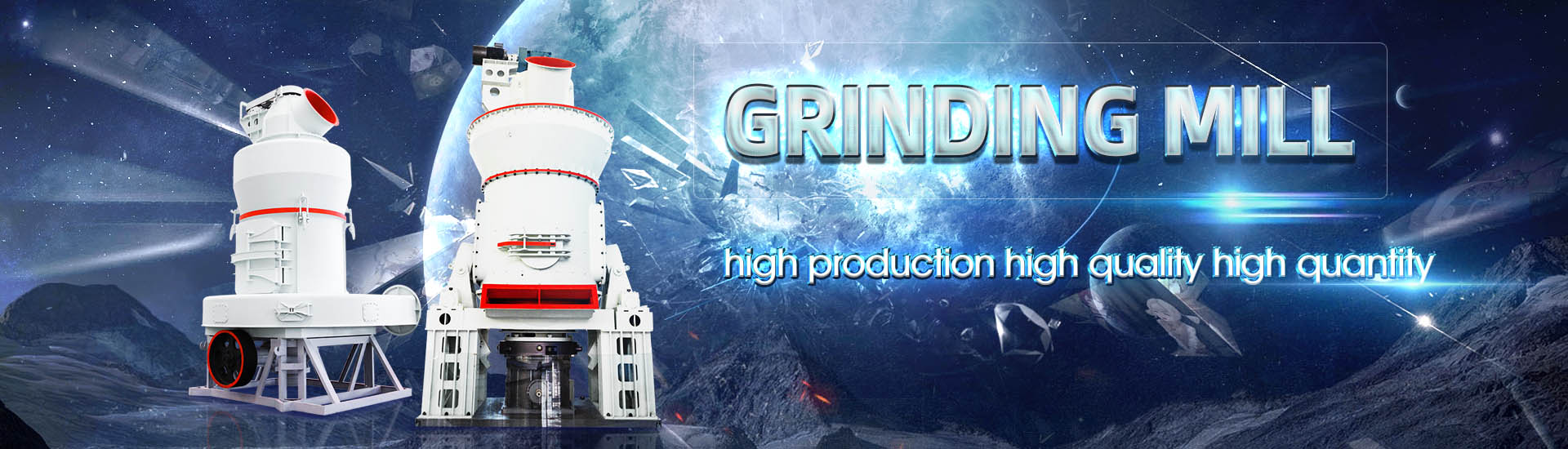
How big is the mill of a cement grinding station with an annual output of 100,000 tons

Cement Grinding Unit Cement Grinding Plant
Take the annual output of 600,000 tons of largescale cement grinding station as an example, there are three common options can be recommended: SCHEME 1 : roller press + φ 32 ×13m ball mill; SCHEME 2 : φ 38 ×13m closed mill;Take the annual output of 600,000 tons of largescale cement grinding station as an example, there are three common options can be recommended: SCHEME 1: roller press + φ 32 ×13m ball mill; SCHEME 2: φ 38 ×13m closed mill;Cement Grinding Plants Cement Grinding Unitonline live calculators for grinding calculations, Ball mill, tube mill, critical speed, Degree of filling balls, Arm of gravity, mill net and gross powerball mill calculations, grinding media filling degree, ball size, mill Optimization of the Cement Ball Mill Operation Optimization addresses the grinding process, maintenance and product quality The objective is to achieve a more efficient operation and OPTIMIZATION OF CEMENT GRINDING OPERATION IN BALL MILLS
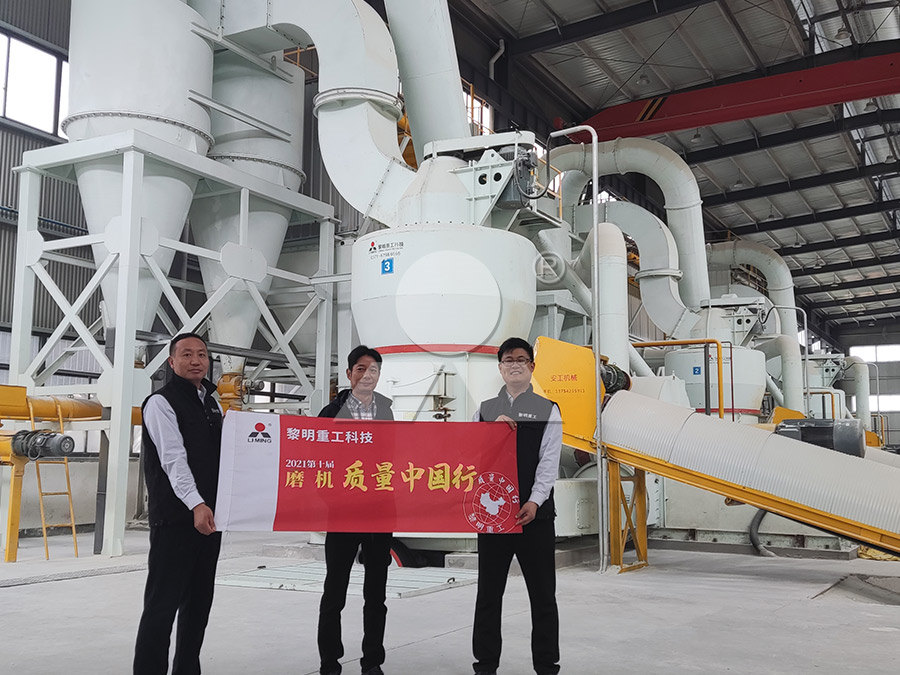
BALL MILLS Ball mill optimisation Holzinger Consulting
Ball mills and grinding tools Cement ball mills are typically twochamber mills (Figure 2), where the first chamber has larger media with lifting liners installed, providing the coarse grinding mill motor power consumption at a mill motor total SEEC of 30 kWh/t This results in k to its design value of around 12 – 15 m/sec above ball charge If the dust from mill ventilation is Thomas Holzinger, Holzinger Consulting, grinding system A 10 MW cement mill, output 270 tonnes per hour A cement mill (or finish mill in North American usage [1]) is the equipment used to grind the hard, nodular clinker from the cement kiln into Cement mill WikipediaCement milling is usually carried out using ball mills with two or more separate chambers containing different sizes of grinding media (steel balls) Grinding clinker requires a lot of energyCement Milling
.jpg)
Cement Grinding Cement Plant Optimization
About 27 to 35 % volume of mill is filled with grinding media Equilibrium charge is that charge where compensation for wear can be done by balls of one size only usually the largest size in 2018年7月1日 This study aimed at optimizing both the energy efficiency and the quality of the end product by modifying the existing flowsheet of the cement grinding circuit As a general Energy and cement quality optimization of a cement grinding circuit2024年1月23日 Initially, raw materials such as clinker and auxiliary materials are conveyed to the