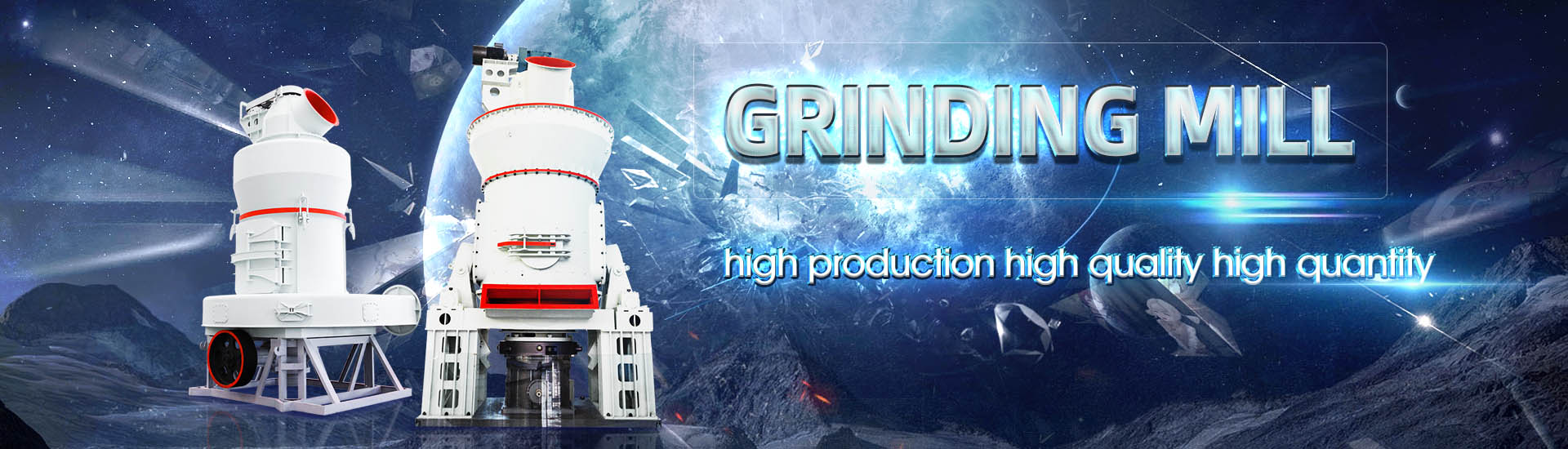
Coal mill separator replacement and lifting plan
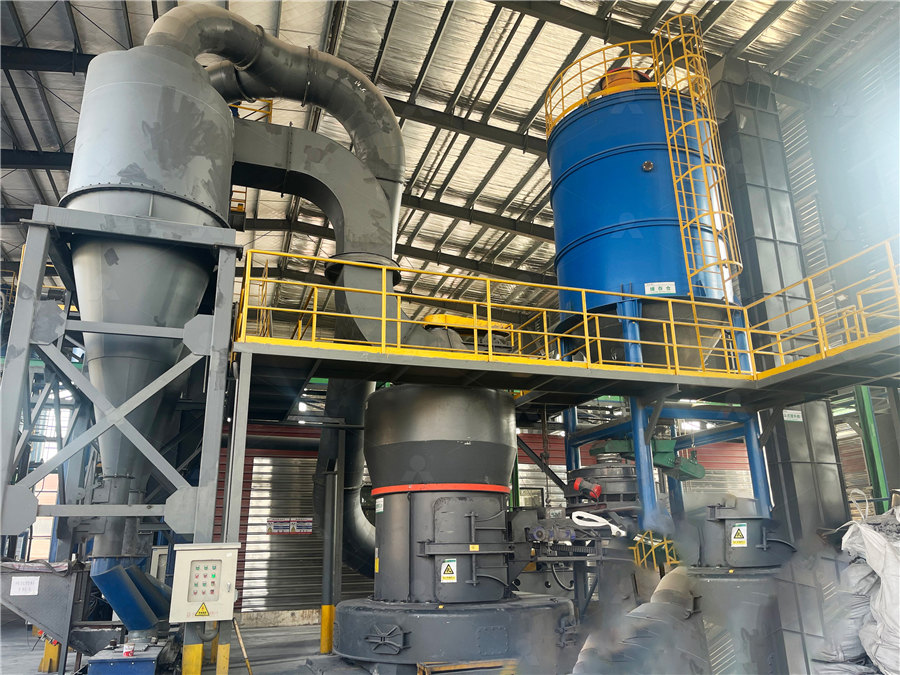
Overhaul Procedure For Coal Mill PDF Scribd
The document outlines the steps for an overhaul procedure of a coal mill It involves 21 steps to remove, inspect, replace, and reinstall components Key The RTKM separator is the obvious choice for new coalgrinding ball mills But it is also an ideal solution for upgrading existing coalgrinding installations, which in most cases incorporate a RTKM separator – for coal grinding ball mills FLSmidth CementThe FGX technology provides an innovative and costeffective dry coal processing process that integrates the separation principles of an autogenous medium separator and a conventional Dry Coal Separators Dry Coal Processing Separators FGX • Execution of coal mill separator modification • Technical key figures: coal mill capacity 20 tph, preheater exhaust gas temperature 360 °C, fine coal moisture max 20 % • Planning of a PROFESSIONAL CEMENT PLANT OPTIMIZATION,
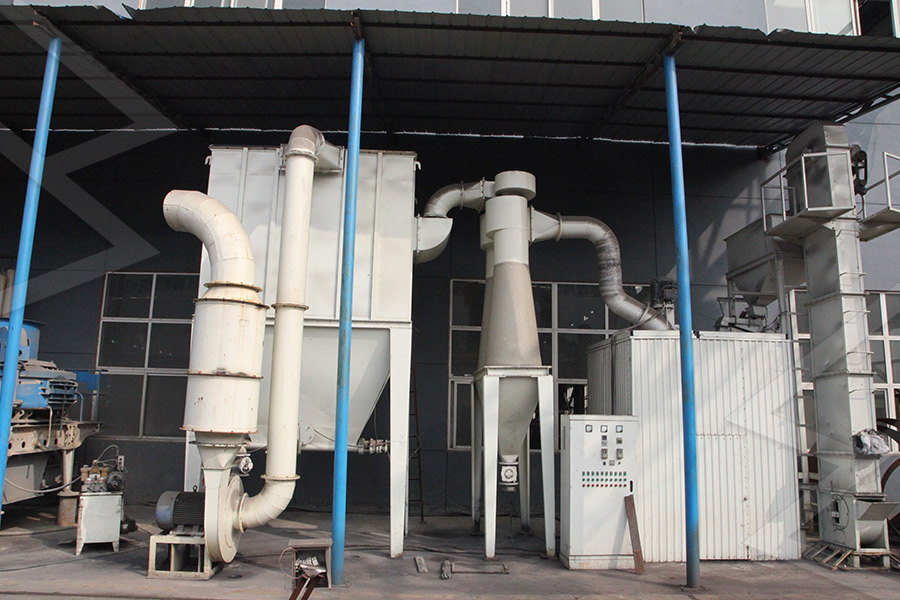
PROCESS OPTIMISATION FOR LOESCHE GRINDING PLANTS
vertical roller grinding mills for grinding: • Coal • Cement raw material • Clinker / granulated slag • Industrial minerals, and • Ores The core elements of these plants are the Loesche vertical Our ATOX® Coal Mill is a compact vertical roller mill that can grind almost any type of raw coal The coal mill utilises compression and shear force generated between the large rollers and the ATOX® Coal Mill FLSmidth CementThe Loesche coal grinding mill range is divided into two serial types: Small twin mills constructed to individual specifications (LM 122 D to LM 202 D), with table diameters from 1,200 to 2,000 LOESCHEMILLSLoesche mills can be adjusted so that in a few minutes a different product quality is achieved The springloaded roller grinding mill for grinding coal was intro 2 µm 5 µm Loesche
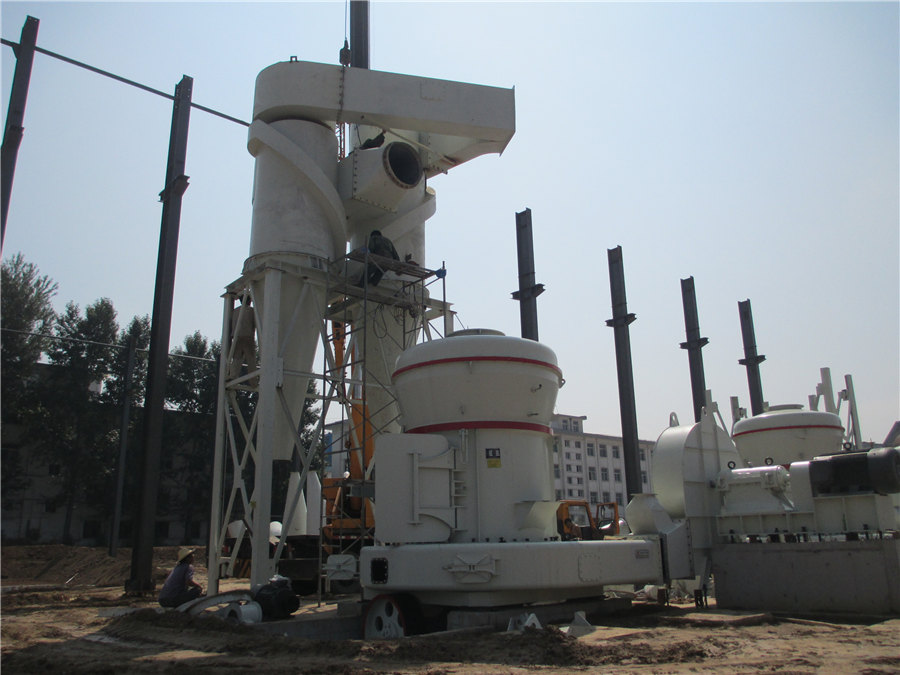
COAL GRINDING IMPS: more than meets the eye Gebr Pfeiffer
