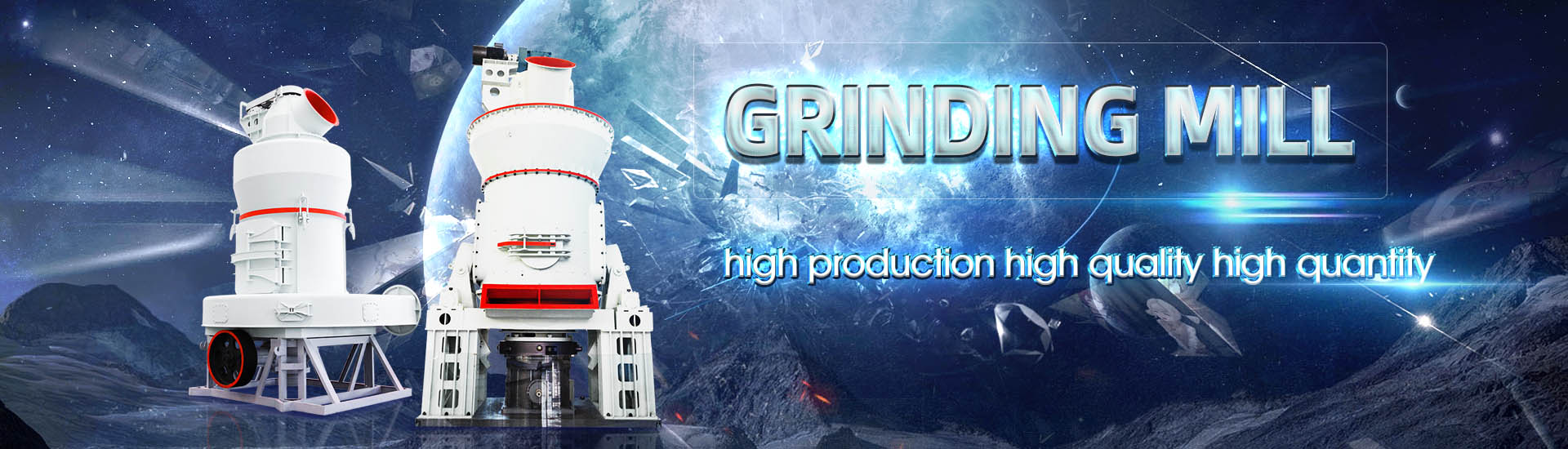
Electrical schematic diagram of cement raw material mill
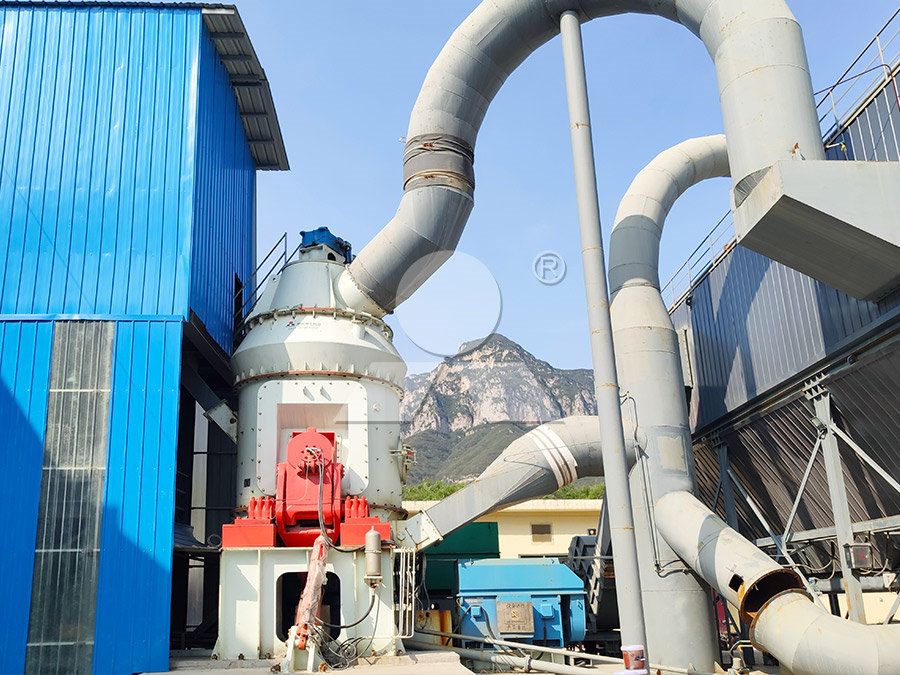
Monitoring Control Systems for Cement Plants Fuji Electric Global
Stable quality by optimal raw material preparation and raw material grinding at maximum effi ciency for energysaving operation of facilities Monitoring and control of burning and cooling Download scientific diagram Schematic of raw vertical roller mill circuit in the Ilam cement plant from publication: Modeling of energy consumption factors for an industrial cementSchematic of raw vertical roller mill circuit in the Ilam Vertical roller mills are adopted in 20 cement plants (44 mills) in Japan In the vertical roller mill which is widely used in the raw material grinding process, raw materials input grinding table Vertical roller mill for raw Application p rocess materialscementplantschematicsmersen Author: Mersen Subject: Main steps of cement manufacturing process showing where electrical components are located Keywordscementplantschematicsmersen
.jpg)
Schematic of ball mill circuit in the Ilam cement plant
investigate relationships between various measured variables and ventilation rate, the data were collected from one of the Raw Material ball mill circuits (line 1) of the Ilam cementSchematic layout of a typical allintegrated cement manufacturing process Red dashed lines depict confined spaces The process commences with raw materials extraction from theSchematic layout of a typical allintegrated cement manufacturing 2018年1月1日 A schematic diagram of the raw mill system in a cement plant is illustrated in Fig 1 In this process, raw materials, such as CaCO 2 , SiO 2 , Al 2 O 3 , Fe 2 O 3 , MgO, K 2 O, Thermodynamic Performance Analysis of a Raw Mill System in a In this research work, the application of population balance model for simulation of a VRM in a cement clinker grinding circuit was investigated The residence time distribution (RTD) was Modeling and simulation of vertical roller mill using population
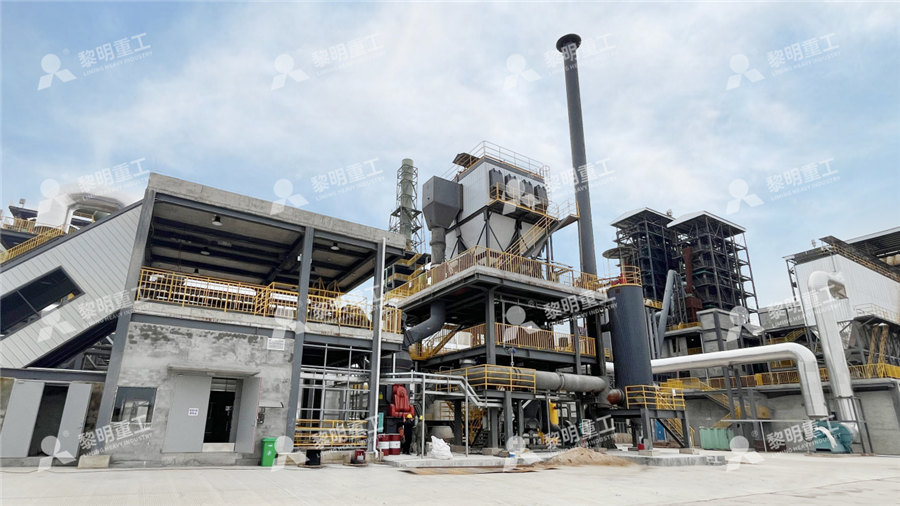
IMPROVING THERMAL AND ELECTRIC ENERGY EFFICIENCY AT
