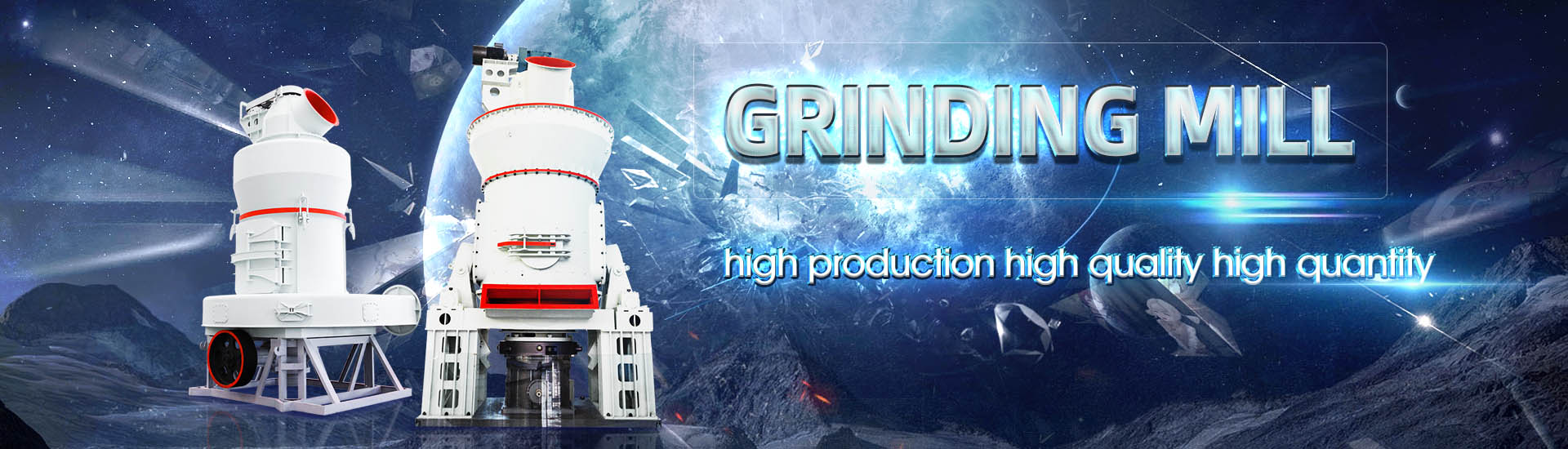
Models and specifications of mining silica ore grinding mill
.jpg)
ISAMILL FINE GRINDING TECHNOLOGY AND ITS INDUSTRIAL
IsaMill is a major development in grinding technology jointly invented by Mount Isa Mines of Australia and Netzsch Feinmahltecknik GmbH of Germany for ultrafine and fine grinding A simple and novel nonlinear model of a runofmine ore grinding mill circuit, developed for process control and estimation purposes, is validated The model makes use of the minimum Analysis and validation of a runofmine ore grinding mill circuit PGM, iron ore, industrial applications and gold processing plants and is the best choice for regrinding concentrates, fine or ultrafine grinding and mainstream grinding The IsaMill™ is IsaMill™ uses horizontal milling to secure better energy efficiency Grinding Solutions Every mining operation’s grinding process is unique Metso, with over a century of experience, designs and manufactures the most comprehensive line of grinding Metso comminution solutions Grinding
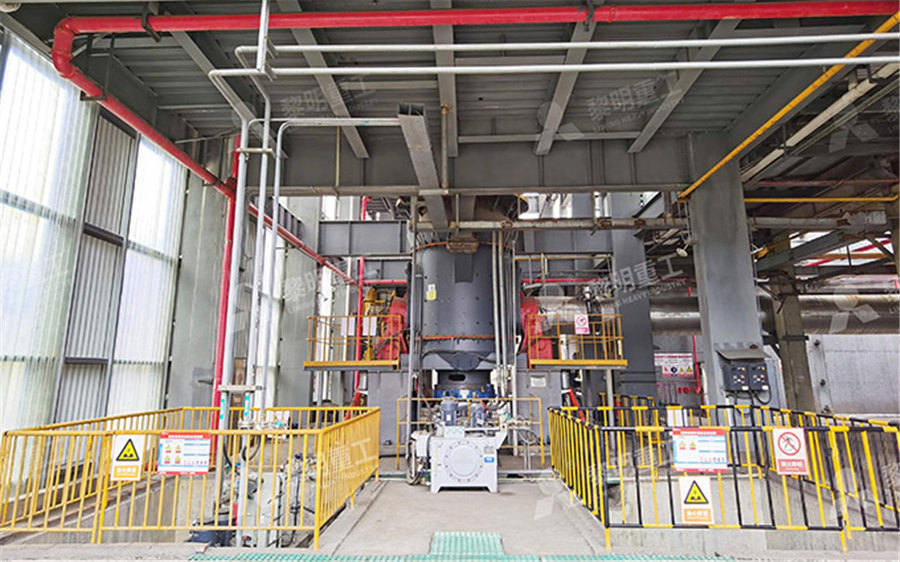
Ore Grinding SpringerLink
2023年7月20日 There are several impact factors of the grinding operation (1) Structure parameters of grinding mill, including its specifications, model, aspect ratio, ore discharging Model predictive control provides an additional tool to improve the control of SemiAutogenous Grinding mills and is often able to reduce process variability beyond the best performance that SAG Mill Optimization using Model Predictive Control Andritz2020年6月1日 Stirred media mills are used by the mining industry for ultrafine grinding to enhance liberation, and to decrease particle sizes of industrial minerals to tailor functional Stirred media mills in the mining industry: Material grindability 2021年9月5日 This study aimed to model bauxite grinding and assess the optimum material filling volume in a laboratory ball mill in order to improve mill and overall process efficiency Modeling of Bauxite Ore Wet Milling for the Improvement of
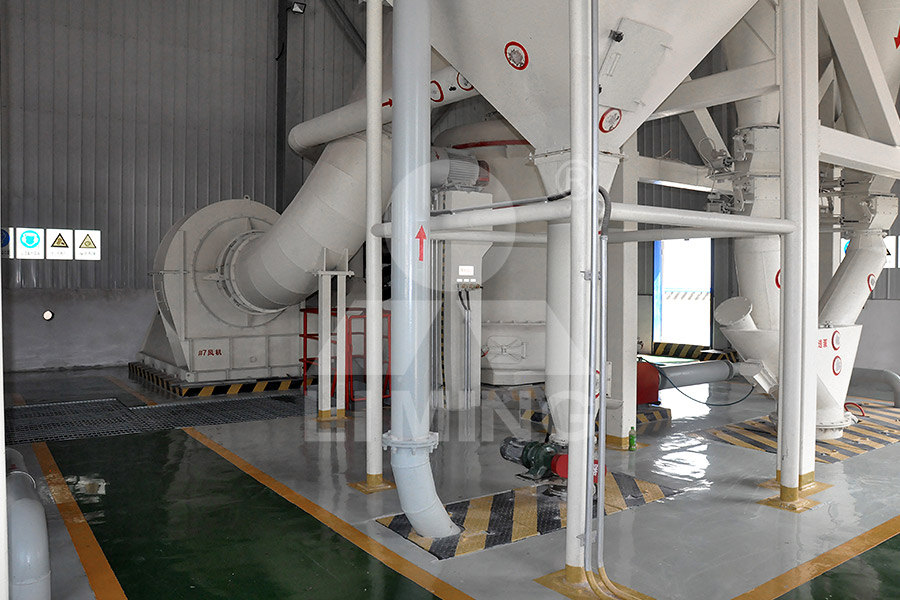
Specifications of industrial ball mills (PBM SBM)
