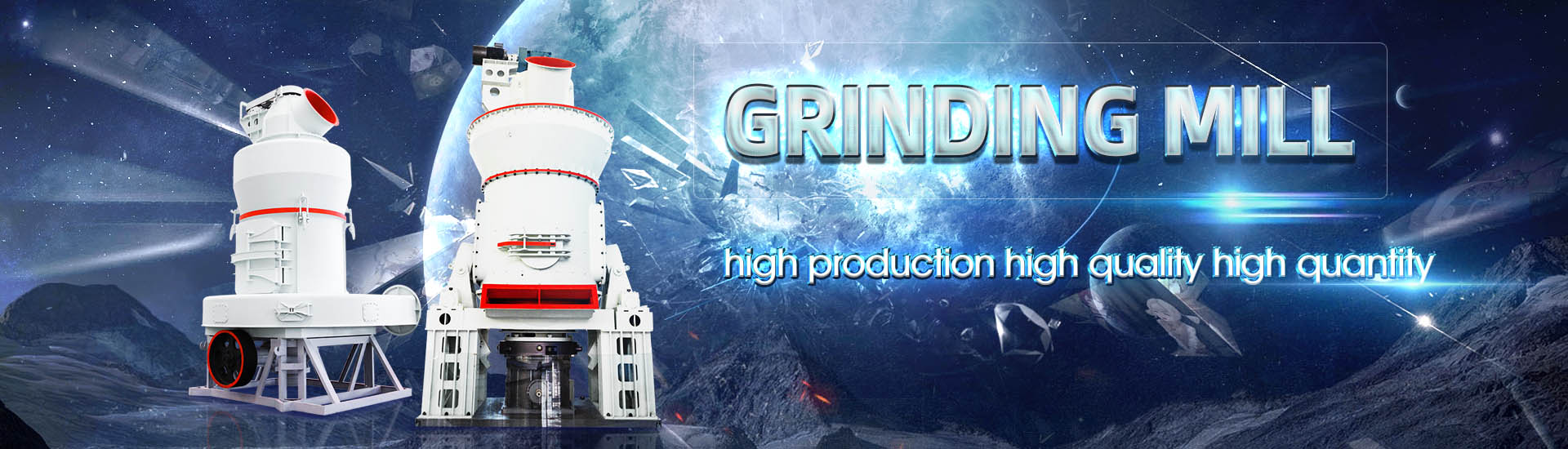
Ore grinding mill energy efficiency index
.jpg)
Quantifying the energy efficiency of fine grinding circuits
2021年11月25日 Two of the most popular methods for estimating grinding energy requirements are the Bond operating work index (OWi) and the Morrell specific comminution energy method Both relate the comminution energy to 2020年6月1日 For fine and ultrafine grinding, the Bond work index is an inappropriate measure of grindability, so alternatives are discussed Using literature data, the variation in the Stirred media mills in the mining industry: Material grindability 2013年12月18日 Fine grinding, to P80 sizes as low as 7 μ m, is becoming increasingly important as mines treat ores with smaller liberation sizes This grinding is typically done using stirred mills such as the Isamill or Stirred Energy Use of Fine Grinding in Mineral Processing2009年6月1日 Four different laboratory ball mills and stirred mills have been tested to grind seven ore samples with feed sizes ranging from 335 mm to 150 μm A case study on full Comparison of energy efficiency between ball mills and stirred
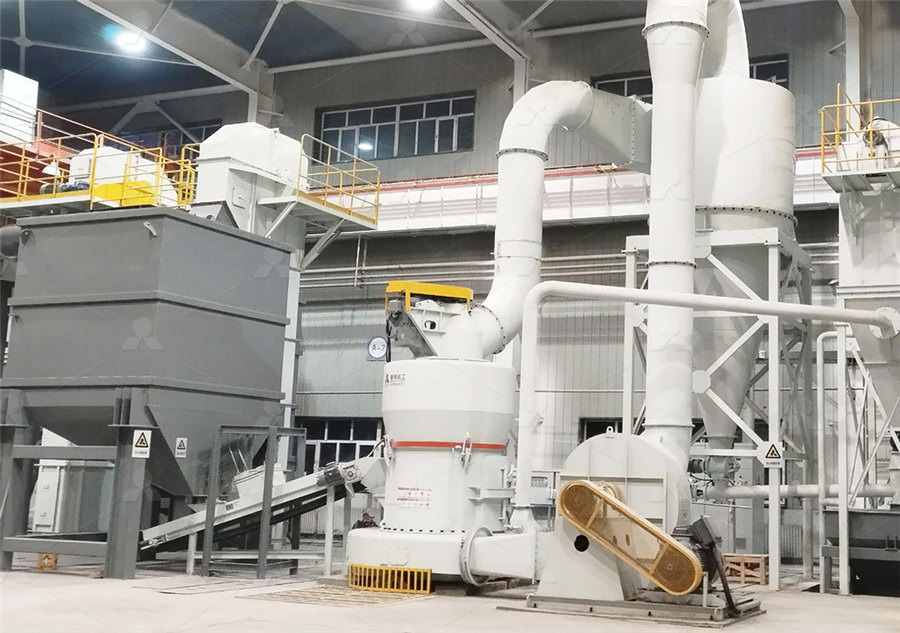
MODELING THE SPECIFIC GRINDING ENERGY AND BALLMILL
Relationship between the Bond work index (w i) and the ore hardness designated by Denver In the next Figure a comparison is made between the specific grinding energy (w) values, which GMG guidelines are peerreviewed documents that describe good practices, advise on the implementation and adoption of new technologies, and/or develop industry alignment They Methods to Survey and Sample Grinding Circuits for Determining 2024年11月11日 In evaluating ore grinding energy consumption using the Bond ball mill work index, discrepancies were identified As a result, an investigation into the determination Exploring the Link between HY Wet Ball Mill Work Index and The effects of different speeds on energy consumption, product particle size, and grinding efficiency were analyzed in this study An experimental vertical stirred mill was used to grind Experimental Study on the Influence of Rotational Speed on
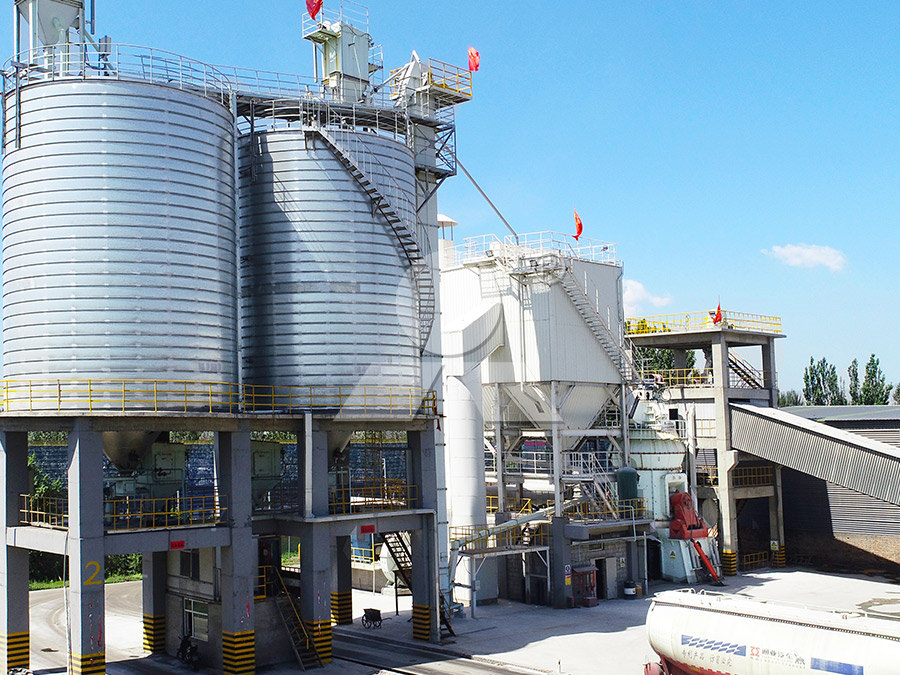
Modeling of Bauxite Ore Wet Milling for the Improvement of
