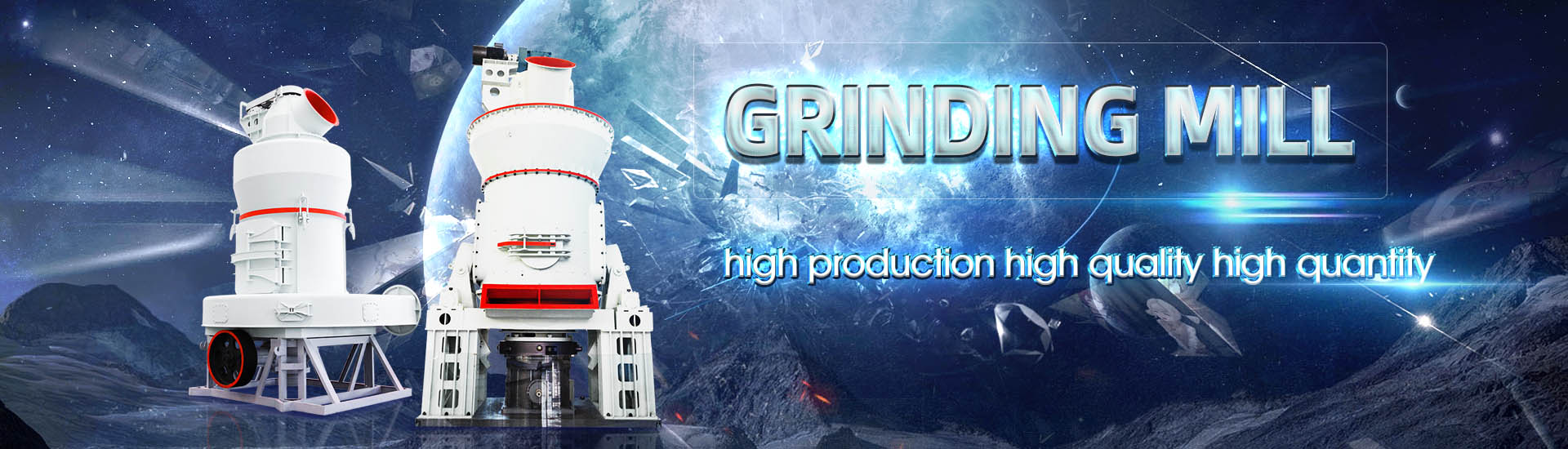
Iron quicklime ore processing process
.jpg)
Iron Ore Processing: From Extraction to Manufacturing
2024年4月26日 Iron ore, a naturally occurring mineral composed primarily of iron oxides, is mined and processed to extract iron for various industrial applications This article provides a comprehensive overview of the iron ore 2023年6月8日 Iron ore sintering is the iron ore powder agglomeration process that changes fine iron ore powder into the lumpy ironbearing raw material used for blast furnace ironmaking Iron Ore Sintering SpringerLink2017年3月24日 Sintering is a thermal agglomeration process that is applied to a mixture of iron ore fines, recycled ironmaking products, fluxes, slagforming agents, and solid fuel (coke) The Iron Ore Sintering: Process: Mineral Processing and Extractive In this study, we present a method to determine the optimum water content using the agitation torque of wet ore powder blended with quicklime First, we investigated the agitation torque for Optimum Water Content Estimation for Wet Granulation of Iron
.jpg)
Influence of quick lime on pore characteristics of hightemperature
2021年10月1日 In iron ore sintering, the bed structure transformation is caused by coalescence process occurring at flame front which determines sinter microstructure This study aims at 2022年10月20日 Making iron and steel from iron ore requires a long process of mining, crushing, separating, concentrating, mixing, agglomeration (sintering and pelletizing), and Iron Ore Processing, General SpringerLink2023年4月5日 The blast furnace and direct reduction processes have been the major iron production routes for various iron ores (ie goethite, hematite, magnetite, maghemite, siderite, etc) in the past few decades, but the Recent Trends in the Technologies of the Direct 2016年8月24日 In the granulation and sintering area, Lu and Ishiyama present an excellent update on recent advances in iron ore sintering, while Pownceby et al examine the influence Full article: Iron ore processing Taylor Francis Online
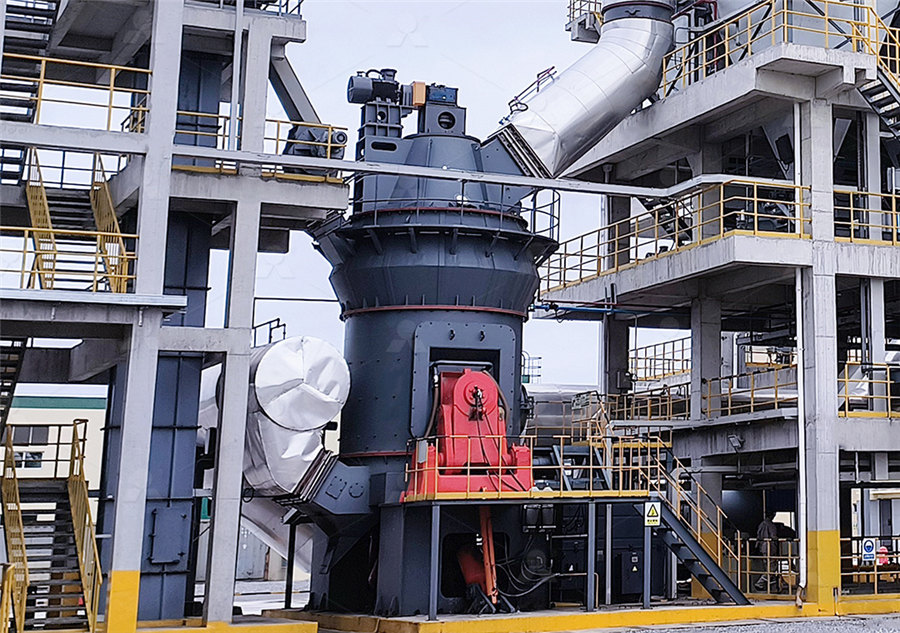
Natural and enhanced carbonation of lime in its
2021年10月4日 The presence of Cacompounds in the steel slag is the consequence of using quicklime (CaO) or limestone (CaCO 3) during the iron and steel making processes Quicklime is used in the hot metal desulphurisation PDF On Jul 11, 2018, Sandra Lúcia de Moraes and others published Iron Ore Pelletizing Process: An Overview Find, read and cite all the research you need on ResearchGateIron Ore Pelletizing Process: An Overview2024年1月1日 Iron ore sintering is the iron ore powder agglomeration process that changes fine iron ore powder into the (rich ore