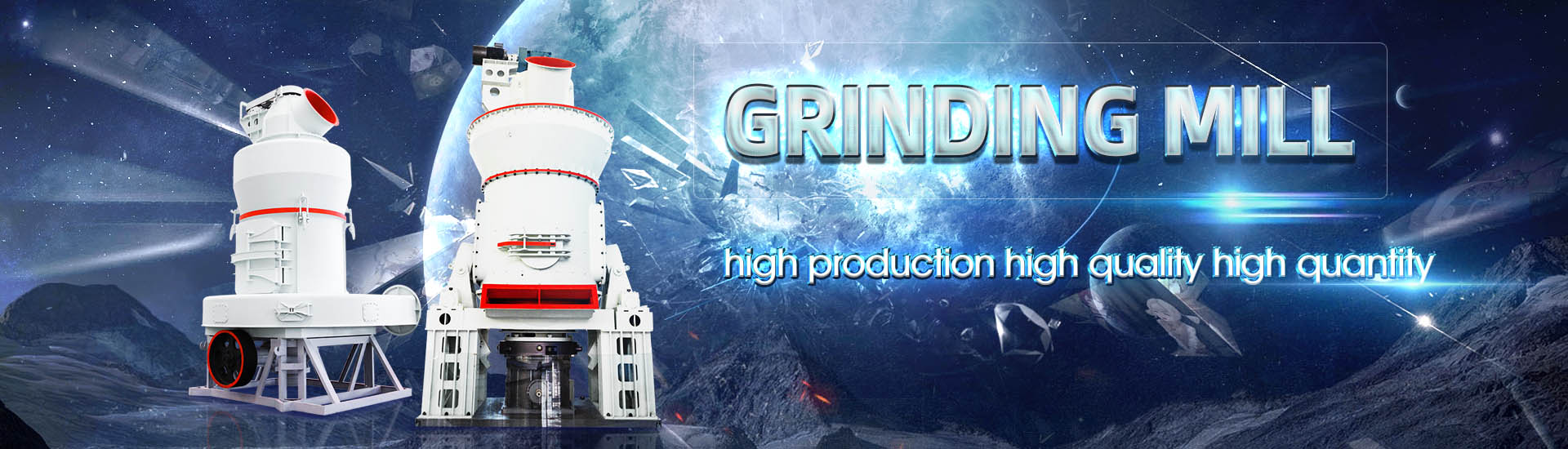
Coal mill site cleaning

Management of coal stockpiles ICSC
Stockpiling is carried out at coal mines, coal preparation plants, transhipment facilities (including export/import facilities) and end user sites such as power plants, coking plants and cement works With mounting pressure to minimise the amount of capital tied up in stockpiles with no return Coal cleaning is the process of removing impurities such as pyritic sulfur, ash, and mercury from coal before its use It involves various techniques like physical cleaning to reduce the Coal Cleaning an overview ScienceDirect TopicsCoal preparation activities (eg, use of dryers), coal gasification , feeding and ash removal) and coal liquefaction processes may generate pointsource emissions of dust and heavy oils (tars) Environmental, Health and Safety Guidelines for Coal ProcessingCoal cleaning is a process by which impurities such as sulfur, ash, and rock are removed from coal to upgrade its value Coal cleaning processes are categorized as either physical cleaning 1110 Coal Cleaning US Environmental Protection Agency
.jpg)
CHAPTER 3 Coal Preparation and Cleaning
coal cleaning is highly site specific But the general procedure involves size reduction to control top size and to free or unlock occluded mineral matter followed by separation of relatively pure Coal preparation, which may also be called washing, cleaning or processing, is the methodology by which coal feedstocks are upgraded in order to reduce freight costs, improve utilization Coal Preparation SpringerLink2006年4月1日 A coal preparation plant typically operates with multiple cleaning circuits to clean individual size fractions of runofmine coal Coal preparation plants are traditionally optimized using the(PDF) Coal preparation plant optimization: A critical 2021年5月1日 Ultrafine grinding and decanter centrifugation to recover clean coal from rejects Centrifugation of coalwaterslurry (50% pulp density) produces 19% ash clean coal Extra Sustainability of coal mines: Separation of clean coal from the fine
.jpg)
Coal wastes: handling, pollution, impacts, and utilization
2023年1月1日 The coal mining industry creates hundreds of millions of tons of rock, waste coal, and cleaning waste streams comprising coal bed methane (CBM), coal sludge, fine coal, coal 2020年10月26日 Handling and disposal of high volume of fine coal tailings is a biggest challenge for coal washeries Separation of clean coal by density separation and flotation shows limited Effective Utilization of Coal Processing Waste: Separation of Low amount of pulverised fuel inside a hot mill The large surface area of the pulverised coal and the high temperature inside the mill lead to