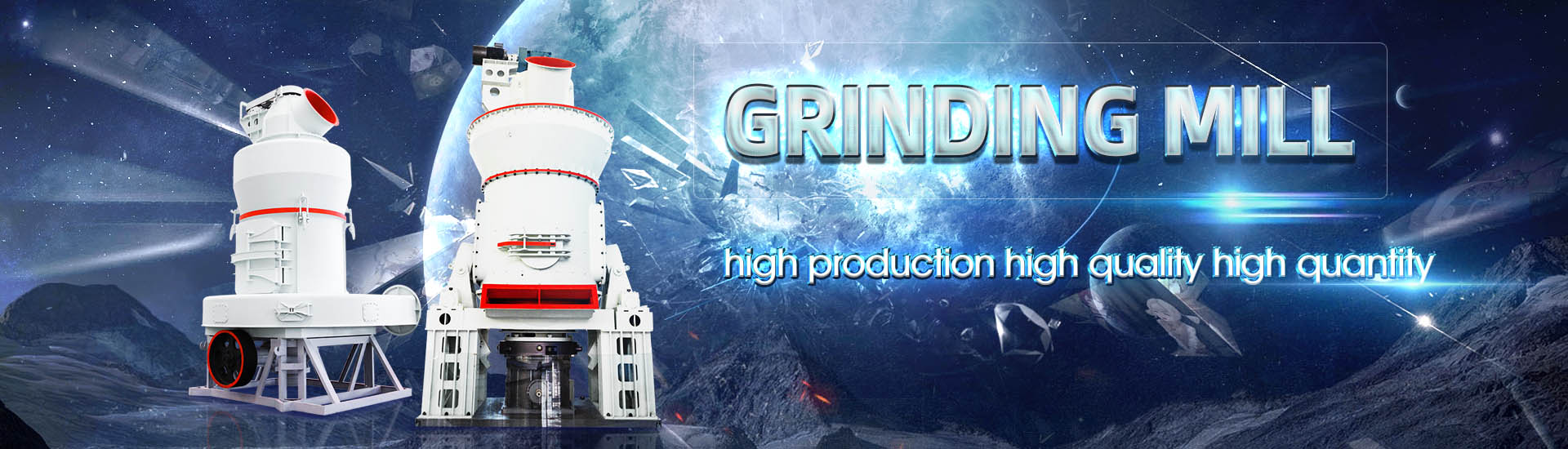
Loading capacity of coal mill
.jpg)
Coal Mill an overview ScienceDirect Topics
As a result, the control of coal mills is one of the areas of most active research since many years and represents the main source of reduced load following capability (LFC) for the coal fired 2015年11月1日 Coal mills are bottleneck in coal–fired power generation process due to difficulty in developing efficient controls and faults occurring inside the mills In this paper, a dynamic A unified thermomechanical model for coal mill operation2023年9月1日 By increasing the capacity of the mill, the percentage of pulverized coal on the third nozzle of the burner and on the second nozzle increases, while the recirculation in the The Influence of Mill Loading on the Distribution of Pulverized are four major mechanisms that happen during the coal crushing in the mills viz, size reduction in the coa coal, transport of the crushe coal and the classification of coal in terms of its A Study on 500 MW Coal Fired Boiler Unit’s Bowl Mill Performance

An investigation of performance characteristics and
2020年8月12日 In a power plant, the coal mill is the critical equipment, whose effectiveness impacts the overall power plant efficiency Uniform coal feeding mass flow rate and required particle size and2012年5月1日 The paper presents development and validation of a coal mill model to be used for improved mill control, which may lead to a better load following capability of power plants Derivation and validation of a coal mill model for controlThe Raymond Bowl Mill is considered the finest vertical roller mill available for pulverizing coal The typical Raymond bowl mill system is designed to simultaneously dry, pulverize, and Raymond Bowl Mill designed and built for flexibility QlarRaymond® Bowl Mills provide the following performance features: Wide range of capacities–base capacities from 8 to 150 tph Easily adjustable fineness–externally adjustable classifier permits selection of fineness from Raymond® Bowl Mill Coperion
.jpg)
Calculate Ball Mill Grinding Capacity 911Metallurgist
2015年10月15日 Learn how to calculate the grinding capacity of your ball mill with 911 Metallurgist This guide provides essential formulas, insights, and tips to optimize your milling process and enhance production efficiency2012年11月17日 20 131Fineness Fineness is an indicator of the quality of the pulverizer action Specifically, fineness is a measurement of the percentage of a coal sample that passes through a set of test sieves usually