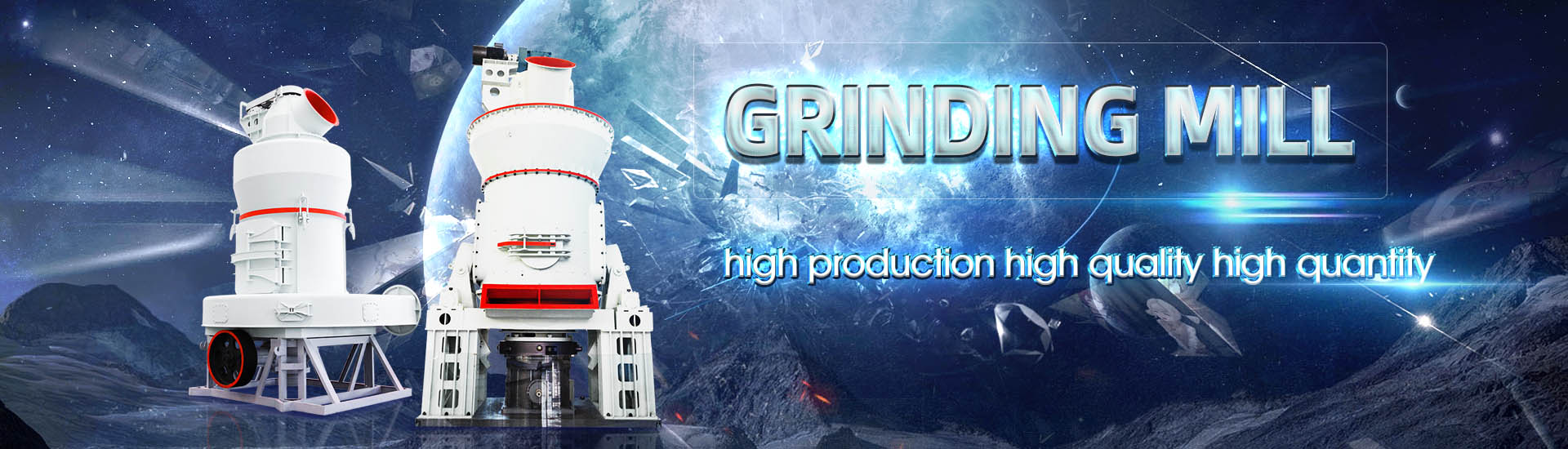
Cement grinding ball forging consumption
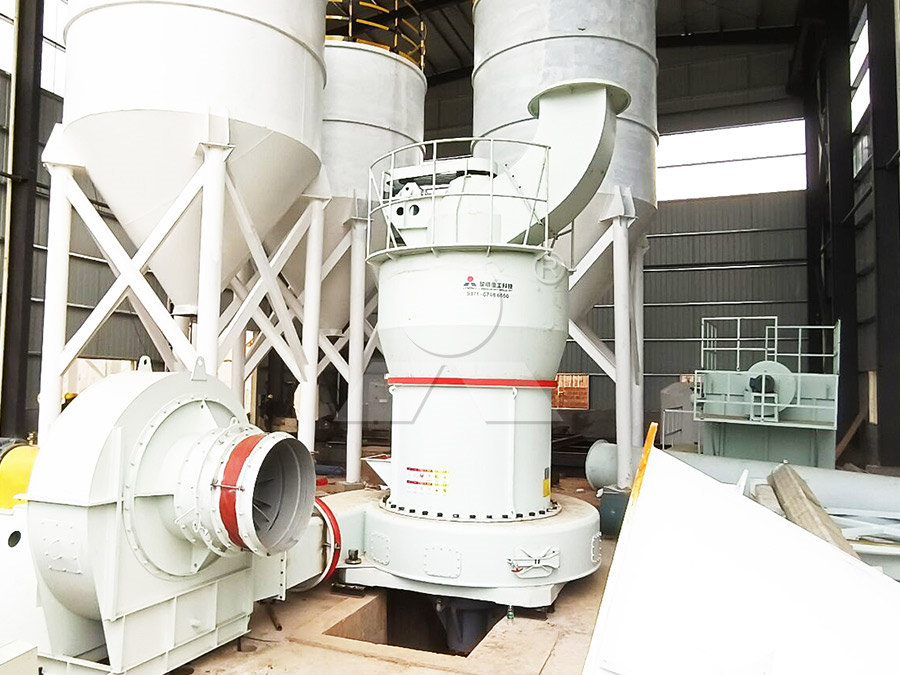
OPTIMIZATION OF CEMENT GRINDING OPERATION IN BALL MILLS
consumption and low production The consumption of energy by the cement grinding operation amounts to one third of the total electrical energy used for the production of cement The optimization of this process would yield substantial benefits in terms of energy savings and 2023年4月23日 the grinding media reduces energy and material consumption in a ball mill Different performances are achieved when(PDF) Grinding Media in Ball MillsA ReviewThe consumption of energy by the cement grinding operation amounts to one third of the total electrical energy used for the production of cement The optimization of this process would yield substantial benefits in terms of energy Optimization of Cement Grinding Operation in Ball As grinding accounts for a sizeable share in a cement plant’s power consumption, optimisation of grinding equipment such as ball mills can provide significant cost and CO 2BALL MILLS Ball mill optimisation Holzinger Consulting
.jpg)
Cement Grinding Cement Plant Optimization
Ball mills with high efficiency separators have been used for cement grinding in cement plants all these years Ball mill is a cylinder rotating at about 7080% of critical speed on two trunnions in Cement grinding In Table 1, three common cement grinding systems are compared on their electrical consumption for a typical 3500 Blaine ordinary portland cement (OPC) Roller press Thomas Holzinger, Holzinger Consulting, grinding system 2020年5月1日 Nowadays, ball mills are used widely in cement plants to grind clinker and gypsum to produce cement In this work, the energy and exergy analyses of a cement ball mill Energy and exergy analyses for a cement ball mill of a new 2006年3月1日 In the cement industry, the clinker grinding step consumes about onethird of the power required to produce one ton of cement This refers to an average specific power Energy efficiency of cement finish grinding in a dry batch ball mill
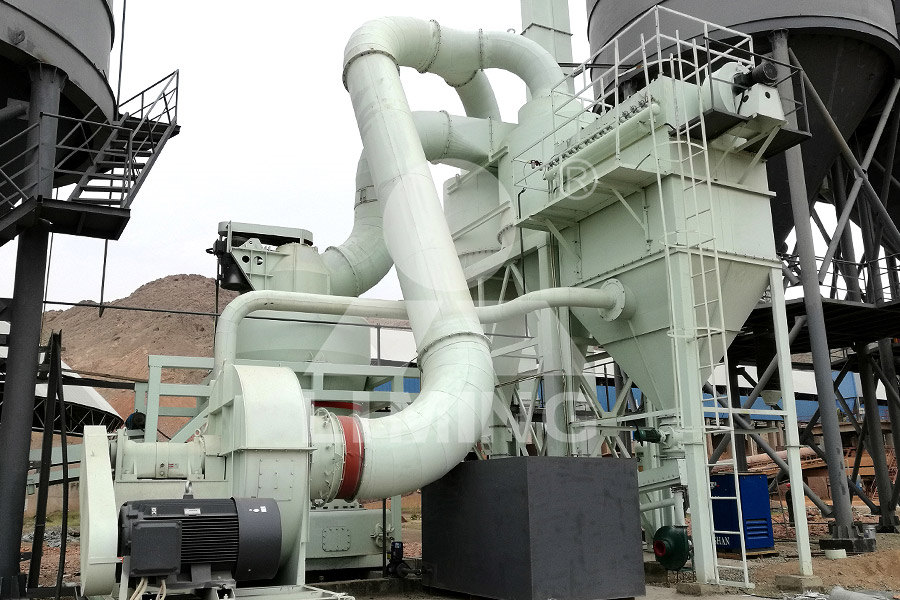
EnergyEfficient Technologies in Cement Grinding
2016年10月5日 Typical specific energy consumption is 30 kWh/t in grinding of cement Barmactype crushers found application as a pregrinder in cement grinding circuits operating with ball mills to reduce the specific energy When transferring to closed circuit а mill size 26×13 m at a constant quality cement (3000 cm2pg) capacity grinding unit was increased from 25 to 38 tph while reducing the specific Analysis of the efficiency of the grinding process in closed circuit Ball mill balls are one type of grinding media for grinding mills such as cement ball mills, SAG mills, The crushing resistance is more than 10 times of the general casting and forging grinding ball Less consumption The forging ball has a Ball Mill Balls For Sale WearResistant Grinding Balls Ball mill optimisation As grinding accounts for a sizeable share in a cement plant’s power consumption, optimisation of grinding equipment such as ball mills can provide significant cost and CO 2 emission benefits to the cement producer n by Thomas Holzinger, Holzinger Consulting, Switzerland BALL MILLS 1 FEBRUARY 2021 INTERNATIONAL CEMENT BALL MILLS Ball mill optimisation Holzinger Consulting
