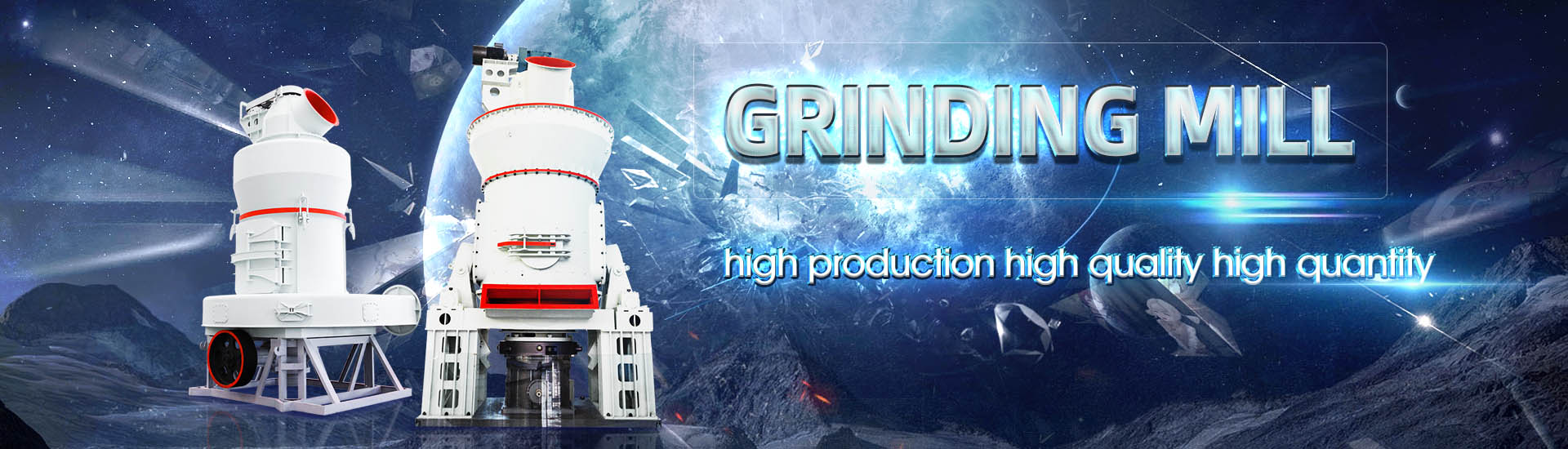
Successful case of adding crushing system to coking plant
.jpg)
Industrial perspective of the cokemaking technologies
2019年1月1日 The adoption of precarbonization technologies, viz, partial briquette, selective crushing, preheating, and stamp charging, was chosen based on the overall technoeconomics Based on the study, the stamp charge cokemaking technology was found suitable based on A main parameter of operation is the bulk density of the coals which can be controlled within the coal handling system upstream of the batteries by screening, crushing, drying and adding Effects and impacts of components of coal handling system on Based on the basic investigation, we tried the fine crushing of high coking pressure coal at commercial cokemaking plants, and it was confirmed during a longterm commercialscale Coking Pressure Control by Selective Crushing of High Coking 2019年10月23日 We have outlined the main innovations in carbon intake, storage, dosing, and crushing in response to the declining quality of coal concentrates for coking batch Rammed Innovations in Coal Preparation and Coke Sorting
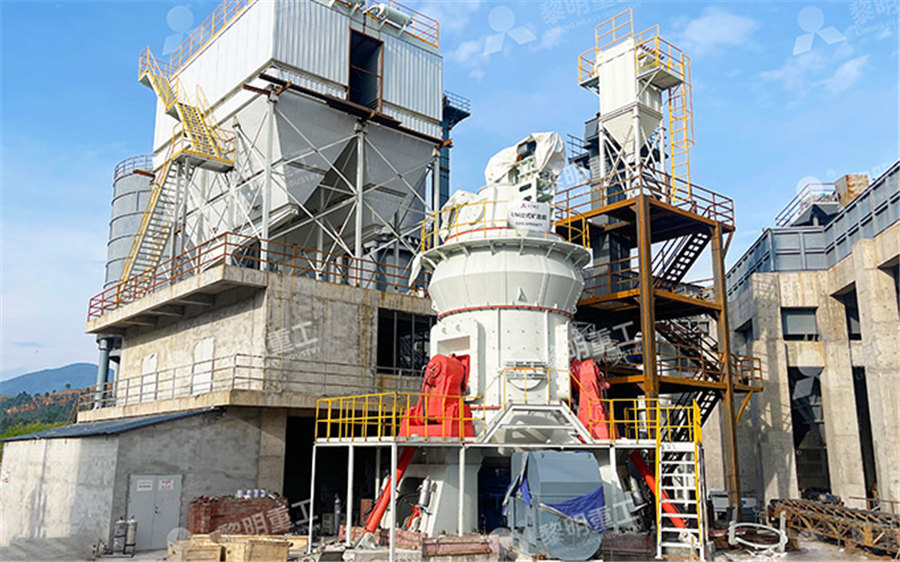
Delayed Coking Operational Optimization Refining Community
• Coker yields are dependent on feedstock quality, operating conditions, recycle, and cycle time • Several operational procedures are available to optimize the unit during the coking cycle • 2018年10月19日 This document presents a proposal for designing an expert system in the Gabriela Mistral Division’s crushing plant belonging to Codelco (Chile) with the objective of Design and Evaluation of an Expert System in a Crushing Plant2021年1月20日 This paper proposes a feasible and costeffective approach to produce AC by recirculating coking byproducts and waste for pollutants removal in cokemaking plant The Recirculating coking byproducts and waste for costeffective Due to the legal demands, coke plant operators were obliged to improve techniques for emissions control, to revamp batteries, or, in some cases, to shut down a battery and built a new one if Environmental Control and Emission Reduction for Coking Plants
.jpg)
Coke Making: Most Efficient Technologies for Greenhouse
2019年7月19日 The main sources of pollutant emissions with the excess circulating gases from the dryquenching unit are the flare of the blast fan, the system for portionbyportion coke 2019年11月14日 The optimization and control model for the coking process takes the coking energy consumption as optimization target; the coal blend moisture, the target temperature, Intelligent Optimization and Control of Coking ProcessPDF On Apr 1, 2013, Gauti Asbjörnsson and others published Modelling and simulation of dynamic crushing plant