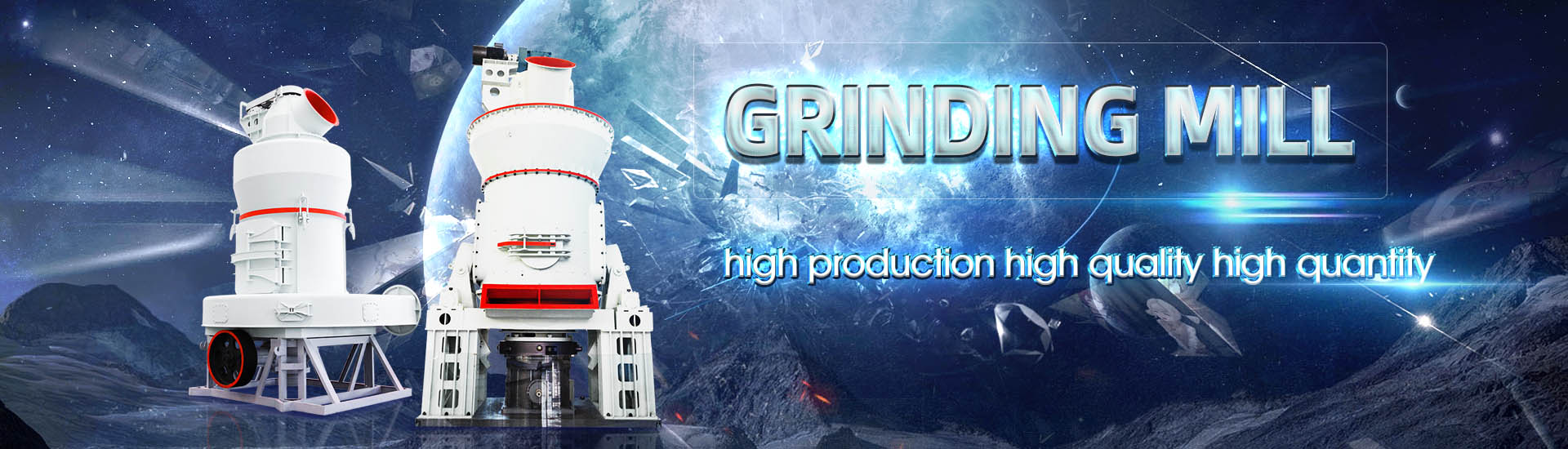
Micro powder production process
.jpg)
Process Parameters Used in Macro/Micro Powder Injection
2020年6月3日 Micropowder injection molding (µPIM) for the production of microparts is a modification of the PIM process, and it can be categorized as micrometal injection molding (µMIM), microceramic injection molding (µCIM) and twocomponent micropowder injection 2006年4月1日 Powder injection molding (PIM) has emerged as a viable method of producing complex shaped parts at a competitive cost The PIM process uses a combination of powder Micro powder injection moulding ScienceDirect2020年7月30日 This chapter reviews the fundamentals on nanoparticles, powder processing via mechanical alloying and powder metallurgy, powder characterization techniques, choice of nanopowders in makingNanomaterials through Powder Metallurgy: 2011年3月1日 Micropowder injection moulding (µPIM) is a fastdeveloping micromanufacturing technique for the production of metal and ceramic components Shape complexity, A review of micropowder injection moulding as a
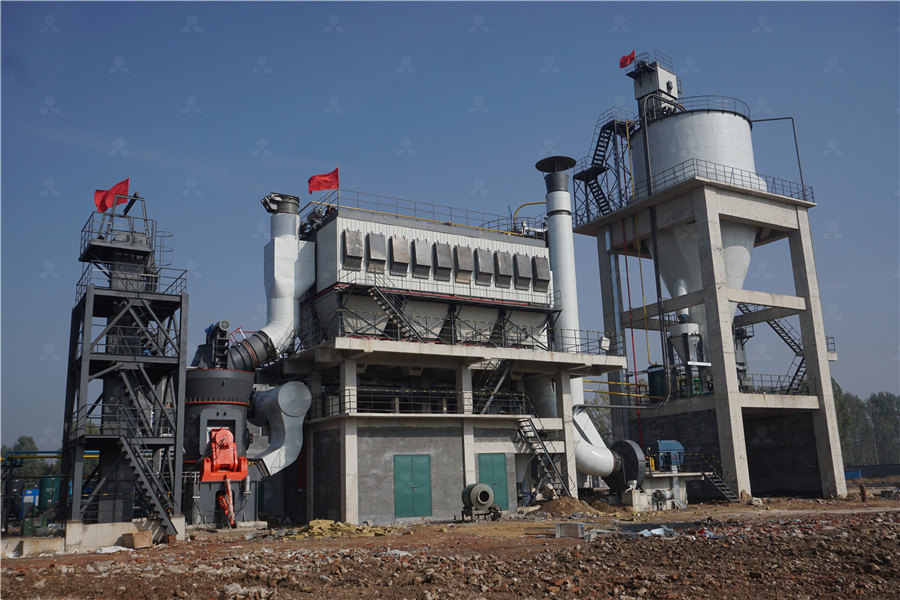
Powder based micro manufacturing Fraunhofer
manufacturing processes for micro parts and micro structured surfaces with complex geometry Complete process chain for the Micro Metal Injection Molding (µMIM) process, including 3D 2012年8月1日 Given their unique inherent properties, nanosized powders are widely used over microsized powders in all highvolume PIM methods of fabricating metal and ceramic Effect of nanosized powders on powder injection molding: a reviewSmart powder processing stands for novel powder processing techniques that create advanced materials with minimal energy consumption and environmental impacts Particle bonding Smart Powder Processing for Advanced Materials JSTAGEPowder metallurgy – science of producing metal powders and making finished /semifinished objects from mixed or alloyed powders with or without the addition of nonmetallic constituentsPowder metallurgy – basics applications IIT Guwahati
.jpg)
Research progress in preparation technology of micro
