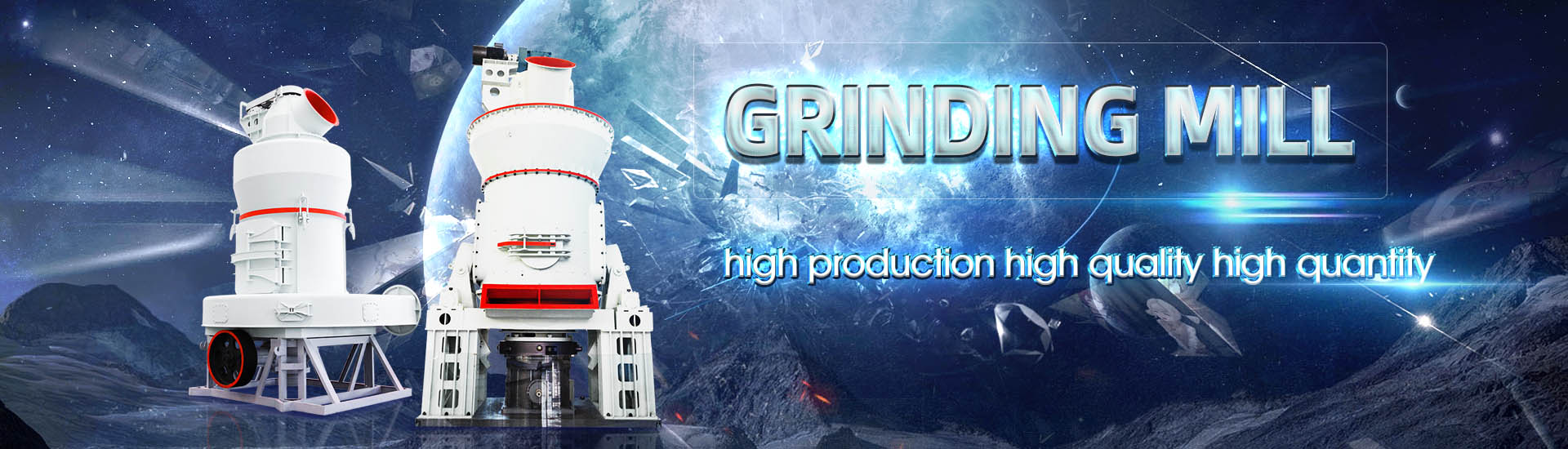
Safety regulations for pulverized coal preparation system
.jpg)
Fire and Explosion Prevention in Coal Pulverizing Systems
The Riley Stoker Corporation coal pulverizing system utilizes the following design and operating principles to maximize safety and availability: l Design in accordance with the NFPA code recommendations where applicable for containment strength, combustion controls, and flame 2005年2月14日 This technical standard specifies requirements for explosion prevention design of coal and pulverized coal preparation systems in fossil fuel power plants It provides Technical Code For Explosion Prevention Design of Coal and 2022年5月13日 根据《中华人民共和国标准化法》《能源标准化管理办法》,国家能源局批准《智能风电场技术导则》等209项能源行业标准(附件1)、《Specification for Preparation of DL/T 52032022 火力发电厂煤和制粉系统防爆设计技术 In the present investigation, pulverized coals with high volatile contents are used as deoxidizer in aluminum silicon smelting process using “Submerged Arc Furnace” (SAF) method SAF Coal Pulverization System: Explosion Prevention and Process Control
.jpg)
27772021 IEEE Recommended Practice for Operation of 300
2021年4月30日 This recommended practice defines the principles and procedures for startup, normal operation, shutdown, daily operation, and maintenance during normal and emergency This study reviews issues related to the efficient and safe operation of coal pulverising systems for large power station boilers Commercial considerations and the need to comply with Coal pulverisers performance and safety, IEACR/79 ICSC2022年10月24日 31 煤粉制备系统 pulverized coal preparation system 水泥工厂熟料煅烧所用煤粉的制备系统,主要包括原煤仓、煤磨(立磨或球磨)、选粉机、煤磨除尘器、煤粉仓、煤粉 水泥工厂煤粉制备系统防火防爆安全规程(征 蚂蚁文库Cite this article: CAO Huihui Safety management method of pulverized coal preparation system[J] Journal of Cement, 2020, 0(9): 41 URL:Safety management method of pulverized coal preparation system
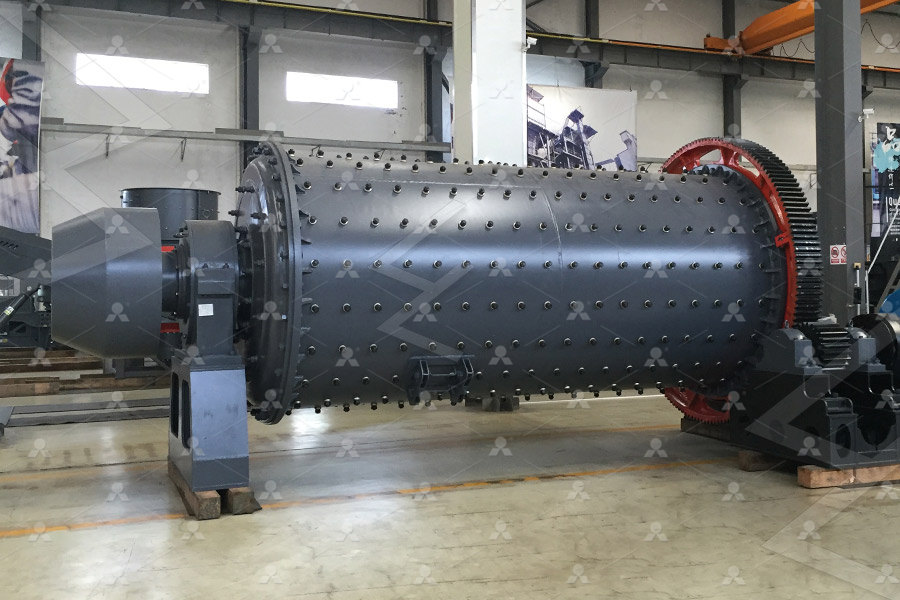
Pulverised Coal an overview ScienceDirect Topics
Pulverized coal (PC) combustion is presently the system of choice for coalfired powergenerating plants In PC combustion, the coal is dried and is ground to a specified fineness, with a Hot blast backpressure as well as pressure drops in pneumatic conveying lines and flow rate control devices require a pressurizing of pulverized coal from atmosphere pressure level to Pulverized Coal Injection Paul Wurth2024年1月1日 The blast furnace injection process system is mainly composed of raw coal storage and transportation system, dry gas preparation system, pulverized coal preparation system, pulverized coal conveying system, pulverized coal injection system, and gas supply system (Fig 1)There is also a computer control center to control the entire pulverized coal Pulverized Coal