rapid oxidation of the coal This results in further heat buildup and the potential for a fire If the mill is restarted without first COAL HANDLING SAFETY Land Instruments InternationalROTARY COAL DRY CLEANING c Coal crusher MJT 30 sistem hammer mill Batu bara dari hopper ukuran 50 mm dihancurkan menjadi maksimal 10 mm, apabila bucket lifter sudah penuh, coal crusher tetap berjalan, Hanya belt conveyor feeder yang berhenti d Bucket lifterROTARY COAL DRY CLEANING MEKAR JAYA TECHNIC
.jpg)
Mill Inerting and Pulverizer/Mill Explosion Mitigation
“inert” environment inside a coal mill, the O 2 level should fall below 14% O 2 – Technically speaking, only Steam, CO 2 and N 2 (Rare) systems are true inerting systems – Steam is the most common inerting media To know with confidence that an inerting environment is Coal dust explosions are among the severe hazards in industries using coal, posing significant risks to personnel and infrastructure These explosions occur when fine coal particles become airborne and come into contact with a heat source in an enclosed environment, leading to a rapid combustion event Given the catastrophic potential of such incidents, robust measures for coal Coal Dust Explosion Protection: Ensuring Safety in industries using 3 Precise Control and Automation: Bellian Machinery's coal mills feature advanced control systems that enable precise control over various operational parameters Operators can adjust grinding variables, such as coal flow and mill rotation speed, in realtime to achieve the desired coal fineness and optimize mill performanceCoal Mill in Thermal Power Plant: Enhancing Efficiency and Vertical Coal Mill Housing design, functions, and work systematics of the Vertical Coal Mill supported by a site survey first S ta rt composition test kit by first cleaning the tested surface using a brushing machine until the surface is shiny Metallographic testing is WEAR ANALYSIS OF VERTICAL COAL MILL PLATE APS
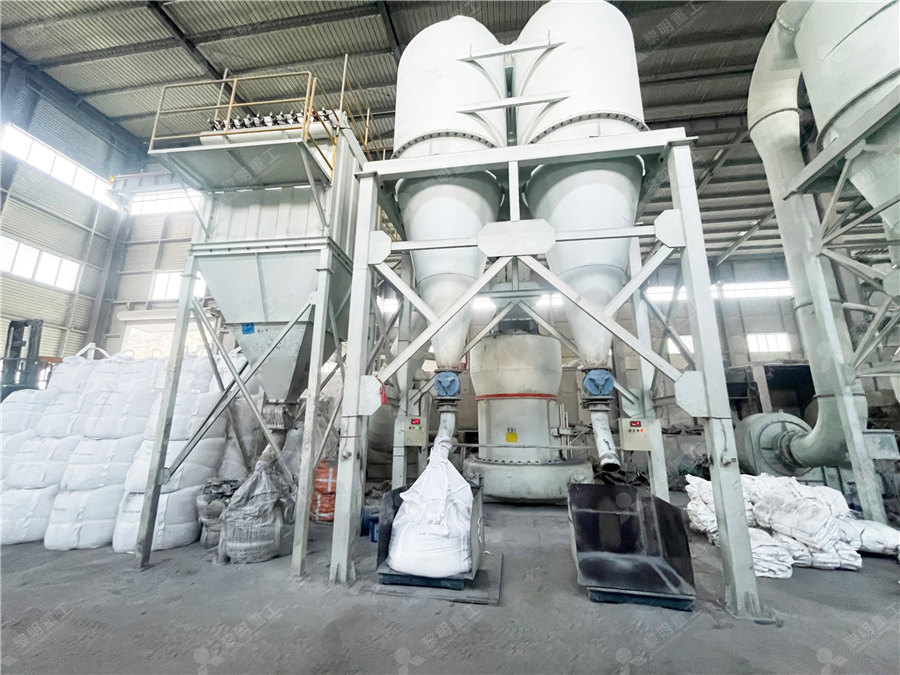
Coal Mill Modeling by Machine Learning Based on onSite
2002年8月31日 This paper presents a novel coal mill modeling technique using genetic algorithms (GA) based on routine operation data measured onsite at a National Power (NP) power station, in England, UK The work focuses on the modeling of an Etype vertical spindle coal mill The model performances for two different mills are evaluated, covering a whole 2018年7月21日 Advanced coal cleaning technologies being developed under the ARCI/CT component rely on extensive liberation of pyrite and ashproducing minerals by comminuting raw feed coal to fine, ie, finer than 600 micrometers (28 mesh) and ultraflne, ie, finer than 45 micrometers (325 mesh) particle sizesCoal Cleaning