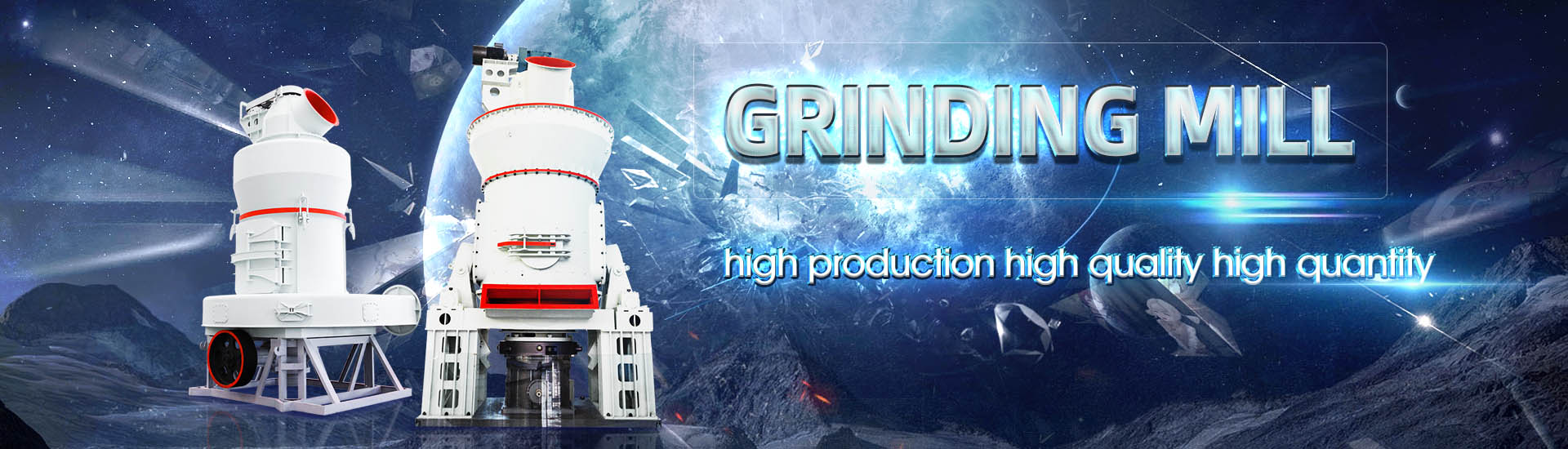
3.8x13m open flow cement mill output
.jpg)
Analysis of material flow and consumption in cement production
2016年1月20日 In the surveyed cement plant, three balances are established between input and output material in the raw mill, clinker production, and cement grinding system 248 t, 469 t, 2015年8月1日 The material efficiency values for a raw mill, pyroprocessing tower, rotary kiln, clink cooler, and cement mill are determined to be 3669%, (PDF) Analysis of material flow and consumption in In Figure 2, the simple flow chart including fundamental inputs and outputs of cement production is presented LCI studies about cement production include different inputs and outputsThe overall input and output of cement productionBall mill optimisation As grinding accounts for a sizeable share in a cement plant’s power consumption, optimisation of grinding equipment such as ball mills can provide significant cost BALL MILLS Ball mill optimisation Holzinger Consulting
.jpg)
The Cement Plant Operations Handbook International Cement
The Cement Plant Operations Handbook is a concise, practical guide to cement manufacturing and is the standard reference used by plant operations personnel worldwide Providing a After implementing the recommendations, an improvement in the performance of mill is observed The output of the mill has increased to 160 t/h with an specific power consumption of 3360 PROCESS DIAGNOSTIC STUDIES FOR CEMENT MILL 2022年5月9日 By initiating a CL for an industrial cement vertical roller mill (VRM), this study conducted a novel strategy to explore relationships between VRM monitored operational Modeling of energy consumption factors for an industrial cement 1987年8月1日 Cement manufacturing process is now operated with the aid of various control systems, such as raw meal composition control, kiln control and mill control Those systems Optimization of Cement Manufacturing Process ScienceDirect
.jpg)
Optimizing the control system of cement milling: Process
2014年3月1日 Based on a dynamical model of the grinding process in closed circuit mills, efficient efforts have been made to optimize PID controllers of cement milling The process 2020年3月1日 The scaleup effect on size reduction is confirmed with cement mill data • The material holdup equation assures the powder filling level as desired • Simultaneous use of A scaleup and design basis of continuous tube mills in cement 2022年1月10日 Alat cement mill dibantu oleh mill fan yang berfungsi untuk mengenerate air flow dalam mill air flow sistem sehingga proses penggilingan, pengurangan moisture, pemisahan, dan transport material Analisa Kinerja Alat Vertical Cement Mill di Pabrik II A 10 MW cement mill, output 270 tonnes per hour A cement mill (or finish mill in North American usage [1]) is the equipment used to grind the hard, nodular clinker from the cement kiln into the fine grey powder that is cementMost cement is currently ground in ball mills and also vertical roller mills which are more effective than ball millsCement mill Wikipedia
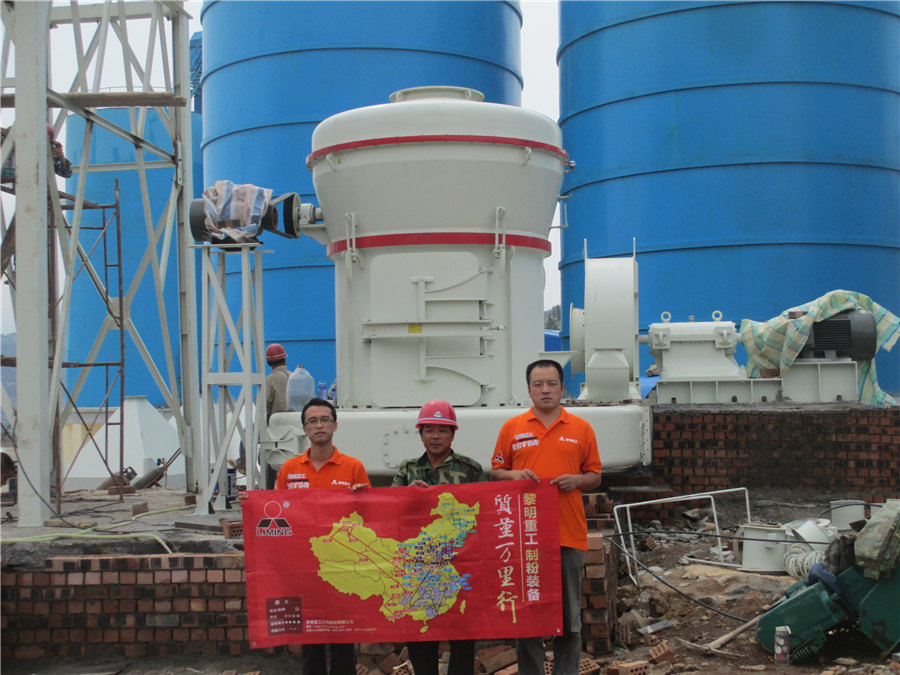