Estimations on energy consumption indicate that milling consumes more than 50 % of the total energy used in mining operations Despite the fact that ball milling is an efficient operation, it is 2023年7月11日 It provides a comparison description of the parameters of available datasets and a classification of their machine learning and deep learning models applied to predict energy Predicting energy consumption of grinding mills in mining 2023年10月20日 To support a highlevel analysis of grinding circuit energy efficiency, it is typically necessary to collect one sample from the grinding circuit feed and one from the grinding circuit product The sampling from the grinding circuit feed is required to allow accurate determination of the grinding circuit feed size and to provide samples for ore characterization Methods to Survey and Sample Grinding Circuits for Determining Energy A crushing plant delivered ore to a wet grinding mill for further size reduction The size of crushed ore (F 80) was 40 mm and the SG 28 t/m 3 The work index of the ore was determined as 122 kWh/t A wet ball mill 1 m × 1 m was chosen to grind the ore down to 200 micronsGrinding Mill an overview ScienceDirect Topics
.jpg)
High Pressure Grinding Roll and Magnetic Separation for Energy
2024年5月31日 This paper presents an industrial verification test, adding a high pressure grinding roll and magnetic separation operation after the thirdstage fine crushing operation to reduce the particle size of ball mill feed and improve the processing capacity of grinding operation The optimal process parameters of high pressure grinding roll and magnetic separation were 1989年1月1日 The Bond work index, W i, as an indicator of the grindability of raw materials is not a material constant but rather it changes with change of size of the grinding productTherefore, in practice we can expect some difficulties and errors when the energy consumption is determined according to this formula in the case when, for a given size of grinding product, the value of Calculation of energy required for grinding in a ball mill2021年12月11日 1 Introduction The efficiency of mineral separation and utilization is part of the research in the fluidized mining technology, and the breakage and liberation of minerals are the key to the efficiency of mineral utilization []When ores containing useful minerals are being processed by relevant equipment and methods, valuable minerals are liberated from gangue The Effect of Grinding Media on Mineral Breakage Properties of 2023年1月13日 Generally, the harder the ore, the coarser the feed, the finer the product, the lower the grinding efficiency of the ball mill and the higher the grinding efficiency index calculated by (kWh Three Major Factors Affecting the Grinding Efficiency of Ball Mill
