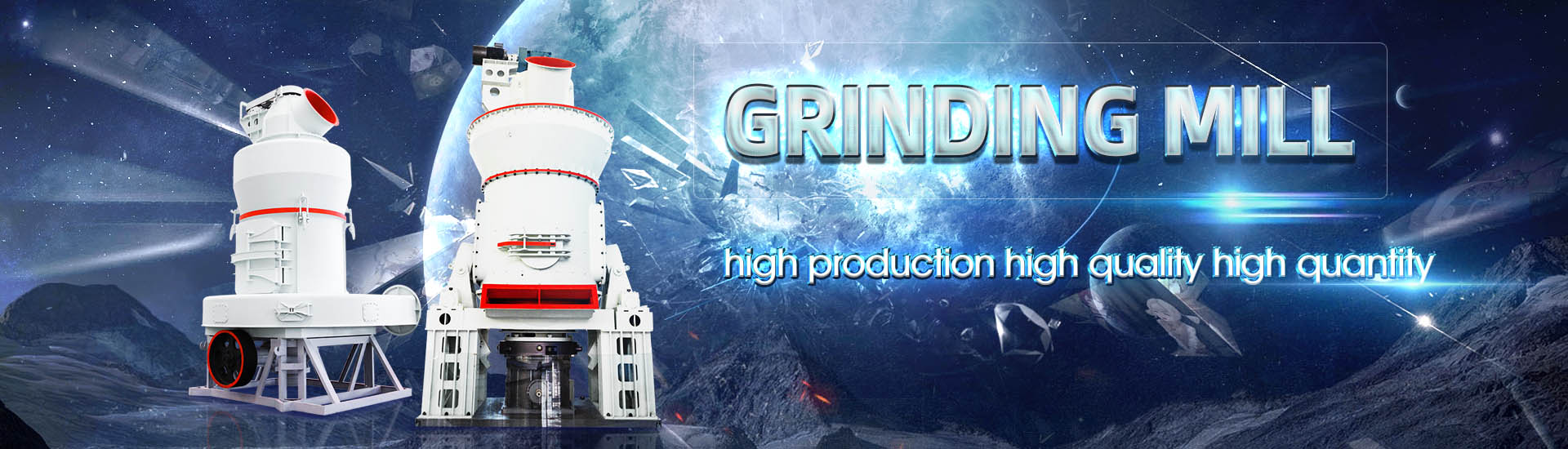
Looking to buy highefficiency and energysaving grinding mill
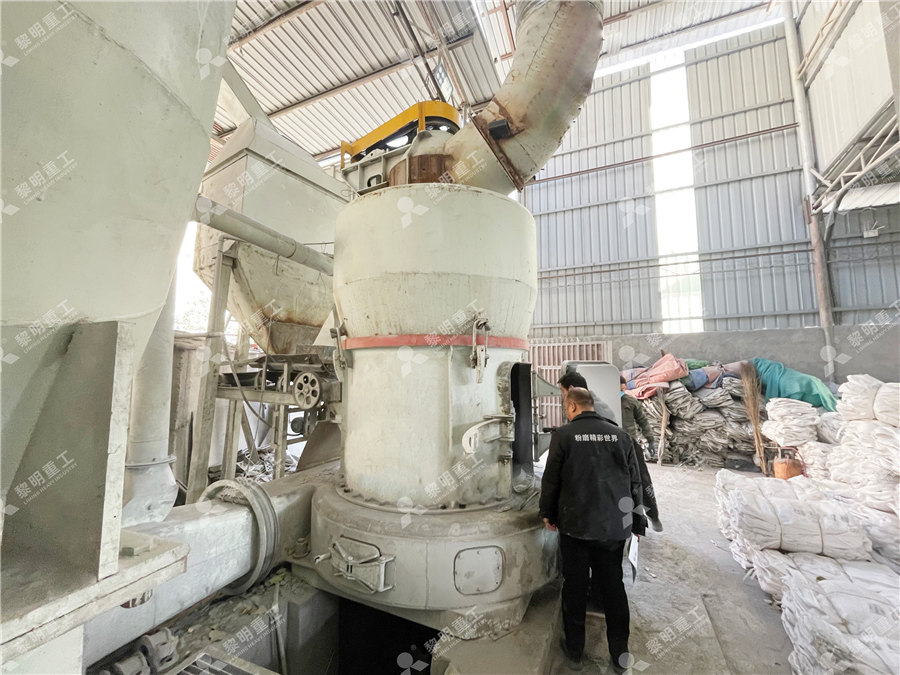
HIGmill high intensity grinding mill Metso
The Metso HIGmill™ is an advanced, energyefficient fine and ultrafine grinding solution that utilizes proven technology With the tall, narrow, vertical body arrangement, grinding media is evenly distributed and mineral particles remain Vertimill® is an energy efficient grinding machine They tend to grind more efficiently than, for example, ball mills with feeds as coarse as 6 mm to products finer than 20 microns This provides up to a 40% higher energy efficiency Vertimill® MetsoAre you looking to increase production, reduce risks, lower operating costs and enhance environmental performance? With over a century of experience, Metso designs and Grinding MetsoThe Emax is an entirely new ball mill designed for high energy grinding The maximum speed of 2000 rpm, so far unrivaled in a ball mill, and the innovative jar design produce highly effective THE REVOLUTION IN ULTRAFINE GRINDING RETSCH
.jpg)
BALL MILLS Ball mill optimisation Holzinger Consulting
As grinding accounts for a sizeable share in a cement plant’s power consumption, optimisation of grinding equipment such as ball mills can provide significant cost and CO 22018年1月1日 However, highperformance dry machining processes (especially of lowstrength materials) offer about 104 times higher energy efficiency than grinding processes with small Energy efficiency of stateoftheart grinding processes2016年10月5日 Energyefficient equipments such as highpressure grinding rolls, vertical roller mills, CKP pregrinders, Cemex ® mills and Horomills ® are used at both finish grinding of cement and raw materialgrinding stages due to EnergyEfficient Technologies in Cement Grinding2023年7月10日 The review concludes that stirred mills have significant potential for achieving the energyefficient ultrafine grinding of particles Stirred mills have unique designs and operations, which provide higher grinding efficiency, lower EnergyEfficient Advanced Ultrafine Grinding of
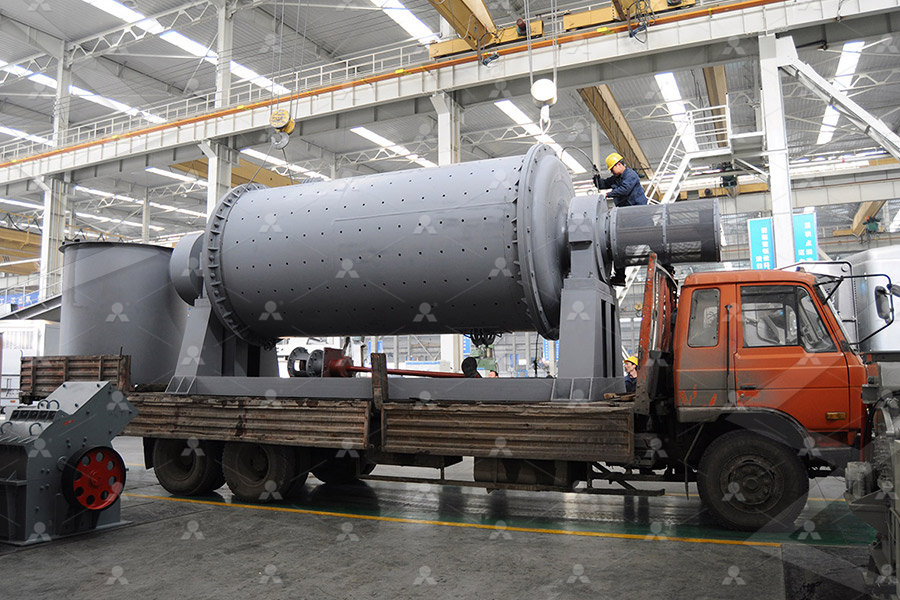
Cement Mill Optimization: Practical Strategies for
Adjusting mill parameters: Finetuning mill parameters such as mill speed, ball charge, filling ratio, and grinding media size can have a substantial impact on the grinding efficiency of the mill For example, a 10% increase in mill speed can 2022年1月1日 A pilotscale grinding technology of ceramic medium stirred mill was proposed in this study Based on the specific productivity and grinding efficiency, the appropriate grinding parameters were ascertained as follows: material ball ratio of 07, ceramic