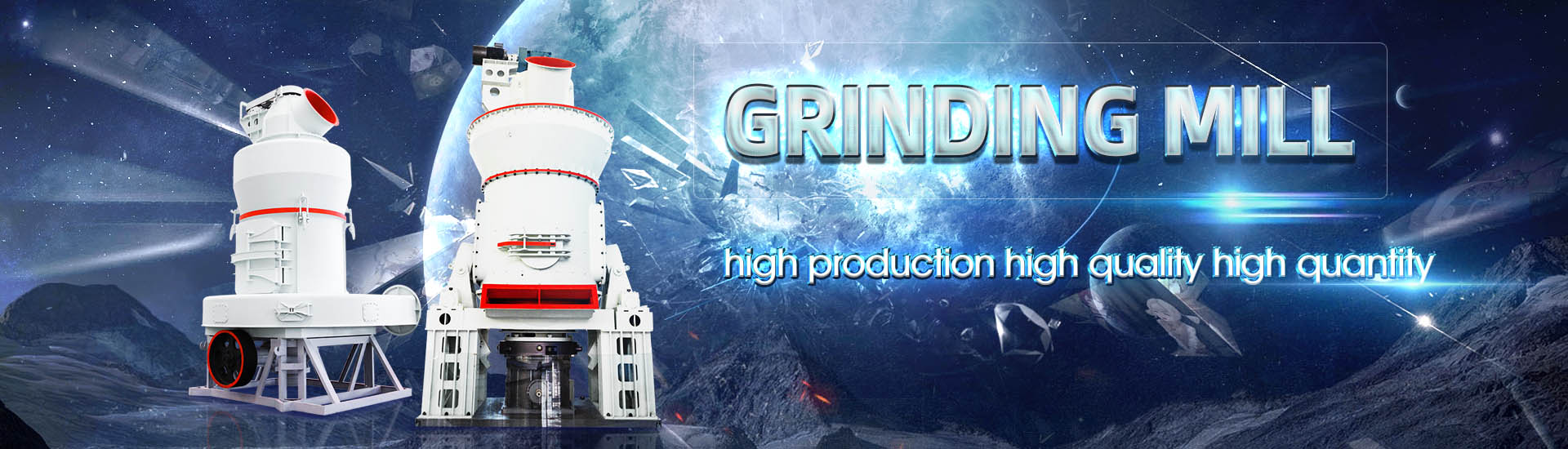
Graphite pouring channel for centrifugal casting
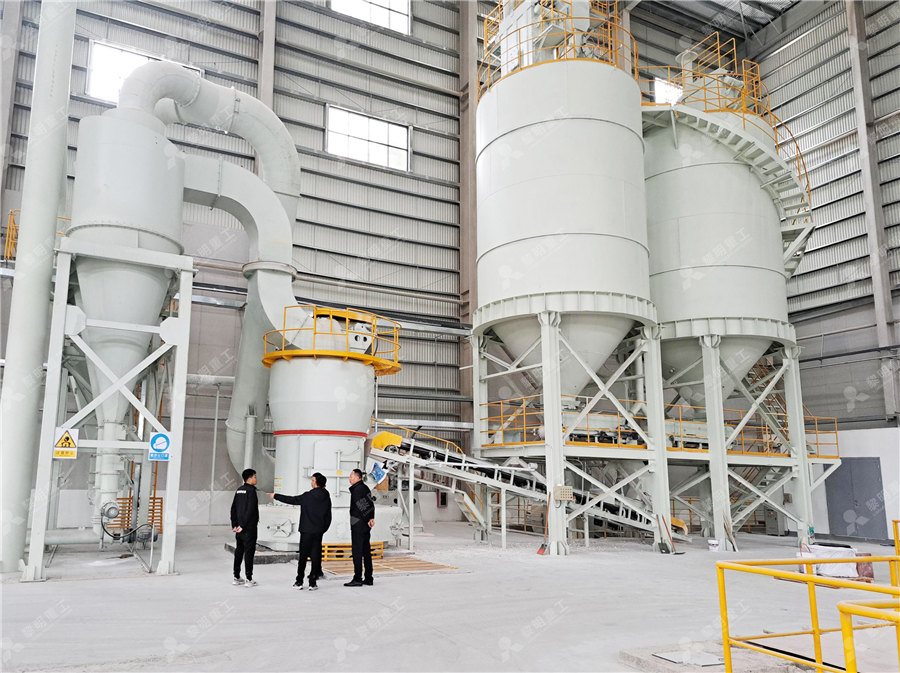
Effect of processing factors on the characteristics of centrifugal
2020年5月22日 High standards of soundness of the casting, resulting from feeding under the influence of centrifugal force, constitute the chief characteristic of centrifugal casting method Centrifugal Casting: Process Capability • Process: molten metal poured into rotating sand, metal or graphite mold • Advantages: wide range of cylindrical parts; good dimensional accuracy • Metal Casting 2 IIT Bombay2016年8月4日 Understanding how molten metals behave during centrifugal casting, and how their properties change due to different process parameters has been a crucial field of study Centrifugal casting technique baseline knowledge, applications, 132 PermanentMold Casting •Also known as gravity die casting •Mold can be made from a variety of different materials –Gray cast iron, alloy cast iron, steel, bronze, or graphite •Most MultipleUseMold Casting Processes New Jersey Institute of
.jpg)
Centrifugal Casting Monmet
Centrifugal castings are made by pouring molten metal into a rotating mold on a vertical or horizontal axis Molds can be made of cast iron or steel, copper, graphite, ceramic, or dry 2018年1月1日 In this alternative casting technology, two bridgelike channels were added between the pouring cup and the top of risers Part of melts in the pouring cup would be A shrinkage cavity model based on pressure distribution for Ti The method of pouring also influences the centrifugal casting characteristics Sarkar