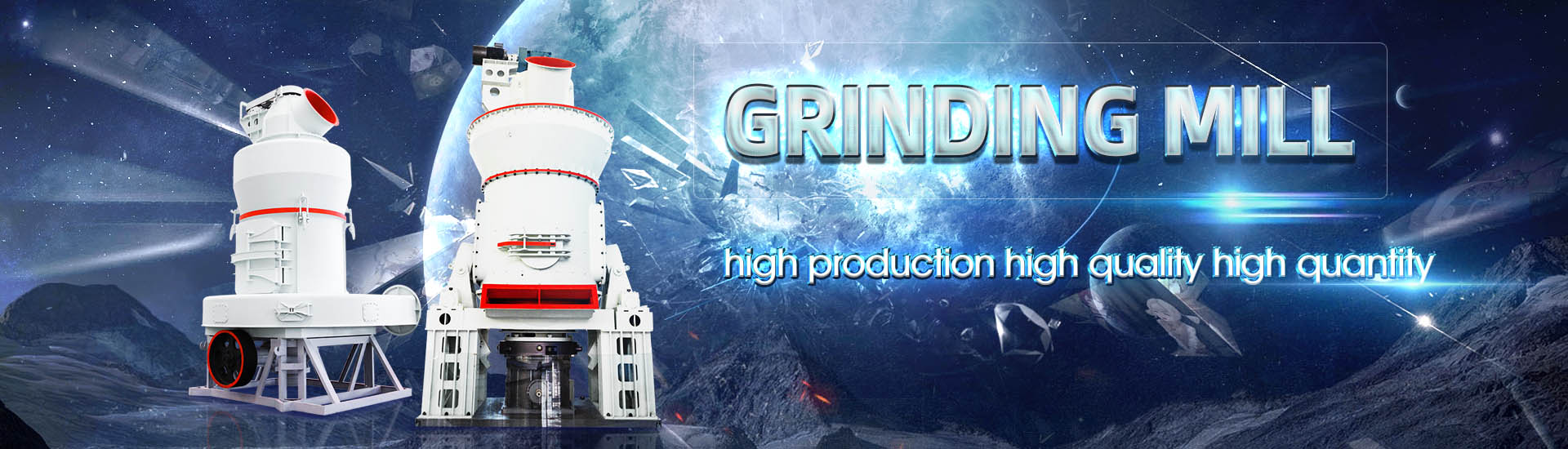
Steel slag deep processing process
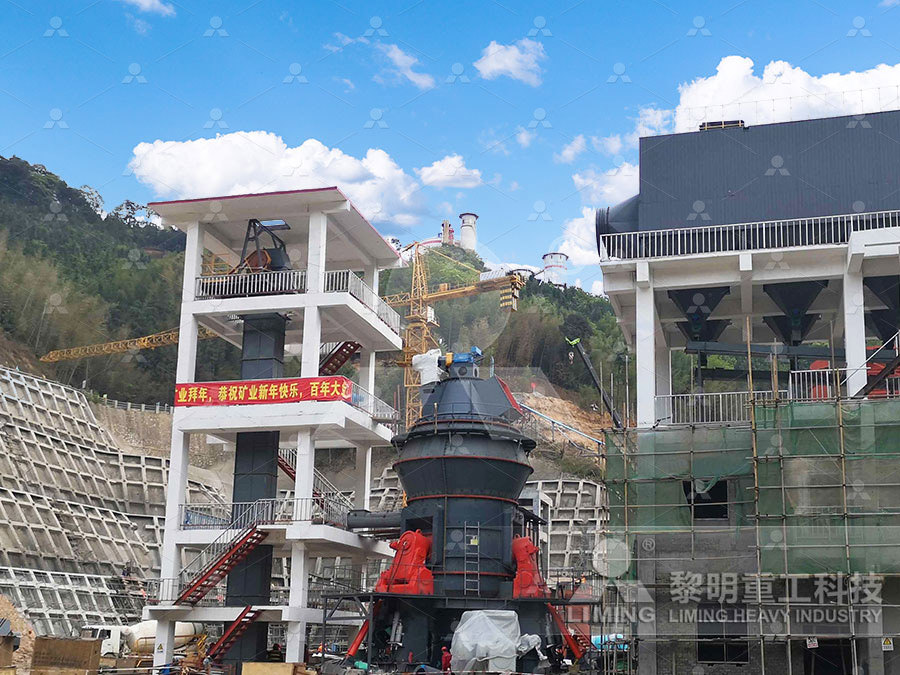
Steel slag in China: Treatment, recycling, and management
2018年8月1日 Steel slag after taping is treated first, but the slagtreatment process (airgranulated process, rotary cylinder process, layerpouring process, and selfdisintegrating 2024年8月19日 Many steel producers aim to avoid their CO 2 emissions by substituting the CO 2intensive blast furnace/basic oxygen furnace route by a gasbased direct reduced iron (DRI) The Steelmaking Transformation Process and Its Consequences for 2023年11月20日 As a protocol, the steel industries now follow a series of pretreatment processes of steel slag so that the recovery process of the metal will be effective Pretreatment of steel slag (such as quenching, crushing, and A Review on Environmental Concerns and 2004年5月14日 Steel slag is a byproduct from either the conversion of iron to steel in a basic oxygen furnace, or the melting of scrap to make steel in an electric arc furnace This paper Steel Slag—Its Production, Processing, Characteristics, and
.jpg)
Treatment of steel rolling sludge incineration slag via iron ore
21 小时之前 Steel rolling sludge, an oilcontaining waste generated during steel production, was difficult to manage Prolonged storage poses significant environmental and health hazards 2020年10月15日 The iron and steel industry is an energyintensive sector, generating large amounts of waste during the steelmaking process, such as CO 2, metallurgical slag, and wastewater It is promising that it is possible to Cotreatment of Waste From Steelmaking Processes: 2005年2月1日 Steelmakers have made attempts to reduce slag volumes in the individual unit processes and to strive towards slagless steelmaking by recycling slags internally A much improved understanding of(PDF) Industrial uses of slag The use and reuse of iron 2024年3月28日 To promote the resource utilization of steel slag and improve the production process of steel slag in steelmaking plants, this research studied the characteristics of three different processed steel slags from four steelmaking Research on the Properties of Steel Slag with Different
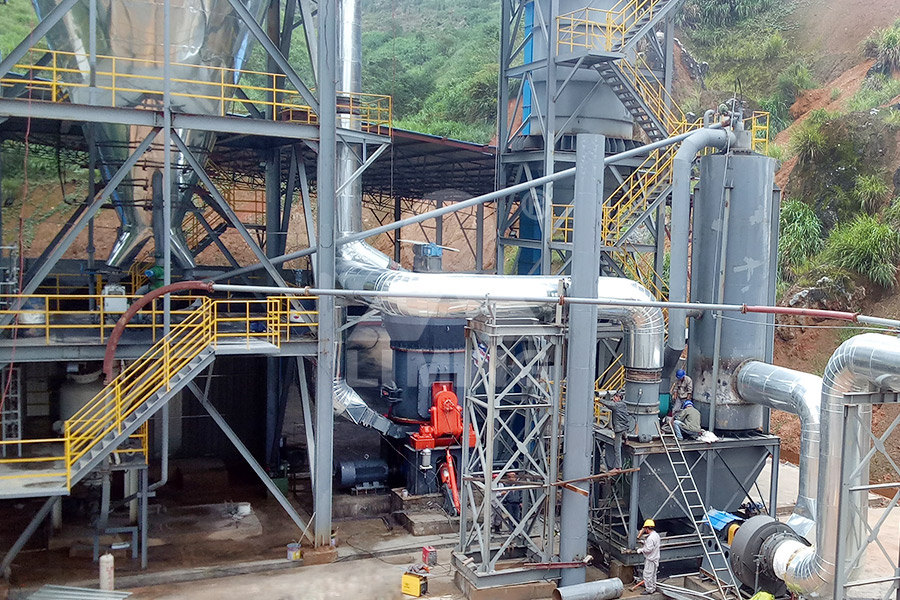
Basic Oxygen Steelmaking Slag: Formation, Reaction,
