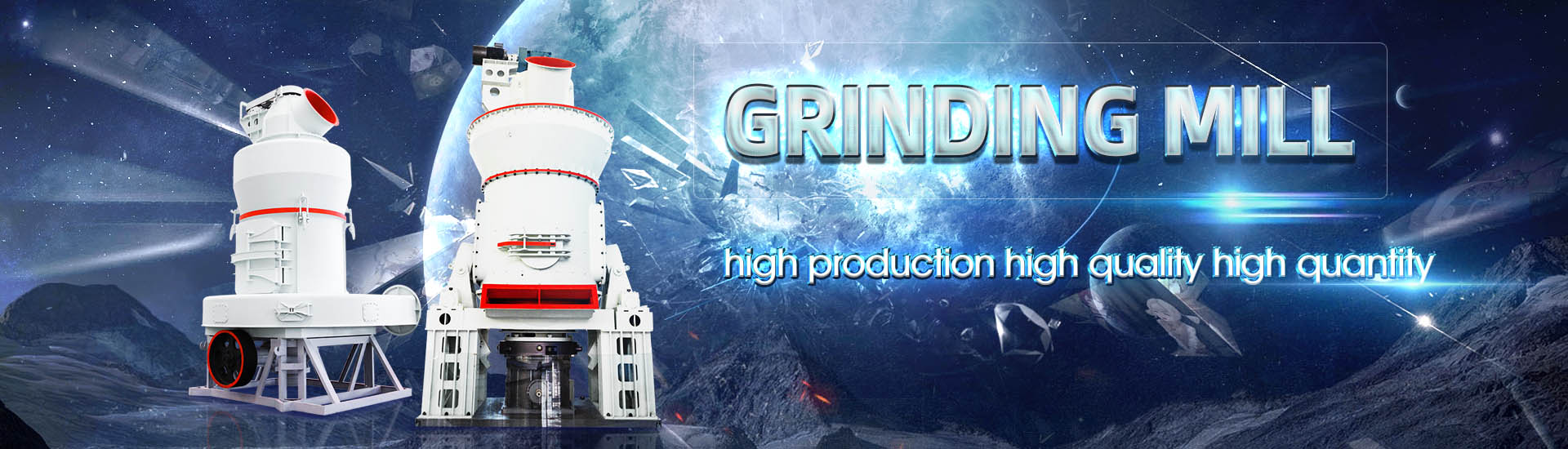
How to separate coke from slag

233: Metallurgy of Iron and Steel Chemistry LibreTexts
As the ore, lime, and coke drop into the furnace (Figure \(\PageIndex{1}\)), any silicate minerals in the ore react with the lime to produce a lowmelting mixture of calcium silicates called slag, which floats on top of the molten iron Molten iron 2024年6月15日 The extended contact duration between coke and slag at the slag liquid level exceeds that at the tuyere level This prolonged interaction allows slag ample time to permeate Physical and chemical properties of metallurgical coke and its 2022年9月25日 In this study, a variety of methods for extracting and separating copper and iron from CSS are reported The extraction and separation technologies include physical methods Extraction and separation of copper and iron from copper The calcium oxide then reacts with silica (sand) impurities in the haematite, to produce slag – which is calcium silicate This is separated from the iron and used to make road surfaces calciumRedox, extraction of iron and transition metals
.jpg)
Generation of iron and steel slag : NIPPON SLAG
During the process of reducing iron ore, it is necessary to remove the silica, alumina (Al 2 O 3), and other nonferrous components contained in iron ore The added limestone fuses with these components and lowers their melting point, 2024年2月29日 To confirm the feasibility of the carbothermic reduction of copper slag at high temperatures, the possible reduction reactions of oxides in copper slag with solid carbon, as Recovery of Metals from Copper Smelting Slag Using Coke and 2020年1月25日 In the study, synthetic leadrich slag is molten on a smallscale bed of metallurgical coke, inside a vertical tube furnace The mechanism of reduction as well as the Reduction of LeadRich Slags with Coke in the Lead Blast FurnaceIn pyrometallurgy, an ore is heated with a reductant to obtain the metal Theoretically, it should be possible to obtain virtually any metal from its ore by using coke, an inexpensive form of crude carbon, as the reductant An 233 Metallurgy Pages
.jpg)
SlagForming in Blast Furnace Ironmaking SpringerLink
2023年6月10日 Liquid blast furnace slag is required to be of well flowing to ensure good separation of slag and iron The formation process of blast furnace slag is mainly divided into 2018年1月11日 The submerged electric arc furnace (SAF) has proven a versatile unit in numerous metallurgical applications for more than a century Countless innovations have made this furnace type become the most The Submerged Arc Furnace (SAF): StateoftheArt 2023年5月24日 Copper slag flotation offers a viable approach for recovering valuable copper from this industrial byproduct By carefully considering factors such as particle size, pH, reagents, temperature, agitation, and froth How to Optimize Copper Slag Flotation for Maximum 2017年6月28日 There are two aspects to this, firstly is actually reducing the pure metal from its oxides, usually called smelting, most metal ores are metal oxides so this is clearly an important part of primary metal production For example in iron production iron oxides are reduced by carbon, usually from coke which is also the fuel which provides the energy for the reactionHow do manufacturer remove oxygen from metal during melting?
