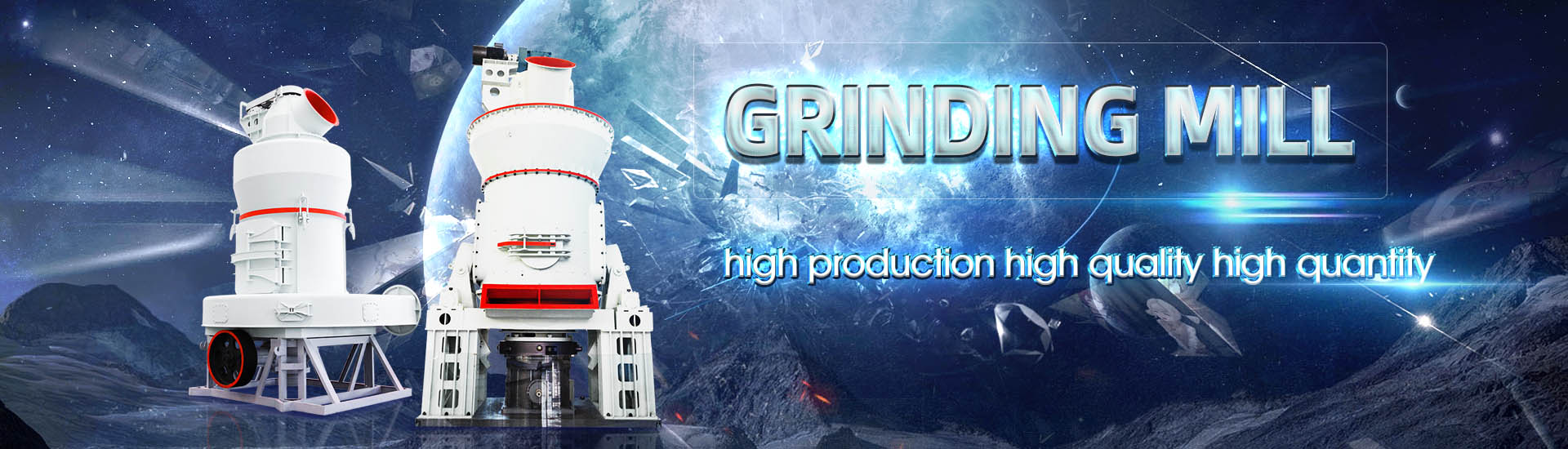
Vertical grinding ore mill crushed particle diameter
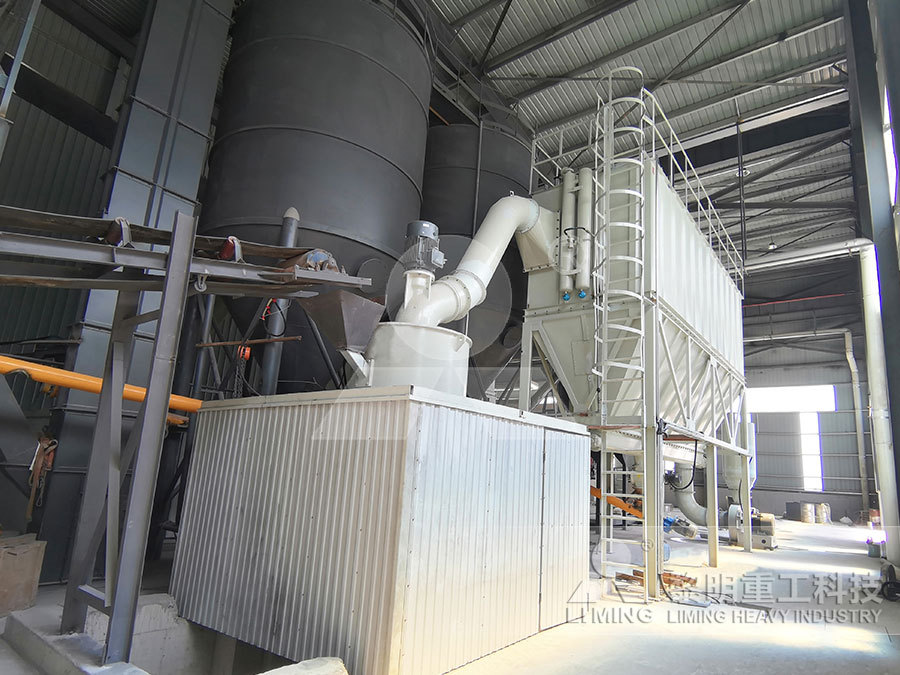
Vertical Roller Mills used for the comminution of mineral ores
Vertical roller mill (VRM) is an established technology in cement and slag grinding applications and Boliden and Gebr Pfeiffer have been collaborating on the application of this technology in the minerals processing industry In such an application a VRM would function as the milling stage 2022年5月31日 In this study, the discrete element method (DEM) was employed to explore the crushing in an overflow VRM without air involved via the bondedparticle model (BPM) Analysis of vertical roller mill performance with changes in material laboratory vertical stirred mill The grinding results show that changes in the feed size, stirring speed, and grinding media size are the primary parameters affecting the particle breakage PREDICTING THE PRODUCT PARTICLE SIZE DISTRIBUTION FROM 2022年5月31日 In this study, the discrete element method (DEM) was employed to explore the crushing in an overflow VRM without air involved via the bondedparticle model (BPM) Analysis of vertical roller mill performance with changes in material
.jpg)
Research of iron ore grinding in a verticalrollermill
2015年3月15日 For the grinding tests, a Loesche mill LM45 (table diameter 045 m) is used (Fig 2 a) This pilot scale mill is a special development for ore grinding, which is reflected by Due to the everincreasing volume of ore to be processed, singleparticle crushing has not been scalable; therefore, the HPGR’s larger “bed compression” sizereduction mechanism, which Flowsheet of the Future: HighPressure Grinding Rolls, Vertical 2014年11月1日 In this study, a coarse sample of iron ore was tested in a pilot scale grinding circuit with a vertical mill Other three samples of pellet feed had already been tested with the methodologyVertical mill simulation applied to iron oresVertical stirred milling is a wellrecognized technology for the secondary, regrind and fine grinding applications and are increasingly replacing coarser ball mill applications in secondary and RECENT DEVELOPMENTS IN COARSE GRINDING USING VERTICAL
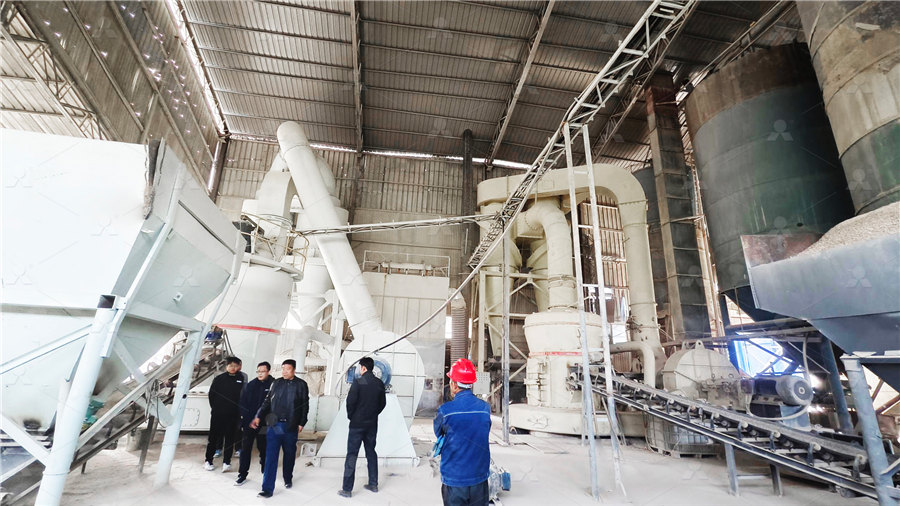
