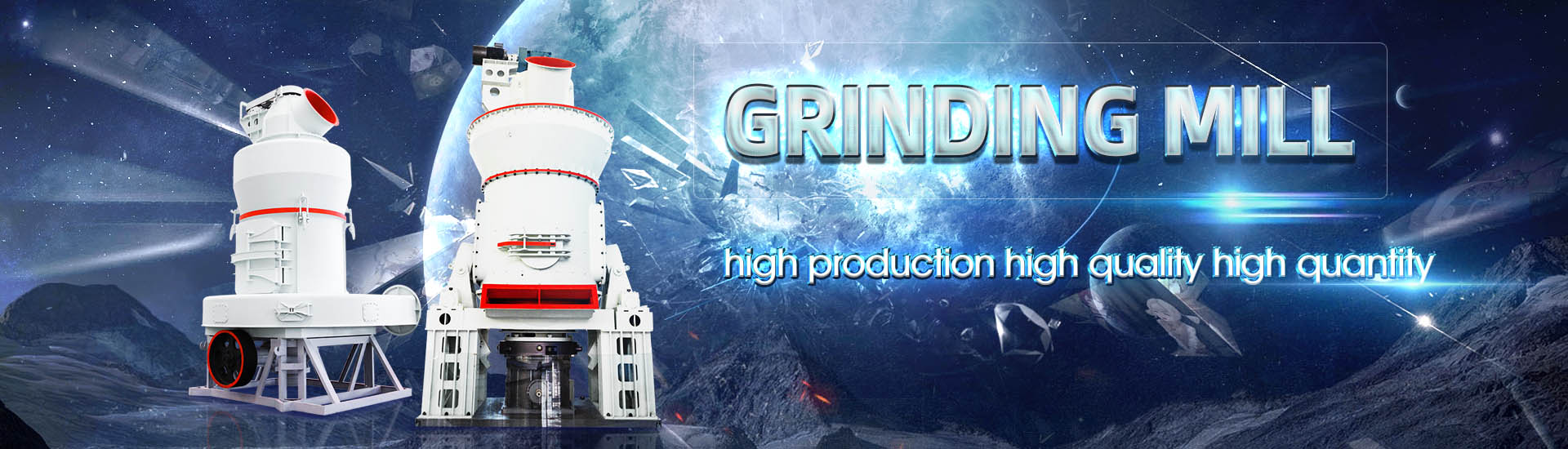
How much is a laterite nickel processing equipment

Processing of Nickel Laterite Ores on the Rise FEECO
Sulfides have long supplied the bulk of the global appetite for nickel But dwindling resources combined with the need to mine at greater (and subsequently less economic) depths to 展开2024年8月7日 Laterites make up over 70 % of both nickel production and known terrestrial resources today and have been the fastest growing source of nickel for some time The Nickel industry Part 2 Processing nickel laterites and smelting2019年8月26日 It is estimated that there are about 140 million tons of nickel available in identified deposits Eightyfour million tons, or 60 percent of the total available nickel is in laterite deposits A deposit in which rain and surface Nickel Processing Equipment, Process Flow, Cases2015年5月1日 This is the third paper in a series examining the economics of processing a hypothetical nickelcobalt laterite using commercially applied processes and two processes that are still underTechnical Cost Comparison of Laterite Treatment
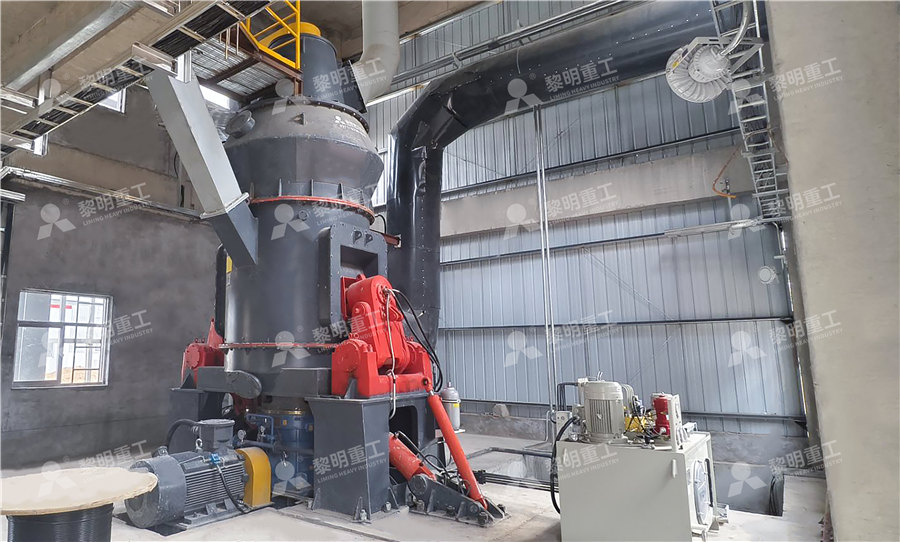
Nickel industry Part 1 Processing nickel laterites and
2024年5月3日 Ore is often processed near the mine site, but there is substantial regional and global trade in nickel laterite ores, and some trade in nickel sulfide concentrates Laterite ores occur as surface deposits and are traditionally Depending on your mineralogical requirements, nickel laterite highpressure acid leaching (HPAL) solutions are available, using Metso Outotec OKTOP autoclaves and other pressure Hydrometallurgical nickel and cobalt plants and processes2014年4月10日 Nickel matte remains after the mining and processing of either lateritic or sulfidic ore Using the fluid bed roasting procedure, a 95 percent pure nickel can be achieved after additional refinement Electric cells provide for a Nickel Mining and Processing General Kinematics2022年8月22日 Laterite ore contributes to about 70% of the world’s landbased nickel resources Hydrometallurgical techniques such as heap leaching (HL), atmospheric leaching (AL), high Recent Progress in Hydrometallurgical Processing of Nickel
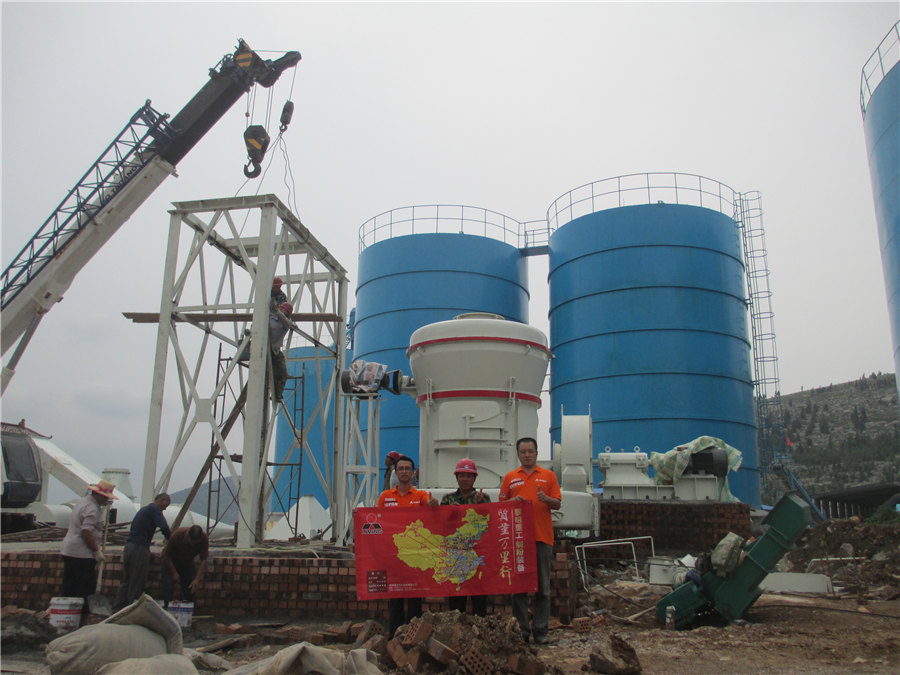
New processing method to deliver huge benefits to
2013年3月13日 Fullscale testing of the process has commenced at a A$35 million pilot plant at CSIRO in Perth The process, developed by Sydneybased company Direct Nickel, could deliver a huge boost to the global nickel industry 2002年8月1日 A greenfield laterite processing operation to produce nickel cathodes via electrowinning, and recover electrowon copper and cobalt sulphide as byproducts was Nickel laterite processing and