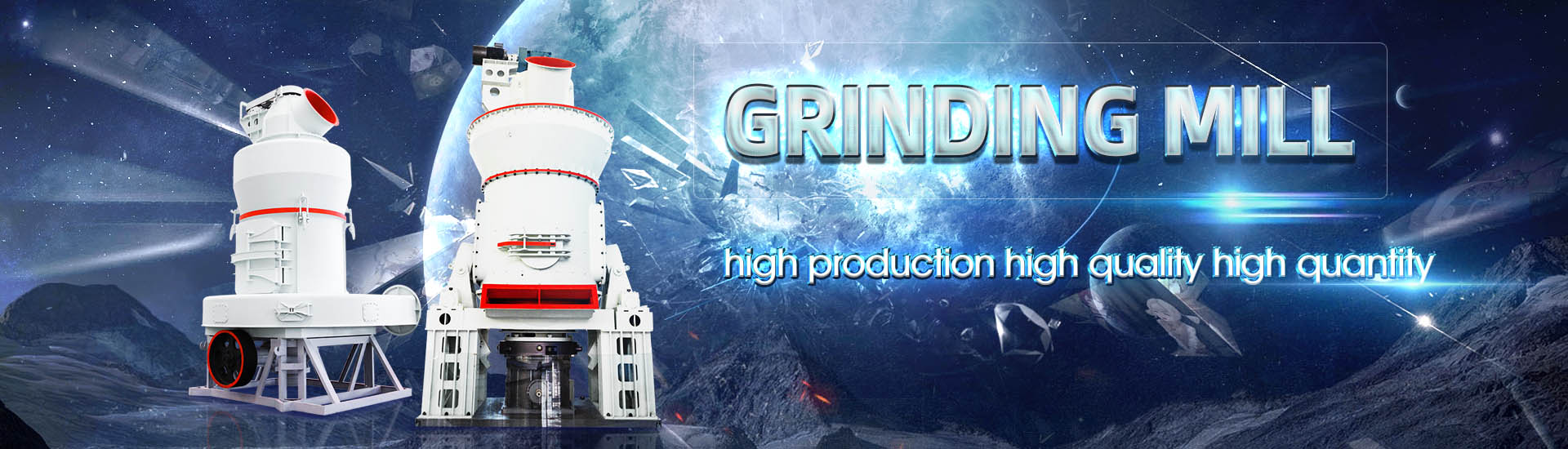
Medium speed coal grinding Causes of increased machine current
.jpg)
Fault analysis and optimization technology of HP bowl type
2021年8月1日 In order to facilitate the staff to complete the maintenance task more quickly and with higher quality, this paper introduces the common faults in HP type bowl type medium speed coalIn order to facilitate the staff to complete the maintenance task more quickly and with higher quality, this paper introduces the common faults in HP type bowl type medium speed coalSHPHGLXP VSHHGFRDOPLOO ResearchGate2020年8月12日 Obtained results indicate that grinding pressure, primary air (PA) temperature and mill motor current have a tendency to rise by increasing coal feeding mass flow rates for An investigation of performance characteristics and energetic The electricity current intensity of coal mills can be reduced or minimized subject to the coal type parameters and the load of the boiler through optimizing the coal mill operations This paper A Modeling and Optimizing Method for Electricity Current
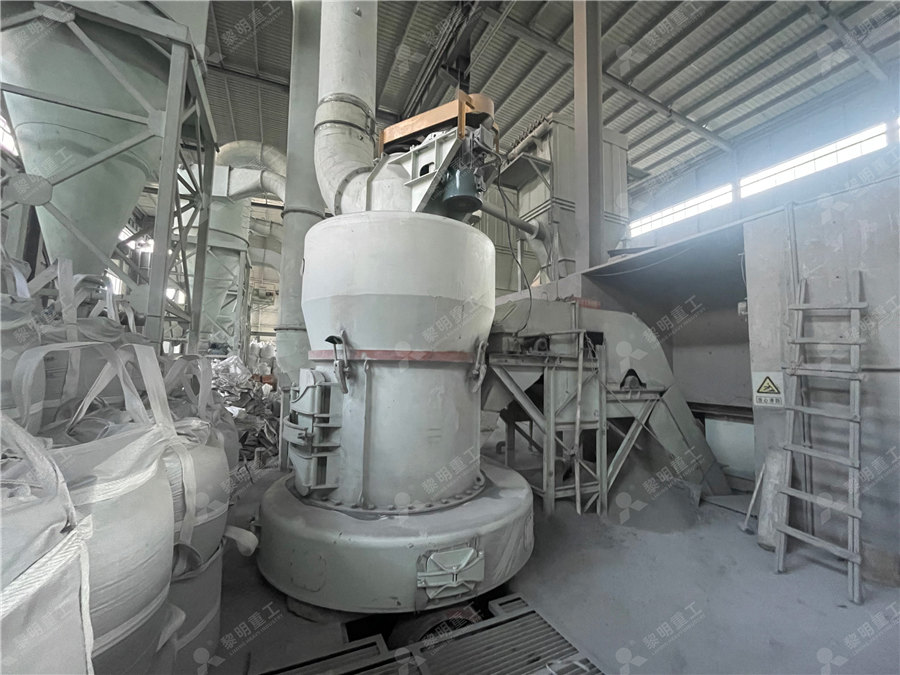
Fault Diagnosis of Coal Mill Based on Kernel Extreme Learning
2022年7月26日 The coal mill of this system is a mediumspeed coal mill of model ZGM123GIII produced by Beijing power equipment group Co, Ltd, and the specific parameters are shown 2017年8月1日 This model can be used to estimate the key parameters that are difficult to measure or cannot be measured: 1) coal powder or raw coal contents in coal mills, which can Modeling of a medium speed coal mill ScienceDirect2015年8月1日 Power plant performance and reliability is highly influenced by coal mills that grind, dry, and transport coal to the furnace This paper presents a review of the current state Review of control and fault diagnosis methods applied to coal Case study – Excessive coal in the mill Mill problems due to all possible causes such as improper aircoal input, change in coal quantity, incorrect settings,Coal IJSER
.jpg)
Modeling and Control of Coal Mill