Figure 1: Cement Production Process Flow Schematic and Typical Energy Efficiency Measures 2 Figure 2: Rotary Cement Kiln (Dry Process with Cyclonic Preheaters) 4 Figure 3: 2021年1月21日 An electrical schematic is a diagram that shows how all of the wires and components in an electronic circuit are connected They’re like a map for building or troubleshooting circuits, and can tell you almost everything you How to Read Electrical Schematics Circuit Basicstwo separate Cement Production lines can be summarized into the following processes ;as can be seen in the process and Quality flow diagram below; 1 Quarrying and Crushing 2 Raw material Storage and Transportation 3 Proportioning 4 Raw material Grinding and Transportation 5 Raw meal storage, homogenization and Kiln feeding 6CEMENT PRODUCTION AND QUALITY CONTROLDownload scientific diagram Schematic of ball mill circuit in the Ilam cement plant from publication: Ventilation Prediction for an Industrial Cement Raw Ball Mill by BNN—A “Conscious Lab Schematic of ball mill circuit in the Ilam cement plant
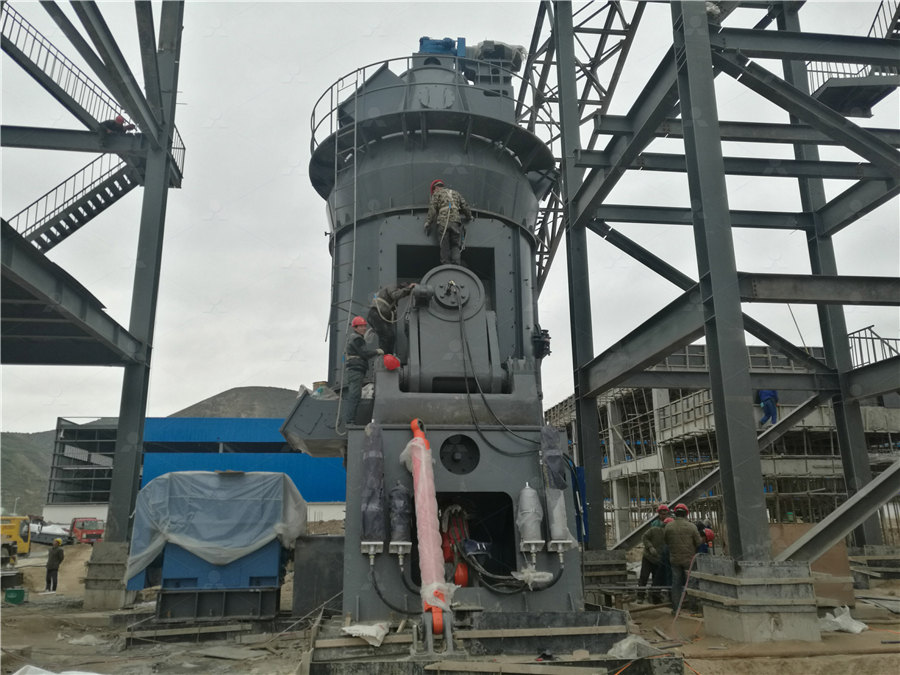
Modeling of energy consumption factors for an industrial cement
80 mm e raw materials were mixed in a certain proportion and fed into a vertical roller mill (LOESCHE mill) e raw vertical roller mill has four rollers, 3000 KW main drive, 48 m table diameter Insufficient mill cooling lead to material agglomeration on balls and liners The grinding is not any more done by balls against material but by material against material SOLUTION Download this post + all manuals and books and Excel sheets and all notes I collected over my 23 years of experiance in Cement industry click here now EVERY COMPONENT OF BALL MILL DETAILED EXPLAINED INFINITY FOR CEMENT Download scientific diagram Schematic diagram of the process integration of a cement plant with an integrated Calooping/CLC unit Abbreviations: R/M, Raw Mill; B/F, Bag Filter; F/D, Fuel Drying Schematic diagram of the process integration of a cement plant in combination with a ball mill for cement grinding applications and as finished product grinding units, as well as raw ingredient grinding equipment in mineral applications This paper will focus on the ball mill grinding process, its tools and optimisation possibilities (see Figure 1) The ball mill comminution process has a high electricalBALL MILLS Ball mill optimisation Holzinger Consulting