designated at 50, Coal mill pulverizer in thermal power plants PPTAir Swept Coal Mill Introduction The airswept coal mill produced by AGICO equipment has reasonable structure, high grinding efficiency, strong adaptation to raw materials, Ball loading capacity: 30t: 1213: 475KW: ZD80: 5: Φ28X8M Air Swept Coal Mill Cement Plant Machinery2011年8月1日 Now suppose this same pulverizer must grind sufficient coal flow to produce full load on the boiler with fuel that is 40 HGI, remember that there will be minor variation in mill capacity, Pulverizers 101: Part I POWER Magazine
.jpg)
CFD Modeling of MPS Coal Mill for Improved Performance and Safety
2009年1月1日 The MPStype pulverizer remains widely used for crushing coal in the power generation industry due to its ability to dry higher moisture coals and wide range of capacity Typically each mill Mill Capacity The ability of a power plant to pulverize coal for combustion is directly related to the load produced and indirectly impacts other areas such as slagging, ash sales and opacity One measure of the grinding nature of a coal is the Hardgrove Grindability Index (HGI) ThisCoping With Coal Quality Impacts on Power Plant Coal 2015年8月1日 Mill problems originate mainly due to poor controls or faults occurring within the milling system As discussed by GQ Fan and NW Rees [3], the control of mills remains very simple in most of the power plants due to the fact that the mill system is highly nonlinear with strong coupling among the variables and it is very difficult to measure some important Review of control and fault diagnosis methods applied to coal Distribution of the coal flow in the millduct system of the As Pontes Power Plant using CFD modeling JL Ferrin a'*, L Saavedra b a Departamento de Matematica Aplicada, Universidad Santiago Compostela, 15782 Spain b ETS Ingenieros Aeronauticos, PL Cardenal Cisneros 3, Universidad Politecnica de Madrid, 28040 Spain ABSTRACT The efficiency of a Power Plant Distribution of the coal flow in the millduct system of the As
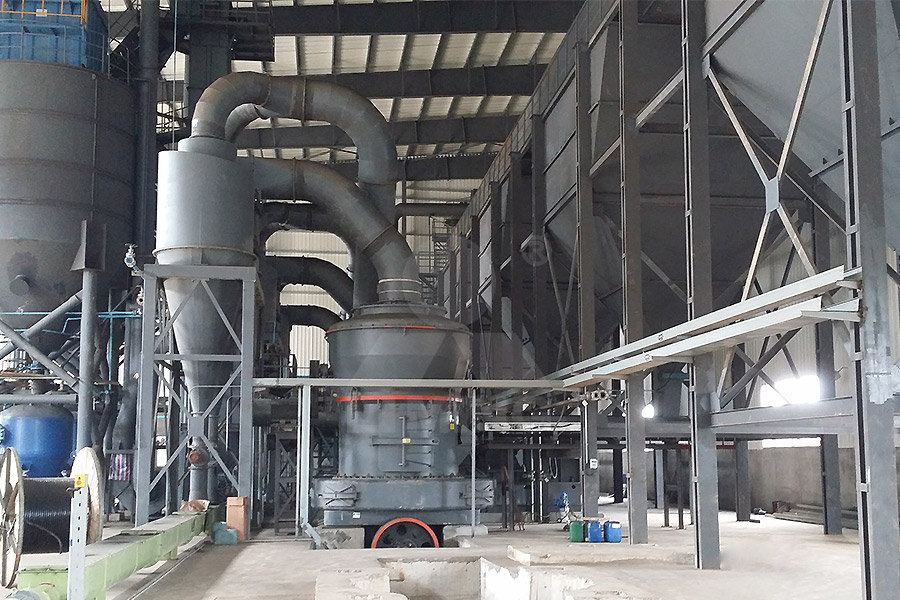
HP Bowl type millspower plant equipment
The maximum internal circulation load of the coal mill can be achieved by increasing the load, that is to say, the maximum capacity of the coal mill is improved, or the grinding output is higher; the smaller Hardgrove grindability and the pulverized coal fineness are selected, and the grinding uniformity is improved at the same time (pulverized coal uniformity coefficient n ≥ 12)The ATOX mill will grind and dry coal containing more than 