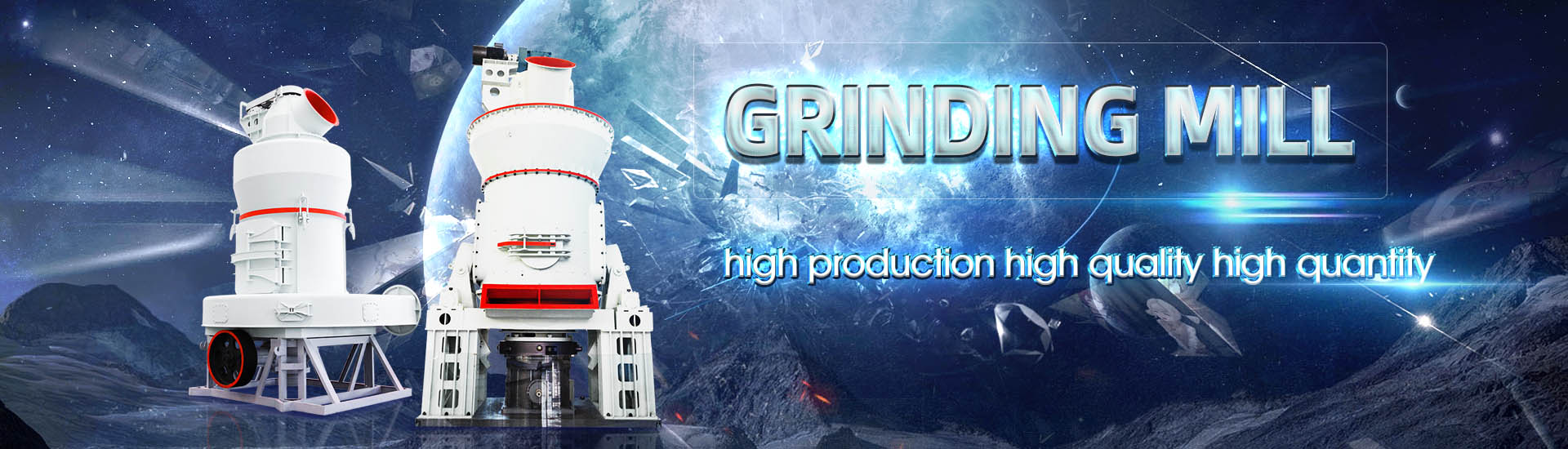
Production implementation standards for vertical ore mills
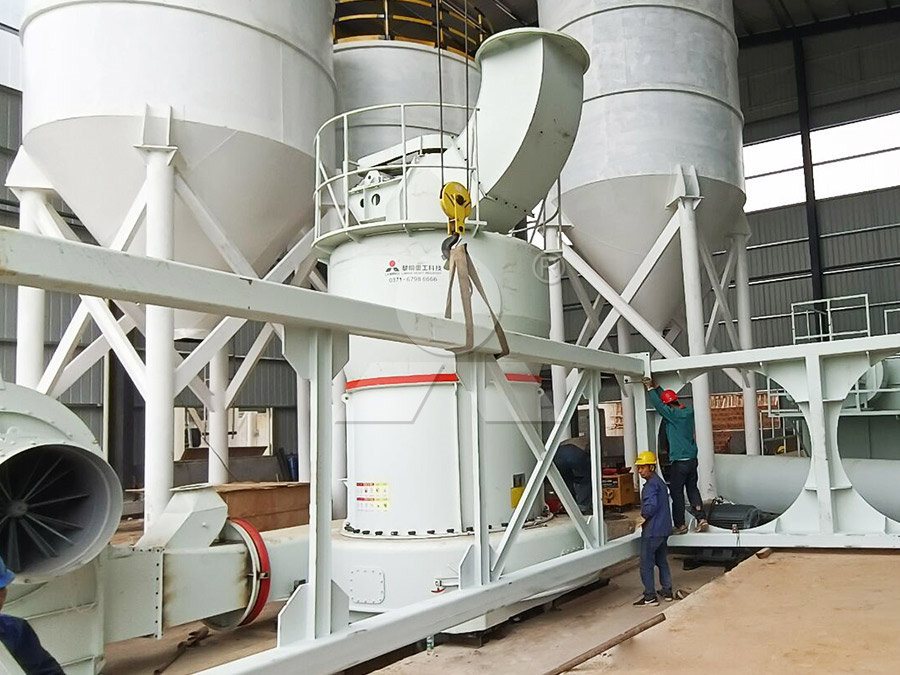
PROCESS OPTIMISATION FOR LOESCHE GRINDING PLANTS
vertical roller grinding mills for grinding: • Coal • Cement raw material • Clinker / granulated slag • Industrial minerals, and • Ores The core elements of these plants are the Loesche vertical 2012年9月1日 Mills (VRM) installations and summarises the main benefits of the dry compressive Loesche grinding technologies in Airflow and OverflowMode Some of these Latest Installations And Developments Of Loesche Vertical Roller Vertical roller mill (VRM) is an established technology in cement and slag grinding applications and Boliden and Gebr Pfeiffer have been collaborating on the application of this technology in Vertical Roller Mills used for the comminution of mineral oresPilot plant test results with various ores showed that low energy consumption feature of vertical roller mills is applicable to the ore industry Grinding test results for zinc ore showed that it is (PDF) Operational parameters affecting the vertical roller mill
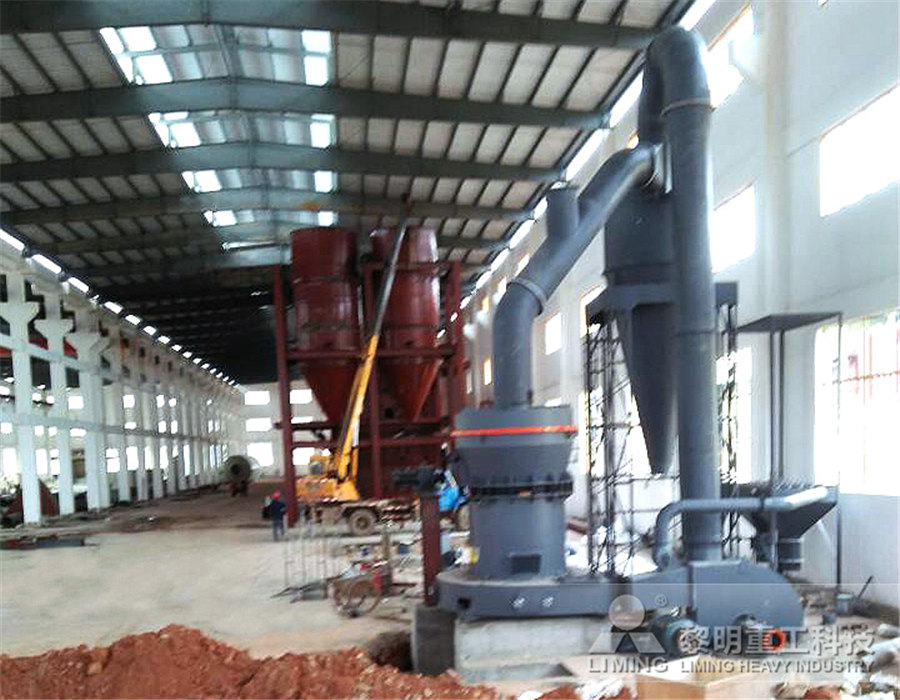
Operational parameters affecting the vertical roller mill
2017年4月1日 Pilot plant test results with various ores showed that low energy consumption feature of vertical roller mills is applicable to the ore industry Grinding test results for zinc ore 2022年1月23日 This work concentrates on the energy consumption and grinding energy efficiency of a laboratory vertical roller mill (VRM) under various operating parameters For design of experiments (DOE), the response surface method Analysis and Optimization of Grinding Performance of The objective of MinetoMill Process Integration and Optimisation methodology is to develop and implement sitespecific mining and milling strategies to minimize the overall cost per tonneUSING PROCESS INTEGRATION OPTIMIZATION TO PROVIDE 2019年4月16日 The paper demonstrates why the Loesche VerticalRollerMill (VRM) is a serious alternative to conventional grinding technologies and where the limitations of the system are VRM's are state of(PDF) LEARNING FROM OTHER INDUSTRIES; WHY THE