Injection of Blast Furnace IronmakingFuel preparation for a pc boiler occurs in a mill, where coal is typically reduced to 70% through a 200mesh (74μm) screen Figure 2 shows a particlesize distribution from a bowlmill grinder typically used in power plants A typical utility specification for particle size distribution of the coal is that 70% of the mass should pass through a 200mesh screen, which is equivalent to 70% Pulverized Coal Boiler an overview ScienceDirect Topics
.jpg)
Characteristics of combustion and ash deposition for pulverized coal
2024年2月6日 Loadfollowing operations of coal power plants are required to cope with the variability in power generation from renewable energy sources This study aimed to optimize combustion in coalfired power plants at low loads by analyzing combustion efficiency, NOx emissions, and ash deposition in a boiler An experiment was conducted by varying the heat 2005年2月14日 This technical standard specifies requirements for explosion prevention design of coal and pulverized coal preparation systems in fossil fuel power plants It provides definitions for key terms related to pulverized coal explosibility and explosion prevention The standard covers system configurations, building structures, equipment design, instrumentation and Technical Code For Explosion Prevention Design of Coal and Pulverized Read chapter 5 COAL PREPARATION, COALLIQUID MIXTURES, AND COALBED Nevertheless, one Pennsylvania utility (Penelec) is currently investigating cofiring its pulverized coal utility boilers with a CWS to provide 20 to (DOE, 1994b) Coalbed methane liberated into mine workings by underground coal mining can be a serious safety 5 COAL PREPARATION, COALLIQUID MIXTURES, AND COALBED 2023年1月13日 The paper provides an outlook on future directions of research and the possible applications for pulverized coalfired boilers One potential direction for future research is to focus on the ways to improve the efficiency of pulverized coalfired boilers This could involve developing new combustion technologies that are able to more thoroughly burn the coal and Pulverized CoalFired Boilers: Future Directions of Scientific
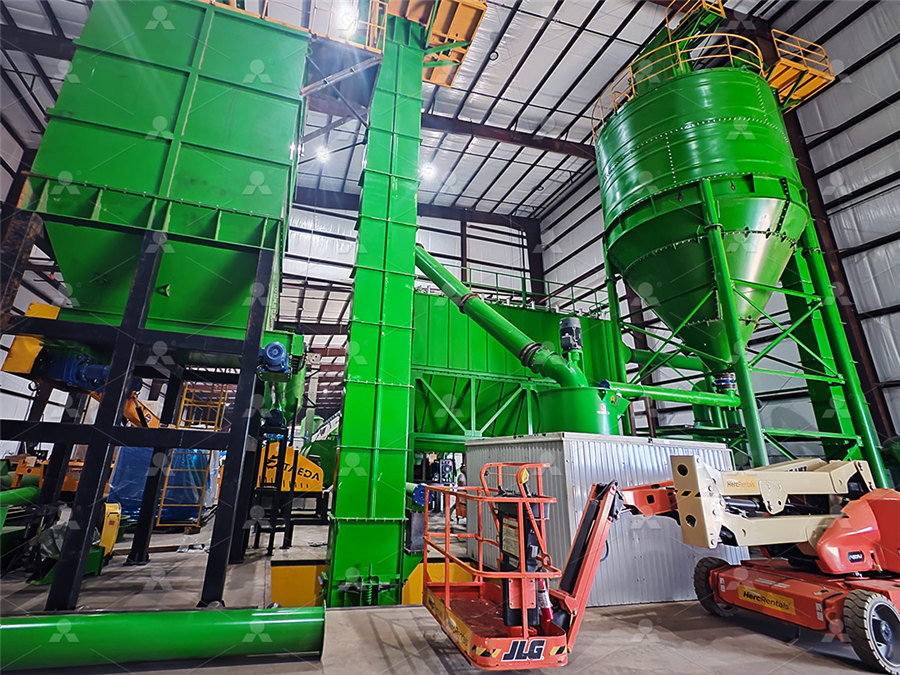
Design for Safety Management System of Coal preparation Plant
2011年1月1日 Table2 Choice Table of safety assessment method Sequence number The evaluation units (evaluation objects) Evaluation methodology 1 The whole operation site of coal preparation plant fuzzy comprehensive evaluation 2 Raw coal system Safety check list method〠event tree analysis 3 Coal storage and return system The preliminary hazard analysis〠Product Name • Lignite Coal Synonyms • Coal Relevant identified uses of the substance or mixture and uses advised against Recommended