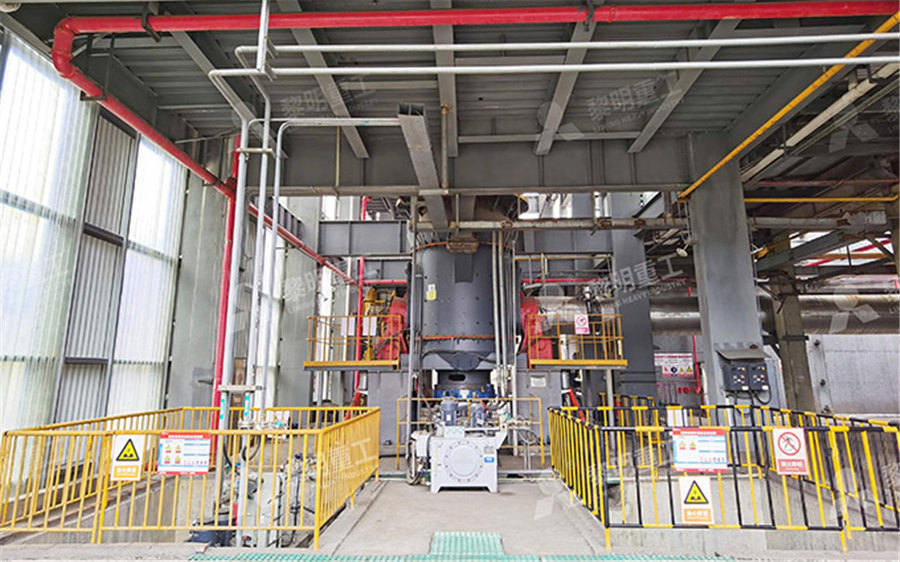
Work Index SpringerLink
2023年7月20日 The selfgrinding work index is an extension of the concept of Bond work index It generally refers to the work index calculated by using Bond’s fracture theory on the principle of ore crushing energy consumption according to the W, F, and P data of a small or semiindustrial or industrial selfgrinding test In this kind of test, McPherson small selfgrinding closedcircuit GRINDING ENERGY AND BALLMILL SCALEUP K G Tsakalakis GA Stamboltzis NTUA AthensGreece Introduction of the Bond work index w i to the above equations Hard ore 180 1961 Medium ore 120 1290 Soft ore 65 0671 Coefficients k Bond work index (w i), kWh/short ton Denver orehardnessMODELING THE SPECIFIC GRINDING ENERGY AND BALLMILL subjected to further separation processes Grinding is characterized by high energy consumption and low energy efficiency (~ 1%) (Cheng et al 2019; Liu et al 1989; NapierMunn 2015) Moreover, grinding efficiency decreases as the particle size get finer due to the increase in the interparticle forces by theEffects of Chemical Additives on Rheological Properties of Dry 1994年11月1日 A new method is proposed for measuring the grindability of solids and the energy efficiency of grinding mills The method is based on a similarity law of fracture mechanics for elastic materials in conjunction with the selfpreserving character of the size distributions formed when feed particles are comminuted individually in compression The singleparticle A new approach to assessing the grindability of solids and the energy
.jpg)
Predicting the grinding energy of vrm depending on material
2021年9月1日 The back calculated K parameter ranges widely for this study, from approximately 4 to 105 The relationship between the K parameter and Ore Index which is determined from the compressed bed breakage test was investigated An increasing trend of Ore Index as the K parameter decreases points to a significant relationship statistically (Fig 7)2016年1月1日 For grinding circuits where the feed to a