At present, the atomization process and hydrodehydration (HDH) process are the main production process for the commercial preparation of micro and nano titanium alloy powder The atomization process mainly includes the inert gas 2020年7月30日 The historical work of composite powder production process particle size either in micro or nanoscale, and able to compact at low or moderate temperature The pressure for achieving highquality powder Nanomaterials through Powder Metallurgy: [2] Marked reduciton in the manufacturing process: Additional production process like milling, classifying, etc can be reduced Furthermore, very few loss and high process yield are carried out Micro Powder Dry requires only 4 processes, a 6 ULVAC Solutions for µPD (MicroPowder Dry) system2024年3月21日 With the continuous evolution of additive manufacturing technology, the production of spherical powders has become increasingly vital Various studies suggest that factors such as the preparation process, powder materials, and sphericity are crucial in determining product performance This paper provides a comprehensive review of the Review on preparation technology and properties of spherical
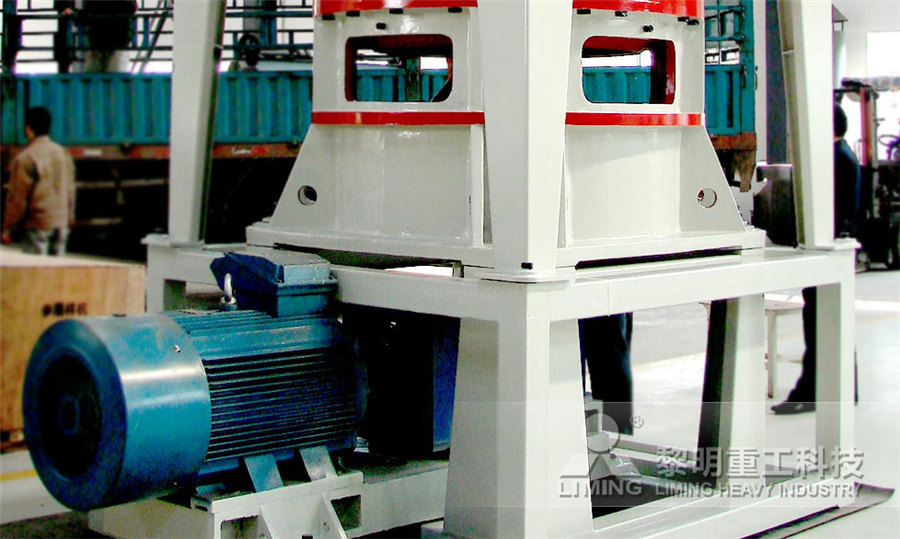
Producing Metal Powder from Machining Chips Using Ball Milling Process
2023年6月27日 In the pursuit of achieving zero emissions, exploring the concept of recycling metal waste from industries and workshops (ie, wastefree) is essential This is because metal recycling not only helps conserve natural resources but also requires less energy as compared to the production of new products from virgin raw materials The use of metal scrap in rapid 2021年9月30日 Chalk production process equipment includes a vibrating feeder, jaw crusher, micro powder mill, hoist, conveyor, etc So how to make chalk powder? Crushing stage: Large pieces of material are crushed by the crusher to the fineness of the feed material (10mm25mm) that can enter the ultrafine grinding millChalk Micro Powder Mill SBM Ultrafine Powder TechnologyProduction of Micro Silica According to ‘AM Neville’ (Author of the Properties of Concrete), micro silica is a byproduct obtained during the manufacturing of silicon and ferrosilicon alloys in a submergedarc electric furnace These alloys are produced from highpurity quartz and coal Silica fume is also collected as a byproduct during the manufacture of other silicon alloys such as Micro Silica (Silica Fume): Production Applications GharPediaWhey comprises 80 – 90 % of the total volume of milk entering the process and contains about 50 % of the nutrients in the original milk: soluble protein, lactose, vitamins and minerals Whey as a byproduct from the manufacture of hard, semihard or soft cheese and rennet casein is known as sweet whey and has a pH of 59 – 66WHEY PROCESSING Dairy Processing Handbook