This article reviews the recent progress on the four important topics of BOS slags: 1) slag formation, ie, dissolution of lime in the BOS slag; 2) hightemperature phase transformation of BOS slags; 3) transient phenomena in BOS slags due 2023年11月15日 Moreover, in the view of the problems that highbasicity refining slag is usually needed for desulfurization of molten steel and lowbasicity refining slag is usually needed for plasticization of inclusions, Wang et al developed a ‘twostage basicity control’ refining method of Sikilled spring steel, which can realize the comprehensive control of desulfurization and oxide Modeling of LF refining process: a review Journal of Iron and Steel 2024年3月16日 In the wake of the era of big data, the techniques of deep learning have become an essential research direction in the machine learning field and are beginning to be applied in the steel industry The sintering process is an extremely complex industrial scene As the main process of the blast furnace ironmaking industry, it has great economic value and Application of deep learning in iron ore sintering process: a review2018年8月1日 After undergoing the layerpouring process and rotary cylinder process, steel slag has a poor stability, For example, the Steelphalt operation at Rotherham in Yorkshire, England, has been processing steel slag to produce road construction asphalts for more than 70 years (Evans et al, 2013)Steel slag in China: Treatment, recycling, and management
.jpg)
Slag Recycling and Metal Recovery MEKA
MEKA is designing and manufacturing customized steel slag processing and metal recovery plants for each projectspecific purposes Our portfolio; MEKA offers standalone machines, process solutions, turnkey plants, separation and sorting technology, and control and automation solutions perfectly tailored to individual requirements2024年1月23日 This study focused on how aging affected the properties of steel slag Steel slag was treated using hydrothermal aging and pressure steaming aging techniques to improve its bulk stability Physical and mechanical characteristics, alkalinity, and mineral constituents, as well as micromorphology of steel slag, were investigatedEffects of the Aging Treatment Process on the Properties of Steel Slag Ecofertec Slag Processing and Metal Recovery Plant ECOFERTEC is designing customized steel slag processing and metal recovery plants for each projectspecific purposes The newest technology ECOFERTEC slag processing plant enables the most costeffective way to remove steel from slag with 300 ton/h capacitySteel Slag Processing — EcofertecThe main challenge of the steel industry for the next decade is the steel production transformation process, starting in Europe The CO 2 intensive blast furnace/basic oxygen furnace (BOF) route will be substituted by a combination of Direct Reduced Iron (DRI), based on natural gas, later on “green” hydrogen, with an Electric Arc Furnace (EAF) or a Submerged Arc Furnace (SAF), The steel production transformation process in Europe: New slag