ball mill is sent directly to the classifier and the cyclone underflow feeds the ball mill (see Figure 310), a question arises as to whether this practice will alter the ball mill work index (BW i) of the material being ground and hence have an impact on the energy used in the mill for grindingSize Reduction and Energy Requirement ScienceDirect2020年6月1日 It has been estimated that approximately 2% of the world's energy usage is applied to mineral comminution, and around a quarter of this is used specifically in metalliferous ore grinding [1] where it is typically the most energy intensive set of operations [2]The purpose of comminution in ore processing is to reduce particle size in order to improve liberation of Stirred media mills in the mining industry: Material grindability 2023年4月24日 Grinding is the final stage of comminution, which reduces particle size to micron size level The size reduction is achieved by attrition, abrasion, and impact between the ore itself and between the ore particles and grinding media []According to Swart et al [], ball mills are mostly used because of their very high size reduction ratio, although they have a very low Grinding Media in Ball MillsA Review [v1] Preprints
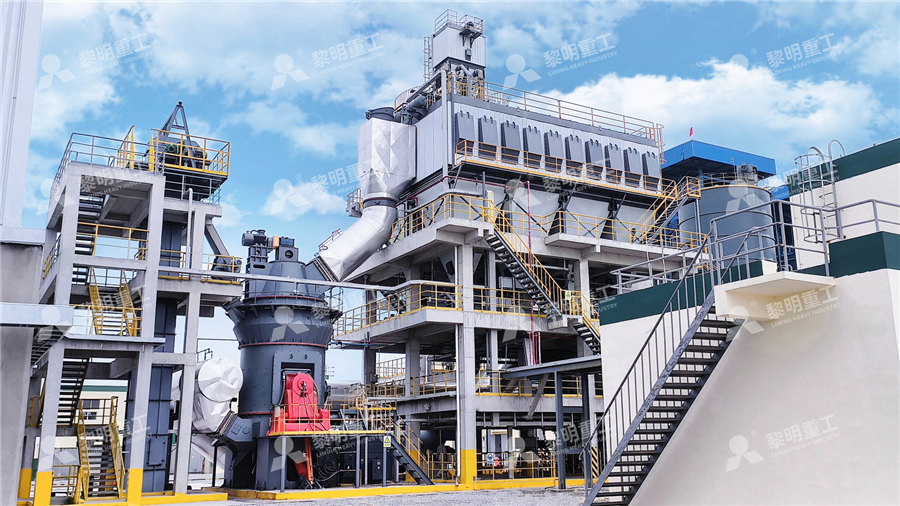
Quantifying the energy efficiency of fine grinding circuits
2021年11月25日 Benchmarking energy efficiency requires three Two of the most popular methods for estimating grinding energy requirements are the Bond operating work index (OWi) high pressure grinding roll and tumbling mill circuits Minerals Engineering 22, 544549 Davis, EW, 1919 Fine crushing in ballmills Transactions of the 2016年11月22日 The grinding zone temperature elevation is dependent on the grinding efficiency and the proportion of grinding energy that enters the workpiece Experimental results (Rowe, Morgan, Black, Mills, Citation 1996 ) show that the energy transfer proportions between the workpiece and grinding wheel remain relatively constant; albeit the energy distribution is Effect of different parameters on grinding efficiency and its 2017年7月1日 Results must therefore be analysed with cautious as the energy efficiency index does not factor in whether or not the product meets the required quality 33 Discussion The basic regulatory PI control of the pump box level and hydrocyclone pressure certainly looks appealing