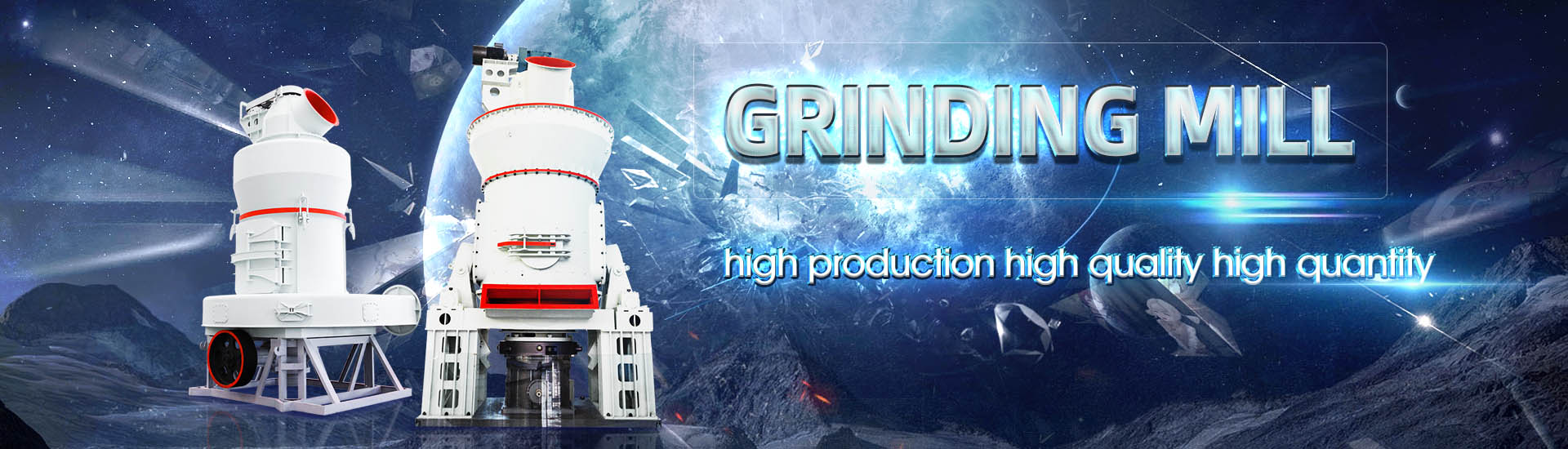
Vertical mill with rod cavity and no pressure
.jpg)
Optimization of VRM Operation RUCEMRU
Vertical Roller Mills Pressure Profile Draw Up Curve Influenced by: •Mill Inlet Pressure •Nozzle Ring Coverage •Classifier Speed •Dam Ring Height •Mill Load •Material Blockage in Hot Gas Vertical Roller Mills (VRM) have a clearly higher energy eficiency than ball mills, even if the ball mill is combined with a roller press This and further arguments led to the increased share of SikaGrind® for vertical roller mills2016年9月1日 The results of setting time, compressive strength, soundness and moisture content showed that both gypsum and hemihydrate had the same performance in vertical Operational parameters affecting the vertical roller mill 2023年6月1日 In this paper, a numerical calculation method for internal particle–fluid coupling system of large vertical mills based on CFDDPM theory and a multiobjective optimization Operation parameters multiobjective optimization method of
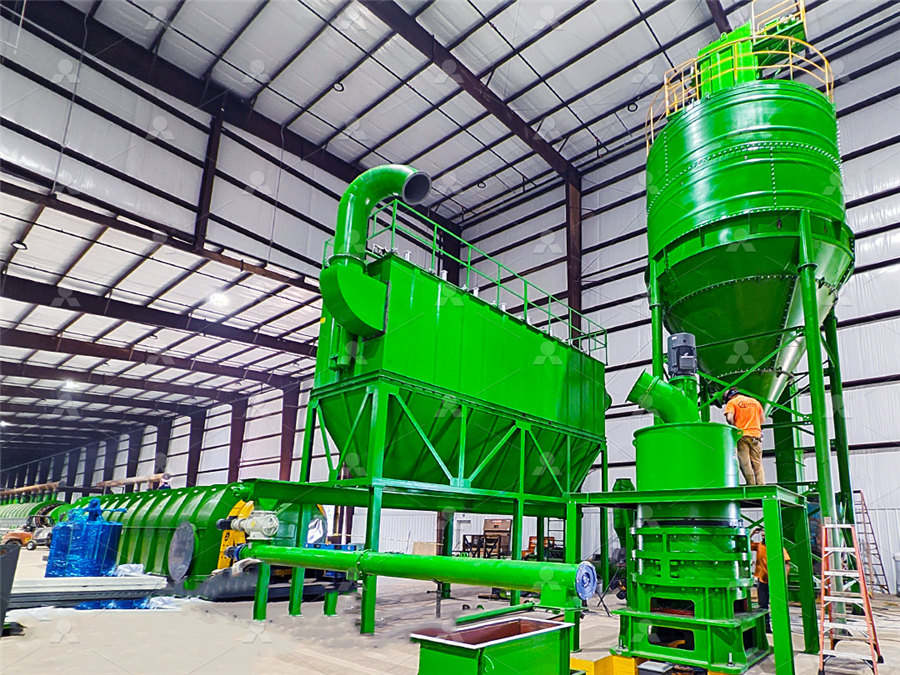
Vertical roller mill for raw Application p rocess materials
Vertical roller mills are adopted in 20 cement plants (44 mills) in Japan In the vertical roller mill which is widely used in the raw material grinding process, raw materials input grinding table Abstract: The lower rocker arm is an important part of the vertical roller mill and its lightweight design is of great significance for reducing the mass and production cost of the rollerOptimization Design of the Lower Rocker Arm of a Vertical Roller a vertical roller mill (VRM) • Surpasses the classic methods if the controlled process demonstrates significant disturbances • A high degree of attention to the process states is required in order PROCESS OPTIMISATION FOR LOESCHE GRINDING PLANTS2017年4月1日 Vertical roller mills (VRM) have found applications mostly in cement grinding operations where they were used in raw meal and finish grinding stages and in power plants Operational parameters affecting the vertical roller mill
.jpg)
coal grinding machine CHAENG
