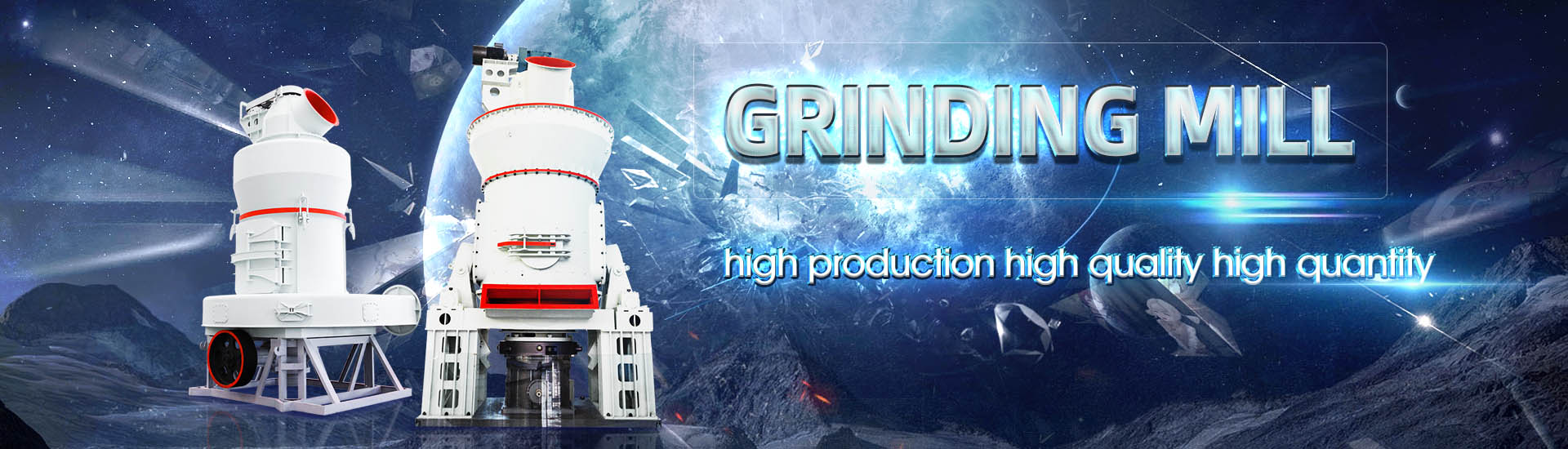
References for ore grinding mills
.jpg)
Ore Grinding SpringerLink
2023年7月20日 According to the different grinding medium, the grinding mill is divided into three types: (1) ball mill – it is used widely, and almost all materials can be triturated by ball mill; (2) rod mill – its efficiency is relatively high with the feeding particle size less than 30 mm and the 2023年10月27日 Grinding media play an important role in the comminution of mineral ores in these mills This work reviews the application of balls in mineral processing as a function of the A Review of the Grinding Media in Ball Mills for Mineral Processing 2023年6月1日 The main parameters of grinding and classification process include measurement of millfeeding quantity, mill load measurement, measurement of ore slurry density, Online Measurement and Control for Ore Grinding and Classification2013年4月1日 This brief investigates the feasibility of applying a robust nonlinear model predictive controller to a runofmine ore milling circuit, and the conditions under which such a [PDF] Analysis and validation of a runofmine ore grinding mill
.jpg)
Optimizing grinding mill performance using extremum seeking
2021年1月1日 A semiautogenous grinding mill is simulated with an extremum seeking controller to maximize the performance of the mill using grind curves Grind curves map the essential 2020年6月1日 Stirred media mills are used by the mining industry for ultrafine grinding to enhance liberation, and to decrease particle sizes of industrial minerals to tailor functional Stirred media mills in the mining industry: Material grindability 2017年9月1日 The objective of this work is to assess the influence of fine grinding in ball mills and stirred mills on valuable mineral liberation and particle shape characteristics of UG2 ore, a Fine grinding: How mill type affects particle shape characteristics 2023年5月5日 Grinding equipment is a type of mineral processing equipment that further reduces the ore particle size of crushed massive or granular ore to powdery material by Grinding Equipment SpringerLink
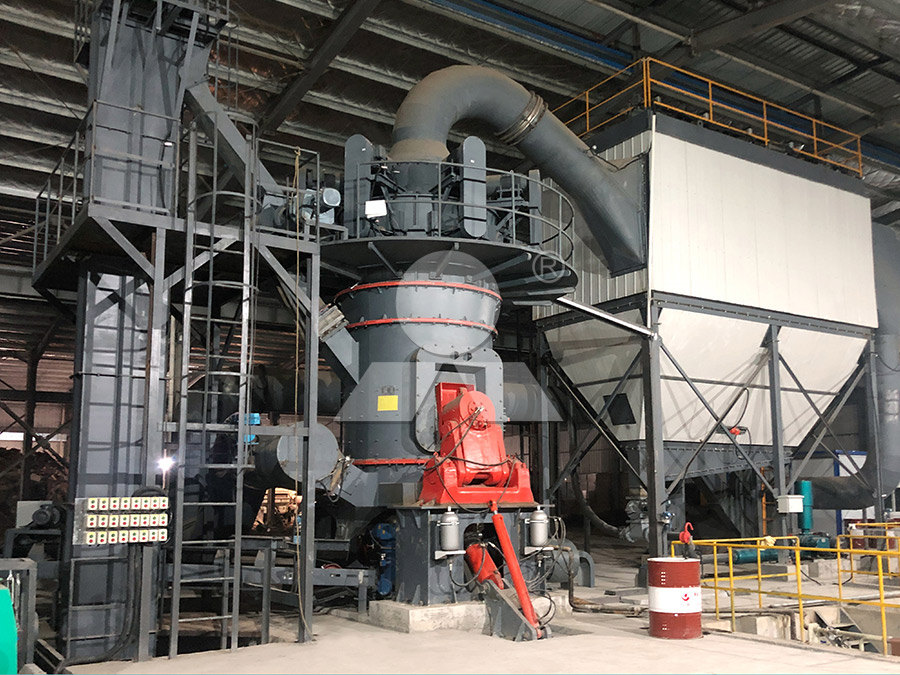