at first glance: constant rod mill feed rate, no risk for the pump box Reducing the energy footprint of grinding circuits: the process 2023年11月1日 Grinding operation is the last preparation stage before beneficiation In this stage, the material undergoes the combined action of impact and grinding, so that the ore particle size is diminished and the qualified materials is provided for succeeding beneficiation operations [1, 2]Generally, the quality of the grinding product is also an important factor to determine the Energy conservation and consumption reduction in grinding
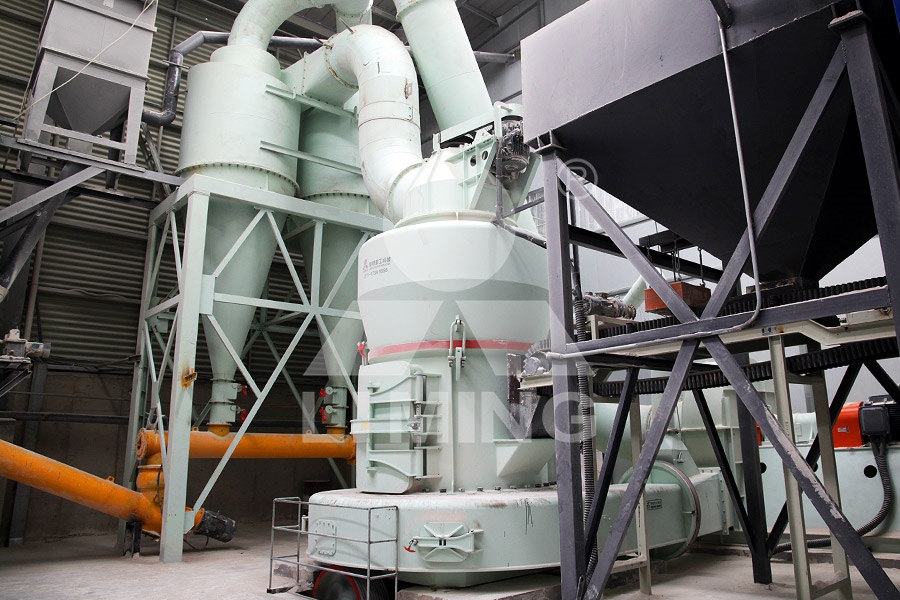
Effect of different mills on the fine grinding characteristics and
2024年9月1日 Fine grinding is a milling method of crushing materials to less than −01 + 001 mm by using grinding, impacting, shearing and other forces within the mill (Kumar et al, 2023)The purpose of grinding is not only to provide a suitable feed size for further processing but also to release valuable minerals from the gangue, which is tightly combined in the ore2023年7月1日 Element based ball mill and hydrocyclone modelling for a copper ore grinding circuit Analysis of ball mill grinding operation using mll power specific kinetic parameters, Advance Powder Turkish Standards, TS 7700, Determination method of grinding work index Google Scholar Valery et al, 2019 Valery, W, Duffy, K Element based ball mill and hydrocyclone modelling for a copper ore 2017年8月1日 This study analyzes the exergy efficiency of comminution using a laboratory sized dry ball mill and a copper mineral ore from central Chile In this research, we develop a minimum work index from uniaxial compression tests results on the ore fitted to Morrell’s comminution energy equation using Hukki’s constant mineral parameterThe efficiency of copper ore comminution: A thermodynamic and SAG mill circuits in hard ore applications by P Rosario*† and R Hall† Synopsis The application of high pressure grinding rolls (HPGR) has been growing in the mining industry for the last 10 to 15 years The major benefits supporting this trend are better energy efficiency, improved grinding capacity, and higher metal recovery inA structured approach to the evaluation T of the energy SciELO
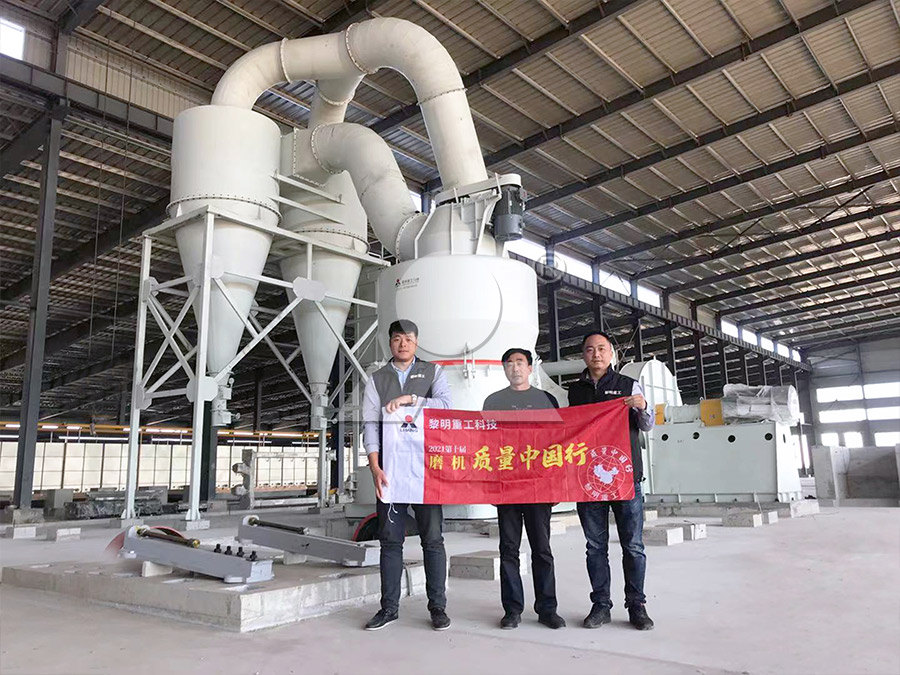
Mill (grinding) Wikipedia