.jpg)
Grinding Media in Ball MillsA Review ResearchGate
Table 1 Chemical composition of typical grinding media (% wt) Adapted from [24] 211 Cast Iron Cast iron can be grey cast iron or white cast iron, but white cast irons are commonly used in 2022年4月20日 The size of the grinding balls should match the specifications of your ball mill and the nature of the material being ground Smaller balls are typically used for fine grinding, while larger balls are more suitable for coarse grinding The correct size and dimension ensure optimal grinding efficiency and energy consumption 4 Wear ResistanceForged Steel Grinding BallsThe consumption of energy by the cement grinding operation amounts to one third of the total electrical energy used for the production of cement Cement ball mills typically have two grinding chambers The first chamber is filled with larger Optimization of Cement Grinding Operation in Ball Mills PEC Nowadays, in the field of cement grinding system of the world cement industry, the major cement grinding equipments include loop flow ball mill, roller press, ball mill semifinishing system, and vertical mill system, in which ball mill and vertical mill are 2 major cement grinding systems in Cement Manufacturing PlantsPower Consumption of Cement Manufacturing Plant
.jpg)
Grinding steel balls play a crucial role in the mineral processi
2023年8月7日 Grinding Steel Ball are the unsung heroes behind the efficiency and productivity of numerous industrial processes These small but mighty spheres play a crucial role in the mineral processing, cement, and power generation industries, followed by precise forging or rolling to attain the desired shape and dimensionsSummary of Grinding in Cement Manufacturing Purpose of Grinding Essential for creating a fine powder from raw materials Prepares material for the next steps in cement production Types of Mills Ball Mills Use steel balls to grind material Higher energy consumption Vertical Roller Mills Use cylindrical rollers for grindingGrinding in Cement Manufacturing: Key Process, Types of Mills, Copper and Gold mining High hardness and good wearing grinding media balls HY mainly produce a range of grinding media balls in the mining and cement industry Application: 1 Mining (Copper, Gold, Iron, Aluminum, Manganese, Zinc, Chrome etc ), Cement Plant , Power station , chemical industry the Hot rolling grinding balls produced by advanced automatic rolling Mining And Cement Use Ball Mill Balls2022年4月8日 The socalled grinding ball consumption usually refers to the part of the balls that cannot be recovered due to mechanical wear and chemical erosion in the grinding process of the ore, 40mm Forging Grinding Ball 45# Hot Rolled Ball Cement Grinding Ball Manufacturer 40mm High Chromium BallsForging Balls Wear Calculation Method AGICO CEMENT
.jpg)
Optimizing Electrical Energy Consumption In Cement Process
