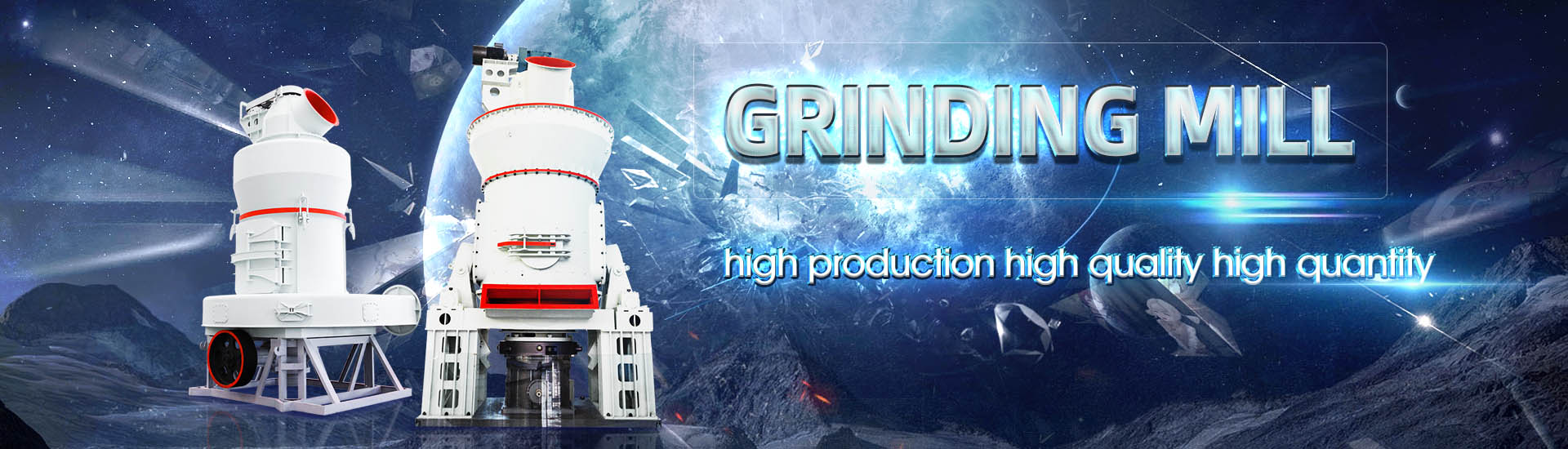
Study on steel ball ratio of the Powder Processing Research Institute
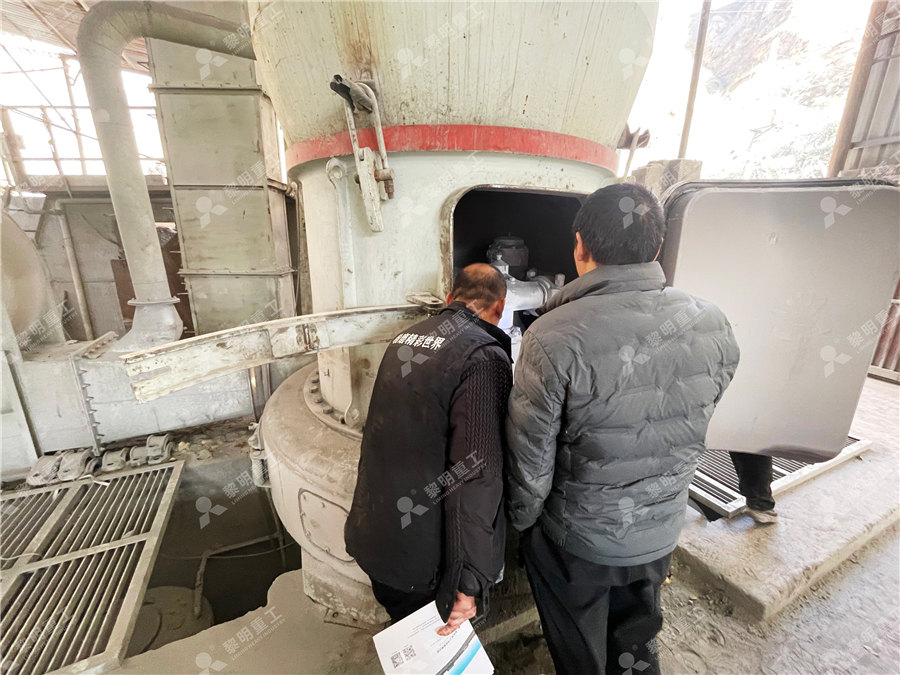
Effect of Ball to Powder Ratios on the Phase Transformation of
2024年1月11日 Nanostructured SAF2507 super duplex stainless steel powders were prepared in a Retsch PM100 planetary ball mill for 20 h at 5:1 and 10:1 ball to powder ratios, 2024年11月19日 The present work investigated an Al45Zn29Mg025Cu (wt%) alloy with superhigh yield ratio and favorable plasticity prepared by an improved powder metallurgy (PM) Superhigh Yield Ratio and Considerable Plasticity in PowderThe milling times of 10 and 40 hours for two diferent balltopowder ratios are investigated for a powder mixture with a composition of Cu271Zr227B (wt%) XRD and SEM analyses wereThe effect of ballpowder ratio on the mechanical and structural 2014年6月15日 The ball to powder ratio (BPR) is a processing parameter that is frequently used in both mechanical (ball) milling and mechanical alloying A number of recent studies provided Why the ball to powder ratio (BPR) is insufficient for describing the
.jpg)
Effect of BalltoPowder Ratio on Morphology, Structure, and
2021年7月12日 It was found that ball milling smoothed the sharp edges and corners of the precursor powder and reduced the size of the precursor powder As a result, the ballmilled 2021年6月1日 This study focuses on the microstructural refinement induced by ball milling in individual metals and Cubased metal mixtures A phenomenological model is developed to (PDF) Effect of ball powder ratio on microstructure and 2018年11月1日 The present study involves the investigation on the effect of processing parameters of powder metallurgy on the microstructure and hardness characteristics of the The ball to powder ratio (BPR) dependent morphology and 2024年1月11日 The paper shows the influence of the 100 hours ball milling process of commercial AISI 316L stainless steel powder and the mixture of powders of its components Effect of Ball to Powder Ratios on the Phase Transformation of
.jpg)
Optimization of the high energy ballmilling: Modeling and