et al [39] reported, bottom pouring in vertical mould for centrifugal casting, accounts for a stable filling Effect of processing factors on the characteristics of centrifugal 2020年1月1日 The pouring rate, pouring temperature, mould temperature, and mould material can be suitably selected and altered in isolation or in combination, to generate a desired Effect of processing factors on the characteristics of centrifugal
-2.jpg)
Influence of pouring methods on filling process, microstructure
2018年6月25日 In this study, the Flow3D simulation software was applied to investigate the influence of pouring methods (with fixed or moving pouring channel) on AZ91 Mg alloy 2023年12月13日 Dr Dmitri Kopeliovich Centrifugal casting is a method of casting parts having axial symmetry The method involves pouring molten metal into a cylindrical mold spinning about its axis of symmetry The mold is kept Centrifugal casting [SubsTech]2022年9月4日 The effects of rotation speed and filling time on the filling and solidification process of the casting during centrifugal casting of super large cylinder liners are investigated by numerical simulation in this paper to enhance casting quality The results show that higher or slower rotation speeds, as compared to the ideal rotation speed, can have a negative impact Influence of Rotation Speed and Filling Time on Centrifugal Casting 2020年11月23日 Types of Centrifugal Casting There are two types of centrifugal casting processes – vertical and horizontal In addition, some manufacturers offer nearnet shaping which combines the benefits of What is Centrifugal Casting and How Does It Work?
