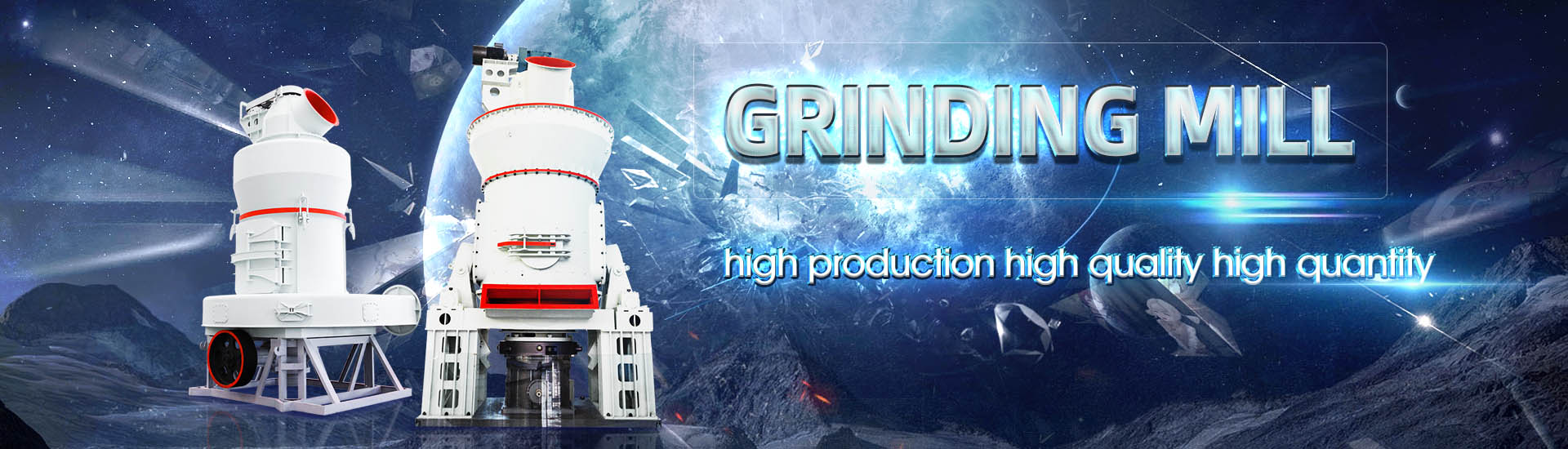
The efficiency of grinding mill to crush concrete mcnqbycom
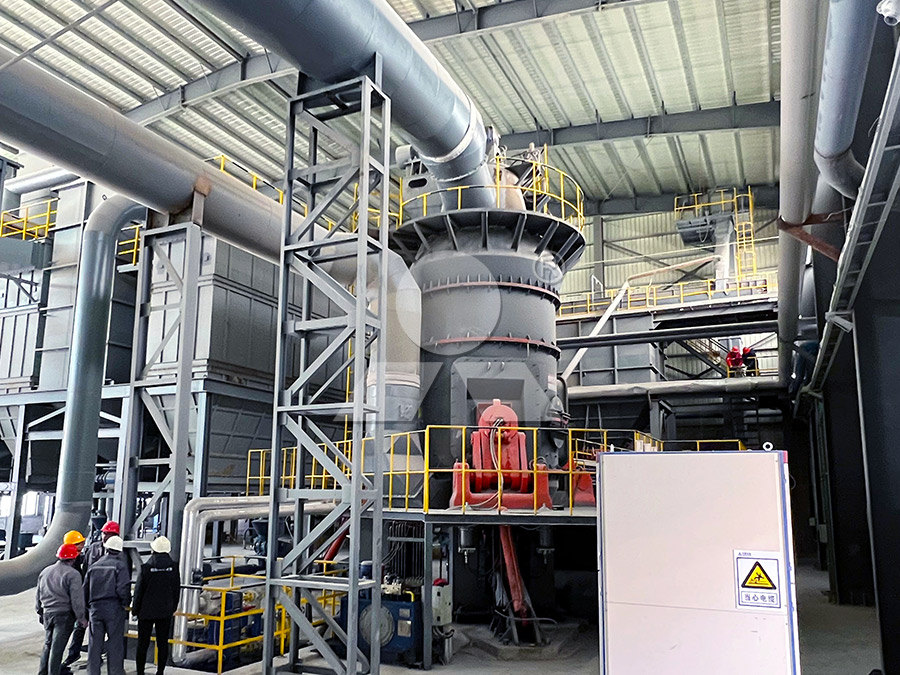
Effect of different parameters on grinding efficiency
2016年11月22日 The grinding efficiency is analysed by considering the rubbing, ploughing and cutting of a singlegrit grinding By analysing the features of 2018年7月1日 This study aimed at optimizing both the energy efficiency and the quality of the end product by modifying the existing flowsheet of the cement grinding circuit As a general Energy and cement quality optimization of a cement grinding circuit2023年6月30日 This article presents a systematic review of the task of improving the energy efficiency of crushing units This is achieved by studying modelling methods and results, the Modeling and Improving the Efficiency of Crushing Equipment2012年5月1日 Energy efficiency of a ball mill depends on a number of factors such as ball filling ratio, the mill length/diameter ratio, size composition of the ball charge, circulation ratio, An industrial comparative study of cement clinker grinding
.jpg)
(PDF) The improvement of mill throughput using Barmac
2007年1月1日 Recent pilot plant studies conducted at Metso Minerals show that significant clinker size reduction occurs in Barmac VSI crushers, which can increase the cement mill 2016年10月5日 This paper presents results regarding the grinding behaviour of two batches of material (clinker) in a ball mill with its own twostep grinding process: the first one with a ball EnergyEfficient Technologies in Cement GrindingOptimization addresses the grinding process, maintenance and product quality The objective is to achieve a more efficient operation and increase the production rate as well as improve the run OPTIMIZATION OF CEMENT GRINDING OPERATION IN BALL MILLS2023年5月3日 In this paper, the specific energy consumption (SEC) and related emissions of a real scale cement factory currently running in Türkiye have been decreased by investigating A comprehensive investigation of a grinding unit to reduce energy
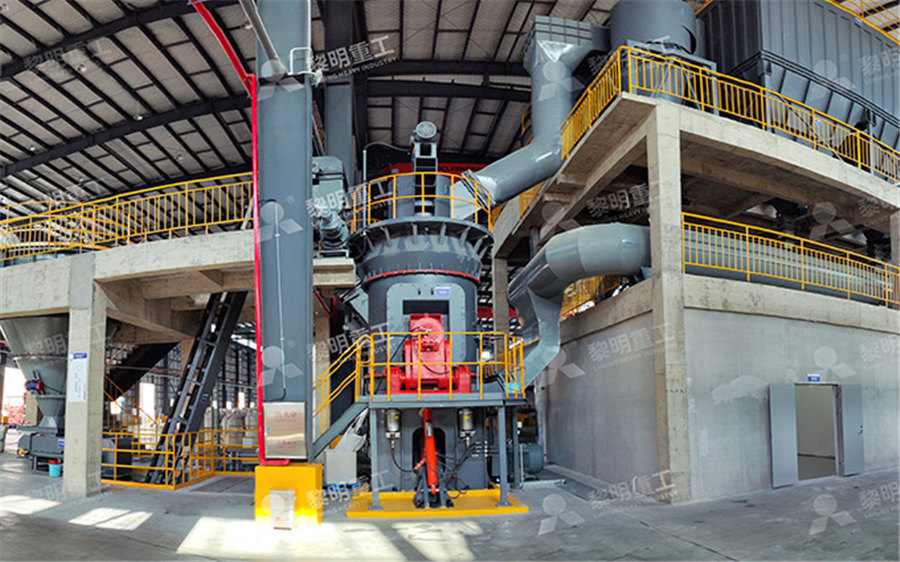
Improved cement quality and grinding efficiency by means of
