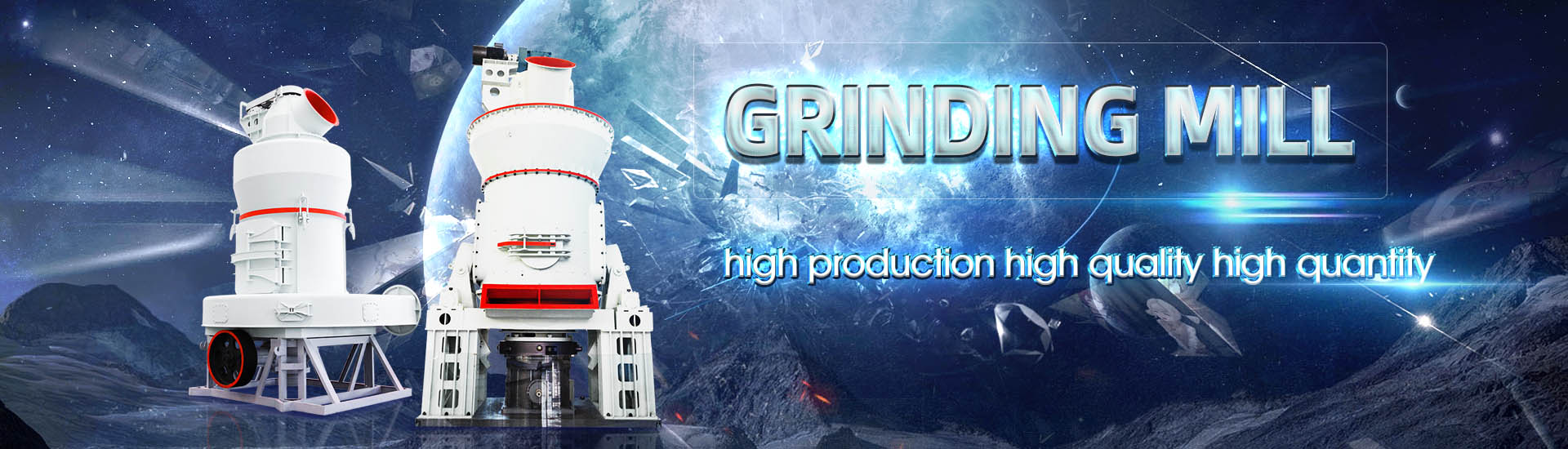
What’s the reason for the high return of raw material vertical mill
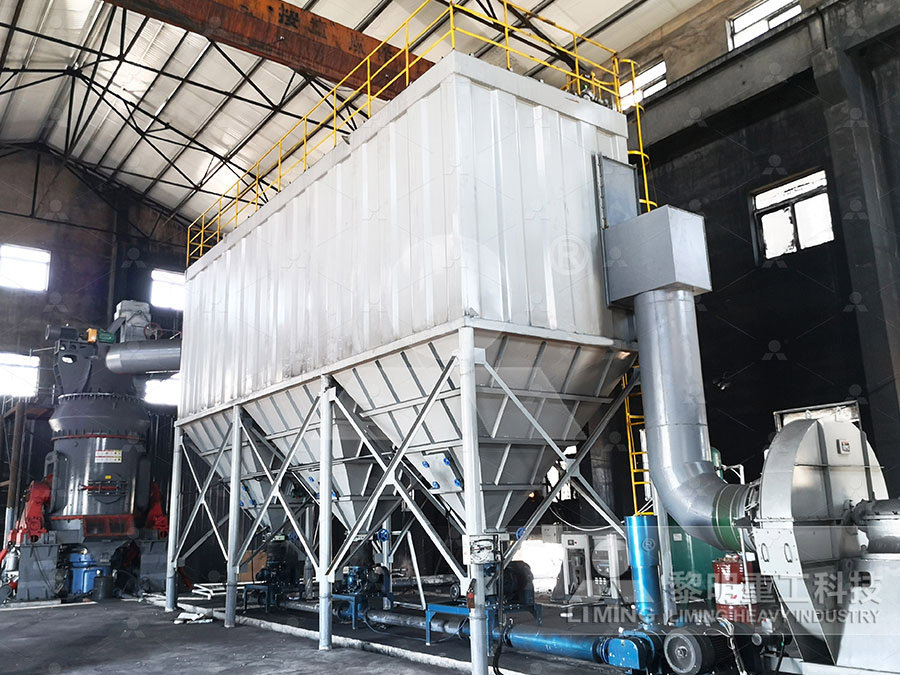
Vertical roller mill for raw Application p rocess materials
Vertical roller mills are adopted in 20 cement plants (44 mills) in Japan In the vertical roller mill which is widely used in the raw material grinding process, raw materials input grinding table are crushed and pulverized on it and transported to separator by kiln exit gas introduced into the 2021年1月1日 For the past three decades the vertical roller mill has emerged to be the preferred choice for grinding raw materials With the grinding capacity of a vertical roller mill and the Review on vertical roller mill in cement industry its performance 2017年9月11日 In this study, an extensive sampling study was carried out at vertical roller mill of ESCH Cement Plant in Luxemburg Samples were collected from mill inside and around the circuit to(PDF) Performance Evaluation of Vertical Roller Mill in Advantages of Vertical Raw Mills: 1 High Efficiency: The vertical raw mill operates with a high grinding efficiency, reducing the amount of energy required to produce the desired particle size The vertical raw mill: A key component in cement production
.jpg)
Loesche vertical roller mills for the comminution of ores and
2001年10月1日 The hydropneumatic spring system is a very versatile feature on the LOESCHE mill because it allows easy adjustment of the grinding process responding to changing 2021年1月1日 Vertical roller mill has proved to be a popular choice for finished cement grinding over all other machineries due to advantages like low power consumption, higher capacity, Review on vertical roller mill in cement industry its performance Vertical roller mill is a type of grinder used to grind materials into extremely fine powder for use in mineral dressing processes, paints, pyrotechnics, cements and ceramics It is an energy Vertical roller mill Wikipediavertical roller grinding mills for grinding: • Coal • Cement raw material • Clinker / granulated slag • Industrial minerals, and • Ores The core elements of these plants are the Loesche vertical PROCESS OPTIMISATION FOR LOESCHE GRINDING PLANTS
.jpg)
Cement grinding Vertical roller mills versus ball mills
It is characteristic of grinding in vertical roller mills that the energy input to the material per pass between roller and table is small, for which reason a large number of passes are required to 2019年4月16日 The paper demonstrates why the Loesche VerticalRollerMill (VRM) is a serious alternative to conventional grinding technologies and where the limitations of the system are (PDF) LEARNING FROM OTHER INDUSTRIES; WHY THE VRM2013年3月1日 This study investigated a