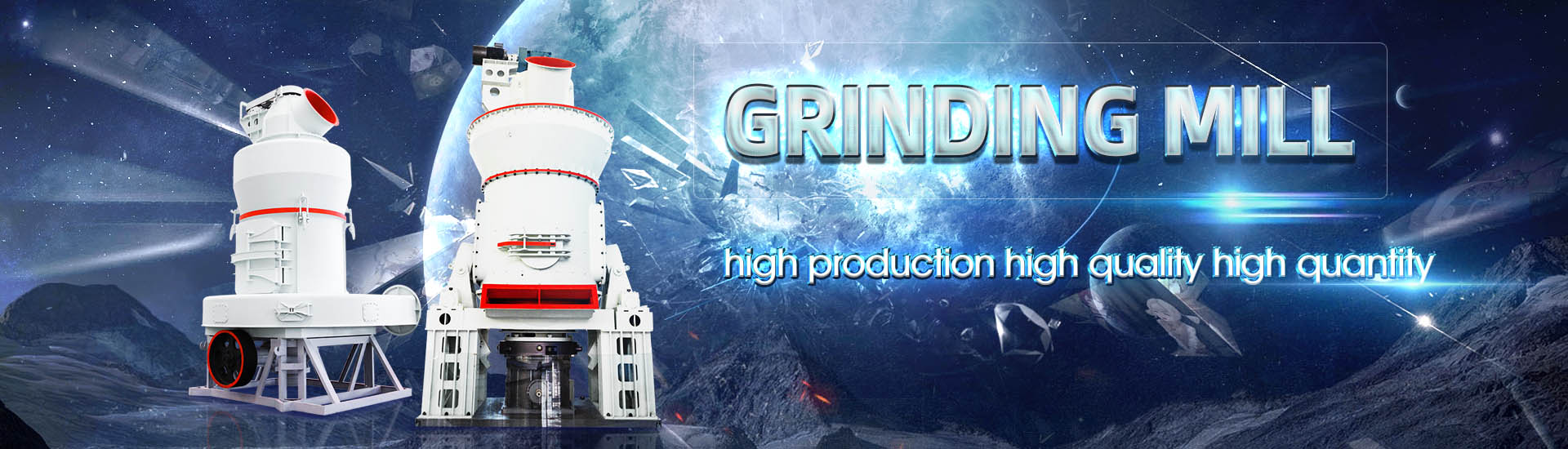
Water slag iron mineral grinding machinery process flow
.jpg)
A new technological approach to the granulation of slag melts of
2021年11月3日 A system analysis of advantages and features of the semiindustrial pilot HVGplant showed that its operation for granulation of slag melts of ferrous metallurgy in enterprises 3 Steelmaking Slag Processing Technology The iron/steel slag processing flow is schematically shown in Fig 2 Steelmaking slag is subjected to the following four processes: ① solidify and Processing and Reusing Technologies for Steelmaking SlagMetallic mineral processing typically involves the mining of ore from either open pit or underground mines; the crushing and grinding of ore; the separation of valuable minerals from 1124 Metallic Minerals Processing US EPA2019年6月18日 Slag produced as a byproduct in industrial processes, contains considerable metals contents, which need to be recovered to avoid environmental contamination In present review, the types,(PDF) Metallurgical Processing Strategies for Metals
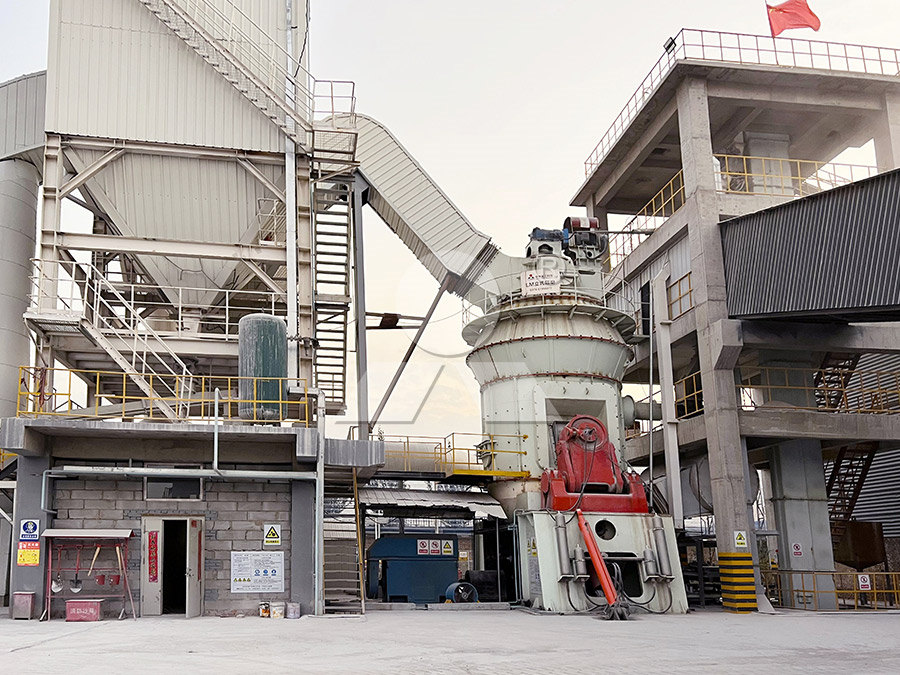
Innovative approaches for an optimized processing of
Combinations of crushing, followed by several grinding stages via rod and ball milling are used Ductile characteristics of the metal contents are used to separate liberated metal phases from 2019年10月29日 In this article, the potential application of iron and steelmaking slag has been reviewed, which included the slag utilization in construction as cement and sand, in water, soil, and gas treatment, as well as in value The potential utilization of slag generated from ironFigure 7 and 8 the process flow diagram of a granulator and heat recovery system for superheated steam production is shown The process parameters shown in these figures are exemplary for aProcess flow diagram of a dry slag granulation system 2024年4月15日 This study explored the recovery of valuable metal elements in the lead smelting waterquenching slag using the method of “roasting–grinding–magnetic separation” at a Iron recovery from lead smelting waterquenching slag by
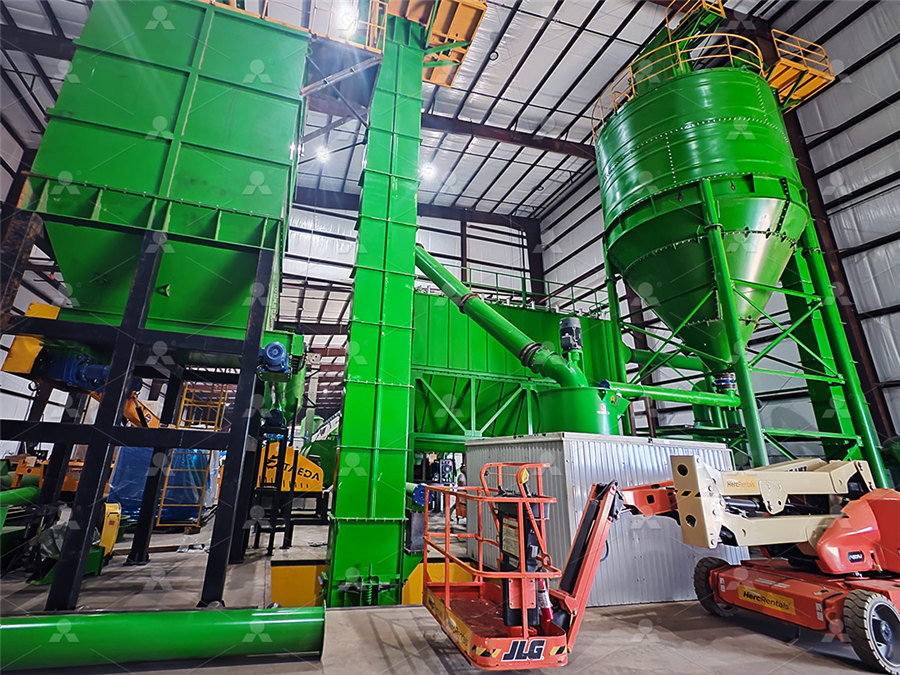
Granulation and Heat Recovery from Metallurgical Slags