Coal mill is an important component of the thermal power plant It is used to grind and dry the moisturized raw coal and transport the pulverized coal – air mixture to the boiler Poor dynamic 2022年7月26日 Aiming at the typical faults in the coal mills operation process, the kernel extreme learning machine diagnosis model based on variational model feature extraction and kernel principal component Fault Diagnosis of Coal Mill Based on Kernel Extreme Learning Machine 2015年8月1日 Mill problems originate mainly due to poor controls or faults occurring within the milling system As discussed by GQ Fan and NW Rees [3], the control of mills remains very simple in most of the power plants due to the fact that the mill system is highly nonlinear with strong coupling among the variables and it is very difficult to measure some important Review of control and fault diagnosis methods applied to coal 2022年2月24日 Curves of mill productivity, power consumed, specific surface of coal dust in terms of the relative rotational speed of the ball drum mill Improving the efficiency of the coal grinding process in ball drum
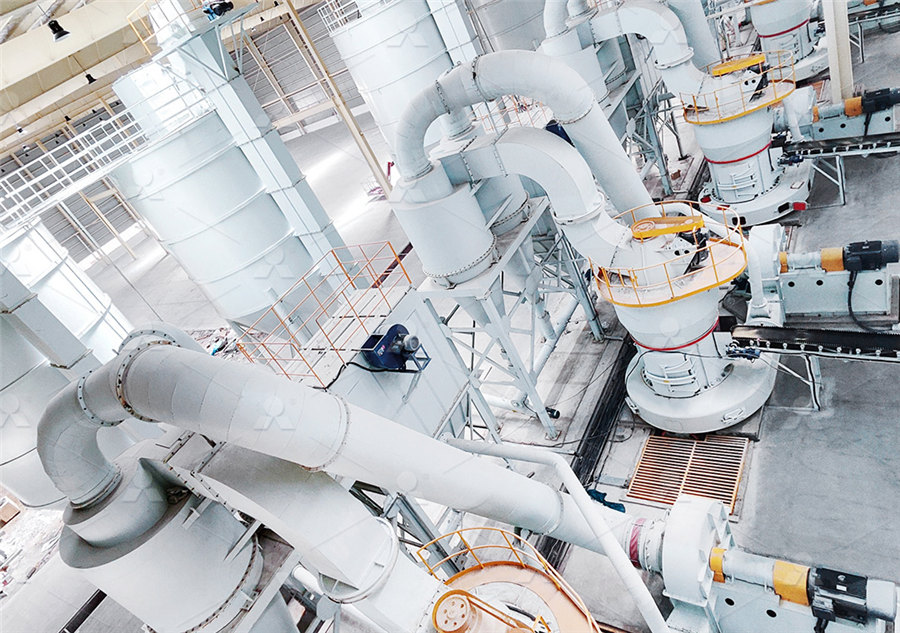
(PDF) Effect of Biomass Carbonization on the Grinding of Coal
2020年8月21日 CO2 emissions from coal power generation could be reduced by maximizing the amount of torrefied biomass that can be used in pulverizedcoalfired power plants2022年3月25日 Under a given production running condition, the electricity current intensity of the coal mill decreases from 479 AM to 465 AM, which is a remarkable achievement for the coal mill running process(PDF) A Modeling and Optimizing Method for Electricity Current 2020年8月12日 As one of the three major forces of coal mills, the grinding force exerts a significant impact on the working process of coal mills and parameters like mill current and outlet temperatureAn investigation of performance characteristics and energetic 2020年1月1日 of a medium speed coal mill is provided in Fig 1 The common malfunctions in coal mill operation are due to coal blockage, coal interruption, and coal selfignitionEarly Warning of Critical Blockage in Coal Mills Based on
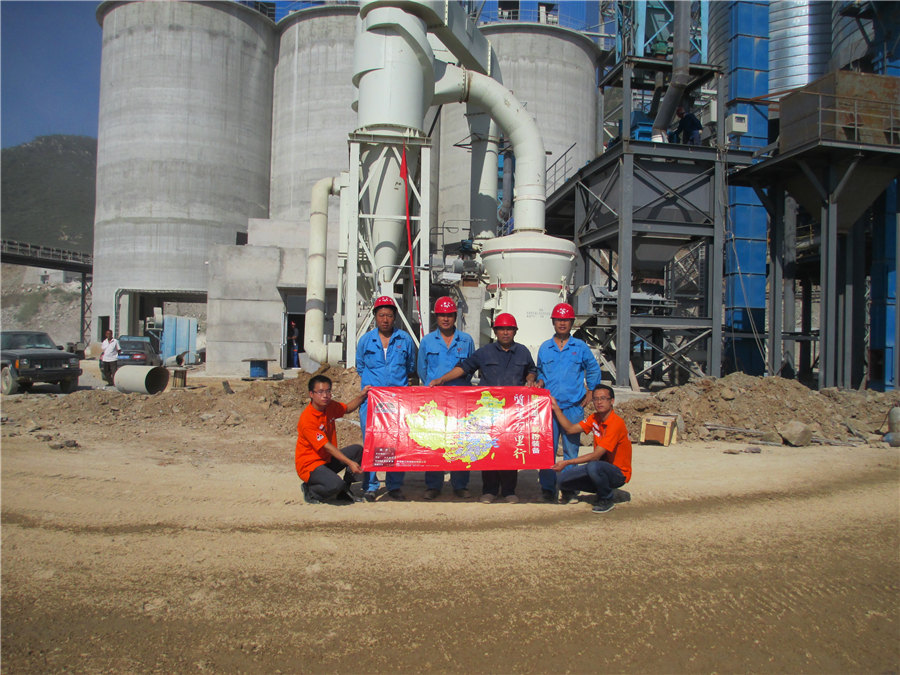
Coal drying Grinding Coal Mill by ASen Medium
