liquid feed is switched to the other drum and the filled COKING PROCESS IN REFINERY The Engineering Our long history in the development and implementation of specialty coke drum life extension and repair processes positions us to be your primary source for coke drum reliability WSI engineered solutions for coke drums Bulge repair and structural shell reinforcement; Lower cone replacement welds utilizing the HotPulse ® critical weld processWSI Coke Drum Services Industryleading Engineered Solutions
.jpg)
Crack Propagation and Remaining Life Assessment of Coke
THERMAL STRESSES IN COKE DRUMS 1097 where a crack with initial depth of 2mm was captured in the shell portion of the coke drum Paris Law was employed to model crack growth and probabilistic lifeare taken from ASME BPVC Sec II part D coke drum is also Fig2 Axisymmetric model of coke drum Fig 3 shows the discretized model of coke drum Element type PLANE 77 is used for the thermal analysis which is the changed into corresponding structural element PLANE 183 for structural analysis Fig3 Discretized model of coke drumiraj FATIGUE ANALYSIS OF COKE DRUM HOT BOXHome About the us CDI is a Houstonbased company that has a team of specialist engineers and technical inspectors with decades of experience in providing technical support for the inspection and structural assessment of coke drums, ensuring their mechanical integrity and operational reliability CDI has led in the development of new technologies that improve theInicio cokedrumintegrity2005年1月1日 Request PDF Techniques for Modeling Thermal and Mechanical Stresses Generated in Catalytic Cracker and Coke Drum Hot Boxes Consideration of heat transfer loading between surfaces during Techniques for Modeling Thermal and Mechanical Stresses
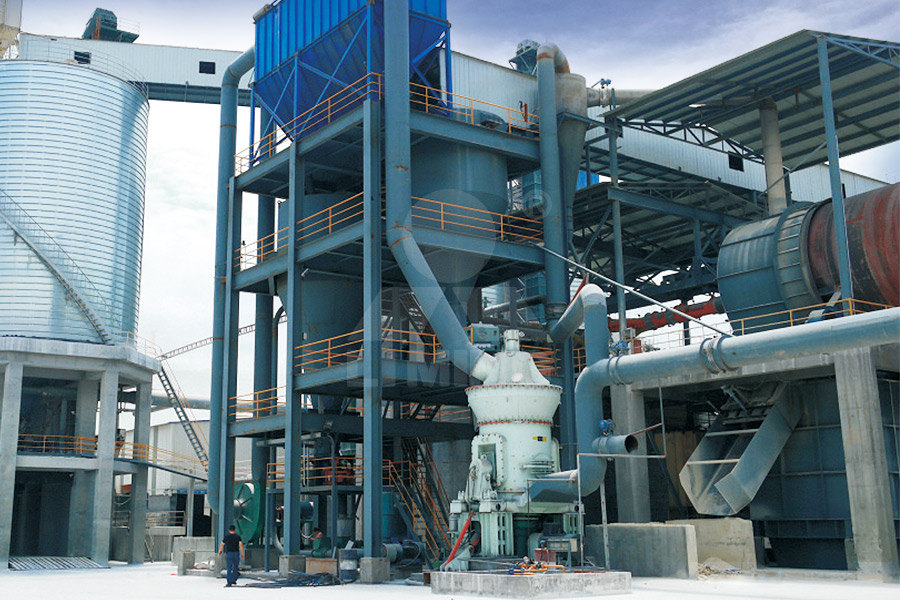
(PDF) Vibration Safety Evaluation Model and Sensor Network
2022年6月6日 Vibration Safety Evaluation Model and Sensor Networkbased Monitoring System for Coke Drums in Operation2022年12月5日 Request PDF Thermomechanical Fatigue Mechanical Behavior and Life Prediction of Coke Drum with CrMo Steel Thermomechanical fatigue tests are performed on SA387Gr11CL2 (125Cr05Mo) low alloy Thermomechanical Fatigue Mechanical Behavior and Life