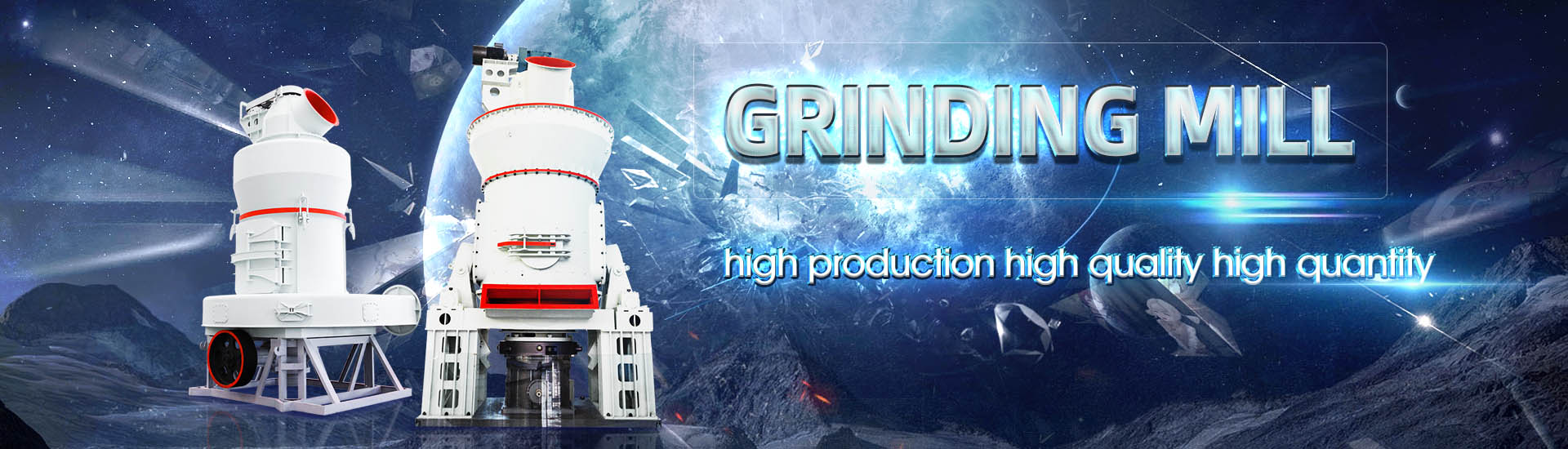
Zinc for Dacromet Aluminum dust, overhaul slag, aluminum electrolyte
.jpg)
Enhancement of the corrosion resistance of zincaluminum
2017年1月25日 The results of the electrochemical measurement showed that, compared with Dacromet coating, Dacromet+Re coating had a longer controlled sacrificial anodic protection 2017年5月8日 The paper describes the characteristics and prinicipal methods of applying zincaluminium flake nonelectrolytic coatings, (”DACROMET”), to a wide range of steel The Application of ZincAluminium Flake Nonelectroytic Surface 1 Barrier protection: Each layer of overlapping Zinc and Aluminum flakes creates a barrier of protection 2 Galvanic action: Sacrificial protection of Zinc protects the base metal from CYM Geomet Decromet 2016 Chin Yuan Metal2016年1月1日 The processes include composite coating, compositionally modulated multilayer coating, pulse plating, thermal spraying (metallizing), waterbased coatings of zinc powder or (PDF) Science and Industry of Processes for Zincbased
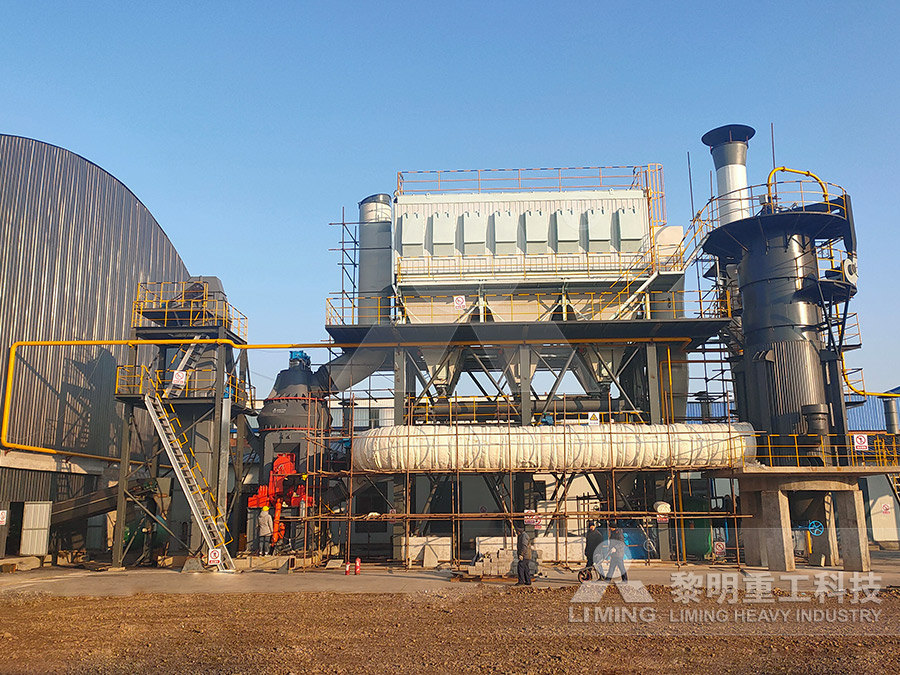
The Application of ZincAluminium Flake Nonelectroytic Surface
Flake zincaluminium coatings are used in industry for decades They can perform high corrosion resistance according to required accelerated tests, but in the field application the corrosion2023年4月25日 This article analyzes and summarizes the composition and hazards of the overhaul slag and the current development status of domestic and international electrolytic 电解铝大修渣处置研究进展The zinc aluminum coating (also called"Dacromet") is a recently developed anticorrosive technology which has the advantages of high anticorrosion,low pollution and no hydrogen Study and Application of the ZincAluminum CoatingDACROMET® is an aqueous solution comprising zinc in flake phase, aluminium metal powder and inorganic compound It is normally treated by dip and spin coating of this aqueous solution DACROMET® Coating Shiva Co

How aluminium additions improve the performance of zinc‐rich
2024年7月19日 Formulations containing aluminium significantly outperformed the standard 100% zincrich coating with the greatest improvement occurring at 10%–15% aluminium by 2023年5月20日 Spent carbon anode (SCA) discharged from the aluminum electrolysis industry is an unavoidable solid waste with an estimated production of 700 kilotons in 2021, which has Regeneration of raw materials for aluminum electrolysis from 2023年9月1日 Lithium (Li)bearing aluminum electrolyte slag is an inevitable byproduct of the aluminum industry, and improper disposal or stacking it may lead to potential environmental hazards This study employed hydrometallurgical Clean Process for Selective Recovery of Lithium 2024年11月6日 Dacromet coating combines zinc flakes, aluminum powder, and inorganic compounds in a waterbased solution Dacromet: Up to 300°C; Zinc plating: Up to 120°C; Thickness consistency: Dacromet: Even coverage; Zinc plating: Variable buildup; Impact resistance: Dacromet: Moderate flexibility;Dacromet Coating: Applications, Benefits, and Techniques