20% moisture in one operation The possibility of customersupplied parts, along with the low civil costs that accompany compact mill installation, add to the excellent economy of the ATOX coal mill Working principles The raw coal enters the mill via a rotary sluice and feed chuteATOX COAL MILL FLSmidth CementThe coal mill in a cement plant should be reliable and should be operated with great care, or it is easy to cause safety accidents In the process of grinding strong drying capacity, and low energy consumption Ball Mill vs Vertical Coal Mill in Cement PlantCombustion Engineering, Babcock Wilcox, and Riley Stoker Corp are major manufacturers of coal pulverizing equipment The four most common coal pulverizers types are: BallTube Mills This type of mill consists of a rotating tube filled with cast alloy balls Coal is introduced through two hollow trunnions on each side of the tubeCoal Pulverizer – Power Plant Pall Corporation
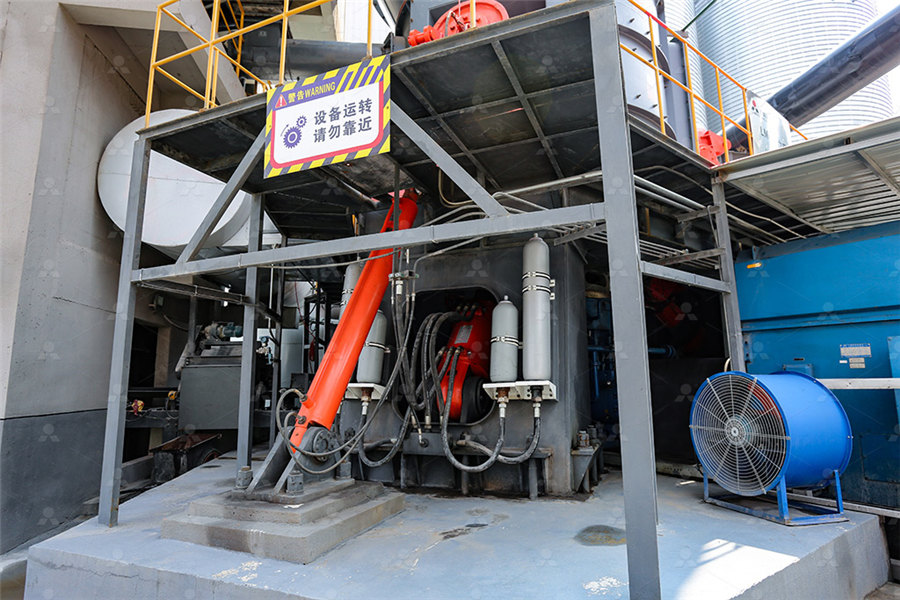
(PDF) Modeling and Control of Coal Mill Academia
Modeling and Control of Coal Mill × Close Log In Log The mass change of coal causes insignificant change in the total heat capacity of the mill (5) The ambient at 2300 seconds, inorder to meet a sudden increase in the load demand the mass flow of raw coal was increased from 77 to 84kg/sec 300 Inlet temperature (deg C 2021年5月20日 Mill operation To operate at 45 per cent load, three mills should be in service and 500 MW units are recommended Coal quality and heating value affect mill loading Mill outlet temperature should be increased slightly for better combustion and flame intensity and stability, as shown in Graph 2 Boiler key parameters for low load operationCompetitive Coal: Coal quality decides low load plant operationpulverizer capacity Capacity of a pulverizer is a minimum of five factors and these five factors are: tons throughput at a given fineness, at a given Hardgrove grindability index (HGI), at a given raw coal sizing entering the mill and at a given coal moisture content Throughput alone is NOT a definition of pulverizer capacity! Please read onPulverizer Capacity is not simply “tons throughput per hour!”From the coal yard, the coal is transfer to the mill bunkers through conveyor belt The bunkers are sized for an effective capacity of twelve (12) hours at BMCR with design coal Each mill bunker has one hopper, connected to the feeders Mills operate when the bunker coal gate valves are opened, coal is allowed to flow to the gravimetric feedersAnalysis of the Coal Milling Operations to the Boiler Parameters
