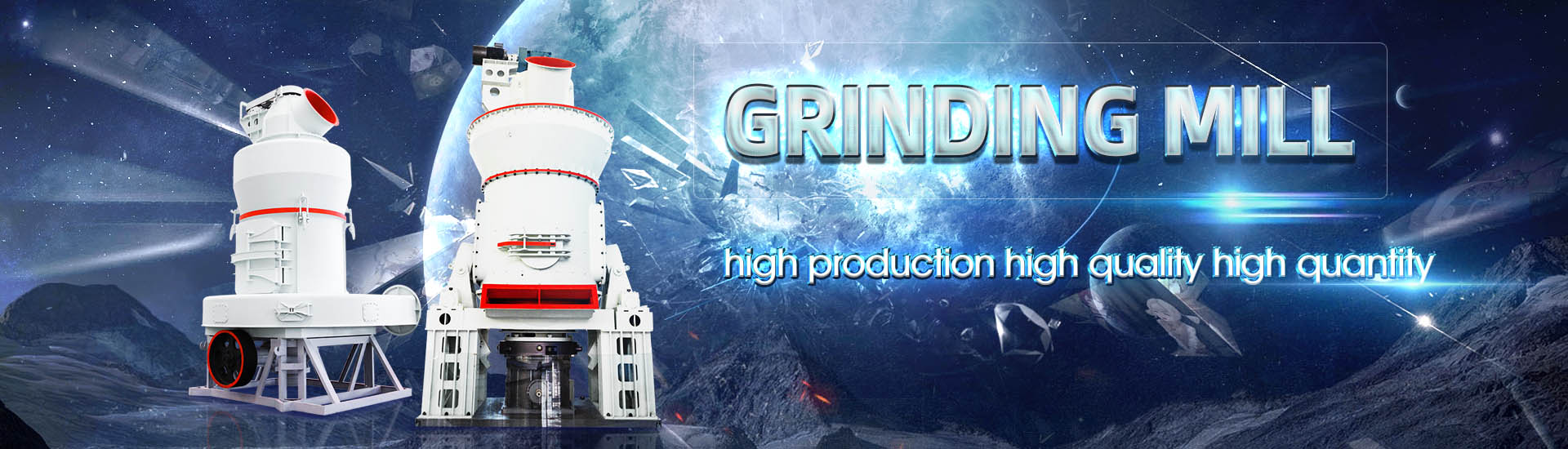
Coke powder making process flow text
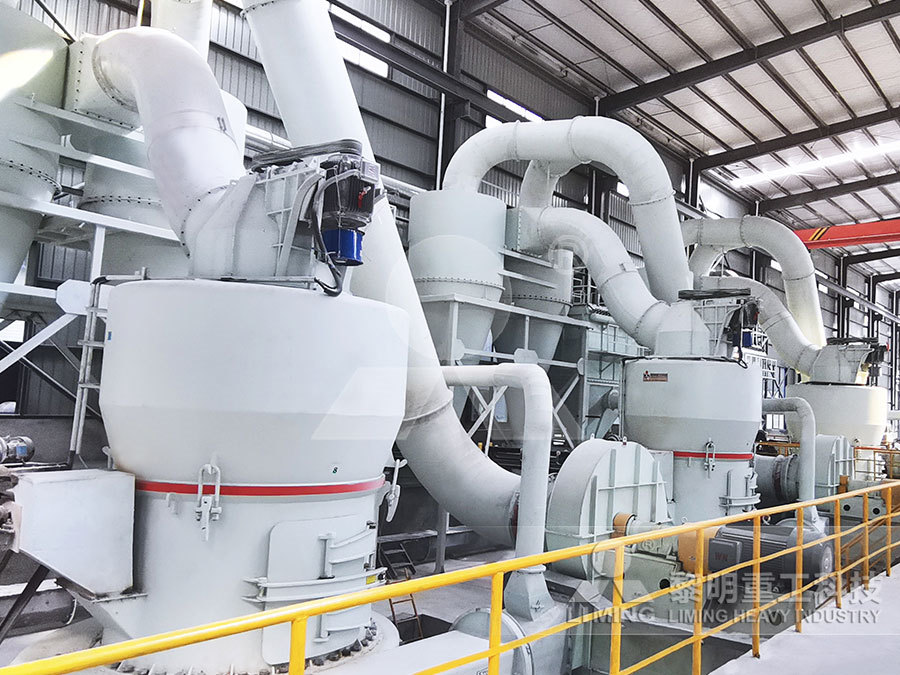
Coke making process flowsheet Download Scientific Diagram
Download scientific diagram Coke making process flowsheet from publication: 19th International Metallurgy and Materials Congress One of the most important factors affecting the cokeTo produce quality metallurgical coke, a hightemperature carbonization process is used Hightemperature carbonization, which takes place above 900°C (1650°F), involves chemical 122 Coke Productionprocess by constructing new coke ovens at Oita and Nagoya Works This paper explains the development of the SCOPE21 process, and reports the operation of Nippon Steel’s Technical Report UDC 662 741 SCOPE21 Cokemaking ProcessThe document discusses various aspects of the coke production process including coke oven design, charging procedures, coking reactions, temperature control, and byproduct recovery 2 Key aspects covered include the swelling 02 Cokemaking Process (54 Slides) PDF Coke (Fuel)

Lecture 32: Coke production National Institute of Technology,
Process flow sheet: Illustrated in Figure At first Bituminous coal is crushed and screened to a certain size Preheating of coal (at 150250 ̊C) is done to reduce coking time without loss of In this study, we studied the feasibility of preparing highquality needle coke from coal liquefaction pitch Nine types of blending pitch (coal liquefaction pitch and anthracene oil mixed withFlow diagram of the preparation process of needle cokeThe redhot coke extruded from the coke oven is cooled by spraying it with water The water used for cooling is vaporized and released into the atmosphere An issue with this conventional 3A5 Coke Dry Quenching Technology (CDQ) 一般財団法人 Specifically, the review introduces new research topics in Industry 50 about AI selfadaptive systems and processes in electronics, robotics and production management The paper proposes alsoThe process flow diagram of the analyzed industrial
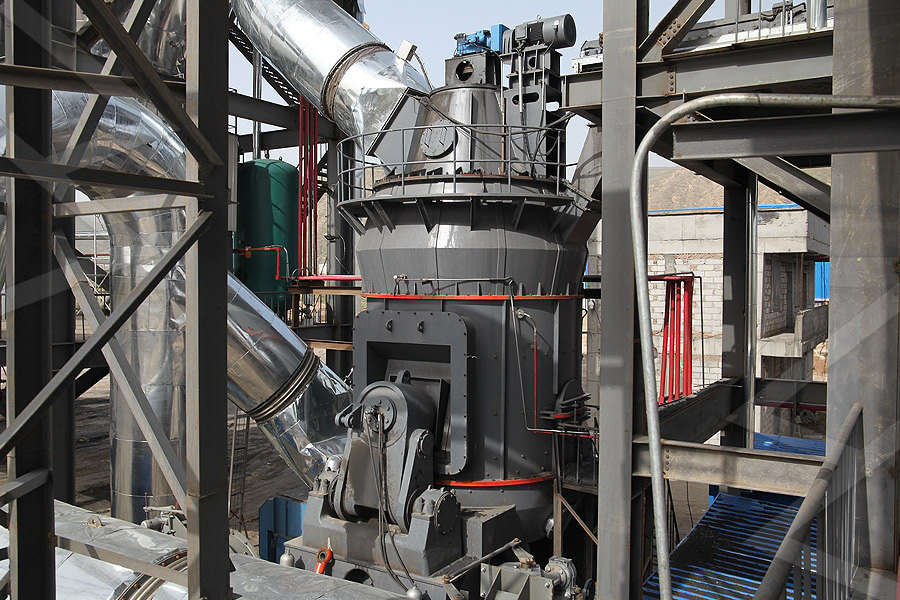
Industrial perspective of the cokemaking technologies
2019年1月1日 Solid particles entrained with COG during the carbonization process reported as quinoline insoluble particles (QI), and they are concentrated in the coal tar QI contains coal 2019年11月10日 Addition of coke powder improves the yield and strength of activated carbon (AC) Adding coke powder primarily inhibits micropores formation Coke powder increases the Activated carbon preparation with the addition of cokemaking by 2013年4月13日 Metallurgical Coke satyendra; April 13, 2013; 1 Comment ; BF coke, coke, Coke breeze, CRI, CSR, Drum test, Micum, Micum test, Nut coke,; Metallurgical Coke Metallurgical coke or ‘Met coke’ or ‘BF (blast furnace) Metallurgical Coke IspatGuru2011年5月1日 The ironmaking process including sintering, coke making and blast furnace (BF) accounts for approximately 90% of CO 2 output from an integrated BFBOF (basic oxygen steelmaking) steel plant [1, 2]Substitution of Biomass for Coal and Coke in