use • Fossil fuel heat source for power generation and coal gasification Details of the supplier of the safety data sheet Manufacturer • Dakota Coal CompanySafety Data Sheet Section 1: Identification Product identifier23 Pulverizer Designs and Pulverized Coal Handling Coal preparation predated pulverized coal firing, particularly for stoker units where sizing has always been very important, particularly in the minimizing of fines Predating the development of pulverized coal firing came the development of pulverizers used in the processing of mineralsPulverised Coal an overview ScienceDirect TopicsCompared to raw coal, pulverized coal boasts a smaller particle size, a larger surface area, and a certain level of explosiveness SRON meticulously considers anticombustion and antiexplosion measures during the design process of the pulverized coal silo, an essential component for the preparation, storage, and supply of pulverized coalPulverized Coal Steel Silo – Coal Storage Silo – Coal Storage
.jpg)
Pulverized coalfired boiler Wikipedia
A pulverized coalfired boiler is an industrial or utility boiler that generates thermal energy by burning pulverized coal (also known as powdered coal or coal dust since it is as fine as face powder in cosmetic makeup) that is blown into the firebox The basic idea of a firing system using pulverised fuel is to use the whole volume of the furnace for the combustion of solid fuels• Use of water spray systems and /or polymer coatings to reduce the formation of fugitive dust from coal storage (eg on sto ckpiles) as feasible depending on the coal quality requirements; • Capture of coal dust emissions from crushing / sizing activities and conveying to a baghouse filter or other particulate control equipment ;Environmental, Health and Safety Guidelines for Coal Processing2022年9月1日 This paper presents plasma technology for pulverisedcoal ignition and improving energy efficiency of power stations Plasma–fuel systems (PFS) were developed to accomplish this technologyPlasma Ignition System to Start Up Pulverized Coal 2020年1月7日 Pulverized coal industrial boilers are widely used in China in recent years for high thermal efficiency and suitable for contract energy management, especially the in service amount is growing Fuel characteristics and explosiveness analysis of pulverized coal
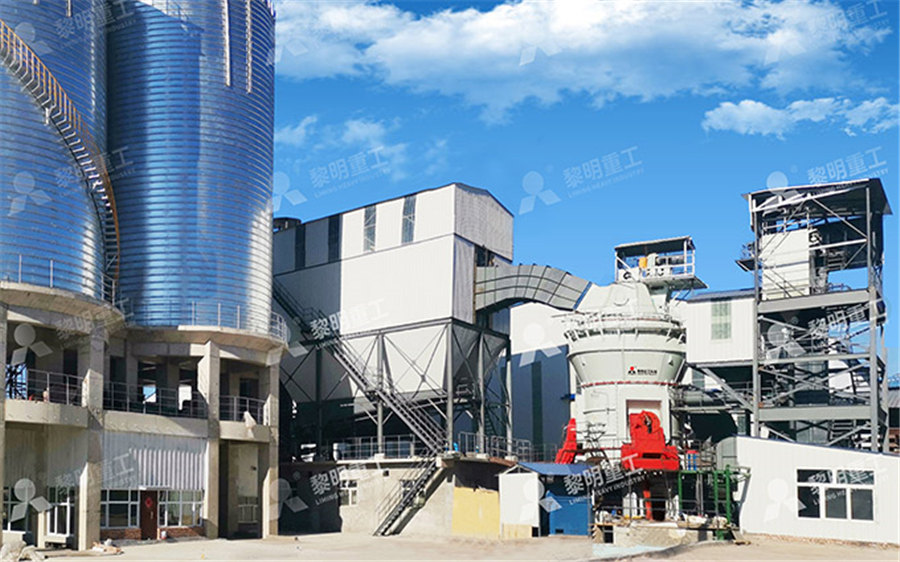
Coal Pulverization System: Explosion Prevention and Process