Numerical Investigation of Vertical Roller Mill Operation Using
2023年12月4日 Cleary simulated the industrialscale ball mill of 5 m diameter using DEM to predict the motion of particles, power, torque, and liner wear by varying the mill speed and 2024年1月17日 Vertical roller mills, VRMs, are widely used for grinding raw materials in factories engaged in the extraction and processing of minerals Any machine used for grinding or crushing consumesParameters for the Grinding Process in Vertical Mills 2019年4月16日 Conference: Applying a Successful Technology from the Cement Industry: Advantages of Grinding Ore in a VerticalRollerMill; At: Antalya, Türkey(PDF) LEARNING FROM OTHER INDUSTRIES; WHY THE LM vertical mill adopts new milling devic and automatic electric control system, saving 40% 50% power consumption compared to ball millSpecial structure design of grinding roller and grinding table, large diameter of grinding roller, LM Vertical Roller Mill, slag vertical mill, coal
.jpg)
PREDICTING THE PRODUCT PARTICLE SIZE DISTRIBUTION FROM A VERTICAL
Figure 51 Breakage function from grinding in a laboratory vertical stirred mill 85 Figure 52 Specific selection function from grinding in a laboratory vertical stirred mill 86 Figure 53 Measured (points) and predicted (dotted lines) product particle size distributionBarite ultrafine vertical roller mill is an industrial vertical grinding mill that can grind nonmetallic ore into fine powder The mill has a high production capacity, high fine powder content, high degree of automation, convenient maintenance, long service life, environmental protection, and energysaving, and is an ideal equipment for largescale production of ultrafine powderBarite Ultrafine Vertical Roller MillLimestone ultrafine vertical mill is a high quality ores material powder grinding mill +17 [ protected] Working Diameters (mm) 1400: 1600: 1700: Number of rollers (pieces) 3: 3: 3: Number of classifier (pieces) 6: 6: 6: the material is crushed by extrusion, grinding and shearingLimestone Ultrafine Vertical Mill2023年7月22日 Ore crushing is the process of breaking, splitting, extrusion, impacting, and grinding of large solid ore with external force to reduce the particle size of large ore materials Ore crushing provides suitable particle size of material for subsequent ore grinding, beneficiation or smelting, which is the preparation process before beneficiation or smeltingOre Crushing SpringerLink
