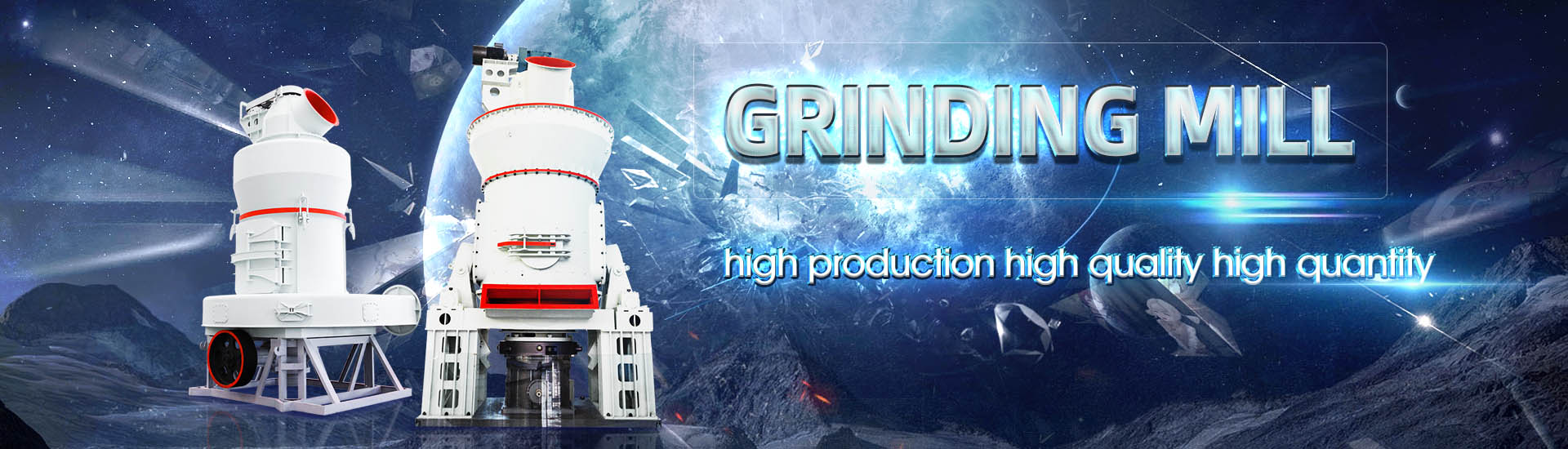
Cement clinker technology
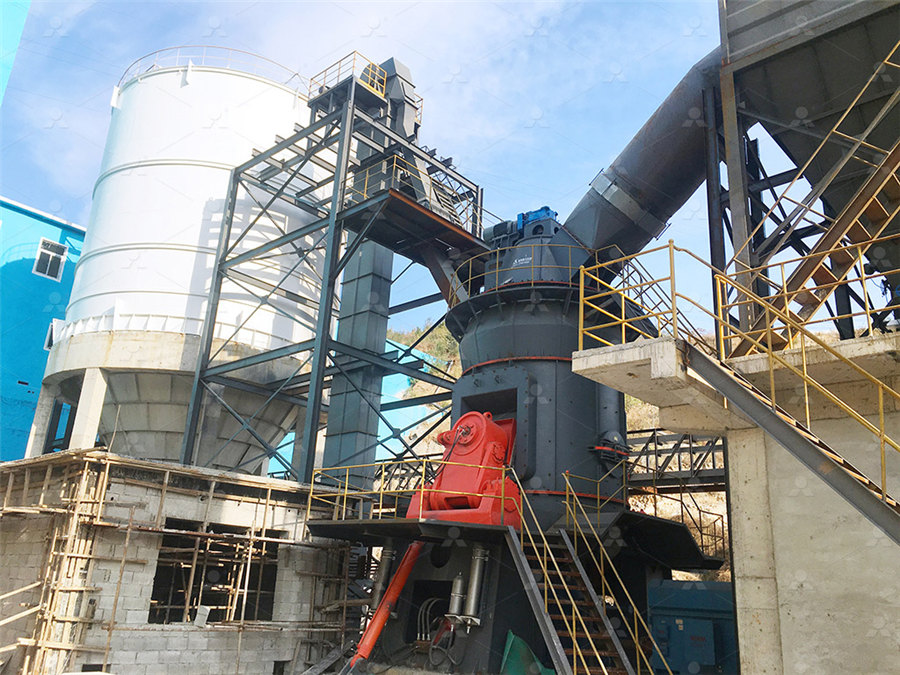
LowTemperature Electrochemical Cement Clinker
Lowtemperature electrochemical cement clinker (eclinker) production is a promising technology for reducing carbon dioxide (CO 2) emissions in the cement industry This Perspective provides an overview of the process and the 2021年12月28日 The current paper presents a critical review of the existent alternative clinker technologies (ACTs) that are under an investigation trial phase or under restricted use for niche applications and that lead to reduced Alternative Clinker Technologies for Reducing Carbon 2022年9月30日 We also show that nearly all of the highest cement producing nations can locally generate and use secondary CMs to substitute up to 50% domestic Portland cement clinker, Cement substitution with secondary materials can reduce annual 2024年5月17日 Microwave heating has the potential to electrify clinker and calcination treatments in the cement sector Microwave absorption of most raw materials increases with Electrification of clinker and calcination treatments in the cement
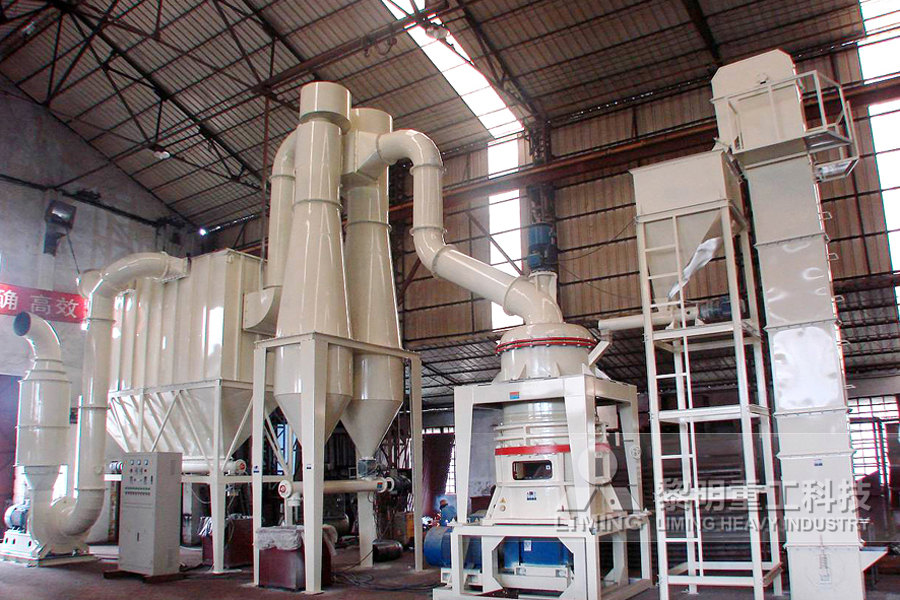
Technology Roadmap LowCarbon Transition in the Cement
Rising global population and urbanisation patterns, coupled with infrastructure development needs, drive up the demand for cement and concrete and increase pressure to accelerate 2019年1月21日 Among various SCMs available for substituting clinker, calcined clays, particularly in combination with lime stone (LC3 Technology), are found to be the extremely promising materials that are available in large enough Recent Progress in Green Cement Technology Utilizing Qiu et al [23] successfully prepared Portland cement clinker via calcination at 1300 °C by replacing clay with CTs and coal gangue CTs have a certain mineralization effect; their Utilization of copper tailings in the preparation of lowcalcium We also show that nearly all of the highest cement producing nations can locally generate and use secondary CMs to substitute up to 50% domestic Portland cement clinker, with many Cement substitution with secondary materials can reduce annual
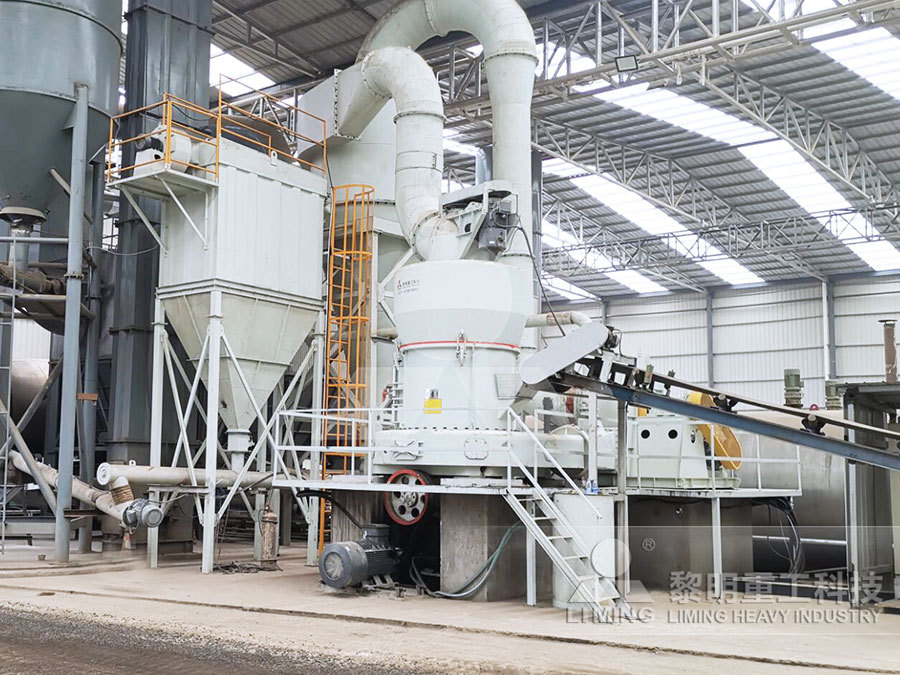
Clinker – MIT Concrete Sustainability Hub
Clinker, the residue formed by hightemperature burning of coal or similar materials, plays an important role in the composition of cement and contributes to the properties of cement in 2024年2月1日 As a major greenhouse gas, large emissions of CO 2 contribute to the global greenhouse effect In 2019, CO 2 emissions from cement industry reached 24 Gt, accounting for 26% of the total industrial emissions (IEA, A review of lowcarbon technologies and projects for 2020年4月3日 Cement