2009年5月15日 Based on a population balance principle and stochastic representation of the particle movement within the grinding system, the Markov chain model for the circuit consisting 2022年1月30日 The Morrell method for predicting the specific energy consumption of conventional crushing, High Pressure Grinding Rolls (HPGRs), and tumbling mill equipment is TheMorrellMethodtoDeterminetheEfficiencyofIndustrial Condition in one of the grinding chambers of the mill Results of Optimization The graphical analysis presented in Figure 2 represents progress of grinding along the length of the mill after optimizing the grinding process rogress of grinding is clearly visible in Desired p the graphs Figure 2: Analysis of longitudinal samplesOPTIMIZATION OF CEMENT GRINDING OPERATION IN BALL MILLS2023年6月30日 and grinding rocks into thermal energy has not yet been completely explored [57] Further research is also required for methods of or e pretreatment in order to increase the energy efficiency of Modeling and Improving the Efficiency of Crushing
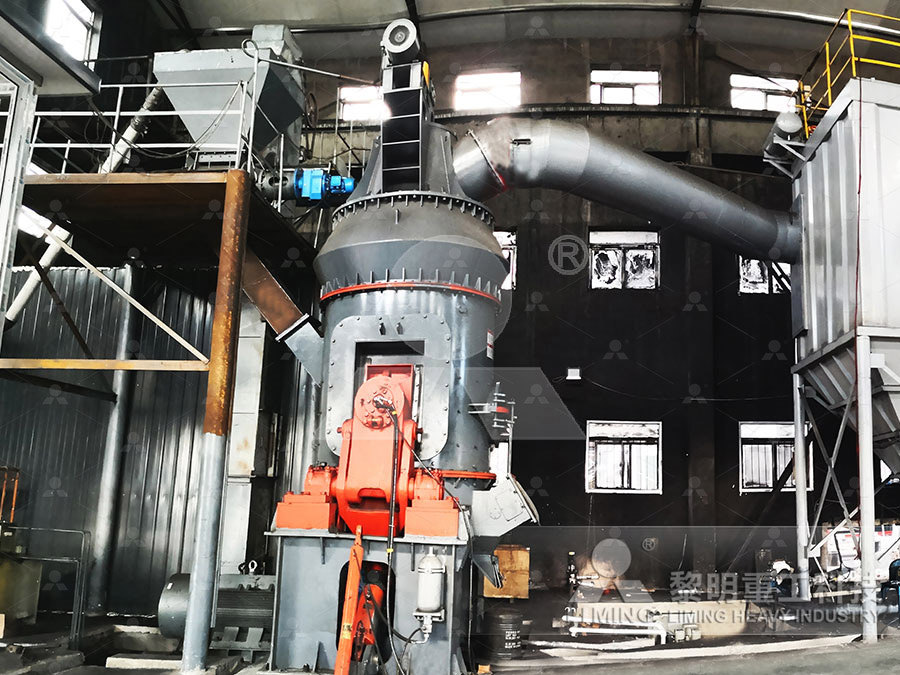
Understanding the operation of grinding mills in the mining and
2 Media andliner Wear: The condition of the grinding media and liners affects the mill's efficiency Wear and tear can lead to a decrease in ball size and a corresponding decrease in mill performance 3 Speed and Load: The speed at which the mill rotates and the load of ore being processed influence the grinding efficiencyThe Raymond mill is a versatile and reliable grinding machine, suitable for producing fine powders for a wide range of industrial applications Its efficiency, ease of maintenance, and ability to handle various materials make it a valuable asset in many industries [Introduction]: Raymond Mill has a strong performance of becoming a complete set with a production system Raymond Mill TAYMACHINERY2023年5月19日 Did you know that 29% of plants spend 5 to 10% of their annual budget on maintenance, and 44% spend more than 40 hours a week performing maintenance? Considering this, crusher and mill efficiency must be one of the focal points of your business Crusher and mill efficiency measures the ability to crush, grind, and convert raw material into a finished productTactics for Optimizing Crusher and Mill Efficiency: A Guide for2018年4月20日 The first two Grinding Efficiency Measurement examples are given to show how to calculate Wio and Wioc for single stage ball mills Figure 1 The first example is a comparison of two parallel mills from a daily operating report Mill How to Measure Grinding Efficiency 911Metallurgist