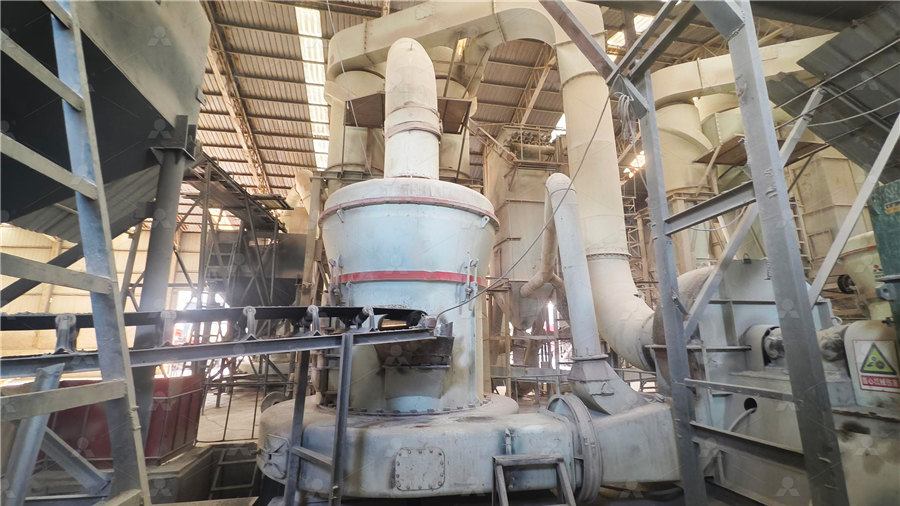
HLM Vertical Grinding Mill Vertical Roller Mill
HLM vertical grinding mill and vertical roller mill is a highefficiency energysaving advanced pulverizing equipment integrating drying, pulverizing, grading and conveying, which has been researched and developed by Guilin Hongcheng Company for more than 20 years Hongcheng HLM vertical grinding mill has the advantages of high grinding efficiency, low power 2013年4月16日 A laboratory scale pintype vertical stirred mill and ceramic beads were employed for the grinding tests The effects of ball diameter (245 mm), stirring speed (200800 rpm) and ball charge Investigation of some parameters affecting the Ultrafine grinding Request PDF On Mar 15, 2015, Mathis Reichert and others published Research of iron ore grinding in a verticalrollermill Find, read and cite all the research you need on ResearchGateResearch of iron ore grinding in a verticalrollermillAll ores have an economic optimum particle size which maximizes the difference between net smelter return (NSR) and grinding costs (Chapter 1): too coarse a grind and the inadequate liberation limits recovery (and thus revenue) in the separation stage; too fine a grind and grinding costs exceed any increment in recovery (and may even reduce recovery depending on the Grinding Mill an overview ScienceDirect Topics
.jpg)
Ultrafine Vertical Mill
Ultrafine vertical mill is a highefficient industrial grinding mill, The materials are driven to the edge of the disc by centrifugal force and crushed into fine powders by rollers Illite ore industrial grinding mill machine can grind illite into 2020年8月12日 Altun et al [15] explored the influence of the parameter settings of a vertical roller mill on grinding performance and demonstrated the influence of grinding pressure values on the size and mass An investigation of performance characteristics and 2014年10月1日 In a test performed in the Loesche test center in Germany, copper slag grinding saved 229% energy in an airswept model and 344% energy in an overflow model [13,14]Copper Ore Grinding in a Mobile Vertical Roller Mill Pilot PlantLimestone Powder Ultrafine Vertical Roller Mill Modle : CLUM Series Finished Size: 4003000 mesh Processing Ability: 3 – 45t/h Max Feeding Size: 10 mm M 1 Set Price: $ Range Of Application: Limestone, Calcium Carbonate, Talc, Limestone Powder Ultrafine Vertical Roller Mill