production begins with limestone, a sedimentary rock Once quarried, it is mixed with a silica source, such as industrial byproducts slag or fly ash, and gets fired in a kiln at 2,700 degrees Fahrenheit What comes Explained: Cement vs concrete — their differences, 2020年12月14日 The baseline used is a ‘frozen technology’ scenario in which 5 GT of cement are consumed in 2050 with a clinker emissions intensity of 0813 (GNR Database figure for 2015) and an average clinkertocement ratio of 065 (IEA ETP figure for 2014), emitting 264 GT CO 2 Making Concrete Change: Innovation in Lowcarbon Cement and
.jpg)
Cement kiln Wikipedia
Portland cement clinker was first made (in 1825) in a modified form of the traditional static lime kiln [2] [3] [4] The basic, eggcup shaped lime kiln was provided with a conical or beehive shaped extension to increase draught and thus obtain the higher temperature needed to make cement clinkerFor nearly half a century, this design, and minor modifications, remained the only Other articles where clinker is discussed: cement: Manufacture of cement: burned product, known as “clinker,” together with some 5 percent of gypsum (to control the time of set of the cement) The three processes of manufacture are known as the wet, dry, and semidry processes and are so termed when the raw materials are ground wet and fed toClinker cement BritannicaOrdinary Portland Cement Clinker is the essential component in producing Cement, which is made of sintering limestoneIn the manufacture of Cement, clinker formed by sintering or fusing without melting to the point of liquefaction, aluminasilicate materials such as clay and limestone during the cement kiln stage and happens as 3 millimeters (012 inches) to 25 millimeters What is Clinker? (Meaning, History, Manufacturing Application)2023年4月19日 Lowcarbon cements The average clinkertocement ratio in the EU in 2017 was 75% (2) The European Standards differentiates five main categories of cements based on their clinker composition The most used cements, Portland and Portlandcomposite cements, have clinker contents over 95% and 65% respectivelyDeep decarbonisation of industry: The cement sector
.jpg)
Alternative Clinker Technologies for Reducing Carbon Emissions
2021年12月28日 The proximity to the BAT for clinker production is certainly an advantage for the industrial implementation of some of the alternative binders mentioned above, however, when looking forward through a perspective of cement industry decarbonization, it is the author’s belief that full or partial conversion of the existing fuelbased technology to electricitybased Manufacturers are implementing innovations including carbon capture, utilization, and storage (CCUS) technology, which may help