Research of iron ore grinding in a verticalrollermill
2015年3月15日 In this study, grinding characteristics of spent carbon anode from aluminum electrolysis in both ball mill and rod mill were analyzed, and compared based on the utilization 2021年1月14日 Ball Mill Work Index tests using crushed feed, and Standard Autogenous Grinding Design (SAGDesign) Tests, patented by Outokumpu (See reference 8 below) The Comparison of Ore Hardness Measurements for Grinding Mill 2012年6月1日 An overview of the current methodology and practice in modeling and control of the grinding process in industrial ball mills is presented Ball mills are used for the second stage of ore grinding in mining operations by proportioning ore piles 56 References; Related Papers; Stay Connected With Semantic Scholar Sign UpGrinding in Ball Mills: Modeling and Process Control Semantic 2021年1月14日 Ball Mill Work Index tests using crushed feed, and Standard Autogenous Grinding Design (SAGDesign) Tests, patented by Outokumpu (See reference 8 below) The comparison of these results gives context to how the various measurements relate to each other and how they can be used to obtain an accurate design for the grinding mills required forComparison of Ore Hardness Measurements for Grinding Mill
.jpg)
Bond´s work index estimation using nonstandard ball mills
2023年9月18日 This work contributes to obtaining new models for rapid Bond Work Index estimation using nonstandard dimensions mills This was done by proposing grinding tests using four types of ores and four 2012年6月1日 As the cylinder starts to rotate, the grinding balls inside the cylinder crush and grind the feed material, generating mechanical energy that aids in breaking bonds, activating the catalyst, and Grinding in Ball Mills: Modeling and Process Control2021年3月15日 Request PDF Comparing strategies for grinding itabirite iron ores in autogenous and semiautogenous pilotscale mills High grade iron ore resources are becoming depleted in Brazil, with Comparing strategies for grinding itabirite iron ores in 1991年6月28日 Maintenance costs associated with wear in coal grinding mills operating in Queensland pulverised coalfired power stations are in excess of $10m per year In other fuelore and mineralore processing industries metal wastage through wear and corrosion is also a major component of maintenance costReview of test methods for abrasive wear in ore grinding