A mill is a device, often a structure, machine or kitchen appliance, that breaks solid materials into smaller pieces by grinding, crushing, or cutting Such comminution is an important unit operation in many processesThere are 2019年1月11日 In addition, the energy consumed by the ball mill for similar fineness (5 µm) was approximately 300 kWh/t energy, whereas the stirred media mill consumes approximately 174 kWh/t energy As a result, the stirred mill consumed less energy because it Performance comparison of stirred media mill and ball (BOND) mill 2021年11月1日 In this study, limestone samples (a total of 108 sample) were collected from two limestone quarriesThe collected samples were initially in the form of palm sized and they were crushed to −236 mm Grinding experiments were conducted in standard HGI (Hardgrove Grindability Index) mill and Ring mill PSD (Particle Size Distribution) analyzes were carried Limestone grindability in terms of HGI and a new approach for the Improving Energy Efficiency in SAG Mills PilotScale SAG Mill Facility Will Help to Optimize Charge Motion and Slurry Flow in PlantScale SAG Mills Reducing Energy Consumption The US mining industry operates approximately 80 semiautogenous grinding mills (SAG) throughout the United States Both mine and mill site variables determine SAGITP Mining: Improving Energy Efficiency in SAG Mills
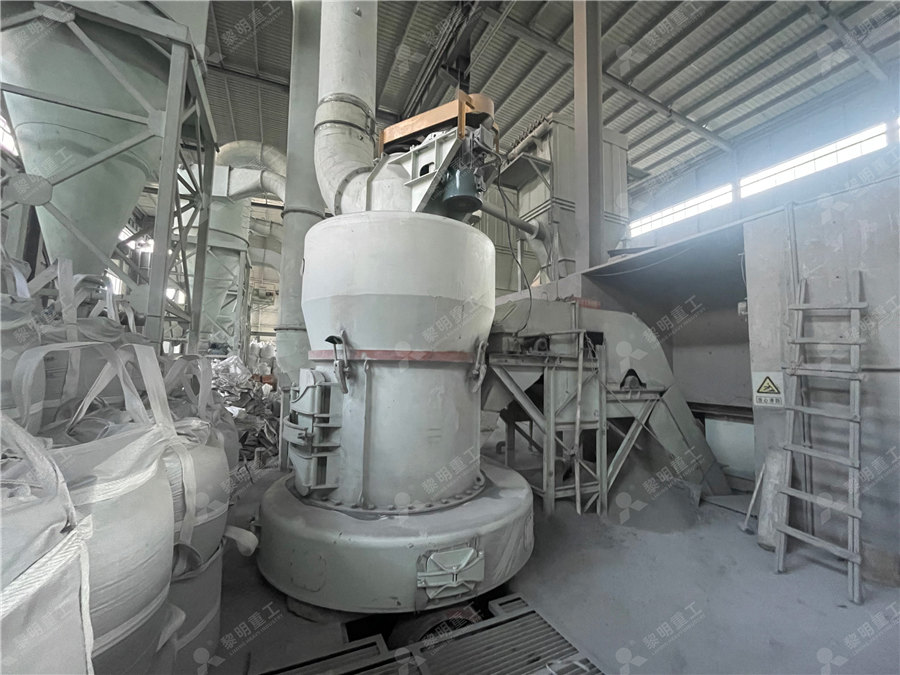
Evaluating the performance of an industrialscale high pressure
2023年1月1日 HPGR with its compressed bed crushing mechanism improves ore grindability with enhanced energy efficiency to prepare feed for the subsequent tower mill The maintenance schedule of the HPGR circuit should be aligned with the grinding and separation operations, to achieve an annual availability exceeding 92 % •2009年6月1日 At product sizes finer than 80% passing 75 μm, the efficiency of ball mill grinding rapidly decreasesThe practical limit to ball mill product fineness is considered to be 40–45 μm (Gao and Weller, 1994)Although ball mills can still be found in the regrind circuits in a number of mineral processing plants, their energy consumption is high, and size reduction efficiency is parison of energy efficiency between ball mills and stirred 2017年11月2日 Defining energy efficiency as the energy required for breakage divided by the energy used by the mechanical system, the energy efficiency for comminution is