Technology 911MetallurgistMINISTRY OF COAL 101 SAFETy IN COAL MINES Coal mining poses several inherent, operational and occupational hazards and associated risks to the work persons Mill Te Per 3 Lac Manshifts 197579 157 196 1224 1278 218 044 1424 289 198084 122 143 1018 1065 129 030 975 226SAFETY IN COAL MINES52 Coal handling 27 53 Coal cleaning 28 54 Combustion 29 55 Coking 31 56 Comments 34 6 Spontaneous combustion 35 61 Factors affecting spontaneous combustion nonconformance At most, if not all, sites, coal is analysed at some stage, either on its way to or from the stockpile or even from within the pile itself It is therefore Management of coal stockpiles ICSC
.jpg)
CoalMill Millfire CO Analyser Codel International PDF
The CODEL system samples the gas content of the mill outlet through a steel sintered filter mounted in the wall of the mill outlet duct infrared gas analyser with stainless steel measurement chamber low maintenance operation high dust loading operation automatic zero calibration remote data display unit; data in ppm Coal Mill CO Gas Analysing System Product Data Coal Mill: The heart of the system, where raw coal is pulverized into a fine powder Various types of mills, such as ball mills, Maintenance schedules should include inspections, cleaning, and replacement of worn components Safety Protocols: Comprehensive safety protocols must be established and followed to prevent accidentsIndirect Firing Coal Grinding Systems: Enhancing Efficiency and Up to 5 acres of public land may be claimed for the purpose of processing minerals Mill sites are limited to lands that do not contain valuable minerals Mineral public lands which are to be used as a mill site for the reduction of ore or in the development of a lode claimMill Site Coal Mining Terms Dictionary The Coal Fields™This manual and data base has been funded by the Coal Services Health and Safety Trust The project is designed to assist in developing a more cohesive and sophisticated understanding of risk management and risk communications within the coal mining industryRisk Management Manual Coal Services
.jpg)
Leaching of trace elements from Pittsburgh coal mill rejects
2017年2月15日 We investigated the leachability of elements from mill rejects from the highsulfur, bituminous Upper Pennsylvanian Pittsburgh coal, using the synthetic groundwater leaching procedure (SGLP), longterm leaching (LTL), and the US Environmental Protection Agency's (EPA's) toxicity characteristic leaching procedure (TCLP), and compared their leaching Some coalfired power plants generate rejects when they mill fuel coal, particularly for burning in PC boilers Depending on the type of coal and the type of mill, the quantity of mill rejects