.jpg)
Ore mill, Ore grinding mill All industrial manufacturers
Ore mills 21 companies 42 products My filters for ore Delete all Manufacturers C; Ceramic Instruments Srl (2) D; Dec Group (6) E; ® Grinding Mills are proven in dozens of milling applications Grinding processors are achieving impressive energy savings (3550%), 45th ©Annual Canadian Mineral Processors Operators Conference , Ottawa, Ontario, January 22 24, 2013 101 Grinding Circuit Flowsheet The milling circuit flowsheet of SantaRita operation is shown in Figure The SAG mill accepts 3 the primary crushed feed ore and operates in closed circuit with pebble crusherAchievement of High Energy Efficiency in Grinding Mills at 2023年10月27日 The ball mill is a rotating cylindrical vessel with grinding media inside, which is responsible for breaking the ore particles Grinding media play an important role in the comminution of mineral A Review of the Grinding Media in Ball Mills for Mineral Processing2017年1月17日 Other process activities, such as spraying the ore with water for dust control or the fact that runofmine ore moisture is approximately 2%5% are not generally considered (Bleiwas, 2012a)Breaking down energy consumption in industrial grinding mills
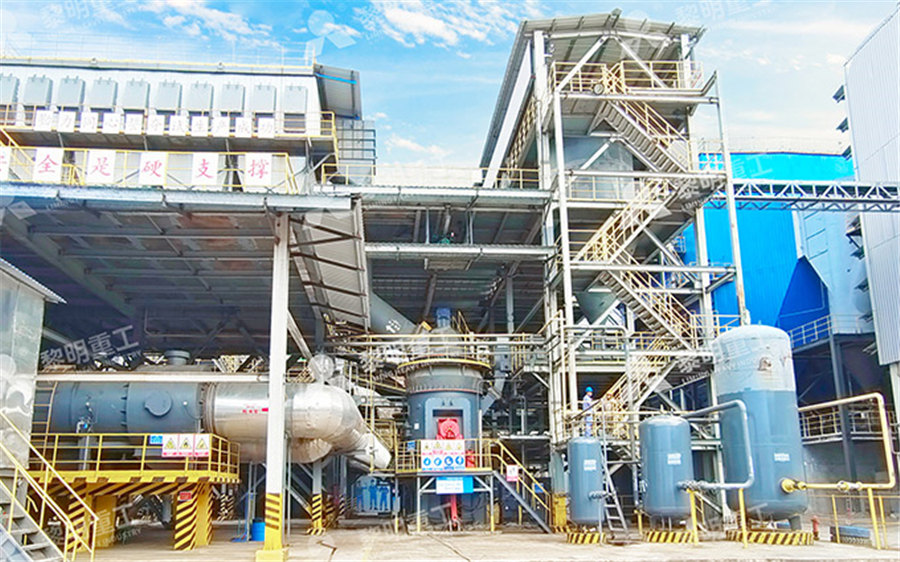
Mechanistic modeling and simulation of grinding iron ore pellet
DOI: 101016/JPOWTEC202107030 Corpus ID: ; Mechanistic modeling and simulation of grinding iron ore pellet feed in pilot and industrialscale ball mills @article{Carvalho2021MechanisticMA, title={Mechanistic modeling and simulation of grinding iron ore pellet feed in pilot and industrialscale ball mills}, author={Rodrigo M de Carvalho and 2022年5月23日 Grinding experiments were conducted in a laboratoryscale stirred mill on a lowgrade PGE bearing chromite ore HighPressure Grinding Rolls (HPGR) product of −1 mm was used as feed material to Modeling and application of stirred mill for the coarse grinding of 2022年3月19日 