80 • Measurement + Control Vol 42/3 April 2009 instmcuk instmcuk Measurement + Control Vol 42/3 April 2009 • 81 Feature: Coal Pulverization System: Explosion Prevention and Process Control Coal Pulverization System: Explosion Prevention and Process Control Abstract: A pulverized coal processing system for produc ing coal powder used in 2022年8月10日 One of the promising ignition technologies is the plasma thermochemical preparation of pulverized coal for combustion using plasmafuel systems (PFS) This technology allows increasing the efficiency of fuel application and improving the environmental performance of thermal power plants, as well as eliminating fuel oil, used traditionally to ignite boilers and Plasma ignition of solid fuels at thermal power plants Part 1 2007年3月1日 A pulverized coal preparation system is one of the indispensable main systems for coalfired boilers in thermal power plants and its operation safety, reliability and costeffectiveness directly Causes of pulverizedcoal leakage from a race pulverizer and its Steel Production: In the steel industry, pulverized coal injection (PCI) is used in blast furnaces to reduce coke consumption and enhance furnace efficiency Cement Production: Pulverized coal is used as a fuel in rotary kilns for cement production, contributing to the clinker formation process Benefits of Pulverized Coal The use of Understanding Pulverized Coal: Benefits, Risks, and Safety
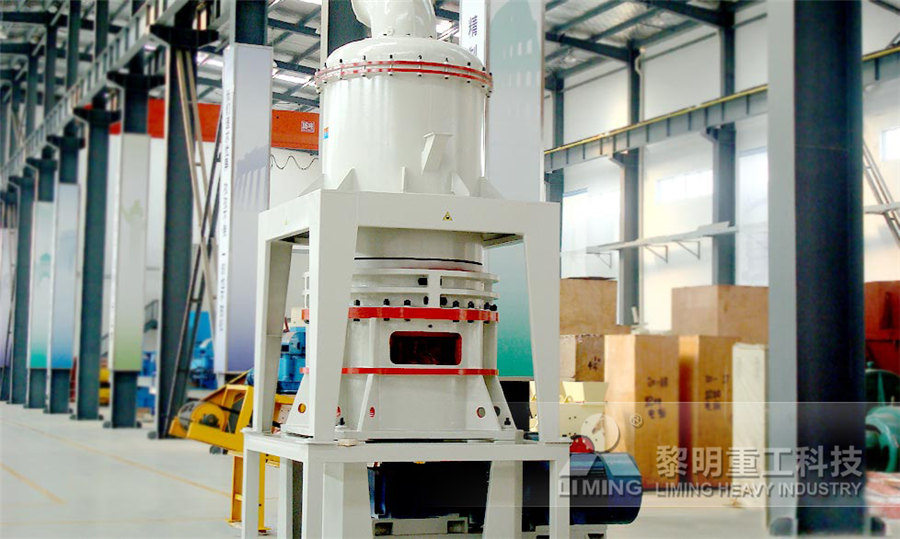
Plasma thermochemical preparation for combustion of pulverized coal
2017年5月1日 A plasma model of thermochemical preparation for the combustion of pulverized coal implemented through the PlasmaKinTherm program for the calculation of plasmafuel systems has been described2012年2月24日 The ash handling is more straightforward in this system since there is no solid ash Disadvantages of Pulverized Coal Firing The initial investment in pulverized coal firing system is more compared to solid firing system The running cost is also higher The pulverized coal produces fly ashesPulverized Fuel Firing of Boiler Electrical4UFig 6 General scheme of plasma arc burner system for pulverized coal combustion In Fig 7, pulverized coal flame of plasma arc burner is shown Fig 7 Pulverized coal flame of plasma arc burner In addition, the results of chemical analysis of the metal that has been smelted from coal ash are shown in Figs 813 Fig 8 Electron imagePlasma Arc Burner for Pulverized Coal Combustion Zenodo2018年10月21日 Fig 1 Pulverized coal combustion and gas composition in raceway The extent of combustion (combustion efficiency), and hence the amount of unburnt material transported out of the raceway, depends on several parameters which include (i) properties of the coal, such as the VM content, particle size and density, and (ii) operating conditions, for example, blast gas Understanding Pulverized Coal Injection in Blast Furnace
.jpg)
Modelling of the pulverized coal plasma preparation for
