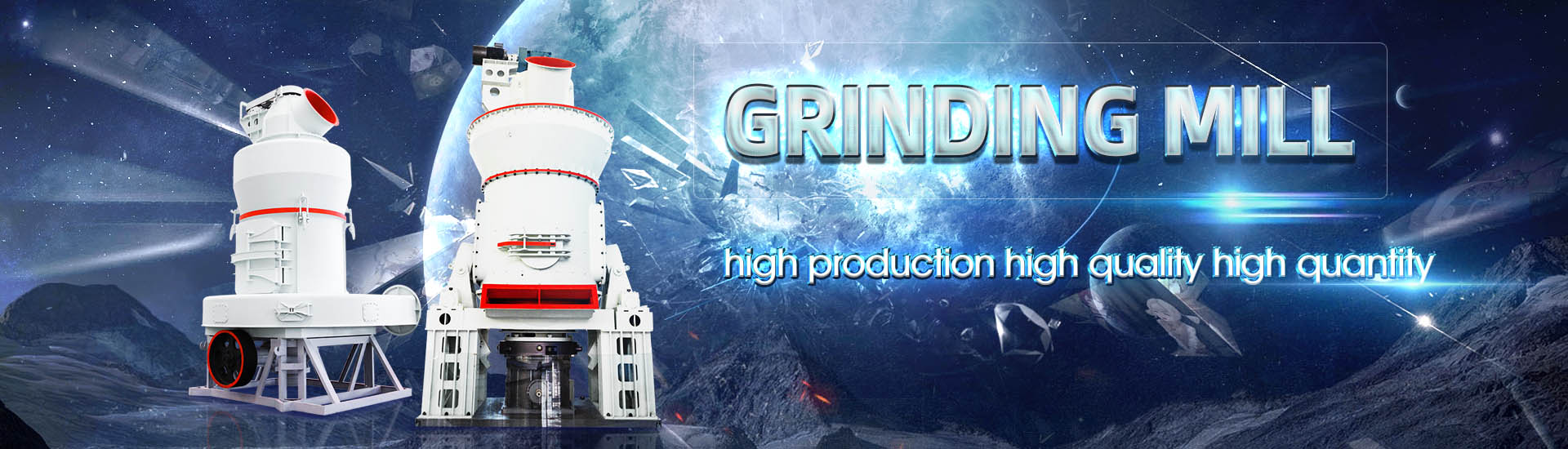
Coal coking plant process flow

Lecture 32: Coke production National Institute of Technology,
At first Bituminous coal is crushed and screened to a certain size Preheating of coal (at 150250 ̊C) is done to reduce coking time without loss of coal quality Briquetting increases strength of coke produced and to make non coking or poorly coking coals to be used as metallurgical cokeDestructive distillation ("coking") of coal occurs in coke ovens without contact with air Most U S coke plants use the KopperBecker byproduct oven These ovens must remain airtight under 122 Coke Production coke making plant consists of coal preparation, coke oven batteries and by product plant Coke making process flowsheet is given in Figure 2 Coke oven batteries are built withCoke making process flowsheet Download Scientific Diagram2017年11月15日 Taking the exergy loss minimization as the optimization objective, an optimization model of coking process is established based on the material balance and energy Exergy analysis and optimization of coking process
.jpg)
Industrial perspective of the cokemaking technologies
2019年1月1日 Process flow of composite coking potential (CCP) model based coal blend design criteria CSR, coke strength after reaction The reserves of good coking coals are becoming 2022年8月5日 Delayed coking units for processing vacuum residues are designed to operate under operating conditions that maximise liquid distillates yield and minimise coke production(PDF) Coking ResearchGate2019年1月1日 This chapter explains the technological principles behind semisoft coking coal utilization from the viewpoint of the mechanism of carbonization and reviews the development The development of cokemaking technology based on the 2024年1月14日 A mathematical model of the coking process in the coking chamber was constructed based on the distributed activation energy model The heat transfer process of the Heat and mass transfer analysis of coal coking process in the
.jpg)
Coke Making: Most Efficient Technologies for Greenhouse
2019年7月19日 The goals of coking process control are realizing steady heating of coke oven, enhancing production of coke oven and quality of coke, reducing energy consumption and Coal processing or coal beneficiation uses physical (mechanical) and/or chemical methods to remove rocks, dirt, ash, sulphur and other contaminants and unwanted materials to produce highquality coal for energy in both local and Coal Processing Multotec2022年8月5日 A schematic flow diagram of the delayed coking is shown in Figure 1 delayed coking process, different types of the coke can be produced Coalbased needle coke is made from Coal Tar Pitch (PDF) Coking ResearchGateA modern coking plant: the Carbonaria plant in Duisburg–Schwelgern, operated by ThyssenKrupp since 2003 ArcelorMittal's Prosper coking plant in Bottrop with its chimney and lowpressure gasometer (Thyssen construction) A coking factory or a coking plant is where coke and manufactured gas are synthesized from coal using a dry distillation processCoking factory Wikipedia
