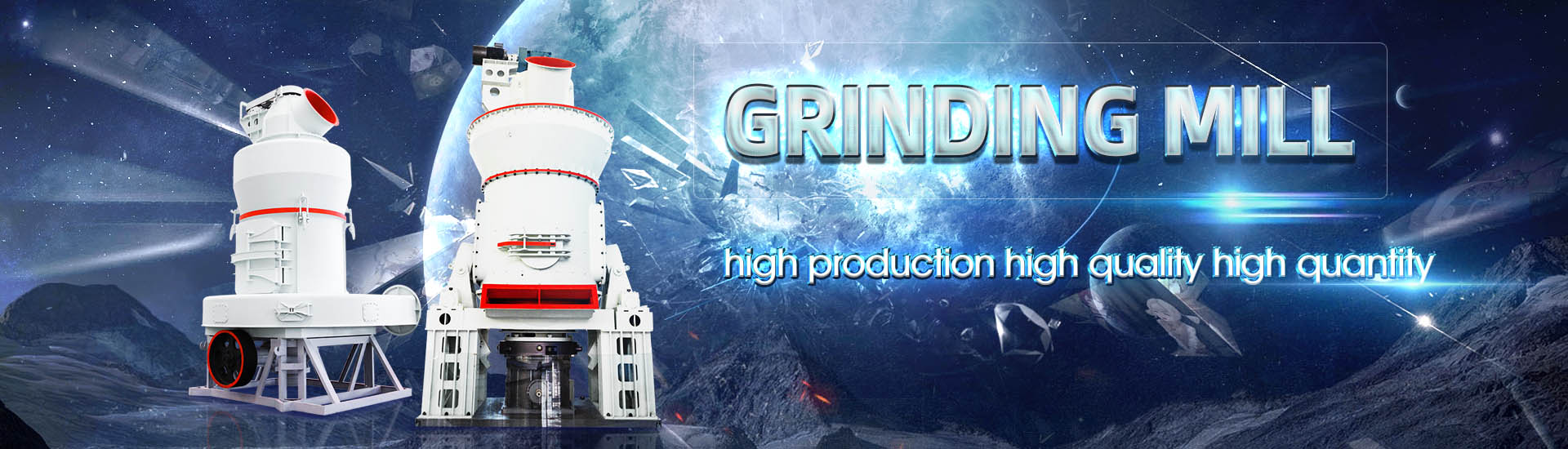
Ore powder factory production process
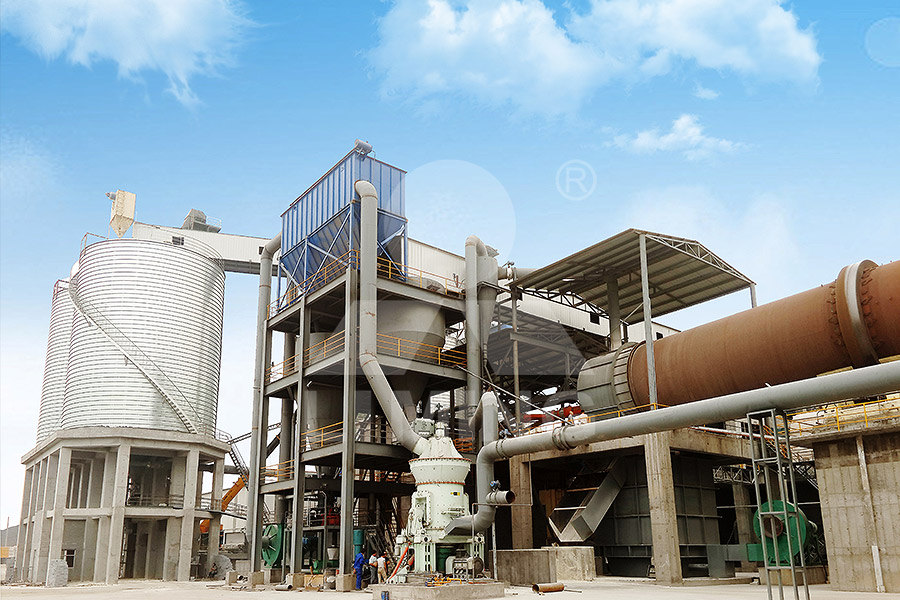
Making Metal Powder MPIF
In this process, molten metal is separated into small droplets and frozen rapidly before the drops come into contact with each other or with a solid surface Typically, a thin stream of molten metal is disintegrated by subjecting it to the impact of highenergy jets of gas or liquid In principle, the technique is applicable to 展开2020年7月13日 Oxide ores are generally processed using hydrometallurgy This process uses aqueous (waterbased) solutions to extract and purify copper from copper oxide ores at ordinary temperatures, usually in three steps: heap Copper Mining and Processing: Processing Copper OresMineral processing, art of treating crude ores and mineral products in order to separate the valuable minerals from the waste rock, or gangue It is the first process that most ores undergo after mining in order to provide a more Mineral processing Metallurgy, Crushing GrindingGranular copper powder can be produced by a number of methods, the most important being atomization, electrolysis, hydrometallurgy and solid state reduction Each method yields a Industrial: Powder Metallurgy Production and Properties
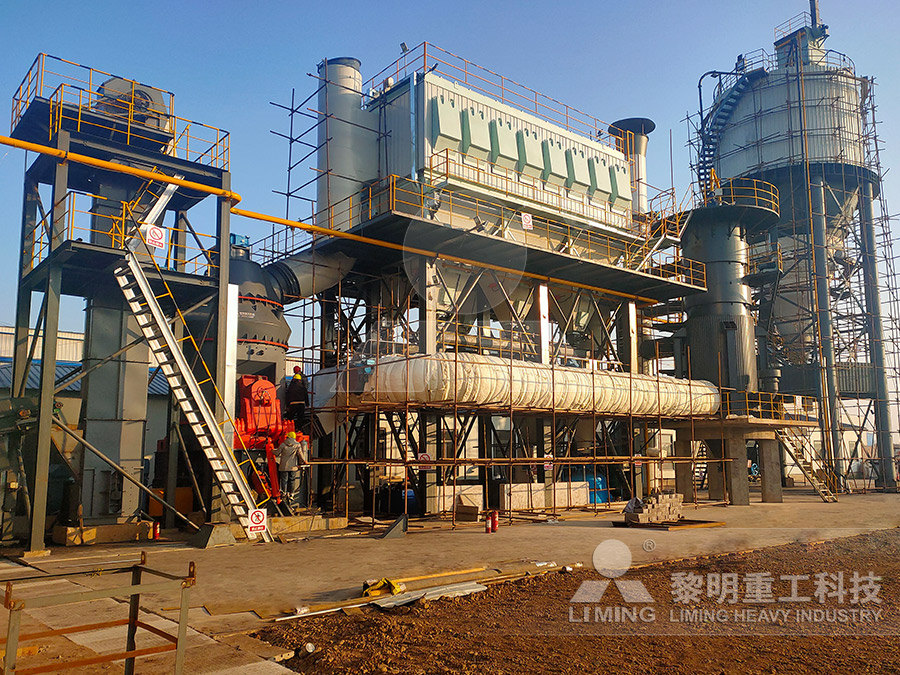
Powder Metallurgy – Powder Processes (Solid State Reduction
There are many ways in which metals may be produced in powder form, comminution of solid metal precipitation from solution of a salt; thermal decomposition of a chemical compound; Virtually all iron powders are produced by one of two processes The longest established of these processes is the sponge iron process, the leading example of a family of processes involving solid state reduction of an oxide In the Powder production technologies Powder Metallurgy Processing of Copper Ore The first step in processing the ore removed from the mine is to break the large rocks of ore into smaller pieces This is accomplished by a variety of subsequent From Ore to Finished Product Copper2021年12月16日 This review provides an overview of titanium resources, of which ilmenite is the main source, as well as it focuses on some effective methods for producing titanium powder through extractive metallurgy Titanium: An Overview of Resources and Production
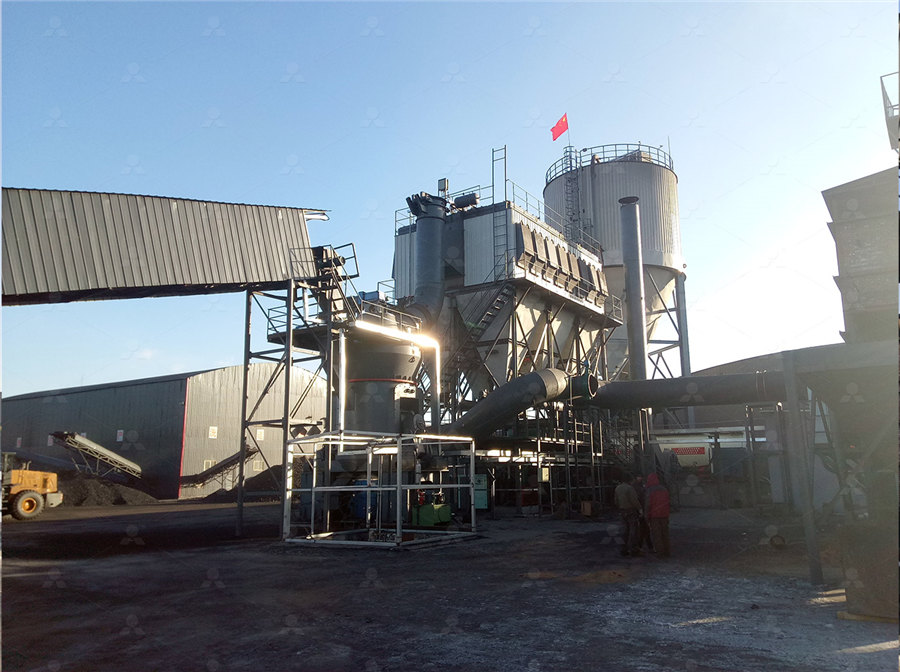