.jpg)
Steelmaking Slag an overview ScienceDirect Topics
Steelmaking slag, or steel slag, is a byproduct from the production of steel during the conversion of hot metal to crude steel in a basic oxygen furnace, or during the melting of scrap in an EAFThe slag is generated as a melt and is a complex solution of silicates and oxides that solidify upon cooling 11 Depending on the specific steel production process, three different types of steel Abstract The state of the art for the recovery of metals from steel industry byproducts using hydrometallurgical processes is reviewed The steel byproducts are different slags, dusts, and sludges from a blast furnace (BF), basic oxygen furnace (BOF), electric arc furnace (EAF), and sinter plant, as well as oily mill scale and pickling sludge The review highlights that dusts and Hydrometallurgical Processes for the Recovery of Metals from Steel 2023年11月17日 Many states use language similar to the North Carolina state statute: “Steel slag that is a product of the electric arc furnace steelmaking process; provided, that such steel slag is sold and distributed in the stream of commerce for consumption, use, or further processing into another desired commodity and is managed as an item of commercial value in a Electric Arc Furnace Steelmaking and Slag Formation, 1 Introduction The basic oxygen steelmaking (BOS) process produced over 70% of the global crude steel in 2018, [] generating 100 to 150 kg of slag (“BOS slag”) for every tonne of crude steel produced BOS slag, a product of hot metal Basic Oxygen Steelmaking Slag: Formation, Reaction,
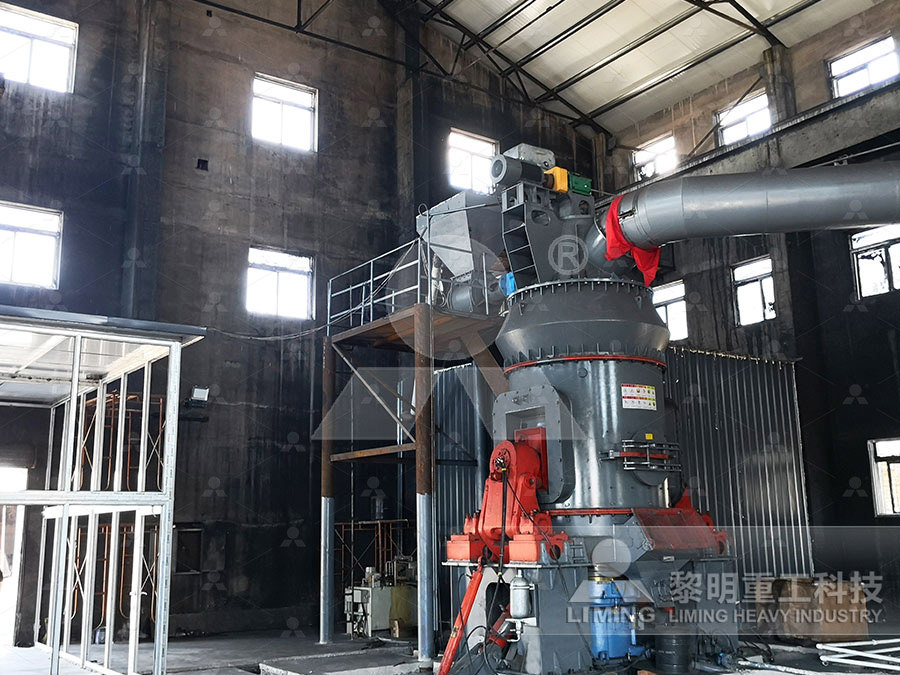
Fabrication of a Sulfur/Steel SlagBased Filter and Its
2024年2月27日 To solve the problems of deep nitrogen removal in wastewater treatment plants and the high value utilization of steel slag in the metallurgical industry, this work aims to prepare a sulfur/steel slagbased filter using the 2023年12月27日 Jaw crusher; It is suitable for processing large steel slag materials (feed particle size ≤ 1200mm) It uses the principle of squeeze crushing, combined with a deep Vshaped and dead zonefree crushing chamberSteel Slag Processing Plant Equipment Selection2024年3月1日 The direct carbonation of steel slag has emerged