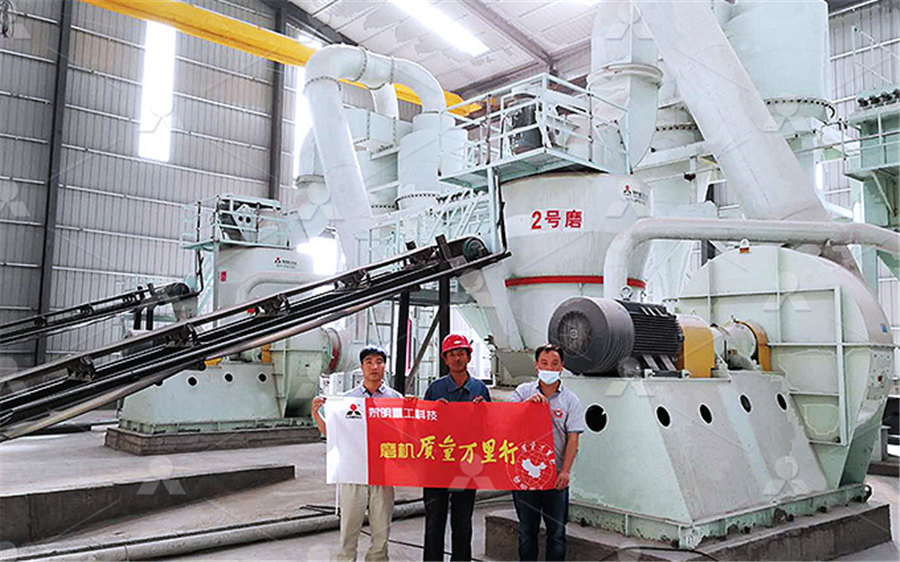
The Evolution and Importance of Grinding Mills in Modern Industry
2023年3月15日 Energy Efficiency: Advances in grinding mill technology have led to the development of energyefficient machines that can perform the same tasks with lower energy consumption, minimizing costs and environmental impact Conclusion Grinding mills have come a long way since their humble beginnings as primitive toolsStep#2 More crushing and less grinding to reduce the feed size into mill Step#3 Reasonable filling rate of steel ball Step#4 Reasonable size and proportion of steel ball Step#5 Refill steel ball accurately Step#6 Appropriate grinding density Step#7 Optimize the grinding process Step#8 Improve the classifying efficiency Step#910 Ways to Improve the Grinding Efficiency of Your Ball Mill2020年10月9日 PDF As one of the machines widely used in mining, a semiautogenous grinding (SAG) mill can significantly improve the roughing efficiency of rock But Find, read and cite all the research Operation Analysis of a SAG Mill under Different Conditions Based on 2016年1月1日 For open circuit grinding [34,35], there is no disagreement with the calculation of the circulating load and classification efficiency, both of which 2 can be characterized relatively accurately(PDF) Analysis of the efficiency of the grinding process in closed
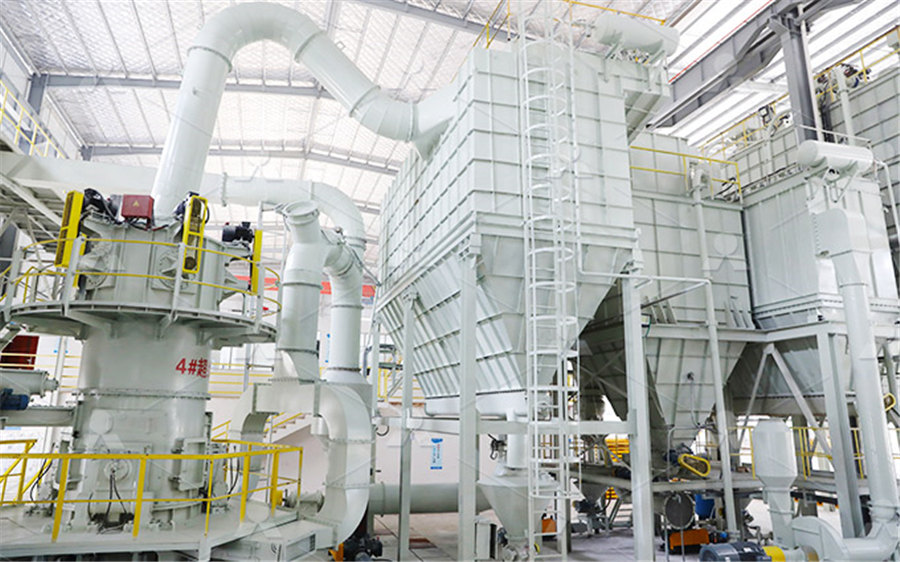
Analysis of process of grinding efficiency in ball and rod mills
2018年9月26日 The aim of the research was to evaluate the efficiency of grinding in a drum mill dependably on the grinding media used (balls, rods) for various feed parameters ie particle size distribution As of 2019, Shibang Industry and its affiliated companies have 5 advanced mining machine production bases and a production base in Xiuwu, Jiaozuo, Henan, which is under construction, with a total production area of 1,200,000 Stone Crushers, Mill and Grinding2023年8月27日 How to crush concrete into gravel at home? If