ball medium size ratio (10 mm: 15 mm: 20 mm = 3:2:5), stirring speed of 110 rpm, grinding concentration of 50%, Highefficiency and energyconservation grinding technology using A regrind ball mill with a mix of small grinding media can be as energy effi cient as an Isa Mill charged with 25 and 35 mm beads In vertical stirred mills, energy savings vary from 30 per cent to 60 per cent To carry out the same fi nal grind, a vertical stirred mill with Millpebs will consume at least 60 per cent less energy than a ball ENERGY SAVINGS AND TECHNOLOGY COMPARISON USING SMALL GRINDING 2017年9月13日 911 Metallurgist is a trusted resource for practical insights, solutions, and support in mineral processing engineering, helping industry professionals succeed with proven expertise How to Calculate Grinding Mill Operating EfficiencyHow to Calculate Grinding Mill Operating Efficiency
43.jpg)
(PDF) Energy Efficient Ball Mill Circuit – Equipment Sizing
2013年7月15日 The ball mill in closed circuit with hydrocyclones is an industry standard, and well known methodologies exist for equipment sizing, selection and design2003年1月1日 The impact of dynamic forces in rockblast fragmentation process has been the subject of investigation for years Nevertheless, while the influence of the macrofragmentation in downstream The Effects of Blasting on Crushing and Grinding Efficiency and Energy 2012年6月1日 As the cylinder starts to rotate, the grinding balls inside the cylinder crush and grind the feed material, generating mechanical energy that aids in breaking bonds, activating the catalyst, and Grinding in Ball Mills: Modeling and Process ControlThe FDS60 nano sand mill features a new pintype grinding component design, ensuring high efficiency, substantial output, and low energy consumption Its compact length/diameter ratio and elevated energy density set it apart The incorporation of a highflux static centrifugal separation sieve with a sizable discharge area ensures that the grinding medium doesn't contact the High efficiency super fineness sand mill FDS60
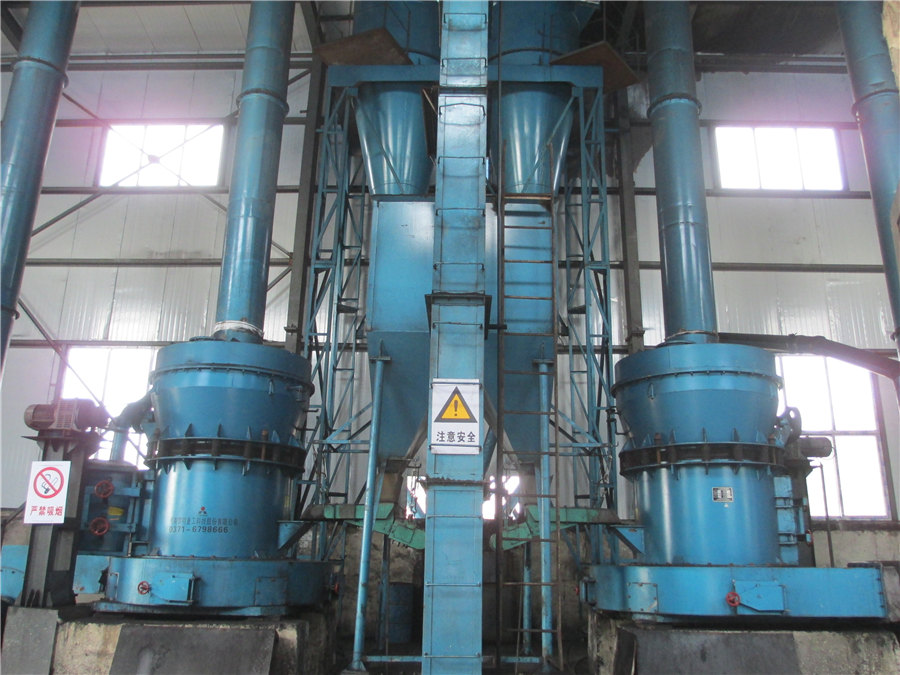
Factors Affecting Ball Mill Grinding Efficiency
2017年10月26日 The following are factors that have been investigated and applied in conventional ball milling in order to maximize grinding efficiency: a) Mill Geometry and Speed – Bond (1954) observed grinding efficiency to be a function of ball mill diameter, and established empirical relationships for recommended media size and mill speed that take this factor into and ultrafine grinding efficiency The SMD utilizes the rotational energy of impeller arms to impart a highenergy motion to the mixture inside the mill With its simplistic design and long maintenance