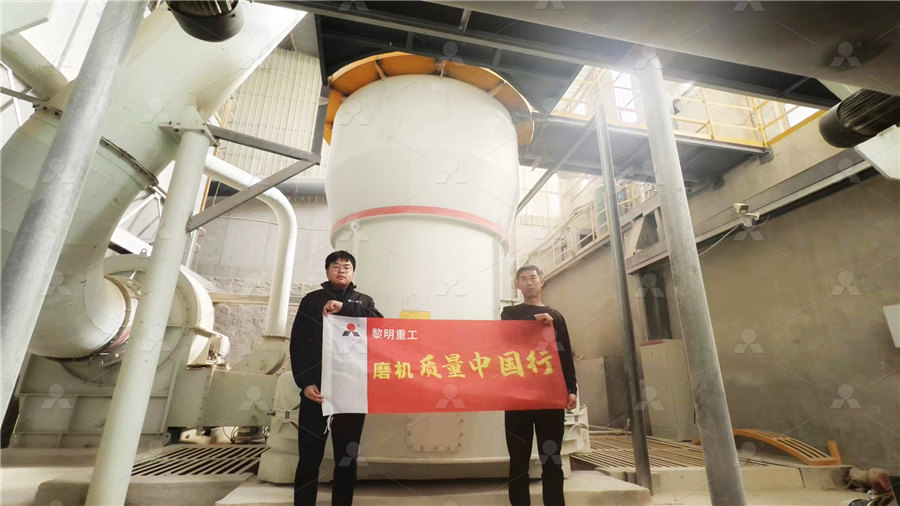
Understanding Electrical Schematics: A Beginner’s Guide
Learn the basics of electrical schematics, including symbols, diagrams, and how to read and interpret them Get started with Electrical Schematics 101 Skip to content ElectraSchematics A Beginner’s Guide to Electrical Circuit Diagrams Electrical schematics are essential tools for understanding and working with electrical circuit diagrams2021年1月22日 In the whole process of cement production, the electricity consumption of a raw material mill accounts for about 24% of the total Based on the statistics of the electricity consumption of the raw A Survey and Analysis on Electricity Consumption of Raw Material Mill The noise intensity was measured at three area of the plants ; raw mill, cement mill, and sillo raw mix There were 23 measuring points where considered as hazardous potential to workersFigure1: Schematic diagram of process units in a cement factoryDownload scientific diagram Schematic layout of a typical cement plant from publication: Energetic assessment of a precalcining rotary kiln in a cement plant using process simulator and neural Schematic layout of a typical cement plant
.jpg)
A Survey and Analysis on Electricity Consumption of Raw Material Mill
Sustainability 2021, 13, 1126 2 of 11 decomposition waste gas as a drying heat source for suspension preheater kiln, etc, have promoted the development of raw material preparation technologyRaw mill is generally called cement raw mill, raw mill in cement plant, it refers to a common type of cement equipment in the cement plantIn the cement manufacturing process, raw mill in cement plant grind cement raw materials Raw mill Cement PlantDownload scientific diagram The use of electrical energy in cement production from publication: Determination of correlation between specific energy consumption and vibration of