generated varies Because of relatively small amounts of mill rejects, they are often comanaged with fly ash and bottom ashGuidance for Comanagement of Mill Rejects at CoalFired Power and Evaluation for Coal Cleaning Jack Groppo 1 and Rick Honaker 2 1 University of Kentucky, Center for Applied Energy Research, Ghent Station and Mill Creek are candidate sites for ash beneficiation to produce pozzolan or filler from fly ash using Economical Recovery of Fly AshDerived Magnetics and Evaluation Coal Injection) 1990 Central coal grinding plant (LM 263 D) for gas and steam power station (coal gasification) 1992 Central coal grinding plant (LM 263 D) for the production of lignite (brown) coal dust 2002 Coal grinding plant (LM 232 D) for grinding wood pellets for power stations 2005 First 4roller pressure mill (LM 434 D) becomesLOESCHEMILLS
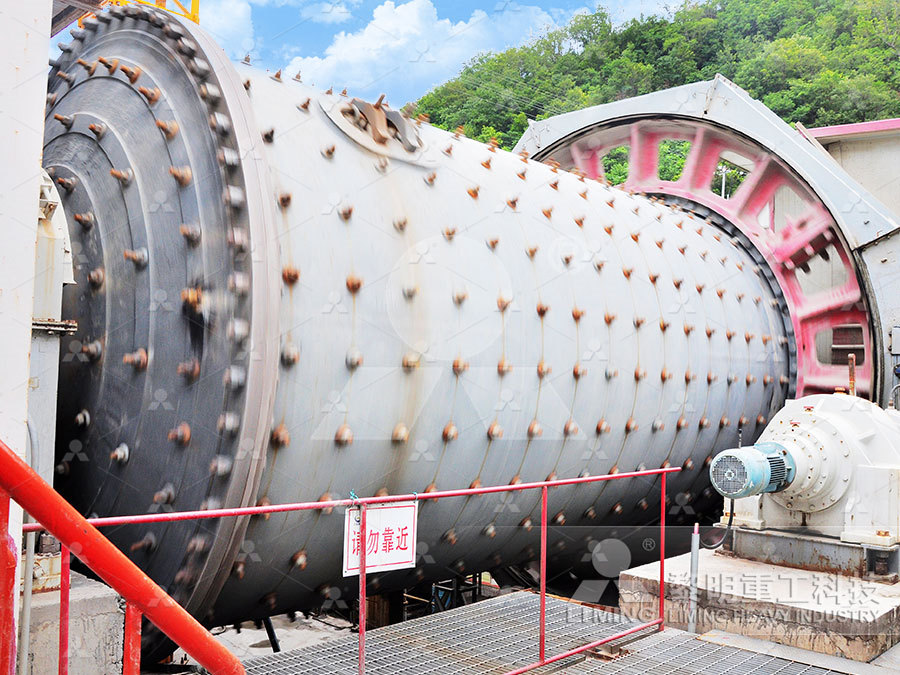
CHAPTER 3 Coal Preparation and Cleaning
matter At present, coal cleaning is accomplished through physical separation of particles low in mineral content from particles high in mineral content In the future it may include chemical and biological treatment for removal of certain impurities from coal In this chapter, the present state of the art of coal cleaningA coal preparation plant typically operates with multiple cleaning circuits based on the particle size distribution of runofmine coal Clean coal product from a plant commonly has to satisfy Flowsheet of a modern coal preparation plant incorporating four Coal grinding is a critical process in various industries, particularly in power generation and cement production However, the process involves significant safety risks due to the combustible nature of coal dust and the mechanical hazards posed by the operation of the mill Ensuring safety during coal grinding is essential to prevent accidents, exAspects of Coal Mill Safety Coal Mill Safety, Explosion and Fire 2020年1月1日 Coal mills have a significant influence on the reliability, efficiency, and safe operation of a coalfired power plant Coal blockage is one of the main reasons for coal mill malfunctionEarly Warning of Critical Blockage in Coal Mills
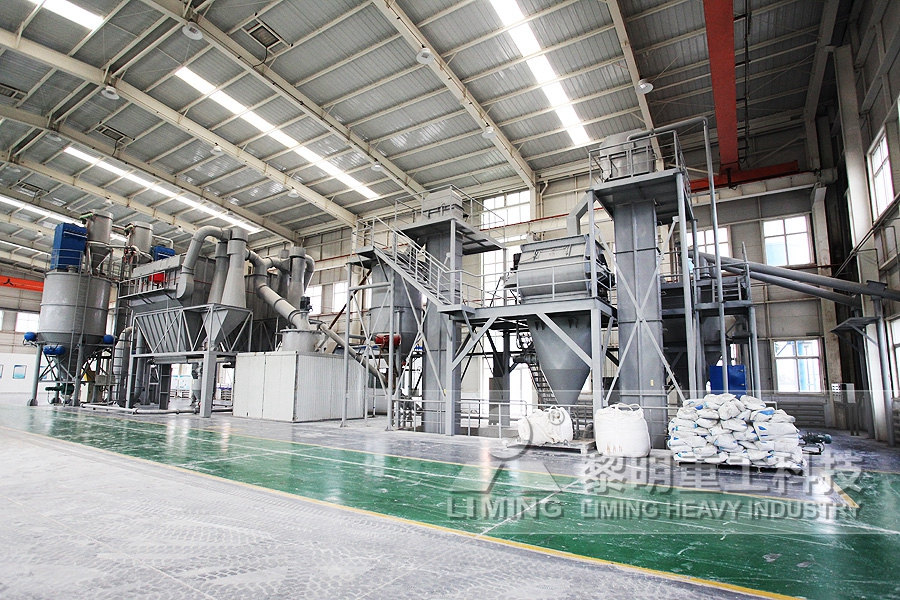
Boiler Mill and Coal Pulverizer Performance GE Steam
Can GE service my boiler mills? YES Our boiler mills and coal pulverizers span the globe and are built in a variety of sizes and capacitiesWe provide customized maintenance solutions, and offer a full spectrum of highquality solutions for • In case of AFR processing in the coal mill (cogrinding), the impact on VOC emissions must be assessed based on the material characteristics If an increase of VOC emissions is expected, a spot measurement should be conducted at the coal