as a promising approach for carbon dioxide (CO 2) utilization and sequestration, holding potential for advancing sustainable steel productionDespite considerably high expectations for these cleaner upcycling pathways, their maturity level remains relatively low and largescale direct carbonation of steel slag is Review article Carbon dioxide sequestration through steel slag Ferrous metal production and ferrous slags George C Wang, in The Utilization of Slag in Civil Infrastructure Construction, 2016 24 Steelmaking processes and steel slag formation As seen in Fig 21, crude iron is refined in a BOF or an EAF to become crude steelIt may also undergo a second refining in a ladle furnace The BOF steelmaking process is currently the dominant Steelmaking Process an overview ScienceDirect Topics
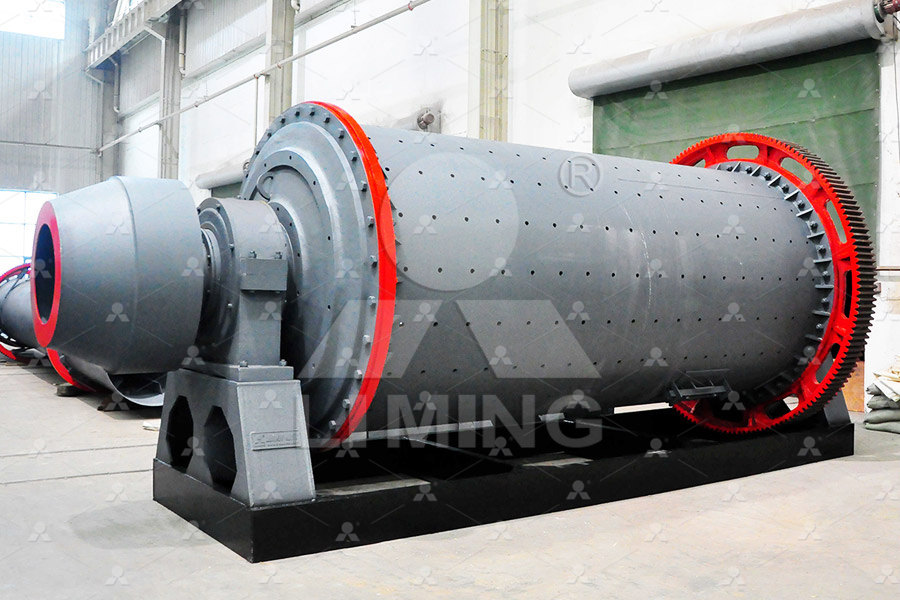
Desulphurization of Steel Metal World Insight
2021年4月7日 Reaction takes place between basic synthetic or refining slag (which is added to the empty ladle) and the liquid steel being tapped Energy of the falling steel stream causes intense mixing of the slag with the steel, during which sulphur is removed from the steel to slag phase But the amount of S removal is not that substantial 2Lime addition2011年10月27日 Under certain conditions this can invert to the γ form while cooling, with an expansion that shatters the surrounding material This process, known as “falling”, was common at some plants in the early years of the twentieth century and was found to make the slag unusable as an aggregate Above: A video of a 'falling' stainless steel slagBasics of slag production Article on the slag industry from Global SlagLinzDonawitz (LD) slag, a byproduct of steel manufacturing process, is rich in iron oxide, calcium oxide, silica, various macro, and micronutrients as well as varying degrees of heavy metals Flowchart of slag production in a modern steel plant2024年2月15日 The problem of steel slag could be solved by expanding the utilization ways of steel slag At present, steel slag has been used in the production of cement, the construction of urban roads and the production of fertilizer (Fronek et al, 2012; Jiang et al, 2018b; Shi and Qian, 2000; Wang and Cai, 2006)In developed countries, the utilization rate of steel slag is close to Vanadium extraction from steel slag: Generation, recycling and
.jpg)
Research on the Properties of Steel Slag with Different MDPI