.jpg)
Regeneration of raw materials for aluminum electrolysis from
2023年5月20日 Spent carbon anode (SCA) discharged from the aluminum electrolysis industry is an unavoidable solid waste with an estimated production of 700 kilotons in 2021, which has been widely identified as the hazardous solid waste A new twostage leaching scheme comprising an aluminum salt leaching and an alkali leaching has been investigated in this 2020年1月25日 Zinc smelting slag is generated by the zinc pyrometallurgical process In general, total contents of zinc and lead of the zinc smelting slag are about 5–15%, while the contents of rare and noble metals are very low []Therefore, it is not economic for the recovery of valuable metals from the zinc smelting slag by the traditional hydrometallurgical processes A Critical Review on Generation, Characteristics, and Utilization of 2024年1月1日 Semantic Scholar extracted view of "Efficient lithium recovery from electrolytic aluminum slag via an environmentally friendly process: Leaching behavior and Green and efficient separation of fluorine from spent aluminum electrolyte by aluminum sulfate solution: Leaching behavior and mechanism Lingqi Meng Tianxiang Hao +5 Efficient lithium recovery from electrolytic aluminum slag via an Download Citation On Aug 1, 2023, Jianping Yang and others published Dissolution behavior of overhaul slag from aluminum reduction cell in a cryolitebased molten salt system Find, read and Dissolution behavior of overhaul slag from aluminum reduction
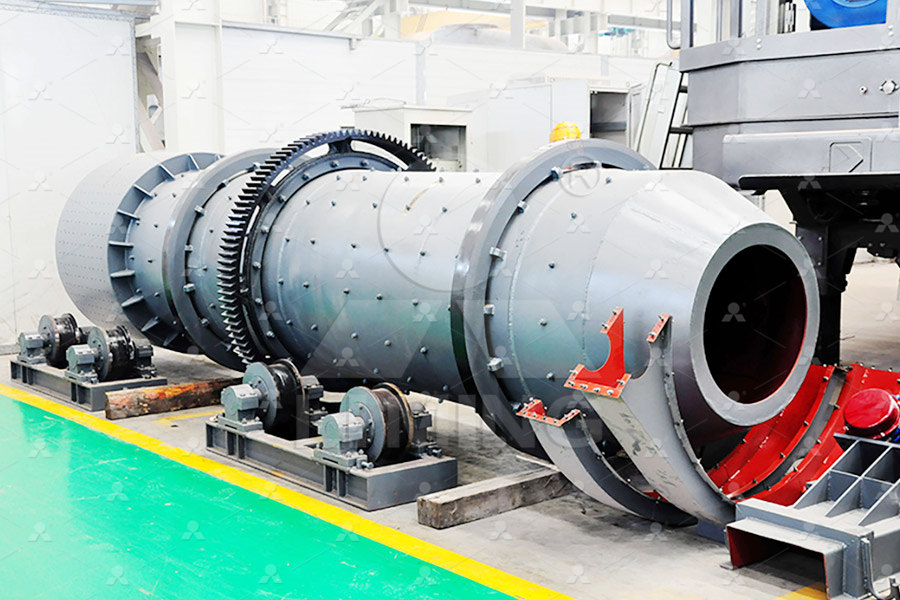
Inhibition effect of aluminum dust explosions by one novel zinc
2022年6月29日 Based on these properties, ZB2335 was adopted and tried to inhibit aluminum dust (30 μm) explosion, results showed that the flame propagation of aluminum dust explosion could be inhibited completely when the mass ratio of ZB2335 to aluminum dust reached 10, which validly prove the feasibility of selecting zinc borate as inhibitor [Zhang et al, 2022]2018年7月18日 Hydrometallurgical recovery of zinc from electric arc furnace dust was investigated on a laboratory scale, using aqueous sodium hydroxide solution as a leaching agentZinc Recovery from Steelmaking Dust by Hydrometallurgical Methods2024年4月1日 No 4 230 Alexander Glinin et al: Outotec ® Ausmelt Technology for Treating Zinc Residues 1 Introduction Zinc production has been steadily increasing by 4 % per annum to 13 million tonnes in Technology Selection for Slag