Process introduction Vertical coal mill, also known as vertical roller coal mill or vertical coal grinding mill, is a mechanical equipment for crushing and grinding coal into coal powerMainly used for grinding raw coal, bituminous coal, and other fuels into coal powder, which is supplied to rotary kiln and other kilns in the cement plant and thermal power plant2020年6月24日 Comparison of Sucker Rod Pump and Progressive Cavity Pump Performances in Batı Raman Heavy Oil Field of Turkey(PDF) Comparison of Sucker Rod Pump and 2023年6月1日 This study aims to improve the output and production efficiency of a large vertical mill by optimizing its operational parameters This paper takes a large vertical mill in LGM as the object, a numerical calculation method of particle–fluid coupling system in large vertical mill based on CFDDPM theory, and a multiobjective optimization method of operating parameters of Operation parameters multiobjective optimization method of With years of technical innovation experience in cement and slag grinding, Shanghai Yingyong Machinery Co, Ltd has successfully developed various models of vertical roller mills Our team of specialists is dedicated to assisting customers worldwide in creating dependable, energyefficient, and highperforming solutions for vertical roller mill grindingOptimize Your Grinding Process with Our Vertical Roller Mills
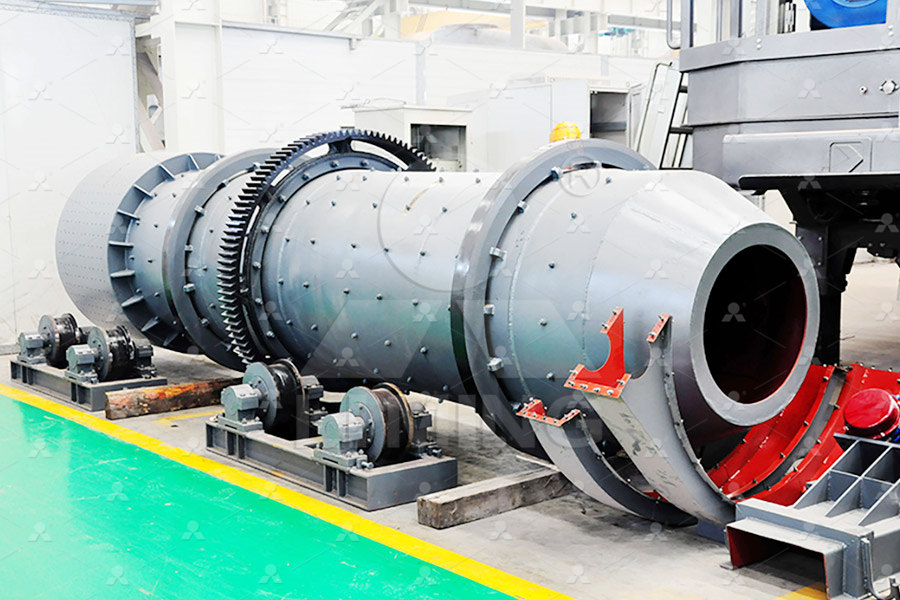
Operation Manual: HRM1700M Vertical Roller Coal Mill
The document provides installation and operation instructions for the HRM1700M Vertical Roller Coal Mill It describes the mill's technical parameters, components, structure, working principles, and installation process Key aspects include grinding rollers that can be removed for maintenance, a hydraulic system that controls grinding pressure, and a separator that High pressure coolant or compressed air with through tool coolant; DC should be no greater than 75% of hole dia Use a large axial cut – maximum a e = 2 x DC; The drilled hole should be entered in a circular path: Control radial engagement, maximum a e = 30% of DC; Control radial engagement to minimize vibration in corners and to maximize Milling holes and cavities/pockets Sandvik Coromantof 80mm The raw materials are mixed in a certain proportion and fed into a vertical roller mill (LOESCHE mill) The vertical roller mill grinds the marital to D 85 of 90µm The ground product is calcined in a preheater to 850900℃ After calcination, the materials enter