OpenCircuit Mill an overview ScienceDirect Topics
Figure 82 shows a flow sheet where the rod mill is in open circuit and the ball mill is in closed circuit with a classifier This is a normal setup as the primary function of a rod mill is to provide a uniform sized feed to the ball mill Figure 83 shows that the rod mill product is classified and a more uniform feed size is, therefore, discharged to the ball mill whose primary function is Guangdong Cement Project Luofu mountain cement group of guangdong 12 million ton output cement grinding station, Equipment List the HFCG180160 rolling machine (output 930 ~ 1 050 t/h, main motor power of 600 kW * 2) 1 + HFV4500X static classifier + DSM4500(Ⅱ) high fine dynamic classifier, Φ32 m *13m double storehouse ball mill (main motor power 1, 600 kW) of Cement plant projects of pregrinding equipment before ball millCement Separator Ball Mill Optimization Update May/2021 , – Low mill output or pool quality productHigh operation or maintenance costs 3 Keep operation in a good efficiency Air speed in mill – Open circuit : 08 to 12 m/sec – Closed circuit : Cement Separator Ball Mill OptimizationOf course, even if we set a more appropriate cement fineness, it is difficult to change the current situation that the flow velocity in the opencircuit ball mill is only 1/21/3 of that in the closedcircuit ball mill with the same specification, which will lead to poor comprehensive performance of finished cement, low system output and unsatisfactory enterprise benefitsBall Mill In Cement Plant Cement Ball Mill AGICO Cement
.jpg)
Everything you need to know about clinker/cement Grinding
Achieve nearer 89 kWh/t at the target mill output instead to go for a more fine ball Open circuit cement mill SLEGTEN The charge composition is also adapted to the Pfeiffer design makes the material flow out of 3 and 9 O’clock positions thereby not entraining the material in the airflow > increase in effective grinding length This flow sheet and sampling map shows the process flow for a cement plant Key components include: 1) Raw materials like iron sand, silica sand, limestone, clay and gypsum being fed into crushers and mills 2) Processed materials being fed into kiln systems for heating and clinkering 3) Clinker being stored and transported to other cement plants or customers 4) A coal mill and Flow Sheet Kiln, Raw Mill N Coal Mill PDF Cement ConcreteCement Mill Application fields: cement, silicate products, new building materials, refractory materials, glass ceramics and other production industries Processing capacity: 65135t/h Motor power: 2454200kw “40 years of senior mining machinery solutions”Cement MillCement Mill Price Hongxing Mining MachineryThe technological flow from cement fabrication • Extraction in open pits of raw materials such as limestone and clay (1 and 2) • Limestone separation and overcrushing (3), where the sizes The technological flow from cement fabrication • Extraction in open
.jpg)
Ball charge optimization INFINITY FOR CEMENT EQUIPMENT