you have concrete in your home that needs to be removed, you have a potential fortune on your hands I feel that crushing concrete into gravel at home is a challenging How to crush concrete into gravel – simple 2023年1月1日 Grinding aids are materials that are added to cement mixtures to improve the characteristics of the cement or increase the efficiency of the milling systems or both in the clinker grinding (finish EFFECTS OF VARIOUS GRINDING AIDS DOSAGE ON COMMINUTION EFFICIENCY
.jpg)
(PDF) The Effects of Blasting on Crushing and Grinding Efficiency
2003年1月1日 This study aimed to investigate the blasting efficiency on different geological units in the blasting area using WipFrag fragmentation analyses and to suggest ways to increase of blasting efficiencyin combination with a ball mill for cement grinding applications and as finished product grinding units, as well as raw ingredient grinding equipment in mineral applications This paper will focus on the ball mill grinding process, its tools and optimisation possibilities (see Figure 1) The ball mill comminution process has a high electricalBALL MILLS Ball mill optimisation Holzinger Consulting2023年11月6日 Grinding aids (GAs) are polar chemicals introduced in cement mills in either liquid or powder form to improve on mill grindability efficiency(PDF) Review of the Effect of Grinding Aids and Admixtures on One way to calculate a ball mill's grinding efficiency is to divide its total static horsepower (TSH) by its total theoretical tonnage (TPT) This number can then be used to compare different types of mills A TSH of 10 hp/tonne is considered to be very efficient, Grinding efficiency of ball mill calculating equation
.jpg)
Improving the efficiency of the material grinding process
2020年10月27日 It was found that the grinding systems of the partitioned grinding process with pregrinding in a pressroll grinder showed the greatest efficiency from their use2023年8月23日 The grinding process involves passing the clinker and additives through the rotating drum of the ball mill, where the grinding media crush and grind the clinker into a fine powder The specific surface area of the resulting cement particles is carefully controlled to ensure proper setting and strength