Request PDF Grinding iron ore concentrate by using HPGR and ball mills and their effects on pelletizing and reduction stages a pilotscale study An iron ore concentrate sample was ground Grinding iron ore concentrate by using HPGR and ball mills and 2019年1月1日 This article presents the results of theoretical and experimental studies on the processes of destruction ore in wet selfgrinding mills under the influence of the aquatic environment on itEffect of water medium upon the process of ore disintegration in
.jpg)
Grindability of binary ore blends in ball mills Request PDF
2013年2月1日 Request PDF Grindability of binary ore blends in ball mills The understanding of how blends of materials grind is of great relevance in both the minerals and the cement industries If benefits Grinding mills reduce the size of materials to a uniform particle size, enabling materials to progress for further processing Grinding mills use a grinding rather than crushing process to achieve the desired results Minerals processing generally uses wet grinding, where water is added to create a slurry that makes grinding more efficientFlexible, efficient grinding systems – FLS2023年4月24日 Grinding is the final stage of comminution, which reduces particle size to micron size level The size reduction is achieved by attrition, abrasion, and impact between the ore itself and between the ore particles and grinding media []According to Swart et al [], ball mills are mostly used because of their very high size reduction ratio, although they have a very low Grinding Media in Ball MillsA Review [v1] Preprints2017年2月1日 Although stirred mills have been used widely in the mineral processing concentrators for fine grinding purposes, till date a standard ore characterisation test is not available for this technologyExtending the application of JKFBC for gravity induced stirred mills
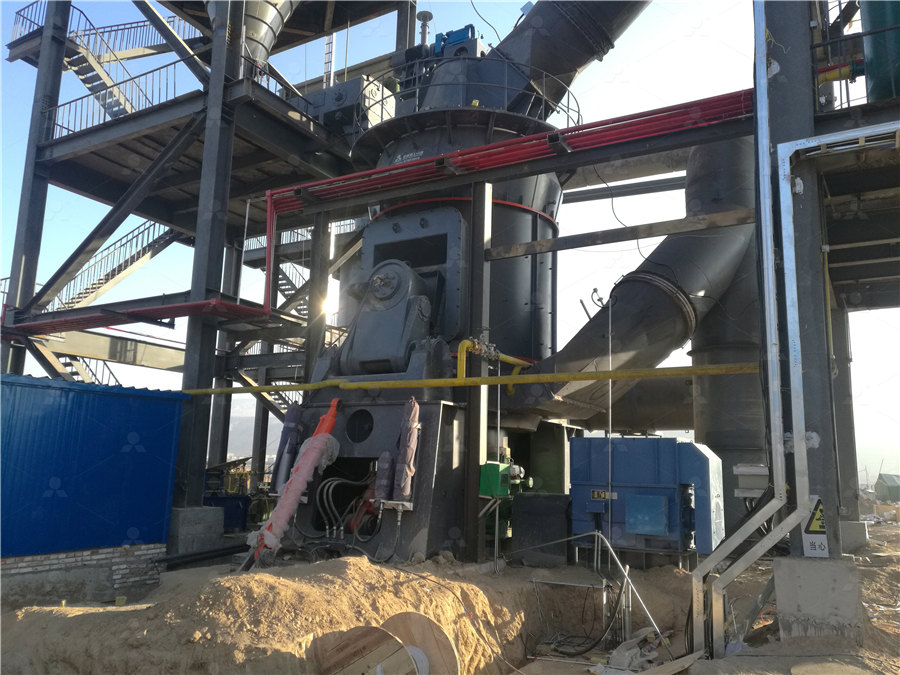
Grinding mills for mining and minerals processing Metso