2019年12月9日 Conventional water granulation of slag has some shortcomings when measured against increasingly stringent requirements for sustainable operations As a “wet” process, 2009年9月23日 Results are presented showing that it is possible to produce metallic iron directly from lowgrade ores The metal is in a form that can be easily separated to produce a high Strategies for processing lowgrade iron ore minerals ResearchGateWhen the mass ratio of the original BOF slag to phosphate tailings was 7:3, the P 2 O 5 content in mixed slag increased to 55% and it was concentrated in one mineral phase which was conducive to The technical flow process of recycling ironrich 2024年8月15日 Comminution involves both crushing and grinding As the first step in mineral processing, comminution is to process large pieces of ore into smaller pieces with the help of crushers and grinders 2 Sizing/Screening Mineral Processing Plants: What You Need to Know
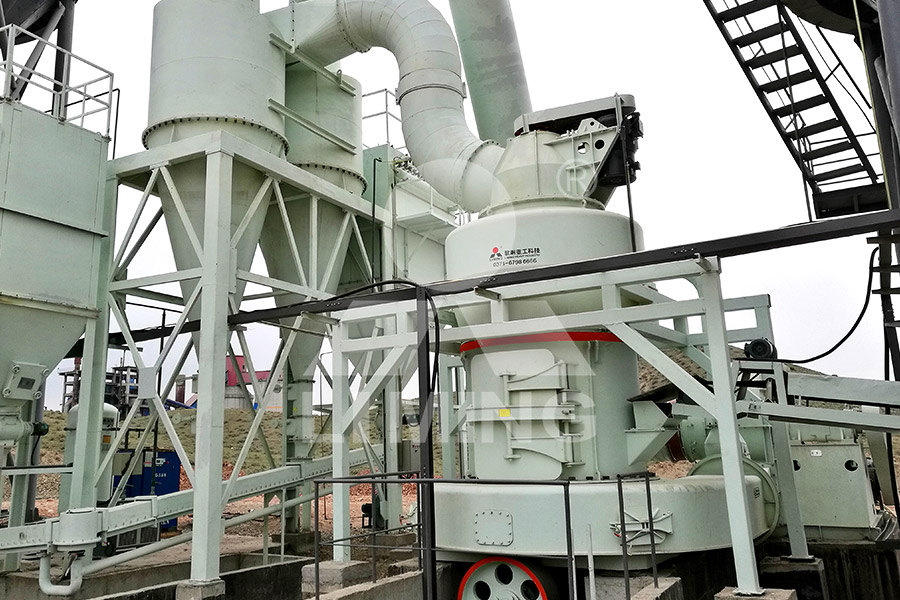
What is a ultrafine slag grinding plant? ultrafine slag
2023年10月19日 Process flow of ultrafine slag grinding The process scope of the ultrafine composite mineral admixture grinding system includes the following steps: starting from the bottom of the storage at 2023年2月15日 Slag bricks Slag brick production process Slag brick is made by mixing, watering, grinding and pressing slag and limestone In the production process of slag brick, the particle size of the slag is generally smaller than 8 mm, and the steam temperature injected into the kiln is about 80 ℃ to 100 ℃, the maintaining time is about 12 hoursHow to Process Slags (with detailed process)? Fote MachineryWhen iron ore is extracted from a mine, it must undergo several processing stages Six steps to process iron ore 1 Screening We recommend that you begin by screening the iron ore to separate fine particles below the crusher’s CSS before the crushing stage A static screen is used to divert the fine particles for crushingThe six main steps of iron ore processing Multotec2014年10月1日 To achieve a stable slagtapping process in entrainedflow coal gasifiers, the acceptable viscosity of coal ash slag is within 5–25 Pas in the temperature range 1200–1500 °C and the tapping Slag properties of blending coal in an industrial OMB coal water
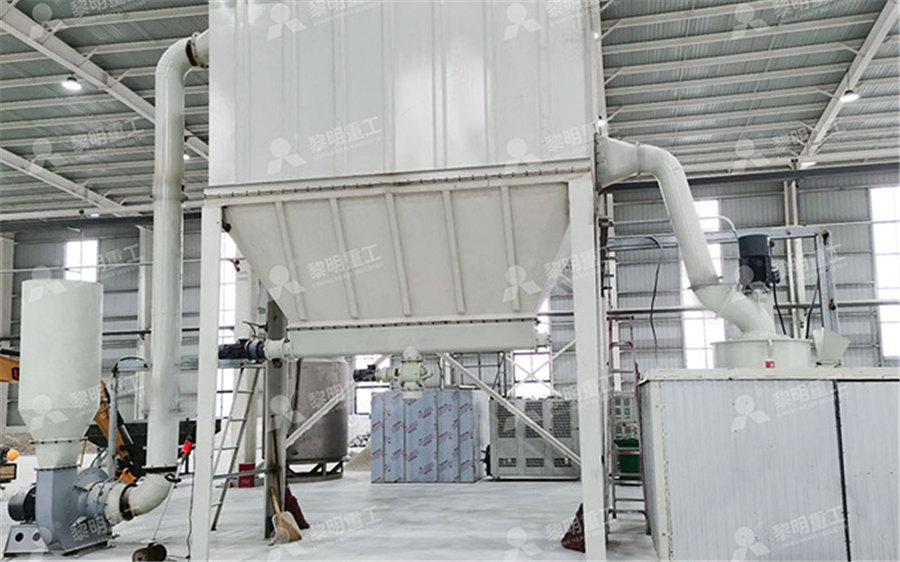
Iron Ore Beneficiation Plant Equipment For Mining Process