development when the cement is mixed with waterWhat Are the Parts of a Cement Mills? Cement Ball Mill 2024年7月17日 Jaw crushers use the compressive and bending action of a fixed jaw plate and a movable jaw plate to crush materials of various hardnesses When the two jaw plates come together, the material is crushed; when the Types of Crushers: Choosing the Right One for Each routine Free download as PDF File (pdf), Text File (txt) or read online for free The document provides instructions for conducting a mill crash stop inspection The key steps include: 1) Stopping the entire circuit at once to avoid distorting How To Do A Mill Crash Stop Inspection: Grinding
.jpg)
CuttingEdge Grinding Solutions Indian Cement Review
2023年8月21日 ICR looks at the inner workings of grinding mills in the cement industry to understand the technological advancements that are reshaping the landscape against the foreground of sustainability Innovations to enhance the 2015年10月23日 In this chapter an introduction of widely applied energyefficient grinding technologies in cement grinding and description of the operating principles of the related equipments and comparisons over each other in terms of grinding efficiency, specific energy consumption, production capacity and cement quality are given A case study performed on a EnergyEfficient Technologies in Cement Grinding IntechOpen2002年11月1日 Unfortunately, the energy efficiency is extremely low in mining operations For instance, the energy efficiency is about 10% in percussive rock drilling (Carrol 1985), 35% in rock crushing The energy efficiency of ball milling in comminutionquently the cost of grinding in a mill can contribute significantly to the overall working costs of the recovery process Naturally one would like to know whether or not the grinding process is the most efficient way in which energy can be utilised to produce a material of fine particle size Traditionally, the absolute efficiency of a comminutionThe determination of the efficiency of the milling process
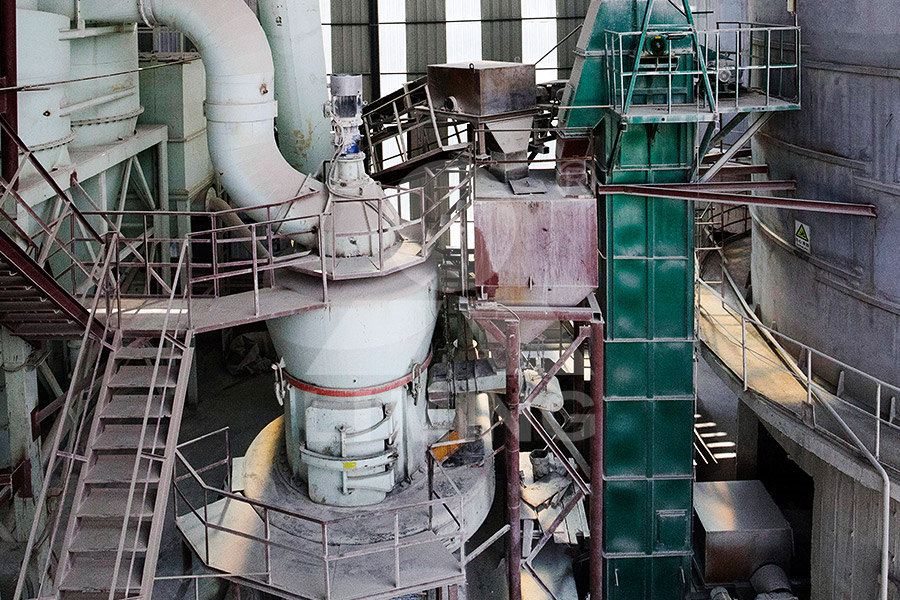
Ball Mill Success: A StepbyStep Guide to Choosing the Right Grinding