a raw mill in The use of electrical energy in cement production• Material grindability • Material temperature • Material moisture • Mixture composition • Composition of raw material • Grinding roller wear • Fineness (Blaine) or residue (VOA) • Mill motor speed • Mill air flow/mill differential pressure • Temperature after the mill • Pressure before the mill • Grinding stock feedPROCESS OPTIMISATION FOR LOESCHE GRINDING PLANTS
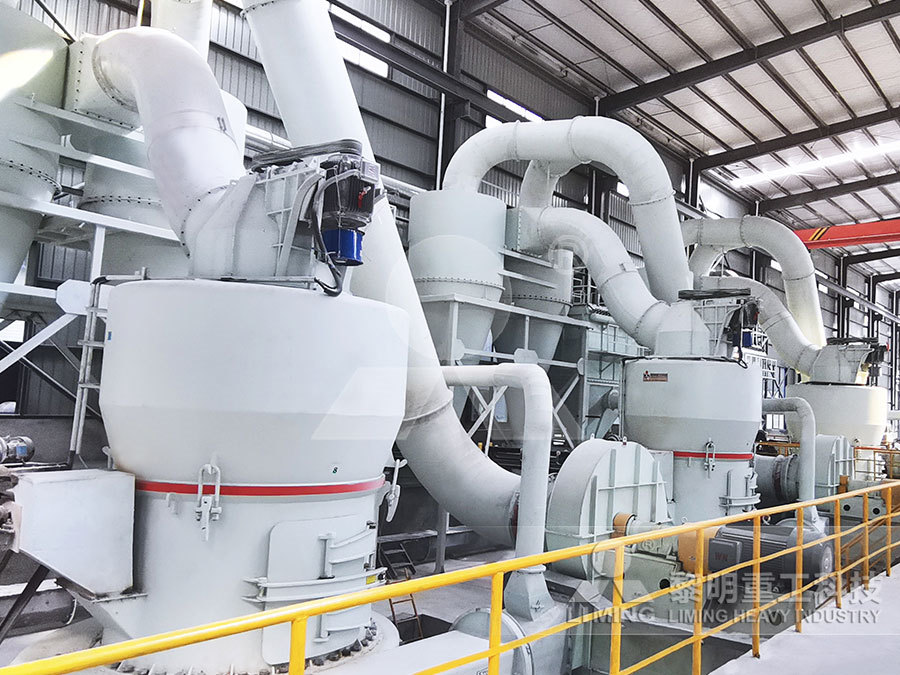
Review on vertical roller mill in cement industry its performance
2021年1月1日 India is the world's second largest producer of cement and produces more than 8 per cent of global capacity Due to the rapidly growing demand in various sectors such as defense, housing, commercial and industrial construction, government initiative such as smart cities PMAY, cement production in India is expected to touch 550–600 million tones per 2024年1月15日 Image used courtesy of Schneider Electric Electrical Diagrams and Prints These drawings are the most common goto resources you encounter when troubleshooting a machine They might actually go by many other names, and here are a few I have run across, but likely there are many more: Wiring Diagrams; Electrical Prints; Line Diagrams Electrical Drawings, Schematics, and Wiring Diagrams: How to Download scientific diagram Flow chart of raw meal production from publication: Effective Optimization of the Control System for the Cement Raw Meal Mixing Process: II Optimizing Robust PID Flow chart of raw meal production Download Scientific DiagramVertical raw mill is one kind of raw mill, generally used to grind bulk, granular, and powder raw materials into required cement raw meal in the cement manufacturing plantVertical raw mill is an ideal grinding mill that crushing, drying, grinding, grading transfer set in one It can be widely used in cement, electric power, metallurgy, chemical industry, nonmetallic ore, and other industriesVertical raw mill Cement Plant
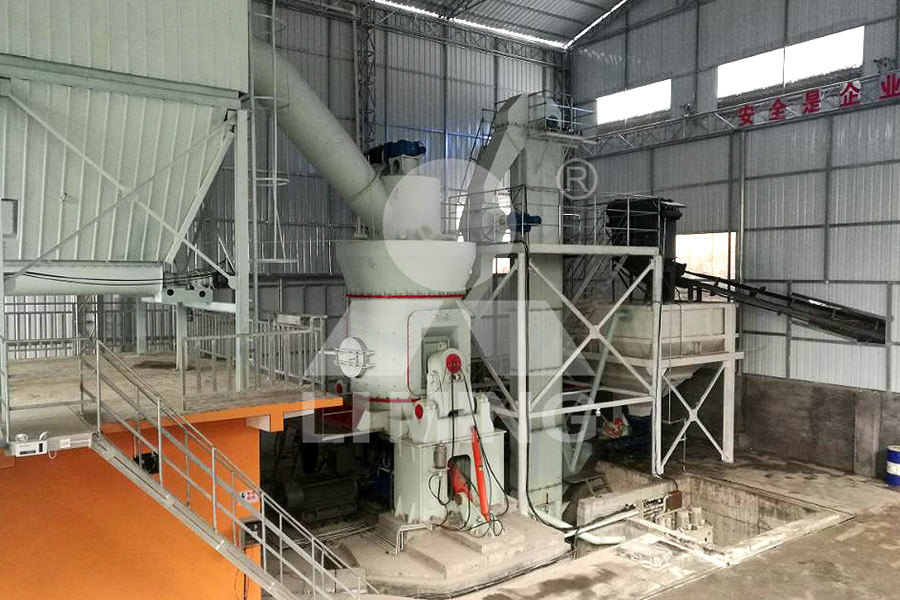
IMPROVING THERMAL AND ELECTRIC ENERGY EFFICIENCY AT CEMENT