.jpg)
Vertical Roller Mills used for the comminution of mineral ores
The Pfeiffer pilot mill used in this study is a semiindustrial vertical roller mill of type MVR with a table diameter of 400 mm The mill can be equipped with different classifiers for specific applications The process layout of the plant (Figure 2) corresponds to that of an industrial plant Figure 2: Process layout of the semiindustrial 2022年1月23日 This work concentrates on the energy consumption and grinding energy efficiency of a laboratory vertical roller mill (VRM) under various operating parametersAnalysis and Optimization of Grinding Performance of Vertical 2015年3月15日 For the grinding tests, a Loesche mill LM45 (table diameter 045 m) is used (Fig 2 a) This pilot scale mill is a special development for ore grinding, which is reflected by several features The mill has four rollers, which are able to stress the particle bed with grinding pressures of up to 5000 kN/m 2Research of iron ore grinding in a verticalrollermilltraditional SAG mill, ball mill, and crusher circuits, as repo rted by Daniel, Lane and McLe an (2010) For this reason, original equipment manufacturers like Weir have increased the size of HPGRs to effectively process larger volumes of ore in a more energyefficient manner (Figure 2) Figure 2—Enduron 26 Metre (m) Diameter x 26 m HPGR,Flowsheet of the Future: HighPressure Grinding Rolls, Vertical
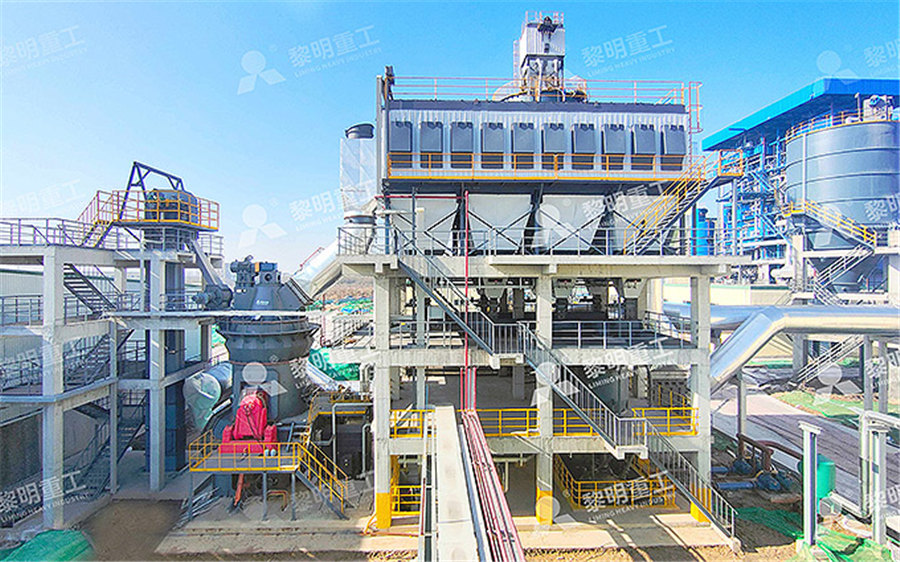
Analysis of vertical roller mill performance with changes in
2022年5月31日 Mineral crushing is the main source of energy consumption in mineral processing According to statistics, this consumption accounts for about 35–50% of the total cost of the mine (Curry et al, 2014), or even higherIt may also account for 18% of the global electrical energy consumption (NapierMunn, 2015)More efficient crushing equipment needs to be 2023年7月20日 Except those that process some placers, almost all mineral processing