.jpg)
Direct Reduced Iron and its Production Processes – IspatGuru
2013年3月16日 Feed material for the DR process is either sized iron ore of size ranging from 10 mm to 30 mm or iron ore pellets of size ranging from 8 mm to 20 mm produced in an iron ore pellet plant The gas based process uses a shaft furnace for the reduction reaction The coal based process uses any one of the four types of reactors for the reduction The various stages of the steel plant is described below COKE MAKING COAL CARBONISATION : Coking coals are the coals which when heated in the absence of air, the reduction process is completed as hot metal flows through layers of cokeCoke OvensSinterBFBOF Route SAILA coke oven at a smokeless fuel plant, Abercwmboi, South Wales, 1976 The industrial production of coke from coal is called coking The coal is baked in an airless kiln, a "coke furnace" or "coking oven", at temperatures as high as 2,000 °C (3,600 °F) but usually around 1,000–1,100 °C (1,800–2,000 °F) [2] This process vaporises or decomposes organic substances in the coal, Coke (fuel) Wikipedia2021年12月8日 Coke chemical companies often have a deficit of coals of particularly valuable grades, the coking coals This work studies the opportunity of producing petroleum coking additives using delayed coking during heavy petroleum residue processing Experiments for the production of a carbon material were conducted using three kinds of heavy petroleum residues Technology of Producing Petroleum Coking Additives to Replace Coking Coal
.jpg)
Raw materials Coking plant ArcelorMittal
To make steel in a blast furnace, coal must first be turned into coke Coke has a dual role in the steelmaking process First, it provides the heat needed to melt the ore, and second, when it is burnt, it has the effect of ‘stealing’ the oxygen from the iron ore, leaving only the pure iron behind In the coking plant, coal is heated in the absence of oxygen to 1250c2017年11月9日 The flowsheets to be simulated consist primarily of coal washing units each with a target specific gravity of separation specified for each washing unit The feed is allocated to each washing unit on the basis of separation by size in the screening operations This is a fairly common arrangement for modern coal washing plant flowsheetsCoal Washing Plant 911MetallurgistCoke Plant Technologies Pioneering coke plant