2016年4月1日 The results showed that the powder weight loss can greatly enhance the performance of milling, while the increase of the number of balls at high BPR ratio, has a quite I want to ball mill 60 gm of Al powder in steel jar with 10mm diameter ball size In my research it was 3mm ball dia, I am curious about the importance of the Ball to Powder Ratio How to calculate ball to powder ratio? ResearchGate2022年11月1日 In order to investigate the bonding behavior between reactive powder concrete (RPC) and normal strength concrete (NSC), splitting tensile test of 81 specimens and double shear test of 27 specimens Study on the bonding performance between reactive powder 2008年7月1日 For example, a lower balltopowder ratio results in less efficient grinding and longer grinding times (BeginColin et al, 2000) Planetary, attritor, and vibration mills are different types of (PDF) Parameters optimization in the planetary ball milling of
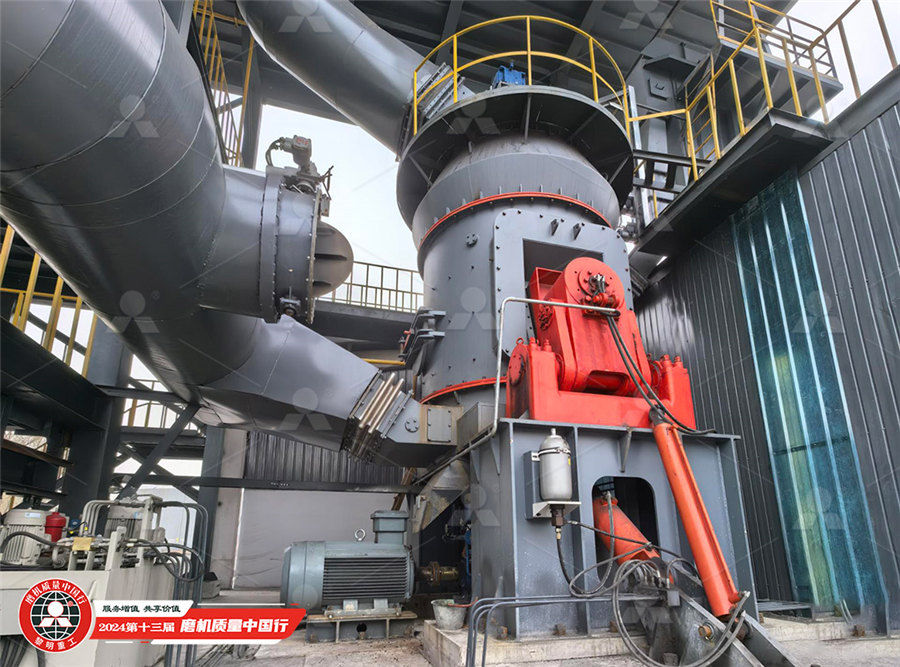
Study on the numerical simulation of laying powder for the
2019年10月26日 Because the selective laser melting (SLM) formation process involves rapid melting and solidification of slices, the SLM process places high demands on the tightness, uniformity, and flatness of the powder layer Based on the discrete element method (particle contact force model, particle collision judgment algorithm, and particle motion equation) and 2015年10月28日 As a significant case study in ceramic powder technology, the model is presented and validated for calcium fluoride (CaF2), ground under different conditions in a planetary mill, and then Modeling of the planetary ballmilling process: The case study 2015年12月10日 Highenergy mill (HEM) has a wide application in material preparation, activation and synthesis In the present study, fly ash was selected to be milled by HEM under the speed of 700 rpm and the balltopowder ratio of 10:1 by weight, but varied periods of milling time The changes in physical and morphology properties of the milled fly ash were determined Comparative study on the characteristics of ballmilled coal fly 2021年8月23日 Laser directed energy deposition (LDED) is a promising additive manufacturing technology based on the fused deposition of metal powder, but the low utilization rate of powder limits its commercial application The deposition process is very complex, and the correlation between physical properties of powder and performance of specimens manufactured has not Study on Recyclability of 316L Stainless Steel Powder by
.jpg)
(PDF) Effect of Ball to Powder Weight Ratio on the