.jpg)
Metal Casting 1 IIT Bombay
•Permanent mold casting –11% •Centrifugal casting –7% •Shell mold casting –6% ME 206: Manufacturing Processes Engineering Instructor: Ramesh Singh; Notes by: into the molten metal àporous castings Pouring Analysis (Sprue Design) 3 2 a t Ah Ah = ME 206: Manufacturing Processes EngineeringDue to this nature, a metal casting undergoing solidification will tend to decrease in volume During the manufacture of a part by casting this decrease in volume is termed shrinkage Shrinkage of the casting metal occurs in three stages: 1 Decreased volume of the liquid as it goes from the pouring temperature to the freezing temperatureThe Metal Casting OperationThe centrifugal casting can be used for metal matrix composite (MMC) melts For example if stir cast aluminium/graphite melt is poured in the rotating mould, graphite particles will segregate in the inner periphery of the centrifugal casting as graphite density is lower than aluminium Thus such casting can be employed for bearing applications5CENTRIFUGAL CASTING worldcollegesfo2024年11月12日 The quality and solidification structure of rotary products produced via horizontal centrifugal casting are contingent upon the thermal–fluid coupling dynamics of the molten metal This study leverages numerical simulation to model the evolution of filling, solidification, and macrostructure in horizontal centrifugal casting Utilizing the cellular Coupling Simulation and Mechanism Analysis of Grain Formation
.jpg)
Centripetal / Centrifugalcasting high white alloyHWA
2021年5月14日 Centrifugal casting is a NEW method of casting parts having axial symmetry The method involves pouring molten metal into a cylindrical mold spinning about its axis of symmetry The mold is kept 2022年7月28日 Centrifugal casting is a popular choice that ensures both quality and consistency Capabilities CNC Machining The second step is rotating the mold to prepare it for pouring Generally, the rate of rotation is between 300 to 3000 RPM The orientation allows the use of graphite, ceramic, or other similar materials for the Centrifugal Casting: Types, Processes, and Industrial Applications2016年3月7日 The evaluation of the casting quality in an experiment of large castings showed that actively cooled casting achieved improved mechanical characteristics Temperature difference method (TDM) In addition to the metallurgical analysis the experimental results are used to determine the heat transfer coefficient between the casting and the sand mold by the Analysis of controlled air cooling for castings by experiment 2022年12月1日 Centrifugal casting consists in rotating a ceramic or composite suspension inside a cylindrical mold around its axis [1], [2], [3]The generated centrifugal force field induces the separation of the components based primarily on a density difference, ie, the solids concentrate towards the mold wall, and the lower density phase remains close to the center of Understanding centrifugal casting in the manufacture of