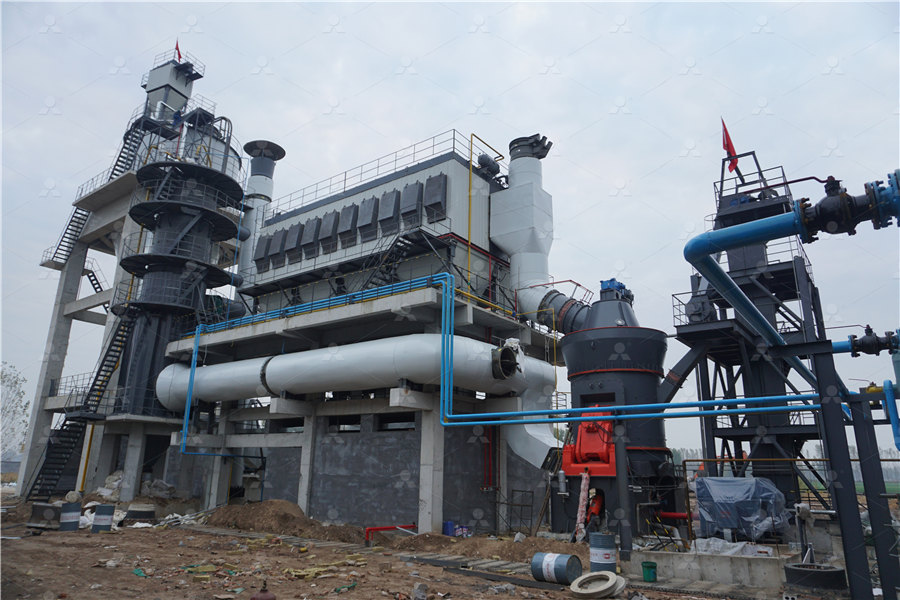
Research of iron ore grinding in a verticalrollermill
2015年3月15日 Two magnetite iron ores were comminuted with a pilot scale verticalrollermill The effect of three mill parameters was quantified using DoE methods The developed concentrator offers an interesting opportunity: a vertical mill operating in parallel with two ball mills During almost two years of operation, several sampling campaigns were conducted to Comparing ball and vertical mills performance: An industrial case Compressive grinding, Dry grinding, Flotation of copper sulfide ore, Mineral liberation, Vertical roller mill INTRODUCTION Copper production is mainly connected to porphyry copper deposits as main INVESTIGATION ON FLOTATION BEHAVIOR OF A COPPER SULFIDE ORE CLUM series ultrafine vertical roller mills have a large capacity, stable operation, low wear, long life, environmental protection and energy saving, simple operation, intelligent control system, easy maintenance, and the fineness can be freely Vertical Roller Mill SBM Ultrafine Powder Technology
.jpg)
Research of iron ore grinding in a verticalrollermill
Request PDF On Mar 15, 2015, Mathis Reichert and others published Research of iron ore grinding in a verticalrollermill Find, read and cite all the research you need on ResearchGate2019年4月16日 Vertical roller mills (VRM) have been used extensively for comminuting both cement raw materials and minerals like limestone, clinker, phosphate, manganese, magnesite, feldspar and titanium(PDF) LEARNING FROM OTHER INDUSTRIES; WHY THE VRM2021年1月1日 Mathematical optimization of scheduling systems in steel manufacturing will help