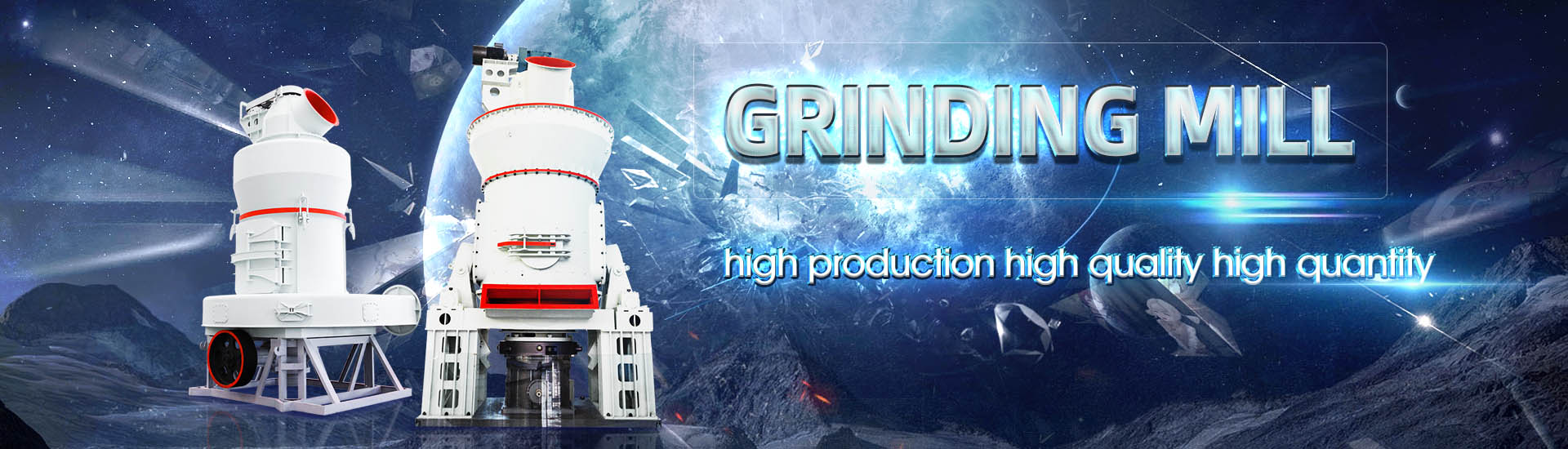
HOME→Ore mill discharge particle size Ore mill discharge particle size Ore mill discharge particle size
Ore mill discharge particle size Ore mill discharge particle size Ore mill discharge particle size
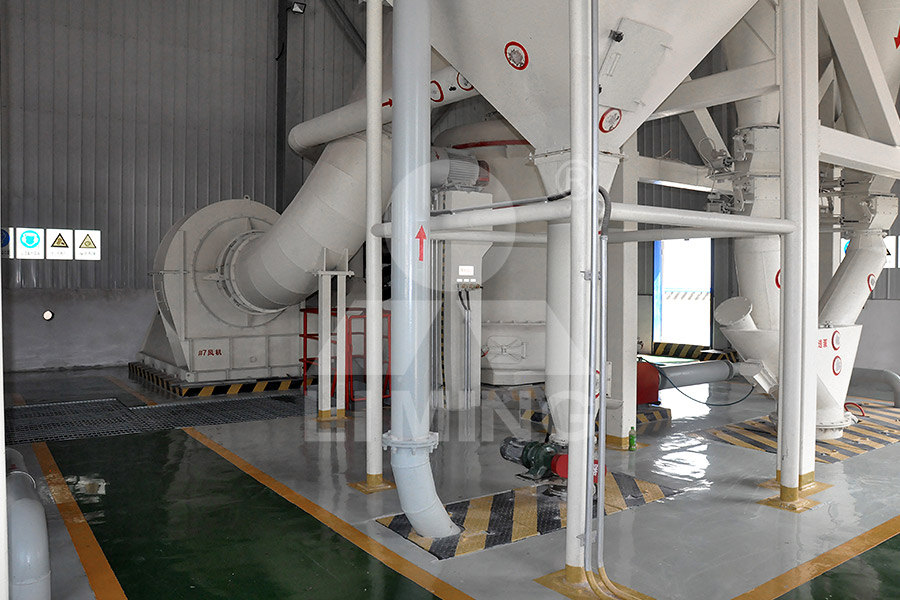
A comparative study on a newly designed ball mill and the
2020年1月1日 Discharge of desired particle size is directly related to critical speed of the mill Mill with lifters has maximum discharge of desired particle size Mill with lifters has minimum Estimated values were obtained through a scaleup process of BD 20 mm balls to industrial mills Investigation of laboratory conditions effect on prediction accuracy of size distribution ofComparison of measured and predicted PSD of mill 2017年9月1日 The objective of this work is to assess the influence of fine grinding in ball mills and stirred mills on valuable mineral liberation and particle shape characteristics of UG2 ore, a Fine grinding: How mill type affects particle shape characteristics 2020年5月28日 The results clearly show that for any ore blend, it is important to know the ore RT before grinding in the ball mill to obtain the desired particle size fraction with acceptable hematite liberation The new approach can be used in Investigation on Iron Ore Grinding based on Particle
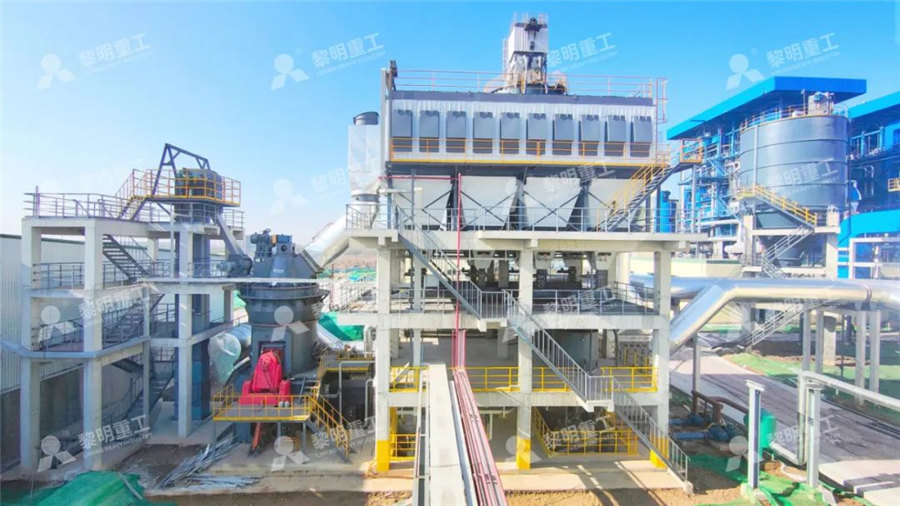
Estimation of Grinding Time for Desired Particle Size Distribution
2020年1月3日 Ball mills are progressively used to grind the ores for particle size reduction and to liberate valuable minerals from the ores The grinding of ore is a highly energyintensive 2021年10月21日 This study presents a novel derived theoretical model for MAassisted leaching in investigating the effects of ball mill parameters on the particle sizes (retained and recovered)Effect of Ball Mill Parameters’ Variation on the Particles of a 2023年3月16日 Feed size was divided into two fractions of (+238 −4) and (+2 −238) millimeters, from which different feeds with different weight and size percent values were fed Fractal approach of particle size distribution description of ball The geological model describes quantitatively and spatially modal composition and texture of the ore The particle breakage model that describes quantitatively what kind of particles will beParticle size distributions of mill feed ( ) and discharge ( )