electrowinning practicenickel processing, preparation of the metal for use in various products Although it is best known for its use in coinage, nickel (Ni) has become much more important for its many industrial applications, which owe their importance to a Nickel processing Extraction Refining Techniques2000年10月1日 In hydrometallurgical nickel laterite, ore is extracted by using High Pressure Acid Leaching (HPAL), Atmospheric Leaching (AL), and SulfationRoastingLeaching (SRL) methods [2,3]Pressure Acid Leaching of Nickel Laterites: A Review
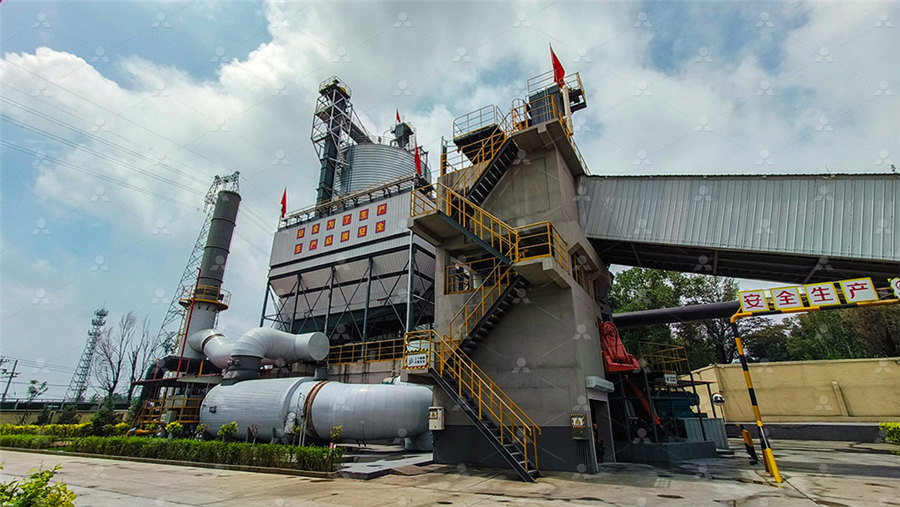
Nickel Laterite Metallurgy SpringerLink
2023年5月28日 HPAL process for short is suitable for processing nickel laterite of limonite type with less than 5% content of magnesium in general to avoid excessive acid consumption Generally, for this type of nickel laterite ore, the contents of nickel and cobalt are 08–15% and 01–02% respectivelyEQUIPMENT FEECO offers a variety of custom equipment and process solutions for the processing of nickel From agglomeration drums for use in the heap leaching process to nickel pelletizing systems, we can develop a process solution that fits your needs, as well as engineer and manufacture the equipment needed to carry out the jobNickel Processing Equipment FEECO International Inc2022年5月31日 The processing methods of laterite nickel ore is mainly divided into two types: pyrometallurgy process and hydrometallurgy process According to the difference of nickel, cobalt content and ore type, and different working conditions, there are 7 kinds of methods to choose from This article will introduce you to these 7 laterite nickel ore processesHow to Extract Laterite Nickel Ore? 7 Processing Methods2024年11月1日 Due to the stringent equipment and scale requirements of HPAL, In an effort to achieve zerowaste metal processing of laterite nickel ore, Zulhan et al(Zulhan and Agustina, 2021) utilized oxides from nickeliron slag as raw materials for the production of Review on comprehensive utilization of nickel laterite ore
46.jpg)
Recent Progress in Hydrometallurgical Processing of Nickel
2022年8月22日 The effects of ore grade on embodied energy and GHG emissions were estimated by Norgate etal for the various nickel laterite processing routes The Leaching of a Turkish lateritic nickel ore in nitric acid solution In Mine Planning and Equipment Selection, Springer, Cham (2014) 10391045Typical nickel laterite ore deposits are very large tonnage, lowgrade deposits located close to the surface They are typically in the range of 20 million tonnes and upwards (this being a contained resource of 200,000 tonnes of nickel at 1%) with some Lateritic nickel ore deposits WikipediaMost