Zinc Fuming Process ResearchGate2024年5月23日 16 Million metric tons of spent carbon electrodes modify carbonrich solid wastes from aluminum electrolysis are produced annually, threatening ecosystems by cyanide and fluoride pollution Here, we review carbonrich solid wastes with focus on sources and hazards, detoxification, separation, recovery, recycling and disposal Treatment techniques The recycling of carbonrich solid wastes from aluminum
.jpg)
A novel approach for lithium recovery from waste lithium
2021年10月1日 And all aluminum electrolysis production ensures that the cryolite ratio of aluminum electrolyte is below 30, and the electrolyte is called an acid electrolyte Based on publicly reported literature, LiF exists as Na 2 LiAlF 6 in the acid electrolyte, whereas LiF exists as its entity for cryolite ratio greater than or equal to 30 (Gao et al, 2002; Li, 2009, Zhang and 2023年8月2日 With global science and technology development, natural resources are gradually consumed and the demand for industrial materials is also gradually increasing []The recovery and recycling of limited resources have become an important topic that must be considered in the future development trend []Aluminum, as an important material, is particularly widely used in Sustainable Recovery of Fluorine from Waste Aluminum Electrolyte 2022年10月9日 Where, γ c refers to the yield of flotation concentrate (%); A c (%) and A f (%) are the ash content of flotation concentrate and feed material, respectively 3 Results and discussion 31 Characterization of raw carbon Recovery of carbon and cryolite from spent carbon Spent aluminum electrolyte slag is a byproduct produced during the electrolysis of aluminum and contains elements such as F, Al, Na, and Li It is a toxic and harmful substance with a stable and complex structure As a consequence of fluorine pollution and low lithium recovery efficiency in the traditional hydro metallurgy process, a novel cleaner production technology was developed Cleaner Process for the Selective Extraction of Lithium from Spent
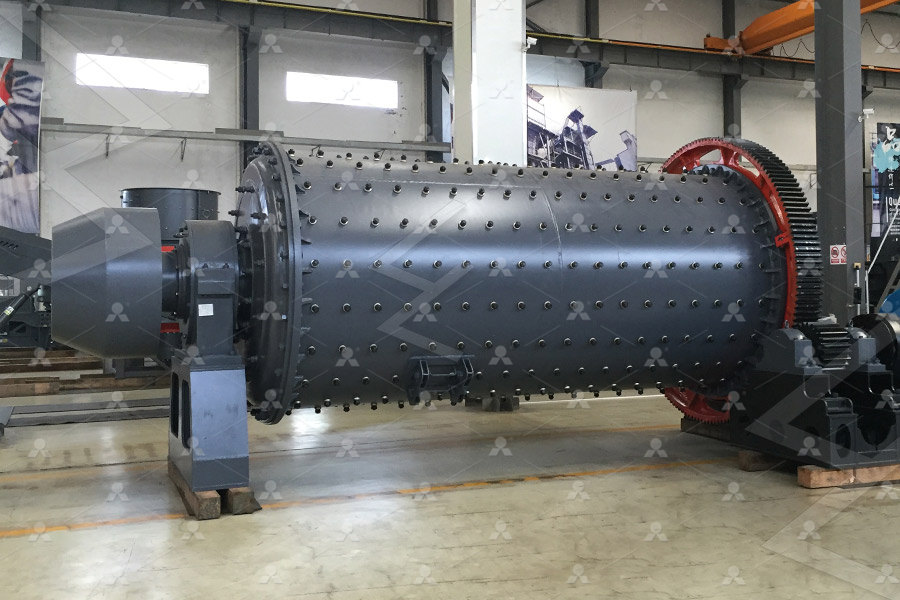
A novel approach for ultrasonic assisted organic acid leaching of
2023年10月1日 Crush and grind the waste aluminum electrolyte fine Fig 1 (b) shows the particle size analysis, and the results show that the average particle size of the treated aluminum electrolyte powder is 4528 μm Fig 1 (c) shows the XRD diagram, which shows that the waste aluminum electrolyte mainly comprises Na 3 AlF 6, CaF 2, LiF, K 2 NaAlF 6, and 2023年7月20日 Metallurgical slag and dust (MSD) are abundant Zncontaining secondary resources that can partially alleviate the shortage of zinc minerals, with hazardous characteristics and a high recycling value In this work, the process