Copper Production: How Is Copper Made? ThoughtCo
2019年9月26日 Copper processing is a complex process that involves many steps as the manufacturer processes the ore from its raw, mined state into a purified form for use in many industries Copper is typically extracted from 2021年9月6日 A pulverization method for micronsized ore powder production by propulsion and rapid unloading of highpressure air is introduced This approach is different from the Micronsized ore powder production by propulsion and rapid 2013年3月16日 DRI production process The DRI production process involves the intimate mixing of prepared (sized) iron ore with a reductant, which is also generally used for heating of the ore bed to the temperature needed to Direct Reduced Iron and its Production Processes – 2021年12月16日 For several decades, the metallurgical industry and the research community worldwide have been challenged to develop energyefficient and lowcost titanium production processes The expensive and energy Titanium: An Overview of Resources and
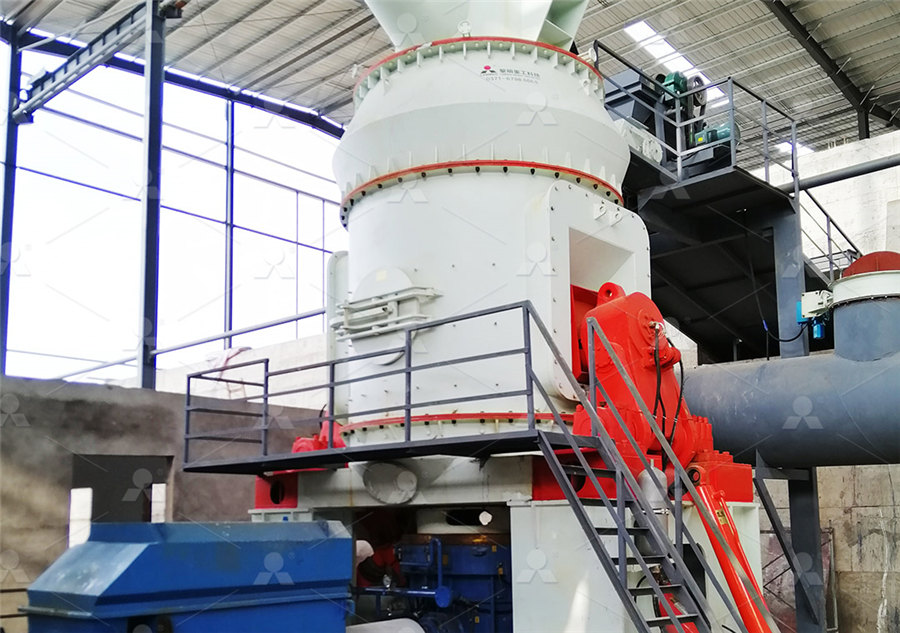
How Cement is Made Cement Manufacturing Process
Stage of Cement Manufacture There are six main stages of the cement manufacturing process Stage 1: Raw Material Extraction/Quarry The raw cement ingredients needed for cement production are limestone (calcium), sand and clay (silicon, aluminum, iron), shale, fly ash, mill scale, and bauxite The ore rocks are quarried and crushed into smaller pieces of about 6 inches2024年4月26日 Iron ore processing is a crucial step in the production of steel, one of the most essential materials in modern society Iron ore, a naturally occurring mineral composed primarily of iron oxides, is mined and processed to extract iron for various industrial applicationsIron Ore Processing: From Extraction to Manufacturing2023年3月15日 In this study, phosphate ore powder was used as raw material, and anhydrous calcium sulphate (CaSO 4) with P 2 O 5 and F − contents of only 001% and 003% was prepared by onestep acidification at atmospheric pressure through regulating the sulphuric acid concentration and reaction conditions Experimentally received: when the sulfuric acid Onestep wetprocess phosphoric acid byproduct CaSO4 and its 2017年7月20日 Ironmaking—From Ore to Iron The iron ore to steel process flowline can follow several different paths forging, extrusion, powder production or investment casting Steel Shaping and Electronic Design Solutions Electronic Test Equipment Electronics360 Environmental Technology Factory Engineering Fastening Technology and Processes Behind Steel Production GlobalSpec