Metso Select™ horizontal grinding mills are a preengineered range of classleading horizontal grinding mills, designed from industry leading experience and expertise The preengineered package eliminates time and costs usually spent in the engineering and selection stages Learn more about the Select™ horizontal grinding mills >2019年11月1日 References (10) Abstract The paper deals with the problems of intensification of grinding in vibration mills with harmonic, biharmonic and polyharmonic vibrationsOptimization of material grinding in vibration mills2022年8月24日 The depletion of the richest ore deposits and the increase in number of mining projects involving deposits with complex mineralogy, higher competence and lower grade has led to an eminent need for Multicomponent modeling and simulation of the Minas Rio iron ore Types of Grinding Mills Grinding mills play a crucial role in the mining process, as they are responsible for reducing large chunks of ore into smaller particles that can be further processed There are various types of grinding mills available, Understanding the SAG Mill in Copper Ore Mining
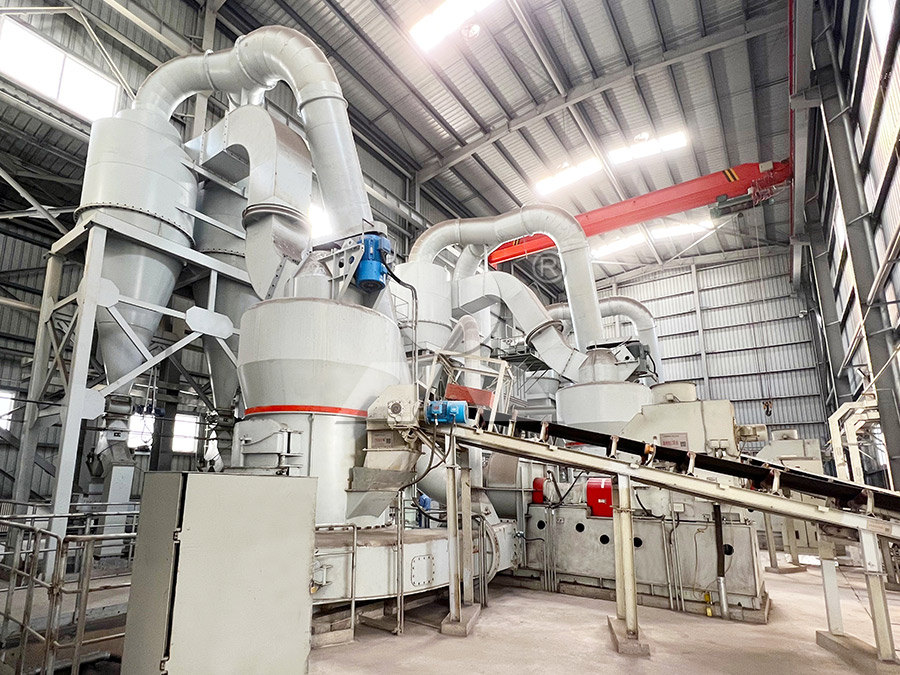
Copper Ore Grinding in a Mobile Vertical Roller Mill Pilot Plant
2014年10月1日 To assess the feasibility of extending this vertical mills' improved performance to ore grinding applications, Altun et al [14] studied chalcopyrite ore grinding processes using a vertical roller 2018年9月17日 Two ore samples were characterized, and benchscale grinding tests were carried out in laboratory mills 30 and 58 cm in diameter The results indicated that coarse compact itabirite ore (pebbles DEVELOPMENT OF A LABORATORY TEST TO DESIGN VERTICAL STIRRED MILLS 2021年7月1日 Grinding circuit data and ore samples were collected from nine industrial ball mills of diameters 3255 m For each of the ores tested there is a simple relation between the parameter and Mechanistic modeling and simulation of grinding iron ore pellet 2022年1月1日 The size of grinding media is the primary factor that affects the overall milling efficiency of a ball mill (eg power consumption and particle size breakage)Effect of grinding media on the milling efficiency of a ball mill
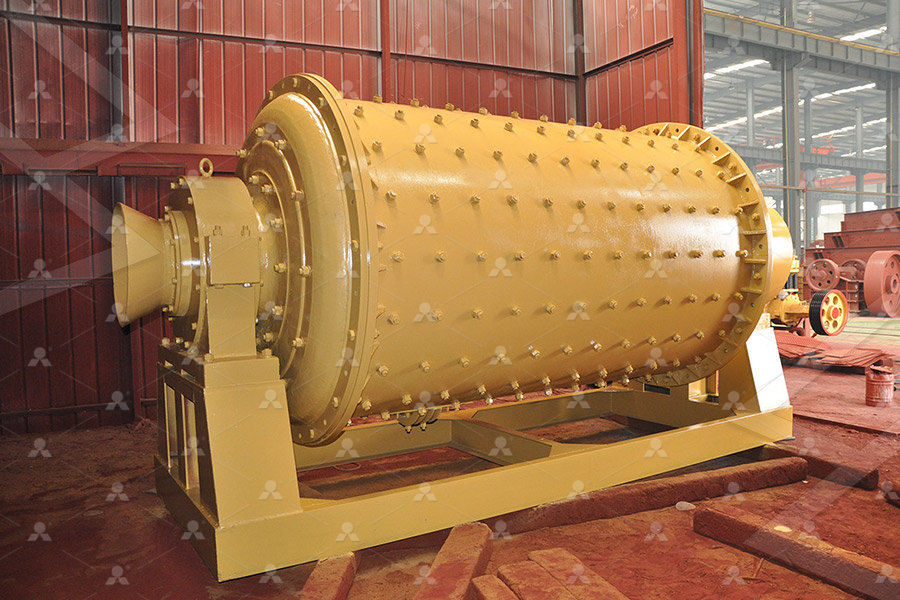
Is media shape important for grinding performance in stirred mills