2023年9月4日 Dry magnetic separator: It is a preclassifier for grinding iron powder to recover iron from waste steel slag 3 Iron ore gravityseparation equipment Select a gravityseparating machine based on the particle size of the iron ore There are fixture gravity separation, vibrating screen separation, and chute separationJune 2022; ARCHIVE Proceedings of the Institution of Mechanical Engineers Part C Journal of Mechanical Engineering Science 19891996 (vols 203210) 236(2):1107(PDF) A comprehensive review on the grinding process: 2022年2月26日 Blast furnace slag can be processed into the following materials by various processes In China, blast furnace slag is usually processed into water slag, slag gravel, expanded slag and slag beadsWater slag is the process of putting the hotmelt blast furnace slag into water for rapid cooling, which mainly includes slag pool water quenching or furnace front What is Blast Furnace Slag and How to Process It?2019年12月9日 Metallurgical slags are produced at a massive rate of over 750 Mt/year, and carry a thermal energy equivalent to 40 Mt/year of coal The potential mineral and thermal energy values of slags are in the order of $22 b and $3–6 b per year Such attractive figures, together with tightening legislation on disposal of slag and the carbon footprint associated with the loss Granulation and Heat Recovery from Metallurgical Slags
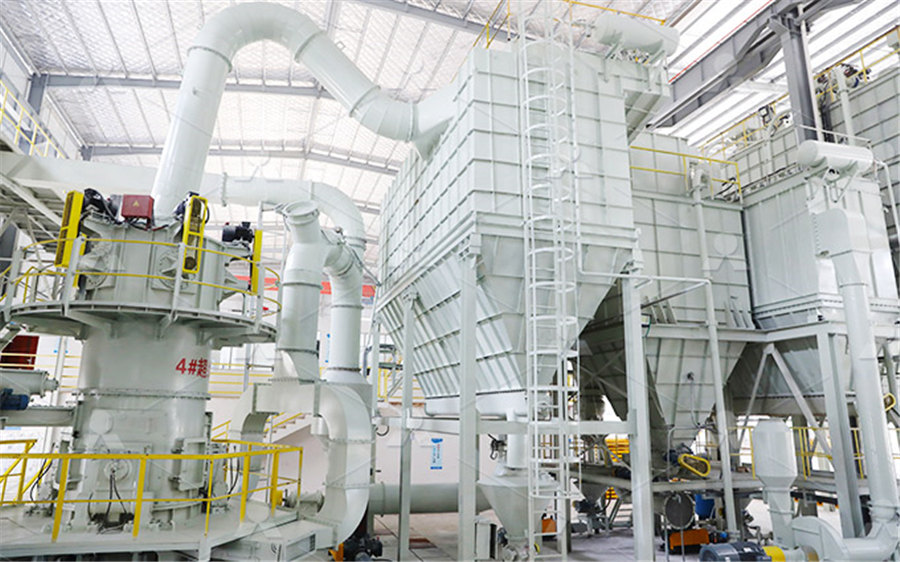
Steel slag recycling crushing and grinding production line
Process flow diagram (wet process): Wet process: The dryprocess steel slag production process does not need to consume precious water resources After the steel slag is crushed, rod milled, and magnetically separated, the slag steel can be selfgrinding to obtain grade A and B scrap steel The iron content of the slag powder can reach more 2022年12月15日 Roughly 10% of the CO2 emissions from iron and steel making are attributable to the direct release of CO2 from the thermal decomposition of carbonates to produce flux, mainly CaO, used for Enhancing CO2 Mineralization Rate and Extent of Iron 2024年3月12日 Steel slag separation typically employs magnetic separation, aiming to extract useful iron metals from the slag Both steel particles and iron powder in the steel slag exhibit magnetism Therefore, magnetic separators Steel Slag Recycling: The Definitive Processing Solution2021年11月3日 The technological factors required to improve the operational properties of granulated metallurgical slags demanded in the building industry have been analyzed In order to satisfy these factors, a new technology for hydrovacuum granulation of slag melts (HVG) has been developed It is shown that the main advantage of the proposed HVG process is the A new technological approach to the granulation of slag melts of