reported to range from 01 to 2% [55, 56] Based on fundamentals of fracture mechanics, Tromans [ 57 ] hypothesized that there is a maximum limiting energy efficiency for comminution of between 5 EnergyEfficient Comminution: Best Practices and Future2023年4月24日 necessary excess energy [16] In ball mill operations, it is always helpful to optimise the grinding media system to minimize the costs of the operation In a research done by Yu et al [16] to optimize grinding media system, there was a 30% increase in grinding efficiency and also a reduction in energy consumptionGrinding Media in Ball MillsA Review Preprints
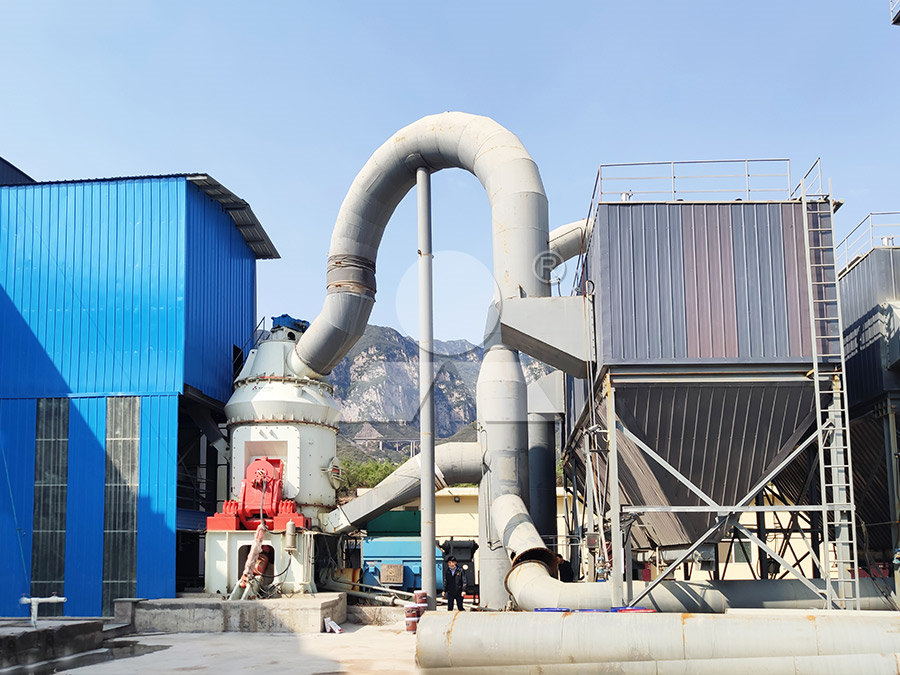
Fine grinding in a horizontal ball mill ScienceDirect
2007年4月1日 The main reason ball mills are not utilised for fine grinding is the perceived poor energy efficiency generally experienced when grinding to fine sizes However there is a trend towards ball mill grinding for product sizes below the traditional ball mill cutoff of 45 and a Bond Work Index test on a gold ore sample2022年10月4日 A notable fact is that the energy efficiency of conventional milling is only about 1%, as mentioned in Sect 1 An earlier experimental study indicated that about 80–90% of the energy input of a ball mill was used in heating the material (Schellinger 1951, 1952), and a recent study showed that over 75% of the electrical energy was used to heat the slurry (Bouchard et Reduction of Fragment Size from Mining to Mineral Processing: A Grinding costs are driven by energy and steel (media, liners, etc) consumption; grinding is the most energyintensive operation in mineral processing On a survey of the energy consumed in a number of Canadian copper concentrators it was shown that the average energy consumption in kWh t −1 was 22 for crushing, 116 for grinding, and 26 for flotation ( Joe, 1979 )Grinding Mill an overview ScienceDirect TopicsOnline SAG Mill Grinding Pulse Measurement and Optimization New Integrated Grinding Technology Will Optimize SAG Mill mill Nation Operations and Reduce Energy The IGB technology will allow the mill • Increases energy efficiency in Usage operators to assess the conditions in the grinding mills by as ore’s characteristics change TheseUS Department of Energy Office of Energy Efficiency and
.jpg)
Benchmarking comminution energy consumption for the