.jpg)
Effect of ball and feed particle size distribution on
2018年2月1日 In another study to investigate ball size distribution on ball mill efficiency by Hlabangana et al [50] using the attainable region technique on a silica ore by dry milling, a threeball mix of DOI: 101016/jmineng2022 Corpus ID: ; Characterization of chalcopyrite ore under high voltage pulse discharge: Particle size distribution, fractal dimension, specific energy consumption, grinding kineticsCharacterization of chalcopyrite ore under high voltage pulse discharge 2016年6月6日 The discharge end of this mill must incorporate some method of conveying the pulp to the outside of the Tests currently under way show urethane to be sensitive to ore pebble or worn ball particle size Particles over SAG Mill Liner Design 911Metallurgist2016年6月6日 For circuits classifying mill discharge at a coarse size (coarser than approximately 10 mm), trommels can also be considered to classify mill discharge Trommels are less favorable in applications requiring high classification efficiencies and can be constrained by available surface area for highthroughput millsSAG Mill Grinding Circuit Design 911Metallurgist
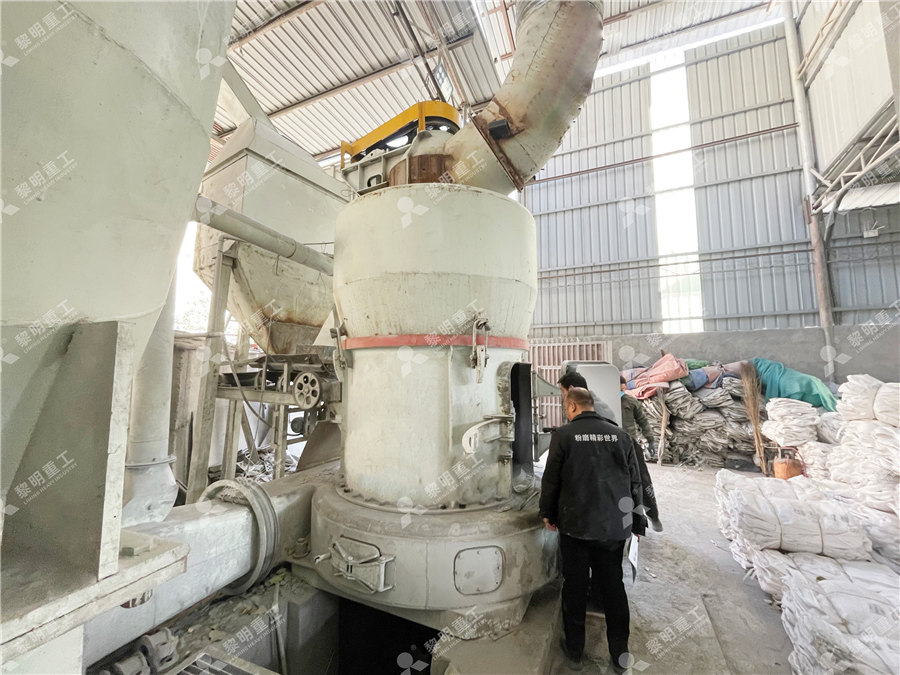
Characterization of chalcopyrite ore under high voltage pulse discharge
2022年6月1日 Request PDF Characterization of chalcopyrite ore under high voltage pulse discharge: Particle size distribution, fractal dimension, specific energy consumption, grinding kinetics In this study 2017年3月20日 [1][2][3] It is generally agreed that the pellets would obtain superior quality when the specific surface area and mass fraction of − 0074 mm particle size of iron ore concentrates respectively Physicochemical Problems of Mineral Processing Investigation The shape of crushed ore affects the product particle size in a ball mill grinding circuit It has also been proposed that green pellet quality is directly related to the amount of fine particles in a pelletizing plant (Dwarapudi et al, 2008; Umadevi et al, 2008; Gul et al, 2014; Van der Meer, 2015) Particle