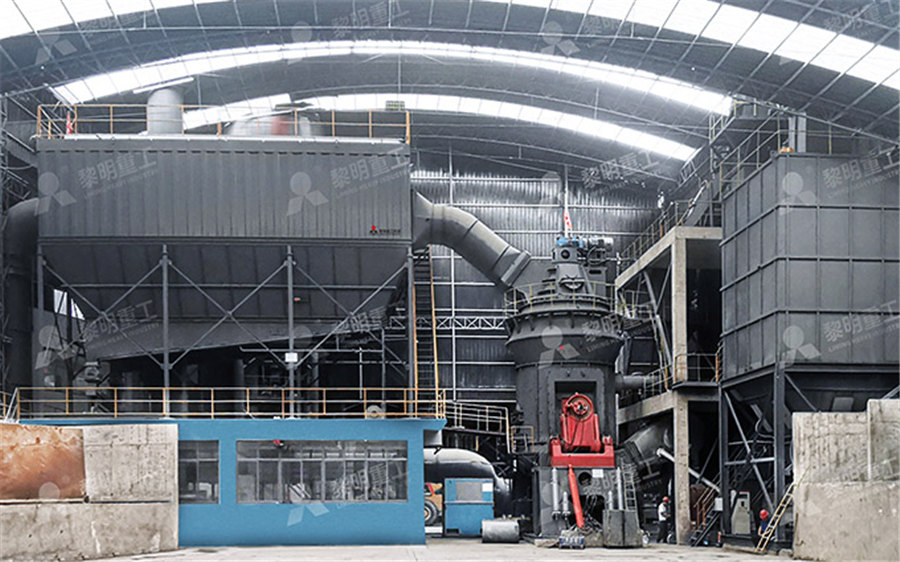
Ball Mill Circulating Load Formula 911Metallurgist
2015年10月9日 Calculating a grinding circuit’s circulating loads based on Screen Analysis of its slurries Compared to %Solids or Density based Circulating load equations, a more precise method of determining grinding circuit tonnages uses the screen size distributions of the pulps instead of the dilution ratiosPulp samples collected around the ball mill or rod mill and This optimizes mill grinding force loading characteristics such that the mill grinding force increases as mill load increases Figure 6 illustrates a typical mill gTinding force loading characteristic The grinding load increasing from 100% to 160% corresponds to mill capacity increasing from 100% to 135%, which reflects mill designCoal Pulverizer Design Upgrades to Meet the Demands of Low need improvement to achieve milloptimal performance Coal feed to the mill is important, this was observed to be a limiting constraint on mill capacity when the coal required exceed nominal load requirement KEYWORDS: Air fuel ratio; pulverised fuel distribution; classifier; elutriation; heat balance; isokineticPerformance optimisation of vertical spindle coal pulverisers1927 First Loesche coal mill delivered for the Klingenberg power station in Berlin 1953 500th coal mill plant sold worldwide 1961 Introduction of hydraulic spring assembly system 1965 Construction of first pressure mill (LM 122 D) 1980 Delivery of first modular coal mill (LM 263 D) 1985 Delivery of first selfinerting coal grinding plant (LM 212 D) for the steel industry (PCI LOESCHEMILLS
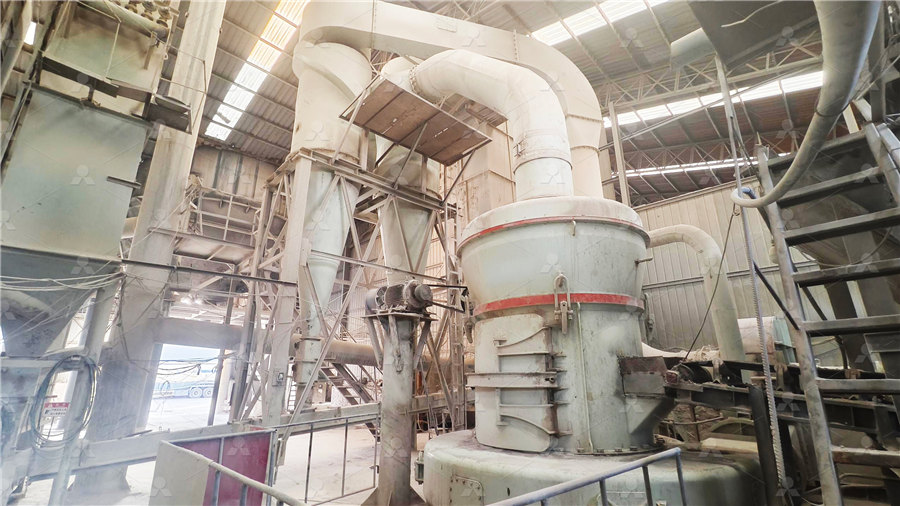
Analysis of the Coal Milling Operations to the Boiler
2020年4月2日 For a given mill load, the total Primary Air (PA) is kept Mill capacity with coal B typical 68 t/h 4 Mill capacity with coal B worst 66 t/h 5 Number of grinding JournalThe mill loading sequence after DOL start 600 800 For analysis of the possibility for the motor speed increase and corresponding coal mill capacity increase, it is necessary to find out coal load influence after the motor startMV VARIABLE SPEED DRIVE FOR COAL MILL CAPACITY IMPROVEMENT 2021年3月31日 3 COAL QUALITY –IMPACT COMPLEX • Pulverizer capacity, fineness wear • Slagging fouling in boiler • Corrosion erosion in boiler • Ash characteristics affect efficient collection in ESP • Affects furnace convective pass heat absorption boiler availability • Quantification of impact is complex 31Mar2021 total output power solutions 3Effect of Coal Quality and Performance of Coal pulverisers / Mills%PDF16 %âãÏÓ 578 0 obj > endobj 601 0 obj >/Filter/FlateDecode/ID[3B1A95957EC903EF9975C4E56>]/Index[578 41]/Info 577 0 R/Length 103/Prev /Root 579 BW ROLL WHEEL PULVERIZERS