cement grinding mill through a feeding system Inside the grinding chamber, The efficient operation of cement grinding mills directly impacts the quality and output of cement production Beyond cement production, How To Optimize The Operation Of The Cement MillPlugGrind® is the only portable grinding station with ball mill or vrm solution from 12 tph to 75 tph Skip to content +34 913 921 055 +34 915 001 834 Contact us; CONTACTO 25 years in the cement industry supplying MODULAR AND PORTABLE GRINDING STATION
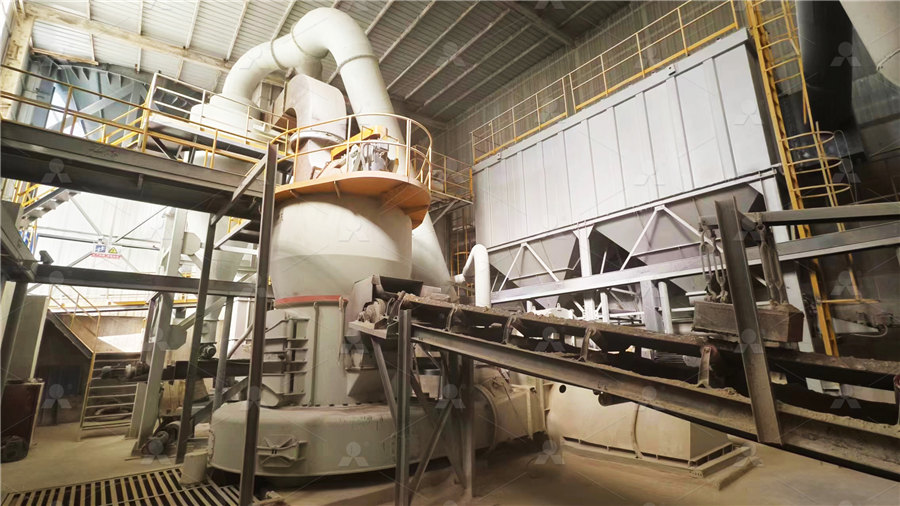
New Features of Cement Grinding Station Design
2024年6月14日 Cement grinding has always been the most powerconsuming part of cement production The cement ball mill in the cement grinding station mainly has two functions: crushing and grinding of materials, and the The cement grinding station with an annual output of 1 million tons adopts the technology of separately grinding clinker and slag, among which the clinker grinding adopts the combined grinding process composed of two Φ 42m × 13m cement millsCement grinding station with annual output of 1 million tonsTake the annual output of 600,000 tons of largescale cement grinding station as an example, there are three common options can be recommended: SCHEME 1: roller press + φ 32 ×13m ball mill; SCHEME 2: φ 38 ×13m closed mill;Cement Grinding Plants Cement Grinding Unit Cement Grinding StationOutput Capacity: 100 ~ 5,000 TPD Grinding Mills: roller press / vertical roller mill / ball mill We will elaborately create the most appropriate cement grinding station scheme for you according to your production demand, and the qualified materials enter the cement mill for further grindingCement Grinding Plant Expert Cement Grinding Solutions from
.jpg)
Cement Grinding Unit Process High Quality Cement Grinding
At the Cement Grinding Stage, 90 – 95% of the clinker is mixed with gypsum and ground in a Cement Ball Mill to produce quality cement OPC 43 and OPC 53 In case of PPC Cement, there is an addition of Fly Ash2023年7月19日 A A Stronin, Grinding of cement clinker in ball mill using dense ball packing and grinding intensifier, in Proceedings of the Conference "Youth and Scientific and Technological Progress", BSTU (PDF) Intensifying the cement grinding process ResearchGateThe FLSmidth OK Mill Free download as PDF File (pdf), Text File (txt) or view presentation slides online The document discusses the FLSmidth OK Mill, which is designed for cement and slag grinding It provides details on the mechanical features and capacity ranges of the OK Mill system Performance data from various cement plants shows the OK Mill achieves the The