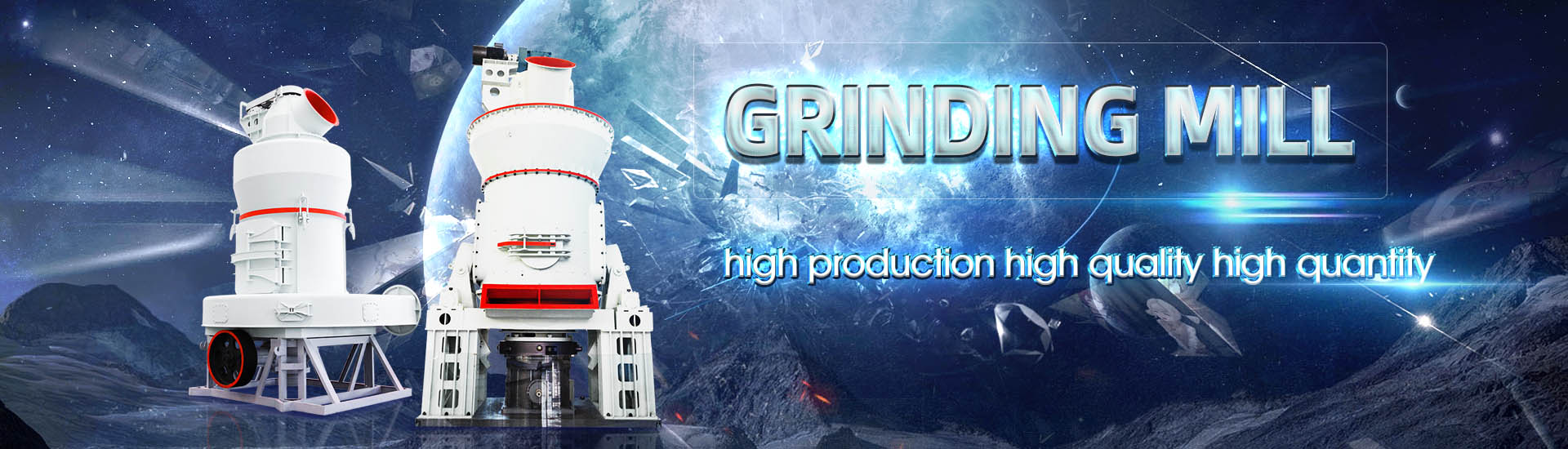
Which 5000 ton cement mill to use
.jpg)
5000 TPD Cement Production Line CEMENTL
Tongli 5000 TPD cement production line includes: rotary kiln, vertical mill, ball mill, rotary kiln cooler and automatic control pared with traditional cement production line, the 5000t/d cement plant designed by Chaeng uses lower energy consumption equipment in the main part of energy consumption, such as 5000 t/d Cement Plant CHAENGThe cement mills are equipped with high efficiency separators to achieve cement qualities with a fineness up to 5 000 cm2/g acc to Blaine tkplay Cemento Progreso, Guatemala, 4500 tons per day plant incl QMR² and QMC²quadropol® thyssenkrupp Polysius Grinding The raw mill is used to grind raw materials into “raw mix” during the manufacture of cement Equipment: Ball mills, vertical roller mills Technical Specifications: Ball Mills: 1030 tons/hour capacity, 5001500 kW motor power Vertical Roller The Comprehensive Guide to Cement Plant Costs: An
.jpg)
Cement Vertical Roller Mill CEMENTL
Ideal for grinding hard, highabrasive materials with high moisture contents, such as clinker, limestone, and furnace slag, our vertical roller mill delivers consistent raw material preparation Cement, made by calcining and grinding limestone and other raw materials, is the most widely used building material As a professional cement company, FTM Machinery offers expert guidance for your cement production How to Make Overview of Cement Making Machine (with Price and Product Name: Mini Cement Plant Capacity: 100 – 700 TPD Equipment: cement crusher, conveyor, preheater, rotary kiln, cement mill, etc Cement plants with a clinker capacity below 700tpd can be called mini cement plants or small Cement Line Capacity 70 600 TPD Mini Cement Compact and easy to install, the FCB Horomill® offers process specificities that are ideal for modern cement plants Thanks to its advanced technology and its use in combination with the Fives Sustainable grinding with FCB Horomill®
.jpg)
Vertical Cement Mill Magotteaux
Magotteaux’s proprietary vertical cement mill technology has been developed through decades of innovation and expertise in grinding processes Our vertical cement mill wear parts are Cement milling Finish milling is the grinding together of clinker with some 35 per cent gypsum, natural or synthetic, for set control, and quite often other components:The Cement Plant Operations Handbook International Cement 2022年3月16日 The cement ball mill is usually around a few tons, because of the cooling effect of water, so the output can