2024年3月28日 To promote the resource utilization of steel slag and improve the production process of steel slag in steelmaking plants, this research studied the characteristics of three different processed steel slags from four steelmaking plants The physical and mechanical characteristics and volume stability of steel slags were analyzed through density, water The galvanizing process has its own builtin means of quality control because zinc will not react with an unclean steel surface Any failures or inadequacies in surface preparation will be immediately apparent when the steel is withdrawn What is the HDG Process? American Galvanizers Steel Slag BOF slag, commonly known as steel slag is another waste from Iron S teel Industry It has shown potential for use as a raw mix component up to 10% in the manufacture of cement clinker Steel slag can also replace granulated blast furnace slag up to 10% in the manufacture of Portland Slag Cement Steel slags are produced at steel SLAG IRON AND STEEL2015年9月8日 During the degassing process, five steel and top slag samples were taken, and their chemical compositions were analysed All steel samples were further analysed by scanning electron microscopyINFLUENCE OF VACUUM DEGASSING ON STEEL

Prediction of reoxidation behaviour of ultralow carbon steel
2020年6月10日 During the slag reoxidation process, when the oxygen in the steel is supersaturated and the slag is low in oxidation, it can easily form sticklike and dendritic shape inclusions of Al2O3 in steelSteel slag production quantity is huge in China With the increasingly strict environmental protection requirements in China, the modification of steel slag to make steel slag resource utilization becomes an urgent task This paper briefly described the characteristics of the steel slag and the problems of resource utilization The research progress of steel slag modification RESEARCH PROGRESS AND PROSPECT OF STEEL SLAG 2017年3月22日 Liquid steel at the end of the BOF process has a high oxygen content (typically 200–800 ppm Citation 4), which is unwanted for the following process steps Therefore most steel plants deoxidise the steel by adding Si, Mn and Al The oxides end up in the slagSulphur removal in ironmaking and oxygen steelmakingHot dip galvanizing is the process of coating iron or steel with a layer of zinc by immersing the metal in a bath of molten zinc at a temperature of around 450 °C (842 °F) During the process, a metallurgically bonded coating is formed which protects the steel from harsh environments, whether they be external []Galvanizing process
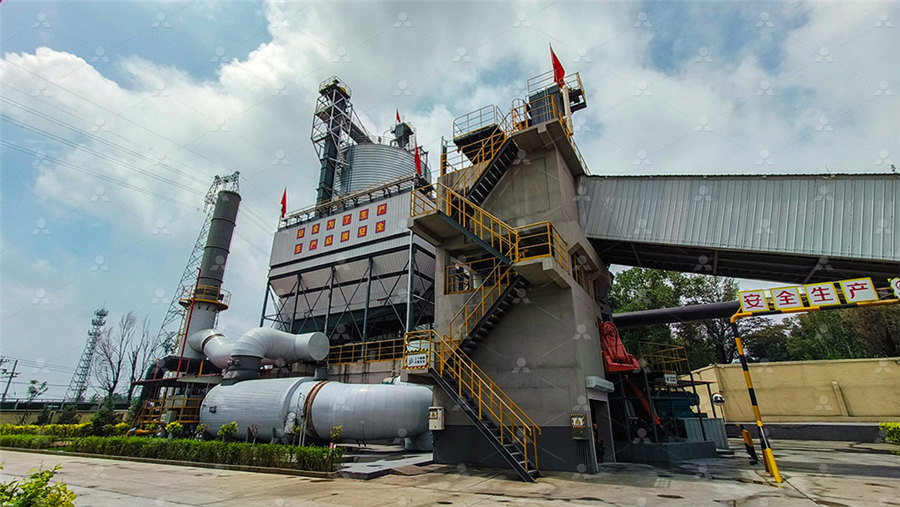