制粉项目-2023.11.17.jpg)
Blast Furnace Slag Ball Mill
According to the characteristics of blast furnace slag, the blast furnace slag grinding line is equipped with a magnetic separator for iron removal Blast furnace slag ball mill adopts a special liner, sieving device, motor, and discharging device In the production process, slag ball mill can not only grind the slag separately, but also mix 2024年4月15日 This study explored the recovery of valuable metal elements in the lead smelting waterquenching slag using the method of “roasting–grinding–magnetic separation” at a roasting temperature of 1250 °C, coal dosage of 125%, roasting time of 90 min, and grinding time of 45 min An iron concentrate with a grade of 9361% and a recovery rate of 9071% were obtainedIron recovery from lead smelting waterquenching slag by 2016年10月28日 The converter steel slag cannot be widely used in building materials for its poor grindability In this paper, the grinding characteristics of untreated and pretreated (ie, magnetic separation) steel slag were compared Additionally, the grinding property of pretreated steel slag was also studied after adding grinding aids The results show that the residues (ie, oversize Comparison of Grinding Characteristics of Converter Steel Slag Water quenching blast furnace slag (WQBFS) is widely produced in the blast furnace iron making process It is mainly composed of CaO, MgO, Al2O3, and SiO2 with low contents of other metal elements Treatment procedure of water quenching blast furnace slag
.jpg)
Mineral Processing Flowsheets 911Metallurgist
2016年3月8日 The Mineral Processing Flowsheets shown on the following pages are based on actual data obtained from successful operating plants Metallurgical data are shown in these flowsheets which incorporate Crushers, Grinding Mills, Flotation Machines, Unit Flotation Cells, and Selective Mineral Jigs as well as other standard milling equipment The Flotation Machine, 2022年9月25日 The results showed that under the conditions of reduction temperature of 1400 °C for 6 h, reducing agent of 20 ml/min, the iron olivine and magnet mineral phases in CSS had been transformed into iron particles, and there was an obvious phase boundary between iron particles and slag phase, which was also conducive to the dissociation of iron particle Extraction and separation of copper