be increased appropriately Small cement ball mills have a wide range of uses, What is a Cement Ball Mill? How to Use It? by 2015年6月30日 One ton of cement produces approximately one ton of carbon dioxide, which is released into the atmosphere [1] Therefore, the Portland cement manufacturing process contributes 68% of greenhouse Energy consumption assessment in a cement production plant
.jpg)
Finish grinding INFINITY FOR CEMENT EQUIPMENT
Normally about 02 m3(min of air per mill kW is drawn through a single compartment mill, compared to 01204 m3/min per mill kW in a multicompart ment mill For effective cooling Lurje [129] recommends for mul ticompartment In cement industry about 110 kWh of electrical energy is consumed to produce one ton of cement and about 26% of the total electrical power is used during farine productionThe use of electrical energy in cement productionFor an OK mill grinding a similar product, the cost of wear parts depends on the maintenance procedures, ie whether hardfacing is applied If hardfacing is not applied the cost is as for the ball mill, ie 015020 EUR per ton of cement If hardfacing is applied, the corresponding figure will be 010015 EUR per ton of cementCement grinding Vertical roller mills VS ball millsHow to Read a Portland Cement Mill Test Report David J Imse, PE Skyway Cement Company, 300 – 500 m2/kg (3000 – 5000 cm2/g) ASTM C204 Blaine Fineness • Blaine Over 118 million tons of combustion byproducts are produced and captured • How to Read a Portland Cement Mill Test Report DocsLib

5000 Ton Dry Process Cement Plant PENGFEI Group
A vertical grinding mill is available for raw material grinding, reducing power consumption by 57kW×h/t Our 5000 ton dry process cement plant is designed to reduce pollution and energy consumption With exquisite designs, it is capable of saving 2013年6月6日 A CEMENT company is expanding its plant in the Visayas to meet Naga City by at least 15 metric tons per year The vertical mill is set to be completed by the second quarter of next year New mill to increase cement production Inquirer NewsThe mill used for this comparison is a 44meter diameter by 136 meter long ball mill with a 5000 HP drive motor It is designed for approximately 90 ston per hour This type twocompartment mill is a state oftheart shell supported cement finish mill The torque and time requirements of the mill with the ballBALL MILL DRIVE MOTOR CHOICES Artec Machine2 Raw Mill The raw mill is used to grind raw materials into “raw mix” during the manufacture of cement Equipment: Ball mills, vertical roller mills Technical Specifications: Ball Mills: 1030 tons/hour capacity, 5001500 kW motor power Vertical Roller Mills: 2050 tons/hour capacity, 10003000 kW motor power Example Brands:The Comprehensive Guide to Cement Plant Costs: An InDepth