2020年7月31日 Secondly the speed of combustion is increased with reaction surface of coal particles and the temp The surface is increased by grinding the coal to a higher fineness represented by lower residue on standard sieve of 90 µ Recommended fineness of ground coal for kiln and PC against volatiles presence is demonstrated as –The vertical roller mill (VRM) shown in Figure 4 is an air swept, mediumspeed, vertical pulverizer with integral classifier It pulverizes coal by applying hydraulicallyloaded grinding pressure through three grin ding rollers onto a rotating bed of coal Grinding pressure can be adjusted to account for variations in coalA Comparison of Three Types of Coal Pulverizers Babcock Powersonable to expect that grinding coal will take about the same amount of grinding element pressure regardless of the type of mediumspeed, vertical spindle pulverizers you use In our experience the spring frame of an MPS mill tuned for maximum true capacity will be set at about 20 tons minimum force on the grinding tires A bowl mill spring or“Blueprint” Your Pulverizer for Improved Performance2020年8月14日 The coal mill is one of the important auxiliary engines in the coalfired power station Its operation status is directly related to the safe and steady operation of the units(PDF) Application of ModelBased Deep Learning Algorithm in Fault
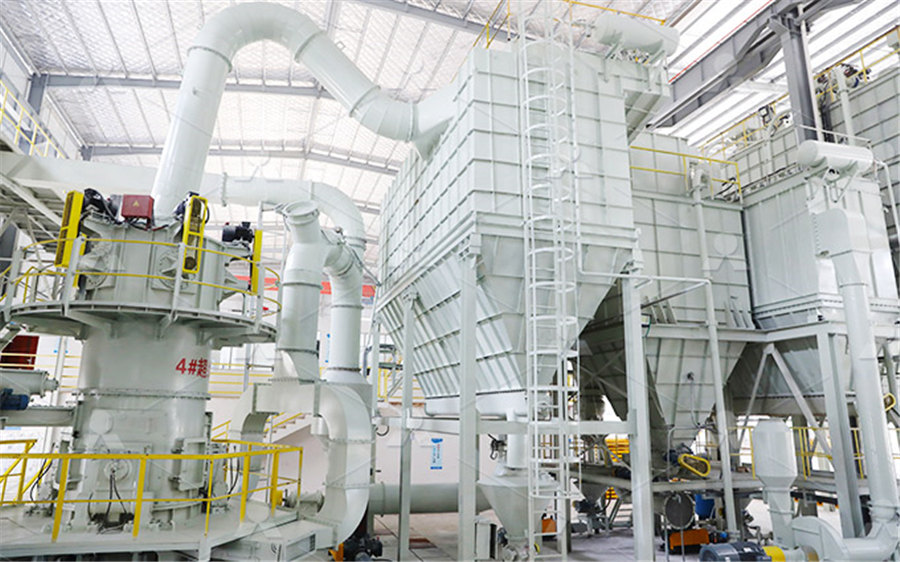
Wet and dry grinding of coal in a laboratoryscale ball mill: Particle
2019年10月1日 Request PDF Wet and dry grinding of coal in a laboratoryscale ball mill: Particlesize distributions In this study, experimental data for wet and dryground coal samples under wet and dry The mediumspeed coal mill system is mainly composed of raw coal bunker, coal feeder, coal mill, primary fan, sealing fan, hot and cold air regulating valves View in fulltext Similar The structure of MPS mediumspeed coal mill systemZGM medium speed roller mill 1 Introduction 11 Purpose ZGM type medium speed roller mill is widely used in coal powder preparation system of electric power, metallurgy, cement, chemical industry and other industries, as well as coal pulverizing system of cement, chemical industry, mining and other industriesZGM type Mediumspeed Rolling coal millpower plant equipment2016年11月22日 