.jpg)
Detection of Malfunctions and Abnormal Working Conditions of a Coal Mill
2018年5月2日 Coal mill malfunctions are some of the most common causes of failing to keep the power plant models have been developed and used in nonlinear model predictive control with results in improving coal load response time and temperature control The (rated capacity 220 MW) The mill is one of six mills supplying the 650 The Raymond® Bowl Mill is considered the finest vertical rollermill available for pulverizing coal Each bowl mill system is designed to achieve thebest solution forthe processing application The mill, feeder, classifier, fan, cyclone,dust collector and other system components are selected to meet the requirementsand characteristics of the material processedRaymond® Bowl Mill Coperion2020年6月29日 COAL MILL PERFORMANCE TEST The pulverisers are the “heart” of a pulverized coal fired power plant and as such, must be set up for maximum effectiveness so that the best furnace performance can be achieved Poor mill performance affects combustion , boiler losses , heat rate of unit , capacity of unit , APH , ESP performance , aux powerclassifications and working of mills in a power plant PPTAug 25, 2016 calculation Ball Mill Grinding Capacity Calculation grinding ball mill load calculation formula, Gold Ore Crusher formula to calculate ball mill Get Price And Support Online » ball mill balls capacity calculations for carbide ball mill balls capacity calculations for carbide hmk dec planetary ball mill hmk is a lab ball formula to calculate ball mill volume loading KOOKS
.jpg)
Correlation Analysis of Boiler Operation Parameters Based on Mill
the gaps between the balls are filled with coal, the grinding mill has been in its most efficient The output power is the coal storage put into ball mill in unit time With the increase of coal storage, the energy of pulverizing balls have boosted gradually Since the ball mill reaches the maximum output, balls have obtained the maximumrecent years, with the increase of installed capacity and the improvement of unit safety, the problems 215 Characteristic curve of ball loading of coal mill Optimization and transformation of 300MV units steel ball coal mill Introduction This article concerns itself with vertical grinding mills used for coal pulverization