lateritic nickel resources occur within a band about 22 degrees of latitude either side of the equator (Fig 1) and the giant, and in some cases highest grade, deposits are concentrated inNickel laterite deposits – geological overview, resources and 2024年1月19日 It finds extensive use in industries such as construction, automotive, aerospace, food processing, and medical equipment 3 Alloys and Superalloys (HPAL): HPAL is a widely used method for extracting nickel from laterite ores, Nickel processing is a complex and multistage procedure that involves various techniques to The Comprehensive Guide to Nickel Processing Miningpedia
.jpg)
Nickel Smelting and Refining International Finance Corporation
ing equipment and are screened to remove boulders Sulfidic ores, often found in conjunction with copperbearing ores, are mined from to the furnace to produce a matte for processing Most laterite nickel processers run the furnaces so as to reduce the iron content sufficiently to produce ferronickel productsNickel laterite processing and electrowinning practice × Close Log In Log in with Facebook Log in with Google or , 65–73 Moskalyk, RR, Pariani, RL, 1984a Metal refining handling equipment justificationPart 1, automating starter sheet Nickel laterite processing and electrowinning 2013年6月25日 The Goro Nickel Mine is one of the world’s largest Nickel Laterite Mines The project is owned by Vale (69%), a joint venture company composed of Sumic Nickel Netherlands, Sumitomo Metal Mining and Mitsui Nickel Laterites: The World’s Largest Source of Nickel2024年1月1日 HPAL process for short is suitable for processing nickel laterite of limonite type with less than 5% content of magnesium in general to avoid excessive acid consumption Generally, for this type of nickel laterite ore, the contents of nickel and cobalt are 08–15% and 01–02% respectivelyNickel Laterite Metallurgy SpringerLink
.jpg)
Review on hydrometallurgical processing technology of lateritic nickel
hydrometallurgical processing is used for ores with low nickel content with the ratio of the main components SiO 2 /MgO, Fe/Ni and Ni/Co 15 and 12 and more than 30, respectively [24] The most common concentration process used before industrial hydrometallurgical processing of nickel laterites is to remove the coarse fraction from the feedstock,2017年1月20日 The nickel laterite processing routes were (1) high pressure acid leaching (HPAL), (2) ferronickel, and (3) the newly developed Direct Nickel (DNi Process) that involves atmospheric leaching of nickel laterite using nitric acid A cradle to gate approach was adoptedA life cycle assessment of a new laterite processing technology2013年3月13日 Technical difficulties and the high