to a rotary kiln and heated to 1450℃ to become clinkerModeling and simulation of vertical roller mill using population 2023年8月28日 Cut blasting is a key step in the drill and blast method In underground engineering, confining pressure has a significant influence on the cut cavity formation process In this study, the smoothed particle hydrodynamicsfinite element method (SPHFEM) considering confining pressure is used to describe the characteristics of the cut blasting process The Numerical Study on Evolution Mechanism of Cut Blasting and Cavity
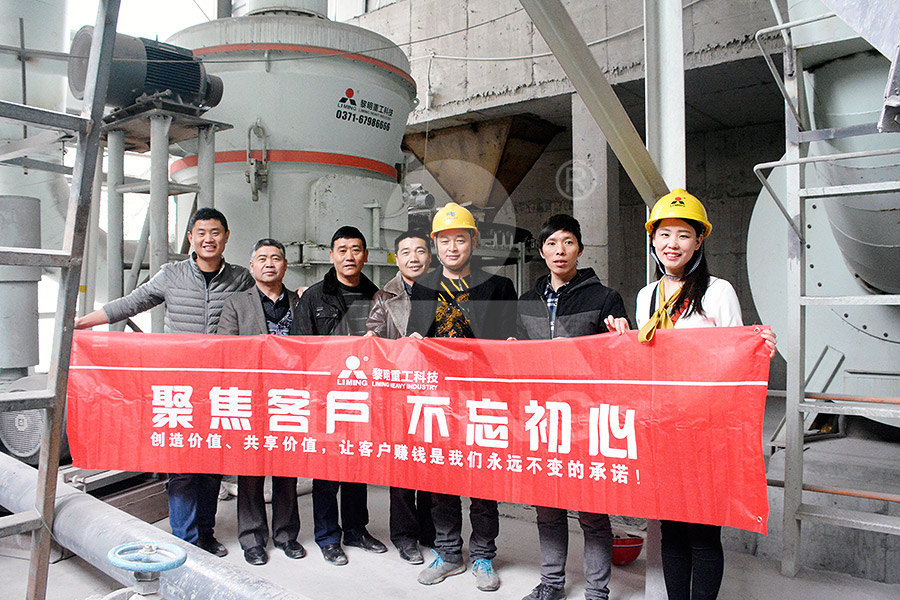
Numerical investigation on the cavity dynamics and multiphase flow
2021年5月1日 From the literature review, one of the earliest studies on the evolution of cavity and splash for vertical water entry of rigid sphere based on highspeed camera technology were performed by Worthington (1908), Worthington and Cole (1897)For the past decade, research on the water entry of projectiles was mainly focused on the experimental investigation of cylinders CLUM Ultrafine Vertical Grinding Mill Discharge fineness: 1503000 mesh Feed size: 15 mm Output: 120 T/HCLUM Ultrafine Vertical Grinding MillFIG 1 illustrates force displacement curves AD in such traditional counter pressure systems utilized in a roller mill Since the cushion effect is directly proportional to the counter pressure magnitude, as the cushion effect is increased, that is, as one goes from the system depicted in curve A toward the system depicted in curve D, the system stiffness, or steepness of the force Vertical roller mill with improved hydropneumatic loading system2009年1月31日 This study investigated a mathematical model for an industrialscale vertical roller mill(VRM) at the Ilam Cement Plant in Iran The model was calibrated using the initial survey's data, and the Grinding process within vertical roller mills ResearchGate
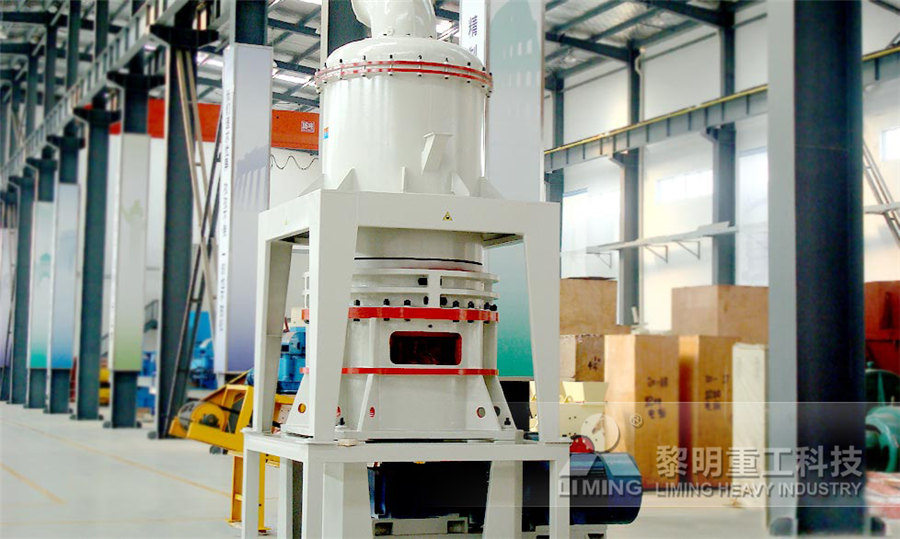
Passive Reduction of Pressure Fluctuation by Using Cylindrical Rod