DOI: 101016/JMINENG201010016 Corpus ID: ; Is media shape important for grinding performance in stirred mills @article{Sinnott2011IsMS, title={Is media shape important for grinding performance in stirred mills}, author={Matthew D Sinnott and Paul W Cleary and Robert D Morrison}, journal={Minerals Engineering}, year={2011}, volume={24}, pages={138 2024年1月1日 As for such grinding mills without grinding medium as mills and disc mills, materials are mainly crushed by the sheer force generated by the moving parts of the equipment, which is a part of ore grinding, and the product particle size is fineOre Grinding SpringerLink1994年10月16日 In the mineral processing industry, conventional tumbling mills crush/grind about a billion tons of rock/ore annually in the US These mills are extremely inefficient, with 97% to over 99% of the Power Draw of Grinding Mills its Measurement and Prediction2020年6月3日 Grinding mills are some of the most important equipment in mines, processing over a few thousand tons of ore every hour It is not uncommon to see these days that a single line of a grinding circuit consisting of a Semi Autogenous Grinding (SAG) mill followed typically by two ball mills generating over USD $1 million of revenues per dayHow grinding mill design changed over the last 30 years
.jpg)
Grinding Mills Common Types 911Metallurgist
2016年11月7日 In Fig 13 is shown a large ball mill, designed for the dry grinding of limestone, dolomite, quartz, refractory and similar materials; this type of mill being made in a series of sizes having diameters ranging from about 26 2017年6月15日 To understand the friction and wear of working mediums in iron ore ball mills, experiments were conducted using the ball cratering method under dry and wet milling conditions, which mimic the Friction and wear of liner and grinding ball in iron ore ball mill2014年1月1日 grinding mills installed in power plants, 5 Operating references More than 1000 MPS mills are in use for grinding cement, ore, coal(PDF) MPS mills for coal grinding ResearchGateRequest PDF On Jul 1, 2023, İbrahim Göktaş and others published Element based ball mill and hydrocyclone modelling for a copper ore grinding circuit Find, read and cite all the research you Element based ball mill and hydrocyclone modelling for a copper ore