intervals, SMD series provides the highest level of availability in the market Up to 40% higher energy efficiency Up to 250 microns feed sizeMetso comminution solutions Grinding2018年7月1日 Among the industries, the nonmetallic industry was reported as the third largest energy user and accounted for about 12% of the global energy use [1]Within this portion, cement industry had the majority of the utilization with 85–12% [1], [2]US Energy Information Administration (EIA) [7] named cement industry as the most energy intensive among the Energy and cement quality optimization of a cement grinding circuit2009年6月1日 At product sizes finer than 80% passing 75 μm, the efficiency of ball mill grinding rapidly decreasesThe practical limit to ball mill product fineness is considered to be 40–45 μm (Gao and Weller, 1994)Although ball mills can still be found in the regrind circuits in a number of mineral processing plants, their energy consumption is high, and size reduction efficiency is parison of energy efficiency between ball mills and stirred
.jpg)
Energy Savings and Improved Recovery with Small Grinding Media
small grinding media represents the best potential to improve grinding efficiency How do the small grinding media perform in industrial grinding mills? The use of small grinding media in regrind mills proved that finer grinding can be achieved at lower energy consumption In ball mills, smaller grinding media versus 25 mm media generate a2023年9月18日 We're talking about the improvement of energy efficiency in feed mill grinding systems What feed mills should be on the lookout for when they're selecting this equipment, and what kind of savings they can expect by implementing a more energyefficient grinding processSustainable grinding and energy savings in feed mills [Podcast]The mill uses a vertical structure, which reduces the size and weight of the equipment, leading to lower energy consumption The optimized design of the grinding chamber and the use of highquality wearresistant materials further enhance the mill's energy efficiency, reducing energy consumption by up to 30% compared to traditional grinding Environmental friendly energysaving MTW europeantype grinding millVertical roller mills are a leading choice for highcapacity cement grinding VRMs are known for their efficiency in grinding clinker, gypsum, and other cement components They offer several advantages: Energy Efficiency: VRMs use less energy compared to traditional ball mills, reducing overall power consumption by up to 30%HighCapacity Cement Grinding Solutions: Enhancing Efficiency
.jpg)
3 ways to improve feed mill energy efficiency