2021年11月23日 A Kulite dynamic pressure transducer (XCQ062 ± 1D) was utilized for unsteady pressure measurements inside the cavity Twelve pressure transducers were flush mounted at the cavity ceiling as well as at the front and rear vertical walls along the centerline of the cavity The locations of the pressure transducers are shown in Fig 22012年1月1日 A 15,000psi stress at rated system pressure, with smooth system operation and no pressure pulses, is considered conservative System pressure spikes that cause 30,000psi stress often are not alarming, but at 30,000psi unit stress, steel's dimensional change is Engineering Essentials: Cylinders Power Motion2021年8月1日 The pressure dependence is reversed close to the pressure side, which leads to an increasing contact area of the considered SSL with increasing differential pressure (see Fig 13 (c)) The results in Fig 13 suggest that the amount of backflow mainly depends on the shape of the SSL closest to the suction side, because any SSL closer to the pressure side exhibits a Modeling pressure pulsation and backflow in progressing cavity 2023年11月16日 Company Introduction: CNBM Hefei Zhongya Building Material Equipment Co, Ltd is a technologyoriented enterprise with the integration of research development, engineering design, equipment manufacture and technical service, which was established by professional scientific technical personnel engaged in research of vertical mill from Hefei Vertical Roller Mill and Vertical Grinding Mill MadeinChina
.jpg)
(PDF) Matrix Model Simulation of a Vertical Roller Mill with High
2014年5月1日 This study investigated a mathematical model for an industrialscale vertical roller mill(VRM) at the Ilam Cement Plant in Iran The model was calibrated using the initial survey's data, and the 2013年3月1日 This study investigated a mathematical model for an industrialscale vertical roller mill(VRM) at the Ilam Cement Plant in Iran The model was calibrated using the initial survey's data, and the Cements ground in the vertical roller mill fulfil the quality CLUM series ultrafine vertical roller millwas produced by Shanghai Clirik Machinery Co, Ltd Relying on 12 years of experience in the production of ultrafine powder and based on German and Taiwan ultrafine vertical mill technologies The top technical team members were joined this project Besides, highquality wearresistant parts are used to develop milling equipment which Ultra fine vertical roller millUltra Fine Millultramillindustrial 2019年11月8日 Progressing Cavity Pump Troubleshooting Guide by North Ridge Pumps Excess Pressure on Outlet Increase pump size or motor size Change piping configuration / system set up to reduce pressure on outlet Company Registration No: VAT Number: GB 324 963 488Progressing Cavity Pump Troubleshooting Guide North Ridge