Previous Post Next Post Contents1 Ball charge optimization2 1 How to use the BP21 2 Description of the main indicators used in this BP2101 The residue on 2mm/4mm before partition wall2102 Material filling level and ball charge expansion211 Cement mill specific power 1st compartment 212 Raw mill specific power 1st compartment Ball charge 2021年6月10日 In cement mills, ventilation is a critical key for maintaining temperature and material transportation However, relationships between operational variables and ventilation factors for an industrial cement ball mill Ventilation Prediction for an Industrial Cement Raw Consequently, he suggested ðEx that it is useful to employ the concept of an exergetic ‘‘improvement potential’’ when analyzing different processes 31 Description of cement process 311 Raw materials preparation Raw Energy and exergy analyses of a raw mill in a cement 2020年11月5日 We compare 3 cement milling and cement mill processes, including cement ball mill, vertical roller mill, and rod mill Simple flow, few production links; Fewer equipment required, less area occupied, the required output capacity, the process technology, your budgetary and financing status, the estimated starting time, 3 Necessary Cement Milling Comparison Ball Mill, Vertical Roller Mill
.jpg)
Simulation and Optimization of an Integrated Process Flow Sheet
2021年3月9日 In this study the process flow diagram for the cement production was simulated using Aspen HYSYS 88 software to achieve high energy optimization and optimum cement flow rate by varying the flow MECHANICAL ELEMENTS OF TUBE MILLS this is a part of ASEC Academy training Courses SUMMARY the mechanical elements of a tube mill could be separated into elements which have a direct function with the grinding process (ie grinding media, liners, diaphragms) and into elements which can be considered as individual units which are connected to each other to a MECHANICAL ELEMENTS INFINITY FOR CEMENT EQUIPMENTball mill open and closed circuits [12] with the installation in all cases the dynamic separator When transferring to closedcircuit а mill size 26×13 m at a constant quality cement (3000 cm2pg) capacity grinding unit was increased from 25 to 38 tph while reducing the specific consumption of electricity from 416 to 293 kWhpt The parameterAnalysis of the efficiency of the grinding process in closed circuit 2021年6月10日 Ventilation Prediction for an Industrial Cement Raw Ball Mill by BNN—A “Conscious Lab” ApproachVentilation Prediction for an Industrial Cement Raw Ball Mill by
.jpg)
Energy and exergy analyses for a cement ball mill of a new
2020年5月1日 Cement industry consumes a huge amount of electrical energy that is about 100 kWh/t (kWh per ton (10 3 kg) of cement) [16]In a cement plant, about twothirds of the total electrical energy is used for particle size reduction of raw materials and clinker [17]There is a diverse range of options to decrease the production expenses as well as CO 2 emissions that 2018年3月1日 The samples were taken from an output chute of a 4 х 135 m opencycle cement grinding mill, at equal intervals during 2 days The grinding intensifier was supplied to a clinker(PDF) Flowability of cement powder ResearchGateThe mill as described would draw power P = 23 D 35 kW where D is the diameter inside the lining in metres, so a 2 m mill would draw 26 kW at the shaft and might grind 23 t/hr on coarse grinding dutyCement Kilns: Size Reduction and GrindingDownload scientific diagram Stages in cement production flow chart [43] from publication: A review on kiln system modeling The purpose of this study is to evaluate performance cement of Stages in cement production flow chart [43] ResearchGate