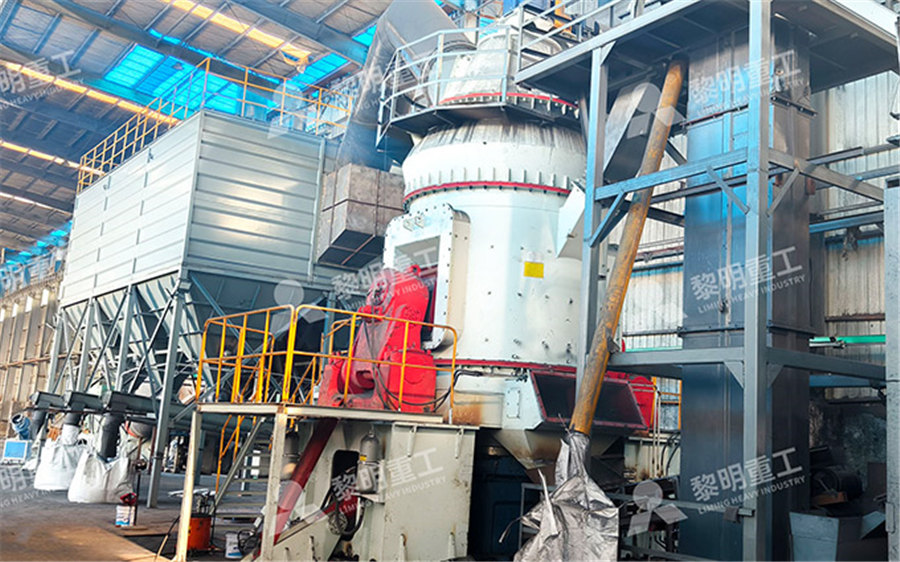
Treatments and Recycling of Metallurgical Slags IntechOpen
2018年11月7日 Steelmaking plants continuously strive to reduce the environmental load in the steelmaking process, resulting in the recycling of energy, water, and other byproducts In this chapter, techniques for the treatment and recycling of metallurgical slags are described Metallurgical slags are considered secondary raw materials and are used or added during the The common ores of iron are both iron oxides, and these can be reduced to iron by heating them with carbon in the form of coke Coke is produced by heating coal in the absence of air Coke is cheap and provides both the reducing agent for the reaction and also the Iron Extraction and Purification / Steel ChemKey2013年8月7日 As all of the minerals melt down, they separate from one another As the process continues, the borax causes the other minerals to oxidize and breakdown even further Gold is unaffected by this reaction and sinks to the bottom of the mixture, intact The mixture of oxidized impurities and flux becomes slag, Using Borax Flux to Refine Gold Manhattan Gold Silver2021年5月13日 22 Computations In this section, the final BF slag compositions formed from different kinds of charge materials are compared Typical slag compositions [15, 16, 19] as well as compositions after replacements are shown in Table 2CaO and MgO are the basic constituents of the slag, whereas SiO 2 and Al 2 O 3 are the acid constituents [] Slag formed from coke ash Effect of Coal and Coke Ash on Blast Furnace Slag Properties: A
.jpg)
Development of onestep process method to separate tin from tin
2023年6月1日 At present, several tin metallurgical enterprises and research institutions have developed and applied various methods, including diaphragm electrolysis, flotation, oxidation roastingacid leaching, and direct chlorination, for treating sulfur slag according to the physical and chemical properties of sulfur slag [12]In the diaphragm electrolysis method, the tin and 2023年3月1日 Steel slag is a byproduct of the steelmaking process In fact, each ton of steel produces 110–150 kg of steel slag China's steel slag reserves are more than 300 million tons, and the annual hoard continues to increase [1]Due to the different steel composition, scattered varieties of converter slag and complex composition exist, which seriously limits the Chinese Efficient separation of iron elements from steel slag based on 2017年3月22日 The stirring takes 5–15 min after which the impellor is lifted again and the bath is allowed to rest for another 5–10 min This is necessary because the slag and the formed CaS need time to ascend to the top After this the slag layer is skimmed off, which takes 10–15 min Citation 2, Citation 16, Citation 28, Citation 31 (Fig 8)Sulphur removal in ironmaking and oxygen steelmaking2020年1月1日 The solids are allowed to settle, and the liquid portion decanted, then the solution is concentrated by evaporation, and then chilled under vacuum to precipitate ferrous iron as light green byproduct ferrous sulfate heptahydrate The removal of iron is critical to the final color of the titanium dioxide, which is otherwise tainted by residual dissolved that remains in the final A brief introduction to production of titanium dioxide and titanium
.jpg)
(PDF) Industrial uses of slag The use and reuse of