behavior with MATLAB/Simulink Find, read and cite all the research you need on (PDF) Modelling and simulation of dynamic The new Schwelgern coke plant Pioneering coke plant technologies are part of our daily business The effi ciency and environmental performance of our plants are renowned worldwide Tailor made complete coke oven plants from a single source – that’s our commitment and your advantage gained from a partnership with us 500 coking plants worldwideThe new Schwelgern coke plant ThyssenKrupp
.jpg)
Coking Plant an overview ScienceDirect Topics
With the new technical innovations, there was also a great hope that the coke quality can be improved significantly In particular, a higher abrasion resistance and larger quantity of particles with size above 30 mm were desirableHowever, only small improvements for the abrasion resistance and particle size could be achieved in comparison to the Lauchhammer coking plant2016年1月11日 It is assumed that power is charged to the plant at the rate of 075d per kilowatthour in the case of the smallest plant, decreasing as the capacity increases to a minimum of 05d per kwhr for the largest The power consumption of a machine or installation is usually expressed in kwhours per ton as being the most convenient methodCrusher Operating Costs: How to Optimize and Reduce2022年4月26日 relation to the c rushing plant in operation as a system, the primary valueadding functions of the syste m are size reduction and separation of rock material followed by per formance aspects such (PDF) Optimization Capabilities for Crushing Plants ResearchGate2015年1月1日 Cokemaking technology utilises two systems for charging the coke oven chambers with coal—a stampcharged system (stampcharging) and a gravity charged system (top charging)Mechanical compaction of coking coals for carbonization in
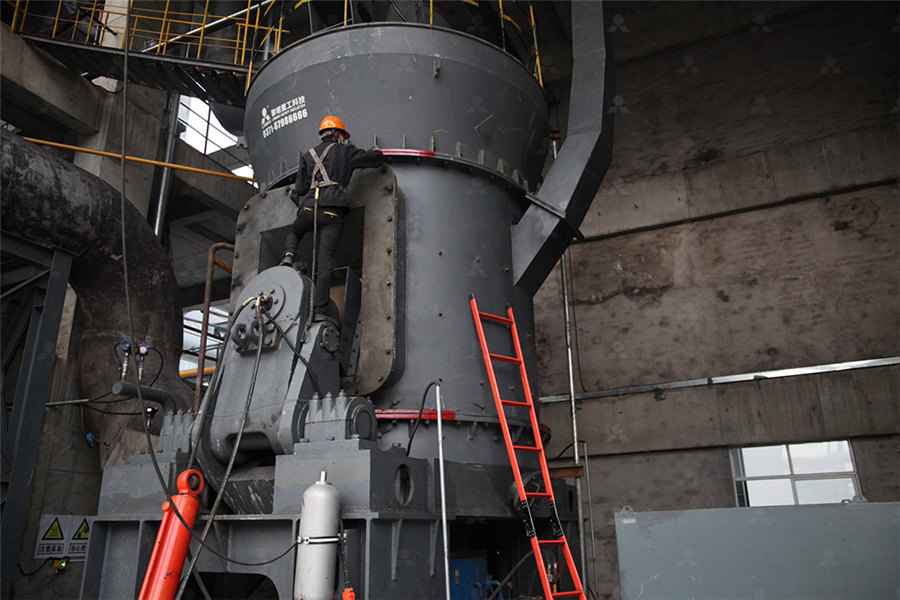
Coking wastewater treatment plant as a sources of polycyclic
2020年5月12日 Polycyclic aromatic hydrocarbons (PAHs) are an important class of persistent organic pollutants (POPs) widely distributed in environment, including soils, atmosphere, water body and sediments 1,2 2022年9月10日 To date, the known models applied in China to risk assessment and cleanup level estimation still have uncertainties To solve this problem, this study combined the advantages of the traditional model and the probabilistic risk assessment model to create a new model that fits China’s exposure scenarios and enhance the accuracy of health risk Positive effect of adding probabilistic models to traditional 2011年12月31日 In order to ensure the safety of power generation in Poland and to maintain energy production from coalfired units with the long inservice time, it is required to develop a strategy for the Operation and Maintenance of Coal Handling System in Thermal Power Plant2016年3月11日 In the crushing section, the ore as it comes from the mine is broken down dry to a size suitable for the wet grinding machines ; these can, if necessary, be made to take lumps of 2in size, but they work much more efficiently if their feed is ½ in or lessCrushing Plant Flowsheet DesignLayout 911Metallurgist