size distributionInvestigation on the particle size and shape of iron ore pellet feed This means that the number of crushing stages can be reduced depending on the feed size accepted by primary grinding stage Image of a “Classical” 3stage ore crushing prior to rod mill [image: (13551)] Diagram of Typical 12 stage ore crushing prior to AGSAG mill [image: (13552)] Calculation of Reduction Ratio in CrushingAMIT 135: Lesson 5 Crushing – Mining Mill Operator Training
.jpg)
Rod Mills: Efficient Grinding Solutions for Mining
2016年6月1日 Mill discharge is generally less than 5% + 4 mesh in The rock will be carried up by the rods as they go through the CASCADE ZONE reducing the size of the rock As each particle of ore becomes smaller it will work towards the CORE ZONE how many rods there are in the mill V and the size of the incoming ore https://metsoRegarding the particle size distribution of industrial discharges from ball mills, Gharehgheshlagh et al [6] propose a perfect mixing model for the investigation of their level of precision and Comparison of measured and predicted PSD of mill dischargeDownload scientific diagram Particle size distributions of mill feed ( ) and discharge ( ) from publication: The physical basis of non random breakage in an ironoxide hosted copper gold ore Particle size distributions of mill feed ( ) and 2020年5月28日 The feed samples of X, Y, and Z iron ores were ground in the BBM (ball mill refers to a BBM of size 300 mm × 300 mm with smooth liners) to identify the PSD, BWI, and RT of each ore Grinding experiments were Investigation on Iron Ore Grinding based on Particle
.jpg)
Particle Size Reduction and Enlargement ScienceDirect
2019年1月1日 This effect is well illustrated by a series of experiments on the grinding of coal in a small mill, carried out by Heywood 1 The results are shown in Fig 51, in which the distribution of particle size in the product is shown as a function of the number of revolutions of the millBall mills are progressively used to grind the ores for particle size reduction and to liberate valuable minerals from the ores The grinding of ore is a highly energyintensive process [1–4] In this process, the size of the particle obtained depends on