2012年12月1日 Wet milling is considered more effective than salt assisted milling and dry milling (Peterson et al 2012) Increase in a ball to powder ratio decreases the particle size (Zakeri et al 2012) but 2023年10月27日 The ball mill is a rotating cylindrical vessel with grinding media inside, which is responsible for breaking the ore particles Grinding media play an important role in the comminution of mineral ores in these mills This work reviews the application of balls in mineral processing as a function of the materials used to manufacture them and the mass loss, as A Review of the Grinding Media in Ball Mills for Mineral Processing As for as ball to powder ratio is concerned, if the purpose is mixing you should go for 510 ration of ball with powder In case if you want to reduce the size or ally the powder then select high Best way to determine the balltopowder ratio in ballmilling?2023年4月28日 The primary goal of this work is to investigate the relationship between particle size and purity and ball milling parameters (milling speed, milling time, ball to powder ratio, and ball size) Changing a number of variables to see how affect the end result is what a parametric analysis of a fourstation ball mill for making ultrafine particles would entailParametric study on four station ball mill for synthesis of ultrafine
.jpg)
(PDF) Effects of balltopowder diameter ratio and
2021年12月1日 The effects of the balltopowder diameter ratio (BPDR) and the shape of the powder particles on EDEM simulation results and time in the planetary ball mill was investigated2024年6月25日 Whole grain flours often exhibit suboptimal processing properties and palatability, limiting their usage in food industry This study investigated the impact of ball milling on the physicochemical properties, thermal properties, crystalline structure and rheological properties of corn flour Ball milling reduced the particle size of the powder to the micron level Unlocking the Potential of Corn Flour: A Study on the 2023年6月25日 This study investigated the synthesis of AgSnO2ZnO by powder metallurgy methods and their subsequent electrical contact behavior The pieces of AgSnO2ZnO were prepared by ball milling and hot Powder Metallurgy: Materials and Processing ResearchGateJournal of Ceramic Processing Research Vol 23, No 6, pp 902~911 (2022) (Received 29 June 2022, Received in revised form 27 September 2022, Accepted 26 October 2022)Study on engineering strength properties of ceramic waste powder
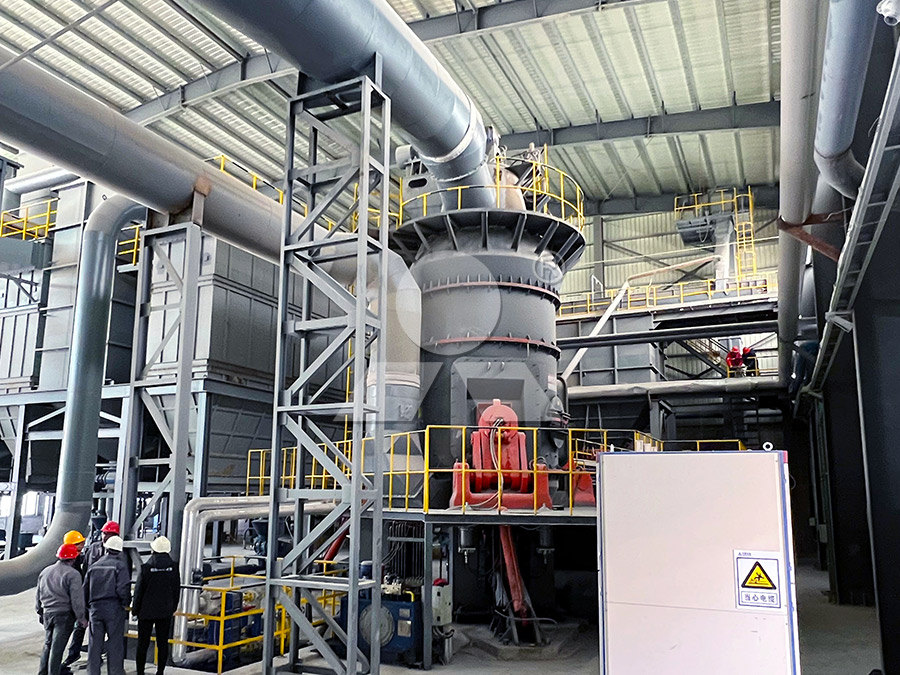
Comparative study on the characteristics of ballmilled coal fly