Why process metal slag at all? REMONDIS´ Lippe Plant
During the next step (the secondary metallurgy process), alloying elements are added to the liquid metal to meet the exact specifications required for the various areas of use A homogenous layer of slag forms on the surface of the hot, liquid high grade steel during the production process2024年3月12日 Leading Technology: We have advanced steel slag processing technology and equipment that can efficiently and environmentally recycle steel slag Rich Experience: With over 40 years of experience in steel slag processing and machinery manufacturing, we have provided professional solutions and services to numerous clients in the fieldSteel Slag Recycling: The Definitive Processing SolutionTailored services designed to embrace the entire slag management process, including safe and efficient slag pot carrying, cooling and maintenance Enabling further slag processing by excavating, removing and transporting slag from lagoons Pot Carrying TippingSlag Management Services Harsco Environmental2021年6月14日 Hightemperature molten steel slag is a large amount of industrial solid waste containing available heat energy and resources This paper introduces an efficient and comprehensive utilization process of hightemperature molten steel slag The waste heat energy in the hightemperature molten steel slag can be fully recovered through the threestage heat ThreeStage Method Energy–Mass Coupling HighEfficiency Utilization
.jpg)
The Effect of Removing HardtoGrind Minerals from Steel Slag
2023年8月22日 Steel slag (SS) is a byproduct of steelmaking process, accounting for 15–20 wt% of crude steel [1, 2]Statistics show that the global crude steel production in 2021 was about 19512 Mt, of which China’s production was 10328 Mt []However, the comprehensive utilization rate of SS in China is less than 30%, which is far from the utilization level of developed 2024年11月1日 In BOF slag and EAF carbon steel slag, the contents of Cr, Co, and Cd are lower, while the contents of P, Mn, and Fe are higher Notably, P is the primary factor limiting their application in steelmaking, whereas Mn and Fe are beneficial components in molten steel and do not hinder the steelmaking process [63]Recent research progress on recycling metallurgical waste slag 2021年5月10日 Due to the free lime in steel slag, they determined that samples formed of 100% steel slag cracked during the autoclaving process, the samples containing 80% steel slag and 20% silica powder had 23 MPa compressive strength, the samples