FLSmidth OK Mill PDF Mill (Grinding) CementFor a cement mill: intermediate or outlet diaphragm For the case of; cement mills with a drying chamber see raw mills Mill working conditions: ventilation air speed through the mill Bigger or smaller than 12 [m/s] Material abrasivity The [%] of slag or pouzzolana content on the fresh mill feed for cement grindingEverything you need to know about clinker/cement Grinding

Cement Grinding Cement Plant Optimization
Ball Mill Ball mills with high efficiency separators have been used for cement grinding in cement plants all these years Ball mill is a cylinder rotating at about 7080% of critical speed on two trunnions in white metal bearings or slide shoe bearings for large capacity millsOutput Capacity: 100 ~ 5,000 TPD Grinding Mills: roller press / vertical roller mill / ball mill Grinding Systems: open circuit / closed circuit / vrm final grinding other commonly used equipment in the cement grinding station include Cement Grinding Plant Expert Cement Grinding Output: 15110 t/h Power: 553550kW Highlights: fully automatic, high efficiency, etc GET QUOTATION What Is A Cement Ball Mill The cement ball mill is a kind of cement grinding mill It is mainly used for grinding the clinker Cement Ball Mill Cement Grinding MachineA cement grinding mill “A” with a capacity of 50 tons per hour utilizes forged steel grinding balls costing Php12,000 per ton, which have a wear rate of 100 grams per ton cement milled Another cement mill “B” of the same capacity uses high chrome steel grinding balls costing Php50,000 per ton with a wear rate of 20 grams per ton cement Answered: A cement grinding mill “A” with a bartleby
.png)
Answered: A cement grinding mill "A" with the bartleby
A cement grinding mill "A" with the capacity of 50 tons per hour utilizes forged steel grinding balls costing P12,000 per ton, which have a wear rate of 100grams per ton cement milled Another cement mill "B" of same capacity uses high chrome steel grinding balls costing P30,000 per ton with wear rate of 10grams per ton cement milledFor the cement industry the ball mill was really an epochmaking breakthrough as for almost 80 years it was the predominant mill for grinding of raw materials and coal, and still today is the most used mill for cement grinding Over the last three decades the vertical roller mill has become the preferred mill for grinding of raw materialsCement grinding Vertical roller mills VS ball millsAGICO Cement is a cement grinding plant manufacturer, we'd like to helps you learn more about cement grinding plant and cement grinding machines Skip to content +86 Cement Grinding Plant Overview