2023年2月23日 Replacing outdated motors on feed processing equipment with highefficiency motors and variable speed drives (VSD), which match input power to the operational requirements, holds vast potential for feed millers “Too many of the world’s electric motordriven systems still use outdated and inefficient technology, and waste energy as a result,” said Mari 2012年12月29日 Energy efficient comminution circuits (efficient classification) 1525% reduction in grinding energy by replacing cyclones with screens (Jankovic and Valery, 2012) CO 2 savings associated with The Impact Of Classification On The Energy Efficiency Of Grinding A regrind ball mill with a mix of small grinding media can be as energy effi cient as an Isa Mill charged with 25 and 35 mm beads In vertical stirred mills, energy savings vary from 30 per cent to 60 per cent To carry out the same fi nal grind, a vertical stirred mill with Millpebs will consume at least 60 per cent less energy than a ball ENERGY SAVINGS AND TECHNOLOGY COMPARISON USING SMALL GRINDING Are you looking for solution to improve the grinding effencicy of your ball mill? Are you faced with the problem like low grinding efficiency, low processing capacity, high energy consumption, unstable product fineness of the ball mill? You are in the right place Here are the 10 ways for your to improve the ball mill performance: Step#110 Ways to Improve the Grinding Efficiency of Your Ball Mill
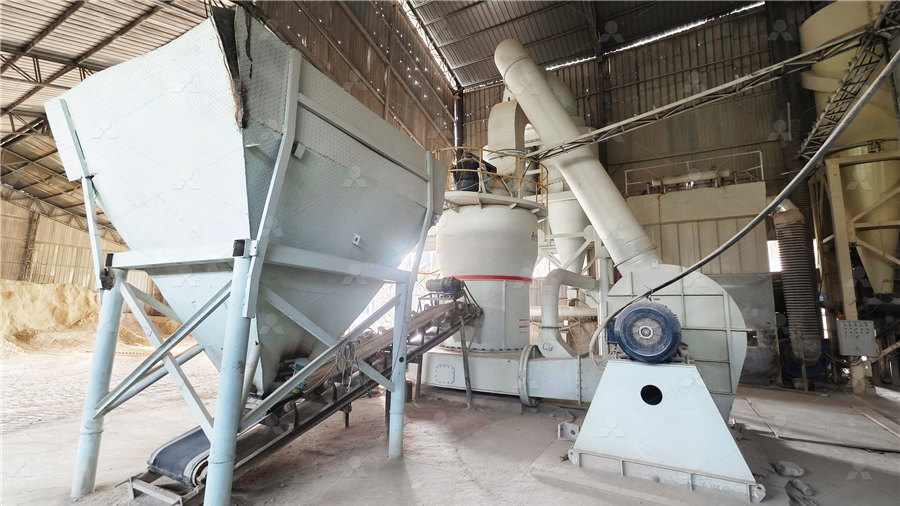
Energy Efficiency Solutions Ball Mill WEG
Ball Mills are widely used in the ceramic and mining industries, where the grinding process requires strict grain size control WEG developed an efficient solution for this applic2019年11月11日 14 November 2024 2 min reading CESCO validates highperformance bagging system for UFC's grain facility in Saudi Arabia CESCO, a global leader in grain handling, storage, and processing solutions, has announced the successful completion of the Factory Acceptance Test (FAT) for a highcapacity bagging line system as part of its extensive project with United EFFICIENCY IN GRINDING AND ENERGY MANAGEMENT IN THE Vibration ball mill is a new type of highefficiency and energysaving grinding equipment It has obvious advantages over traditional rotary ball mill in grinding fine and ultrafine powder materials The grinding efficiency of vibrating ball Vibration Ball Mill New Design Double Tubes 2022年12月5日 Materials and experimental setup The experimental setup is composed of a hammer mill; brand: THURM, Germany; Type: DDR/GDR KMERA 112M2 3/1 It is driven through a belt by a threephase asynchronous motor with the following features: cos \(\varphi\) — 087; rate frequency — 50 Hz; rate speed — 2880 rpm; rate power — 4 kW The corn powder Improvement of the granularity of flour and energy saving by