powder, concentrate powder), flux (limestone, dolomite, quicklime, etc), fuel (coke powder and sintering, and sinter processing (Fig 1) Sintering raw material preparation stage consists of Iron Ore Sintering SpringerLink2022年7月15日 Iron ore sintering is an agglomeration process of iron or e fines, fluxes, fossil fuel (coke and coal), and some ironbearing waste materials in the ironmaking and steelmaking industry [(PDF) Influence of Sinter Parameters on CO Emission in
.jpg)
Discover Optimized Lime Products for Iron Ore Preparation
Sintering of iron ore has always been a potential process to improve emissions and reduce costs Carmeuse research on lime characteristics for sinter enabled to offer engineered products and customized services for improving quality of the sinter, Milled Quicklime In the hot metal desulphurization process, Iron Ore Sintering: Process D FernándezGonzáleza, I RuizBustinza b, J Mochón , C GonzálezGascac, and L F Verdejaa aDepartment of Materials Science and Iron Ore Sintering: Process ResearchGateResource Recovery and Recycling from Metallurgical Wastes S Ramachandra Rao, in Waste Management Series, 2006 98 Production of Ceramic Tiles from Iron Ore Tailings Current practice of washing iron ore before it is processed for extractive metallurgical operation results in three products, coarse ore lumps with sizes in the range 1080 mm, which are directly charged Iron Ore Processing an overview ScienceDirect Topics2015年1月1日 Iron Ore: Mineralogy, Processing and Environmental Issues summarizes recent, key research on the characterization of iron ores, including important topics such as beneficiation (separation and Iron ore: Mineralogy, processing and environmental sustainability
.jpg)
Optimum Water Content Estimation for Wet Granulation of Iron Ore
2023年1月19日 Wet granulation plays an important role in the processing of fine ore powder Water content is a critical process parameter that determines the granule properties during wet granulationThe crude ore is loaded into trucks, which dump the material into the loading pockets or into the inpit crusher located in the Luce pit","3825":"IOC\u2019s operations are integrated across our mine and processing plant in Labrador City, Newfoundland and Labrador; our port , stockpile and vessel loading facility in SeptIles, Quebec; and the 418kilometre railway, run by QNSL, a Our Mining Process Iron Ore Company of Canada2023年12月19日 Discover the iron ore mining process, from blasting to export, and its vital role in steel production Learn about iron ore extraction and where it begins its processing phase Generally, and in Australia, the world's largest iron ore producer, the material is simply crushed in the jaw and then cone crusher into fines (small Iron Ore Mining Process: From Extraction to ExportDry iron ore beneficiation is without doubt currently being driven forward by Vale in Brazil The company wants to increase its capacity from 340 Mta iron ore at present to 450 Mta in future, dry beneficiation is to be further increased by 10 Dry beneficiation of iron ore Mineral Processing