Vertical roller mills are not only used for grinding cement raw materials but also find an application in grinding a wide variety of coal types in cement and power plants Gebr Pfeiffer SE (GPSE) 2023年11月22日 Eriez has designed the Hybrid Wet Drum Separator as a replacement unit for a traditional wet drum separator The hybrid drum, coupled with the selfleveling tank, maintains the current layout of a standard wet drum Advances in Magnetite Recovery Coal Age2019年11月7日 Comprehensive treatment,we should have a test on the 300 MV unit steel ball coal mill pulverizing systemAt the same time,analyze the main operating parameters before modificationTransform the Optimization and transformation of 300MV units steel ball coal mill 2009年1月1日 Coal pulverizers play a critical role in the functioning and performance of a PCfired boiler The main functions of a pulverizer are crushing, drying and separating the fine coal particles CFD Modeling of MPS Coal Mill for Improved
.jpg)
Effects of Mill Speed and Air Classifier Speed on Performance of
2021年6月29日 Nowadays, ball mills are widely used in cement plants to grind clinker and gypsum to produce cement The research focuses on the mill speed as well as air classifier speed effect on the two 2014年1月1日 Two mill systems are employed for most coal grinding applications in the cement industry These are, on the one hand, vertical roller mills (VRM) that have achieved a share of almost 90% and, on (PDF) MPS mills for coal grinding ResearchGate• Execution of coal mill separator modification • Technical key figures: coal mill capacity 20 tph, preheater exhaust gas temperature 360 °C, fine coal moisture max 20 % • Planning of a rice husk and tyre chip feeding facility to substitute 14 % of the primary fuelPROFESSIONAL CEMENT PLANT OPTIMIZATION, Mill Training Manual Alstom Free download as PDF File (pdf), Text File (txt) or read online for freeMill Training Manual Alstom PDF Coal Mill (Grinding)
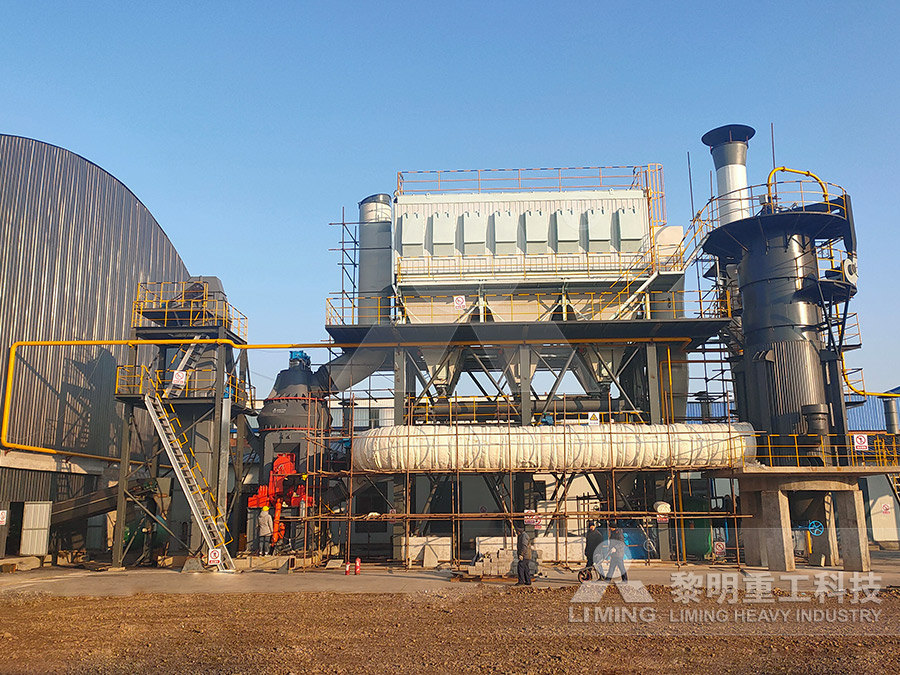
Coal mill pulverizer in thermal power plants PPT SlideShare
2012年11月17日 20 131Fineness Fineness is an indicator of the quality of the pulverizer action Specifically, fineness is a measurement of the percentage of a coal sample that passes through a set of test sieves usually designated at 50, 100, and 200 mesh A 70% coal sample passing through a 200 mesh screen indicates optimum mill performance The mill wear and The ATOX coal mill is suited for various installation