technologies are part of our daily business The effi ciency and environmental performance of our plants are renowned worldwide Tailor made complete coke oven plants from a single source – that’s our commitment and your advantage gained from a partnership with us 500 coking plants worldwideCoke Plant Technologies ThyssenKrupp2019年11月14日 Coking is a complex process It features a large time constant, strong nonlinearities, and timevarying characteristics To achieve good control performance, it is important to obtain a precise COT in a realtime fashion; but this is difficult owing to restrictions imposed by the structure of a cokeoven and operating costsIntelligent Optimization and Control of Coking Process
CFB石灰石脱硫剂制备64.jpg)
Coking Plant an overview ScienceDirect Topics
Coke production from low rank coals Herbert Richter, André Werner, in LowRank Coals for Power Generation, Fuel and Chemical Production, 2017 1143 Development of the BHTcoking facility in Schwarze Pumpe For the lignite, refinements combine Schwarze Pumpe (later known as gas combine Schwarze Pumpe) and three hightemperature coking plants were planned Download scientific diagram Coke making process flowsheet from publication: 19th International Metallurgy and Materials Congress One of the most important factors affecting the coke batteries Coke making process flowsheet Download Scientific DiagramThe blended coal mass is heated for 12 to 20 hours for metallurgical coke Thermal energy from the walls of the coke chamber heats the coal mass by conduction from the sides to the middle of the coke chamber During the coking process, the charge is in direct contact with the heated wall surfaces and develops into an aggregate "plastic zone"122 Coke Production2021年5月11日 Based on utility, coals are classified into coking type and noncoking type Further, coking coals are subdivided into four groups: prime coking coal, medium coking coal, semicoking coal, and weakly coking coal Prime coking coals when subjected to the carbonization process at high temperature produce coke of metallurgical standardsMineral Beneficiation and Processing of Coal SpringerLink
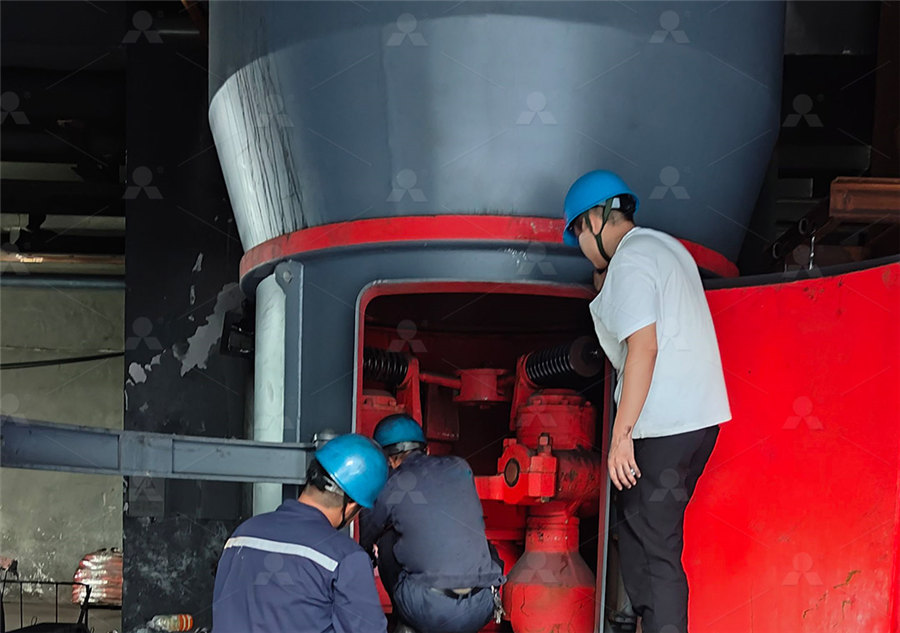
Coal beneficiation: theory and practice ScienceDirect
2023年1月1日 Hard coking coal (HCC) represents the premium band of coking coals used solely for steel production through the blast furnace process These coals range from high volatile through low volatile bituminous in rank and can soften and resolidify into a coherent, porous mass when heated from 300°C to 550°C in the absence of air in a confined space2024年8月20日 Below is an overview of what happens to the coal during the coking process 1 Metallurgical Coal Sourced and Prepared