2014年10月15日 Levin (1992) proposed a new method for calculating the size specific energy (SSE) requirements of an ore based on the mass of fine material produced, usually defined by the proportion of material below 75 μm The difference between the two indices is that the work index is based on P 80 which is always fairly close to the size of the largest particle, whereas the high energy consumption, lower throughput, and loss of ultrafine chromite Laboratory studies indicated the differences in the grinding properties (work index, breakage rate, etc) and liberation sizes of these ores Studies also revealed that grinding media size, particle retention time, and pulp density are crucial in coarse grinding Based v117n1a11 Performance optimization of an industrial ball mill for 2021年11月1日 In addition, they indicate that the Bond ball mill work index is equal to 153 kWh/ton, and to improve ore grinding energy efficiency [5] It is worth noticing that significant heat is usually generated in ore grinding, and this can be considered as an efficiency related lossExperimental characterization of chalcopyrite ball mill grinding 2014年11月28日 An analysis during an energy audit at Wesfrob Mines Ltd (now closed) showed that the relationship between specific electricity consumption (kW h/tonne) and throughput for the total operation as well as for the separate crushing and grinding stages was inversely related (Doyle, 1979); energy savings at the mill could be achieved either by increasing the amount of The link between operational practices and specific energy consumption
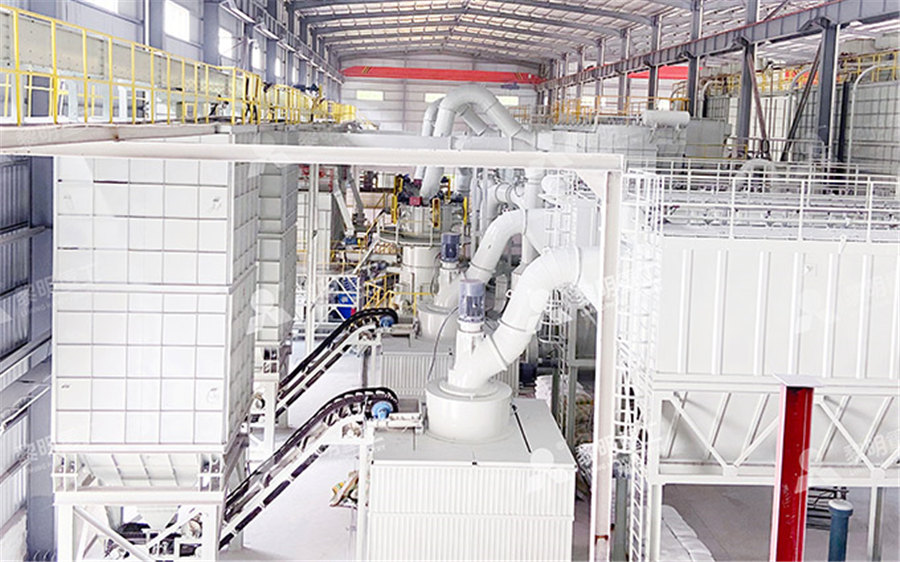
Size reduction performance evaluation of HPGR/ball mill and
2023年1月1日 It can be concluded that the ball mill should be operated at a higher mill speed for good grinding efficiency Download: Download highres image (407KB) Download: Download fullsize image; Therefore, PGE bearing lowgrade chromite ore needs an energyefficient grinding mill for the downstream beneficiation process2015年3月15日 For the grinding tests, a Loesche mill LM45 (table diameter 045 m) is used (Fig 2a) This pilot scale mill is a special development for ore grinding, which is reflected by several features The mill has four rollers, which are able to stress the particle bed with grinding pressures of up to 5000 kN/m 2Research of iron ore grinding in a verticalrollermill