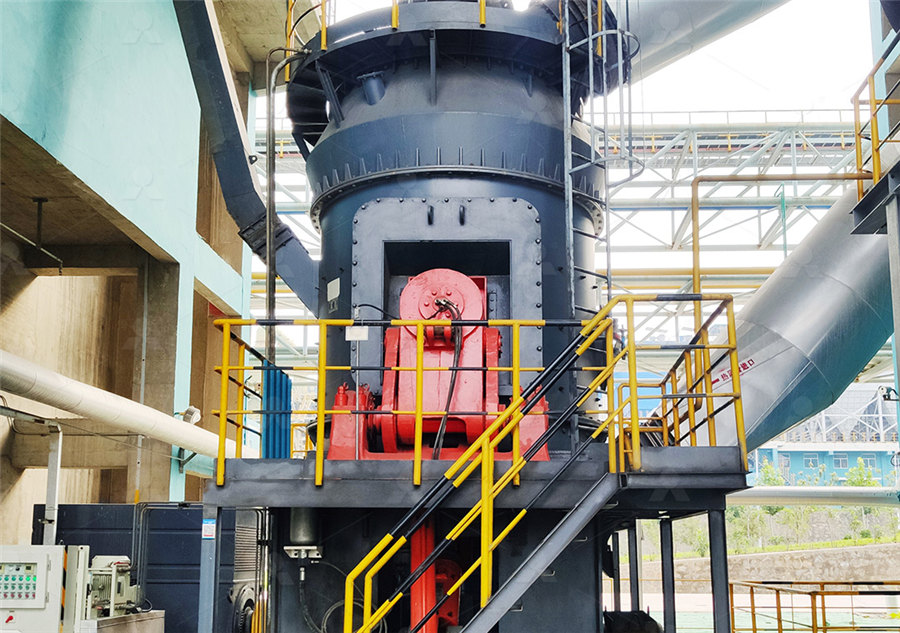
Activated carbon preparation with the addition of cokemaking
2019年11月10日 As a byproduct of cokemaking, the utilization of coke powder is a challenging issue for which rendered an extended service life by resistance to crush and wear during the transportation and regeneration process activation time of 90 min, nitrogen flow of 100 mLmin −1 and heating rate of 5 ℃min −1 The Download scientific diagram Process flow chart for jaggery powder preparation from publication: Review on Recent Advances in Value Addition of Jaggery based Products Jaggery is sugarcane Process flow chart for jaggery powder preparationDownload scientific diagram A simplified process flow chart for a steelmaking process with a coke oven and blast furnace from publication: Pathways for Increased Use and Refining of Biomass in A simplified process flow chart for a steelmaking process with a coke 2019年4月13日 For powder coke fuel fluidized combustion, operating oxygen (≤30%) and primary air rate (≤40%) were low and the average operating bed temperature was high (≥960 °C), which seriously affected the selfdesulfurization capacity of the powder coke fuel and led to an increase in SO 2 emission concentration in the operation of oxygen from high to low (such as Study on Powder Coke Combustion and Pollution Emission
.jpg)
Clean Preparation of Formed Coke from Semicoke by the
2023年7月17日 In order to address the low thermal efficiency of lowrank coal combustion and the accompanying serious environmental issues, formed coke was prepared using a carbonization consolidation method with lowrank coal semicoke The test for briquetting and carbonation consolidation conditions revealed that the optimal parameters were a briquetting pressure of 2024年2月21日 Coke quality prediction is always a difficult problem because of the correlation among the indexes of blending coal In this paper, the coal resource data, coal and coke quality data and coking process parameters of Masteel 763m coke oven coking production in recent two years are statistically analyzedCoke Quality Prediction Based on Blast Furnace Smelting Process 2022年1月6日 The coke reactivity index and coke strength after reaction are critical parameters for the efficient operation of a blast furnace Therefore, maintaining desired qualities of the produced