conditions of recycling Zn from MSD materials leaching by ammonium acetate (NH3CH3COONH4H2O) were optimised using Recovery of Zinc from Metallurgical Slag and Dust by Ammonium 2021年7月30日 The aluminum metal and molten salt flux are tapped after the process, where the cooled flux along with the mixture of nonmetallic components is called salt slag or salt cake54 Salt slag contains 5–7 wt% residual aluminum metal, 15–30 wt% aluminum oxide, 30–55 wt% sodium chloride, and 15–30 wt% potassium chloride and, depending upon the A Review of Secondary Aluminum Production and Its Byproducts2021年1月12日 The most promising approach for recovering carbon slag for industrial applications among them is flotation, which is an effective method for the separation of fine mineral particles [12] and has The Study of Carbon Recovery from Electrolysis Aluminum Carbon Dust
.jpg)
Regeneration of raw materials for aluminum electrolysis from
2023年5月20日 Due to chemical corrosion and erosion by molten aluminum liquid and electrolyte, the carbon anode of the aluminum electrolytic cell would fall off into the electrolyte during the primary aluminum electrolysis process to produce spent anode carbon (SCA), which has been listed as one of the typical hazardous solid wastes in the National Hazardous Waste 2020年12月1日 The rapid development of the electrolytic aluminum industry in China and the increasing demand for aluminum products have led to the development of many lowgrade bauxite mines with an average Li 2 O content of at least 058% (Wang et al, 2013)Due to the use of this lowgrade bauxite in the electrolytic aluminum process, the content of lithium in the Novel process for the extraction of lithium carbonate from spent 2020年1月28日 With the rapid development of the aluminum reduction industry, the amount of carbon dust, aluminum dross and spent potlining generated in the aluminum reduction process has also increased It is estimated that 8–12 kg of carbon dust, 10–12 kg of aluminum dross, and 20–30 kg of spent potlining will be produced for each ton of aluminum produced [ 2 , 3 ]Characteristic Analysis of Hazardous Waste from AluminumOn August 2nd, China Nonferrous Metals Industry Association organized an expert meeting on scientific and technological achievements in Kunming, Yunnan Province, and completed the "electrolytic aluminum overhaul slag" jointly Electrolytic aluminum overhaul slag harmless
.jpg)
Purification of zinc sulphate electrolyte with