energy is used for many operations like Crushing,Grinding,Rolling etc, The present paper deals with the methods and technologies that can be adopted in cement process plants to optimize Electrical energy consumption to conserve energy Index Terms Cement industry, Energy conservation, Electrical Energy, Optimization2021年1月25日 Choice and consumption of grinding media is related primarily to the volume and charecteristics of the ore Detour Gold GRINDING BALL USAGE: MEDIA APPLICATION SUITABILITY: Tower Mills: 05”15” grinding Grinding Balls and Other Grinding Media: Key 2021年3月7日 What is Forged Steel Grinding Ball? Forged Steel Grinding Balls are a ball milling product with multiple industrial uses It is a type of grinding mediaOther types of grinding media are Cast Iron Grinding Balls and Steel What is Forged Steel Grinding Ball and How to Buy 2022年4月1日 In fact, the consumption of steel balls in a cement ball mill has a lot to do with the material of the steel balls In general, the consumption of balls per ton of cement is between 0407kg 3 Influencing factors of ball consumption In general, the ball consumption per ton of cement is between 0407kg, but it is also affected by many How should Cement Grinding Media Consumption be calculated
.jpg)
80mm Steel Forged Balls AGICO CEMENT
2022年8月31日 Grinding ball production adopts a fully automatic grinding ball production line, which realizes all automatic flow operations from raw materials to finished products, changes the disadvantages of high energy consumption, high pollution, and high emissions of traditional forging products, and completely realizes cutting, heating, and spinningGrinding Aid Effectiveness in Cement Ball Mill Web: bulawali : bulawali@gmail, ali@bulawali LinkedIn: Ali Bulawali The introduction of the grinding aid (GA) has been started more than 50 year ago, to facilitate clinker grinding in cement mills improve mill output despite of the above features, the wear of mill interior parts well be increase`Grinding Aid Effectiveness in Cement Ball Mill AcademiaEach FOX Forged Steel grinding ball is solid from surface to center These sturdy, well built, shockabsorbing steel balls are the perfect hardness for ball mill grinding Whether you are grinding raw materials in ball mills, or using planetary ball mills on a smaller scale to get a finer particle size, these are the forged steel balls for youForged Steel Ball FOX Forged Steel Grinding Ball Fox Industries2017年4月29日 In the previous discussion the fact was established that the work done by a ball when it strikes at the end of its parabolic path is proportional to its weight and velocity; then, since the velocity may be considered as constant for all the balls in the mill, the work done by a ball is proportional to its weight Since the amount of ore crushed varies as the work done upon it, it Grinding Media Wear Rate Calculation in Ball Mill
.jpg)
Ball Mill For Cement Grinding – Cement Ball Mill Ball Mill