Metallurgical coal — as opposed to thermal coal, a type of coal which is used for generating electricity — contains high concentrations of carbon, which is critical to the coking processWhat Is Coking? What Happens to the Coal? CadenceNoncoking coal is used in coalbased DRI plants (SI plants) as well as in thermal power plants As per 2011 findings, the total coking coal reserves in India are 33474 billion tons, out of which 1767 billion tons is of “proved” category and total noncoking coal resources of 25239 billion tons, out of which 9633 billion tons is of “proved” category [ 11 ]Coking Coal an overview ScienceDirect Topicscoking derivatives 2 THE COAL COKING PROCESS Bituminous coals with a carbon content of around 7590 wt% (all the percentages referring to coal and coke in this review are expressed on a dry and mineral matterfree basis, dmmf) are primarily used in the coking process for the production of metallurgical coke15 When coal isChemicals from Coal Coking
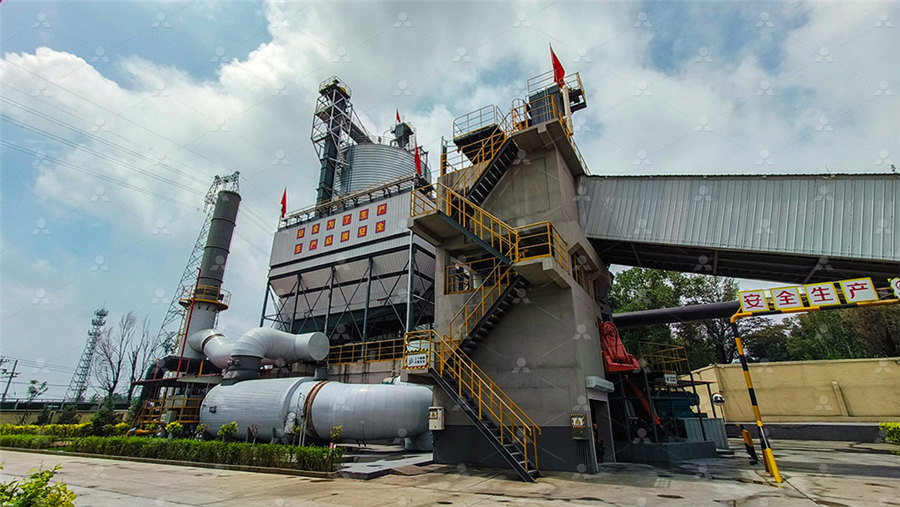
Understanding Coke Making in Byproduct Coke
2015年3月9日 Fig 1 Typical flow diagram of a byproduct coke oven plant Environmental issues The coke oven is a major source of fugitive air emissionsThe coking process emits particulate matter (PM), volatile organic 2023年1月5日 Metallurgical coal (also called "met" coal) is an important raw material used in the steelmaking process, although very small amounts of coal (relative to the amount used for electricity) are needed The coal used to make Coal to Make Coke and Steel University of KentuckyA coking plant is used to produce coke (coking coal) from metallurgical coal Coking plants consist of coke ovens (aka coking ovens, coke furnaces, coking furnaces) Coal is used to reduced iron ore to produce pig iron (aka hot metal) in the blast furnace (BF)However, it cannot be burned directly in the furnace because it contains numerous harmful byproducts that gets generatedCoking plant Global Energy MonitorCoking is the process of heating coal in the absence of oxygen to a temperature above 600 °C (1,112 °F) to drive off the volatile components of the raw coal, leaving behind a hard, strong, porous material with a high carbon content called cokeCoke is predominantly carbon Its porous structure provides a high surface area, allowing it to burn more rapidly, much like how a Coking Wikipedia
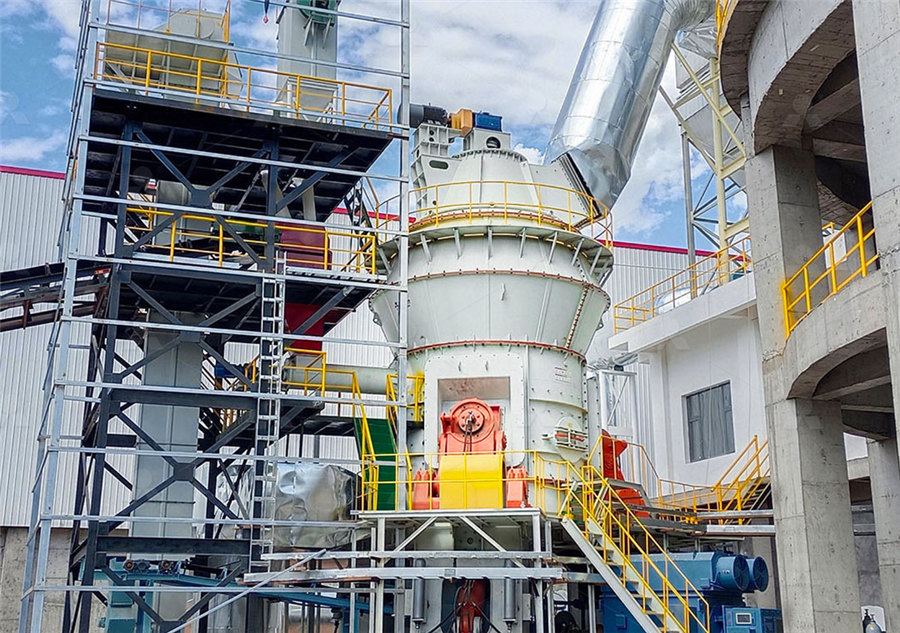
Optimizing the coke oven process by adjusting the temperature