types, whether inert or noninert, and direct or indirect firing systems An inert system designed for indirect firing is the most common solution for cement plants Equipped with the highefficiency RAKM dynamic separator, the ATOX coal mill will grind any type of coal to the required finenessATOX COAL MILL FLSmidth CementA cement mill separator is also referred to as a cement classifier because it also plays an important role in precisely controlling the grain size of finished cement products SINOMA has developed models of cement separators for meeting various application scenarios such as raw mill, coal mill, clinker, and slag grindingCement Mill Separator High Efficiency Cement SeparatorA bowl mill for a coal pulverizer with an air mill for primary entry of air, comprising a substantially closed separator body ( 2 ) having a central axis; and a bowllike grinding table ( 3 ) mounted on a shaft ( 4 ) rotatable about said central axis, cooperating with a plurality of grinding rolls ( 6 ) The airmill is provided with multiple entry openings ( 17′, 17″; 18′, 18″; 21, 25 USB2 Bowl mill for a coal pulverizer with an air mill for
.jpg)
HP Bowl type millspower plant equipment
Due to the improvement of the roller structure of HP coal mill, the roller replacement can be carried out directly on the machine, Generally speaking, when the required pulverized coal fineness R 90 ≤ 16%, HP coal mill with xxv international mineral processing congress (impc) 2010 proceedings / brisbane, qld, australia / 6 10 september 2010 investigation of the classification operation in a coal pulverising INVESTIGATION OF THE CLASSIFICATION OPERATION IN A COAL 2009年9月20日 A control oriented model was then developed by Fan (1994) and Fan and Rees (1994) In 2009, coal flow and outlet temperature of mill were modelled using mass and heat balance equations for startup Modeling and Parameter Identification of Coal Mill2022年2月24日 Curves of mill productivity, power consumed, specific surface of coal dust in terms of the relative rotational speed of the ball drum mill Composition of the balls loading the mill with a standard Improving the efficiency of the coal grinding process in ball drum
.jpg)
Investigation of Excessive Wear of Ashaka Coal Mill Riser Duct and