to further reduce a cement plant’s carbon footprint Pulverizing The clinker keeps cooling and a ball mill How Cement is Made Portland Cement Association2020年5月15日 Heidelberg Cement has discovered an alternative clinker technology called TernoCem The technology works on an altered chemical composition and lower burning temperatures The company reports that CO2 Future of Cement: LowCarbon Technologies and2024年11月4日 CEMENT TRAINING TECHNICAL SERVICES An emphasis on the understanding of the pyroprocess technology system: – Raw Mix Design, Burnability, and Clinker Quality – Optimization of Heat Consumption – Operation and Process Diagnostic Studies and Productivity Enhancement of the Clinker Production – Energy Conservation and Energy Audit PYROPROCESS TECHNOLOGY COURSE The Cement Institute
.jpg)
Cement substitution with secondary materials can reduce annual
Various cements with clinkertocement mass ratios of ~05 are standardized and/or available (eg, CEM III–V, LC3,19) However, progressively decreasing the clinkertocement mass ratio is increas2024年5月17日 Given the cement industry’s significant impact on global CO 2 emissions, and with the – not yet sufficiently exposed – decarbonation potential and benefits of MW technology in mind, this literature review focusses on the technological potential of MW heating for hightemperature clinker and calcination treatments relevant for the cement and lime industriesElectrification of clinker and calcination treatments in the cement 2024年10月1日 Implementing solar calciner technology to sinter the cement clinker in the Spanish cement industry could avoid 14–17 % of CO 2 emissions into the atmosphere The concept of Portland cement clinker production using concentrated solar energy was first demonstrated by Oliveira [22]Technology verification of Portland cement clinker production The manufacture of conventional cement is very polluting In particular, it requires a lot of energy to produce clinker, the main component of cement To reduce its carbon footprint by 80% by 2050, the cement industry must therefore innovate Hoffmann Green is fully committed to this mission Decarbonated cement 0% clinker is already an accessible realityHoffmann Green Cements: first decarbonated cements 0% clinker
.jpg)
Roadmap to a netzero carbon cement sector: Strategies,
2024年5月1日 Hybrid and Integrated Cement Plants: Hybrid cement plants combine traditional cement production with innovative processes, like electrolysis to produce clinker or renewable hydrogen as a heat source Integrated facilities diversify their production by comanufacturing cement and other products like green chemicals, utilizing the waste streams efficientlySo the calcination of cement clinker is the key process of cement