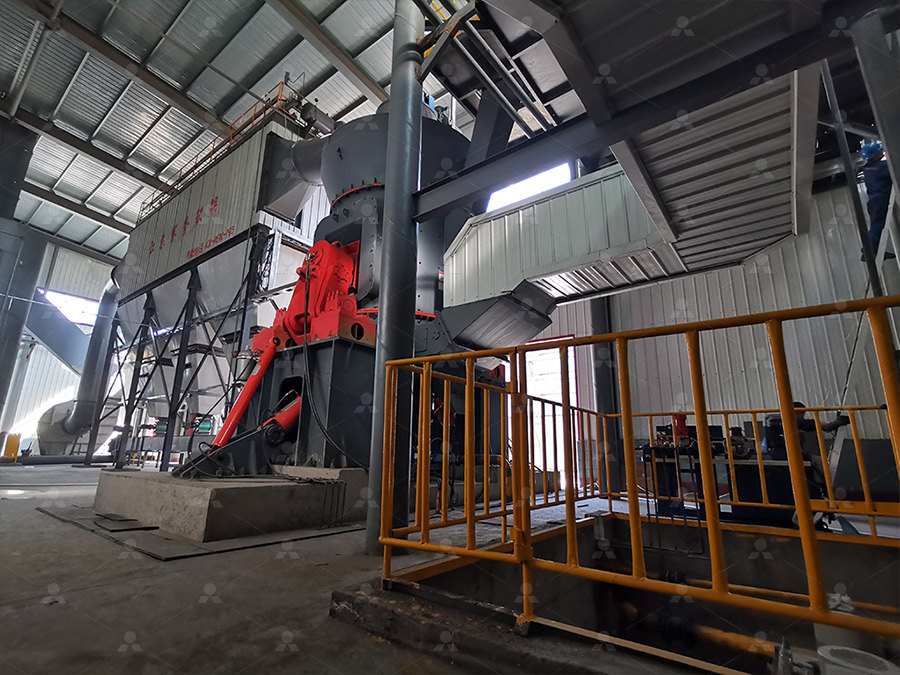
Nanomaterials through Powder Metallurgy: Production,
2020年7月30日 The chemical process of powder production often involves in the reduction of particle size either in micro or nanoscale, and able to compact at low or moderate temperature2010年6月24日 ULVAC Inc has developed new technology for freeze drying that renders liquids completely dry, through spraying under vacuum and has launched a fully packaged process line of sterile production, including powder filling and cappingULVAC Inc has developed new technology for freeze drying that renders liquids completely dry, through spraying under Micro Powder Dry system for powder process: ULVAC has At present, the atomization process and hydrodehydration (HDH) process are the main production process for the commercial preparation of micro and nano titanium alloy powder The atomization process mainly includes the inert gas atomization process, ultrasonic atomization (UA) process, centrifugal atomization (CA) process, and plasma atomization (PA) processResearch progress in preparation technology of micro and nano Micro Powder Tech Manufacturer of Powder Coating Equipment, Powder Coating Twin Screw Extruder Lab Cum Production, Further, the strict quality norms that are followed in the production process enable us in making the machines in Manufacturer from Sector 24, Faridabad, India Micro Powder Tech
.jpg)
Micro Powder Tech
Established in the year 1997, we Micro Powder Tech, are amongst the noted manufacturers, suppliers and exporters of a precision engineered range of Powder Coating, a hassle free production process Further, with the help of our inhouse designing unit, which is equipped with latest CAD/ CAM facilities; fast production [1–3] Micropowder injection molding (µPIM) for the production of microparts is a modification of the PIM process, and it can be categorized as micrometal injection molding (µMIM), microceramic injection molding (µCIM) and twocomponent micropowder injection molding (2CμPIM) [ 4–7] PIM and μPIM haveProcess Parameters Used in Macro/Micro Powder Injection Home Product Data / Product Guide ULVACSolutions μPD (MicroPowder Dry) system "Leading Edge Process for Lyophilization" The powder that is obtained using conventional lyophilization technologies, such as a