coke as per coal blend chemistry and coke oven battery parameters is essential However, the coke reactivity index (CRI) and coke strength after reaction (CSR) vary from Variability in Metallurgical Coke Reactivity Index (CRI) and Coke 2013年4月1日 According to the characteristics of quench oil and coke powder, an experimental setup is designed with a hydrocyclone for a pilot test The relationships between structure size, flow rate Pilot Test on the Removal of Coke Powder from Quench Oil Using
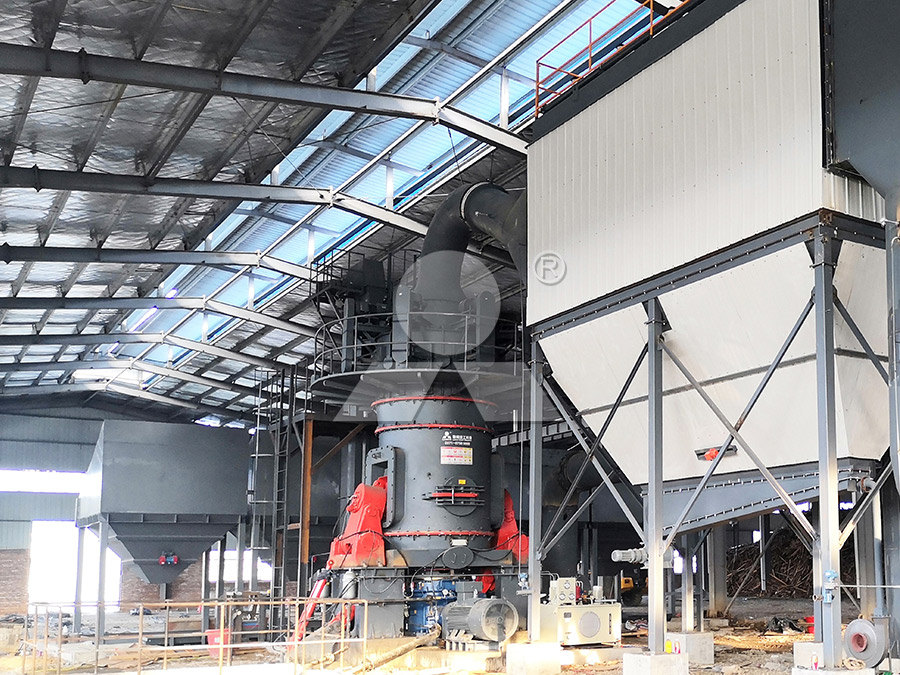
Numerical study of volatiles production, fluid flow and heat
2015年4月25日 The heat recovery stamp charge coke making process is quite complicated due to the evolved volatile matter during coking, is partially combusted in oven crown and sole flue in a controlled manner 2017年7月6日 Carbon anodes used in Hall–Héroult electrolysis cells are involved in both electrical and chemical processes of the cell Electrical resistivity of anodes depends on electrical properties of its constituents, of which carbon coke aggregates are the most prevalent Electrical resistivity of coke aggregates is usually characterized according to the ISO 10143 Electrical Resistivity Measurement of Petroleum Coke Powder2018年1月31日 Introduction A sintering process not only consumes a large amount of fossil fuels, but also releases a great number of contaminants [1] Coke, as one of a raw material, is added into the raw mixture in the second proportioning phase of a sintering process so as to provide energy for burning to cause physical changes and chemical reactionsOptimization of coke ratio for the second proportioning phase in This process consists essentially of an externally heated vertical retort In this process, coke briquettes (60–70% calcine and 30–40% coal) fed from the retort top flow downward to the reaction zone where the reduction of zinc oxide by carbon takes place at 1523–1573 K (1250–1300 ᵒC)Metallurgical Coke an overview ScienceDirect Topics
.jpg)
A synergy model of material and energy flow analysis for the
2021年1月1日 A synergy model of material and energy flow analysis for the calcination process of green petroleum coke in rotary kiln January 2021 Thermal Science 26(00):188年2月16日 Sintering is a thermal agglomeration process that is applied to a mixture of iron ore fines, recycled ironmaking products, fluxes, slagforming agents and solid fuel (coke)(PDF) Iron Ore Sintering: Process ResearchGatesion Since the largest Carbon consumer is an iron making process in steel works, the engineers are making effort to reduce the carbon consumption Coal and coke consumed in a blast furnace plays roles as the heat source, reducing agent and spacer