production Among them, clinker kiln as the clinker production equipment is the core of the whole cement production line Both its quality and manufacturing technology have a direct impact on cement products, so the choice of clinker kiln is very important for cement manufacturersCalcining Technology Of Clinker Kiln Cement Rotary Kiln AGICOFrom a cement performance viewpoint, faster cooling of the clinker enhances silicate reactivity The cooled clinker is then conveyed either to the clinker store or directly to the clinker mill The clinker store is usually capable of holding several weeks' supply of clinker, so that deliveries to customers can be maintained when the kiln is not operatingManufacturing the cement kiln Understanding Cement2024年11月6日 In the pilot plant, belite cement clinker is produced from previously seldomused finegrained crushed concrete and limestone at less than 1000 degrees Celsius in an electrically heated rotary kiln To limit such emissions, the Karlsruhe Institute of Technology (KIT) is developing netzero circular concretePilot Plant Produces Climatefriendly Cement Clinker
.jpg)
Sustainable Cement Storage: The Impact of Clinker
2024年3月15日 Sustainable Clinker Storage in China One cement producer achieving major sustainability gains through clinker silo upgrades is Anhui Conch Cement, China’s largest cement manufacturer The company was facing rising Production of clinker in a reducing atmosphere in a cement kiln can seriously degrade the quality of clinker and the cement produced from the clinker However, an industrial cement kiln is tolerant of reducing conditions without Quality Composition of cement clinker2022年9月30日 In this paper we report the maximum potential for cement substitution with secondary materials to reduce CO2 emissions globally (13 Gt CO2eq in 2018) and on a countrybycountry basisCement substitution with secondary materials can reduce annual 2019年4月20日 In this work, the cement clinker is prepared with a simulated test of steel slag multiphased clinker sintering technology A cement clinker raw meal design method based on the particle size distribution and the thickness of reactive film was established, the properties of multiphased cement clinker, grindability and hydration property is Process to utilize crushed steel slag in cement industry directly
.jpg)
Description of cement production technology Akmenės cementas