In this study, the perfect mixing model was used to investigate its accuracy level, under different laboratory conditions, in predicting the particle size distribution of industrial ball mills2014年1月1日 An analysis of the kinetics of dolomite grinding in a dry ball mill reveals that the following approximations apply for the parameters of the batch grinding model: the size discretized selection Population balance model approach to ball mill 2020年1月3日 Iron ores obtained from different sources differ in their chemical and physical properties These variations make the process of grinding a difficult task The work carried out in this context focuses on three different samples of iron ore, viz, high silica high alumina, low silica high alumina, and low silica low alumina The grinding process for all the three iron ores is Estimation of Grinding Time for Desired Particle Size Distribution Raw ore (20 mm) High pressure grinding roll Wet screening +3 mm3 mm Wet permanent cylinder magnetic separator Tower mill Tailings Overflow outlet Fig 1 Tower mill grinding after rough separation process of highpressure grinding roll products in an iron mine Table 1 Particle size analysis resultsPrediction and optimization of tower mill grinding power
.jpg)
Grinding in Ball Mills: Modeling and Process Control
2012年6月1日 Basic kinetic and energy models of the grinding process are described and the most commonly used control strategies are analyzed and discussed +1 Figures uploaded by Vladimir Monov2023年4月23日 grinding media in a grinding mill with about 2630 wt% chrome by Chen et al [37] using a phosphate ore in a modified ball laboratory ball mill whose electrochemical potential could be controlled(PDF) Grinding Media in Ball MillsA Review ResearchGateAlso the Premier™ mills and Select™ mills come ready to be easily integrated with our mill reline equipment and full mining portfolio providing a onestopshop for your minerals processing needs! Premier™ horizontal grinding millsGrinding mills for mining and minerals processing Metso2021年9月5日 Three models, namely the GGS, RR, and logistic model, were used to determine the PSD of the grinding mill products, in order to identify the best applicable model to the experimental data Nonlinear least square analysis using the Solver tool of Microsoft Excel was used to fit the experimental data, and the model parameters of Equations ( 4 ), ( 6 ), and ( 8 ) Modeling of Bauxite Ore Wet Milling for the Improvement of