2019年3月8日 257 HighEfficiency Fans for Cement Mill V ents Raw material preparation is an electricityintensive Cement Production Process Flow Schematic and Typical Energy E ciency MeasuresThis document provides an overview of cement production including: The types of cement and their raw material compositions The schematic diagram of the cement production process and descriptions of the bins and mill components Cement Mill Report PDF Cement Mill (Grinding)2022年5月9日 Schematic of raw vertical roller mill circuit in the Ilam cement plant Full size image Table 1 Monitoring variables in the Ilam cement plant (STD: Standard deviation)Modeling of energy consumption factors for an industrial cement 2018年9月10日 The simulator was used for the thermodynamic performance of a raw mill (RM) and raw materials preparation unit in a cement plant in Nigeria using actual operating data The raw mill has a capacity (PDF) Thermodynamic Analysis of Raw Mill in

Schematic of cement production Download Scientific Diagram
Suspension preheater is a raw mix preheating equipment used in a cement plant The heat is used to raise raw mix temperature up to 800 0C 900 0CAs the perflow diagram of the wet process of cement manufacturing, The following are the major advantages of the Wet Process of Cement Manufacturing, Raw material can be mixed easily, so a better homogeneous material can be obtained The crushed materials are ground into a fine powder called raw meal in a raw millWet Process Of Cement Manufacturing With Flow ChartIn this study, the raw material blending process in the Nuh Cement Factory in Turkey was investigated Here, three different feed streams, which are low grade, high grade and iron ore, are controlled by weigh feeders and, after mixing on a conveyor belt, fed to the raw mill A simplified schematic diagram of the raw mill blendingMATHEMATICAL MODELING OF A CEMENT RAWMATERIAL Download scientific diagram Process flow diagram for the cement manufacturing process, showing electricity and heat consumption or inputs [39] from publication: Energy Savings Associated with Process flow diagram for the cement manufacturing process,
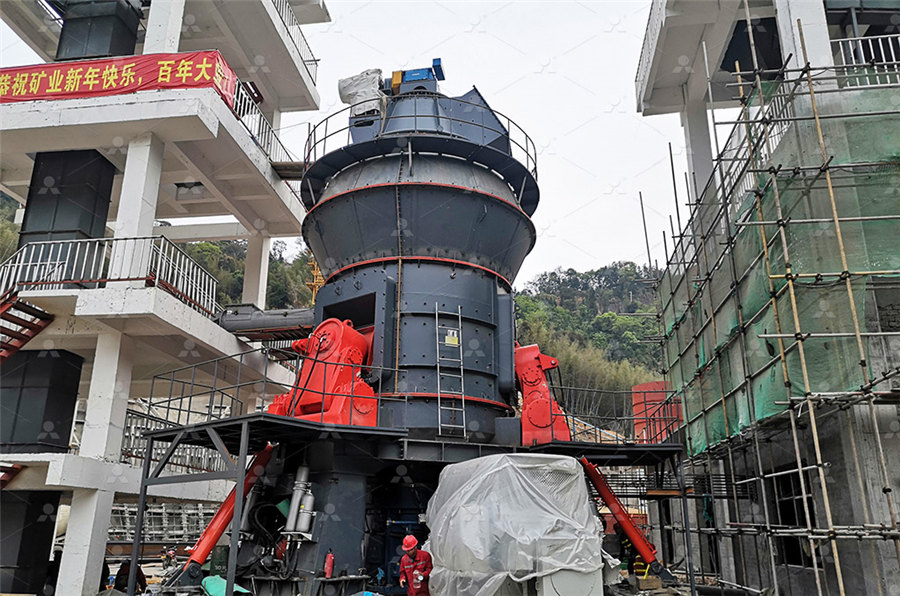
(B) schematic diagram of the raw mill fan ResearchGate