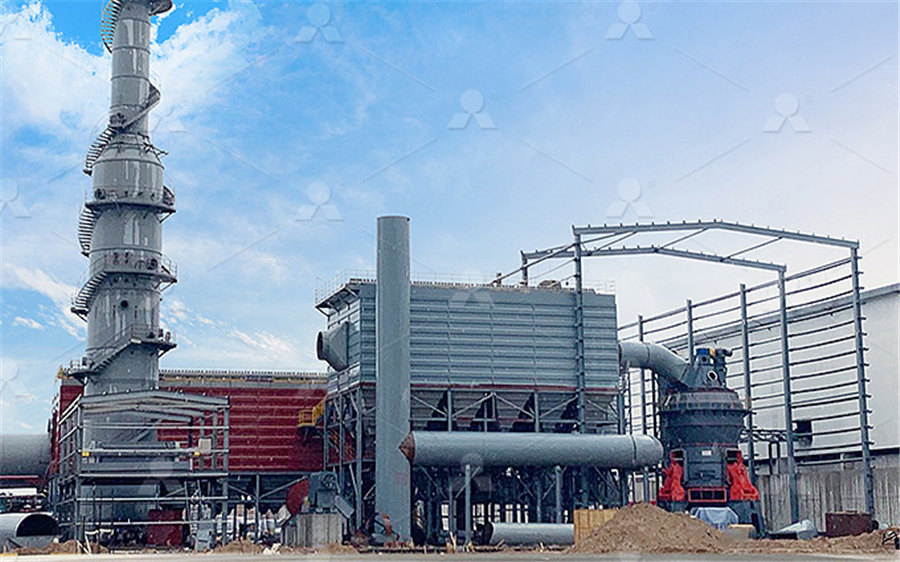
Coal and its application in the cement production
2021年8月29日 A year, factories usually have to produce about 800,000 tons of clinker, if in the past they had to use more than 136,000 tons of 4A bran coal, now thanks to the application of the solution of using coal oxide in the production of Internationally, the cement produced in the US has a relatively high carbon intensity, expressed as emissions per ton of cement capacity for plants up to 22005000 tpd) and planetary coolers (used for 10% of the world Kingdom Everything you need to know about Energy Efficiency In the current practice, onestring preheaters are usually proposed for a production rate of up to 50006000 ton/day A twostring preheater is recommended for production rates higher than 6000 ton/day For production Everything you need to know about Preheaters and A cement mill (or finish mill in North American usage [1]) is the equipment used to grind the hard, nodular clinker from the cement kiln into the fine grey powder that is cement Most cement is currently ground in ball mills and also vertical roller mills which are more effective than ball millsCement mill Wikipedia
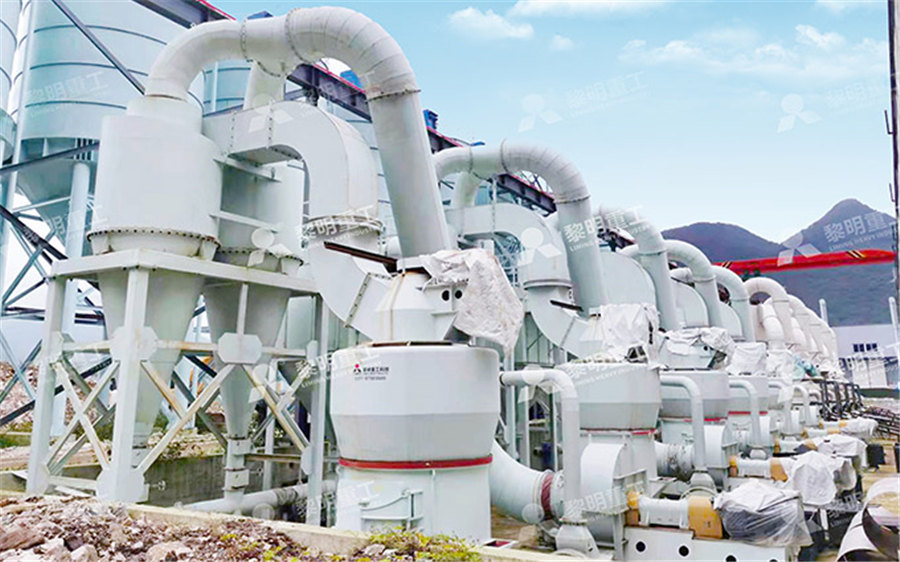
IMPROVING THERMAL AND ELECTRIC ENERGY EFFICIENCY AT CEMENT
2019年3月8日 use and now account for over 90 percent of cement consumption worldwide (41 billion tons in 2016) Cement accounts for at least 5 percent of anthropogenic emissions of greenhouse gases, and Cement mill fans is a longterm supporting product of 3000~5000: 730~960: 400~900: Grate Cooler Fan: The air: 20: 20000~50000: 6000~13000: 1450~2900: In cement industry raw mill exhaust fans handle 22 ton of exhaust gases for the production of 1 ton of clinker Raw mill exhaust fans are operated with very adverse situations because the Cement mill fansFor example, the power consumption of Pizhou China United cement grinding has been reduced to 23 degrees per ton, Manufacturing Plant solutions and equipment for various sizes of Cement Manufacturing Plant, we can customize the cement mill types of equipment for each step of the cement production process, from raw material crushing, Power Consumption of Cement Manufacturing PlantThe consumption of energy by the cement grinding operation amounts to one third of the total electrical energy used for the production of cement The optimization of this process would yield substantial benefits in terms of energy savings and capacity increase Optimization of the Cement Ball Mill OperationOPTIMIZATION OF CEMENT GRINDING OPERATION IN BALL MILLS