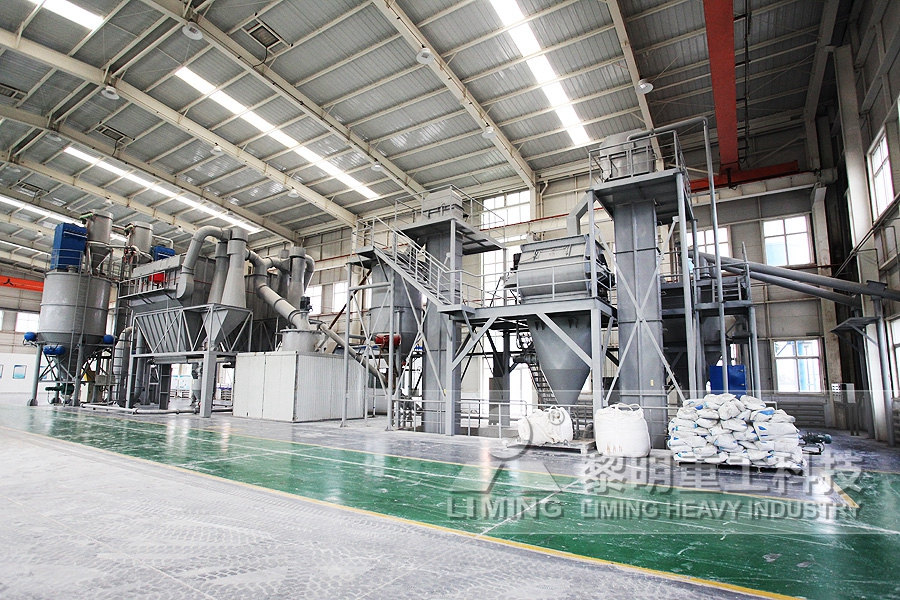
Analysis of material flow and consumption in cement production
2016年1月20日 In the surveyed cement plant, three balances are established between input and output material in the raw mill, clinker production, and cement grinding system 248 t, 469 t, and 341 t of materials are required to produce a ton of the product in raw material preparation, clinker production, and cement grinding stages; waste gases account for the largest proportion of the Keywords: Vertical roller mill, cement grinding, performance evaluation INTRODUCTION Cement production is highly energy consuming process with energy utilization of around 110150 kWh/t (Villa, 2005)Performance Evaluation of Vertical Roller Mill in Cement Grinding: TABLE 3 This type of mill is designed typically for a gas flow up to 25 kg of air per kg of coal, at maximum output Higher figures (up to 35 kg/kg) can occur in direct/semi indirect firing particularly if the mill is run at lower capacityCOAL PREPARATION AND FIRING INFINITY FOR CEMENT EQUIPMENT2020年2月1日 Rather than huge expansion, most industries will focus on maximizing resources for maximum pro tability Consequently, a study of the impact of operational parameters on ball mill energy e ciency Energy and exergy analyses for a cement ball mill of a new
.jpg)
MODELING AND SIMULATION OF A CLOSED LOOP BALL MILL
1SKISHORE SUBRAMANIAM, 2VENKATAESHS, 3RAMKUMAR KANNAN, 4JAYALALITHAS, 5GURU PRASAT 1,2,3,4Sastra University,Thanjavur, 5FLSmidth PvtLtd Abstract The concept of modeling and simulation in a ball mill grinding process have grown exponentially in recent past owing to the competition in the cement industry2013年2月1日 Stirred media mill is one of the most energyefficient types of grinding equipment for wet ultrafine grinding Nevertheless, in a dry mode several problems arise, such as aggregation Mechanical activation of cement in stirred media mill2014年3月1日 For each cement type a PID set is selected and put in o peration in a closed circuit cement mill recycle elevator power and the mill feed flow rate u controller output (36)1 Optimizing the control system of cement milling: Process 2018年9月10日 The exergy and m ass flow diagram of the local raw mill is presented in F igure 3 and shows that m ost of the exergy input to the sy stem was due to hot gas and dust (966% ) followed by the (PDF) Thermodynamic Analysis of Raw Mill in Cement
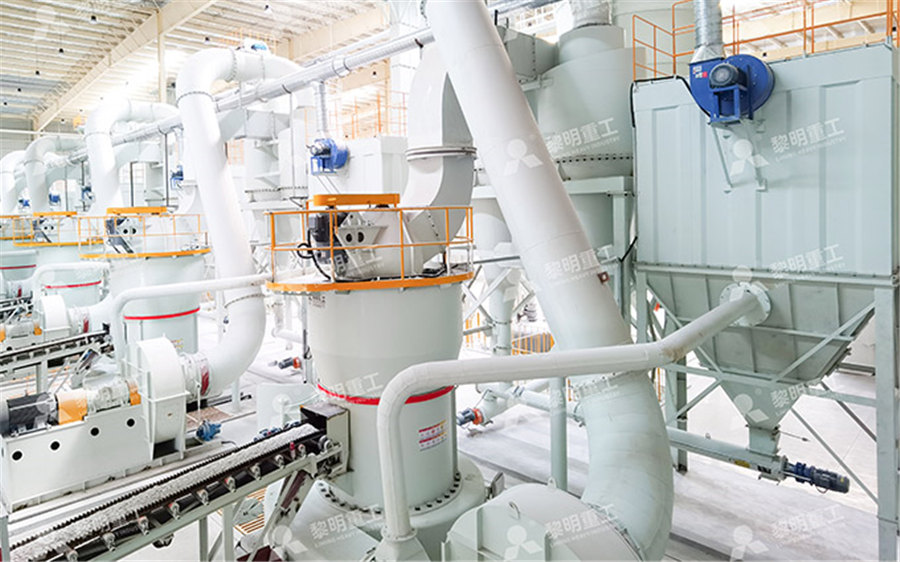
Cement Mill HXJQ