mathematical model for an industrialscale vertical roller mill(VRM) at the Ilam Cement Plant in Iran The model was calibrated using the initial survey's data, and the Cements ground in the vertical roller mill fulfil the Another environmentally sustainable way to combat high raw material costs is to prioritize optimizing your organization to embrace energy – and waterefficient processing methods Not only does this help reduce greenhouse gas emissions, but it will also make your business less vulnerable to energy and water price hikesBlog Strategies to mitigate the high raw material cost impact CCI
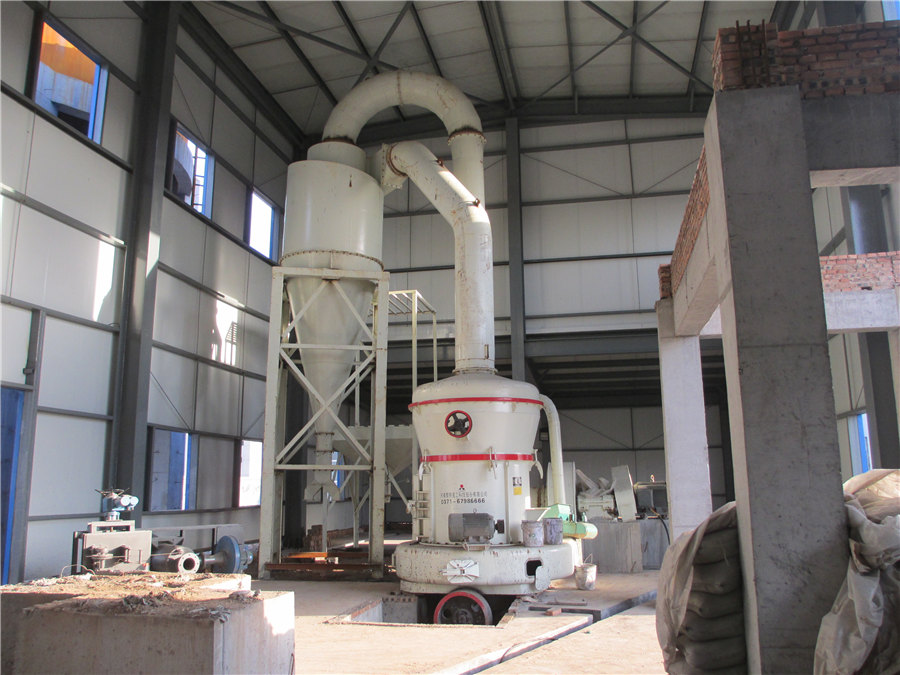
An investigation of performance characteristics and
2020年8月12日 This study shows the performance of a currently running vertical roller coal mill (VRM) in an existing coalfired power plant In a power plant, the coal mill is the critical equipment, whose 2023年5月15日 For the last 500 years, the West has mapped Africa as a source of raw materials, disrupted vibrant African value addition, and arrogated itself as the place where industrial revolutions (value (PDF) Africa’s move from raw material exports toward mineral The main difference is that classic raw material processes such as raw material introduction, the main use of raw materials (ie their conversion in manufacturing processes) and raw material deletion are eventbased processes, whereas portfolio management is timebased (ie taking a perpendicular view at raw materials or a snapshot at the month end or end of the quarter in Raw Material Excellence in the chemical industry, a game changer 2014年7月25日 Vertical roller mill (VRM) is a largescale grinding equipment, which is used to grind raw materials from block/granule into powder Due to harsh production environment and inconsistent raw Vibration Analysis of a Vertical Roller Mill: Modeling and Validation
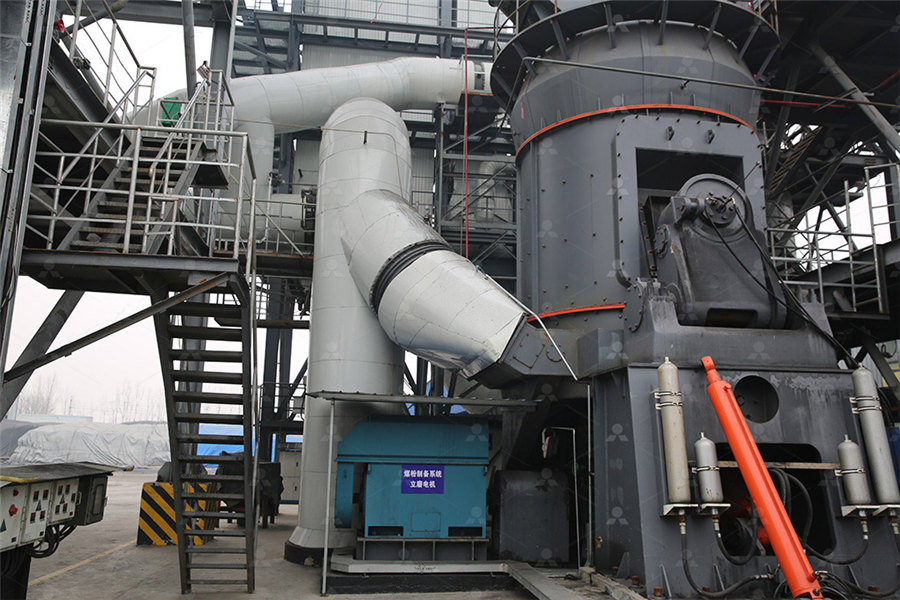
Rawmill Wikipedia
A mediumsized dry process roller mill A raw mill is the equipment used to grind raw materials into "rawmix" during the manufacture of cement Rawmix is then fed to a cement kiln, which transforms it into clinker, which is then ground to make cement in the cement millThe raw milling stage of the process effectively defines the chemistry (and therefore physical properties) of the 7 // Almost any plant for the grinding of cement raw material is a combination of machines specially adapted to the particular physical properties of the material to be ground As a result, our plants work efficiently without any trouble » Highly efficient grinding, drying, and separating in one unit » Outstanding production capacities exceeding 1,400 t/h in one single millPFEIFFER MILLS FOR THE CEMENT INDUSTRYDry Grinding: Open