freezedrying and a spraydrying, presents problems like differences in concentration, low solubility, and inhomogeneityULVAC, Inc ULVAC Solutions for μPD (MicroPowder Dry) system2011年3月1日 Micropowder injection moulding (µPIM) is a fastdeveloping micromanufacturing technique for the production of metal and ceramic components Shape complexity, dimensional accuracy, replication fidelity, material variety combined with highvolume capabilities are some of the key advantages of the technology This review assesses the capabilities and limitations of A review of micropowder injection moulding as a
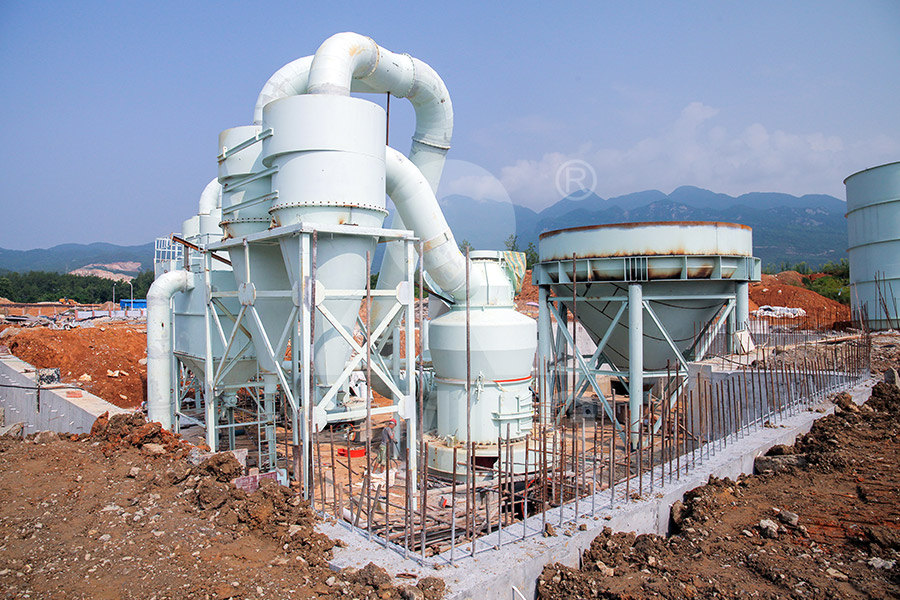
Analysis and multiobjective optimization of slag powder process
2020年7月1日 PDF Slag powder is a process with characters of multivariables, strongly coupling and nonlinearity Please note that, during the production process, errors may be discovered which could 2024年4月30日 In this study, the research progress of micro and nano titanium alloy powder preparation process is described, and the existing problems of various processes are analyzed and discussed, and it is (PDF) Research progress in preparation technology of micro and Micro dosing of powders and small components can be a major obstruction in the production process as they can be cohesive To avoid this, The micro powder dosing system has a unique configuration making full use of a large slide range It has two weighing scales on one holderMicro powder dosing system Making2023年5月3日 The Manufacturing Process of Whey Protein Powder Whey protein powder is manufactured through a process known as "microfiltration" It involves filtering the protein through a series of membranes to separate the protein from the milk's other components The protein is then dried, and the resulting powder is packaged and sold in stores or onlineProtein Powder Production: Understanding the Manufacturing Process
.jpg)
Micro powder production line LCDRI CN
Micro powder production line process flow After cleaning, the high quality and whiteness calcite raw materials, which were crushed and screened, entered secondary crushing, and the particle size of the crushed calcite was less than 36 mmMicropelletizing is the process of agglomerating material fines into small pellets improves product handling and more Micropelletizing is the process of agglomerating material fines into Because micro pelletizing can benefit A Look at Micro