reaching these goals (Tang et al, 2001, Dios et al, 2016, Dutta et al, 2018)Better scheduling of the hot rolling mill will have a direct impact on punctuality, efficient use of raw materials and energy, the robustness of the production process against small perturbations, and a reduction A review of planning and scheduling methods for hot rolling mills 7 // Almost any plant for the grinding of cement raw material is a combination of machines specially adapted to the particular physical properties of the material to be ground As a result, our plants work efficiently without any trouble » Highly efficient grinding, drying, and separating in one unit » Outstanding production capacities exceeding 1,400 t/h in one single millPFEIFFER MILLS FOR THE CEMENT INDUSTRY
.jpg)
RECENT DEVELOPMENTS IN COARSE GRINDING USING VERTICAL STIRRED MILLS
Pilot test work was carried out by Mazzinghy et al (2015) on a batch ball mill and pilot scale vertical mill to assess the energy efficiency factor The results shows that the scaling factor of 135 was required to adjust the ball mill energyspecific breakage rates to match the breakage rates in a vertical mill The vertical mill2014年10月20日 Regrind of metallic ores with vertical mills: conducted in the standard 8"×10" jar, together with current and predicted global metal production rates, ore grades and grind or liberation Regrind of metallic ores with vertical mills: An overview of the 2014年11月1日 The application of vertical mills in regrind circuits is consolidated This type of mill is now attracting interest in primary grinding applications, due to its higher efficiency when compared to Vertical mill simulation applied to iron ores ResearchGate2022年6月1日 Technoeconomic case study on Oxyfuel technology implementation in EAF steel mills – Concepts for waste heat recovery and carbon dioxide utilization June 2022 Cleaner Engineering and Technology (PDF) Technoeconomic case study on Oxyfuel technology implementation