the energy consumption of the ball mill The major challenge encountered in theEstimation of Grinding Time for Desired Particle Size Distribution2020年1月3日 Ball mills are progressively used to grind the ores for particle size reduction and to liberate valuable minerals from the ores The grinding of ore is a highly energyintensive process [1,2,3,4] In this process, the size of the particle obtained depends on the energy consumption of the ball millEstimation of Grinding Time for Desired Particle Size Distribution Effect of ball and feed particle size distribution on the milling efficiency of a ball mill: An attainable region approach N Hlabangana a, G Danha b, *, E Muzenda b a Department of Chemical Engineering, National University of Science and Technology, P O Box AC 939, Ascot Bulawayo, Zimbabwe b Department of Chemical, Materials and Metallurgical Engineering, College of Effect of ball and feed particle size distribution on the milling
.jpg)
How to Control a SAG Grinding Mill Circuit 911Metallurgist
2017年8月5日 No longer can he grab a handful of mill discharge to estimate the size distribution and viscosity or cut a liter sample to determine the pulp density The operator is separated from the mill discharge by a sump or screen 5 or 6 meters across He is fortunate if he can even see what is coming out of the mill, let alone get a reasonable sample2016年3月21日 F = tonnage of ore to mill; 0 = tonnage of ore in overflow; S = tonnage of sand; M = tonnage of ore in mill discharge; and Ds, Do, and Dm are the liquidtosolid ratios of the sand, overflow, and classifier feed at the points where they leave or enter the mon Basic Formulas for Mineral Processing Calculations2012年6月1日 on mill dimensions, the type of the mill (overflow or grate discharge), the speed of rotation, the mill loading, the final product size required from a given feed sizeGrinding in Ball Mills: Modeling and Process ControlThe efficiency of the mill to break ore is a function of both the feed size distribution and the relative hardness of the ore When the feed size of a SAG mill becomes coarser, ie α r increases Correlation Between F80 and Mill Performance for a SAG Mill
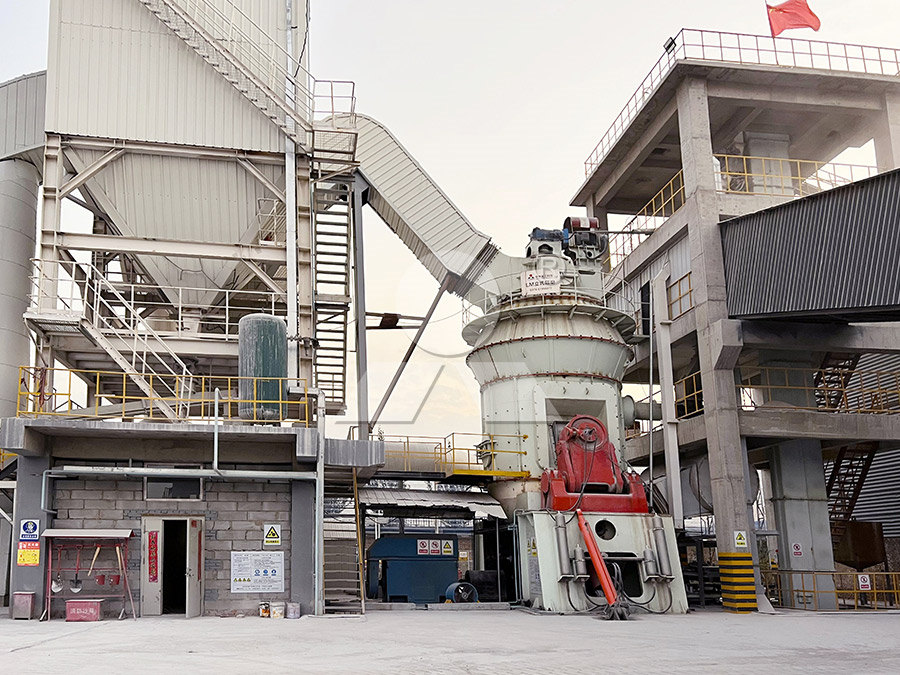