The cutting chip may not form in each grit pass in the grinding zone Thirdly, grinding cutting speed is much higher than that of other machining process Normally, it is 10 times higher High grinding speed provides increased material removal rate, but it also introduces the problem of high grinding temperatureEffect of different parameters on grinding efficiency and its
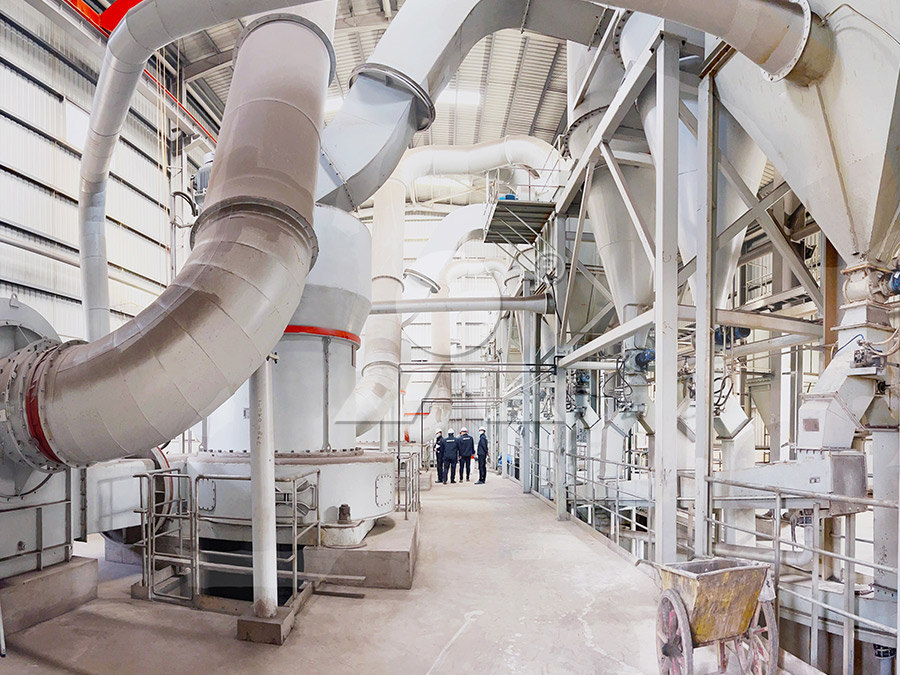
MTM MediumSpeed Grinding Mill Zenith Crusher
MTM MediumSpeed Grinding Mill Features Upgraded Structure The innovative change of the spring connection structure not only reduces shock of large materials on the aixs and bearing, but also enhances crushing strength of rollers Energysaving Production Its electricity consumption is lower than that of ball mill of the same level by over 60%2024年3月1日 The main influencing factors for grinding damage include abrasive grit size, grinding depth, workpiece feed speed, and wheel speed According to the research of Sabia et al [13], the grinding subsurface damage depth (SSD) of glass ceramics is proportional to 5 times the average abrasive grit sizeMa et al [14] found that the SSD of fused silica is 4–6 times the Optimization of grinding process for hard and brittle materials 2017年10月26日 The following are factors that have been investigated and applied in conventional ball milling in order to maximize grinding efficiency: a) Mill Geometry and Speed – Bond (1954) observed grinding efficiency to be a function of ball mill diameter, and established empirical relationships for recommended media size and mill speed that take this factor into Factors Affecting Ball Mill Grinding Efficiency2017年8月1日 In thermal power plants, mediumspeed mills are widely used for grinding coal particles, where hot primary air is used to dry the ground pulverized coal particles (PCPs) in the meantime [8] However, when moisture in lignite is higher than its designed value, the original drying capacity of coal mills often fails to dry PCPs to a desired levelModeling of a medium speed coal mill ScienceDirect
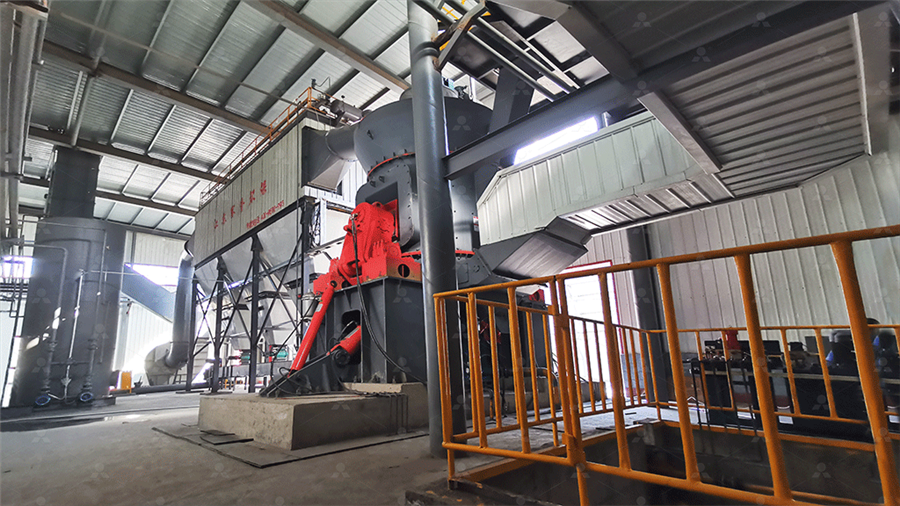
Modeling of a medium speed coal mill Semantic Scholar