.jpg)
The Improvement of Mill Throughput Using Barmac
ABSTRACT The increasing demand for ‘‘finer cement’’ products, and the need for reduction in energy consumption and green house gas emissions, necessitate the optimization of grinding circuitsPeople in the cement industry use the terms“harder to burn” and “easier to burn a consistent, reliable kiln feed metering system The feed kiln rate is typically ratioed to the kiln speed (eg, 15 tons of kiln feed per 10 revolutions of A typical direct firing system uses a mill/fan combination to simultaneously Everything you need to know about Kiln System Operations in Cement AGICO CEMENT is a cement equipment manufacturer provides cement mill, cement calssifier and related cement equipment needed in the cement plant FREE to ask now! Skip to content +86 info@cement How To Measure Your Cement Mill And Cement A cement grinding mill "A" with a capacity of 50 tons per hour utilizes forged steel grinding balls costing P12, 000 per ton, which have a wear rate of 100 grams per ton cement milled Another cement mill "B" of the same capacity uses high chrome steel grinding balls costing P50, 000 per ton with wear rate of 20 grams per ton cement milledAnswered: A cement grinding mill "A" with a bartleby
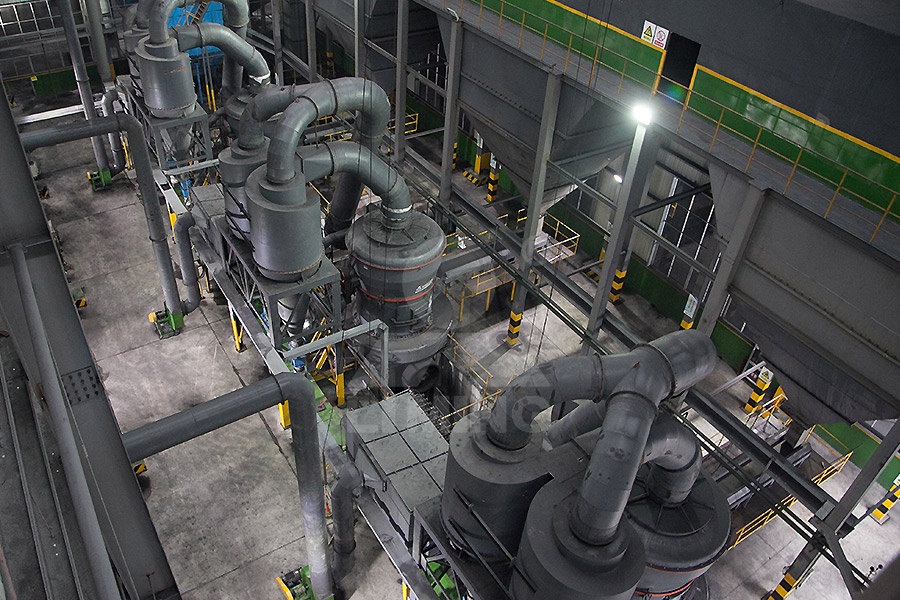
5000 Tons/Day New Type Dry Process Cement Production Line
The 2500t / d cement clinker production line adopts a new dry process, with an annual output of 775,000 tons of cement clinker and a total cement output of 105 million tons / year A cement production line and auxiliary facilities from limestone crushing to We are ready to help you to start your new plant to produce cement, minimum quantity is 100 tons per day ,8 hours, proximate cost US$ 4 million, so if you have this financial capacity , or if you use big amounts of cement is very interesting, maybe you produce big quantities of concrete products like, concrete blocks, concrete pavers, concrete roof tiles other concrete products so you better How to Start a Cement Mill Business2023年1月1日 Clinker along with up to 5% gypsum is ground together in a cement mill older cement production facilities can result in CO 2 emissions of about 1000 kg CO 2 per ton cement clinker The replacement of some portion of the Portland cement used in a specific concrete mixture offers potential as a method of