plants have grinding operations, in which materials are crushed by the impact and abrasive action of grinding medium (steel rod, steel ball, gravel, or ore block itself) to meet the requirements of separation operation, and the particle size of the product is generally less than 5 mm Based Ore Grinding SpringerLinkDownload Citation The Vertical Mill Slag MicroPowders' Particle Size Distribution and Microstructure Analysis Vertical mill grinding system is one of the important cement grinding equipments The Vertical Mill Slag MicroPowders' Particle Size Distribution 2015年3月15日 Vertical Agitated Media Mill modeling has become subject of a research project due to its potential application as a secondary grinding mill as well as regrind and pellet feed preparation projectsVertical Agitated Media Mill scaleup and simulation
.jpg)
Understanding the SAG Mill in Copper Ore Mining Process
The Tower Mill is another type of grinding mill used in the mining industry This vertical mill consists of a cylindrical chamber filled with grinding media, which are stirred by a shaft that moves vertically up and down Tower Mills were developed to overcome some of the limitations of both ball mills and SAG millsFigure 51 Breakage function from grinding in a laboratory vertical stirred mill 85 Figure 52 Specific selection function from grinding in a laboratory vertical stirred mill 86 Figure 53 Measured (points) and predicted (dotted lines) product particle size distributionPREDICTING THE PRODUCT PARTICLE SIZE DISTRIBUTION FROM A VERTICAL 2017年9月1日 This situation makes it necessary to examine parameters such as the type of grinding material (coal/ore), grinding type/medium, grinding technique, particle size, shape, size distribution Fine grinding: How mill type affects particle shape characteristics 2017年1月10日 This paper evaluates the effects of operating parameters on fine particle grinding process with a vertically stirred media mill The effects are investigated through size reduction under different Effect of operating parameters on fine particle grinding in a
.jpg)
Modeling and simulation of vertical roller mill using population
