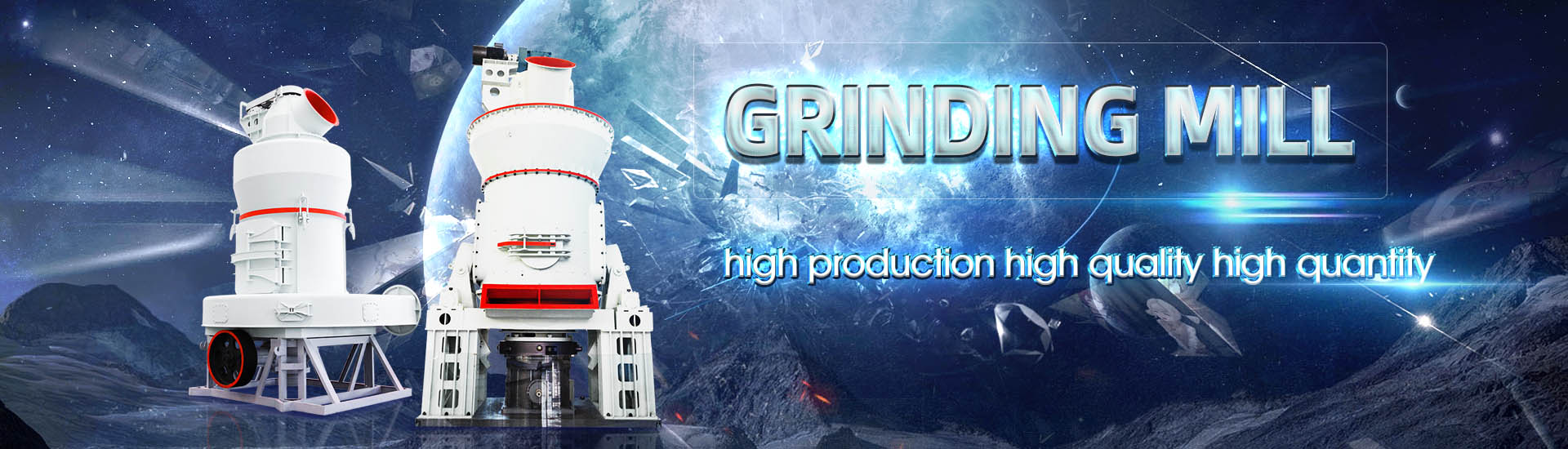
Secondary crushing method in underground mines
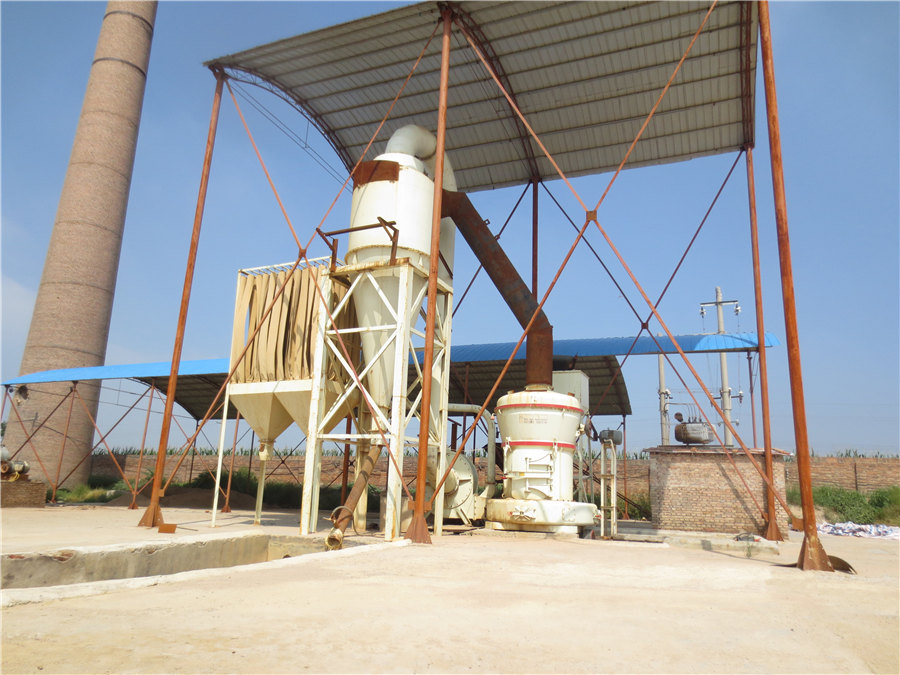
STUDY AND OPTIMISE THE SECONDARY AND
An investigation aimed at studying and optimizing the Secondary and Tertiary crushing circuits’ conditions was conducted at the Konkola West mill Concentrator in Chingola The concentrator treats sulphide and oxide ores, which consists 2010年2月1日 Underground mining: roomandpillar mining of thick seams –“Benching” Different approaches allow either the top or bottom part of the seam to be mined out first(PDF) Underground mining Methods ResearchGate2018年8月29日 In 2017, a secondary crushing circuit was installed to remove the SAG mill throughput bottleneck and increase production of highly competent underground ore from 135 The application of secondary crushing at the Jundee gold mine2020年2月1日 The critical factors in the design stage of deep underground mining projects are to establish suitable location and layout of openings; determination of suitable excavation method, sequential excavation and Ground behaviour analysis, support system design and
.jpg)
Limestone and Crushed Rock Department of Energy
Most crushed and broken stone is mined from open quarries; however, in many areas, factors favoring largescale production by underground mining are becoming more frequent and 2019年11月16日 In this paper, a novel secondary mining technology is suggested incorporating a novel concept of building a key bearing layer (KBL) through backfilling in the previously Design of the Key Bearing Layer and Secondary Mining In primary crushing the largest lumps of ore mined must be dealt with In secondary crushing the maximum sized piece is unlikely to exceed 6″ in average diameter and some of the unwanted Secondary Crushing SpringerLink2016年7月13日 Mining methods are traditionally grouped into open pit and underground mining This subdivision will be followed in this chapter In addition, a brief introduction is made to ‘unconventional’ mining methods, including in Mining Methods SpringerLink
.jpg)
(PDF) ROCK BLASTING FOR MINING ResearchGate
2017年4月15日 Such methods reduce the crushing effect around the borehole and are a secondary blast may be required to reblast a portion of the rock to reduce it to a (an underground mine at Montana 2020年10月1日 The arrival of underground mine optimisation techniques date back to the 1980's through the introduction of an optimal stope layout method (Lizotte and Elbrond, 1985) Over the last two decades there has been growing interest in three main areas associated with underground mine optimisation These include: •Production scheduling optimisation for sublevel stoping mines Typically the underground mines