2024年8月8日 The strategic selection of grinding media is crucial for maximizing the efficiency and effectiveness of ball milling operations As illustrated through various considerations and realworld examples, the right choice of grinding media can dramatically influence the quality of the final product, operational costs, and overall process successFIGURE 4 Particle size distributions of collected samples (Survey 2) Bond work indices and breakage characteristics under compression were determinedPerformance Evaluation of Vertical Roller Mill in Cement Grinding2020年7月1日 Grinding processes in cement production technology are quite energyintensive The mechanism of action of surfactants on the course of the clinker grinding process has not been fully studiedInfluence of Clinker Microstructure on Grinding Efficiency in 2023年8月22日 Steel slag (SS) is a byproduct of steelmaking process, accounting for 15–20 wt% of crude steel [1, 2]Statistics show that the global crude steel production in 2021 was about 19512 Mt, of which China’s production was 10328 Mt []However, the comprehensive utilization rate of SS in China is less than 30%, which is far from the utilization level of developed The Effect of Removing HardtoGrind Minerals from Steel Slag on
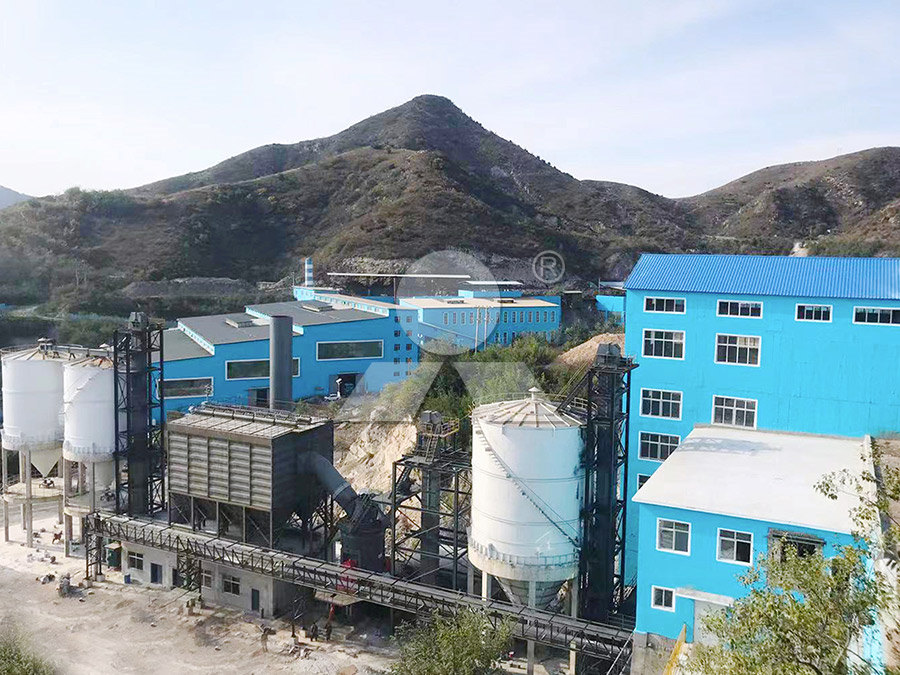
Effects of Operating Parameters On The Efficiency of
The document discusses the effects of operating parameters on the efficiency of dry stirred milling Stirred media mills can be operated either vertically or horizontally, with horizontal configuration allowing for higher media fillings, 2017年5月19日 Cement industry is characterized by sizeable energy demand which accounts for about 110kWh (375 thm) per ton of cement in modern plants Industry impacts heavily also on CO2 emissionsOverview of cement grinding: fundamentals, 2024年3月28日 By evaluating the features, applications, and technical specifications of the Soil Mill DP50, Disc Mill DP100, and Vibratory Disc Mill VM3, you can make an informed decision and choose the most appropriate disc mill Disc Mills: Important Tools for Efficient Sample 2024年6月14日 The grinding process plays a crucial role in industry, allowing for the reduction of particle sizes of raw materials and substances to the required fineness—either as a finished product or for further technological processes The high demand for micro and nanopowders or suspensions is associated with the high energy consumption of the milling process Therefore, The Influence of the Grinding Media Diameter on Grinding Efficiency