.jpg)
Silica Sand Processing Equipment Micron Grinding Ball Mill Air
The company′s main products are: Wet ball mill (grinding) production line, dry ball mill with sorting machine production line, high purity stone English system sand machine, air classifier, the board type magnetic separator, quartz pickling equipment, drum washing machine, vertical ring high gradient magnetic separation machine, hydraulic classifier, scrubbing machine, dryer, 2013年4月1日 Rocks are defined as too large to be discharged from the mill, whereas solids, defined as particles small enough to leave the mill, consist of outofspecification coarse ore and inspecification fine ore fractions The model incorporates a unique prediction of the rheology of the slurry within the mill A new hydrocyclone model is also presentedAnalysis and validation of a runofmine ore grinding mill circuit 2018年2月1日 In another study to investigate ball size distribution on ball mill efficiency by Hlabangana et al [50] using the attainable region technique on a silica ore by dry milling, a threeball mix of Effect of ball and feed particle size distribution on the milling grinding is one such process employed at several mining operations in Australia including Mount Isa Mines Limited in Australia Mount Isa Mines is a business unit of MIM Holdings Limited MIM is an Australianbased international mining and mineral processing company with around 8000 employees worldwideISAMILL FINE GRINDING TECHNOLOGY AND ITS INDUSTRIAL
.jpg)
Iron Ore Processing: From Extraction to Manufacturing
2024年4月26日 The choice of grinding mill depends on factors such as the desired product size, capacity requirements, and energy consumption b Autogenous and SemiAutogenous Mills: In some cases, autogenous (AG) 2018年7月1日 A hybrid nonlinear model predictive controller (HNMPC) is developed for a runofmine ore grinding mill circuit A continuoustime grinding mill circuit model is presented with a hydrocyclone cluster as the primary classifier The discretetime component is the switching of hydrocyclones in the hydrocyclone