Cement Mill is the key equipment for second grinding after cement clinker are precrushed by the system The mill output improves 15–20% than general mill In addition, Open flow: Brim: ZD60: 45: 245: 658: 438: Φ22×75: Open flow: Brim: ZD70: 5: 380: 810: 648: Φ22×11: Open flow: Brim: D110:2017年10月20日 1 Introduction Nowadays, cement manufacturing is an energyintensive industry The energy costs of cement industry are about 40% of the product cost that indicates that this sector is one of the biggest CO 2 Heat Integration in a Cement Production IntechOpen2006年12月1日 Utlu et al, [3] study on the raw mill subsystem reported that the energy efficiency of the cement was 843% but without consideration of the precalcining rotary kilnEnergy and exergy analyses of a raw mill in a cement productionAdditional tools required It will increase the plant off time Increasing Man hours and manpower Liner replacement, bolt tightening will be complicated 31 Inlet Chute Design Considerations The following parameters are considered while designing the mill inlet chute for powdery materials UMS ø46m Cement mill It is the mostly sold mill in FLS DESIGN AND ANALYSIS OF BALL MILL INLET CHUTE FOR ROLLER PRESS CIRCUIT
.jpg)
Cement mill, Cement grinding mill All industrial manufacturers
Output: 50 kg/h The fast mill for all tasks With a freely adjustable rotor speed of 2,000 – 4,000 rpm, The GRMK vertical cement mill of CHAENG adopts a new generation of cement grinding technology, which integrates grinding, drying and powder selecting functionsHigh production efficiency and large output; High fine and high yield cement mill is mostly used in the opencircuit grinding system, with many features such as systemic equipment, Open flow: Brim: ZD60: 45: 245: 658: 438: Φ22×75: Open flow: Brim: ZD70: 5: 380: 810: 648: Φ22×11: Open flow: Brim: D110:Cement Mill FTM Mining Machine(3) Schematic view of cement mill is shown in Fig2 U is the feed flow rate in Tons/hr Yr is the recirculating flow of fine particles in Tons/hr and Yf is the fine product flow in Tons/hr Z is the ball mill load in Tons Hardness of material inside the mill is denoted as d Clinker, gypsum and slag together form the input to the ball mill Development of Fuzzy Logic Controller for Cement Mill2016年10月5日 In this chapter an introduction of widely applied energyefficient grinding technologies in cement grinding and description of the operating principles of the related equipments and comparisons over each other in terms of grinding efficiency, specific energy consumption, production capacity and cement quality are given A case study performed on a EnergyEfficient Technologies in Cement Grinding IntechOpen
.jpg)
Cement Manufacturing Process INFINITY FOR CEMENT EQUIPMENT
Raw mill, Coal Mill and Cement mill drying; Heating and power generation; Speed of Clinker Cooling Rapid cooling prevents growth of crystals and its size; gives suitable clinker nodule; solidify the clinker in to glass state; Improve C 3 S and reduce C 2 S leads to Easy grindability; Lower energy consumption; Improve hydration and cement 2019年3月8日 253 Optimizing the Operation of a Cement Mill Cement Production Process Flow Schematic and Typical Energy E ciency Measures • Net power output of the waste heat recovery systemIMPROVING THERMAL AND ELECTRIC ENERGY EFFICIENCY AT CEMENT