2021年2月15日 The coking process consists of carbonization of coal in ovens with vertical heating walls During this process, coals soften to become plastic, decompose, swell, agglomerate, and finally resolidify In the coking process, two vertical plastic layers are formed parallel to the heating walls, which proceed towards the center where they coalesce 2017年2月14日 Coal based DRI plants are flexible with respect to plant location since noncoking coal is widely distributed in large deposits and is easy to transport Most plants employ reduction process which is carried out in rotary kilns These plants use wide variety of raw materials and noncoking coalCoal based Direct Reduction Rotary Kiln Process – IspatGuruCooking coal and noncoking coal are two types of coal with different properties and uses Let’s explore each of them: a High carbon content: Cooking coal has a high carbon content, typically ranging from 60% to 90% This high carbon content is Understanding the Differences: Cooking Coal vs NonCoking CoalCoal stockpile Coal stacker Coal reclaimer Coal needs to be stored at various stages of the preparation process, and conveyed around the CPP facilities Coal handling is part of the larger field of bulk material handling, and is a complex and vital part of the CPP Stockpiles provide surge capacity to various parts of the CPP ROM coal is delivered with large variations in Coal preparation plant Wikipedia
.jpg)
ENVIRONMENTAL Central Coalfields
other nearby mines for supplying beneficiated Medium Coking Coal to steel plant for production of metallurgical coke The process flow sheet of Washeryhas been appended as AnnexureI 14 The production of clean coal, middlings and generation of rejects from the Washery for the lastThe blended coal mass is heated for 12 to 20 hours for metallurgical coke Thermal energy from the walls of the coke chamber heats the coal mass by conduction from the sides to the middle of the coke chamber During the coking process, the charge is in direct contact with the heated wall surfaces and develops into an aggregate "plastic zone"122 Coke Production2019年12月31日 This chapter describes the process of coalification, which gradually turns plant debris into coal, involving heat, pressure and the effects of timeThe Origin and Classification of Coal ResearchGatePlant oils and biodiesel 6 Composition and reactions of wood 7 Reactive intermediates 8 All coals, regardless of whether they are caking or coking coals, leave a solid carbonaceous residue at the end of the carbonization 23 Carbonization and coking of coal Cambridge
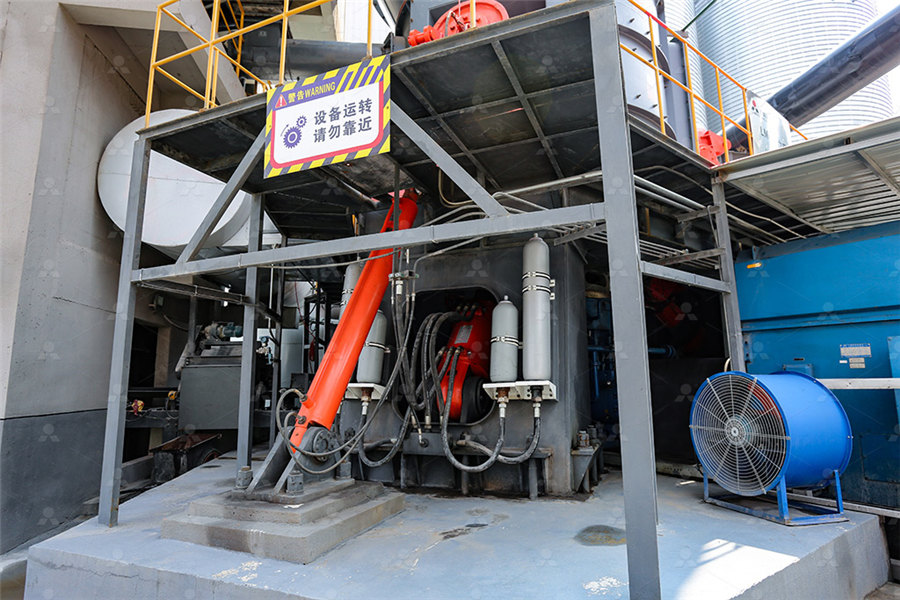
Prospects for Coalbased Direct Reduction Process KOBELCO