reducing environmental impactCoal utilization in the cement and concrete industries2021年7月28日 kWh/ton of Material Technology; 070: Single Stage Crusher: 065: Double Stage Crusher: 1110: Raw Mill Vertical Roller Mill: 1650: Raw Mill Ball Mill: Cement Mill Ball Mill Closed Circuit: 2320: Cement Mill Ball Mill with HPRG: 065: Packing Plant: 067: Compressor upto clinkerisation:Indian Cement Sector CMA
.jpg)
Vertical Cement Mill Magotteaux
Understanding Our Proprietary Vertical Cement Mill Technology Magotteaux’s proprietary vertical cement mill technology has been developed through decades of innovation and expertise in grinding processesOur vertical cement mill wear parts are designed to provide optimal grinding efficiency, quality, and reliability for cement productionOur systems and parts are like no 2020年4月4日 Flying cement is a cement capacity 5000 tons/day factory Right now they use soft starter to drive vertical roller mill Figure 1 The original main electrical circuit diagram Detailed motor parameters are list as follow: Table 1Vertical Motor ParametersINVT GD5000 MV Drive for Cement Vertical Raw Mill 63KV Heavy 2013年6月25日 Rather than filing and forgetting after the cement delivery, use the mill certificate to your Logically, then, no single sample – be it a small sample for laboratory testing or a 30ton bulk delivery – will have exactly the composition or performance reflected by the average values in the accompanying certificate To How to Read a Cement Mill Certificate: Part 1The amount of CO2 produced for 1 ton of cement can vary depending on a number of factors, including the specific production process, the type of kiln used, and the source of the fuel used However, on average, it is estimated that the production of 1 ton of cement results in the emission of around 900 kg of CO2 [PCA]Cement Production Demystified: StepbyStep Process and
.jpg)
50 ton cement silo
50 ton cement silo, 1Esay to delivery, 2 Customized sizing and layout to specific requirement, 500020000kg: color:optional : Facebook Twitter LinkedIn Google Google+ 50 ton 1 , usage for grain storage 2 , Hopper type silo have selfflow function 3 , can be used in plant ,mill for seeds and feeds 800 ton Cereal Steel Silo,assembly High quality Daily Capacity 5000~12000 Tons Cement Plant Equipments Large Cement Equipment from China, It is one of the few enterprises capable of providing complete sets of cement main equipment, and produces the largest Daily Capacity 5000~12000 Tons Cement Plant2016年3月1日 Assuming 57Bnt of cement production in 2050 and 350400Mt of coal8 used to