use a mechanised bord and pillar mining method, the distance between the mines is approximately 30 km along strike Maximum depthCRUSHING AND MATERIALS HANDLING AT NGEZI PLATINUM MINES 2014年4月1日 Real estate in an underground mine is not cheap, so the design of primary crushing plants has more limitations underground than on the surface However, the primary crushing and transportation of ore to the surface is often Below the surface: Setting up an underground primary jaw crusher
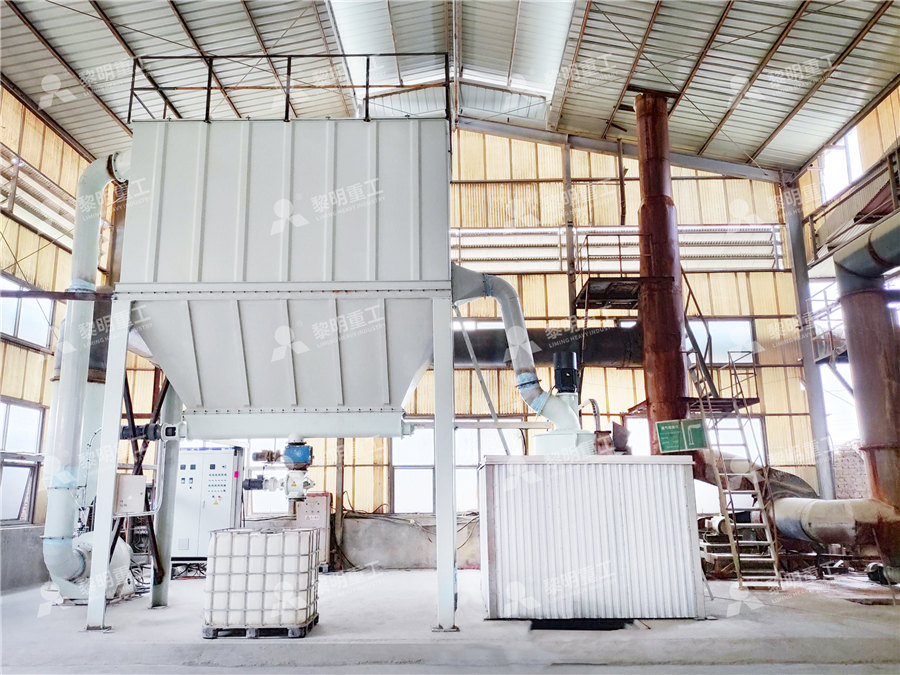
SUPPORT IN UNDERGROUND HARD ROCK MINES Rocscience
The choice of the type of support installed in a particular underground excavation depends upon the extent of the zone of loosened or fractured rock surrounding that excavation A very crude guide to support selection is given in Table 1 Active rock reinforcement Underground mines use two principal types of rock reinforcement tensioned2023年1月1日 In the deep underground environment, financial costs are higher, which is a persistent disadvantage, since any advantage gained in deep underground mines may be valuable to shallow underground mines Therefore, the financial disadvantage must be compensated by an increase in certainty to mitigate the cumulative impacts of resource model Moving towards deep underground mineral resources: Drivers, 2022年12月28日 It is mainly used for stripping openpit mines, building tailings dams, leveling sites and forming waste rock cushions, and etc The large blocks produced by blasting often need to be broken up by supplementary blasting, which is called secondary blasting In addition, controlled blasting methods are also used in mining blastingMining Blasting SpringerLink2023年12月16日 The complexity of coal and gas outburst as mine disasters is immense, and they pose a severe threat to the safety of underground employees and inflict significant damage to coal mine production (Dennis, 2019; Hou, 2021; Zhang et al, 2023a, c)China has attached great importance to coal mine safety and has achieved remarkable results, effectively reducing the Energy Evolution and Coal Crushing Mechanisms Involved in Coal
.jpg)
Extraction Methods SpringerLink
2024年2月11日 Further aspects to be considered in the development of an aggregate underground mine are ventilation (it must be supplied to all underground workings), removal of underground water by pumping, access (using ramp and tunnel since shafts normally need very high expenditures per ton of production) including its location and size, drilling and blasting 2023年2月11日 Scientific Reports Drilling and blasting designs for parallel hole cut and Vcut method in excavation of underground coal mine galleries Skip to main content Thank you for visiting natureDrilling