having 80% steel slag and 20% fly ash had 53 MPa, and the samples having 50% steel slag and 50% cement had 762 Review Steel slag and its applications in cement and concrete At present, steel slag is primarily used as road bed material and civil construction material, and 30% of steel slag is used as road bed material Expansion characteristic is a big problem when steel slag is used as road bed material It is a phenomenon where the free lime contained in steel slag, although in a very small quantity, reacts withDevelopment of Steamaging Process for Steel Slag
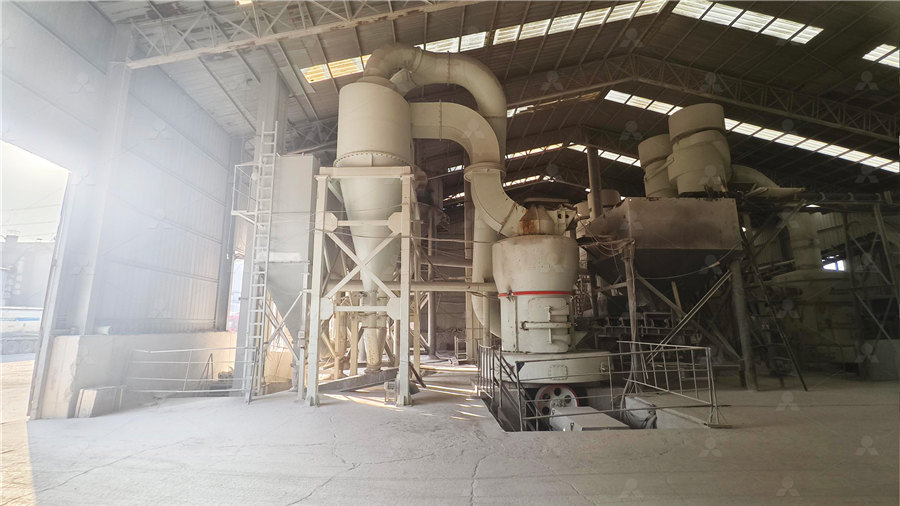
Iron and SteelMaking Process SpringerLink
2020年6月10日 231 Bessemer Process Today’s modern steelmaking practice had been initiated about 200 years ago, when Henry Bessemer patented his process in 1856, and the process was introduced as Bessemer process of steel making The Bessemer process follows bulk steel production in large quantities and made it suitable for various applications2021年8月10日 1 Introduction The basic oxygen steelmaking (BOS) process produced over 70% of the global crude steel in 2018, [] generating 100 to 150 kg of slag (“BOS slag”) for every tonne of crude steel produced BOS slag, a product of hot metal element (eg, Si, Mn, Fe, P) oxidation and flux (eg, lime, dolomite) dissolution, plays a critical role in the production of high Basic Oxygen Steelmaking Slag: Formation, Reaction, and 2005年5月31日 Request PDF Steel Slag — Its Production, Processing, Characteristics, and Cementitious Properties Steel slag is a byproduct from either the conversion of iron to steel in a basic oxygen Steel Slag — Its Production, Processing, Characteristics, and 2012年1月1日 The grindability index of steel slag is 07, in contrast with the value of 096 and 10 for blast furnae slag and standard sand respectively [4]The steel slag mainly consists of SiO 2 ǃCaOǃFe 2 O 3 ǃFeOǃAl 2 O 3 ǃMgOǃMnOǃP 2 O 5 [5]The chemical component of steel slag varies with the furnace type, steel grades and pretreatment methodAn Overview of Utilization of Steel Slag ScienceDirect
.jpg)
Thermodynamic modelling of liquid steel tapping process to
2024年9月9日 Liquid steelslag interaction, flux addition to slag, various metallic additions to steel and refractory dissolution to slag were taken into account in the model Multiple simulations were performed with varying amounts of carryover slag and composition of steel and slag of initial samples from the ladle furnace were equated with the predicted values from FactSage kinetic