of 80mm The raw materials are mixed in a certain proportion and fed into a vertical roller mill (LOESCHE mill) The vertical roller mill grinds the marital to D 85 of 90µm The ground product is calcined in a preheater to 850900℃ After calcination, the materials enter to a rotary kiln and heated to 1450℃ to become clinker2024年11月1日 Numerical Study of Flow Field and Particle Motion Characteristics on Raw Coal Vertical Roller Mill Circuits Author links open overlay panel the MMLM2550 (supplied by Jiangsu Dahuan Group, China; grinding table diameter of 2550 mm) VRM as resulting in qualified particles being crushed by grinding rollers Numerical Study of Flow Field and Particle Motion Characteristics 2015年3月15日 For the grinding tests, a Loesche mill LM45 (table diameter 045 m) is used (Fig 2a) This pilot scale mill is a special development for ore grinding, which is reflected by several features The mill has four rollers, which are able to stress the particle bed with grinding pressures of up to 5000 kN/m 2Research of iron ore grinding in a verticalrollermillBall mills are progressively used to grind the ores for particle size reduction and to liberate valuable minerals from the ores The grinding of ore is a highly energyintensive process [1–4] In this process, the size of the particle obtained depends on the energy consumption of the ball mill The major challenge encountered in theEstimation of Grinding Time for Desired Particle Size Distribution
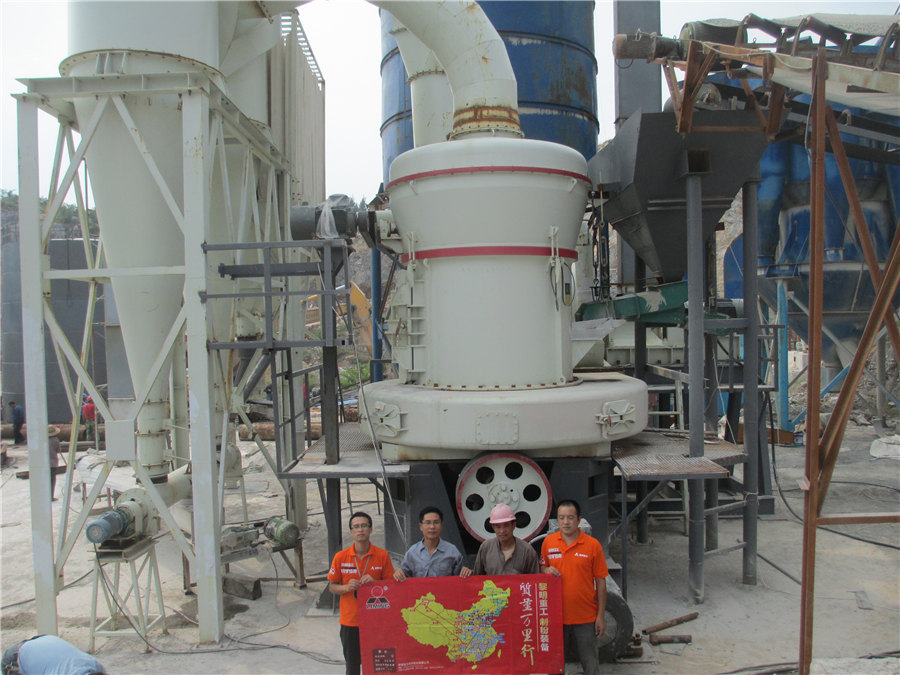
NRRI advances efficient grinding technology on the
2024年5月6日 A crucial step in mineral processing – and in Minnesota’s iron ore processing – is comminution, a process of crushing and grinding Large rocks must first be crushed and then ground down to tiny particles to expose the 2019年3月3日 Prziwara et al studied grinding aids' effects on bulk properties such as product neness, particle size distribution, powder ow ability, surface area and surface energy [8] some studies on the Modeling and simulation of vertical roller mill using The coal vertical mill, also referred to as the vertical roller coal mill, is an advanced equipment developed by our company It combines modern technology with our extensive experience in powder manufacturing This coal pulverizer efficiently integrates coal grinding and drying, providing highperformance and energysaving