.jpg)
Iron processing Definition, History, Steps, Uses, Facts
Iron processing, use of a smelting process to turn the ore into a form from which products can be fashioned Included in this article also is a discussion of the mining of iron and of its preparation for smelting Iron (Fe) is a relatively dense metal with a silvery white appearance and distinctiveThe Pelletizing Process The production of iron ore pellets from fines to finished product can differ based on a variety of factors As such, it’s important to note that the process described here is a generalized approach subject to many variations In general, three primary phases occur in iron ore pelletizing: Mixing/PreconditioningIron Ore Pelletization FEECO International IncSteel production resources available to view: Steel Wheel, Where Steel Is Made, How Steel Is iron ore and limestone to produce pig iron Coal traditionally has been a key part of the cokemaking process The coal is crushed and ground into a powder and then charged into an oven where it is heated to approximately 1800°F in the absence of Steel Production American Iron and Steel Institutethe 19th century, is by far the most important process used in the production of aluminum oxide from bauxite The process has been refined and improved since its inception Fig 22 shows that the production of alumina is a complex chemical process The alumina content of bauxite ores varies from one deposit to another, and methods of treatChapter 2 Production and Processing of Aluminum The

Ore processing (Mekanism) Official Feed The Beast Wiki
Mekanism provides 4 tiers of systems to process ores and obtain two to five ingots from 1 ore The complexity of the systems rises with each tier and at the higher tiers various secondary machines are required to produce consumables for the main ore processing line The following page shows the layout of these systems as well as some ingame pictures and descriptions 2024年5月13日 Steel production techniques span a broad spectrum of methods tailored to meet diverse production needs and accommodate varying resource availability