Download scientific diagram (B) schematic diagram of the raw mill fan from publication: Condition Monitoring Based on Vibration Analysis for Defect Diagnosis of Rolling Element Bearing (Case Download scientific diagram Schematic diagram of AG/SAG mill process mechanisms after (NapierMunn et al, 1996) from publication: Multicomponent AG/SAG mill model The JKMRC has been Schematic diagram of AG/SAG mill process mechanismspassivation – 13 Cement quality – 14 Setting time – 15 ASTM cement types and specifications – 16 European EN 197 cement specification – 17 Composite cements (intergrinds and blends) – 18 Supersulphated cement – 19 Calcium aluminate cement (CAC) – 20 Shrinkagecompensating cements (SCC) – 21 ISO 9001:2000 Quality 8The Cement Plant Operations Handbook International Cement 2015年8月1日 The results show that approximately 248t, 469t, and 341t of materials are required to produce a ton of the product in raw material preparation, clinker production, and cement grinding stages (PDF) Analysis of material flow and consumption in
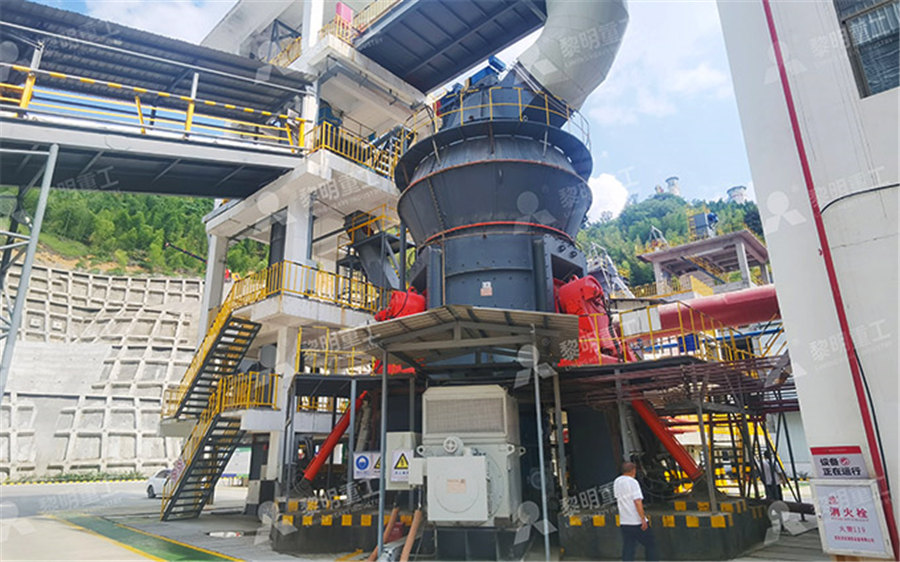
Analysis of vertical roller mill performance with changes in material
2022年5月31日 Mineral crushing is the main source of energy consumption in mineral processing According to statistics, this consumption accounts for about 35–50% of the total cost of the mine (Curry et al, 2014), or even higherIt may also account for 18% of the global electrical energy consumption (NapierMunn, 2015)More efficient crushing equipment needs to be Download scientific diagram Schematic diagram of CPM CL5 pellet mill from publication: Biomass Feedstock PreProcessing Part 2: Densification ResearchGate, the professional network for Schematic diagram of CPM CL5 pellet mill ResearchGateOur bestinclass OK™ Mill is a globally successful vertical roller mill solution for grinding raw material, cement and slag Its cuttingedge design features consistently deliver the highest quality products with the greatest efficiency It is affordable to install and cost effective to operate over your cement plant’s lifetimeOK™ Raw and Cement MillHowever, new cement