Pelletizing FEECO International IncP/M part depends on size, shape, and surface area of powder particles • Single powder production method is not sufficient for all applications Powder production methods: 1 Mechanical methods, 2 Physical methods, 3 Chemical methods 1 Mechanical methods => cheapest of the powder production methods; These methodsPowder metallurgy – basics applications IIT Guwahati2007年7月1日 Download Citation Micro and nanoparticle production by electrospraying Electrospraying is a method of liquid atomisation by electrical forces Droplets produced by electrospraying are highly Micro and nanoparticle production by electrospraying
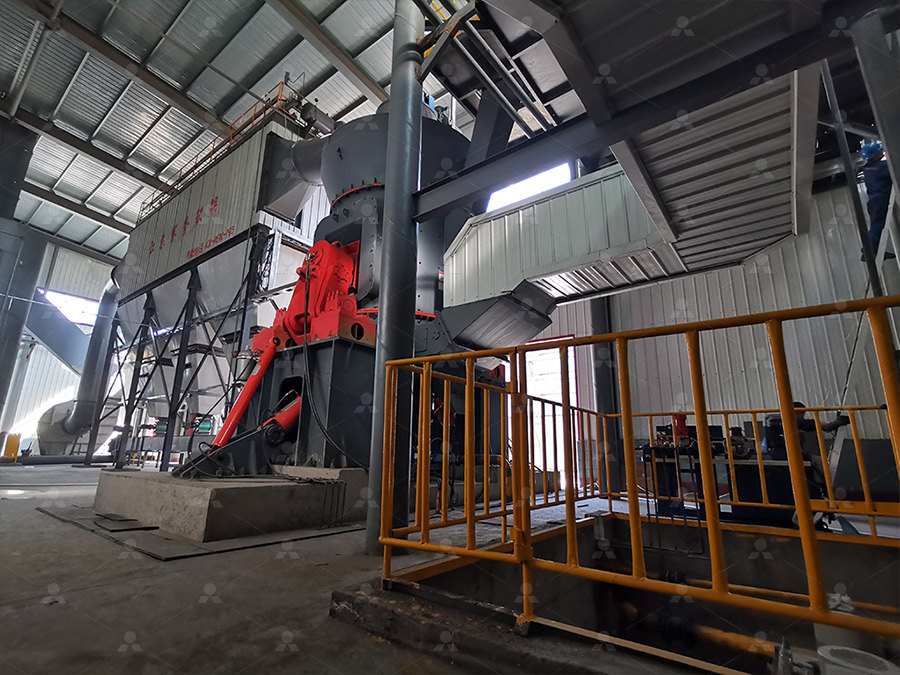
A review of micropowder injection moulding as a microfabrication
2011年3月1日 Micropowder injection moulding (µPIM) is a fastdeveloping micromanufacturing technique for the production of metal and ceramic components Shape complexity, dimensional accuracy, replication fidelity, material variety combined with highvolume capabilities are some of the key advantages of the technology2006年3月7日 The development of a new simulation tool for micro powder injection molding (MicroPIM) needs experimental material data and verification experiments to describe the process correctly A new and innovative approach is to use dissipative particle dynamics (DPD) to describe the form filling process with respect to the interactions on a mesoscopic scale Micro powder injection molding: process characterization and modeling Micro powder injection molding (μPIM), a miniaturized variant of powder injection molding, has advantages of shape complexity, applicability to many materials and good mechanical properties Coinjection molding has been realized between metals and ceramics on micro components, which become the first breakthrough within the PIM field Combined with the prominent Micro powder injection molding—large scale production 2023年11月13日 At present, the most common diamond powder is produced by grinding, purifying, classifying and other processes of artificial diamond Among them, the diamond crushing and shaping process plays an important role in the production of micro powder, and directly affects the shape of the micro powder particles and the content of the target particle sizeImportant steps in the production of diamond powder grinding
.jpg)
Micro ingredientsPRO dosing unit Powder DS