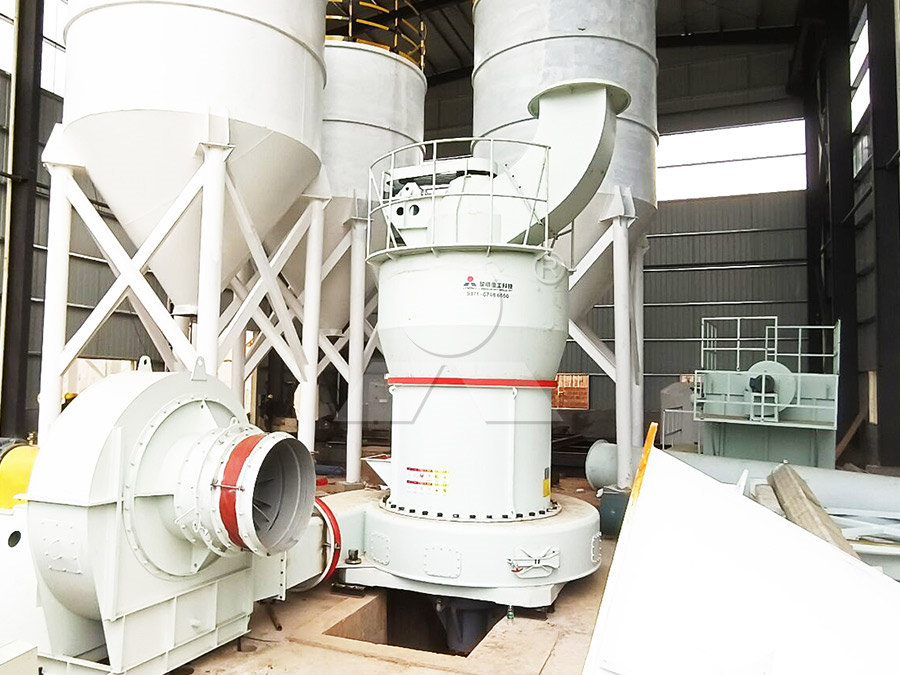
Effect of processing factors on the characteristics of
2020年1月1日 Centrifugal castings are produced by pouring liquid metal into rotating moulds It solidifies under the influence of centrifugal forces, directed from the center to the periphery of the mould on 2011年2月26日 For permanent mold casting micro structured steel molds and graphite molds were used Composite casting was investigated for surrounding a micro part by melt, and for pouring a metal melt into a micro The majority of the experiments were performed with the centrifugal casting machine “Vacutherm 33 Titan” by Linn New approaches in microcasting: permanent mold casting and 2016年5月26日 During the centrifugal continuous casting process, unreasonable casting parameters can cause violent level fluctuation, serious gas entrainment, and formation of frozen shell pieces at the meniscus Thus, in the current study, a threedimensional multiphase turbulent model was established to study the transport phenomena during centrifugal continuous casting Modeling on Fluid Flow and Inclusion Motion in Centrifugal alloy made by centrifugal casting They used two kinds of pouring positions including a fixed pouring channel and a moving one Their results indicated that the properties of samples prepared using the moving pouring channel were better than those of the cast workpiece made by the fixed pouring channel They also reported that the average tenEffects of Mold Rotation Speed and Cast Thickness on the
.jpg)
Centrifugal Casting: Definition, Parts, Working Process, Types
2022年3月26日 When it comes to the casting process, centrifugal casting is a very good and efficient type of casting process In this article, we will study the Definition, Parts, Working Process, Step Involved, Types, Materials, Applications, Advantages, and Disadvantages of Centrifugal Casing in detail Notes: The whole article PDF you can download at the end of the Methods for making various nickel based superalloys into engineering components such as rings, tubes and pipes (70) by melting of the alloys (60) in a vacuum chamber (50) or under a low partial pressure of innert gas and subsequent centrifugal casting of the melt in the graphite molds (80) rotating along its own axis under vacuum or low partial pressure of inert gas are providedCentrifugal casting of nickel base superalloys in isotropic graphite Advantages of Continuous Casting for Bronze Bushings Continuous casting offers several advantages