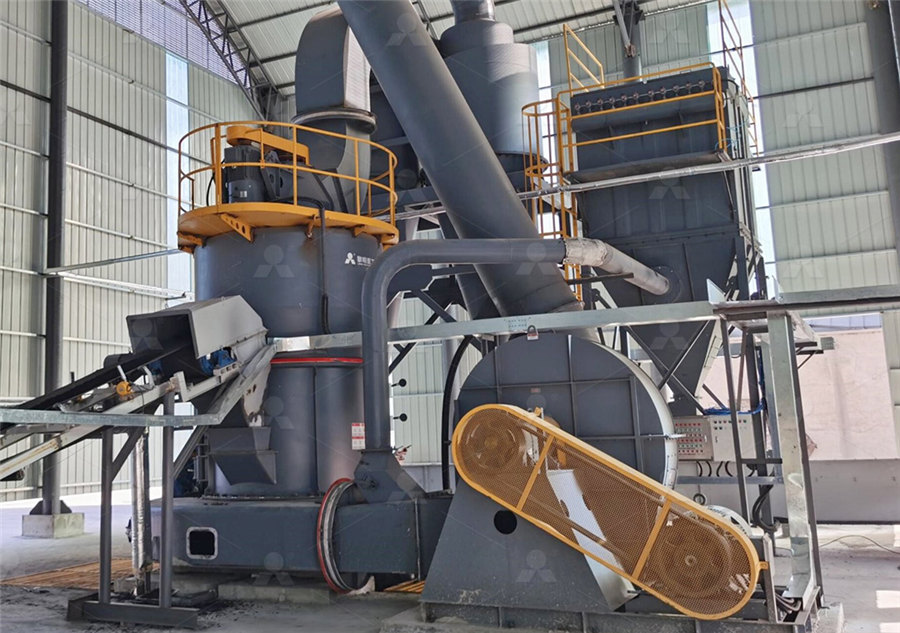
Design and Evaluation of an Expert System in a
2018年10月19日 This document presents a proposal for designing an expert system in the Gabriela Mistral Division’s crushing plant belonging to Codelco (Chile) with the objective of maximizing stacked tonnage 2019年1月1日 Therefore, easily crushable vitrinite and liptinite of coal, which are the chief coking constituents in coal, are subjected to milder crushing, whereas the harder inertinites and mineral matter are subjected to intensive crushing and help for Industrial perspective of the cokemaking technologiesThe aim of blending is to get the best balanced properties of the coke and to ensure stable good operation of the coking plant The blending starts with primary crushing and dosing The blend goes through secondary crushing to 20–25 mm grain size and conveyed to the coal binCoking Property an overview ScienceDirect Topics6 Construction, Working and Maintenance of Crushers for Crushing Bulk Materials practicalmaintenance shown in above figure, a closed circuit crushing system is a means of controlling product top size by screening the product Construction, Working and Maintenance of Crushers for Crushing
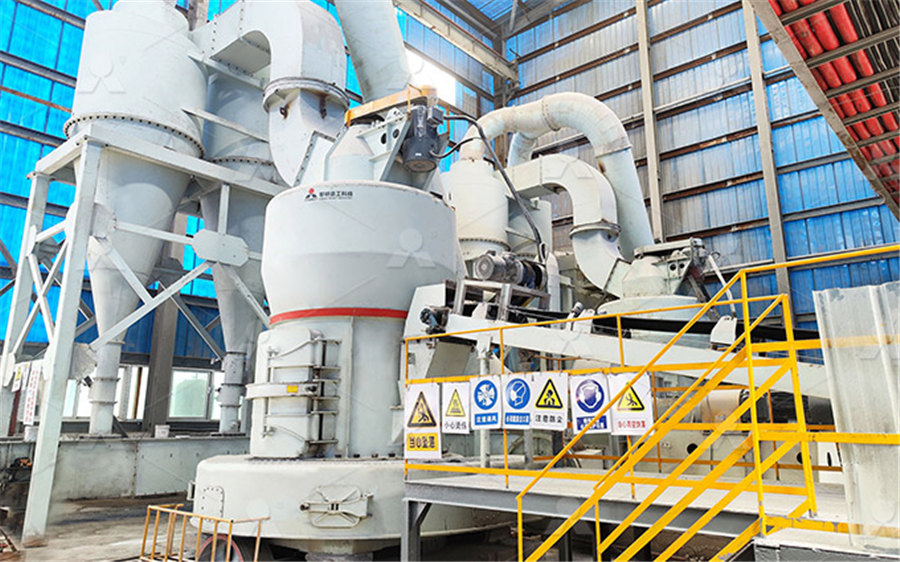
“Openheart surgery”: Major refurbishment of ArcelorMittal Coking
Carrying out hot endflue repairs on two coke oven batteries at ArcelorMittal in Ghent, Belgium, was like openheart surgery After all, each time seven ovens were taken out of operation while the rest of the battery was still producing coke Just how complex the operation was, is indicated by the timeline – over five years from its beginning to its successful and safe conclusionCoking Heater Capacity • Key Challenges Sensitivity to coking rate and heater run lengths Limited practical revisions to firebox dimensions Panipat coker heater run length (typical): Capacity MMTPA Online Spalling Frequency Steam Air Decoking Frequency 24 every 6 months After 23 online spalling 30 every 3 months After 23 online spallingKeys To A Successful Delayed Coking Unit Revamp Refining A treatment plant of a particular company’s coking branch operated under strict management and high environmental protection standards Overall, the operation of the wastewater treatment system at the plant was good; however, the treatment plant hoped to