2015年12月10日 In the present study, fly ash was selected to be milled by HEM under the speed of 700 rpm and the balltopowder ratio of 10:1 by weight, but varied periods of milling time2021年1月1日 In this paper, the milling parameters of high energy ball mill (Fritsch Pulverisette 7) like vial geometry, number and size of balls and speed of the mill were modelled and discussedModelling of the HighEnergy Ball Milling Process2018年4月19日 The highenergy ball milling method was adopted to explore the influence of ball milling parameters, such as milling speed and additive amounts of process control agent (PCA) on tungsten powderEffect of Ball Milling Parameters on the Refinement of Tungsten Powder2015年4月22日 In the present research work, silicon nitride (Si3N4) and graphite (Gr) ceramic powders are ball milled to obtain homogeneous mixing and consistent density of combined powder The ballmilled On the Use of Ball Milling for the Production of Ceramic Powders
.jpg)
The ball to powder ratio (BPR) dependent morphology and
2018年7月1日 The nanocrystalline tungsten powder with the minimum grain size of around 5 nm was fabricated by mechanical alloying The powder refinement process and the influence of ball to powder ratio (BPR 2022年7月15日 The significant growth of Additive Manufacturing (AM), visible over the last ten years, has driven an increase in demand for small gradation metallic powders of a size lower than 100 µm(PDF) A Comparative Study on Laser Powder Bed Fusion of 2012年6月1日 The feed material is typically composed of the BFRs and the catalyst, both in powder form As the cylinder starts to rotate, the grinding balls inside the cylinder crush and grind the feed Grinding in Ball Mills: Modeling and Process Control2021年7月12日 With the conventional gas or water atomization process of synthesizing metallic powders, it is difficult to obtain graphite structure in a gray cast powder particle because of rapid cooling of the molten droplets In this work, a fabrication method of gray cast iron powder with graphite structure was proposed based on a structural transplantation route In the fabrication Effect of BalltoPowder Ratio on Morphology, Structure, and
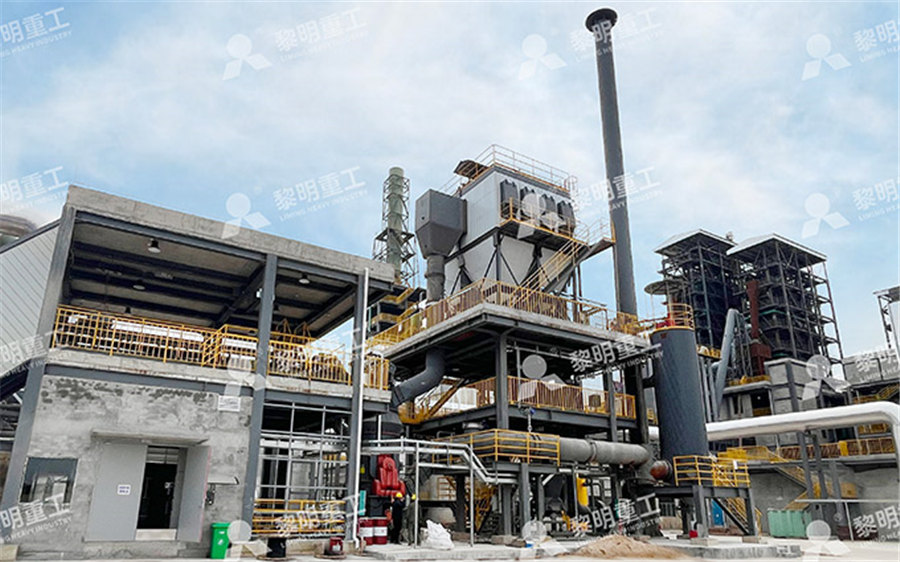
A study of nanocrystalline nickel powders developed via high