During grinding of clinker and gypsum in cement mills, cement is produced Depending on the type of cement, granulated blast furnace slag, A more detailed description of the cement production technology and diagrams you can see here Company details Akmenės cementas AB Legal address: J Dalinkevičiaus g 2, LT85118 NAUJOJI AKMENĖ It provides an update of the Cement Technology Roadmap 2009: Carbon Emissions Reductions up to 2050, and sets a strategy for the cement sector to achieve the decoupling of cement production growth from related direct CO2 emissions through improving energy efficiency, switching to fuels that are less carbon intensive, reducing the clinker to cement ratio, and Technology Roadmap LowCarbon Transition in the Cement 2019年1月18日 El Clinker está compuesto por diversos elementos como el aluminato tricálcico, silicato bicálcico y tricálcico y ferrito aluminato tetracálcico, y aunque para conseguir el cemento como tal, se necesita utilizar otros componentes, los componentes del Clinker son los que hacen posible que el cemento reaccione con el agua y le da resistencia, esa que tanto se exige y ¿Que es el Clinker? Componentes basicos sobre el cementoThe global clinkertocement ratio 1 has increased at an annual average of 11% since 2015, from 066 increasing to 071 in 2022 This number hides significantly different regional trends China, despite having one of the lowest clinkertocement ratios globally, saw an increase from 057 in 2015 to 065 in 2022Cement IEA International Energy Agency
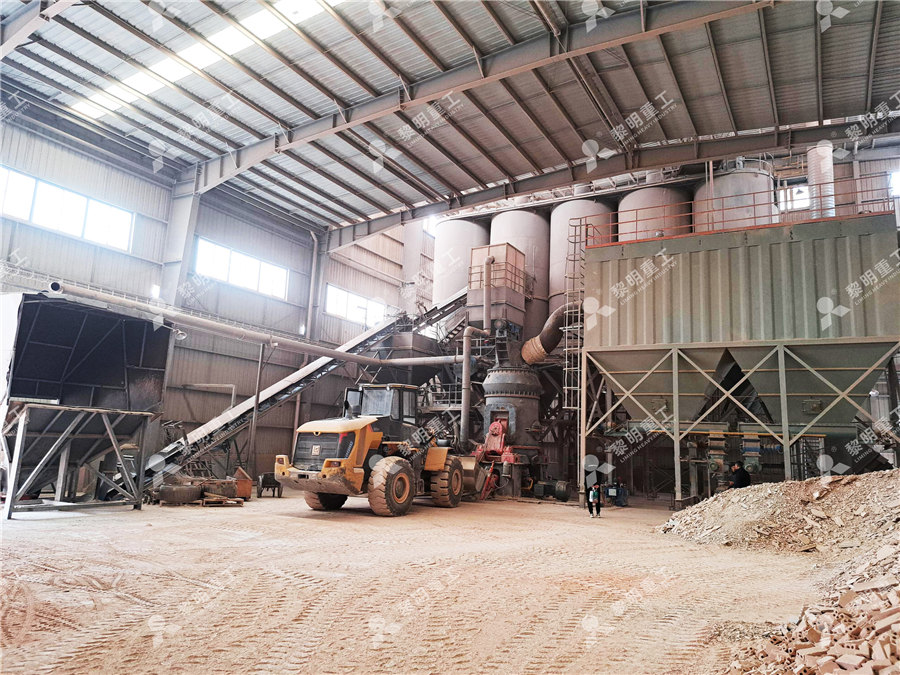
Conveyor Belt for Cement Industry: Technology Solutions
2024年5月23日 The conveyor belt for cement industry is designed to handle heavyduty tasks, ensuring the continuous movement of limestone, clinker, and other materials essential for cement production The significance of conveyance systems in cement processing plants cannot be overstated, as they streamline operations, reduce manual labor, and enhance overall productivityThe chemical composition of Portland cement clinker indicates that the rawmaterial components are predominantly calcareous with successively smaller amounts of siliceous, aluminous, and ironrich constituents Occurrences of rocks that on burning without any admixture give a cement clinker are extremely rareAdvances in Cement Technology ScienceDirect2024年11月23日 Cement Composition, Properties, Major Cements: Portland cement is made up of four main compounds: tricalcium silicate (3CaO SiO2), dicalcium silicate (2CaO SiO2), tricalcium aluminate (3CaO Al2O3), and a Cement Composition, Properties, Major CementsReaction (1), the decarbonation of limestone, is the cause behind the largest source of CO 2 emissions in cement production Thus, reducing the amount of CaO in the binder results directly in a reduction of CO 2 emissions The second one is the hydraulic ability, or reactivity, of the phases that are present in the CaOSiO 2 system Besides the main oxides, CaO and SiO 2, in their Alternative Clinker Technologies for Reducing Carbon Emissions
.jpg)
EnergyEfficient Technologies in Cement Grinding IntechOpen