2005年2月1日 The importance of understanding slags, their reusability, their specific roles and improvements in functions to lead a significant reduction in slag volumes in iron and steel industry is discussed2021年1月4日 In this study, hydrometallurgical processes involving pressure acid leaching and solvent extraction were developed to aid recovery of indium from zinc slag, which is produced in the imperial smelting process Four different acid leaching methods were studied, namely atmospheric leaching, atmospheric leaching with KMnO4, roastingatmospheric leaching, and Recovery of Indium from Hard Zinc Slag by Pressure Leaching and 2024年2月15日 The problem of steel slag could be solved by expanding the utilization ways of steel slag At present, steel slag has been used in the production of cement, the construction of urban roads and the production of fertilizer (Fronek et al, 2012; Jiang et al, 2018b; Shi and Qian, 2000; Wang and Cai, 2006)In developed countries, the utilization rate of steel slag is close to Vanadium extraction from steel slag: Generation, recycling and 2016年2月29日 Once the slag is cool, this can be separate from lead and precious metals by using a hammer or any device than can break the slag The metallic product is named button and have to be processed in the other smelting process called cupellation By this second stage, Gold Smelting Refining Process 911Metallurgist
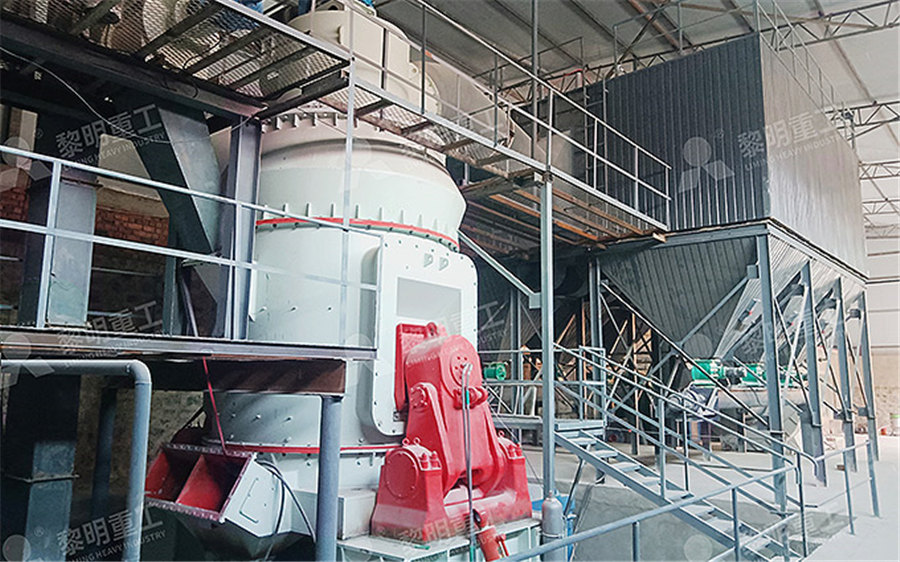
Blast Furnace Ironmaking SpringerLink
2023年10月6日 The smelting process of blast furnace is carried out in the shaft furnace of a closed countercurrent reactor and heat exchanger The complex physical changes and chemical reactions are completed in the process of the countercurrent movement of the charge and gas in which the raw materials containing iron oxide (sinter, pellets, etc), coke, slag flux (limestone) The ore is loaded into a blast furnace along with measured quantities of coke and limestone Hot combustion air is supplied to the furnace and some form of fuel used to raise the temperature The iron is reduced from the ore by carbon in the coke, the limestone aiding slag separation from the molten iron The slag and molten iron are tapped off from the bottom of the furnace, the Iron Ore Smelting Process Bright Hub Engineering2013年4月1日 A considerable amount of waste slag from the pyrite roasting process is produced every year Recovery of iron from the waste slag is of great interest for maximum use of mineral resource (PDF) Recovery of iron from waste slag of pyrite ResearchGate2020年7月1日 The chlorination of slag started above 300 °C, and the temperature shifted to approximately 200 °C in the cases where carbon and chlorine coexisted 2 Fe in the slag was almost completely volatilized by chlorination up to 1000 Separation of valuable elements from steel making slag by chlorination
.jpg)
Characterization and Recovery of Copper from Converter Copper Slag
2018年8月1日 Converter copper slag can be viewed as an important secondary resource for valuable metals, considering its high commercial value The current research investigates the recycling of copper by a combination of theoretical and experimental methods Based on a modified Stokes equation, it was determined that copper droplets in the molten slag exhibited 2019年7月15日 Maximum purities were obtained at 150–165 g cm −3 for inertinite, 172–178 g cm −3 for isotropic coke, and 188–195 g cm −3 for anisotropic coke The gravity separation had been used to separate unburned carbon from the coarse fraction (+100 mesh) of fly ash and the carbon recoveries of three samples were >80% [31]Separation of unburned carbon