and blasting designs for parallel hole cut and Vcut method The ASM sector, lacking resources and capital access, compared to the medium and large mines of the world has not been able to evolve towards the stateoftheart methods and technologies that are applied to REM: Int Eng J, Ouro Peculiarities of drilling and blasting in underground Longhole stoping is a high production and lowcost mining method for metalliferous mine It is a very popular method chosen when open pit mining activities are no longer economical and mines move to underground operations This method is a variant of sublevel stoping in which longer blastholes with larger diameters (100–165 mm) are usedOverview of Underground Metalliferous Mining SpringerLink
.jpg)
Optimization of blasting parameters and prediction of vibration
2023年5月1日 Mineral resources have changed the economic pattern of local cities to a certain extent, thus promoting the economic development of remote areas in China [3]Blasting technology not only determines the safety, quality, and cost of mining, but also has a significant impact on the subsequent bucket loading, transportation, crushing, and other processes as 2023年2月28日 Learn everything you need to know about primary crushing, secondary crushing, and tertiary crushing in this comprehensive guide Discover the types of crushers used in each stage, their working principles, and the advantages and disadvantages of each process Get answers to frequently asked questions and improve your understanding of the comminution The Complete Guide to Primary Crushing, Secondary Crushing, 2021年11月20日 Conventional underground coal mining relies upon the use of continuous miners in order to extract coal reserves from underground coal seams In combination with the continuous minersshuttle cars Optimum Utilisation of Continuous Miner for Improving Production 2022年9月25日 Learn about the primary methods of underground mining of Australia (2016), there are around 70 operating underground rock mines active within Australia The majority of underground mines are located in Western Australia, Activate is used to superactivate water sprayed to control dust in material crushing, Underground Mining in Australia Primary Methods
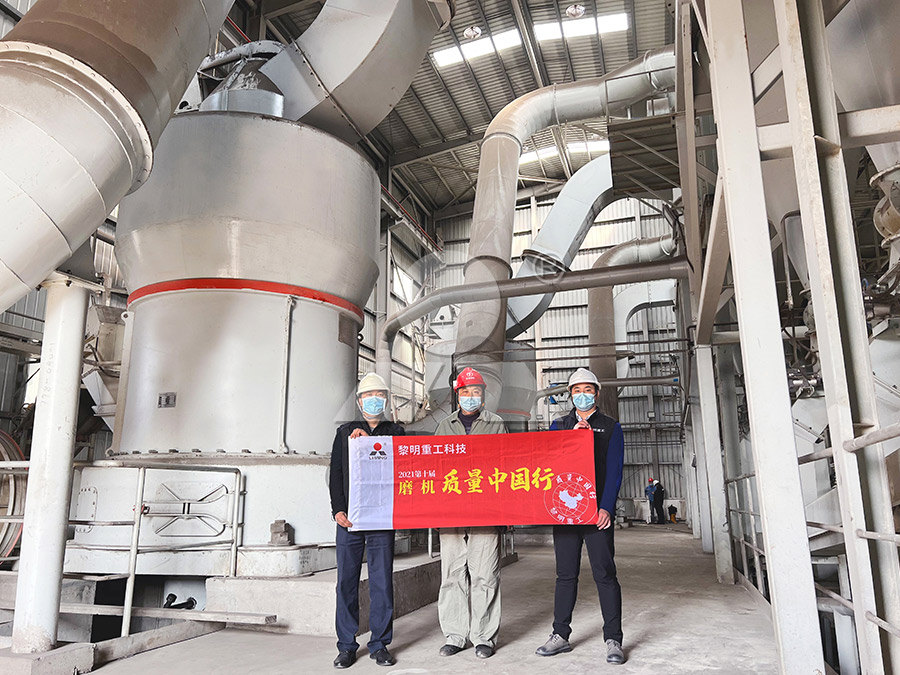
Blasting Techniques Used in Underground and Opencast Mines Mining