.jpg)
How to Measure Grinding Efficiency 911Metallurgist
2018年4月20日 The first two Grinding Efficiency Measurement examples are given to show how to calculate Wio and Wioc for single stage ball mills Figure 1 The first example is a comparison of two parallel mills from a daily operating report Mill Energysaving ball mill is a new kind of ball mill grinder developed by us for solving the shortcomings of ordinary ball mill, such as high energy consumption, low output, and low finenessIt is a highefficiency grinder in the ball mill series, which is widely favored by users In the production process, the energysaving ball mill reduces the energy consumption by 30%, High Efficiency Energy Saving Ball Mill For Sale AGICO Ball Mill High grinding efficiency: The grinding force is increased through hydraulic pressurization, improving the grinding efficiency, and the output is large Low energy consumption, saving 30–50% power consumption than ball mills Environmentally friendly: The mill is sealed as a whole and works under negative pressure, without dust spillageEnergysaving and Efficient Vertical Roller Mill Fote Machinery2024年5月31日 This paper presents an industrial verification test, adding a high pressure grinding roll and magnetic separation operation after the thirdstage fine crushing operation to reduce the particle size of ball mill feed and improve the processing capacity of grinding operation The optimal process parameters of high pressure grinding roll and magnetic separation were High Pressure Grinding Roll and Magnetic Separation for Energy Saving
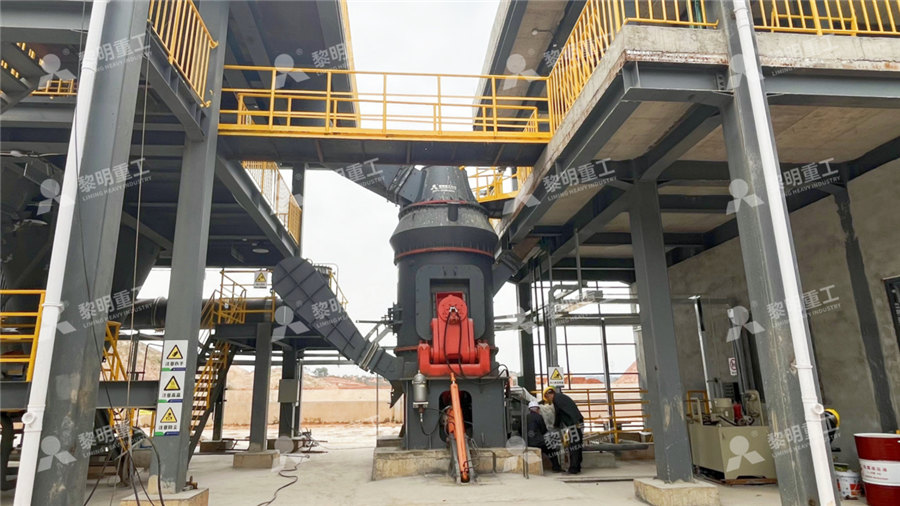
Applications of Efficient EnergySaving Cement Grinding
2010年10月1日 Joint grinding system is the preferred cement grinding system of current cement process design, the advantages are high productivity, low energy consumption of system and low noise, etc2023年4月23日 high speeds of about 90%, causing breakage o f large ore particles wh ilst reducing the mill’s energy efficiency The num ber of cataracting media increases as mill speed increases [ 62 ] (PDF) Grinding Media in Ball MillsA Review ResearchGate2013年8月1日 Energy Efficiency Improvement and Cost Saving Opportunities for Modern stateoft heart concepts utilize a highpressure roller mill and 1993) Various new grinding mill concepts (PDF) Energy Efficiency Improvement and Cost Grinding efficiency is the unit energy consumption rate of the mill, which represents the amount of material with a particle size of 0043 mm newly generated for every 1 kW•h of energy consumed Energy conservation and consumption reduction in grinding
.jpg)
Vertical Stirred Mill Mineral Processing Equipment