and iron from copper smelting slag 2019年8月23日 From the perspective of mineral processing technology, the iron ore is divided into: magnetite ore, weak The fine sieving and regrinding process is an effective method to improve the grade reasonable, and Iron Processing Equipment, Process Flow, Casesmagnetic separator to recove iron from steel slag r While, the hematite is weak magnetic mineral, and the iron share is 1835% So, the magnetic intensity should not be too low Although quartz and plagioclase have high iron contents, their iron grade and iron share are relatively low and cannot be recovered in a weak magnetic field In view DRY MAGNETIC SEPARATION TECHNOLOGY FOR THE RECOVERY OF IRON MINERALS
.jpg)
Carbon mineralization of steel and ironmaking slag: Paving the
2024年4月1日 Carbon mineralization technology has emerged as a promising method for permanently sequestering CO 2 by transforming it into a thermodynamically stable solid carbonate material Recently, alkaline industrial waste, particularly from steel and ironmaking processes, has been identified as a proper feedstock due to its high potential for CO 2 storage and the 2023年11月8日 The process of titanium slag production is the process of smelting ilmenite concentrate in arc orethermal furnaces (OTF) in a semiclosed mode with the use of a powder mixture to obtain titanium slag of a specified content of iron oxide, as well as associated metalTitanium Slag Production Process: Technologies To Improve 2019年5月23日 Also, the ferrous acid salt mineral is an abrasive resistance mineral Thus, the mineral phase of iron in steel slag is the main abrasive resistance mineral component The mineral phase of iron in steel slag is mainly the solid solution of ferrous oxide, and there are multiple mineral symbionts of few magnetite, sosmanite, and prehensive Utilization Technology of Steel SlagDownload scientific diagram Process flow sheet for Pelletization using dry grinding process from publication: Iron Ore Pelletization Technology and its Environmental Impact Assessment in Eastern Process flow sheet for Pelletization using dry grinding process
.jpg)
Process Flow of Recovering Ferrochrome from Ferrochrome Smelting Slag