2016年10月5日 In this chapter an introduction of widely applied energyefficient grinding technologies in cement grinding and description of the operating principles of the related equipments and comparisons over each other in terms of grinding efficiency, specific energy consumption, production capacity and cement quality are given A case study performed on a 2012年12月1日 According to the CSI’s “Getting the Numbers Right” (World Business Council for Sustainable Development, 2009), the dry manufacturing process with preheaters and precalciner technology, used in a large number of cement production plants globally, had an average specific energy consumption of 3,605 MJ/t clinker in 1990 but saw a reduction of around 6% by 2006Trends and developments in green cement and concrete technologyClinker Clinker Long Son is a provider of Clinker products to the Southern market with years of experience To replicate that success, Long Son Co, Ltd will provide Clinker products with guaranteed quality meeting the needs of cement production as well as the needs of export to demanding markets where the company is implementingClinker Cement production plants Long Son2024年8月23日 ICR explores the details of the grinding process, which is a critical stage in cement manufacturing, which significantly impacts the final product’s quality and characteristics By finely grinding raw materials into clinker and mixing them with gypsum, cement manufacturers ensure the fineness and uniformity essential for strong and durable cementFrom Clinker to Cement Indian Cement Review
.jpg)
Cemex Recognized at COP29 for Solar Clinker Breakthrough
2024年11月20日 Cemex has been awarded the NetZero Industries Award at COP29 for developing a revolutionary clinker decarbonization process using concentrated solar power The breakthrough technology, developed in collaboration with cleantech company Synhelion, enables solarpowered clinker production, a key component in cement manufacturingThe partnership, The cement kiln is a vital component of the cement manufacturing process, playing a critical role in the production of highquality clinker Advances in kiln technology have significantly improved energy efficiency, reduced emissions, and enhanced the overall sustainability of Comprehensive Guide to Cement Kilns: Processes, Types, Lowtemperature electrochemical cement clinker (eclinker) production is a promising technology for reducing carbon dioxide (CO2) emissions in the cement industry This Perspective provides an overview of the process and the development of the electrochemical reactors for cement production (ie, “cement electrolyzers”), highlighting the potential to revolutionize cement LowTemperature Electrochemical Cement Clinker Production