Population balance model approach to ball mill optimization in iron ore
3 BALL MILL MODEL The population balance model may be expressed by Equation (1): > @ ¦ i1 1 i b ij m j j i j i S Ht dt d H m t (1) where: S i (t) is the size discretized selection function for As stated, the mill feed size distribution data are summarised into three fractions: the fine fraction is interpreted as minus mill discharge grate size material, the medium fraction as critical size and the coarse fines, minimising the % medium while maintaining adequate % coarse is the objective of mill feed size optimisation ResultsThe Importance of Primary Crushing in Mill Feed Size OptimizationPREDICTING THE PRODUCT PARTICLE SIZE DISTRIBUTION FROM A VERTICAL STIRRED MILL by VTM mill processing copper ore 104 Figure 611 Schematic of the mobile mount system and sampler designed to collect the Vertimill discharge sample PREDICTING THE PRODUCT PARTICLE SIZE DISTRIBUTION FROM 2014年1月1日 The model previously implemented in Modsim™ has been successfully applied to represent the vertical mill operated with different ores The simulations produced particle size distributions that Population balance model approach to ball mill optimization in iron ore
.jpg)
HPGR effect on the particle size and shape of iron ore pellet feed
HPGR effect on the particle size and shape of iron ore pellet feed using response surface methodology Armin Abazarpoora, Mohammad Halalia, Rasool Hejazib and Majid Saghaeianb aMaterials Science 2021年1月22日 Gao et al [15,23] established the IsaMill particle sizeenergy equation that described the relationship between energy consumption and the characteristic particle size of grinding products Nevertheless, only a part of characteristic particle sizes (eg, D30, D40, D50) of the grinding products were employed in the sizeenergy equation, which limited the Impact of ball filling rate and stirrer tip speed on milling iron ore 2020年1月1日 The discharge end design of a ball mill plays an important role in discharging the desired particle sizes (−150 + 10 µm) and the percentage of recirculating load from the discharge end of the A comparative study on a newly designed ball mill and the 2017年2月13日 Center peripheral discharge Rod Mill for minimal slimes in final product CERAMIC LINED BALL MILL Ball Mills can be supplied with either ceramic or rubber linings for wet or dry grinding, for continuous or batch type operation, in sizes from 15″ x 21″ to 8′ x 12′Ball Mills 911Metallurgist