2019年1月1日 Purification of zinc sulphate electrolyte with modified zinc dust and kinetics of cadmium cementation (2019) IMPC 2018 29th International Mineral Processing Congress, pp 256025682024年2月1日 Overhaul slag, as one of the main hazardous solid wastes generated in the electrolytic aluminum, has high research value [12] The electrolytic cell lining is eroded by continuous chemical corrosion of hightemperature molten metal and salt, resulting in expansion and peeling off, leading to low production efficiency and degradation of performance [13]A novel approach for extracting lithium from overhaul slag by low 2019年6月27日 Tang Y, Lu L, Roesky HW, Wang L, Huang B (2004) The effect of zinc on the aluminum anode of the aluminum–air battery J Power Sources 138(1–2):313–318 Article CAS Google Scholar Zaromb S (1962) The use and behavior of aluminum anodes in alkaline primary batteries J Electrochem Soc 109(12):1125–1130Indepth structural understanding of zinc oxide addition to 2010年7月15日 Today, approximately 30% of global zinc production arises from recycled zinc The growing interest in secondary zinc materials, as a valuable resource, and stricter environmental legislation that restricts dumping of these hazardous materials has increased interest in their recycling [1]The disposal and utilization of EAFD are problems for all steel Hydrometallurgical process for zinc recovery from electric arc
.jpg)
Selective preparation of lithium carbonate from overhaul slag by
2024年5月1日 The reason is that the lithium content in the overhaul slag is relatively low, and the minimum amount of sulfuric acid is enough to completely transform the lithium compound into NaLi(SO 4) More aluminum compounds are converted to NaAl (SO 4) 2, when m(H 2 SO 4)/m(overhaul slag) increase from 10 to 14Lithium (Li)bearing aluminum electrolyte slag is an inevitable byproduct of the aluminum industry, and improper disposal or stacking it may lead to potential environmental hazards This study employed hydrometallurgical processes to selectively leach lithium from Licontaining aluminum electrolyte slag, using sodium carbonate solution as the leaching agentClean Process for Selective Recovery of Lithium Carbonate from 2014年3月7日 Lead blast furnace slag (LBFS) produced from the process of lead smelting is a hazardous solid waste, which contains potentially toxic elements (Pb, Zn, As, and Cd) with high mobility and solubilityMineralogical Reconstruction of Lead Smelter Slag for Zinc 2009年12月1日 The poor densification characteristics of "CA70" specimens sintered in the temperature range 12501450 °C can be explained in terms of the evolution of the highmelting CA 2 phase in these Utilization of aluminum sludge and aluminum slag (dross) for the
.jpg)
The Study of Carbon Recovery from Electrolysis