costs of existing processing methods are massive and continuing roadblocks,” Mr Debney said “There is a desperate need for a solution to the laterite processing problem that is threatening world supply Other forms of nickel reserves, such as sulphides, are running out and there are few new discoveries”New processing method to deliver huge benefits to global nickel HydroPyro Integration in the processing of Nickel Laterites Authors: Anne Oxley a, b and Dr Nic Barcza c a Alyssum Ventures Ltd, Isle of Man, IM8 2005; ref 4 M G King 2005; ref 5) when the future of nickel laterite processing seemed likely to be HPAL This is largely because recent projects to come online have seen huge HydroPyro Integration in the processing of Nickel Laterites
.jpg)
Enhanced methods for nickel recovery from lowgrade ores and
Fig 2: End use nickel consumption in 2022 Each year, the global demand for nickel exceeds three million tonnes [1] Industry experts estimate that 44 to 46 million tonnes of nickelbearing scrap are collected and recycled annually This recycled scrap contains approximately 350,000 tonnes of nickel [2], meeting about 12% of the total annual demand A Muntaqin, et al Jurnal Kimia Riset, Volume 7 No 1, Juni 2022 20 – 27 Online ISSN: 25280422 23 Table 1 The XRF test results of nickel ore Elements Unit This Research Safitri et al (2021 THE EFFECT OF SULFURIC ACID CONCENTRATION ON NICKEL PDF On Mar 11, 2019, Sait Kursunoglu and others published Hydrometallurgical Processing of Nickel Laterites—A Brief Overview On The Use of Solvent Extraction and Nickel/Cobalt Project For The (PDF) Hydrometallurgical Processing of Nickel With the material’s use in lithiumion batteries for electric vehicles constantly on the rise, the nickel industry is gearing up for growth, with a flurry of activity as producers look to get their hands on this nowessential battery metal Nickel Meeting Nickel Demand for Lithiumion Batteries
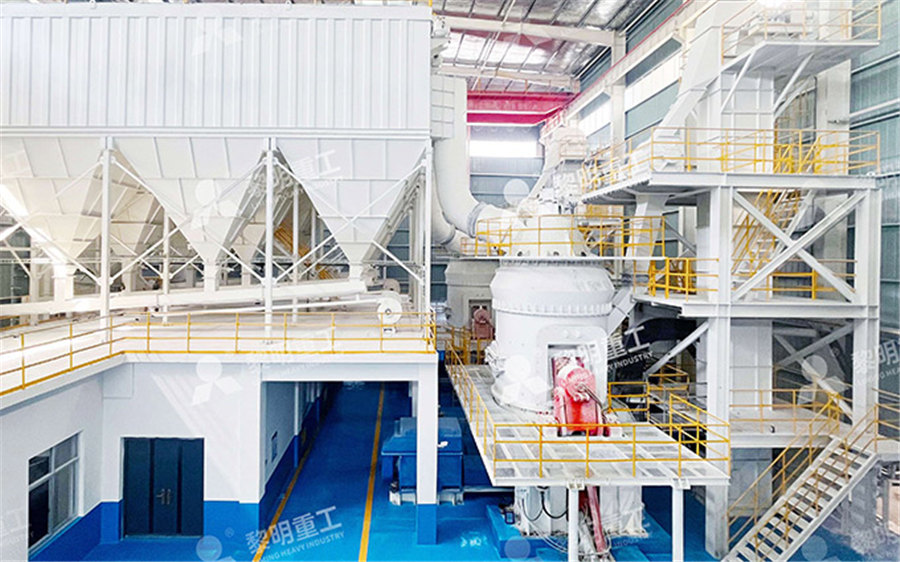
Nickel Laterites—Mineralogical Monitoring for Grade
2021年10月24日 Nickel laterite ore is used to produce nickel metal, predominantly to manufacture stainless steel as well as nickel sulfate, a key ingredient in the batteries that drive electric vehicles Nickel laterite production 2007年5月1日 Alternative approaches to downstream processing of nickel laterite heap leach liquors are described and reviewed is available, significant scaling of the process equipment resultsDOWNSTREAM PROCESSING OPTIONS FOR NICKEL LATERITE Nickel laterite makes up 70% of the world’s nickel reserves, and at the rate that nickel sulphide deposits are being depleted, production is switching to laterites which now account for 60% of the world’s nickel