For over 60 years of experience in the mineral processing industry, CITIC Heavy Industries (CITIC HIC) has been always committed to increase the grinding efficiency of minerals by constantly searching for ways to improve and Advantages of EnergySaving Grinding Balls As one of the leading cast grinding balls factory, we developed the energysaving grinding balls which didn't deform or lose roundness from large to small, and the breakage rate was extremely lowF or small size grinding balls, we have 20mm grinding ball for example in the range Φ4mm80mm Even under harsh industrial and mining Regrind Ball Grinding Media, EnergySaving Grinding Ballsand ultrafine grinding efficiency The SMD utilizes the rotational energy of impeller arms to impart a highenergy motion to the mixture inside the mill With its simplistic design and long maintenance intervals, SMD series provides the highest level of availability in the market Up to 40% higher energy efficiency Up to 250 microns feed sizeMetso comminution solutions Grinding2024年8月23日 An energysaving ball mill is a kind of equipment specially used for grinding ore, stone, or other pared with traditional ball mills, energysaving ball mill reduces energy consumption and improve grinding efficiency by optimizing design and using a more efficient energy transmission systemEnergysaving Ball Mill VS Cement Ball Mill JXSC Mineral
.jpg)
Energy Use of Fine Grinding in Mineral Processing
2013年12月18日 Fine grinding, to P80 sizes as low as 7 μm, is becoming increasingly important as mines treat ores with smaller liberation sizes This grinding is typically done using stirred mills such as the Isamill or Stirred Media Detritor While fine grinding consumes less energy than primary grinding, it can still account for a substantial part of a mill’s energy budget Overall 2019年3月8日 IMPROVING THERMAL AND ELECTRIC ENERGY EFFICIENCY AT CEMENT 252 Replacing a Ball Mill with a Vertical Roller Mill, HighPressure Grinding Rolls, fuel energy saving of 50 to 80 MJ per ton IMPROVING THERMAL AND ELECTRIC ENERGY EFFICIENCY AT The grinding mill has a small length to diameter ratio, poor wear resistance, long grinding time, and low work efficiency The working efficiency of the cement separator is low so that the micro powder with particle size between 3 and 32μm can’t be separated Energy Saving Measures of Cement Grinding Plant Select energysaving cement millHow to Make Your Cement Grinding Plant More Energy Saving?2009年6月1日 Stirred mills are used in fine and ultrafine grinding where the liberation occurs at very fine sizes [11] [12] [13][14][15][16][17] The stirred media mills are introduced in different process Comparison of energy efficiency between ball mills and stirred