Theoretically speaking, the heat source and reducing agent can be substituted by electricity andStress Field and Solid Flow Analysis of Coke Packed Bed in Blast 2002年5月1日 Request fulltext PDF Figure 21 below shows the coke making process using a The wPET/dcoal composite was synthesized via a cocarbonization process at 700 °C under a constant flow of Coal for metallurgical coke production: Predictions of coke
.jpg)
The Role of Coke in Steel Making Process Cabaro Group
2024年3月25日 These chemical interactions underscore coke's integral role, as they define the inherent qualities of the final steel product—such as tensile strength, hardness, and ductility—emphasizing its indispensability in the traditional steel making process Quality and Properties of Coke for Efficient Steel Making The performance of coke in the 2019年11月14日 Coking is a complex process It features a large time constant, strong nonlinearities, and timevarying characteristics To achieve good control performance, it is important to obtain a precise COT in a realtime fashion; but this is difficult owing to restrictions imposed by the structure of a cokeoven and operating costsIntelligent Optimization and Control of Coking ProcessRequest PDF On Aug 1, 2024, Caiping Hu and others published Oxalate enhanced reduction of Cr(VI) by cokemaking byproductCoke powder Find, read and cite all the research you need on ResearchGateOxalate enhanced reduction of Cr(VI) by cokemaking byproductCoke powderDownload scientific diagram Process flow chart for making buttermilk from publication: Development of functional buttermilk by soluble fibre fortification Buttermilk has a potential to become Process flow chart for making buttermilk
.jpg)
Preparation and electrochemical properties of coke powder
2012年7月20日 Coke powder activated carbons (CPACs) were prepared using coke powder as raw materials The asprepared CPACs were characterized by energy dispersive spectrometer, scanning electron microscopy, Xray photoelectron spectroscopy and Xray diffraction The BET surface area and porous properties of CPACs were evaluated by nitrogen adsorption at 77 K sion Since the largest Carbon consumer is an iron making process in steel works, the engineers are making effort to reduce the carbon consumption Coal and coke consumed in a blast furnace plays roles as the heat source, reducing agent and spacer Theoretically speaking, the heat source and reducing agent can be substituted by electricity andStress Field and Solid Flow Analysis of Coke Packed Bed in Blast coke is pushed out of the oven in less than 1 minute, through the coke guide and into a quench car After the coke is pushed from the oven, the doors are cleaned and