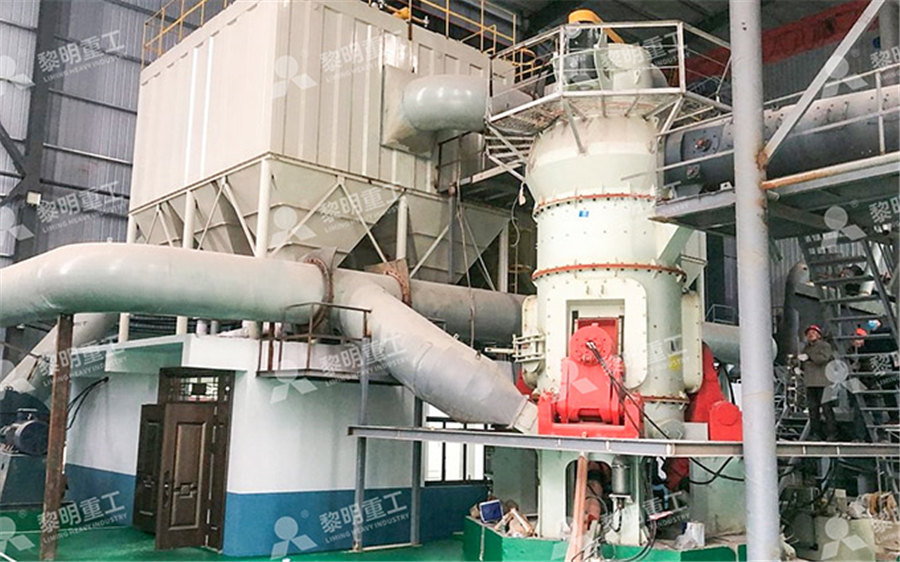
Production standards for iron ore ball mills LinkedIn
2024年6月5日 As an important equipment in mining machinery, the production standards of iron ore ball mills directly affect the performance, service life, and production efficiency of the equipment In order CLIRIK Machinery produces all kinds of vertical roller mills for ore powder making, such as Raymond roller mill, ultrafine grinding mill, ultrafine Compare the advantages and disadvantages of ultrafine mill and ultrafine vertical roller mill in the production of ultrafine stone powder View More >> Happy New Year From CLIRIK Machinery 2022 Vertical Roller Grinding Mill Machine CLIRIK Machinery 2020年10月1日 As a result of the assumptions, the authors proposed a mixed integer programming model containing a binary variable related to oremovements occurrence using underground machines (LHDs and trucks) and integer variables related to ore tonnage, lower and upper bound of extracted average grade, compared to desired mill gradeProduction scheduling optimisation for sublevel stoping mines 2001年10月1日 LOESCHE vertical roller mills are widely used for the comminution of raw materials in the cement industry, for the comminution of clinker and blast furnace slag and for the production of LOESCHE vertical roller mills for the comminution of ores and minerals
.jpg)
Picture: Loesche GmbH, Germany CEMENT SikaGrind® FOR VERTICAL ROLLER MILL
Vertical Roller Mills (VRM) have a clearly higher energy efficiency cement production with newly installed mills comes from VRM Standard mortar without SikaGrind® Standard mortar with SikaGrind® LS43 1 10 100 60 50 40 30 20 10 00 Particle size [µm] Volume [%]2020年8月4日 Optimizing Feed Milling Processes for Enhanced Efficiency and Quality: A Comprehensive Technical Study(PDF) Optimizing Feed Milling Processes for Enhanced Efficiency 