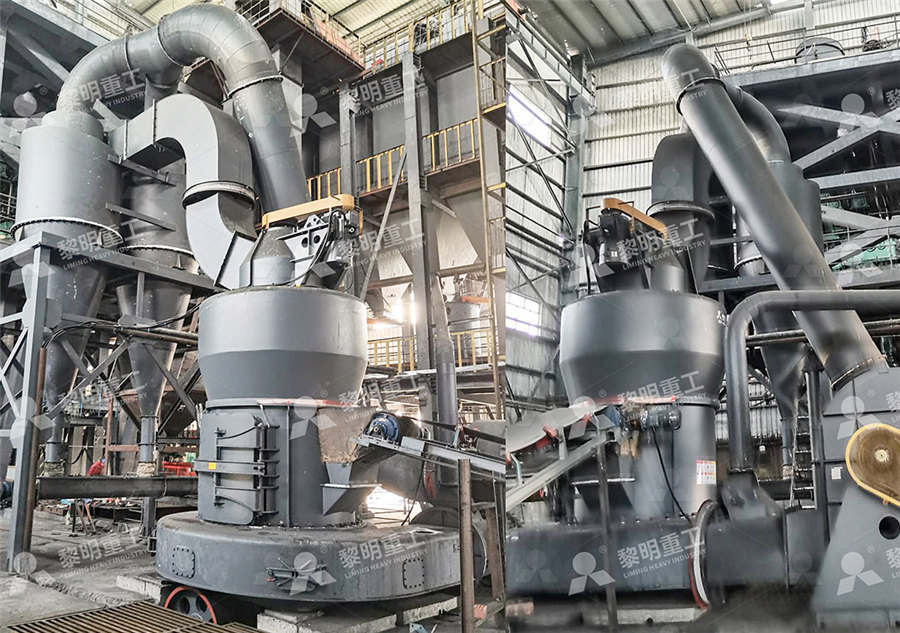
Development MPC for the Grinding Process in SAG Mills Using
2024年2月1日 DOI: 103390/ma Corpus ID: ; Development MPC for the Grinding Process in SAG Mills Using DEM Investigations on Liner Wear @article{Beloglazov2024DevelopmentMF, title={Development MPC for the Grinding Process in SAG Mills Using DEM Investigations on Liner Wear}, author={Ilia Beloglazov and Vyacheslav impact and abrasion Grinding mills exist in a large variety of sizes and models for different types of grinding The mills investigated in the research work presented in this thesis are autogenous pebble mills of the discharging type which utilize the ore itself as Structural Analysis and Condition Monitoring of Grinding Mills: A 2022年2月28日 Comparing dry and wet grinding curves in a ball mill in the same condition (an equal amount of materials and grinding media has been used on each pair of wetdry experiments) (Fig 17) indicated two significant differences at higher power values of wet grinding, specifically when speed exceeded 06 critical speed and for higher ω Pmax in the Grinding SpringerLink2019年4月16日 Vertical roller mills (VRM) have been used extensively for comminuting both cement raw materials and minerals like limestone, clinker, phosphate, manganese, magnesite, feldspar and titanium(PDF) LEARNING FROM OTHER INDUSTRIES; WHY THE VRM
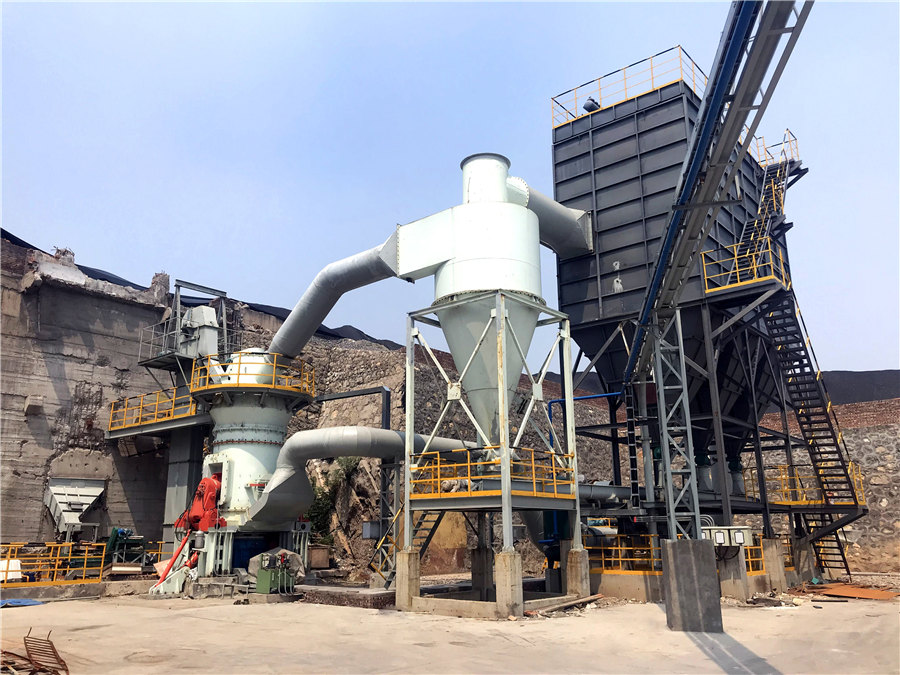
Copper ore grinding in a mobile vertical roller mill pilot plant
2015年3月10日 Vertical roller mills (VRM) have been used extensively for comminuting both cement raw materials and minerals like limestone, clinker, phosphate, manganese, magnesite, feldspar and titanium These mills combine crushing, grinding, classification and drying operations in one unit and have advantages over conventional machines and literature reports that 15% 2023年7月10日 The present literature review explores the energyefficient ultrafine grinding of particles using stirred mills The review provides an overview of the different techniques for size reduction and (PDF) EnergyEfficient Advanced Ultrafine Grinding of Particles