Integrated steelmaking, a comprehensive process that melds raw Steel Manufacturing: Process, Types, and Standards2022年3月21日 Significant academic research and moderate commercial process innovation on rareearth element (REE) processing have been underway for decades The last several years have seen exponential growth in research due to growth in demand of REE that is threatened by supply risks and environmental obstacles The REE industry appears to be at the intersection Processing the ores of rareearth elements MRS Bulletin2024年6月13日 The third stage: ore dressing – mixed flotation process The copper ore powder that meets the requirements is fed into the flotation machine for mixed flotation The copper ore powder after flotation is fed into the dryer for drying, and finally, copper concentrate is obtained Copper Ore Crushing EquipmentCopper Introduction And Ore Crushing JXSC Mineral
.jpg)
Gold Smelting Refining Process 911Metallurgist
2016年2月29日 Intensive cyanidation is a good option, but obviously, the material can be sent to the leaching process employed to treat the raw ore Gold and silver recoveries are between 995 to 997% Although slag production weight is variable, a typical operation can generate 10 kilos of slag per 1000 oz of goldIn the steel industry, the raw material for steel production is iron ore And in the first stage of the production process for this material, iron ore is agglomerated using lime and coke fines At the end of this step, the resulting product is called sinter The charcoal used is processed in the coke oven plant and transformed into cokeSteel production process: what are the steps? Blog IndustriALLEach step of the cement production process is carefully monitored to ensure efficiency and quality Grinding, Mixing, and Blending The rock fragments are finely ground and combined with other ingredients including clay, chalk, marl, shale, slate, sand, and iron oreHow Cement is Made Portland Cement AssociationFerrosilicon is manufactured through a process called carbothermic reduction Here’s a simplified overview of the manufacturing process: Raw Material Preparation: Silicon dioxide (quartz or silica) is crushed and sized Carbon materials (coal, coke, or charcoal) are prepared Iron ore or scrap iron is added as the iron source Furnace Charging:What Is Ferro Silicon Production Process?