Nickel laterite is normally processed by pyrometallurgy (ie heat), hydrometallurgy (ie acid), or in some cases blending with What is nickel laterite? Homeland Nickel2023年2月15日 laterite nickel ore mostly exists in sapropelic deposits, and the content of laterite nickel increases with depth The raw nickel ore is always companied by clay and impurities The washing ore process can remove clay and impurities before crushing and beneficiation operations, which improves operating efficiency and helps to obtain highgrade nickel The Best Mining Equipment for Philippines Nickel Ore You
.jpg)
Nickel Laterite Technology—Finally a New Dawn? Springer
Nickel Demand (kt) 1970 1974 1978 1982 1986 1990 1994 1998 2002 2004 Nickel Demand Growth ’70−’90 = 28% /y Nickel Demand Growth ’93−’03 = 40% /y Figure 2 World nickel demand growth 1,800 1,700 1,600 1,500 1,400 1,300 1,200 1,100 1,000 2001 2003 Thousands of Tonnes 2005 2007 Existing World Producers Small Sulphide Projects 2023年12月19日 13–25% nickel Processing Froth flotation, smelting, and refining: relatively cheaper The Operation consists of three low‑grade nickel laterite deposits, formed from the weathering of ultramafic parent rock into a thick lateritic regolithNickel Geoscience Australia2003年7月1日 Global nickel reserves in 2018 reached up to 89 million tonnes, of which about 21 million tonnes or 2359% originated from nickel laterite deposits in Indonesia [4] Nickel laterite deposits in Nickel Laterites: A Review Request PDF ResearchGate2008年3月1日 Today, there is an increasing focus on the processing of the huge reserves of nickelrich laterite ores due to declining global reserves of nickel sulphides In 2003 it was estimated that 72% of the world landbased nickel resources were contained in nickel laterites, although these only accounted for 42% of the world nickel production ( Sudol 2005 )Atmospheric acid leaching of nickel laterites review ScienceDirect

(PDF) Nickel Laterite Smelting Processes and Some
2019年9月3日 Lowgrade ferronickel is simply an iron–nickel alloy that contains lower nickel than standard ferronickel does (ie, minimum of 15%) According to the literature, within a very shortequipment and providing reliable engineering data that could be used to build the fullscale plant The CESL Nickel Laterite flowsheet is shown in Figure 1 4 Figure 1: CESL Nickel Laterite Flowsheet CCD S L Pressure Acid Leach Purification 1 pH 35 Purification 2 pH 45 65THE APPLICATION OF THE CESL NICKEL PROCESS TO LATERITES2014年1月1日 Effect of sulfuric acid concentration on the leaching rate of metals (Leach temperature: 80°C, sulfuric acid concentration: 14 mol/L, time: 2 h, pulp density: 100 g/L, agitation: 500 rpm)Recovery of Nickel and Cobalt from a Low Grade 2023年1月19日 Rao MJ, Li GH, Jiang T et al (2013) Carbothermic reduction of nickeliferous laterite ores for nickel pig iron production in China: a review JOM 65:1573–1583 Article Google Scholar Norgate T, Jahanshahi S (2011) Assessing the energy and greenhouse gas footprints of nickel laterite processing Miner Eng 24:698–707An Overview of Nickel Utilization from Laterite Ore