2017年8月1日 Semantic Scholar extracted view of "Modeling of a medium speed coal mill" by Yaokui Gao et al As the vital auxiliary machine of the coalfired power plant, Calculation of energy required for grinding in a ball mill N Magdalinovic Engineering, Materials Science 1989; 342003年5月1日 Pulverizing the slice sample into the minimum particle sample particle size of 00750125 mm leads to an increase in the pore volume per unit mass of coal by 3953% and 1829% for tested medium Studies of the relationship between coal petrology and grinding 2017年5月1日 As the significant ancillary equipment of coalfired power plants, coal mills are the key to ensuring the steady operation of boilers In this study, a fault diagnosis model was proposed on the Modeling of a medium speed coal mill ResearchGate2020年4月7日 Monitoring and diagnosis of coal mill systems are critical to the security operation of power plants The traditional datadriven fault diagnosis methods often result in low fault recognition rate or even misjudgment due to Modeling of Coal Mill System Used for Fault
.jpg)
Coal Pulverizer Design Upgrades to Meet the Demands of Low
coal pulverizer systems supplied by RPI originally designed for low, medium and high speed pulverization have undergone design upgrades and improvements These machines include Ball Tube Mills (BTM), MPS mills and Atrita@ Pulverizers, respectively The Atrita@Pulverizer has been upgraded for better coal fineness and longer service life BTM2014年9月9日 The dense medium cyclone (DMC) process used in coal beneficiation plants is studied from a control system perspective Employing the dynamic model of the DMC process derived from mass flow balance Medium Density Control for Coal Washing Dense Medium Cyclone Circuits2023年1月1日 Mediumspeed vertical spindle mills such as Most coal mills are designed around achieving 100% throughput at 50–52 HGI and grinding lowHGI coals can lead to problems regarding their capacity to deliver (1500°C) Generally, coal combustion efficiency increased with temperature, but some coals showed poorer combustion Advances in pulverised fuel technology: understanding coal grinding 2020年7月2日 This paper focuses on the determination of the selection function parameters α, a, μ, and Λ together with the exponent factors η and ξ describing the effect of ball size on milling rate for a (PDF) Effects of Ball Size Distribution and Mill Speed and Their