only (coal pulverizers), although vertical grinding mills can and are used for other purposes The 3D model in the saVRee database represents a Vertical Grinding Mill (Coal Pulverizer) ExplainedGrinding machine noise and vibration information are to change closelyrelated auxiliary variable with mill load, and these two input quantities are easy to be subjected to the influence of coal, coal moisture content and steel ball loading capacity, variation along with operating mode, its feature that characterizes mill load also can change thereupon, pressure class signal also can reflect CNA Thermal power plant ball mill load softsensing
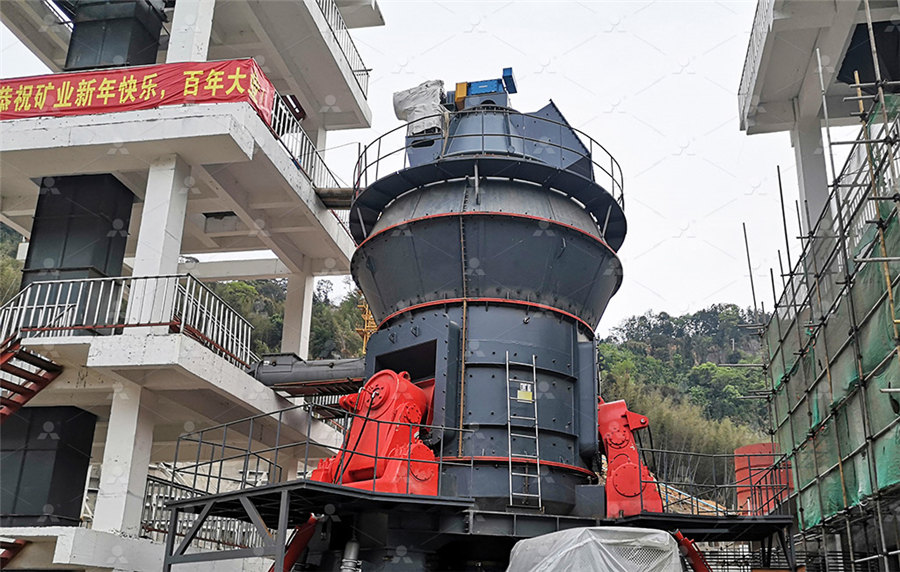
Experimental investigation of load behaviour of an industrial scale
2009年12月1日 Mill load (ie the load level of coal powder), which is critical in improving the production capacity and energy efficiency of pulverizing system in thermal power plant, has not been effectively Golyshev and I S Mysak [47] suggested a method to estimate the mill load and the grinding capacity using power consumption of the electric motor (PF) flow and the mill load As a result, the control of coal mills is one of the areas of most active research since many years and represents the main source of reduced load following Coal Pulverizers an overview ScienceDirect Topics2020年4月7日 diagnosis method of coal mill system, this paper constructs a dynamic model of the coal mill system and proposes a fault sample acquisition method Based on the established model, massive faultModeling of Coal Mill System Used for Fault Simulation2019年1月1日 This paper analyzes the effects of coal grindability and its characteristics on the grinding capacity and power consumption for beater wheel mill during exploitation in thermal power plant TENT B Practical assessment of grinding capacity and power consumption
.jpg)
Correlation Analysis of Boiler Operation Parameters Based on Mill
2015年10月13日 Coal fired boiler includes the combustion system, steamwater system, attemperation system, air and flue gas system, pulverizing system and the soot blower system []Ball mill is an important part of the combustion system, and the coal pulverizing and treating process is shown in Fig 1The coal falling into coal feeder from coal bunker is grinded up in 2022年2月24日 and a screw conveyor with a capacity of 60 t/h [11] Coals from the bunkers are transported to the raw coal a weight load of the mill with coal of 1500 g, equal to 187 g/hImproving the efficiency of the coal grinding process in ball drum