plants using natural gas (eg, the MIDREX process and HYL process) have the characteristics of requiring a smaller capital expenditure and no coking coal Many direct reduction plants have been built in developing contries, particularly those that produce natural gas In 2018年12月26日 Coal Tar and its Distillation Processes satyendra; December 26, 2018; 5 Comments ; Anthracene, Cresol, Crude tar, Dehydration, HBTA, Hydrocarbons, Phenol, tar, tar distillation,; Coal Tar and its Distillation Processes Coal tar, also known as crude tar, is the byproduct generated during the high temperature carbonizing of coking coal for the production of Coal Tar and its Distillation Processes IspatGuruDownloadable (with restrictions)! Taking the exergy loss minimization as the optimization objective, an optimization model of coking process is established based on the material balance and energy balance The optimization problem is solved with the practical production data of a coking plant The minimum exergy loss and the optimal design parameters are obtainedExergy analysis and optimization of coking processsecond to coking coals in quality and degrade the charge, which finally affects the coke quality15,16 In general, 28 The plant capacity and process lines are organized so that the potential crude material for the petroleum coking additive industrial production can be three kinds of heavy petroleum residuesTechnology of Producing Petroleum Coking Additives to Replace Coking Coal
.jpg)
Exergy analysis and optimization of coking process
2017年11月15日 Taking a typical coking plant as an example, the optimization model is solved and analyzed with the practical production data The dosages of 1/3 coking coal (m coal,1), gas coal (m coal,2), fat coal (m coal,3), lean coal (m coal,4) and coking coal (m coal,5) in five coal storage rooms are optimizedits Angul plant is operating gas based DRI plant by domestic coal Talcher Fertilizer Limited (TFL) is also going ahead with mixing of pet coke in high ash domestic noncoking coal for urea production In order to achieve 100 MT coal gasification projects in India by 2030, Ministry of Coal has taken several steps All coal companies have been National Coal Gasification MissionRaw Coal Transportation: Belt conveyors are used to transport raw coal from storage areas or coal yards to the coal preparation plant Coal Crushing and Sizing: Belt conveyors move the coal to crushing and sizing units where it is processed before being fed into the coking process Coke Oven Charging Conveyor to Charging Bunkers:Coal Handling Conveyor In Coking Plant SKE Industries2016年8月7日 Coal plays a dual role in the Kiln Part of coal is used as fuel to supply the desired heat so as to take the raw materials to the desired temp But main role of coal is to supply carbon in the reduction process Dolomite is used as sulphur scavenger which finally comes out with the char Char contains ash of coal and other impurities of iron oreProcess Description and flow diagram of Coal Based DRI Plant