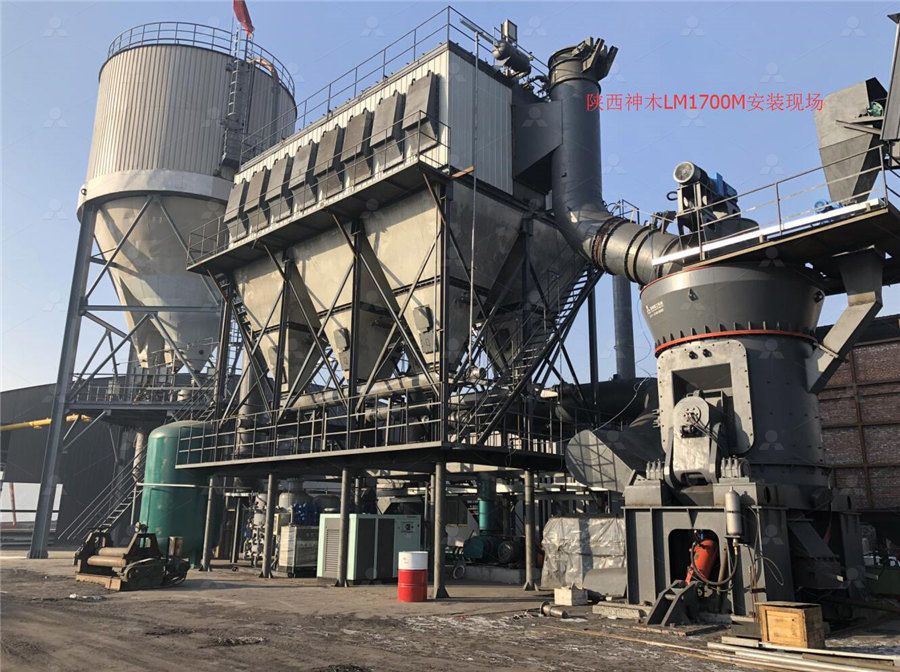
Rod Mill Grinding 911Metallurgist
2017年7月4日 The size discretized initial breakage rate functions were found to be inversely proportional to particle holdup and almost directly proportional to particle size A linearized grinding model that results from the firstorder Taylor’s series expansion of the breakage rate expression was found to give good simulations of the mill product size distributions without 2017年9月1日 There were no sampling points on the cyclone overflow nor ball mill discharge, so the particle shape characteristics of the ball mill discharge have to be inferred from the IsaMill feed The slurry density of the ball mill feed sample was low at 47%, and that of the IsaMill samples was 51%Fine grinding: How mill type affects particle shape characteristics 2023年9月22日 In this paper, we have highlighted some selected significant developments that have taken place during the last ten years or so in our understanding the size reduction of the particulate materials in ball mills using the traditional population balance model These developments relate to experimental technique and design of experiments, nature of grinding Selected Advances in Modelling of Size Reduction in Ball Millsmental data to validate the simulated particle size distribution None of this research has addressed the effect of feed particle size distribution on the prediction of the discharge particle size distribution using a DEMPBM modeling approach In this paper, a study of the effect of feed particle size distribution is presented Experimental workDEMPBM approach to predicting particle size distribution in
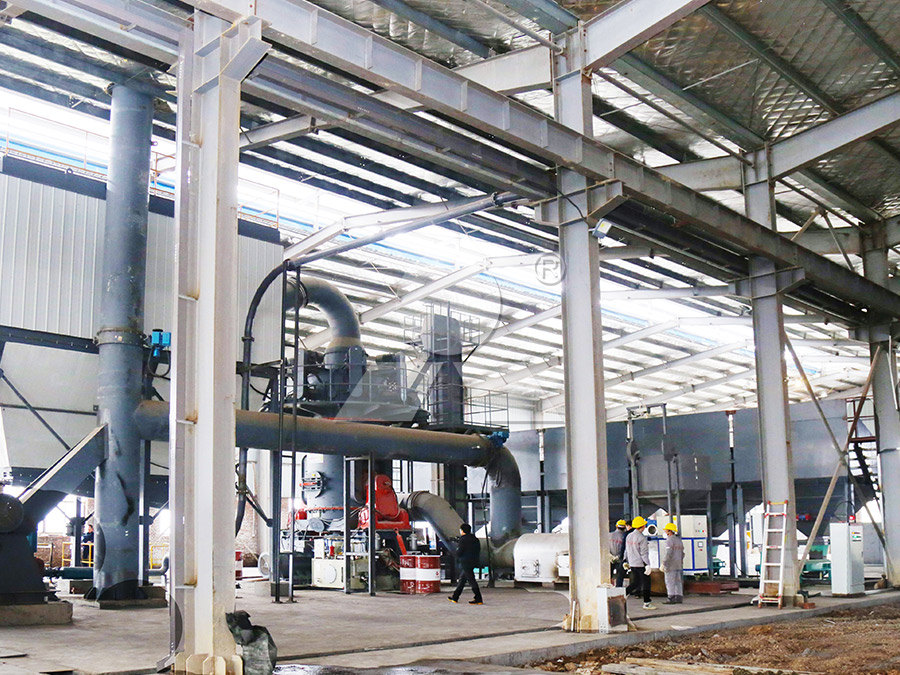
Rod Mill SpringerLink