Cement Grinding Unit AGICO CementOptimization of a Fully Airswept Dry Grinding Cement Raw Meal Ball Mill Closed Circuit Capacity With the Aid Free download as PDF File (pdf), Text File (txt) or read online for free This document discusses optimizing the production capacity of a fully airswept industrial scale twocompartment cement ball mill through simulation The mill has two compartments, with the first Optimization of A Fully AirSwept Dry Grinding Cement Raw Meal
.jpg)
An Introduction to Clinker Grinding and Cement Storage
would be a length of 135 m and a diameter of 25 m, with a speed of approximately 20 revolutions per minute Such a mill would normally have a load of approximately 90 tons of grinding media, graduated from 90 mm to 60 mm in the first chamber, 50 mm to 15 mm in the second chamber and 15 mm down in the final chamber2016年10月5日 In this chapter an introduction of widely applied energyefficient grinding technologies in cement grinding and description of the operating principles of the related equip‐ ments and comparisons over each other in terms of grinding efficiency, specific energy consumption, production capacity and cement quality are given A case study per‐ formed on a EnergyEfficient Technologies in Cement GrindingThe cement output is rated at 200 MTPH and the motor rating is 8700 HP (metric HP), equal to 6400 kW at 15 RPM The motor was manufactured by Brown, Boveri and Comp, Baden, Switzerland The 5 m diameter mill was supplied Mill drives INFINITY FOR CEMENT EQUIPMENT2017年10月26日 The following are factors that have been investigated and applied in conventional ball milling in order to maximize grinding efficiency: a) Mill Geometry and Speed – Bond (1954) observed grinding efficiency to be a Factors Affecting Ball Mill Grinding Efficiency
.jpg)
Cement Mill Cement Grinding Machine AGICO
Coal mill is the main equipment in the pulverized coal preparation processBecause calcining topgrade cement clinker requires a stable supply of coal powder as the fuel of cement kiln, and more than 85% of pulverized coal This paper presents aspects of monitoring material dust emissions from stationary emission sources (monthly dust measurements performed on cement mill stacks—mill outlet and separator outlet)The flowchart of cement grinding, A, Bsampling points 1 The document discusses optimizing cement grinding circuits It presents tools like the Bond method and population balance models that can be used to analyze and optimize cement grinding 2 It provides details on the typical cement production process and how around 40% of energy is consumed during the final grinding of clinker Optimizing this grinding