Read this article to learn about the blasting techniques adopted in underground and opencast mines Blasting Techniques Adopted in Underground Mines: Drilling Patterns in Stone: Drilling patterns, also called shothole patterns, are named after the type of cut holes used and the principal patterns are: (1) Pyramid cut or cone cut (2) Wedge cut (3) Drage cut (4) Fan cut (5) 2015年5月13日 Underground mine backfilling is a form of ground improvement that has to be carried out in the mine sites The backfilling provides ground support and regional stability, thus facilitating ore removal from nearby regions The large underground voids created by the ore removal are backfilled with the waste tailings in the form of paste fills, hydraulic fills, and Underground Mine Backfilling in Australia Using Paste Fills and 2024年11月14日 Mining Underground, Safety, Techniques: When any ore body lies a considerable distance below the surface, the amount of waste that has to be removed in order to uncover the ore through surface mining becomes prohibitive, and underground techniques must be considered Counting against underground mining are the costs, which, for each ton of Mining Underground, Safety, Techniques Britannica%PDF16 %âãÏÓ 4215 0 obj > endobj 4235 0 obj >/Encrypt 4216 0 R/Filter/FlateDecode/ID[87C03FABF6FB2246BC4F9AB649B4B217>]/Index[4215 26]/Info 4214 0 R/Length 101 AusIMM – Leading the way for people in resources
.jpg)
Rock Fragmentation Evaluation towards BlastToMill Concept of
2021年9月29日 the performance of the crushing and grinding operations will enhance the overall efficiency and profitability of the mine Assessment of a blast on the performance of the primary crushing as part of the blast optimization strategy is an added step to the blasttomill concepts of the fragmentation process of hard rock miningunderground mines The particle size distribution of fragmented rock in mines significantly affects operational performance of loading equipment, materials handling and crushing systems A number of methods to measure rock fragmentation exist at present, however these systems have a number of shortcomings in an underground environmentApplication of laser scanning to measure fragmentation in2018年5月29日 Grade control in underground mines aims to deliver quality tonnes to the process plant via the accurate definition of ore and waste It comprises a decisionmaking process including data collection and Integrating the Theory of Sampling into 2001年1月1日 In underground mines, where noncaving methods are used to extract The secondary ore stope is divided into four layers office and living buildings, buildings for crushing, beneficiation Underground Mining Methods—Engineering Fundamentals and International
.jpg)
Heat Stress in Underground Mines and its Control Measures: A