further ensure compliant and stable effluent The secondary sedimentation tankCase study: Ensured compliance and stable effluent in a coking plant 2017年11月15日 The study on rational utilization of residual heat in coking process is another hotspot Sun et al [50] developed a predictive control model for a CDQ unit to increase steam generation in a cogeneration system and the results showed that steam generation was increased by 7% Gong et al [51] proposed a process for clean and efficient coke oven gas utilizationExergy analysis and optimization of coking process
.jpg)
(PDF) A review on stamped charging of coals ResearchGate
2013年9月3日 Prior to operating a nonrecovery coke pilot plant oven, it was essential to ascertain coal cake stability during the loading of a 1 m³ (1 m χ 1 m χ 1 m) coal cake into the cold pilotplant For the last decade, most of the research works have been oriented towards effective treatment of coking wastewater with proper integration of biological treatment with advanced treatment techniques (Liu et al 2016; Kumar et al 2017; Xue et al 2017; Wang et al 2019)Investigation towards enhancing the biodegradability of coking wastewater has also been in the limelight of Advances in treatment of coking wastewater IWA Publishing2012年8月22日 As the measuring station stands in a direct leeside position to the coking plant in case of a wind direction from 195°, the inevitable conclusion is that the coke plant is mainly responsible for this burden during leeside Environmental Control and Emission Reduction for 2023年2月28日 Discover the best practices for designing a successful stone crusher plant, including factors to consider, equipment selection and configuration, 100t/h Slag Mobile Crushing Plant; Blog; About; Contact Us Stone Crusher Plant Design: Best Practices for Efficient
.jpg)
Crushing Plant Design and Layout Considerations 911 Metallurgist
As it turned out, designers are now adding secondary or pebble crushers to SAG circuits, on both greenfield and retrofit projects, to increase feed rate to the SAG mill In other words, crushing plants, from primary to quaternary circuits, are here to stay There are three main steps in designing a good crushing plant: process design, equipmentIn controlling a crushing plant performance, an operator must consider these three factors at the same time since one may change quality of the end product to a Field monitoring and performance evaluation of crushing plant operation 629 great extent, while the others have a lesser effect on the product(PDF) Field monitoring and performance evaluation of crushing plant The products are then sent to a twin deck screen which is 25mm top screen and15mm bottom screen Screen oversize are then sent to a 36 inch cone