Cement Environmental Directive HolcimAbstract: Fine coal cleaning involves the use of densitybased separators and circuits that utilize the unique characteristics of each unit to achieve the optimum performance For particles smaller than 015 mm, froth flotation is the most effective technology, although densitybased separators have shown the potential to be an adequate substitute for difficulttofloat coalsCleaning of fine and ultrafine coal Semantic Scholar1997年7月1日 As an alternative to wet coal cleaning at the mine mouth, a practical and economically sound dry coal cleaning technology called the MagMill has has been focused on sampling a variety of pulverizers Three (3) different types of pulverizers (ball, roller, and bowl mill) which are commonly used by the utility industry have been Dry coal cleaning in a MagMill (Conference) OSTIGOV
.jpg)
SOP Startup Shutdown and Operation of Coal Mill
This document provides the standard operating procedure for starting up, operating, and shutting down Coal Mill 1 2 It outlines the specific sequence that equipment should be started and stopped in to avoid material accumulation and jamming It also provides instructions for maintaining appropriate operating temperatures and residue levels within quality standards Coal is currently beneficiated predominantly in wet condition The conventional methods for processing of coarse coal like heavy media bath, jigging etc utilizes water In the near future, coal resource and water resource is going to have a reverse distribution thus posing several hurdles to wet beneficiation technologies in coal cleaningCoal Feed Systems For Boiler and Coal Milling Plant Gravimetric Coal Mill PPT Free download as Powerpoint Presentation (ppt / pptx), PDF File (pdf), Text File (txt) or view presentation slides online The document provides an overview of coal mill operation, protections, and interlocks It discusses coal combustion theory, coal properties, coal mill components and operation, and troubleshooting The coal mill grinds coal into fine particles for Coal Mill PDF Combustion Chemistry2022年11月1日 Vertical Coal Mill (VCM) is equipment for grinding and pulverizing coal into micron size to 10% to improve cleaning and deoxidation for welding on contaminated surf acesWEAR ANALYSIS OF VERTICAL COAL MILL PLATE ResearchGate
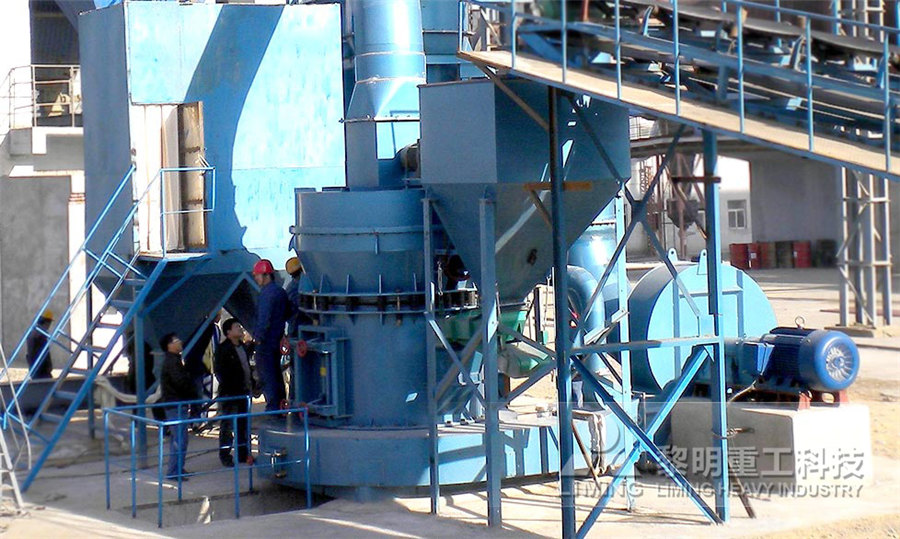
Standard Practice for Preparing Coal Samples for Analysis