2021年4月6日 Chromium iron slag treatment process The treatment plan of ferrochrome smelting slag comprehensively adopts the processes of crushing, screening, jigging, and dewatering First, coarse crushing is used to crush a large piece of ferrochrome smelting slag in two stages to obtain ferrochrome smelting slag below 30mm2016年3月11日 By improved efficiency a decrease in energy consumption per ton of crude milled should be achieved Further savings resulting from finer crushing are realized in the concentration or mineral recovery phase of a process These benefits are rather difficult to quantify due to the varying complexities of the concentrators and benefication processesCrushing Plant Flowsheet DesignLayout 911Metallurgist2024年11月21日 In the past, a lot of experimental research work on this type of iron ore beneficiation, including reduction roasting – weak magnetic separation process of the selection index is relatively good, but because of its technical difficulties is the need for ultrafine grinding, and the current conventional beneficiation equipment and chemicals Various Types Of Iron Ore Beneficiation Processes JXSC Machineryof concentrates to ease further handling and refining Figure 11241 is a general flow diagram for metallic mineral processing Very few metallic mineral processing facilities will contain all of the operations depicted in this figure, but all facilities will use at least some of these operations in the process of separating valued minerals 1124 Metallic Minerals Processing US EPA
.jpg)
A pilotprocess for calcium hydroxide production from iron slag
2022年6月1日 Although the grinding energy per kg of slag was low (0016 kWh/kg slag), the low efficiency of calcium extraction during leaching (below 10%) caused a large grinding specific energy consumption (21 – 24 kWh/kg Ca(OH) 2), underscoring the importance of improving the calcium extraction from slag to decrease the energy consumption and CO 2 footprint of the 2023年5月15日 Steel slag is the main solid waste generated in the steelmaking process, accounting for 15 to 20% of crude steel output [1]China's crude steel output in 2021 was 1035 billion tons [2], more than half of the global crude steel output (19505 billion tons) [3], and the steel slag output exceeded 120 million tonsIn contrast, the comprehensive utilization rate of Comprehensive utilization of steel slag: A review ScienceDirect2024年2月3日 Fine slag (FS) is an unavoidable byproduct of coal gasification FS, which is a simple heap of solid waste left in the open air, easily causes environmental pollution and has a low resource utilization rate, thereby restricting the development of energysaving