repositioned The oven is then ready to receive another charge of coal The quench car carrying the hot coke moves along the battery tracks to a quench tower where122 Coke Production2022年11月15日 As a byproduct/waste from coke production, about 40 Mt of metallurgical coke powder (CP) was generated in China annually The utilization of coke powder is conducive to the environmental and economic sustainability [14]Generally, coke powder has an average diameter less than 5 mm, and similar physical and chemical properties to coke such as high carbon Coke powder improving the performance of desulfurized
.jpg)
Activation mechanisms on potassium hydroxide enhanced
2020年1月1日 In this study, effects of the KOH addition on the microstructures development in coke powder during its activation process were investigated The obtained AC products were characterized using the specific surface area and pore structure analyzer, Xray powder diffractometer (XRD), scanning electron microscope (SEM), highresolution transmission Download scientific diagram Coke Dry Cooling Plant Flow Process from publication: Advances in Green Steel Making Technology A Review The aim of this research work is to increase the quality Coke Dry Cooling Plant Flow Process ResearchGateDownload scientific diagram Flow chart of powder metallurgy process from publication: Effect of Powder Metallurgy Process and its Parameters on the Mechanical and Electrical Properties of Copper Flow chart of powder metallurgy process ResearchGatelowering of the coke:iron ratio used in the blast furnace (e g, increased use of pulverized coal injection) There were 18 coke plants operating in the U S in 2007 1221 Process Description19, 16, 194 Most coke is produced in the U S using the “byproduct” process, and three plants used a “nonrecovery” process in 2007122 Coke Production

Recirculating coking byproducts and waste for costeffective
2021年1月20日 Therefore, the idea that utilization byproducts/waste for AC production came up (Fig 2), using byproducts and wastes such as coke powder, coal tar pitch, benzene residue, etc from cokemaking as raw materials for AC production which further treat wastewater and flue gas from cokemaking The process not only could utilize the cokemaking by 2019年2月13日 Coke breeze is the main heat source in sintering process Its combustion yields enough amounts of heat which melts the sinter mix One of the factors that significantly affect the course of coke breeze combustion is its grain size [1,2,3]It is known that finegrained coke reduces permeability of the sinter mix and the use of coke breeze with particle size below 1 Effects of Particle Size of Coke on Iron Ore Sintering Process2021年6月1日 