Pregrinding:it refers to adding a grinding machine in front of the cement ball mill to increase the output of the original grinding system by a large margin This method features large investment and relatively complex process but it can increase the output of cement ball mill by up to 50%2016年1月1日 The wear of balls used during a grinding process is considered one of the losses that cause an increase in the operating cost allocated to the ball mill [21]A comparison of wear rates of ball mill grinding mediaComparison of cement grinding systems for ordinary portland cement at 3500 Blaine, 4% limestone Ball mill Combi grinding system Finish grinding Ball mill with cage rotor separator Roller press in semifinish mode and ball mill VRM Roller press Specel Energy consumption mill motors kWh/t 30 25 17 17 % at mill motor (ball mill 100%) % 100 83 57 57Thomas Holzinger, Holzinger Consulting, grinding system As a ball mill grinding media supplier, Skip to content [gtranslate] info@ballmillmachines +86 Home; Ball Mill Application Menu Toggle Cement Ball Mill; Gold Ball Mill; Coal Ball Mill; Limestone Ball BALL MILL GRINDING MEDIA
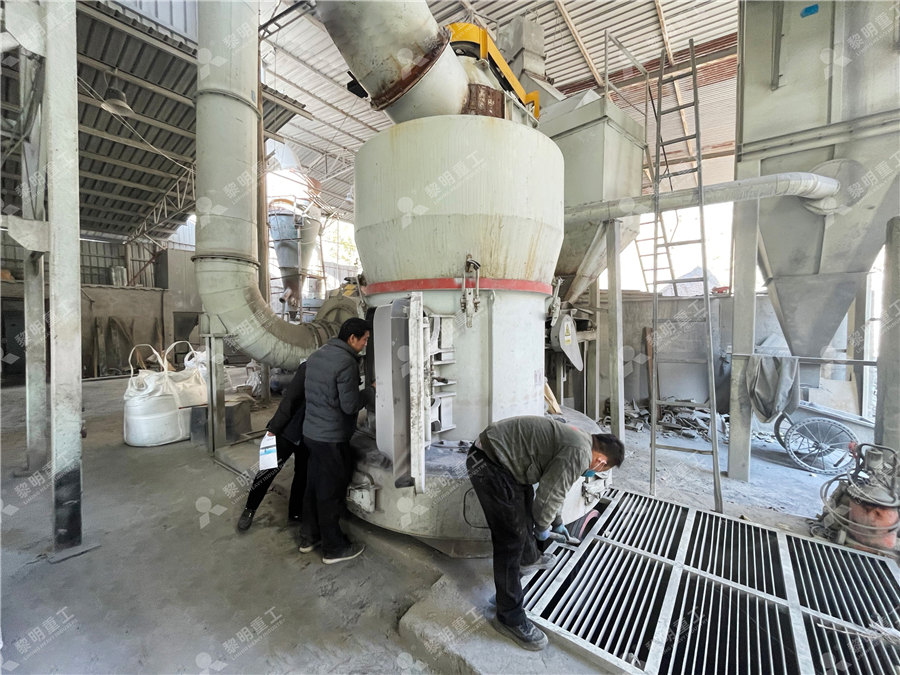
Cast Grinding Balls vs Forged Grinding Balls: Making
2024年10月25日 In the realm of industrial operations, particularly within mining and cement production, the role of grinding balls cannot be overstated These spherical tools are pivotal in the grinding process, tasked with reducing 2020年7月24日 The energy consumption of grinding is the subject of many studies, especially in the case of ball mills for grinding clinkers [8, 9], fuels [10], iron ore [11], hematite ore [12], sulfide ore [13 Determination of granulometrical composition of the clinker by grinding The benefit of the OK mill is in particular pronounced when grinding to a high fineness and/or when slag is included in the cement Grinding aid For ball mills grinding OPC to a fineness of up to around 3600 cm2/g (Blaine) grinding aid is usually not required; it may not even be feasible considering the cost of grinding aidCement grinding Vertical roller mills VS ball millso 120⁰ C causes excessive gypsum dehydration media coating if mill ventilation is poorImprovements in New Existing Cement Grinding Mills by Tim
.jpg)
How To Choose Steel Balls For Ball Mill? Grinding Balls Cement
2024年2月27日 As a grinding media of ball mill, ball mill balls are various, how to choose suitable grinding balls? We supply casting balls and forging balls with competitive price, factory delivery, get a FREE quote! Skip to content +86 s about which has been widely used in cement dry ball mills, Size of the grinding media typically varies in a range of 48 mm The grinding tools reach a tip speed of 5 times the critical speed, rather creating a constant cloud of grinding media than a revolving mass of rolling and falling balls inside the rotating shell of a ball mill, at a maximum of 07 times the critical speed onlyLet’s talk: polysius® booster mill – the next level in cement Advantages at a glance: Modular design and small footprint enable integration in existing grinding plants Production increase in range of 1020 %, depending on the fineness, especially for smaller ball mill systems up to 100 tph Quality improvement by use of the additional grinding stage, for example to improve the early strength while maintaining the original production ratepolysius® booster mill thyssenkrupp Polysiusgrinding balls 50 and 60 mm in diameter prepared by screw rolling It is shown that presence of flakes significantly reduces grinding ball impact resistance regardless of their quenched microstructure parameters In this case there is no significant effect of ball microstructure parameters after heat treatment on their impact resistanceSTUDY OF GRINDING BALL QUALITY PROPERTIES DURING