for the production of bronze bushings: High Efficiency: Continuous casting streamlines the production process, reducing labor and energy costs while maximizing output Uniformity: Bronze bushings manufactured through continuous casting exhibit consistent Casting Process Continuous Casting Vs Centrifugal CastingOn this page you'll find ceramic and graphite crucibles for your convenience Our ceramic crucibles are perfect for centrifugal casting machines and are made of fused silica with a clay bond The graphite crucibles are made for electric melting furnaces We have many different products to help you in your metal melting and all of your casting Casting Crucibles Crucibles on Jewelry Tools
.jpg)
Casting Defects and its Optimization Method in Centrifugal Casting
2017年1月19日 Centrifugal casting parameters, including alloy and mold temperature, melt pouring rate, rotational speed, and mold wall thickness, can be varied to reduce defects and improve mechanical 2024年6月5日 Die castings of brass and bronze present a problem in pressure casting because of their high casting temperatures These temperatures range from 870 to 1040 °C and make it necessary to use heatresisting alloy steel for the dies to reduce their rapid deteriorationIntroduction to Casting SpringerLinkThe centrifugal casting can be used for metal matrix composite (MMC) melts For example if stir cast aluminium/graphite melt is poured in the rotating mould, graphite particles will segregate in the inner periphery of the centrifugal casting as graphite density is lower than aluminium Thus such casting can be employed for bearing applications5CENTRIFUGAL CASTING University of Babylon2023年10月4日 Effect of centrifugal speed on the maximum porosity To study the effect of different pouring temperatures on the hot tearing of castings, different pouring temperatures (700 ℃, 730 ℃, 760 (PDF) Microstructure and hot tearing sensitivity
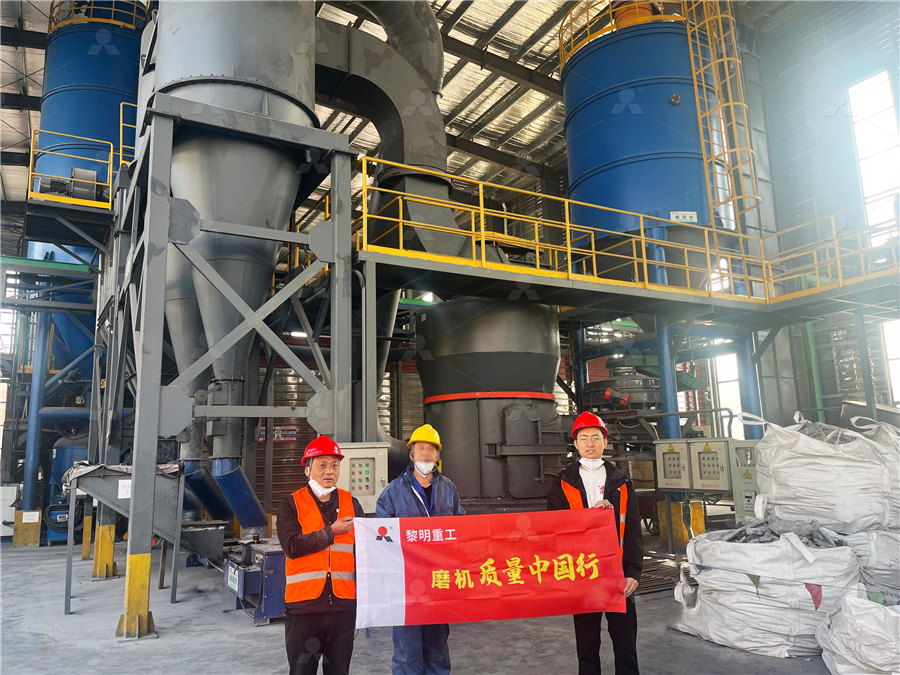
DESIGN AND DEVELOPMENT OF A CENTRIFUGAL CASTING
areas, using centrifugal casting For this purpose a special design of a vertical axis centrifugal casting machine was developed A detailed study of the centrifugal pouring process and the inherent fluid dynamics was performed to develop a conceptual design and operation parameters and input/output system variables were establishedSome manufacturers produce centrifugal components, with some shaping the OD, die rotating about the vertical axis This vertical casting that OD Shaping by pouring graphite, sand, or ceramic molds into the die – resulting in significantly less postprocessing like All About Centrifugal Casting What Is Centrifugal Castingmicrostructure analysis of Spheroidal Graphite Iron (SGI) castings to determine the quality