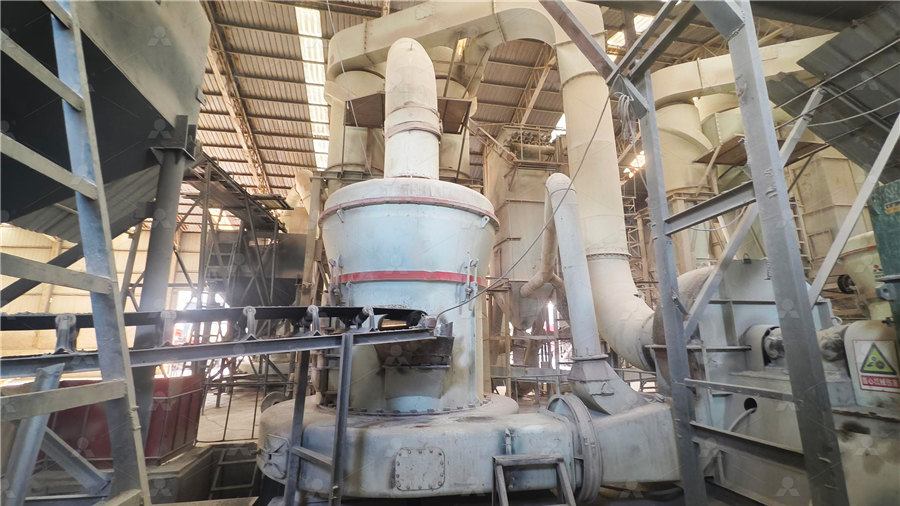
Its Processing and Application in Iron and Steel Industry
2017年7月7日 The processing for limestone for these products is described below The first process takes place at limestone mines where the mined ore undergo crushing and screening for the separation of the different size fractions of the ore In the iron and steel plant, in some of the places, raw limestone is further processedKEY WORDS: granulation; iron ore; agitation torque; quicklime; water content Wet granulation plays an important role in the handling of fine ore powder In the wet granulation process for pig iron, water is added to agitate the ore powders in a granulator, such as a drum mixer, and fine ore powders are agglomerOptimum Water Content Estimation for Wet Granulation of Iron Ore Phosphorus removal: Phosphorus, contained in the iron ore and the scrap metal that are used to start the steelmaking process, can seriously damage the properties of steelIn large quantities, it lowers the ductility of the steel making it easy to fracture when it is coldworked Quicklime added to the metalmaking process extracts the phosphorus in the steel, lowering its proportion to Lime, an essential component in the steel industryThe iron ore production has significantly expanded in recent years, owing to increasing steel demands in developing countries However, the content of iron in ore deposits has deteriorated and lowgrade iron ore has been processed The fines resulting from the concentration process must be agglomerated for use in iron and steelmaking This chapter shows the status of the Iron Ore Pelletizing Process: An Overview IntechOpen
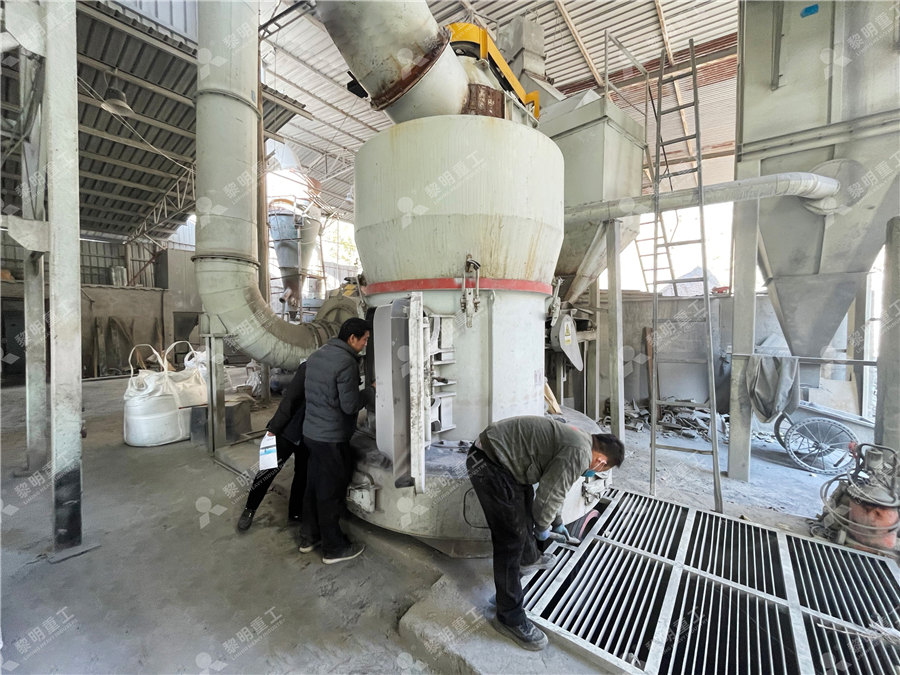
Iron processing Ores, Smelting, Refining Britannica
Iron processing Ores, Smelting, Refining: Iron ores occur in igneous, metamorphic (transformed), or sedimentary rocks in a variety of geologic environments Most are sedimentary, but many have been changed by weathering, and so their precise origin is difficult to determine The most widely distributed ironbearing minerals are oxides, and iron ores consist mainly of Iron Ore production in the Pilbara Activities involved in finding, mining and processing iron ore at our Pilbara operations have been simplified in the following diagram Rio Tinto operates 11 iron