.jpg)
Design and Realization Of Roller Mill Control System ResearchGate
QianHong Wang et al / Physics Procedia 33 ( 2012 ) 437 – 443 439 temperature, pressure, and flow rate, things as a simulation signal and equipment as state of switchVRM operations Free download as PDF File (pdf), Text File (txt) or view presentation slides online The document provides information on controlling parameters for a vertical roller mill (VRM) system It discusses how increasing or decreasing various parameters like grinding pressure, feed rate, water supply, fan damper setting, and separator vanes impact the mill VRM Operations PDF Nozzle Mill (Grinding)2023年3月15日 Greener More Automated The operation of LM grinding mill is stable and has small vibration, so that the noise is small The system is sealed in an integral manner and works under negative pressure, so that there is no dust spilling and the environment can keep clean with the emission standard far better than the international standardLM Vertical Grinding Mill SBM Mill Crusher152 mm [5] for the crab cavity including the space for cryogenic shielding, thermal contraction and the cavity wall thickness Thus the inner radius of the outer can of the crab cavity will be limited to 145 mm for all designs outlinedinthis paperto meetthese spatialrequirementsAt 400 MHz an elliptical cavity similar to the KEKB cavityDesign and testing of a four rod crab cavity for High Luminosity
.jpg)
Copper Ore Grinding in a Mobile Vertical Roller Mill Pilot Plant
2014年10月1日 In a test performed in the Loesche test center in Germany, copper slag grinding saved 229% energy in an airswept model and 344% energy in an overflow model [13,14]Description Characteristics of Summit ® HeavyDuty vertical boring mill and milling (VBM) machines Summit ® HeavyDuty vertical boring mills and milling (VBM) machines offer smooth running, superior speed control, and maximum reliability in a costeffective solution Summit’s 48″ 60″ (single column) and 80″ – 120″ (double column) vertical boring mills feature closedgrain Vertical Boring Mill