.jpg)
Technique to Investigate Pulverizing and Abrasive Performance of Coals
2021年11月4日 Three types of interactions between mineral particles and grinding components, Fnnormal force, Fttangential force, mmass, vspeed 2015年5月7日 The mean value of coal flow parameter is 13584 kg/s, coal mass accumulation is 2,196 kg, coal output temperature is 83296 0C, coal moisture is 0021, and coal fineness is 75338 % View Show Review of Control and Fault Diagnosis Methods Applied to Coal 2024年8月27日 Grinding media plays a crucial role in the energy transfer during the mineral particle size reduction process []The energy carried by these media, along with its distribution and conversion, significantly impacts the mill’s production capacity, grinding efficiency, and final particle size of the product []The size, shape, ratio, and filling rate of the grinding media are Investigating the Influence of Medium Size and Ratio on Grinding the cascading motion of the grinding medium can only be qualitatively described in a simple manner In the process of grinding, different motions of the grinding medium follow different grinding mechanisms It is worth denoting that a throwing medium has an impact effect while a cascading medium facilitates the grinding effectPAPER OPEN ACCESS You may also like IOPscience
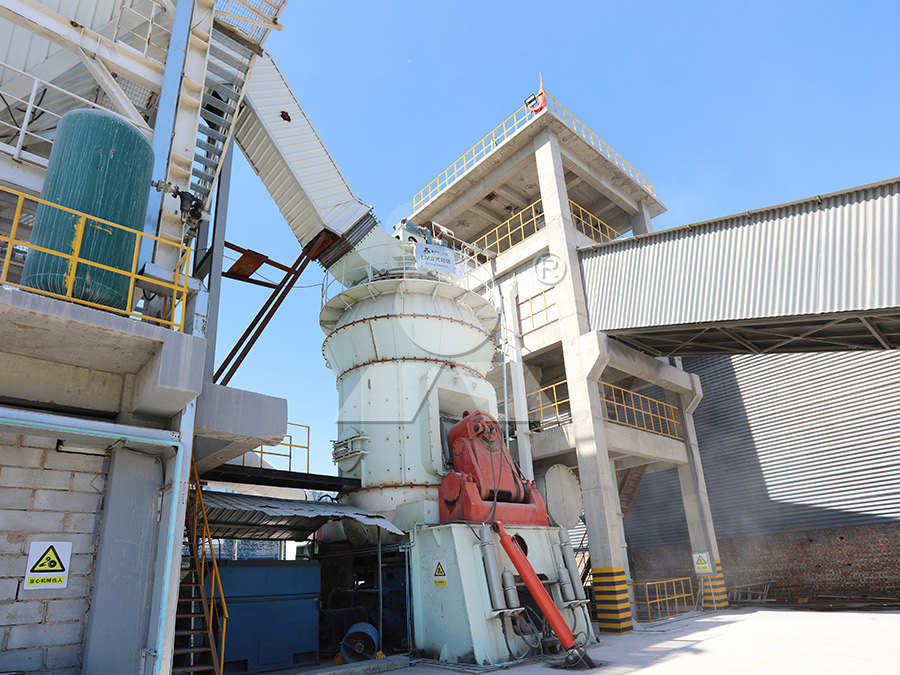
EnergyEfficient Advanced Ultrafine Grinding of
2023年7月10日 The present literature review explores the energyefficient ultrafine grinding of particles using stirred mills The review provides an overview of the different techniques for size reduction and the impact of energy 2014年2月1日 In this article, effects of moisture content and coal mixtures on grinding properties of the samples of two different fine coals, which were used in the Göltaş Cement Factory in Isparta (Turkey The Effects of Moisture Content and Coal Mixtures 2004年10月17日 Process and wear state are inferred from statistical signal processing of AE signals (Oppenheim and Schafer 1989) coupled with 'datadriven' pattern classification, multivariate statistical MONITORING OF DENSE MEDIUM CYCLONE PERFORMANCE 2015年9月10日 As a result of the high grinding speed, the time required to form a single grinding chip is very short during ultrahigh speed grinding In addition, the elastic deformation layer on the surface of a workpiece is much shallower2731 Because of the reduction in the swelling ratio with increased grinding speed, the bulging height formedCFRP Grinding Wheels for High Speed and UltraHigh Speed Grinding
.jpg)
Schematic diagram of the working principle of MPS medium speed coal
Download scientific diagram Schematic diagram of the working principle of MPS medium speed coal mill [1] from publication: Fault Diagnosis of Coal Mill Based on Kernel Extreme Learning Machine 2019年8月11日 Water scarcity dictates to limit the use of water in ore processing plants particularly in arid regions Since wet grinding is the most common method for particle size reduction and mineral A comparative study on the effects of dry and wet grinding on 2009年1月1日 Wider coal lines and larger power plant units necessitate measures for increasing the capacity of the mills without driving up power consumption and installation costsCFD Modeling of MPS Coal Mill for Improved Performance and Safety2015年8月1日 Mill problems originate mainly due to poor controls or faults occurring within the milling system As discussed by GQ Fan and NW Rees [3], the control of mills remains very simple in most of the power plants due to the fact that the mill system is highly nonlinear with strong coupling among the variables and it is very difficult to measure some important Review of control and fault diagnosis methods applied to coal

Microgroove grinding of monocrystalline diamond using mediumfrequency
2020年8月1日 That is the workpiece is suffering higher grinding resistance forces Hence, the feedrate of PCD wheel is decreased by 4 % (realtime) and the surface reground again by two passes before feeding ends In the case of average current being less than predetermined current, the feedrate is gradually increased by 2 % to improve grinding efficiency