ore mines in the Pilbara and the specific sequence of activities varies from mine to mine Excellence in planning, scheduling and quality controlIron Ore production in the Pilbara2023年9月18日 Visit our Australian Mining Product and Services to see what our professionals are equipped with to help you in your processing iron ore journey or what other services we can offer Alternatively, call us on 1300 241 620 to speak to our experts today and learn all about the mining iron ore process Types Of Iron Ore In AustraliaTop 6 Steps Of Iron Ore Processing Australian Mining Services2024年3月16日 The sintering process is an intricate system with a protracted process flow The steps in the manufacturing line are primarily composed of the ingredients and mixing process, the sintering operation process, and the treatment of the sintered ore [39, 40]22 Important parameters and characteristics of sintering process As shown in Fig 2, all variables affecting Application of deep learning in iron ore sintering process: a review
.jpg)
Influence of quick lime on pore characteristics of high
2021年10月1日 Wet granulation plays an important role in the processing of fine ore powder Water content is a critical process parameter that determines the granule properties during wet granulation2021年12月1日 Lime, in the form of dry quicklime, is added to the ore during the transfer process, typically via screw feeder from a lime silo directly onto an ore transfer conveyer belt, before being stacked on the cyanidation heap leaching pad The pH target and subsequent cyanidation leaching is then similar to that of nonrefractory ore heap leachingLime use in gold processing – A review ScienceDirectInterpretation on Iron Ore Granulation Process Based on Particlesize Analysis Xiaobo HUANG,1) Xuewei LV2) Dolomite, serpentine, limestone and quicklime are the four fluxes, and coke breeze is the fuel used in sinter mixtures Seven iron ores (OreA to OreG), OrePIB and RSF (Return Sinter Fines) are the socalled iron bearing materiInterpretation on Iron Ore Granulation Process Based on Particle 2023年1月1日 Flowsheets for lowgrade ore processing of different iron ore mines vary significantly; however, the underlying principle of operation is very similar Methodology for selection of beneficiation flowsheet is already defined in the above sections For beneficiation of coarser fraction (+1 mm), jigging is widely usedIron ore beneficiation: an overview ScienceDirect
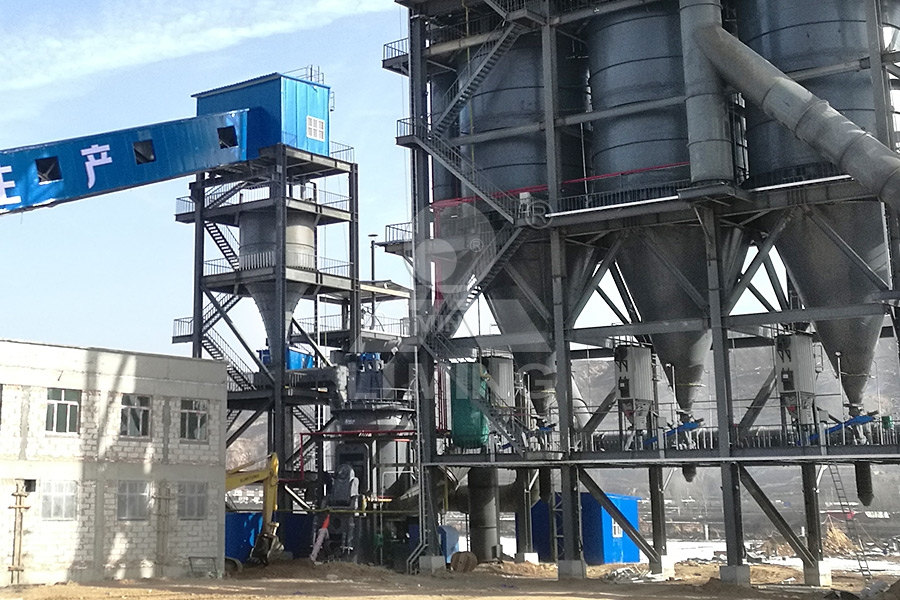
(PDF) Flotation of Iron Ores: A Review ResearchGate