Activated coke can be classified into molding and powder types Columnshaped activated coke (diameter of 5−9 mm) are often used, but they have some disadvantages, such as low utilization efficiency of inner surfaces, high internal diffusion resistance, complex manufacturing process These disadvantages restrict its applicationActivated coke preparation by physical activation of coal and PDF On Aug 1, 2019, Kun Shen and others published Modeling and Simulation of Carbonization Chamber Heat Transfer Process in Coke Oven Find, read and cite all the research you need on ResearchGateModeling and Simulation of Carbonization Chamber Heat Transfer Process
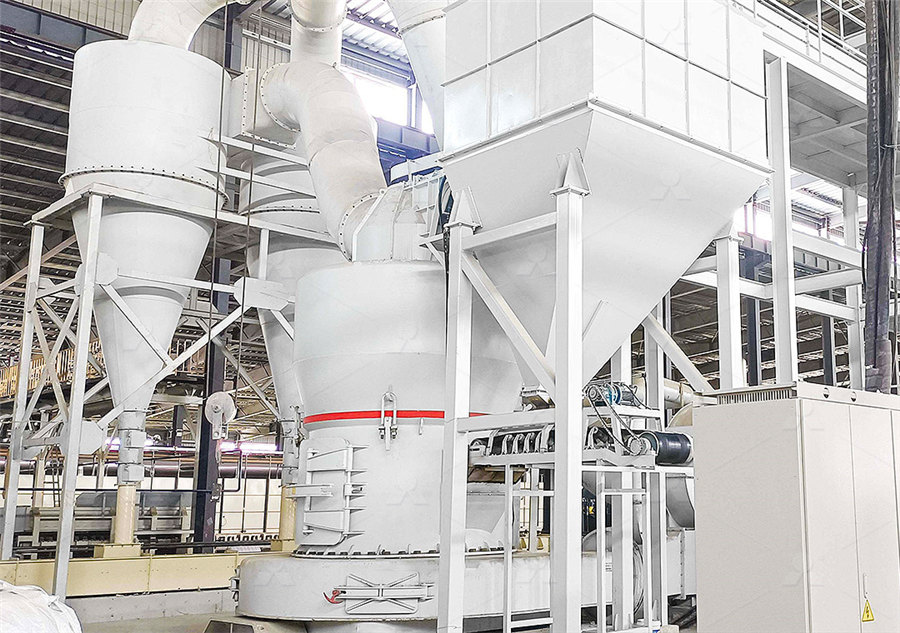
Optimum nut coke for the iron making blast furnaces
2016年6月15日 Cokeore mixed charging (COMC) can greatly improve the permeability of the softeningmelting (SM) or cohesive layer and enhance the reduction of Fe, Si, Mn, Ti, and V within it2022年12月15日 A significant amount of CO2 gas is emitted from blast furnaces in ironmaking processes because large amounts of coke and pulverized coal are consumed as the reducing agent and heat sourcePossibility and Process of the Use of Upgraded Coal and Coke 2020年1月1日 Reactor structure and process flow sheet of bluecoke production technologies described also named as nonrecovery ovens and burned the volatiles completely in the burning galleries to provide heat for the cokemaking process Powder Technol, 326 (2018), pp 101113 View PDF View article View in Scopus Google ScholarBluecoke production technology and the current stateoftheart 2023年2月28日 Optimizing coal blending is important for highquality development of coking industries, among which deep understanding of relationships between coal characteristics and coke quality is critical This work selected four typical coals from Shanxi Province in China to investigate influences of their structures and properties on coke quality Although these Study on Relationships between Coal Microstructure and Coke
.jpg)
Flow diagramPreparation of powder coating ResearchGate
Download scientific diagram Flow diagramPreparation of powder coating from publication: Ultrasonic SensorsAssisted Corrosion Studies on Surface Coated AlSi9Cu3 Alloy Die Castings A novel 2024年3月19日 Abstract The hot strength and mechanical strength of metallurgical coke are the critical parameters for efficient blast furnace operation Therefore, producing the desired qualities of coke like coke strength after reaction, coke reactivity index, and coke M10/M40 is essential for optimizing the cost and productivity of hot metal Hence, the intrinsic property of coal is LowCost Ironmaking: Metallurgical Coal Prospective Coke and