circuit Ball mill, closed circuit Ball mill, vertical roller mill, Roll Press or Roll press in circuit with ball mill However, it would be seen that the most significant process and types used for raw material grinding operations in modern cement industry are: Process: Dry Closed circuit drygrinding Type of mill: Ball and Raw Material DryingGrinding Cement Plant OptimizationMultiDrive® as compared to a twomill solution with conventional drives For this comparison, the following cost items were considered: » Vertical roller mill(s) » Mill gearbox(es) » Mill motor(s) + frequency converter(s) » Local manufacture of VRM parts » Foundation for VRM » Foundations for plant fi lter and plant fan » Transportation DDPPFEIFFER VERTICAL MILL WITH MULTIDRIVE MORE POWER

PFEIFFER VERTICAL MILL WITH MULTIDRIVE MORE POWER
MultiDrive® as compared to a twomill solution with conventional drives For this comparison, the following cost items were considered: » Vertical roller mill(s) » Mill gearbox(es) » Mill motor(s) + frequency converter(s) » Local manufacture of VRM parts » Foundation for VRM » Foundations for plant fi lter and plant fan » Transportation DDPThe conversion taking place in kiln system as raw meal is heated gradually to clinkerization temperature (1450 0 C) as shown below in table 1 Kiln system has seen a sea of development since 1950s to till date, from vertical shaft kilns to Clinkerization Cement Plant OptimizationAs you can tell, it is sometimes difficult to choose between horizontal mill vs vertical mill since each of these tools has a number of specialty uses To help you make your decision, we decided to pit the horizontal milling machine vs Horizontal vs Vertical Milling Machines: What’s the 2023年12月19日 On vertical machining centers, a vertical head runs perpendicular to the worktable’s surface, and the cutting tool rotates in a vertical spindle to remove material from the workpiece Although durability and precision are the hallmarks of both milling styles, most agree that horizontal mills are preferable for heavyduty applications, but, as mentioned, vertical mills Vertical Milling Machines vs Horizontal: Differences Explained
.jpg)
PROCESS OPTIMISATION FOR LOESCHE GRINDING PLANTS
• Material grindability • Material temperature • Material moisture • Mixture composition • Composition of raw material • Grinding roller wear • Fineness (Blaine) or residue (VOA) • Mill motor speed • Mill air flow/mill differential pressure • Temperature after the mill • Pressure before the mill • Grinding stock feed2023年10月8日 This research describes the impact of raw material prices on the financial performance of the organization Where this research aims to determine the effect of raw material price fluctuation on (PDF) The Role of Raw Material Price Fluctuations on Our bestinclass OK™ Mill is a globally successful vertical roller mill solution for grinding raw material, cement and slag Its cuttingedge design features consistently deliver the highest quality products with the greatest efficiency It is affordable to install and cost effective to operate over your cement plant’s lifetimeOK™ Raw and Cement Mill2024年7月25日 Types of Vertical Integration Backward Integration: A company seeks to acquire a raw material distributor or provider at the beginning of a supply chain Backward integration moves the ownership What Is Vertical Integration? Investopedia
.jpg)
(PDF) Vertical Farming: The Only Way Is Up? ResearchGate
2021年12月21日 PDF Vertical farming is on its way to becoming an addition to conventional agricultural practices, highyielding, highquality, and easytoharvest crops optimized for a highly controlled2017年2月28日 In this paper a review of systematic use of 7 QC tools is presented The main aim of this paper is to provide an easy introduction of 7 QC tools and to improve the quality level of manufacturing Methodology for Optimisation of Raw Material ResearchGateStudy with Quizlet and memorize flashcards containing terms like What do the vertical boundaries of a firm refer to? a The activities the firm itself performs versus purchases from independent firms b The level of expertise of the firm's workforce c The breadth of products a firm produces d The production output level for a firm e The government's environmental regulations, Which of Chapter 3 Flashcards QuizletMaterial shortages caused prices to double or triple Material shortages in industries with higher fixed costs create damaging conditions because it leads to low usage of expensive facilities In this situation, vertical integration makes sense because there is more reliability in the availability of raw materials and other needed supplies18 Advantages and Disadvantages of Vertical Integration
)D`ERF`389RMI4.jpg)
Measuring rawmaterial criticality of product systems through an
2021年12月4日 Purpose The concept of criticality concerns the probability and the possible impacts of shortages in rawmaterial supply and is usually applied to regional economies or specific industries With more and more products being highly dependent on potentially critical raw materials, efforts are being made to also incorporate criticality into the framework of life cycle A Bridgeport mill is a standard manual kneetype vertical milling machine The reason that many people refer to a manual mill simply as a “Bridgeport” is because it’s one of the most famous brand names that’s found in most machine shops Essentially, Bridgeport invented the modern manual milling machineWhat’s