2019年11月19日 PDF A tremendous amount of research has been done on refining the flotation process for iron ore and designing the reagents which go into it This Find, read and cite all the research you 2019年6月11日 World resources are estimated to be greater than 800 billion tons of crude ore containing more than 230 billion tons of iron The only source of primary iron is iron ore, but before all that iron ore can be turned into steel, it must go through the sintering process Sinter is the primary feed material for making iron and steel in a blast furnaceSintering: A Step Between Mining Iron Ore and Steelmaking2017年10月17日 Smelting Reduction Figure 2: The smelt reduction vessel (SRV) is the core technology component of the Hismelt process Source: RioTinto While years of ironmaking technology innovations have optimized blast furnace productivity, two alternative processes—smelting reduction and direct iron reduction— are growing in adoption The From Ore to Iron with Smelting and Direct Iron Reduction2017年2月9日 HG Li et al, Melting characteristics of iron ore fine during sintering process J Iron Steel Res 18, 11–15 (2011) Google Scholar S Machida et al, Experimental evaluation of chemical composition and viscosity of melts during iron ore sintering ISIJ Int 45, 513–521 (2005) Google ScholarHigh Temperature Mineralization Mechanism of Granules During Iron Ore
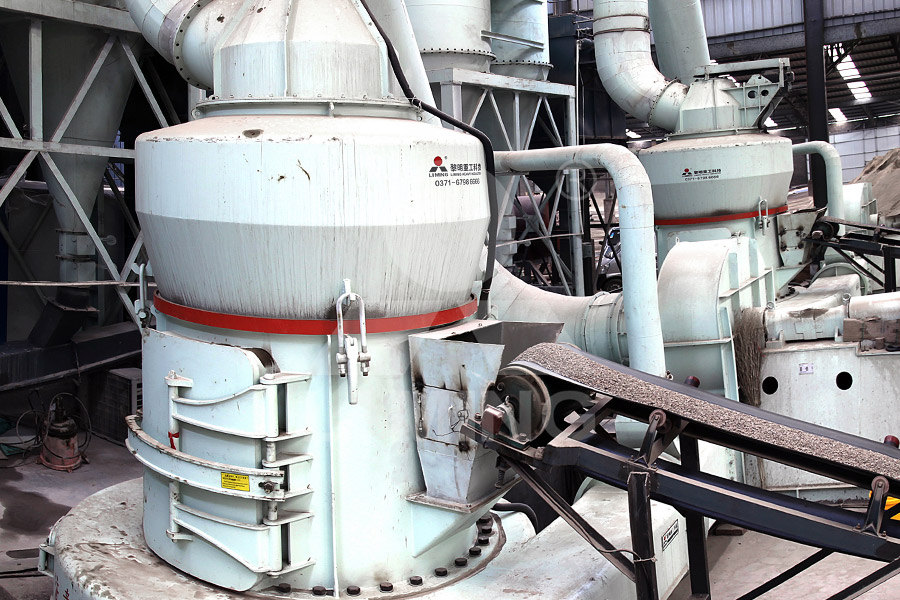
Copper Mining and Processing: Processing Copper Ores
Copper processing is a complicated process that begins with mining of the ore (less than 1% copper) and ends with sheets of 9999% pure copper called cathodes, which will ultimately be made into products for everyday useThe most common types of ore, copper oxide and copper sulfide, undergo two different processes, hydrometallurgy and pyrometallurgy, respectively, silica from bauxite ore and for causticization in the manufacturing of alumina Dolomitic quicklime is used to produce metallic magnesium by thermal reduction which reduces magnesium oxide Lime is also used in the processing of ores and the subsequent smelting and refining of copper, zinc, lead, and other nonferrous ores EnvironmentalQUICK LIME AND BYPRODUCTS PEC Consulting Group2020年7月1日 Sintering is the most extensively used and economic agglomeration process to prepare iron ore fines for blast furnace use Granulation is the most critical factor controlling iron ore sintering process, as it improves sinter mix permeability Currently, sinter plants are receiving significant proportion (up to 40%) of − 150 μm microfines in iron ore fines, which makes Modification of Wet Granulation Process During Iron Ore 2020年11月16日 The sinter process of iron ore with biomass carbon instead of coke breeze as fuel was investigated via thermodynamic analysis in this paper through a comparison of sinter composition indexes, metallurgical properties, Thermodynamic Analysis of Iron Ore Sintering Process