2021年6月1日 One of the promising ignition technologies is plasma thermochemical preparation of pulverized coal fuel for combustion (PTPC) [3, 4] using plasmafuel systems (PFS) The most common PFS scheme is 2021年4月20日 In general, the effect of biomass direct cofiring on safety, pulverizing system performance, furnace efficiency, and NOx emission in fullscale furnaces is rarely studiedExperimental Study and Design of Biomass CoFiring in a FullScale Coal High Efficiency Pulverized Coalfired Power Generation Technology 4D2 Lowrank Coal Upgrading Technology 4C1 Coal Cartridge System (CCS) 4C2 Coal Water Mixture Production Technology (CWM) 4C3 safety and preparationTechnology Innovation in the Coal Industry 一般財団法人 2022年1月27日 The explosion of coal mill system in cement production is related to various reasons, so in the production of pulverized coal, attention should be paid to controlling the concentration DISCUSSION ON SAFETY PRODUCTION OF COAL MILLING SYSTEM
.jpg)
Coal Preparation Systems for Boilers Springer
of coal preparation systems Pulverized coal (PC) firing is the dominant method used in modem power sta tions So, most of this chapter will focus on coal preparation systems for PC boilers and their design Fluidized bed (FB) firing is developing very quickly and find ing its way to wider applications in largescale commercial boilers1996年12月4日 Coalfired boiler systems will continue to be major contributors in the future New pulverized coalfired systems routinelyinstalled today generate power at net thermal cycle efficienciesranging Technology Development for Advanced Pulverized CoalFired 6 Sampling, DirectFired System 61 In the directfired system, the coal is pulverized and delivered directly to the furnace in an air stream It is difficult to obtain representative samples, as it is necessary to sample the coal from a moving stream of coalair mixture inside the pipe between the pulverizer and furnace It is preferable toStandard Test Method for Sampling and Fineness Test of Pulverized Coal25 10Modelling pulverized coal of the plasma pulverized preparation
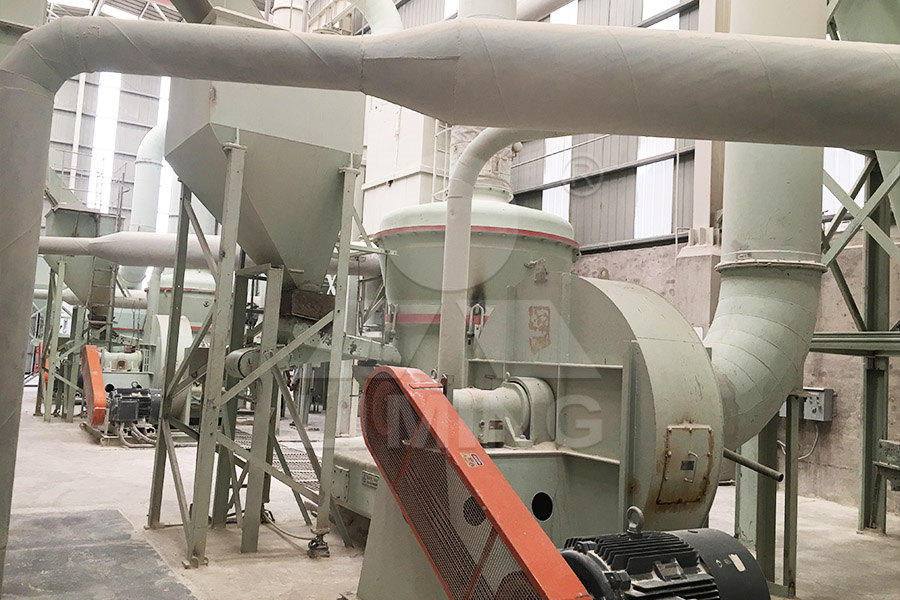
Research on PLC Based Pulverized Coal Sample Preparation
2013年1月1日 In view of China’s current coal crushing equipment size is too large, this paper aim to design a small coal sample preparation system This system utilizes the principle of the cone crusher for Coal being fed into any combustion system normally contains moisture Typically, anthracite has moisture contents between 2 and 45% Bituminous and subbituminous coals have typical values of 1–122% and 141–31%, respectively However, lignite and brown coal have values of Fundamentals of pulverised coal combustion ICSC2023年6月15日 The blast furnace injection process system is mainly composed of raw coal storage and transportation system, dry gas