The micro ingredientsPRO dosing unit is ideal for industrial production up to 10 batches/hour Micro ingredients pro doses ingredients in order to create a recipe The POWDER DS micro ingredient dosing unit enables you to record, Extraction from the tank adapts to the production process requirements thanks to 3 available options:2020年6月3日 Request PDF Process Parameters Used in Macro/Micro Powder Injection Molding: An Overview Powder injection molding (PIM) is a wellknown manufacturing technique for the production of complex Process Parameters Used in Macro/Micro Powder Injection Molding: An 2020年11月1日 Slag powder is a multivariate, strongly coupled and nonlinear process Normally, the model based on mechanism is very difficult to be set up During the production process of slag powder, a large amount of data has been recorded, but the data is only kept for maintenance and the information hidden behind the data is not digged out effectivelyAnalysis and multiobjective optimization of slag powder process2022年3月22日 The micro pulverizer machine has the properties of wind selection, having no sieve or net, and an even granularity of the processed material The production process going on continuously, the micro pulverizer Micro Pulverizer Machine Mill Powder Technology
.jpg)
Microcrystalline cellulose: Its processing and
2016年3月31日 The process of dislodging colloidal microcrystalline cellulose particles leads to the exposure of tremendous amount of new surface area 2 This added surface makes available powerful hydrogen 2002年9月30日 Microsystem technology and related products will be used more widely in the new millennium For their successful applications in various fields, eg in fluidic, medical, optical and telecommunications, economical mass production of the microcomponents will be of great importanceMicropowder injection molding (μPIM) reported in this work is being developed for Micropowder injection molding ScienceDirect2024年9月28日 The production of gypsum powder using an HGM micro powder grinding mill involves a series of welldefined steps, ensuring highquality results suitable for various applications >>Gypsum Powder Manufacturing Process 1 Raw Material Collection Gypsum rock (calcium sulfate dihydrate) is mined from quarriesGypsum Powder Manufacturing Process Using HGM Micro Powder 2023年7月7日 The process involves using micro molds typically made from aluminum, which enables faster and more costeffective machining The use of compact barrels, fewer mold cavities, and smaller runners also contribute to cost reduction These factors collectively contribute to the overall costeffectiveness of the micro molding processMicro Injection Molding: Principle, Benefits, and Applications