clusterHybrid nonlinear model predictive control of a runofmine ore 2023年10月16日 The models developed durin g the MinetoMill were used in combination with the mine plan and additional ore characterisation data conducted by Chapada to forecast plant throughput according to Full MinetoMill Optimization Continuous Improvement of 2020年6月3日 The design of such grinding mills is extremely critical, requiring sophisticated software tools, proprietary calculation worksheets, and experienced technical engineers and drafters This blog will review how the mill design process has changed over the last 30 years While most of the changes have been positive, new issues and problems have risen in the How grinding mill design changed over the last 30 years
.jpg)
Ore mill, Ore grinding mill All industrial manufacturers
Find your ore mill easily amongst the 42 products from chemical industry, etc, it has two ore grinding Compare this product Remove from comparison tool ball processing) foothold in diamond mines By the late 1990s the HPGR became standard equipment for processing iron ores Successful hard rock mining installations followed about Grinding Mills: Ball Mill Rod Mill Design PartsCommon types of grinding mills include Ball Mills and Rod Mills This includes all rotating mills with heavy grinding media loads This article focuses on ball and rod mills excluding SAG and AG mills Although their concepts are very similar, they are not discussed herePhotographs of a glass ended laboratory ball mill show Grinding Mills 911Metallurgist2019年1月30日 Mill power models have been used in a variety of ways in industrial practice since power directly equates to throughput and fineness of ground product We first start with HoggFuerstenau Power Model and show how this model successfully predicted the power draw of many grinding mills in several mining operations Then, we show how this model was on the The Evolution of Grinding Mill Power Models Mining, 2018年12月24日 ABSTRACT In this study, simulation aided design of grinding circuit for a gold mine in Iran is presented The main parameters for the design of the grinding circuit are the ore specifications and EVALUATION OF THE ALTERNATIVES FOR GOLD ORE GRINDING