2019年6月1日 Minimum average particle size of 700 nm was achieve at a milling speed of 300 rpm and balltopowder ratio (BPR) of 15:1 while minimum Xray peak area ratio of 0080 was obtained at a milling 2023年6月1日 The aim of the present work is to study the behavior and strength of rehabilitation of composite columns that are made from concrete core and surrounded steel tubes under the effect of axial Experimental Study on Ultimate Strength of Steel Tube Column 2023年3月31日 Copper matrix composites exhibit excellent mechanical and thermal properties The composite consists of copper (Cu), zirconium (Zr), and boron (B) and is produced using the powder metallurgy technique The highenergy ball milling was applied for mechanical alloying of the CuZrB powder mixture to achieve the desired ratio for obtaining a copper matrix The Effect of BallPowder Ratio on The Mechanical and Structural 2014年9月17日 Major process variables involved in MA, such as milling time, milling speed, balltopowder weight ratio, and process control agent (PCA), are of high importance for the structure and morphology (PDF) Effect of milling parameters on mechanical ResearchGate
.jpg)
(PDF) Producing Metal Powder from Machining Chips Using Ball
2023年6月27日 Nevertheless, parameter factors, such as the type of ball milling, balltopowder ratio (BPR), rotation speed, grinding period, size and shape of the milling media, and process control agent (PCA 2021年1月1日 Depending on the grinding conditions (short grinding time, ball diameter, stainless steel ball and grinding powder ratio), the crystallite size decreased from 34 nm to 8 nmEffect of HighEnergy Vibrating Ball Milling in the Reduction of the 2020年9月9日 The present study involves the investigation on the effect of processing parameters of powder metallurgy on the microstructure and hardness characteristics of the green as well as sintered specimens of magnesium The processing parameters include the highenergy ball milling time, compaction pressure, and sintering temperature From SEM images of 1, 3, Studies on the Effect of Processing Parameters on Microstructure and 2023年11月23日 Kaolin is one of the most important clay minerals that attracts attention due to its various application areas such as the ceramic industry In this study, the effects of solid/ball ratio and grinding time on the mechanical activation of kaolin were investigated Samples with 10 µm particle size were activated in The Fritsch Pulverisette 5 Ball Mill (Two Chamber Mill) at Effect of solid/ball ratio and grinding time on the mechanical
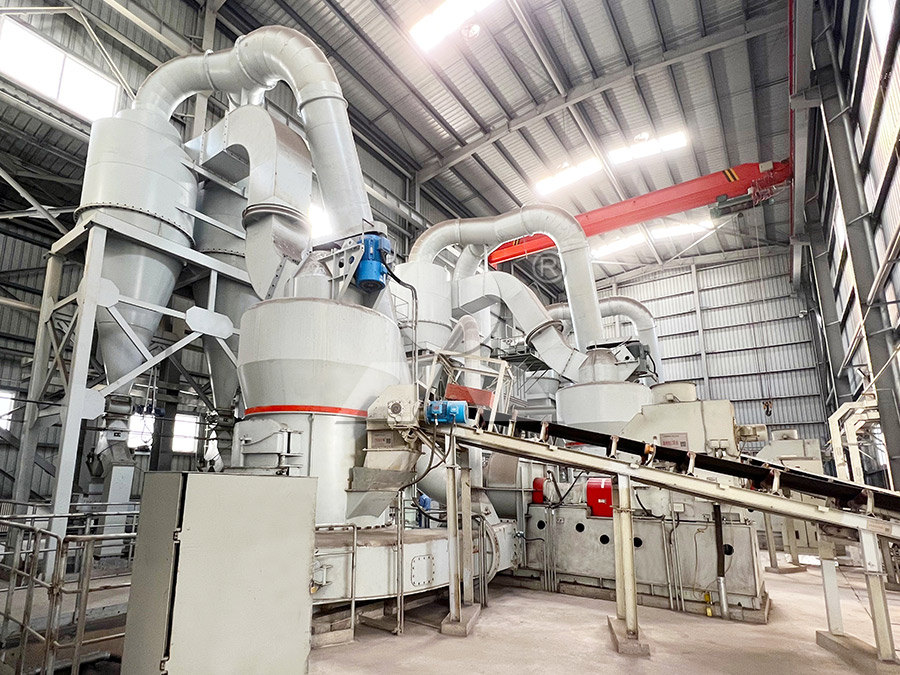