.jpg)
Copper Mining and Processing: Processing Copper Ores
Copper processing is a complicated process that begins with mining of the ore (less than 1% copper) and ends with sheets of 9999% pure copper called cathodes, which will ultimately be made into products for everyday useThe most common types of ore, copper oxide and copper sulfide, undergo two different processes, hydrometallurgy and pyrometallurgy, respectively, 14 Production Process 5 20 Key Performance Indicators of Direct Reduction of Iron Process 9 21 Capacity Utilization 10 22 Yield 10 37 Switch Over to Iron Ore Pellets 27 38 Artificial Neural Network for Accretion Control 28 39 Moisture Reduction from Coal 29 310 Energyefficient Motors 30ENERGYEFFICIENT TECHNOLOGY OPTIONS FOR DIRECT REDUCTION OF IRON PROCESS2021年11月5日 Today, Metso Outotec can offer processes and equipment that cover the full gold value stream from ore to dore This includes all three main oxidative processes for the treatment of refractory gold concentrates – BIOX, From ore to dore: Four main processes in gold 2014年11月26日 Iron Ore Pellets and Pelletization Process satyendra; November 26, 2014; 0 Comments ; bentonite, binder, Grate kiln, induration, Pelletization Pellets, straight grate,; Iron Ore Pellets and Pelletization Process Pelletizing of iron ore was started in the 1950s to facilitate the utilization of finely ground iron ore concentrates in steel productionIron Ore Pellets and Pelletization Process IspatGuru
.jpg)
Research progress in the preparation of iron by electrochemical
2023年3月14日 For decades, the steel production industry has been one of the largest sources of CO2 emissions, accounting for 7% of global CO2 emissions, of which 70% is emitted in the ironmaking process Currently, the main lowcarbon iron production route is hydrogen metallurgy, which uses renewable energy to generate electricity, electrolyze water to produce hydrogen, In the Blast Furnaces, we melt iron ore into liquid iron at high temperatures Iron ore has a sandlike structure that can put out the fire in the furnace Because of that, you can't put it in the furnace just like that The ore is first baked to make it into porous Process of steelmaking Tata SteelWhile looking up youtube videos and flowcharts on setting up the 5x ore process, I'm playing Sky Factory 4 now and what I have been using is Mekanism's gasburning generators running on ethylene (which also makes Hydrogen to send to your Ethylene production for power gen), to Crusher, to Enrichment chamber to Energized 5x Ore Process Flowchart for Mekanism Mod : r/feedthebeast2020年1月1日 Other process for producing intermediate grades of titanium dioxide from ilmenite includes the Murso process, which involves hightemperature oxidative roasting (900–950°C), hydrogen gas for reduction, and leaching in 20% hydrochloric acid to remove iron [6] The Laporte and Benelite processes are very similar to the Murso process [7], [8]A brief introduction to production of titanium dioxide and