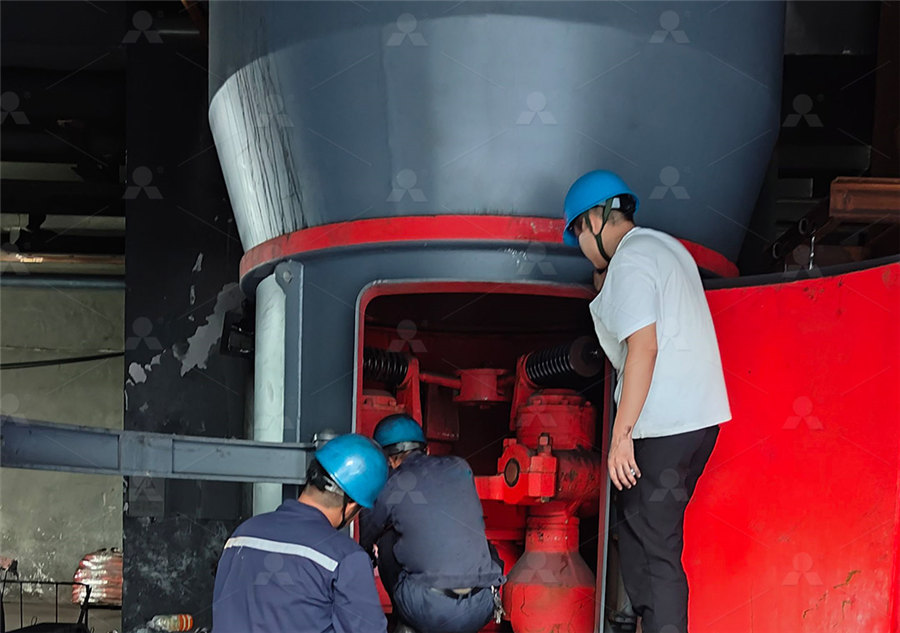
(PDF) Feasibility and necessity of mine to mill
2021年4月19日 Regarding this background, this article describes the feasibility of mine to mill optimization from three aspects: (1) different energy efficiencies between drillingblasting and crushinggrinding 2024年10月1日 Recent advancement in numerical modelling has enabled simulation of industrial scale grinding mill for optimised grinding dynamics and wear prediction of shell liners (Cleary, 2019, Cleary et al, 2020a, Cleary and Owen, 2019, Xie et al, 2021)Earlier studies adopted discrete element modelling to capture the transient and cumulative shear and impact forces A novel IoT sensor and evolution model for grinding mill liner which use both ore and steel balls as grinding media (Wei and Craig, 2009b) In the case of a ball mill the ore is crushed before it enters the mill, whereas a SAG mill receives runofmine (ROM) ore directly (Stanley, 1987) A SAG mill in a singlestage closed circuit con guration, as shown in Fig 1, is considered for this study A descriptionAnalysis and validation of a runofmine ore grinding mill circuit Several popular models are available, with different specifications to suit various mining and mineral processing applications Here are some common models of gold ore ball mills: 1 Wet Overflow Ball Mill: This mill incorporates a steel drum with a layer of grinding media (steel balls or ceramic balls) insideWhat are the models of gold ore ball mills?
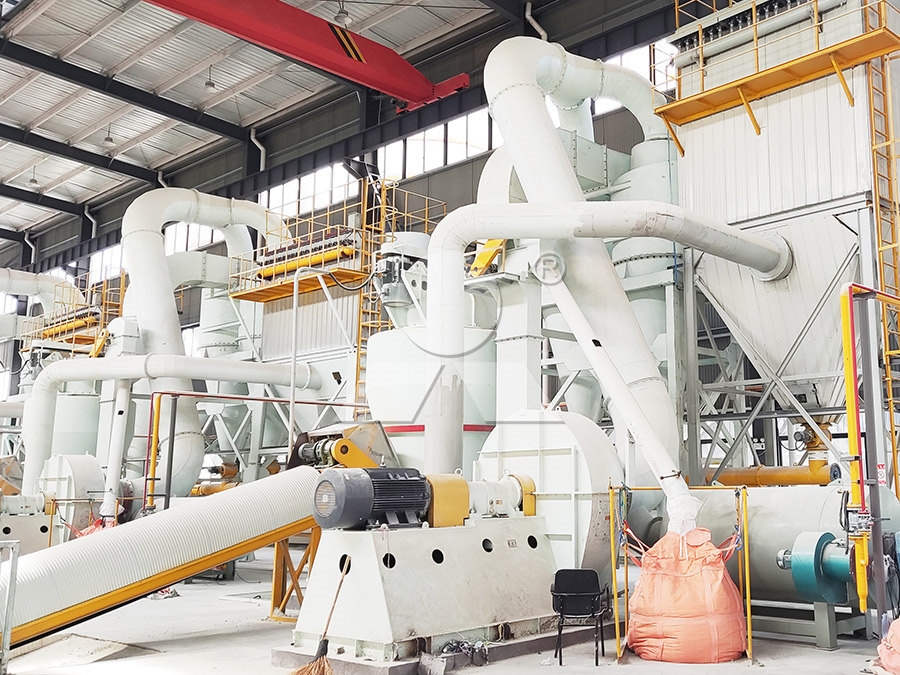
Grinding and grading equipment in beneficiation JXSC Mining
2021年8月13日 The specifications of ball mills and rod mills are expressed in simplified inner diameter D and cylinder length L For example, a common type of ball mill produced by a JXSC mining machinery and drying of materials Mainly used in the chemical and building materials industry, but recently there is a trend for ore grinding The The rod mill is another type of grinding mill used in the copper ore mining process This machine uses steel rods as the grinding media instead of balls, which are commonly used in ball mills The rods grind the ore by tumbling within the mill, similar to the action of a rotating drumUnderstanding the SAG