2024年1月17日 Based on the data of global mineral production and ore recovery in mining and mineral processing, this paper presents the annual production of 25 minerals and calculates the annual losses of 20 Parameters for the Grinding Process in Vertical Mills Using Ultrafine vertical mill is a highefficient industrial grinding mill, Advantages of CLUM vertical mill production line Highly automated, Illite ore industrial grinding mill machine can grind illite into powder up to 3000 mesh, including ultrafine mill, Ultrafine Vertical Mill
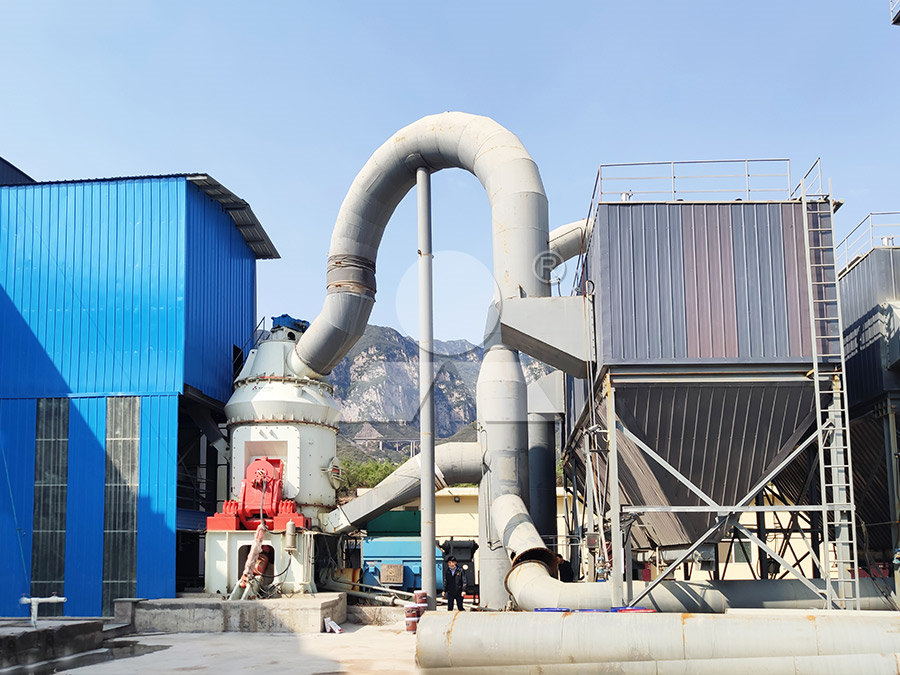
(PDF) Modeling and application of stirred mill for the coarse
2022年5月23日 Grinding experiments were conducted in a laboratoryscale stirred mill on a lowgrade PGE bearing chromite ore HighPressure Grinding Rolls (HPGR) product of −1 mm was used as feed material to Table Energy saving effect of the vertical roller mill Ball mill Specific power Cost estimation About 14million US$ [Newlybuilt] and about 230 million US$ [retrofitted], including the cost of supplemental facilities [200tRM/h] [1US$=¥110] Related matters References Fig1 Vertical roller mill Vertical roller mill Effect(%) Production % 100 Vertical roller mill for raw Application p rocess materialsThe coal vertical mill, also referred to as the vertical roller coal mill, is an advanced equipment developed by our company It combines modern technology with our extensive experience in powder manufacturing This coal pulverizer HighEfficiency Vertical Coal Mill Enhancing Coal 3 Features The EIRICH TowerMill product family ranges in installed power from 10 hp to 1,500 hp / 75 kW to 1,120 kW with throughputs from 05 up to 400 metric tons per hour* *depends on reduction ratio and material propertiesEIRICH TowerMill Vertical agitated media mill
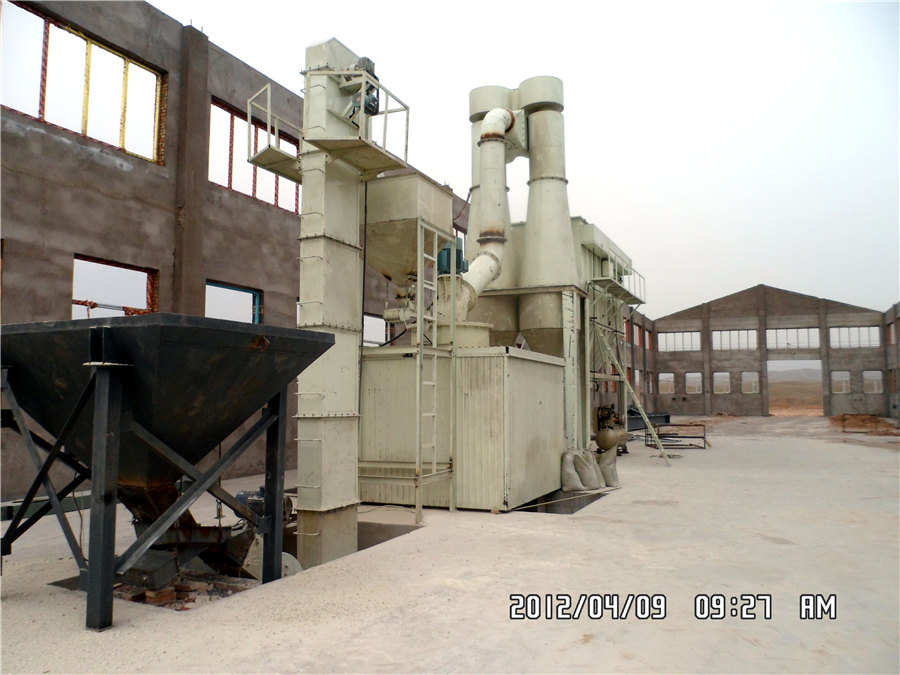
Copper Ore Grinding in a Mobile Vertical Roller Mill Pilot Plant