coal gasification technologies The multiscale analysis of FS performed in this study indicates typical grain size Multiscale analysis of fine slag from pulverized coal gasification in 2024年11月21日 Using magnetic separation in sand washing plants can improve product quality, purity and production efficiency, while achieving resource recovery and environmental protectionThese advantages make magnetic separation a commonly used process in sand washing plants It effectively removes unwanted iron particles from the sand, improving the Highefficiency Magnetic Separation Process In Sand JXSC Machinery
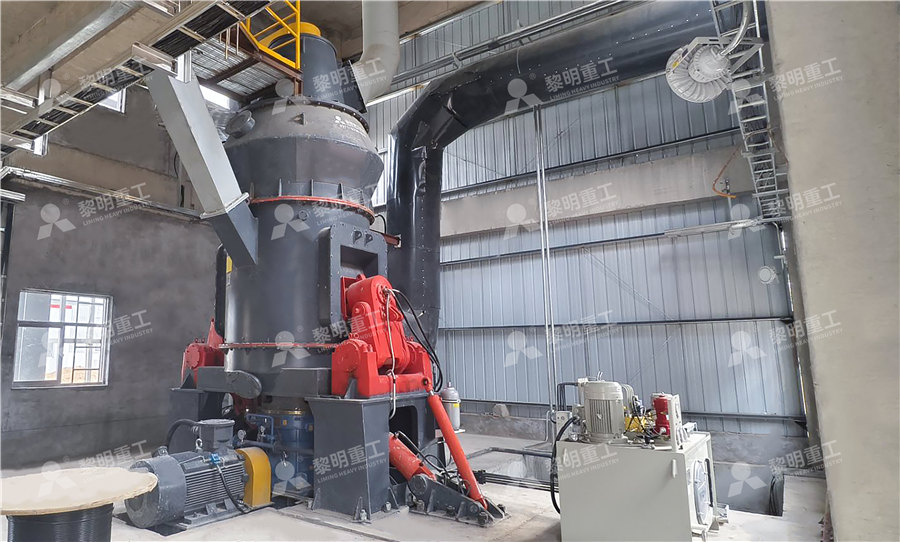
Dry beneficiation of iron ore Mineral Processing
On account of the low process costs, DSO ores with iron content of 58 % are produced For magnetite ores, beneficiation is typically more complex with finer ore grinding and downstream DMS (Dense Media Separation) and LIMS (LowIntensity Magnetic Separation) separation processes For DMS and LIMS, various technologies are usedVolume of water in feed L311 H : 9 7 9 7 7 7 L578m 7 Volume of water in underflow L04 H578 L231m 7 in underflow L 6 5 ; ; H 5 4 4 ; > 6 7 5 Solids concentration L 485% verflow L578 F231 L347m 7 overflow L = 7 7 > 7 8 ; Volume of water in o Solids concentration in H100 L2 % alance in mineral processing is discussed through some Lecture 11: Material balance in mineral processing 911 It is a carbon adsorption process of monovalent gold cyanide [KAu (CN)2] after the cyanide leaching of goldbearing materials CIP usually applies in flotation gold concentrate, high argillaceous oxidized gold deposit, mercury mixing, and gravity separation tailingsGold Cil/Cip Process Hongji Mine MachineryCopper processing is a complicated process that begins with mining of the ore (less than 1% copper) and ends with sheets of 9999% pure copper called cathodes, which will ultimately be made into products for everyday useThe most common types of ore, copper oxide and copper sulfide, undergo two different processes, hydrometallurgy and pyrometallurgy, respectively, Copper Mining and Processing: Processing Copper Ores
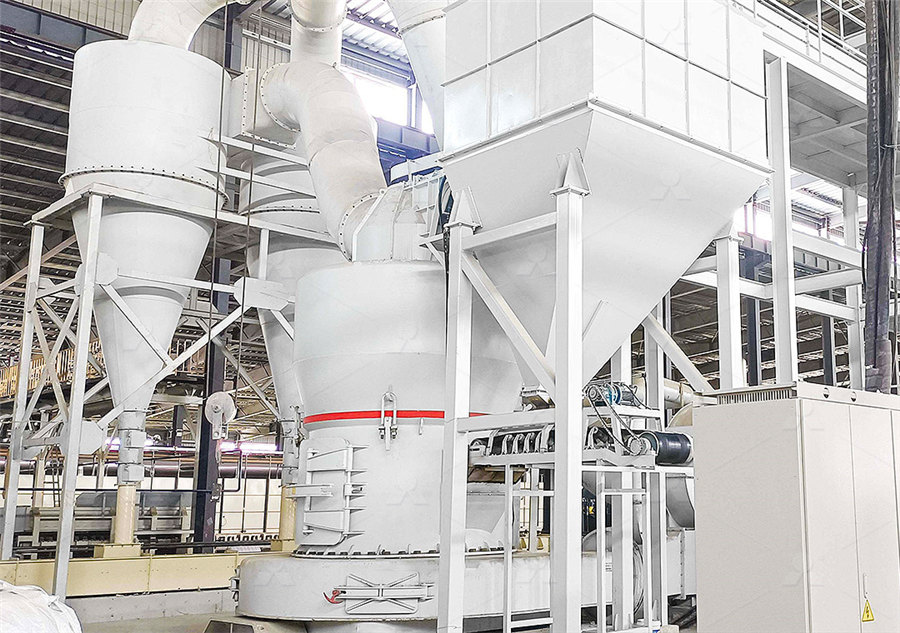
(PDF) Recovery of high grade iron compounds from LD slag by
2013年1月1日 From this investigation, two flowsheets of treatment of LD slag are suggested to recover high grade iron material for recycling in metallurgical processes Calcium and silicon oxide rich product