.jpg)
How Many Factors Affect Grinding Efficiency of Ball Mill?
2023年9月21日 01 Grinding concentration on ball mill grinding Grinding concentration is one of the important factors affecting the working efficiency of ball millThe influence of grinding concentration is mainly reflected in three aspects: the specific gravity of the slurry, the degree of adhesion of the ore particles around the steel ball and the fluidity of the slurry2020年2月1日 5 The ball mill system in grinding machines is substituted with a compact and modern vertical roller mill which has better drying capacity and energy efficiencyEnergy and exergy analyses for a cement ball mill of a new 2009年6月1日 In this study, the milling of clinker was evaluated by varying the mill speed (24 and 72 RPM), residence time (3 and 5 hours) and grinding media load (30 and 40 %) in a ball millCement clinker grinding: Evaluation of mill spin speed, 2023年10月19日 Energy Efficiency: Energy consumption during clinker grinding can be significant Therefore, efficient grinding techniques and technologies are employed to minimize energy use and reduce production costs, contributing to the sustainability of the cement industry Types of Clinker Grinding Techniques used in cement manufacturing processClinker Grinding Techniques in Cement Manufacturing JM
.jpg)
Solids Choose the Right Grinding Mill Chemical Processing
Combining impact and shearing actions enhances mill efficiency Proper selection of media milling equipment is vital for success in all three areas There are many different types of grinding mills (Table 1) Some devices, such as ball mills, are more suitable for coarse materials2020年1月11日 Working site of ball mill grinding media refilling In addition to the grinding media proportion and frequency, other factors such as the grinding media material, the shape and so on can improve the ball mill efficiency Consult a professional engineer for details The optimized grinding media can improve the ball mill efficiency by about 30%5 Ways to Improve the Ball Mill Efficiency FTM