2022年1月14日 Heat stress is a major concern for the health, safety and productivity of miners working in hot and humid underground mines At greater depth, heat inside underground mines increases due to geothermal gradient, heat released from highcapacity machinery, exposed rock surface, autocompression of air, human metabolism, etc Prolonged physical work in thermal 2021年9月22日 InPit Crushing and Conveying (IPCC) systems are receiving more attention today due to current characteristics of openpit mining operations and what is expected to occur in the futureOVERWIEW OF INPIT CRUSHING CONVEYING TECHNOLOGY IN OPEN PIT MINES2023年2月28日 Secondary Crushing Secondary crushing is the second stage of crushing that takes place after the primary crushing The secondary crusher is the equipment that reduces the size of the materials further, after they have been reduced by the primary crusher The secondary crusher has a size reduction ratio ranging from 3:1 to 5:1Primary and Secondary Crushing: Understanding the Basics A 2021年6月26日 Shaft stability evaluation (SSE) is one of the most crucial and important tasks in view of the role of vertical shaft in mining engineering, the accuracy of which determines the safety of onsite workers and the production rate of target mine largely Existing artificial methods are limited to the amount of data and complex process of modeling as well as rare Evaluation of vertical shaft stability in underground mines: comparison
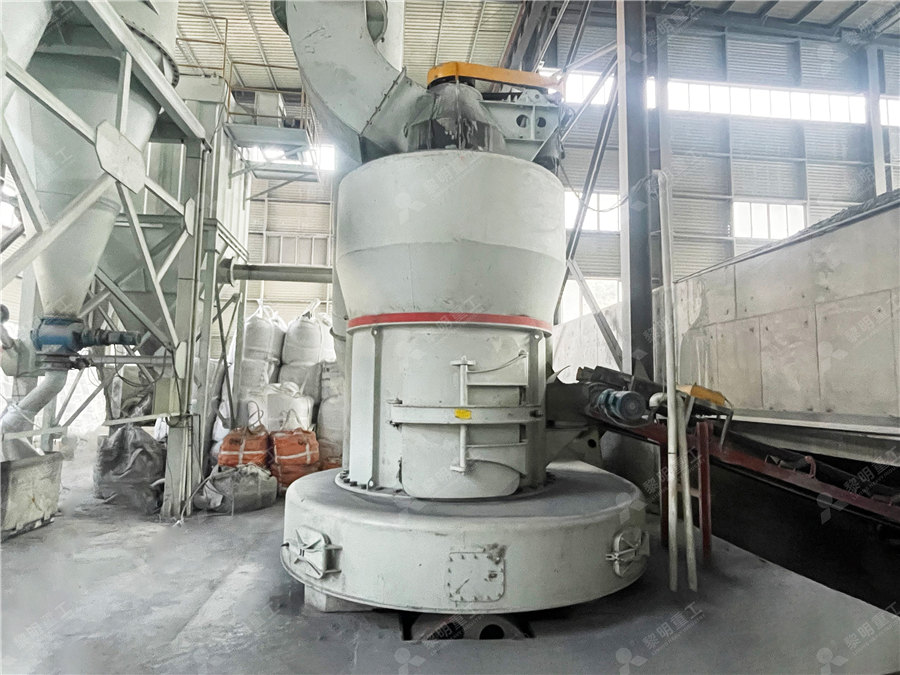
Retrieving surface secondary subsidence in closed mines with
2023年4月20日 The groundwater recovery in closed mines causes surface secondary subsidence or uplift, which threatens the safety of buildings around the mines However, due to the longlasting surface subsidence in closed mines, the coherence points selected by permanent scatterer (PS) interferometric synthetic aperture radar (InSAR) are not enough to reflect the Drawing upon numerical studies, published laboratory results and comminution theory, a new methodology has been developed for the prediction of drawpoint size distributions throughout the operational life of a cave mine The method is ‘hybrid’ because it utilises both numerical modelling and empirical comminution relations to track the evolution of caved rock size distributions A hybrid methodology for secondary fragmentation prediction in cave mines2018年8月29日 Northern Star Resources Limited Jundee Gold Mine in Western Australia operates a comminution circuit that consists of a primary crusher, 385 MW semiautogenous grinding (SAG) mill, 18 MW ball mill and pebble recycle crusher In 2017, a secondary crushing circuit was installed to remove the SAG mill throughput bottleneck and increase production of The application of secondary crushing at the Jundee gold mineMINING METHODS (UNDERGROUND COAL) 10 INTRODUTION TO UNDERGROUND COAL MINING : 11 Classify Underground Coal Mining Methods Method of winning coal in underground mines are classified into two main categories : 1 Bord and pillar (also known as pillar and stall) and its modification 2 Longwall (i) Advancing, (ii) RetreatingLECTURE NOTES ON UNDERGROUND COAL MINING OSME