replacement of the mill internal components The frequent failure of the mill components significantly affects the overall reliability of the mill, thereby impacting on the availability of coal to be utilised for kiln burning Abrasive wear is caused by the sliding of hard particles over a surface, or between two surfacesThe ball mill is a traditional coal pulverizer machine, which has been widely used since it was invented In the cement plant, the new dry process cement manufacturing requires the moisture content of coal powder to be 05% ~ 15%, while that of raw coal is 15% ~ 40%Coal Mill in Cement Plant2014年3月1日 JKMRC of Queensland University is the only reported research team who got the samples from the industrial mill and analyzed the actual operation condition of the coal mill [13], [14] Comparing to the E ball mill of Tarong power plant in Australia, the mediumspeed mills have several significant advantages, which are widely used recentlyBreakage and separation mechanism of ZGM coal mill based on Hard coal is a sedimentary rock which was formed by deposition and carbonization of plant remains It is hard and resistant More than 50% of its weight is made up by carbon Therefore it is classified as highrank coal Other fossil fuels like subbituminous coals with high moisture contents as well as brown coal and lignite are lower rankedCoal mills for all requirements Gebr Pfeiffer
.jpg)
Modeling and Control of Coal Mill
Abstract: The paper presents development and validation of coal mill model (including the action of classifier) to be used for improved coal mill control The model is developed by using the mass and heat balance equations of the coal mill Genetic Algorithm is used to estimate the unknown parameters that are used in the model validationSOP startup Shutdown and operation of Coal Mill Free download as Word Doc (doc / docx), PDF File (pdf), Text File (txt) or read online for free This document provides the standard operating procedure for starting up, SOP Startup Shutdown and Operation of Coal MillRaw coal enters the coal ball mill through the feeding device At this time, hot air with a temperature up to 300℃ enters the coal mill barrel from the intake pipe The raw coal falls on the