Mill in Copper Ore Mining Process2020年3月31日 This laboratory study investigates selective grinding and beneficiation options for a Greek bauxite ore First, a series of batch grinding tests were carried out in order to investigate the Grinding Behavior and Potential Beneficiation Options of Bauxite OresSpeed also plays a role in ore grinding; too high of a speed can cause damage to the mill gears and other components, while too low of a speed can cause excessive wear on these same components It is important to find a balance between these two variables in order to achieve optimal grinding performanceFactors affecting ores grinding performance in ball mills
.jpg)
General specification of the chemical composition of silica sand
Download scientific diagram General specification of the chemical composition of silica sand for glassmaking [50,58] from publication: Gold Mine Tailings: A Potential Source of Silica Sand for 1 Grindability: The grindability of the ore affects the efficiency of the grinding mill Harder ores require more energy and longer grinding times, which can impact the mill's performance and operational costs 2 Media andliner Wear: The condition of the grinding media and liners affects the mill's efficiencyUnderstanding the operation of grinding mills in the mining and DOVE Rod Mills are supplied in a wide range of capacities and specifications DOVE supplies 2 models of small Rod Mills designed for laboratories milling process, capacity range of (5000g/Hr – 20 Kg/Hr) For small to large scale Rod Mills Grinding Mills DOVESilica Sand Mining introduces Foundry silica sand is the quartz as the main mineral composition, particle size of 0020 mm to 3350 mm refractory particles, according to the mining and processing methods of different can be divided Silica Mining Processing Equipment Flow Chart
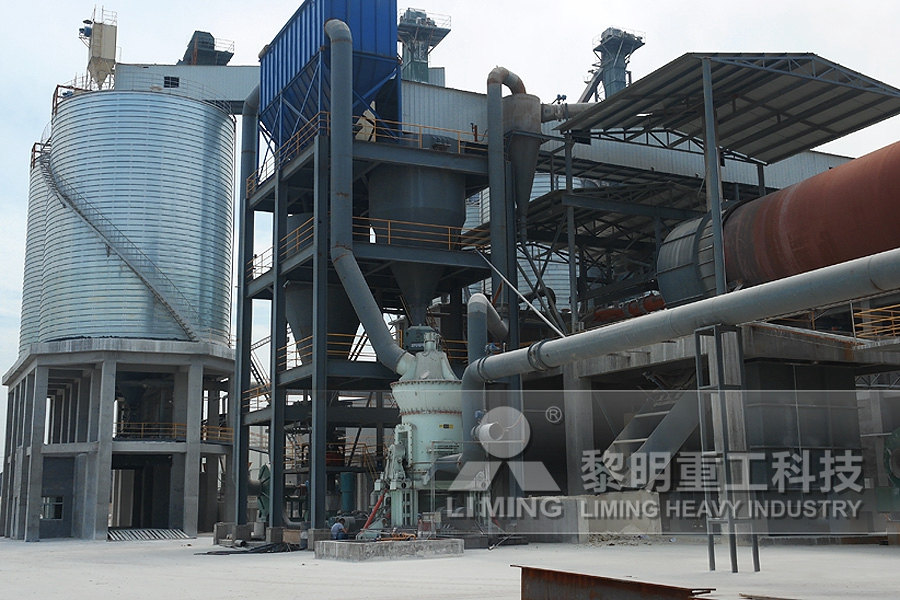
Estimation of Grinding Time for Desired Particle Size Distribution