kilns are of the 'dry process' type Dry process kilns In a modern works, the blended raw material enters the kiln via the preheater tower Here, hot gases from the kiln, and probably the cooled clinker at the far end of the kiln, are used to heat the raw meal As a result, the raw meal is already hot before it enters the Manufacturing the cement kiln Understanding Cement
.jpg)
Schematic of Cement Production Process
2023年10月29日 From here it is conveyed to the mixing bed where it is mixed to a homogeneous material by means of stack and rake Additives such as high grade limestone, sand and iron ore are added and then conveyed to the raw mill where it is dried and ground to a fine powder The raw meal is transferred to the preheater were the material is preheatedFor example, in the dry process of cement production, the raw meal is ground into powders, while in other cement production methods, slurry, spherical, and massive raw meals are also commonly seen However, no matter what form the raw meal is, its chemical composition must be stable, and its fineness and moisture must meet the requirements of clinker calcinationCement Raw Meal Homogenization Process in The Cement Download scientific diagram 1 Schematic diagram of the integrated steel manufacturing process Rough values of some of the raw material and byproduct streams are presented in parentheses from 1 Schematic diagram of the integrated steel manufacturing Schematic diagram of double roll crusher With widely varying raw material characteristics as well as feed and product size requirements, Brundick, H, “Drying and grinding of extremely moist cement raw materials in the Loesche mill,” ZKG International, No2, 1998, pages 6471Brundick, Horst, and Schäfer, Everything you need to know about cement Materials Preparation and Raw

Rawmill Wikipedia
A raw mill is the equipment used to grind raw materials into "rawmix" during the manufacture of cement Rawmix is then fed to a cement kiln, which transforms it into clinker, which is then ground to make cement in the cement mill The raw milling stage (ie it takes place by collision between lumps of raw material), and is