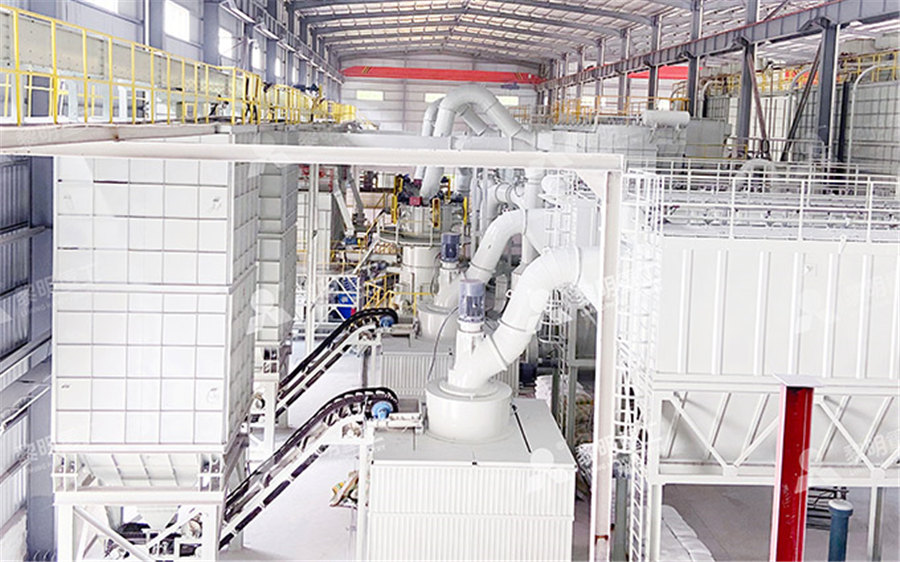
Talcum Powder Production Process
2023年9月6日 Talcum powder, also known as talc powder or baby powder, is a cosmetic product made from talc, a mineral composed mainly of magnesium, silicon, and oxygenIt is widely used for its absorbent and lubricating properties and has various applications in personal care and hygiene The production process of talcum powder involves several steps, including 2023年4月5日 The blast furnace and direct reduction processes have been the major iron production routes for various iron ores (ie goethite, hematite, magnetite, maghemite, siderite, etc) in the past few decades, but the challenges of maintaining the iron and steelmaking processes are enormous The challenges, such as cumbersome production routes, scarcity of Recent Trends in the Technologies of the Direct Reduction and Since aluminum is 100 percent recyclable, the manufacturing process doesn’t end once it reaches the consumer Many recyclable aluminum products undergo a secondary production process Secondary production is the process of turning scrap into aluminum that can be used again in the manufacturing of another productAluminum Processing Production Explained HARBORThen you can take the most important step – copper ore granulation Here are three types of granulator that are recommended to you When you only start a small scale copper ore granulation, it is advisable to buy pan pelletizer, whose capacity is 16 t/hHowever, for large scale copper ore pellets making, drum granulator is the most suitable oneCopper Ore Pellets Production Line Process of Making Pellets
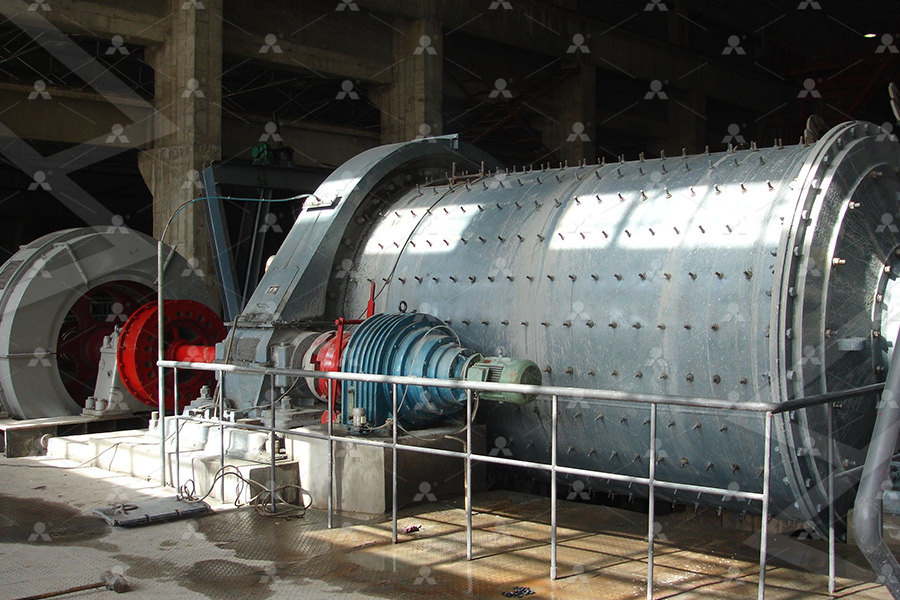
Nickel processing Extraction, Refining, Alloying
Nickel processing Extraction, Refining, Alloying: The extraction of nickel from ore follows much the same route as copper, and indeed, in a number of cases, similar processes and equipment are used The major differences in 2024年5月30日 Quartz Crushing Jaw crushers are the ideal choice for primary crushing of quartz ore, effectively breaking down the highhardness mineral Subsequently, cone crushers (or impact crushers) further reduce the quartz to Quartz Processing Mastering the Art of Stone to 2019年1月1日 World production of DRI Table 2 summarizes the world production of DRI from the year 2010 to 2017 as recorded by World Steel Association Production of DRI has increased from 72 Mt in 2010 to 863 Mt in 2017, accounting for 7% of the total iron ore production in 2017 (World Steel Association, 2018)A review of ironmaking