2021年1月12日 A large amount of carbon dust is generated in the process of aluminum smelting by molten salt electrolysis The carbon dust is solid hazardous waste but contains a large quantity of recyclable components such as carbon 2010年9月15日 Besides, the corrosion of equipments would also be very serious So, the conventional hydrometallurgical process is not favorable for treating such slag To our knowledge, this zinc slag can be directly melted into anodes and electrorefined to produce high purity zinc, at the same time, aluminum can be turned into saleable Al(OH) 3The recovery of zinc from hot galvanizing slag in an anion 2020年12月4日 A manganese leaching efficiency higher than 83% is reached under these conditions, with a corresponding 22% iron, 23% lead, 68% zinc and 65% aluminum Precipitation of Mn, Fe, Al, Zn, Al and Pb Recovery of Manganese from Zinc Smelter Slag ResearchGate1997年11月1日 The direct recycling of flue dust is not usually possible since it contains some undesirable elements (zinc and alkaline metals) that can cause operational difficulties in the blast furnaceZinc recovery from blast furnace flue dust ResearchGate
.jpg)
(PDF) Hydrometallurgical process for zinc recovery from
Hydrometallurgical process for zinc recovery from electric arc furnace dust (EAFD) Stripping of the loaded organic phase by zinc spent electrolyte (625 g/L Zn2+ ) at T: 40 C with diluted H2 SO4 (3 mol/L) (4 followed by selective stripping with sulphuric acid solutions of different dilutions, from copper smelter slag leach 2024年2月1日 Aluminum metal was produced using the cryolitealumina molten salt electrolysis method (Ishak et al, 2017) A large amount electrolytic aluminum slag (EAS) is generated during the electrolysis process, as the falling of carbon particles on the anode into the electrolysis cells and the accumulation of lithium fluorine result in energy consumption and electrolyte scrapping Efficient lithium recovery from electrolytic aluminum slag via an 2023年5月22日 The dissolution performance of black aluminum dross (BAD) in cryolite electrolyte is key to its recovery by molten salt electrolysis The stable operation of the electrolyzer depends mainly on the rapid dissolution of BAD in Na3AlF6AlF3Al2O3 electrolyte system In this paper, the dissolution performance and behavior of BAD and its main components in the Dissolution characteristics of black aluminum dross in Na2023年4月25日 Process flow for recycling and treatment of electrolytic aluminum overhaul slag Figure 2 Process flow of high temperature fire method for harmless treatment of overhaul slag Figure 3 Alkali leaching recovery process of electrolytic aluminum overhaul slag Figure 4 Cement kiln collaborative treatment of overhaul slag process flow电解铝大修渣处置研究进展
.jpg)
Table 1 Chemical composition of aluminum dross, white dust
Download Table Chemical composition of aluminum dross, white dust and Mgcontaining waste solution from publication: Synthesis of HydrotalciteLike Materials from Various Wastes in Aluminum