Effect of ball and feed particle size distribution on
2018年2月1日 In another study to investigate ball size distribution on ball mill efficiency by Hlabangana et al [50] using the attainable region technique on a silica ore by dry milling, a threeball mix of 2020年3月1日 In this study, M20 grade concrete with marble dust in 0%, 5%, 10%, 15% and 20% in proportion along with ratios of steel wires were used and tested for 7 28 days on mechanical parametersExperimental investigation on the effect of steel fiber embedded 2022年4月5日 Beef meatball (BM) is a traditional delicious snack with rich nutrition and unique flavor, making it a preferred choice for most consumers However, the quality of BM is easily affected by many An overview of factors affecting the quality of beef meatballs 2019年4月15日 The effects of processing parameters in ball milling and the different behaviors of CuNb and CuMo alloys during milling were investigated High powder yields can be obtained by changing the BPR (PDF) Effects of Ball Milling Processing Conditions and Alloy
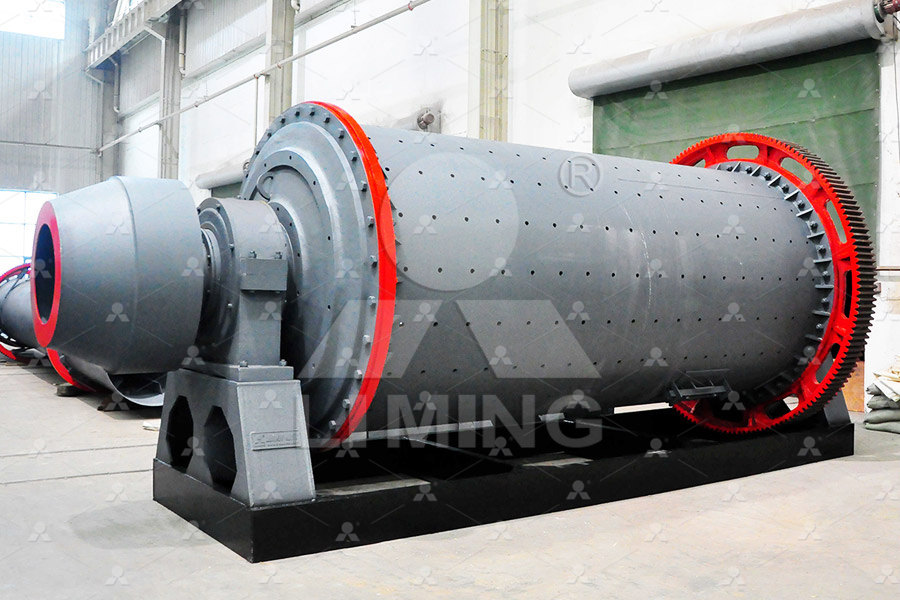
Why the ball to powder ratio (BPR) is insufficient for describing
DOI: 101016/JIJHYDENE201403009 Corpus ID: ; Why the ball to powder ratio (BPR) is insufficient for describing the mechanical ball milling process @article{Kuziora2014WhyTB, title={Why the ball to powder ratio (BPR) is insufficient for describing the mechanical ball milling process}, author={P Kuziora and Magdalena 2019年8月1日 The mechanosynthesis of hexagonal rhenium carbide (Re2C) from the elements is explored as a function of the balls to powder ratio (BPR) Burgios's equation has been used to calculate the Effect of ball to powder ratio on the mechanosynthesis of Re2C and 2020年11月16日 Ground iron and steel slag with excellent performance was prepared using the uniform test design The influence of the fineness and content of steel slag powder on the fluidity and strength of the powder mortar was studied, the regression equations of fluidity and compression strength of different ages are derived, and the contour map is drawn Based on Study on the Properties of HighPerformance Ground Iron and Steel 2020年7月30日 Significant progresses in materials science and engineering have developed a novel technology in which materials can be designed and engineered at nanoscale, socalled nanotechnologyNanomaterials through Powder Metallurgy: Production, Processing