ore, viz, high silica high alumina, low silica high alumina, and low silica low alumina The grinding process for all the three iron ores is carried out individually in Bond’s ball mill and the total retention time taken by each iron ore sample is calculated The present investigation focuses on utilizing the calculated retention time of the Request PDF On Mar 15, 2015, Mathis Reichert and others published Research of iron ore grinding in a verticalrollermill Find, read and cite all the research you need on ResearchGateResearch of iron ore grinding in a verticalrollermillJoyalGrinding Mill,Fine Grinding Mill,Micro Powder Mill,Ultrafine Mill,Raymond Mill From China ManufacturerThis page is about the grinding mill,includes micro powder mill,high pressure mill,ygm model,raymond mill,3r,4r,5r,6r and ball mills,if you want to buy these Joyal operates at the frontiers of the Mining machinery We use good JoyalGrinding Mill,Fine Grinding Mill,Micro Powder Mill,Ultrafine Mill 2016年1月1日 In wet grinding practice, highstress abrasion occurs over a small region when ore particles are trapped between the grinding balls and the mill liner, and the load is sufficient to fracture A comparison of wear rates of ball mill grinding media
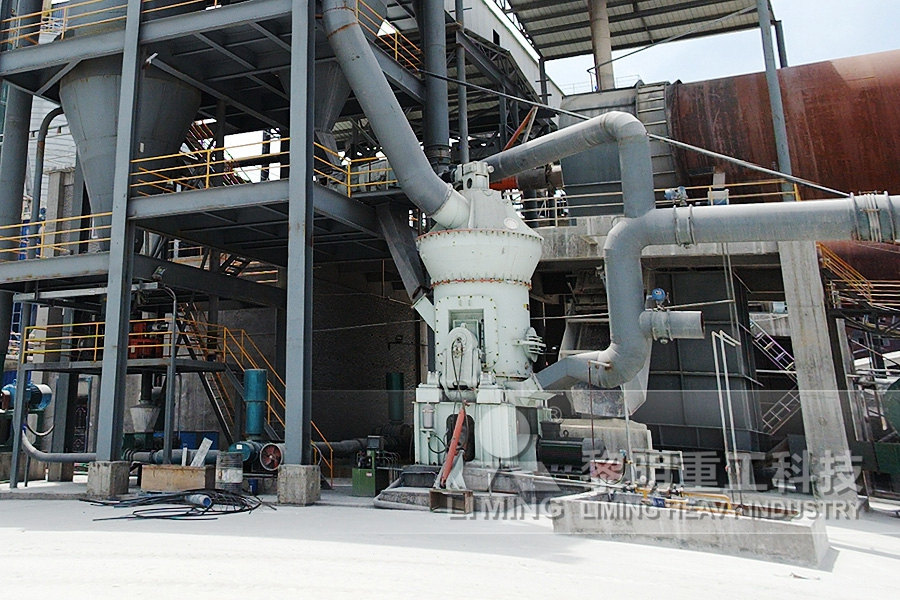
Modeling and simulation of vertical roller mill using population
(Schaefer, 2001) Fig 1 illustrates the grinding parts of a Loesche vertical roller mill The grinding material is comminuted in the Loesche roller grinding mill between the rotating horizontal grinding track and stationary grinding rollers Grinding is affected primarily by compression866 IEEE TRANSACTIONS ON INDUSTRY APPLICATIONS, VOL 41, NO 3, MAY/JUNE 2005 Technical Evaluation and Practical Experience of HighPower Grinding Mill Drives in Mining Applications José R Rodríguez, Senior Member, IEEE, Jorge Pontt, Senior Member, IEEE, Patricio Newman, Rodrigo Musalem, Hernán Miranda, Luis Moran, Fellow, IEEE, and Gerardo Technical evaluation and practical experience of highpower grinding Constant speed Low speed synchronous motors Synchronous motors are widely used in mill driving systems at a constant speed using an air clutch between the motor shaft and mill pMining Grinding and Processing WEG2018年8月17日 The concept of ore blending is a very relevant notion in modern high tonnage production mines It is not only essential for the prolongation of the mine life of the concerned mine but as well as a The effects of ore blending on comminution behaviour and