2023年5月3日 Therefore, rod mill has the function of selective grinding, and its products are uniform in particle size and overgrinding is slight The rod mill is mainly used for gravity or magnetic separation of tungstentin ore and other rare metal ores In some cases, the rod mill can replace the shorthead cone crusher for fine crushing2015年3月10日 Characterization of chalcopyrite ore under high voltage pulse discharge: Particle size distribution, fractal dimension, specific energy consumption, grinding kinetics 2022, Minerals Engineering Citation Excerpt :Copper ore grinding in a mobile vertical roller mill pilot plant2021年2月8日 The discharge volume before clogging is a Poisson process for small orificetoparticle size ratio; The oneparticle discharge asymptote N d = 1 for size ratio d o /d The effect of particle shape on discharge and clogging2017年9月30日 The ore particle size distribution is an important basis for the evaluation of crushing effect The particle size parameters mainly include the particle area, perimeter, equivalent diameter, shape factor and so on In order to obtain the ore particle size distribution, we mainly study the following aspects: (1)Research of Ore Particle Size Detection Based on Image Processing
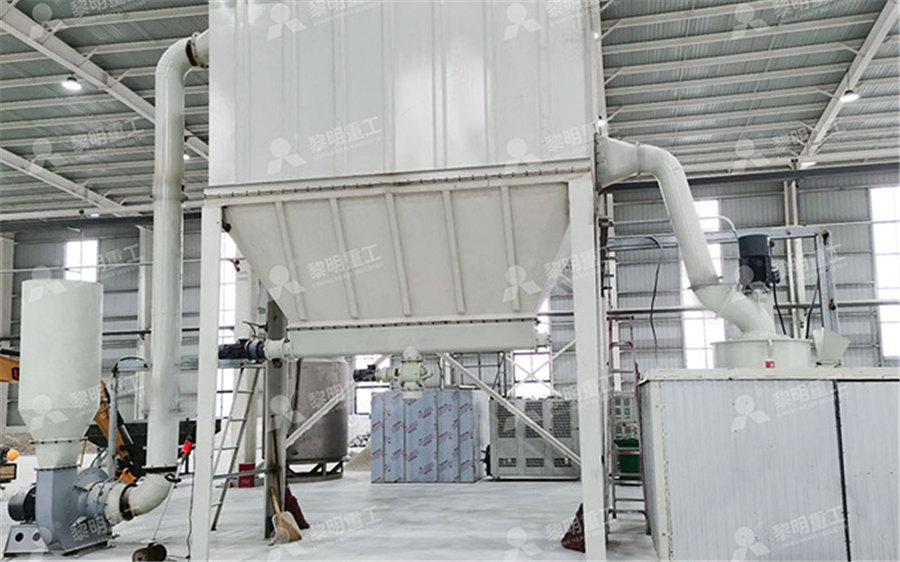
Fractal approach of particle size distribution description of ball
2023年3月16日 Feed size was divided into two fractions of (+238 −4) and (+2 −238) millimeters, from which different feeds with different weight and size percent values were fed to mill at three feeds of Particle Size Reduction and Enlargement JF RICHARDSON, JR BACKHURST, in Chemical Engineering (Fifth Edition), Volume 2, 2002 The rod mill In the rod mill, high carbon steel rods about 50 mm diameter and extending the whole length of the mill are used in place of ballsThis mill gives a very uniform fine product and power consumption is low, although it is not suitable Rod Mill an overview ScienceDirect TopicsNumerical modelling (such as Discrete Element Method and Smoothed Particle Hydrodynamics) of solids/fluid flow inside mills and trommels capable of predicting product size distribution, mill power,SIMULATION OF OVERFLOW BALL MILL DISCHARGE AND 2017年3月4日 Also, we propose a method for tracking the ore particle size distribution on the conveyor based on the UNet neural network that was trained on the dataset utilizing pseudolabels obtained with SIZE REDUCTION BY CRUSHING METHODS ResearchGate