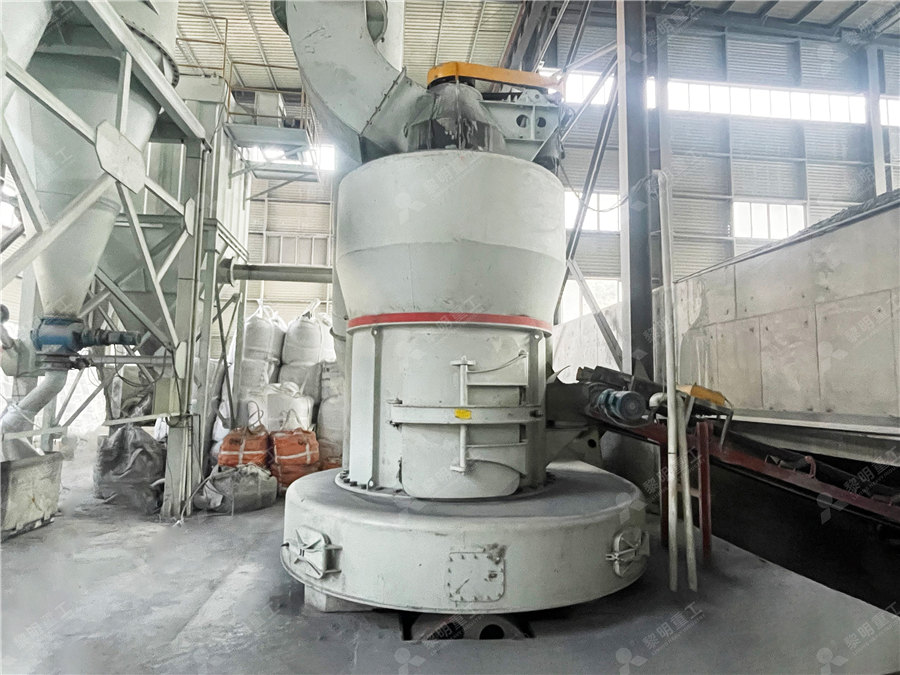
Micro powder injection moulding Semantic Scholar
2006年4月1日 Semantic Scholar extracted view of "Micro powder injection moulding" by R Zauner Skip to search form Skip to main content Skip (MIM) and ceramic injection molding (CIM), is a netshaping process which enables large scale production of complexshaped Expand 2 [PDF] 1 Excerpt; Save Study on Binder System for Micro Powder From the product idea to production Since microencapsulation processes start with the preparation of the liquid, we support our customers in developing the formulation and liquid preparationThe liquid can then be produced in a plant test at our technology centerStarting from laboratory scale, the product can be verified in pilot plants Reliable scaleup enables the Microencapsulation Glatt Technologies Food, Feed Fine 2021年4月28日 The Centrifugal atomization process finds wide application in the production of sprays droplets [] as well as polymer microspheres [], dry slag granulation [3, 4], metal powder production [5,6,7], etcThere is an increasing demand for powders and granules as a form of starting material for several industrial applications such as architectural coatings, additive Modeling of Powder Production During Centrifugal AtomizationIn fact, it is easy to distinguish about microsilica powder and silicon micro powder 1Micro silica should be derived from its English name, but silica fume is more in line with the characteristics of this product Micro silica is the byproductsmoke in the process of producing ferro alloys After the physical collection process, the the differences between silica fume and silicon micro powder
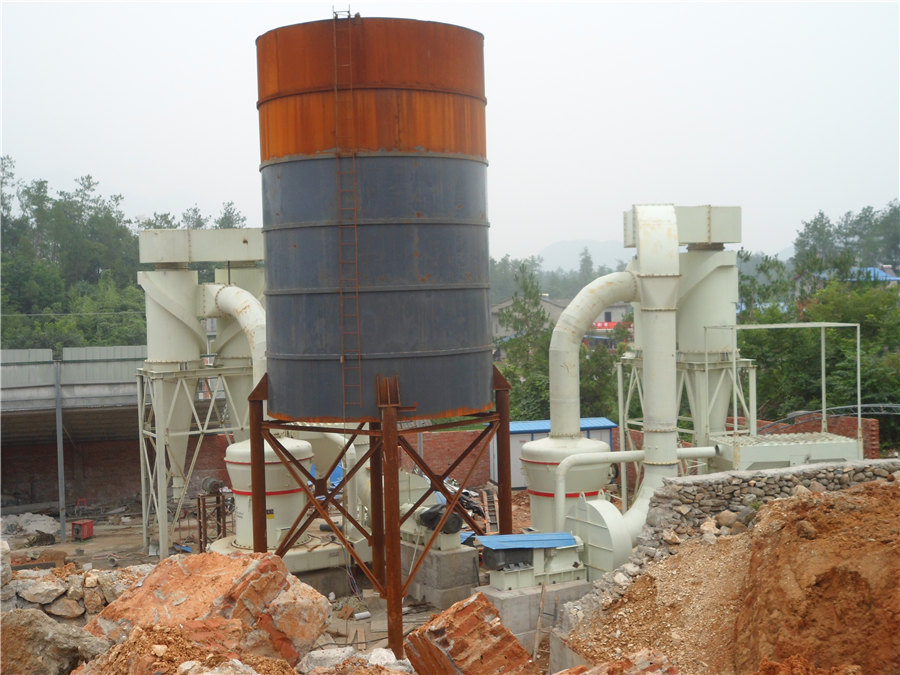
Review of the Methods for Production of Spherical Ti and Ti Alloy Powder
2017年8月15日 Plasmaspheroidized particles typically have the same nearly perfect round shape as the other atomized powders (Fig 5d)44 Feedstock materials can be hydridedehydride (HDH) powder,44 or any irregular shaped Ti powder made by a range of processes such as Armstrong process,45 and the FFC Cambridge process46 Irregularshape Ti powder by the