from coal fly ash: A reviewMany studies have been carried out using ore dressing to separate the manganese oxides from the ore The separation of manganese impurities by magnetizing roasting followed by lowintensity magnetic separation is not Silicomanganese alloy from rich manganese slag A blast furnace is charged with iron ore, charcoal or coke (coke is charcoal made from coal) and limestone (CaCO 3 ) Huge quantities of air blast in at the bottom of the furnace, and the calcium in the limestone combines with the silicates to How Iron and Steel Work HowStuffWorks
.jpg)
Effect of Coal and Coke Ash on Blast Furnace Slag Properties: A
2021年5月1日 However, the coke properties of the coke sample with added woody biomass could be improved by removing the partly volatile matter of woody biomass before mixing with caking coal, and as a result Slag and coke under two electrodes but mainly slag under the third electrode were reported [24] Another study [27] Isozaki et al (2002) proposed a method to separate and recover iron and zinc from EAF exhaust gases using a coke bed filter and a zinc condenser to prevent the formation of the dust, Slag Separation an overview ScienceDirect Topics2024年2月3日 Fine slag (FS) is an unavoidable byproduct of coal gasification FS, which is a simple heap of solid waste left in the open air, easily causes environmental pollution and has a low resource utilization rate, thereby restricting the development of energysaving coal gasification technologies The multiscale analysis of FS performed in this study indicates typical grain size Multiscale analysis of fine slag from pulverized coal gasification in The now closed Doe Run primary lead smelting facility in Herculaneum, Missouri Plants for the production of lead are generally referred to as lead smeltersPrimary lead production [clarification needed] begins with sinteringConcentrated lead ore is fed into a sintering machine with iron, silica, limestone fluxes, coke, soda ash, pyrite, zinc, caustics or pollution control particulatesLead smelting Wikipedia
.jpg)
Reduction of LeadRich Slags with Coke in the Lead Blast Furnace
2020年1月25日 Several studies on lead blast furnaces, using sinter as feed, indicate that the majority of reduction reactions occur in the region where the temperature exceeds 800 °C, labelled “melting zone” in Fig 1, since feed material starts to melt there [3,4,5,6,7,8,9]This illustrates the importance of reactions between liquid slags, rich in PbO, and metallurgical coke2024年1月1日 Copper slag (CS) is a solid waste produced during copper smelting, mainly containing 30–––40 % Fe, 174–448 % Zn, and other trace amount metal elements (Shibayama et al, 2010, Gümüşsoy and Başyi̇ği̇t, M, Uzun Kart, E, , 2023)It is reported that China currently produces over 60 million tons of CS annually and possesses a stockpile of 130 million tons of Twostage method recovery of metals from copper slag: Realize Copper can be extracted from nonsulfide ores by a different process involving three separate stages: Reaction of the ore (over quite a long time and on a huge scale) with a dilute acid such as dilute sulfuric acid to produce a very dilute copper(II) sulfate solution Concentration of the copper(II) sulfate solution by solvent extractionThe Extraction of Copper Chemistry LibreTextsanorthite The intensity of the peak at 700ºC for the slag is lower than fly ash, which can explained by the finer particle size of the fly ash 10 0 10 20 30 40 50 60 70 200 400 600 800 1000 1200 1400 TºC µV FA SL Fig2 DTA traces of IGCC Fly ash ( )and IGCC Slag( ) The expanding capacity of the ELCOGAS fly ash and slag was followed by Production of Lightweight Aggregates from Coal Gasification