a Bridgeport Mill? The Beginner’s GuideProcess introduction The GRMK vertical cement mill of CHAENG adopts a new generation of cement grinding technology, which integrates grinding, drying and powder selecting functions It can save 30% of power per ton compared with traditional ball mill At the same time, it has many advantages, such as less auxiliary equipment, multiple functions, small occupied area and little VERTICAL CEMENT MILL Xinxiang Great Wall Machinery Co, MultiDrive® as compared to a twomill solution with conventional drives For this comparison, the following cost items were considered: » Vertical roller mill(s) » Mill gearbox(es) » Mill motor(s) + frequency converter(s) » Local manufacture of VRM parts » Foundation for VRM » Foundations for plant fi lter and plant fan » Transportation DDPPFEIFFER VERTICAL MILL WITH MULTIDRIVE MORE POWER
.jpg)
Lathe vs Mill: What’s the Difference and Which is Better?
2023年2月26日 By the end, you'll have a complete understanding of the distinctions and be able to choose the one that's better for your project So, let's get started and explore Lathe vs Mill! Quick Breakdown A lathe is used for machining cylindrical objects, while a mill utilizes cutting tools to shape or create components from solid materials2023年8月8日 Grinding: The raw materials, such as limestone, clay, shale, etc, are fed into the vertical mill and ground to a fine powder known as raw mealWhat is the separation process in a vertical raw mill? LinkedInThe vertical roller mill (VRM) is a type of grinding machine for raw material processing and cement grinding in the cement manufacturing processIn recent years, the VRM cement mill has been equipped in more and more cement plants around the world because of its features like high energy efficiency, low pollutant generation, small floor area, etc The VRM cement mill has a Vertical Roller Mill Operation in Cement Plant2021年1月29日 Vertical roller mills, VRMs, are widely used for grinding raw materials in factories engaged in the extraction and processing of minerals Any machine used for grinding or crushing consumes around Increase productivity of vertical roller mill using seven QC tools
.jpg)
(PDF) Performance Evaluation of Vertical Roller Mill
2017年9月11日 Due to the compact design and material transportation system of vertical roller mills (VRM), some important streams (total mill feed and discharge, dynamic separator feed and reject) remain in the 2020年2月10日 Vertical disintegration in manufacturing industries has been an increasing trend since the 1990s in many countries According to a prevailing management paradigm of focusing on core competencies, firms should have Vertical (Dis‑)Integration and Firm Performance: A 2015年4月9日 Some of the