preparation system, pulverized coal preparation system, pulverized coal conveying system, pulverized coal injection system, and gas supply system (Fig 1)There is also a computer control center to control the entire pulverized coal Pulverized Coal Injection of Blast Furnace Ironmaking• Use of water spray systems and /or polymer coatings to reduce the formation of fugitive dust from coal storage (eg on sto ckpiles) as feasible depending on the coal quality requirements; • Capture of coal dust emissions from crushing / sizing activities and conveying to a baghouse filter or other particulate control equipment ;Environmental, Health and Safety Guidelines for Coal Processing
.jpg)
COAL GRINDING SYSTEMS SAFETY CONSIDERATIONS PEC
pulverized coal that then ignites explosively Also, an inrush of air may create a pulverized coal dust cloud that explodes Accumulations of Pulverized Coal Dust All leaks, spills, and any accumulations of coal or coke dust must be cleaned up promptly around coal mill grinding and firing systems ecause of the potential for spontaneous b pulverized coalfired systems to meet future power generation needs in a cost effective and environmentally acceptable manner Key trends in these efforts include:Technology Development for Advanced Pulverized CoalFired 6 Sampling, DirectFired System 61 In the directfired system, the coal is pulverized and delivered directly to the furnace in an air stream It is difficult to obtain representative samples, as it is necessary to sample the coal from a moving stream of coalair mixture inside the pipe between the pulverizer and furnace It is preferable toStandard Test Method for Sampling and Fineness Test of Pulverized Coal2021年4月30日 Scope: This recommended practice defines the principles and procedures for startup, normal operation, shutdown, daily operation, and maintenance during normal and emergency conditions for a 300 MW to 600 MW pulverized coalfired boiler and its main auxiliary equipment This recommended practice applies to 300 MW to 600 MW pulverized coalfired 27772021 IEEE Recommended Practice for Operation of 300

Coal Preparation SpringerLink
According to the annual census of coal preparation plants conducted by Coal Age [], the USA operates 286 coal preparation plants in 12 statesThis number is relatively small by comparison to the worldwide fleet which is estimated to be 2,283 plants []The capacity of the plants can range from less than 200 t/h for small operations to 6,000 t/h or more for large industrial plantsPulverized Coal Injection Tank Pressure Control Using Fuzzy Based Gain Regulation for Model Reference Adaptive Controller Özgür Aslan 1 , Rıfat Hacıoğlu 2 , Aytaç Altan 2Pulverized Coal Injection Tank Pressure Control Using Fuzzy Based