2014年10月1日 In a test performed in the Loesche test center in Germany, copper slag grinding saved 229% energy in an airswept model and 344% energy in an overflow model [13,14]With years of technical innovation experience in cement and slag grinding, Shanghai Yingyong Machinery Co, Ltd has successfully developed various models of vertical roller mills Our team of specialists is dedicated to assisting customers worldwide in creating dependable, energyefficient, and highperforming solutions for vertical roller mill grindingOptimize Your Grinding Process with Our Vertical Roller MillsFig 1 Flowsheet of modular vertical roller mill 5000 R4 The required throughput rates were achieved in short time All fineness figures met the target values as well without anyGrinding Process Optimization Featuring Case Studies and SBM provides reliable and energysaving technologies and solutions, and its products cover ultrafine grinding mills, vertical mills, wet mills, coarse mills, crushers, CLUM vertical mills are suitable for largescale and highvolume nonmetallic ore grinding production lines The equipment is controlled intelligently, SBM Ore Ultrafine Grinding Mill

Vertical Mill Mining Magotteaux
Magotteaux: The global leader in wear parts for Vertical Mill grinding circuits Magotteaux has established itself as a global leader in wear parts for vertical mill grinding circuits by consistently delivering innovative solutions that address the complex requirements of multiple industries Our commitment to innovation, quality, and customer satisfaction has earned us the trust and The application of vertical roller mills (VRMs) for ore grinding is a part of the strategies against rising energy consumption (Reichert et al, 2015) The VRM technology was introduced in the mid'90s for grinding clinker and slag by LOESCHE (Schaefer, 2001) Fig 1 illustrates the grinding parts of a Loesche vertical roller millModeling and simulation of vertical