assessment parameters of SGI casting such as nodularity, nodule count, nodule size and percent of ferritepearlite The strength and hardness of the SGI castings is dependent on these quality parameters Key words: Spheroidal Graphite, Iron Casting IA Review on Analysis and Optimization of Parameters for 2018年3月12日 Some small metal castings, like jewelry, are made using a centrifuge that swings an entire mold around a central point, pulling metal from a crucible as it whirls These castings are not true centrifugal castings, but a form of pressure casting Centrifugal castings have no seams and impurities can be machined from the bore Pressure castingMetal Casting Methods: Life of a Casting Reliance Foundry
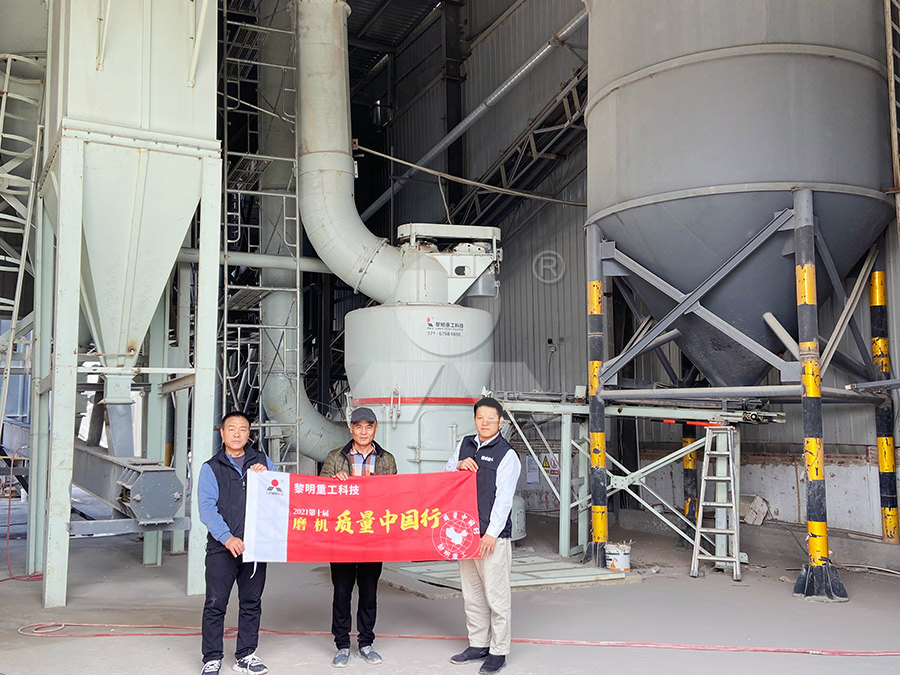
Metal Casting Supplies PMCSupplies PMC Supplies
Here at PMC Supplies, we specialize in offering tools for both melting down precious and nonprecious metals and pouring them into a mold We carry graphite, steel, and cast iron molds to mention a few Spin casting or centrifugal casting is a method in which a rubber mold is produced by using centrifugal forceIn order to improve casting quality, it becomes critical to accurately predict the casting molding and solidification processes The numerical simulation of solidification processes has become an important method in casting production [25]Jun et al [26] established a numerical model to study the influence of different process parameters on centrifugal casting flow pattern, and further Microstructure and Hot Tearing Sensitivity Simulation and centrifugal casting filling process Pouring position as the input heat source has great influence on the temperature field evolution [8] solidification time of casting pipe by moving pouring channel was 266 s However, it was beyond 30 s for the pipe by the (a) 305 rmin1 (b) 390 rmin1 (c) 495 rmin1 199Influence of pouring methods on filling process, microstructure 2017年5月9日 3 • Centrifugal casting, sometimes called rotocasting, is a metal casting process that uses centrifugal force to form cylindrical parts • This differs from most metal casting processes, which use gravity or pressure to fill the Centrifugal casting 1 PPT SlideShare
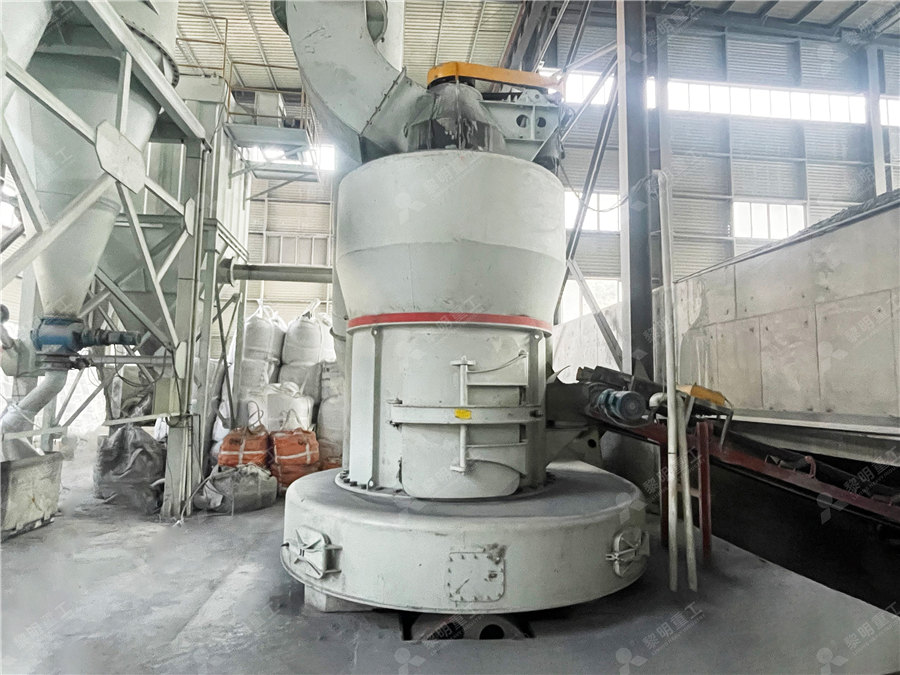
CENTRIFUGAL CASTING worldcollegesfo
The centrifugal casting can be used for metal matrix composite (MMC) melts For example if stir cast aluminium/graphite melt is poured in the rotating mould, graphite particles will segregate in the inner periphery of the centrifugal casting as graphite density is lower than aluminium Thus such casting can be employed for bearing applications5These processes are true centrifugal casting, semicentrifugal casting, and centrifuge mold casting The article discusses the