circuit can Cement Grinding Optimization PDF Mill (Grinding) Cement2024年2月23日 The operation of the cement raw mill is a critical step in cement production By grinding the raw materials into a fine powder, these powders can be more easily mixed with other cement ingredients and burn more evenly during the cement clinker process Therefore, the efficient operation of the cement raw mill directly impacts the production efficiency and quality How Does a Raw Mill Work in a Cement Industry
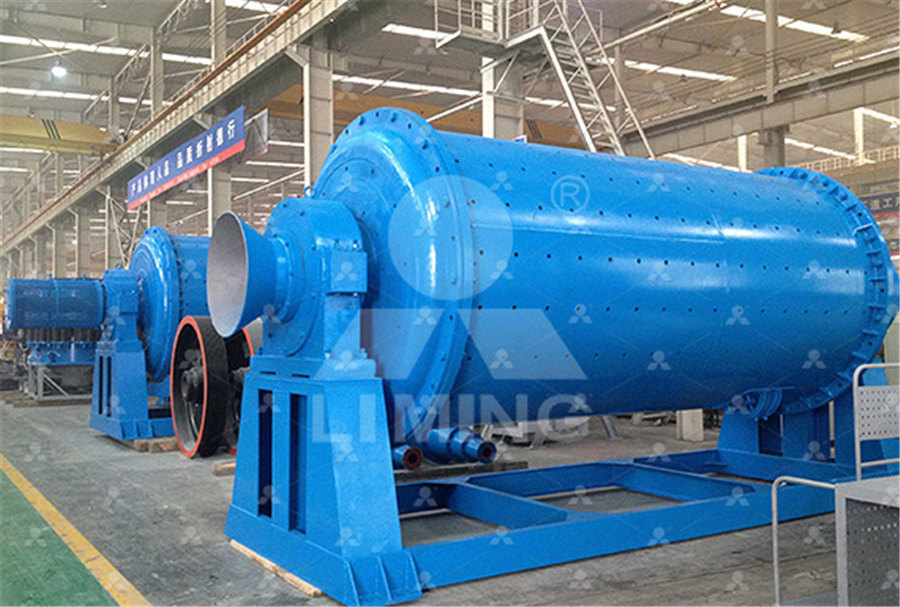
Improvements in New Existing Cement Grinding Mills by Tim
o 120⁰ C causes excessive gypsum dehydration media coating if mill ventilation is poorand cement Roller presses are used mainly in combination with a ball mill for cement grinding applications and as finished product grinding units, as well as raw ingredient grinding equipment in mineral applications This paper will focus on the ball mill grinding process, its tools and optimisation possibilities (see Figure 1) The ball millBALL MILLS Ball mill optimisation Holzinger ConsultingΦ22×75m Cement Mill : 700 t/d : GRMR2231 Vertical Raw Mill : GRMC1221 Vertical Coal Mill : Ф3×48m Rotary Kiln : GRMK3041 Vertical Cement Mill : 1000 t/d : GRMR2231 Vertical Raw Mill : GRMC1231 Vertical Coal Mill : Φ33×52m Rotary Kiln : Φ26×13m Cement Mill : 1500 t/d : GRMR3031 Vertical Raw MillCement Production LineFigure 3f: Clinker grinding mill The output from the mill produces both the required fine cement and partially ground coarse particles A system incorporating an air separator through a bucket elevator and air slides separates the fine and coarse constituents The coarse product will be returned back into the mill for further grindingEVERYTHING YOU NEED TO KNOW ABOUT ESTABLISHING CEMENT GRINDING PLANT
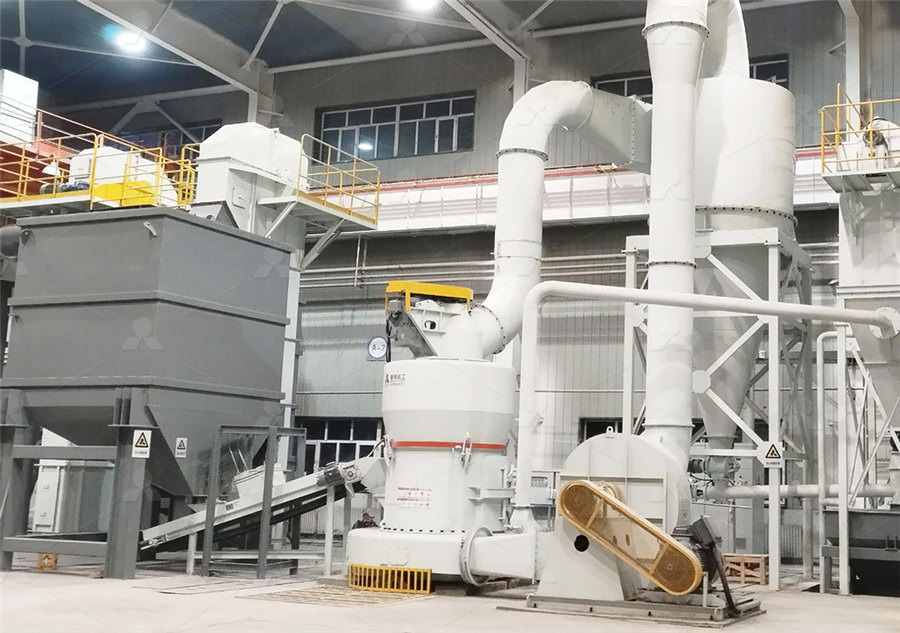
Grinding Process Optimization Featuring Case Studies and
mills for cement grinding, a 245 tph vertical roller mill was added A Technical Concept The rating of the modular vertical roller mill 5000 R4 mill is based on grinding tests conducted at the 2009年6月1日 In this study, the milling of clinker was evaluated by varying the mill speed (24 and 72 RPM), residence time (3 and 5 hours) and grinding media load (30 and 40 %) in a ball millCement clinker grinding: Evaluation of mill spin speed, CHAENG can provide the complete solutions of 15100t/h cement grinding station for you Please send to for The system configuration is reasonable, the production efficiency is high, the output is large The cement grinding stationA cement ball mill is ready for transportation There are many kinds of industrial equipment used in a cement plant, including thermal equipment, grinding equipment, dust removal system, transportation system, storage system, and so onWhen placing an order, we may need to order different equipment from multiple manufacturers at the same timeHow to Start a Cement Factory