characteristics and requirements to be considered when selecting a grinding mill are given below Material properties – The choice of mill type is primarily dependent upon the properties of the material which is Grinding Mills and Their Types – IspatGuru2024年6月25日 Horizontal integration and vertical integration are different strategies that help businesses grow through acquisitions Learn more about each and find out how they differHorizontal Integration vs Vertical Integration: What's
.jpg)
The Revised German Raw Materials Strategy in the Light of Global
2021年1月6日 Faced with this global competition for raw material supply, it is doubtful if the revised German raw materials strategy is sufficient to meet the challenges in a world that increasingly requires CRMs for the production of high technology, where a retreat of free trade can be observed (Fajgelbaum et al, 2020) and where the biggest economies are actively Part Three: Raw Mill Process of Raw Mill The proportioned raw material is feed first to a grinding mill In the mill, particles ground in to very fine sizes In the grinding unit, drying, grinding and mixing takes place simultaneously Hot gas from clinker burning unit is passed into the grinding unit to assist the drying and grinding processCement Manufacturing Process INFINITY FOR CEMENT EQUIPMENT2017年4月1日 In the airswept mode, the verticalrollermill and a high efficiency dynamic classifier are suited above each other as a single unit (Fig 1) Material is fed to the grinding chamber and transported by table rotation to the grinding gap between the fixed grinding rollers and the mill table Crushing and grinding take place by compressive grindingOperational parameters affecting the vertical roller mill 2016年3月21日 Pulp Densities Pulp densities indicate by means of a tabulation the percentages of solids (or liquidtosolid ratio) in a sample of pulp This figure is valuable in two ways—directly, because for each unit process and operation in milling the optimum pulp density must be established and maintained, and indirectly, because certain important tonnage calculations are Common Basic Formulas for Mineral Processing Calculations
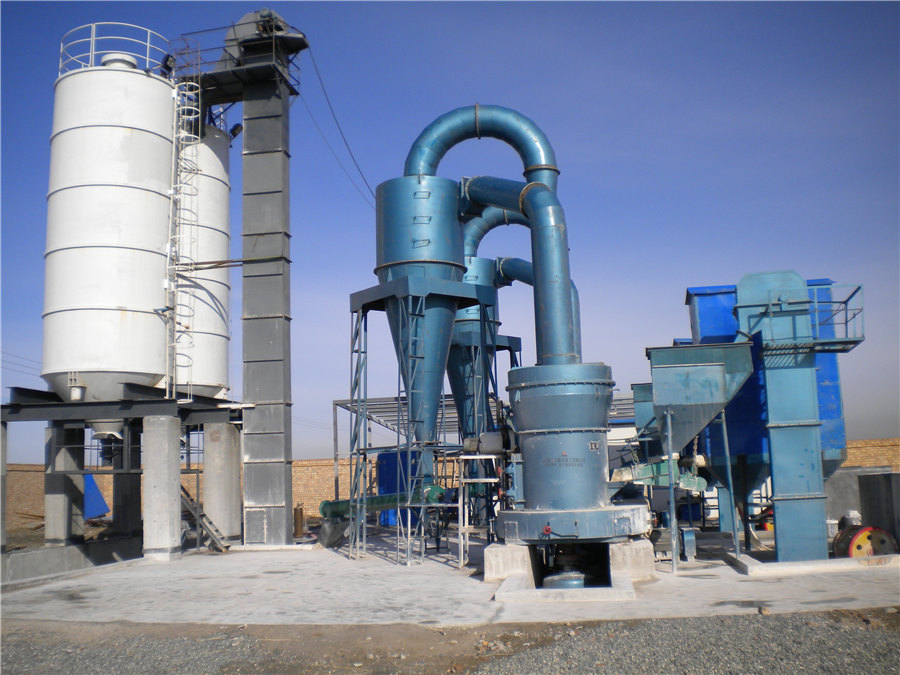
Why Vertical Integration Is The Path To Strategic Advantage
2024年1月29日 Tesla's approach to vertical integration—owning as many aspects of production as possible, from raw materials to final assembly—is a stark contrast to the traditional automotive industry model 2021年1月22日 In the whole process of cement production, the electricity consumption of a raw material mill accounts for about 24% of the total Based on the statistics of the electricity consumption of the raw A Survey and Analysis on Electricity Consumption of Raw Material Mill