roller mill using population Journal of Ecological Engineering Volume 18, Issue 5, Sep 2017, pages 37–49 Research Article DOI: 1012911//76210 THE TRANSITIONAL CHANGE ON THE IMPLEMENTATION OF ISO 14001:2015 IN COPPER ORE MILL – CASE STUDY Arif Susanto1,2, Nur Budi Mulyono2 1 2 Doctoral Program of Environmental Science, School of Postgraduate Studies, Universitas THE TRANSITIONAL CHANGE ON THE IMPLEMENTATION OF 2012年9月24日 Copper concentrate regrind at Sossego plant using Vertical Mill conducted in the standard 8"×10 a semiautogenous mill for processing copper and gold sulfide ore The mill is located in Copper concentrate regrind at Sossego plant using Vertical Mill
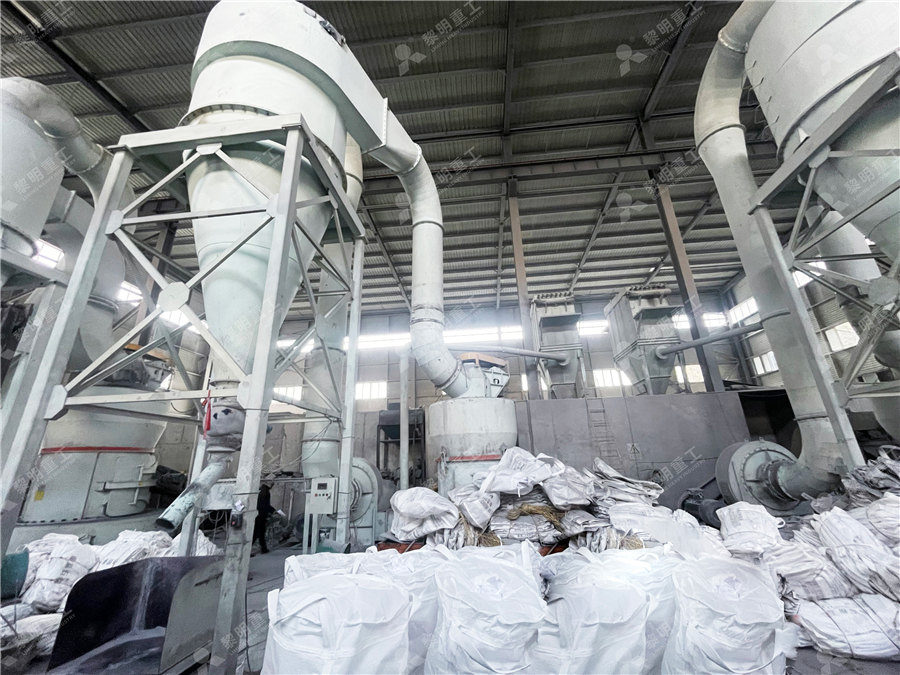
Technical Notebook CEMENT ADDITIVES FOR VERTICAL MILLS
page 05 2 vertical mills introduction page 07 3 principles of vertical grinding systems page 07 31 vertical mill components page 07 32 how does a vertical mill work? page 08 4 a new generation of grinding additives: maga/vm and mape/vm page 08 41 mill output increase page 09 42 quality and water demand optimisation page 09 52 vErTICAl rollEr MIlls INTERNATIONAL CEMENT REVIEW FEBRUARY 2019 to the EU’s ATEX directive and highest international standards Process description The metered and metalfree grinding material is transported to two 150tph raw material silos, from where it is supplied to the mill and fed by the infeed rotary lockvErTICAl rollEr MIlls Improving fuel security Gebr Pfeiffer2015年3月15日 It was found that the ball mill consumed 5467 kWh/t energy to reduce the F 80 feed size of 7222 lm to P 80 product size of 2754 lm while stirred mill consumed 3245 kWh/t of energy to produce Vertical Agitated Media Mill scaleup and simulation Applications of vertical mills in industrial production Vertical mills have become indispensable in modern industrial production, offering numerous benefits and solutions in various sectors In the cement industry, vertical mills are widely employed for grinding raw materials such as limestone, clay, and iron oreApplications of vertical mills in industrial production