.jpg)
High pressure acid leaching of a refractory lateritic nickel ore
2011年9月1日 Leaching temperature, leaching duration, sulfuric acid to ore weight ratio and particle size of the limonitic nickel laterite ore were studied Optimum parameters determined as 255 o C, 030 sulfuric acid to ore weight ratio, a particle size of 100% −850μ, 1 h of leaching duration with 30% w/w 873% of Ni and 888% of Co in the ore extracted into the PLS but, 2012年2月15日 This characteristic is suitable for producing heatresistant equipment such as aircraft engines In addition, Ni has a stainless feature Geology of laterite nickel deposit in Sorowako area, South Sulawesi Province In Proceedings of 29th Indonesian association of geologists, Bandung, Indonesia (pp 37–43) Thompson, S A (2000)Geostatistical Modeling of Ore Grade Distribution from Nickel and Cobalt Production Michael S Moats, William G Davenport, in Treatise on Process Metallurgy: Industrial Processes, 2014 223 Extraction of Nickel and Cobalt from Laterite Ores About 40% of the world’s primary nickel production starts with laterite oresLateritic Ni, Co deposits contain layers of one or both of (1) nickeliferrous, cobaltiferrous goethite Laterite Ore an overview ScienceDirect Topics2013年4月15日 Nickel laterite ores account for over 60% of global nickel supply They are the product of intensive deep weathering of serpentinites under humid tropical conditionsNickel Laterite Ore Deposits: Weathered Serpentinites
.jpg)
The Thunder From Down Under – A History of Nickel Laterites –
2009年3月27日 Nickel can be produced from either sulphides or laterite ore About 72% of the world’s nickel resources are laterites found mainly in tropical locales such as Indonesia, Cuba, Brazil and New Caledonia The remaining 28% are sulphides primarily located in Canada and Russia Australia has both sulphide and laterite nickel deposits2021年3月29日 Nickel can be found in laterite ores, sulfide ore, in secondary resources, and nonland resources like sea nodules[6,7] However, only 40 pct of nickel scrap can be recovered as secondary sources, nonland resources require high investment and operational costs, thus, sulfides and lateritic ores are the most important nickel sources[6,8,9,10,11,12] The identified Roasting and Leaching Behavior of Nickel Laterite Ore