lifting plate of the drying chamber and is continuously Coal Ball Mill Grinding for Different Kinds of effectiveness in the case of coal grinding plants Whether it is a roller mill for coal, limestone, granulated blast furnace slag or cement grinding, the sepol® QM or RM highefficiency separator is integrated into the mill housing of our roller mills sepol® QM and RM: the compact one for roller mills Layout of a quadropol® plant configurationbrochure sepol separator myPolysiusService
.jpg)
Analysis of Coal Mill Operation PDF Mill (Grinding) Scribd
Analysis of Coal Mill Operation Free download as PDF File (pdf), Text File (txt) or read online for free This document analyzes the comilling of coal and wood biomass in a ringball mill It describes tests conducted pulverizing hard coal with additions of 8% and 16% pine sawdust at different moisture contents Key findings include: 1) Biomass has weaker grinding properties Section 2 : Coal Handling Plant 21 Introduction 2 1 22 Brief description of coal handling plant system 2 2 23 Design criteria and broad features 2 5 24 Performance requirements 2 17 25 Codes and standards 2 19 Annexure2A Typical scope of work for coal handling plant 2 STANDARD DESIGN CRITERIA/ GUIDELINES FOR BALANCE OF 2010年1月1日 Sampling ports were firstly drilled on a ZGM95 coal mill in the power plant in China, and the coal samples from various points in the pulverizer were collected under the different operation Investigation of the classification operation in a coal pulverising Coal Pulverizer are designed to reduce the size of the incoming raw coal to a fineness that will result in good furnace performance The grinding surface in the pulverizer resembles a shallow dish or bowl Therefore the name “Bowl Mill” has been adopted to refer to this piece of equipment Components of Bowl Mill Coal Pulverizer GearboxBowl Mill Coal Pulverizer COAL HANDLING PLANTS
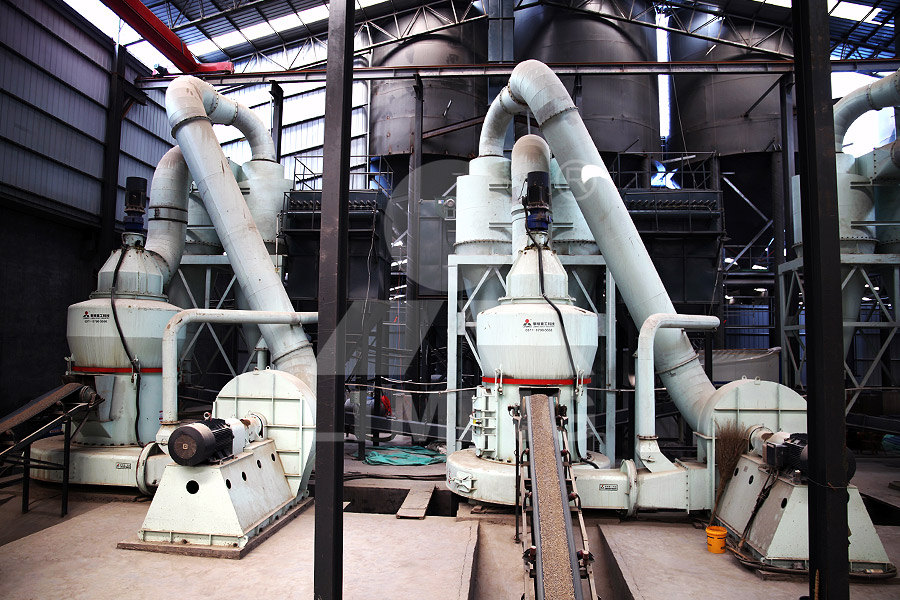
Cement Separator HighEfficiency Cement Mill Separator