and Turning Machines Summit Machine ToolVertical Roller mills Vertical Roller mills Main parts of a vertical roller mill Mill body feed Hydraulic system Nozzle and retention ring mill body seperator Vertical roller mill: frame type Polysius: Polroll Gbr Pfeiffer: MPS Vertical roller mill: rocker arm type Loesche: LM Kobelco: OK Processes inside a vertical roller mill GrindingParts of Vertical Roller Mill INFINITY FOR CEMENT EQUIPMENTVertical mill USB2 (en) * : : Mitsubishi Heavy Industries, Ltd Vertical mill USB2 (en) : : Sustainx, Inc Energy storage and recovery utilizing lowpressure thermal conditioning for heat exchange with highpressure gas USB2 (en) USB2 Vertical roller mill with improved hydro
.jpg)
Research on Dynamic Response of Cold Rolling Mill
2023年1月25日 The vibration of the vertical system of a cold rolling mill is a major concern for factory production In factory production, it is found that the thickness control system with dynamic stiffness 2024年1月29日 This research aims to evaluate horizontal and vertical constrained rod casting (CRC) molds on hot tearing susceptibility (HTS) of AlxCu casting alloys with 22, 36, 75, and 125 percent Cu The hot tears on the casting product were observed using a macroscopic approach In addition, the hot tearing susceptibility of each casting product prepared using Evaluation of Horizontal and Vertical Constrained Rod Casting 2023年11月28日 The diagram shown in Fig 1 defines several parameters in accordance with the metal rolling principle h 0 represents half of the strip entry thickness, while h 1 denotes half of the strip exit thickness, h c is half of the loaded roll gap h' c is the speed of roll system motion The radius of the work roll is given by R, and the centers of the work roll at static and dynamic Dynamics and stability analysis of rolling mill system during 2017年4月1日 The control of the circulating load is achieved by adjusting the pressure drop over the mill comprising out of the gas flow and the solid loading inside the mill Comparison of the vertical roller mill and rodball mill circuit on the gold extraction Proceedings of XIIIth International Mineral Processing Symposium, Bodrum, TurkeyOperational parameters affecting the vertical roller mill
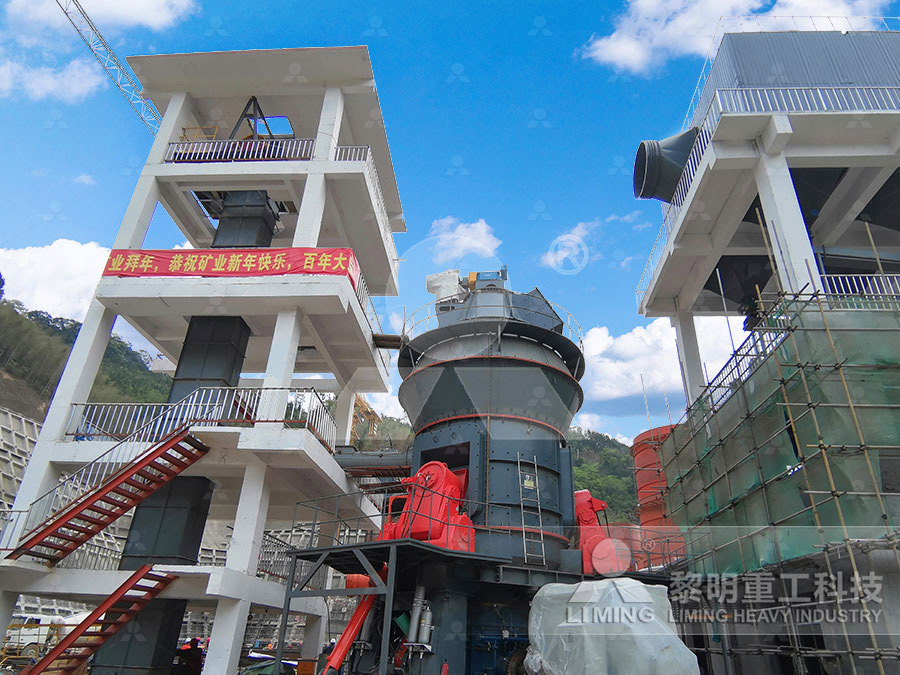