produce 42Bnt of cement in 2014, we arrive at coal consumption of 475 540Mt for the cement industry in 2050 However, this is not the end of the calculationCoal for cement: Present and future trendsA cement grinding mill "A" with the capacity of 50 tons per hour utilizes forged steel grinding balls costing P12,000 per ton, which have a wear rate of 100grams per ton cement milled Another cement mill "B" of same capacity uses high chrome steel grinding balls costing P30,000 per ton with wear rate of 10grams per ton cement milledAnswered: A cement grinding mill "A" with the bartleby
.jpg)
Answered: A cement grinding mill “A” with a bartleby
A cement grinding mill “A” with a capacity of 50 tons per hour utilizes forged steel grinding balls costing Php12,000 per ton, which have a wear rate of 100 grams per ton cement milled Another cement mill “B” of the same capacity uses high chrome steel grinding balls costing Php50,000 per ton with a wear rate of 20 grams per ton cement The vertical roller mill (VRM) is a type of grinding machine for raw material processing and cement grinding in the cement manufacturing processIn recent years, the VRM cement mill has been equipped in more and more cement plants around the world because of its features like high energy efficiency, low pollutant generation, small floor area, etc The VRM cement mill has a Vertical Roller Mill Operation in Cement PlantPENGFEI dry process cement plant avails of MLS3626 vertical grinding mill, designed to produce 2500 tons of cement clinker everyday Its φ4×60m rotary kiln combines preheating and decomposing system and fivestage cyclone preheater2500 Ton Dry Process Cement Plant PENGFEI Group2020年4月4日 Keywords: GD5000, Medium voltage inverter, Vertical raw mill, Cement industry 1 Brief introduction So far, INVT GD5000 series MV drives already widely used in Cement industry for applications like ID fan, FD fan, Boiler feed pump, pre INVT GD5000 MV Drive for Cement Raw Mill 11KV 4MW Motor
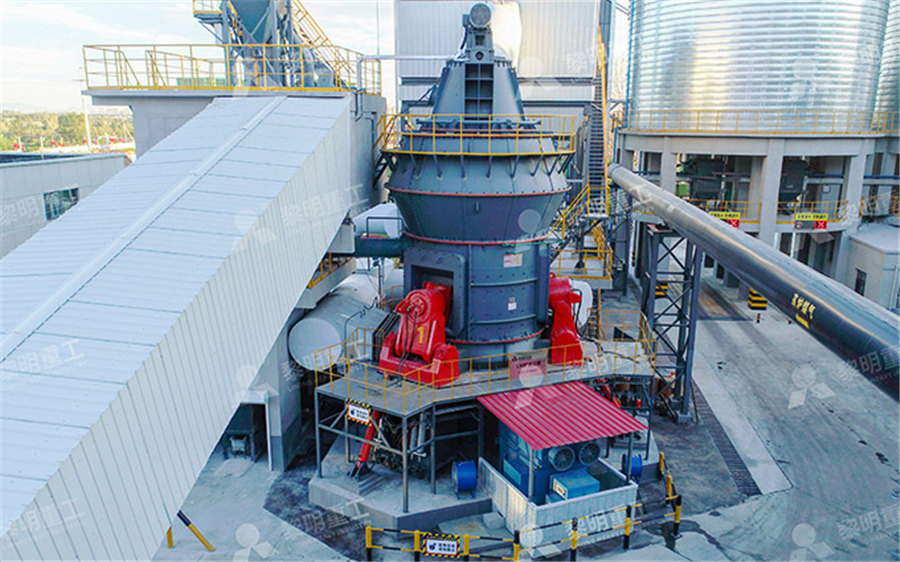
Cement ball mill DARKO
A cement ball mill has the capacity typically ranging from 10 to 300 tons per hour A cement ball mill is a crucial piece of equipment in the cement manufacturing process, used for grinding clinker and additives into fine cement powder It operates by rotating a cylinder filled with steel balls, 2008年8月1日 KO TINI AND HASSAPIS: A HYBRID A UT OMA TON MODEL OF THE CEMENT MILL CONTR OL 685 Fig 5 Mill automaton with hardness value 143 Let us now consider the limited number of experimental dataA Hybrid Automaton Model of the Cement Mill Control