.jpg)
Cement Grinding StationHongji Mining Machinery
How to build a cement grinding station? The layout of cement production is to establish cement clinker production lines in mining areas and cement grinding stations near cement sales markets to reduce transportation costs If the clinker production line is built near a city, about 16 tons of cement raw material will be needed for every 1 ton A cement grinding mill "A" with a capacity of 50 tons per hour utilizes forged steel grinding balls costing P 12,000 per ton, which have a wear rate of 100 grams per ton cement milled Another cement mill "B" of the same capacity uses high chrome steel grinding balls costing P 50,000 per ton with wear rate of 20 grams per ton cement milledSolved A cement grinding mill "A" with a capacity of 50 tonsThe document discusses the OKMill, a vertical roller mill for grinding cement or slag Some key points: The OKMill uses proven technology licensed from Onoda and Kobe Steel and is suitable for grinding blended cement or slag It provides energy savings of 2040% compared to tube mills It has a simple and spacesaving layout with a vibrationproof grinding bed and highly wear OK Mill PDF Mill (Grinding) CementCommissioning Guide Lines Free download as PDF File (pdf), Text File (txt) or read online for free The document provides instructions for commissioning various components of a cement plant, including the raw mill, limestone crushing, shale/gypsum/coal crushing, raw meal handling, and kiln startup It describes checking equipment is correctly installed and calibrated before Commissioning Guide Lines PDF Mill (Grinding) Cement
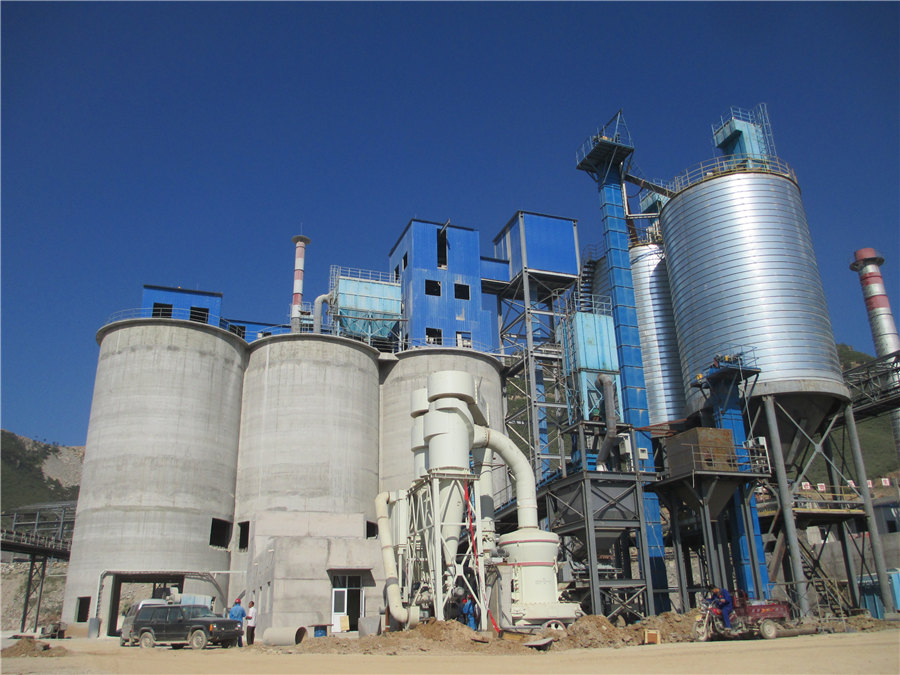
Cement Mill Optimization: Practical Strategies for Enhanced
Adjusting mill parameters: Finetuning mill parameters such as mill speed, ball charge, filling ratio, and grinding media size can have a substantial impact on the grinding efficiency of the mill For example, a 10% increase in mill speed can result in up to 10% higher production rate, while optimizing the ball charge can lead to a 510% reduction in energy consumption2023年8月21日 In Udaipur Cement Works Limited, we use the following types of mills for grinding raw materials and cement: • Vertical Roller Mill (VRM): We employ the Loesche (LM 384) and Gebr Pfeiffer (MVR 6000C6) technology Grinding process is a critical stage in cement production