Copper ore grinding in a mobile vertical roller mill pilot plant
2015年3月10日 Comparison of the vertical roller mill and rodball mill circuit on the gold extraction; such as the application of highpressure roller mill [Altun et al, 2015; Ma et al, 2021; Bilen et al, 2021] In recent years, the crushing equipment and 2019年11月2日 The rolling mill with hydraulic system is widely used in the production of strip steel For the problem of vertical vibration of the rolling mill, the effects of different equivalent damping coefficient, leakage coefficient, and proportional coefficient of the controller on the hydraulic screw down system of the rolling mill are studied, respectively First, a vertical Research on the Vertical Vibration Characteristics of Hydraulic Screw 2019年10月10日 processes Article Bifurcation Characteristic Research on the Load Vertical Vibration of a Hydraulic Automatic Gauge Control System Yong Zhu 1, Shengnan Tang 1,2,*, Chuan Wang 1,3,*, Wanlu Jiang 4, Xiaoming Yuan 2,4 and Yafei Lei 4,* 1 National Research Center of Pumps, Jiangsu University, Zhenjiang , China; 2 State Bifurcation Characteristic Research on the Load Vertical Vibration A vertical roller mill, also known as a vertical grinding mill or vertical mill, is a comprehensive grinding equipment integrating crushing, drying, grinding, grading, and conveying Vertical grinding mills can be widely used in electric power, metallurgy, construction, chemical industry, and other industries to make powder, especially for materials such as cement clinker, coal Energysaving and Efficient Vertical Roller Mill Fote Machinery
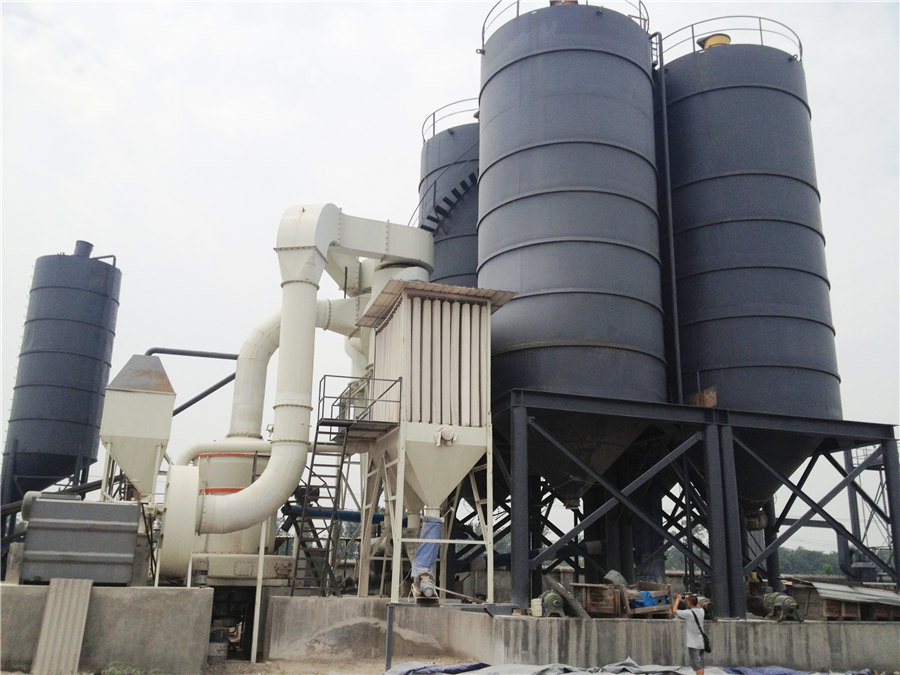
Raymond Mill Models And Parameters
2021年8月27日 Raymond mill is a vertical mill It is widely used because of its small footprint, low investment cost, and simple operation Raymond mill is widely used in the industrial field, especially in the field of mine milling It can pulverize different raw materials Processing is divided into many different models according to the output2014年7月25日 In this paper, vibration characteristics of a Vertical Roller Mill (VRM) are studied by using physical parameters of an operating VRM The mathematical model is derived and simulated for a set of Vibration Analysis of a Vertical Roller Mill: Modeling and Validation