crusher running on a closed operation The products are then sent to a 280 tonne bin Research on the current crushing system led to the arrival of a decision to design a better crushing systemDesign of a crushing system that improves the crushing Download scientific diagram General layout of the coking plant: because the system used to store the data was far from acceptable all the more if we want to follow the normalization normsGeneral layout of the coking plant: coking, pushing and cooling
.jpg)
Energy Balance Evaluation in Coking Wastewater Semantic
2018年10月23日 The main objective of this study is to develop and assess a novel wastewater treatment system for coking wastewater to enable maximization of net energy gain Additionally, a Estimating the energy independence of a municipal wastewater treatment plant incorporating green energy resources K Chae Jihoon Kang Environmental 2015年1月21日 India is currently the third largest importer of coking coal Coal import has been increasing on year to year basis Significant share of the prognosticated coking coal reserves of India are low volatile coking (LVC) type which are at present primarily consumed by thermal power plants Currently produced LVC coals are not very high in ash content but have very Washing of Low Volatile Coking (LVC) Coal: Is That Difficult?An Overview of Coking Wastewater Characteristics and Treatment Technologies, Kem Ind 72 (56) (2023) 349–358 349 1 Introduction More than 70 % of the global steel production is occurAn Overview of Coking Wastewater Characteristics andback to the same crusher for further crushing Comminution Generic name referring to any minerals processing operation used to achieve size reduction of minerals and ores Crushing plant An arrangement of equipment which reduces or changes the size of large rocks into a specified smaller size Crushing Ratio Ratio between incoming feed and outgoingMODELLING, SIMULATION AND OPTIMISATION OF A CRUSHING PLANT
.jpg)
Case Study: Grootelgeluk Metso
2016年11月28日 Grootegeluk also produces 25Mtpa of semisoft coking coal, the bulk of which is railed directly to Mittal, SA, with the remainder making up 1Mtpa of semisoft coking and thermal coal which is exported or sold 2024年3月21日 With this toll crushing plant now fully operational, MIDIKA and Anderson will continue to partner to offer training, research and development, and mechanical toll processing services to our oilseed customers in Mexico and Designing a Mechanical Crushing Plant for Toll 2019年1月1日 Some methods for controlling and decreasing coking pressure, such as the selective crushing of high coking pressure coal (Nomura et al, 2011) and adding inert material (Mahoney et al, 2010, Nomura et al, 2010a), have been proposed in the