.jpg)
Cement Grinding Plant Expert Cement Grinding
Cement Grinding Unit EPC Solution With a strong RD team, experienced engineers, and firstclass technical services, we aim to provide users with the most advanced and optimized cement production solutions The main task of The annual cement consumption in the world is around 17 billion tonnes and is increasing by 1% every year []Cement industries consume 5% of the total industrial energy utilised in the world []A total of 40% of the total energy Predictive Controller Design for a Cement Ball Mill Established in 2000, We Jinan Zhongwei casting and forging grinding ball Co,Ltd, good wear resistance, no breakage and even wearing They are mainly applied to various mines, cement plants, power stations and chemical industries 2000 Jinan Zhongwei Casting And Forging Grinding Ball 2024年2月22日 On the other hand, steel grinding balls are better suited for heavyduty operations involving the grinding of hard materials, such as in mining and cement production Their superior impact strength and durability make them the preferred choice for both dry grinding, where their robustness can handle the high impact of materials, and wet grinding, where their Ceramic vs Steel Grinding Balls: A Comprehensive Comparison for
.jpg)
25mm Grinding Forging Ball AGICO CEMENT CHINA
2022年8月16日 25mm Grinding Forging Ball August 16, 2022 agico SEO The 25mm Grinding Forging Ball adopts the current advanced oil quenching process (pushrod automatic oil quenching production line)FLS Cement flsmidthcement 3 Ball mill for cement grinding Cement grinding is a crucial stage of the flow sheet, where both cement quality and process efficiency are decided Achieving the required fineness with maximum efficiency is down to the design of the ball mill and how well it runs An inefficient systemBALL MILL FLSmidth CementCement go out to grind the important parameter that temperature is cement grinding quality control, at ball mill, carry out in the process of cement grinding, have most mechanical kinetic energy and be converted into heat energy, and the height that enters to grind clinker temperature all can affect ball milling builtin temperature, heat energy gathers too much and enters to Water spraying device in cement grinding mill Google Patents2012年6月1日 As the cylinder starts to rotate, the grinding balls inside the cylinder crush and grind the feed material, generating mechanical energy that aids in breaking bonds, activating the catalyst, and Grinding in Ball Mills: Modeling and Process Control
CFB石灰石脱硫剂制备64.jpg)
(PDF) Intensifying the cement grinding process ResearchGate
2023年7月19日 For over 60 years technological additives used in process of grinding cement Application of cement grinding aids can improve performance of ball mills, reduce specific energy consumption, and 2023年10月23日 The compatibility of grinding aids (TEA/glycol) and superplasticizers (PC/SNF) in lowand highC3A cements, as well their mutual effect on the properties of pastes and fresh/hardened mortars were (PDF) A study of different grinding aids for lowenergy cement