.jpg)
Diamond Mining Methods Diamond Museum Cape Town
Stage 1 – Crushing Once the diamond bearing ore and gravel is collected, it is transported to a primary crusher The primary crusher is responsible for reducing the size of the ore into smaller, more manageable pieces or chucks measuring no larger than 150mm2020年4月1日 Preexcavated withdrawal channel (PWC) is an effective means to shorten the withdrawal time of fully mechanized working face and improve the efficiency, safety, and reliability during the withdrawalFundamentals of modern ground control management in Australian 2015年8月24日 The goal of the following project was to study the effect of production blasting on loading and hauling times, secondary breaking times and primary crushing times at the Experimental Mine of the The effects of Drilling and Blasting Performance on Fragmentation in underground mines; the crushing and grinding of ore; are separated by magnetic or electrostatic methods in a dry environment Secondary crushing (SCC 30302406)d 003 D 0012 D Tertiary crushing (SCC 30302407)d 003 E 001 E Wet grinding Neg Neg1124 Metallic Minerals Processing US Environmental Protection
.jpg)
Advances in screening technology in the mining sector
Coal processing has changed significantly in recent decades Especially in large coal mines, boiler coal is increasingly extracted by openpit mining and by socalled surface mining and no longer so much by underground mining If possible, coal found at depths of up to 90 m is today mined by the open pit methodGeotechnical Considerations in Underground Mining/Department of Industry and Resources Guideline Document No: ZME723QT 10 INTRODUCTION The potentially hazardous nature of underground mining requires the application of sound geotechnical engineering practice to determine the ground conditions, the ground support and reinforcement requirements, as well Geotechnical considerations in underground mines Department 2017年3月16日 In other work, laser scanning was also used to measure rock fragments in underground mines, to assess the blasting efficiency and evaluate the performance of loading equipment and crushing systems Application of laser scanning to measure fragmentation in underground mines928 Ventilation plans for underground mines 929 Monitoring of toxic, asphyxiant and explosive gases 30 DESIGN CONSIDERATIONS 31 Primary Ventilation The basis of effective ventilation of underground mines is the adequacy of the primary ventilation system, that is the total volume flow through the mine which isUNDERGROUND VENTILATION (METALLIFERROUS MINES) GUIDELINE