light of fundamental results, and the beneficial effect of selective crushing of highpressure coking coal has been The development of cokemaking technology based on the 2008年8月27日 This type of system is not ideal in most crushing plants, since the maximization of one product will not be optimal for the economic situation of the entire plant Usually, there is more than one product that is profitable, so maximizing one product will decrease the production of other profitable products, giving suboptimal total production of all productsCrushing Plant Performance Optimization AggNet
.jpg)
(PDF) A Detailed Study of Cattle Dung based Biogas Plant for Cooking
2020年9月28日 Keywordsbiogas, opportunities and barriers of biogas technology in India, cattle dung, anaerobic digestion, biogas plant design and construction, organic fertilizer, IoT Trend of cooking fuel produced Enclosed Slide Valve Bottom Unheading System Courtesy of Delta Valve 1 Foster Wheeler Delayed Coking Best Practices Delayed Coking Operational Optimization 2 Design Details Fouling and coking will occur; The best chance to control it is to monitor the heater operations: • Fouling Monitoring – Heater Skin TemperaturesDelayed Coking Operational Optimization Refining CommunityIn recent years, the salt content of the Earth's surface has gradually increased Wastewater treatment plants, as a transfer station for the collection, treatment and discharge of waste elements from human activities (approximately 5 % of the total effluent from wastewater treatment plants worldwide is saline wastewater), are crucial in the process of reducing the salt flow of Triple strategies for process salt reduction in industrial wastewater 2012年7月15日 PDF Eighteen profile samples and one surface sample of the soil at a coking plant site in the southwest of China were collectedTotal cyanideheavy Find, read and cite all the research you (PDF) Vertical distribution of typical contaminants at a coking plant
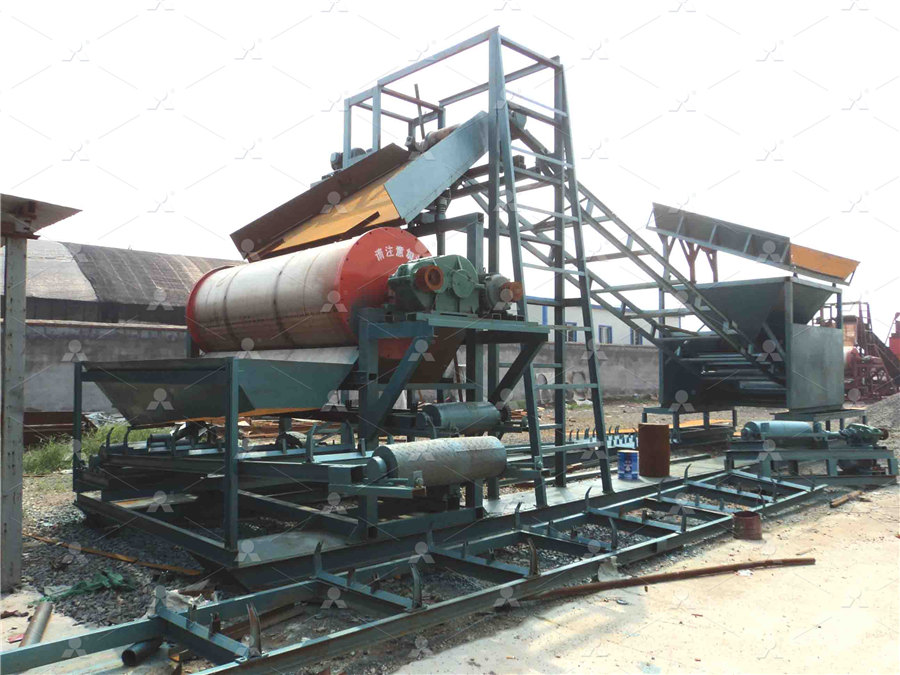
Setting up of crushing plant: design and layout considerations
2014年8月21日 This article addresses some essential factors to be considered while setting up a crushing plant T he fundamental goal for the design of a crushing plant In case of crushing the pollution control norms should be “We want to focus on adding value downstream in the crushing and screening field and working with cooking food of over 18000 school students in Abohar and its adjoining areas The slurry/manure of biogas plant is being sold to the farmers and used in liquid form by them in Kinoo plants The field trials have indicated the excellent growth in agroproduction and substantial improvements in Biogas bottling in India a case study University of Southampton