circulation and thus the potential for drying the coal 611 Pulverizer or Mill—For final reduction of laboratory sample to the 250µm (No 60) sieve size, the following equipment may be used: 612 Hammer Mill—Completely enclosed to avoid loss of dust or moistureMill Training Manual Alstom Free download as PDF File (pdf), Text File (txt) or read online for freeMill Training Manual Alstom PDF Coal Mill 2023年2月1日 The ratio between combustible organic matter and inorganic impurities of coal is also one of the variables in coal classification Coal gangue is a significant residue of coal mining and cleaning, which accounts for approximately 10–15% of raw coal [3]The first group of impurities in coal, which are also the most commonly encountered, are quartz (SiO 2) and clay Conventional and recent advances in gravity separation This mill can work in underpressure (it is standard) or overpressure VERTICAL ROLLER MILL KTM TIME PRESSURE Grinding of coal and other explosive materials requires observing of safety rules of operation: Materials can explode under the following conditions: 1 Concentration of dispersed coal dust in the atmosphere, 2 Over limit content of O 2GRINDING AND SEPARATING TECHNOLOGY SYSTEMS

Detection of Malfunctions and Abnormal Working Conditions of a Coal Mill
2018年5月2日 Coal mill malfunctions are some of the most common causes of failing to keep the power plant crucial operating parameters or even unplanned power plant shutdowns Therefore, an algorithm has been developed that enable online detection of abnormal conditions and malfunctions of an operating mill Based on calculated diagnostic signals and defined DuBois origins in the paper industry occurred more than 60 years ago in the field of paper machine cleaning We continue to develop new technologies every year to remain a lead supplier of paper machine cleaning technology DuBois has a comprehensive line of paper machine system cleaners and paper mill surface cleanersPaper Mill Cleaning Paper PulpAcronyms and abbreviations 2 Contents Ash management in coalfired power plants ICSC2024年3月16日 A vertical coal mill is a type of industrial milling equipment used to crush and grind coal into powder for use in thermal power plants and the cement industry, Routine cleaning of the mill interior, housing, and surrounding areas ensures a How Does a Vertical Coal Mill Work
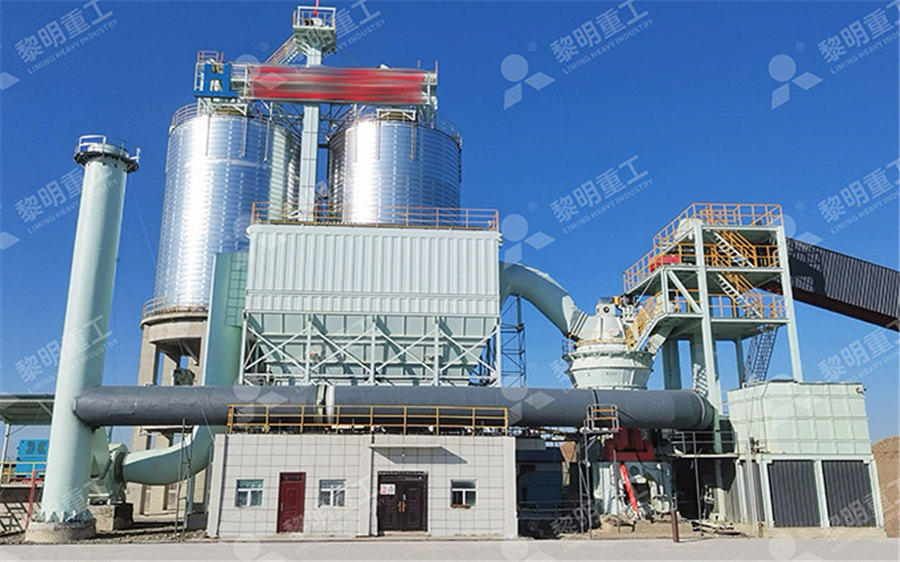
Dry coal cleaning with a MagMill Request PDF ResearchGate
2001年11月1日 Request PDF Dry coal cleaning with a MagMill This paper presents the preliminary test results obtained using a 038kg/s (3,000lb/hr) beta prototype MagMill In processing Upper Freeport Mechanism of Coal Dust Explosions A coal dust explosion occurs when fine coal particles become airborne and come into contact with an ignition source in an enclosed or confined space The explosion hazard is magnified by the following factors: Dispersion: Coal dust must be dispersed into the air to create a dust cloudCoal Dust Explosion Hazards: Understanding the Risks and