.jpg)
(PDF) Iron Ore Sintering: Process ResearchGate
2017年2月16日 Sintering is a thermal agglomeration process that is applied to a mixture of iron ore fines, recycled ironmaking products, fluxes, slagforming agents and solid fuel (coke)2015年8月3日 The first process that most of the ores or minerals undergo after they leave any mine, is mineral processing or mineral/ ore dressing It is a process of ore preparation, milling, and ore dressing (PDF) Overview of Mineral Processing Methods ResearchGateIs there a table of ore processing systems in modded Setup is Grinder > Multismelter (Requires Quicklime) > Centrifuge > Furnace Quicklime is produced via the Kiln (multiblock, look it up on EMasher's site) Also, IC2 Exp is ~24x with a small amount of byproduct (64 Iron Ore > 156 Iron Ingot, 14 Gold Ingots Comparison of ore processing systems : r/feedthebeast Reddit2023年11月15日 PDF Iron Ore, Iron Ore Pellets, Direct Reduced Iron )DRI( Pellets, Iron Ore Pellets Market, Pelletizing Process, Sintering, Binder, Induration Find, read and cite all the research you need (PDF) IRON ORE PELLETIZING PROCESS ResearchGate
.jpg)
A critical review on metallurgical recovery of iron from iron ore
2024年4月1日 In the processing of various iron ores, the resulting IOTs demonstrate a diverse phase composition, often influenced by the presence of lowgrade goethitehematite ore and associated clay minerals The phase composition of IOTs, as presented in Table 2, varies significantly due to the diverse mineralogy inherent in the iron ore extraction process2017年2月13日 Flue gas recirculation (FGR) has been implemented for exhaust gas emissions reduction in iron ore sintering However, the mechanism of NO x reduction through FGR is still unclear In this paper, the laboratory potgrate sintering test showed a 30% reduction in gas flow and 1551% reduction in NO x emissions achieved with a 30% FGR ratio, and the sinter NO x Reduction in the Iron Ore Sintering Process with Flue Gas Crushing, a form of comminution, one of the unit operations of mineral processing Mineral processing is the process of separating commercially valuable minerals from their ores in the field of extractive metallurgy [1] Depending on the processes used in each instance, it is often referred to as ore dressing or ore milling Beneficiation is any process that improves (benefits) the Mineral processing Wikipedia2017年1月1日 Effective technology for a complex wasteless processing of the iron ores has been designed and includes three main components (plats): comminution plant, briquette plant, pigment plant(PDF) Effective Processing of the Iron Ores ResearchGate