.jpg)
(PDF) Operational parameters affecting the vertical roller mill
Grinding test results for zinc ore showed that it is possible to decrease the total grinding energy consumption from 2011 to 1140 kW h/t by using vertical roller mill instead of AG/SAGball mill circuit (van Drunick et al, 2010)The rod mill is another type of grinding mill used in the copper ore mining process This machine uses steel rods as the grinding media instead of balls, which are commonly used in ball mills The rods grind the ore by tumbling within the mill, similar to the action of a rotating drumUnderstanding the SAG Mill in Copper Ore Mining Process2017年10月1日 Recently, the application of Vertical Farming into cities has increased Vertical farming is a cultivating vegetable vertically by new agricultural methods, which combines the design of building A Review of Vertical Farming Technology: A Guide for Implementation JM series vertical stirred ball mills is a kind of high efficiency ultrafine ore grinding equipment (also called tower mill or vertical spiral stirred ball mill), mainly adopted for the ultrafine grinding test research, also for the small scale industry grinding production, to provide reliable technical parameters for industrial production JM Vertical Stirred Ball Mills – ZJH minerals
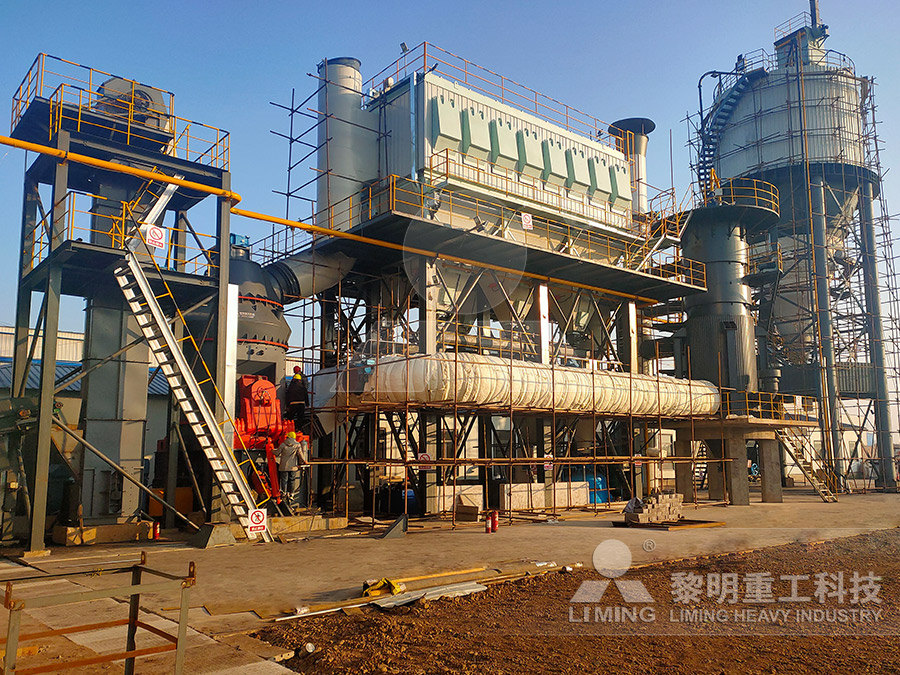
Research of iron ore grinding in a verticalrollermill
2015年3月15日 The grinding parts of a Loesche mill (Fig 1) are a rotating table (1) with a horizontal grinding track and rollers (2), which are pressed onto the table by lever arms and a hydro pneumatic spring systemBetween the working surfaces of track and rollers, particle bed comminution takes place A dynamic air separator (3) is located above the grinding chamber,