cooling, inoculation, fluxing, and extraction of castings It reviews mold heating and coating techniques as well as the various molds used The three most common defects observed in centrifugal castings are also discussedCentrifugal Casting Casting Handbooks ASM Digital LibraryMetal Casting History (India) 3000 BC Earliest castings include the 11 cm high bronze dancing girl found at Mohenjodaro 2000 BC Iron pillars, arrows, hooks, nails, bowls and daggers or earlier have been found in Delhi, Roopar, Nashik and other places 500 BC Large scale stateowned mints and jewelry units, and processes of metal extraction and Metal Casting2024年11月12日 Centrifugal Casting Controls Impurities Unique to the centrifugal process is the high force that effectively isolates less dense substances in the casting’s bore area These impurities are later machined away, leaving a defect free part Molten metal is fed into a rotating mold where a centrifugal force of up to 100Gs is applied to the metalCentrifugal Casting Process: Advantages and Limitations
.jpg)
Numerical Simulation on Solidification during Vertical Centrifugal
2023年12月29日 The Ti6Al4V (TC4) alloy wheel hub has exhibited some defects that affect the properties during the vertical centrifugal casting process Therefore, the analysis of the solidification process would contribute to solving the abovementioned problems In this study, an orthogonal experimental design was employed to optimize the process parameters (rotational A final feature of true centrifugal casting is direct pouring into the mould, without the need for gates and runners This results in very high yields that can reach up to 100% Both vertical and horizontal techniques can be used to cast a range of nonferrous and ferrous materialsCentrifugal casting: Process and applications vesuvius free mold which was patented in 1935 Vacuum casting, combined with centrifugal casting was also attempted in 1935, and patents on this method were finally issued in 1940‐42 However, successful vacuum‐centrifugal casting was not ac‐complished until 1948 by AL EnglehardtCentrifugal Casting MarmaraCentrifugal casting types: (a) horizontal axis and (b) vertical axis [8 ,9] 1565 Due to the referred advantages of this process, a possible solution for the pistons production pouring channels of square section In the superior halfdie a pouring basin made of thermoDESIGN AND DEVELOPMENT OF A CENTRIFUGAL CASTING
.jpg)
Graphite Permanent Mold Casting ALBCO Foundry
The graphite permanent mold casting process begins with pneumatically clamping two graphite blocks in a press Molten metal is poured into a sprue or pouring basin at the top of the mold Once the metal has solidified, the graphite molds are separated and the castings are removed