featuresHighEfficiency Vertical Coal Mill Enhancing Coal Pulverizationof 80mm The raw materials are mixed in a certain proportion and fed into a vertical roller mill (LOESCHE mill) The vertical roller mill grinds the marital to D 85 of 90µm The ground product is calcined in a preheater to 850900℃ After calcination, the materials enter to a rotary kiln and heated to 1450℃ to become clinkerModeling and simulation of vertical roller mill using population
制粉-10.25公众号.jpg)
Dolomite Ultrafine Vertical Roller Mill
The vertical roller mill integrates crushing, drying, grinding, and conveying +17 [ protected] Particle size distribution: SBM Micro Powder Technology is an excellent manufacturer of ore crushing and grinding equipment in China All equipment is directly supplied by the factory, with real prices and higher cost performanceBall Mill Grinding Process Handbook Free download as PDF File (pdf), Text File (txt) or read online for free This document provides guidance on ball mill grinding processes It covers topics such as ball mill design including length to diameter ratios, percent loading, critical speed, and internals evaluation Methods for assessing ball charge, wear rates, and liner management are Ball Mill Grinding Process HandbookIn a ball mill or pebble mill the sizereduction is carried out by impact as the balls or pebbles drop from near the top of the shell In a large ball mill the diameter of shell may be 3 m and 425m in length The balls are 15 to 125 mm in diameter; the pebbles in a Size Reduction1: Grinding – Unit Operations in Food ProcessingInvestigation on the particle size and shape of iron ore pellet feed using ball mill and HPGR grinding methods Armin Abazarpoor, Mohammad Halali Materials Science Engineering Department, Sharif University of Technology, Azadi Street, PO box 1136511155, Tehran, Iran, Corresponding author: f (Armin Abazarpoor)Investigation on the particle size and shape of iron ore pellet feed
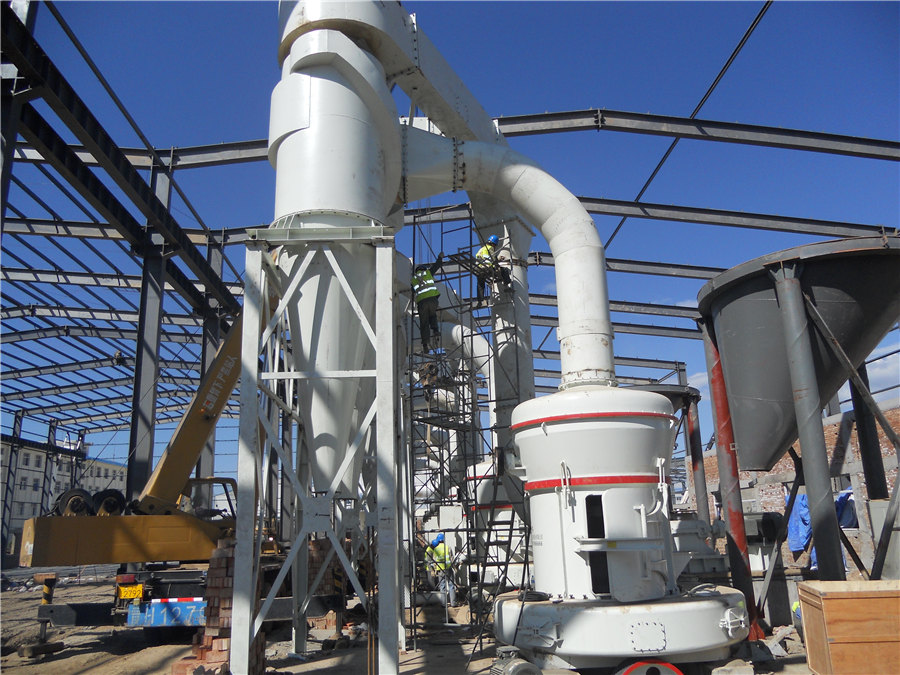
Review on vertical roller mill in cement industry its
2021年1月1日 Big feed size The vertical roller mill can grind the material of particle size of 5% of the grinding roller diameter The feed size is generally 40 to 100 mm and can reach 120 mm in case of large VRM