The interior of the cement mill separator usually includes a conical cylinder, which is equipped with a set of rotating impellers When the cement clinker enters the separator from the cement mill, it will be forced to form in the cylinder through the action of the impellers swirling airflowThe introduction of hot air helps to improve the drying effect of coal powder and carries coal powder into the coal mill shell during the coal grinding process Coal Powder Conveying System The pulverized coal conveying system is used to transport pulverized coal from the pulverizer to the target location, such as a combustion furnace or a pulverized coal storage binAir Swept Coal Mill Cement Plant Equipment Coal Grinding Mill5 VERTICAL ROLLER MILL KTM Main data Type Min motor power Max motor power Min capacity Max capacity [kW] [kW] [t/h] [t/h] KTM 400 11 18,5 0,1 0,8 KTM 800 37 55 2 5 KTM 1000 55 90 4 8 KTM 1200 90 132 6 12 KTM 1400 132 200 9 18 KTM 1600 200 315 12 24 KTM 1800 315 400 20 38 KTM 2000 400 500 29 50 KTM 2200 500 630 39 64 KTM 2400 630 800 GRINDING AND SEPARATING TECHNOLOGY SYSTEMSThe quadropol® concept for coal or pet coke grinding, with adapted table speed and high efficiency separator sepol®, ensures a safety mill operation and serves reliable the kiln burning process Mombasa Cement Ltd ordered a QMK² quadropol® thyssenkrupp Polysius Grinding
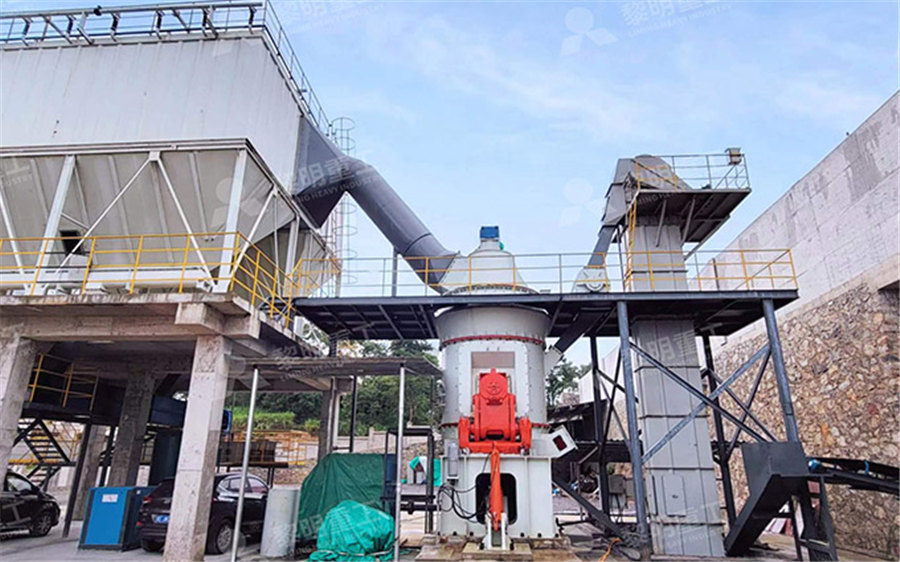
Problem Analysis and Optimization Test for Separation Process of Coal
2016年10月22日 Xie Guangyuan, Wu Ling, OU Zeshen, et, al Study On Separation And Dewatering Techniques Of Recovering Clean Coal From Fine Coal[J] Journal of China Coal Society, 2004,29(5):602605 Google Scholar Xie Guangyuan, Wu Ling, Ou Zeshen, et alResearch on fine coal classified flotation process and key technology[J]Coal mills, also known as pulverizers, play a critical role in power plants by grinding coal into fine powder, which is then used in various pyroprocesses This article explores the key aspects of coal mill safety, including potential hazards, preventive measures, and best practicesCoal Mill Safety: A Critical Aspect of Power Plant Operations Coal Coal mills, essential components in power generation and various industrial processes, pose significant safety risks if not properly managed These mills, used to grind coal into a fine powder for combustion, present potential hazards such as fire, explosion, and mechanical failures This article outlines best practices and precautions to ensure thBest