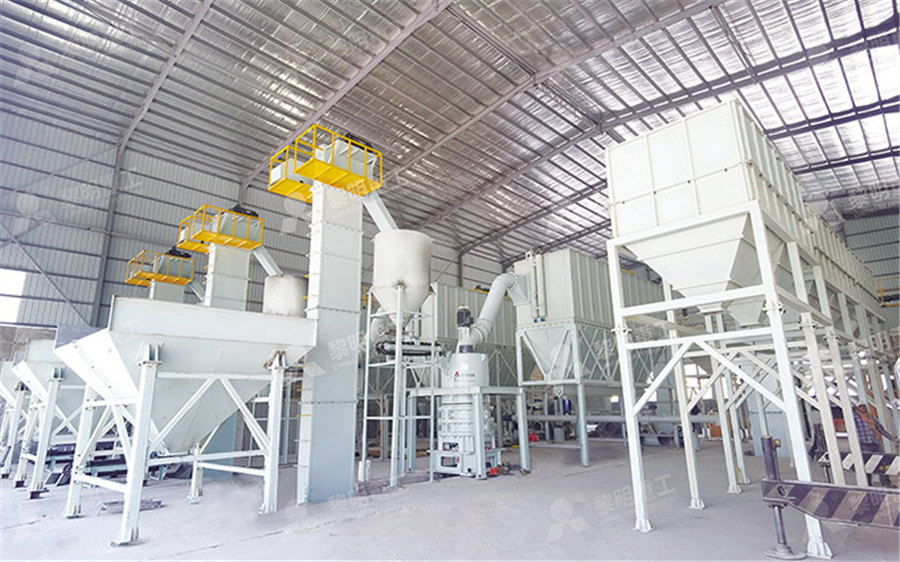
What is Smelting Difference, Process, And Uses
2023年11月30日 Common fuel sources include coal, coke, natural gas, and electricity Energy Input: The fuel source provides the energy required to heat the furnace to the necessary smelting temperature 3 Reducing Agent Role in The common ores of iron are both iron oxides, and these can be reduced to iron by heating them with carbon in the form of coke Coke is produced by heating coal in the absence of air Coke is cheap and provides both the reducing IRON AND STEEL chemguide2019年7月1日 Around 20 million tons of slag is produced annually in Europe, half of which is produced is BOS slag (Liu et al, 2016), meaning that large quantities of industrial byproducts are produced each yearOne obvious alternative to landfilling such byproducts would be to reutilize the slag in steelmaking or use for secondary applications (Joulazadeh and Joulazadeh, 2010)The recycling and reuse of steelmaking slags — A review2019年6月1日 The reduction of leadrich slag with metallurgical coke is one of the major reactions in the dripping zone of the lead blast furnace However, because the conditions of this zone are hard to SlagCoke Interactions in the Lead Blast Furnace ResearchGate
.jpg)
232: Principles of Extractive Metallurgy Chemistry LibreTexts
Originally, charcoal was used, but industrialscale smelting uses coke, a crude form of carbon prepared by pyrolysis (heating) of coal The basic reactions are Smelting separates the material to separate into 2 layers (copper matte: bottom layer containing molten sulfides of Fe and Cu and silicate slag: top layer formed by reaction of Abstract The state of the art for the recovery of metals from steel industry byproducts using hydrometallurgical processes is reviewed The steel byproducts are different slags, dusts, and sludges from a blast furnace (BF), basic oxygen furnace (BOF), electric arc furnace (EAF), and sinter plant, as well as oily mill scale and pickling sludge The review highlights that dusts and Hydrometallurgical Processes for the Recovery of Metals from 2013年11月14日 In the study, the waste slag was first crushed to a particle size of 150–203 μm in diameter by a jaw, hammer and pulverizer Then, the crushed waste slag was mixed with petroleum coke crushed to 150–203 μm in diameter as a reducing agent At the same time, the crushed waste slag was uniformly mixed with the coke using a VmixerA physicochemical separation process for upgrading iron Blast furnace slag is a combination of silica and other nonferrous components of iron ore, ash from coke used as a reducing material, and limestone auxiliary material Because its specific gravity is less than that of pig iron, during the heating process the molten slag rises above the pig iron allowing it to be easily separated and recoveredGeneration of iron and steel slag : NIPPON SLAG ASSOCIATION
.jpg)
Using a DirectCurrent Arc Furnace to Recover Cobalt from Slags
tity of iron as oxide in the slag NiCu SLAG CLEANING Many nickelcopper smelters employ a slagcleaning process whereby the concentrates are fed to a furnace that produces a matte (for further treatment) and a slag (which is stockpiled) The furnace matte is treated in a converter (often a PeirceSmith) to remove most of the remaining iron