by direct reduction processes: Quality In parallel, integrating digital technologies, such as realtime data analytics and sensorbased sorting, optimizes ore processing, yielding dramatic efficiency improvements in gold processing innovation Electrification of mining fleets; Realtime data and analytics for process optimization; Advances in ore sorting and preconcentration techniquesUnderstanding Gold Processing Techniques MINERALS BASE
.jpg)
A Guide To Copper Production and Manufacturing Process
2022年12月23日 Copper production and manufacturing can be mysterious to those unfamiliar with the industry From mining to the finished product, there are many steps involved in producing copper Let’s take a look at how it’s done Copper production process Copper production begins with acquiring raw materials like ore, concentrate, or mattethe iron ore fines, which are difficult to process in their initial form, in a preplaced powder bed to make the pellet production route more sustainable and wastefree Additionally, the laser processing of the materials was carried out in a manner partially similar to the laser powder bed fusion (LPBF) process, where theLaserassisted reduction of iron ore using aluminum powder DiVABall or rod mills crush and grind the mined ore to fine particles, releasing molybdenite from the gangue (worthless rock) The grinding mills shown here reduce rocks from the size of soccer balls to the size of gravel Further ball milling reduces the material to the consistency of face powderMolybdenum ProcessingAccording to the USGS, US (synthetic) graphite production in 2006 was 132,000 tonnes valued at $495 million and in 2005 was 146,000 tonnes valued at $391 million, and highmodulus graphite (carbon) fiber production in 2006 was 8,160 tonnes valued at $172 million and in 2005 was 7,020 tonnes valued at $134 million 2 Modern ManufactureOpen Knowledge Wiki Manufacturing and Production of
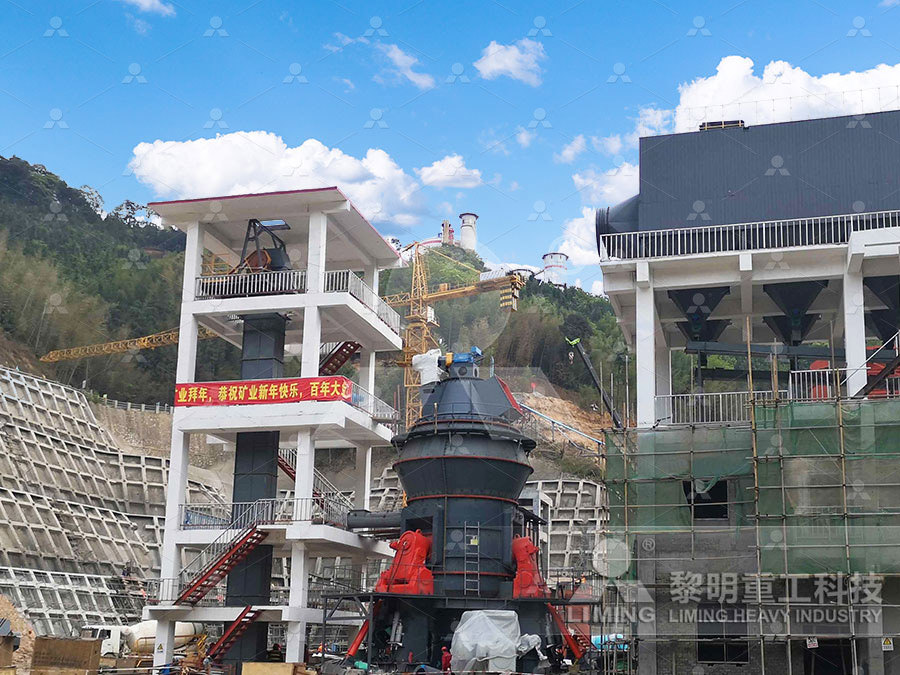
From Ore to Iron with Smelting and Direct Iron Reduction
2017年10月17日 Figure 1: Steelmaking byproducts for blast furnace (BF), basic oxygen furnace (BOF) and electric arc furnace (EAF) processes Source: World Steel Association (worldsteel) The first step in the production of steel or cast iron alloys is the reduction of iron ore—which contains iron oxide and gangue or mineral impurities—to unrefined, reduced iron form2023年5月6日 The production process of copper ore processing mainly includes crushing, ore grinding, flotation, purification, and drying Skip to content JXSC Mineral Home; Here also need to use auxiliary equipment – a classifier, which can classify and screen the copper ore and release the copper ore powder that meets the requirementsCopper Ore Production Process JXSC Mineral