Practices and Precautions Coal Mill Safety, Explosion and Finally, the temperature equation is based on heat balance equation of the coal millThe significant heat contribution comes from the primary air flow , moisture of the incoming coal particles, coal flow into the mill (1) and from grinding the moisture coal particles and temperature depends on the The mass of pulverised coal on the table grinding rate and the amount of coal (PDF) Modeling and Control of Coal Mill Academia
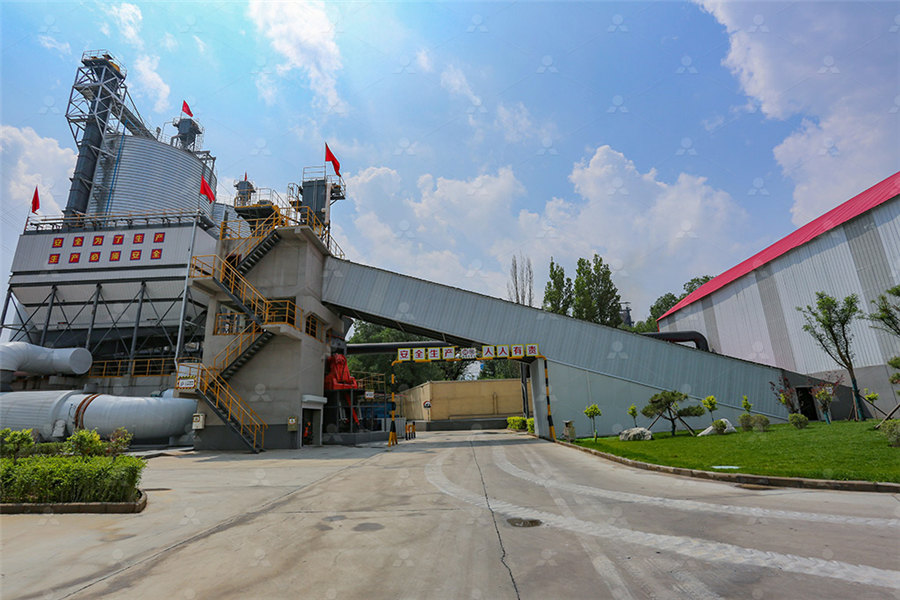
How To Measure Your Cement Mill And Cement Classifier?
With the increase of cement mill specifications and the requirement of energy saving, high yield, and high quality of cement grinding plant, the closedcircuit grinding is an inevitable trend of cement grinding unitThe essential equipment of a closedcircuit grinding system is a cement classifier, also known as a cement separatorThe function of the cement classifier is to select Introduction This article concerns itself with vertical grinding mills used for coal pulverization only (coal pulverizers), although vertical grinding mills can and are used for other purposes The 3D model in the saVRee database represents a vertical grinding bowl millOther grinding mill types include the ball tube mill, hammer mill, ball and race mill, and , roll and ring millVertical Grinding Mill (Coal Pulverizer) Explained saVReeCOAL MILLppt Free download as Powerpoint Presentation (ppt), PDF File (pdf), Text File (txt) or view presentation slides online The document discusses coal mill equipment, including the names, functions, and working principles of different types of equipment It focuses on vertical roller mills (VRM), describing the three main sections of VRM separation, drying, and grindingCoal Mill PDF Coal LigniteDynamic Separator for Coal Mill Productivity: 10–60 t/h Motor power: 15–90 kw Air quantity: 21000– m3 Application range: coal, ore, etcDynamic Separator for Coal Mill HXJQ Machinery
.jpg)
Wet and dry grinding of coal in a laboratoryscale ball mill: Particle
2019年10月1日 Request PDF Wet and dry grinding of coal in a laboratoryscale ball mill: Particlesize distributions In this study, experimental data for wet and dryground coal samples under wet and dry